How to implement a barcode inventory system
Deliveries are coming and going, overwhelming you and your staff trying to keep track of these items whizzing around you.
It can quickly become very chaotic, especially during high demand. Disorganization when handling your inventory serves only to disrupt your business and even harm its reputation. So, how exactly do other companies overcome this task?
At this critical stage, when your order volumes are increasing, you need to know how to implement a barcode system for inventory to keep your company scaling.
This article contains everything you need to know about barcode inventory systems, helping you decide if they are something you need and how to implement them into your workflow.
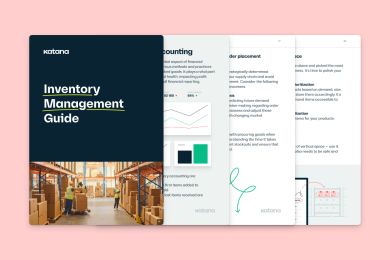
Table of content
- What are barcodes?
- What are the benefits of using barcodes?
- What is a barcode inventory system, and how it works?
- What are the 4 main benefits of a barcode inventory system?
- How to implement a barcode inventory system for your business?
- What to consider when choosing a barcode inventory management system?
- Katana’s barcode inventory system
- Barcode inventory system FAQs
What are barcodes?
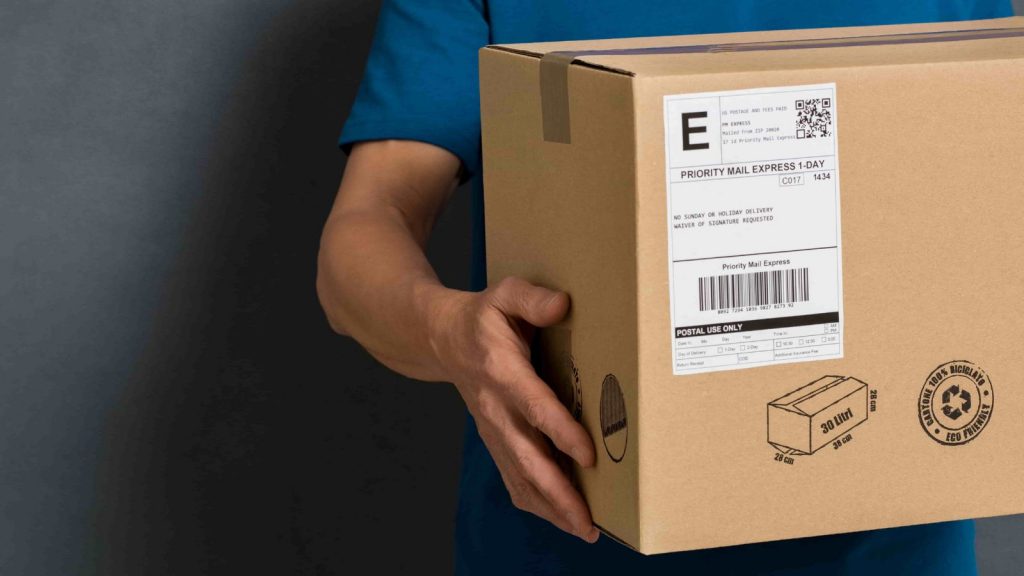
A barcode is a machine-readable code representing information about the product to which it is attached.
A barcode can encode many different pieces of information, such as the price or weight of an item, and can come in many different forms. The two most common are 1D and 2D barcodes.
1D barcodes
1D barcodes are linear or one-dimensional barcodes that consist of black and white bars. They are used for storing information about the item to which it is attached and can be scanned by a laser scanner or camera. 1D barcodes typically contain numerical values but may also encode alphanumeric characters, such as a product name or serial number. Depending on the application, these barcodes can be printed in various sizes and formats.
You can commonly find 1D barcodes on products in retail stores, but they are often also used in digital applications such as ticketing systems and loyalty cards. They are an efficient way to store information and are used in various applications, from part tracking to product identification.
1D barcodes can be scanned quickly and accurately, making them ideal for automating inventory processes. With the right technology, 1D barcodes can also capture additional information, such as expiration dates or batch numbers. This makes them invaluable in tracking products throughout their lifecycle. Some examples include UPCs and ISBN codes for books.
2D barcodes
2D barcodes, also known as matrix codes or two-dimensional barcodes, are made up of black and white cells arranged in a grid pattern. Unlike 1D barcodes, which contain short alpha-numerical values, 2D barcodes can store more complex data such as URLs, text files, and images. These types of barcodes provide users with more flexibility to store larger amounts of data and increase security against data tampering.
Popular examples of 2D barcodes include QR codes and DataMatrix codes. These types of barcodes are often used in industrial processes, such as tracking materials in manufacturing or identifying drugs in pharmaceutical production. They are also commonly found on printed documents, business cards, and packaging.
2D barcodes are an efficient way to store and share information quickly and accurately. With the right technology, they can also be used for authentication purposes, such as verifying a user’s identity or proving that an item is genuine.
Barcodes conveniently store information about products and make it easy to scan and track them.
However, they are not perfect. Barcodes can be hard to read if they are damaged or dirty, and they can also be counterfeit. This can be difficult to spot, so it is important to check the legitimacy of a barcode before relying on it and keep your knowledge up-to-date when implementing an inventory system with barcode scanning.
What are the benefits of using barcodes?
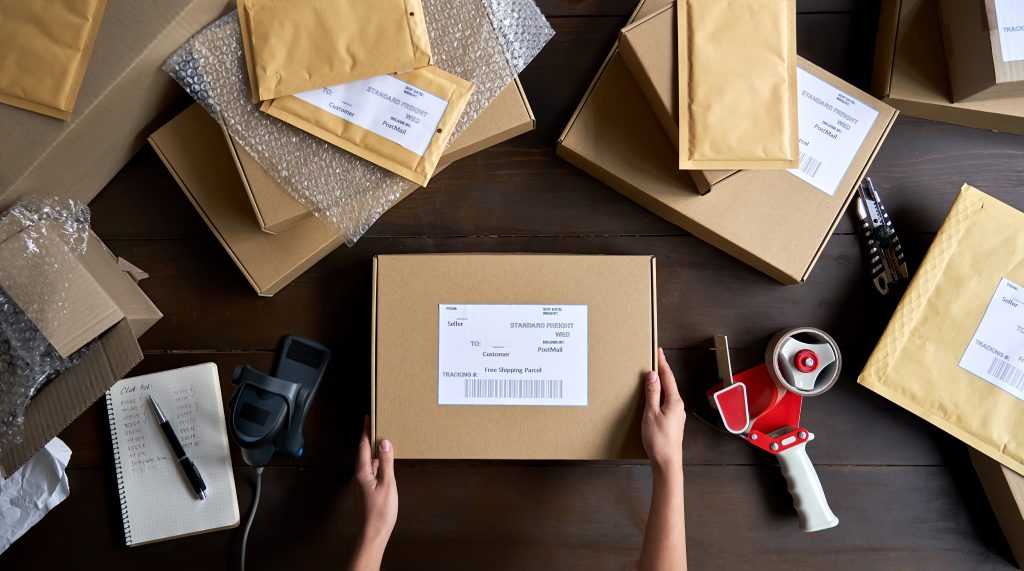
Barcodes offer several significant benefits in various industries and applications, which is evident, seeing how widely they are used. Let’s go over the main ones.
- Efficiency and speed — Scanning barcodes is much faster than manual data entry. This speed significantly reduces transaction time, leading to shorter lines and more efficient inventory management.
- Accuracy — Barcodes eliminate the possibility of human error. The chances of errors in manually entered data are significantly higher than those in barcodes. A barcode scan is fast and reliable and takes infinitely less time than entering data by hand.
- Cost-effective — Barcode systems are relatively cheap to design and print. They do not require extensive training to use and can save money by reducing errors and saving time.
- Inventory control — They provide an excellent way to track inventory and are especially useful in retail and warehousing. Barcodes provide a real-time count of stock levels, leading to more efficient inventory management.
- Versatility — Barcodes are incredibly versatile. They can be used for any kind of necessary data collection. This could include pricing or inventory information, but barcodes are also used in logistics and supply chain management for tracking shipments and products.
- Better data availability — Since barcodes can hold a lot of data in a small space, they allow for the storage of detailed product information. This data can be easily accessed by scanning the barcode.
- Reduction in training time — The training time required for staff to learn how to handle a barcode scanner is minimal compared to the training for complete inventory or data entry systems.
- Improved decision-making — Because barcodes offer real-time data collection and accuracy, they enable more informed decision-making in various business aspects.
- Tracking and tracing — Barcodes are essential in tracking and tracing processes. They are used in healthcare for tracking patient information and medications, in logistics for tracking packages, and in retail for tracking products throughout the supply chain.
- Standardization — Barcodes provide a standardized method for labeling and identifying products, which is useful in global trade and supply chain management.
Overall, barcodes enhance the efficiency and accuracy of data collection and management, providing a simple yet powerful tool for a multitude of industries.
Next, let’s take a closer look at barcode inventory management systems.
What is a barcode inventory system, and how it works?
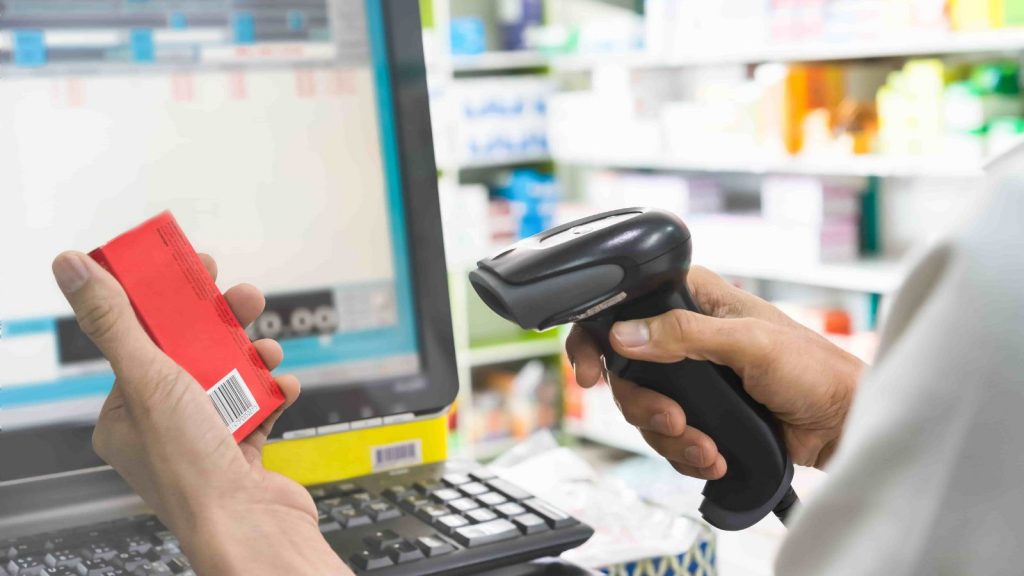
A barcode inventory system is a method of tracking products using barcodes. These barcodes are printed on labels and affixed to items, allowing for quick scanning with a reader or smartphone. This system enables real-time visibility into the location and quantity of each item in your warehouse or store.
When an item is scanned, its information is transmitted to a database for tracking and monitoring. Access to accurate product data facilitates better decision-making regarding stocking levels, purchasing patterns, and more.
Additionally, a barcode inventory system simplifies the generation of reports on performance metrics, such as sales numbers and bestsellers.
This system also aids in eliminating waste by preventing unnecessary restocking and reducing product loss. If managing your business’ growth is challenging due to multiple locations or a vast array of products, implementing a barcode-based inventory system can significantly ease this process.
With precise information about the location of each item, you can make informed decisions about storing new products and reorganizing existing inventory.
If you are experiencing issues with your current inventory management system, such as product loss or damage, inaccurate counts, or misplaced items, a barcode system might be a solution. It can enhance the tracking of your inventory and mitigate these issues.
Additionally, a barcode system increases visibility into your inventory, helping you identify when items are low in stock and need reordering.
If any of the challenges mentioned above resonate with you, investing in a barcode inventory system could be beneficial. Barcodes can save you time and money by improving accuracy and efficiency in your inventory management.
Need a barcode scanning system that syncs with your e-commerce or accounting software?
Be sure to check out the following articles:
What are the 4 main benefits of a barcode inventory system?
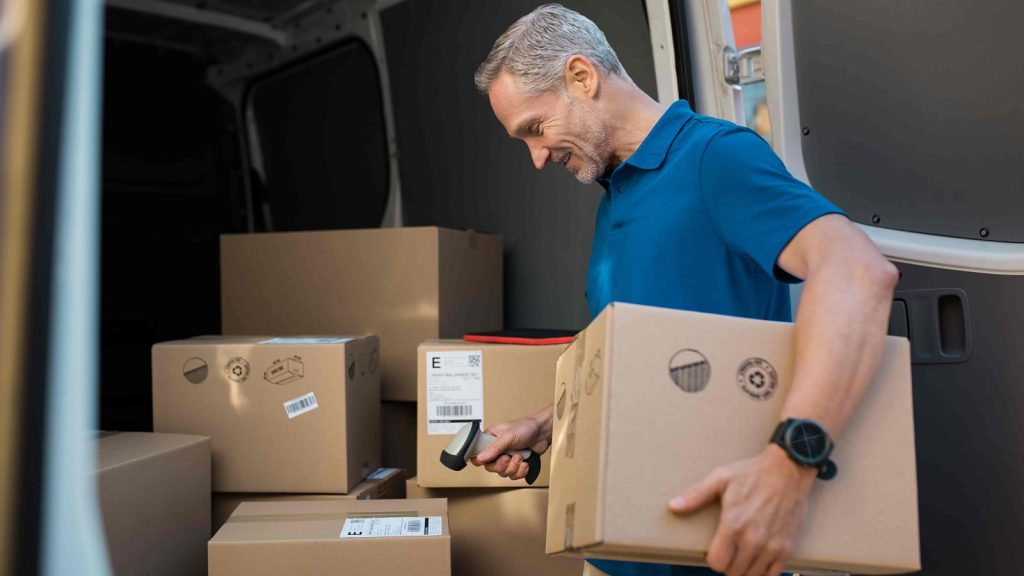
A barcode inventory system helps you:
- Improve your inventory control
- Make better-informed business decisions
- Reduce losses due to theft or errors
- Improve customer satisfaction
But let’s take a closer look at all of these points.
1. Improve your inventory control
There are many reasons why improving your inventory control is important.
Perhaps the most obvious reason is that it can help you save money. If you have better inventory control, you can order less stock and avoid building dead stock items that may become outdated or damaged. In addition, good inventory control can help you keep track of your stock levels to reorder items before they run out and avoid bottlenecks that can cause disruptions to your business operations.
This can also help you to avoid losing sales due to stockouts.
Aside from the financial benefits, good inventory control can also help to improve your customer service levels. If customers cannot find the products they need in your store, they may go elsewhere. This could lead to lost sales and a tarnished reputation.
Improving inventory control can be challenging, but the rewards are well worth the effort. By improving your inventory management, you can boost your bottom line and keep your customers happy.
2. Make better-informed business decisions
Barcodes in shop floor planning can significantly enhance decision-making regarding products and services.
For example, suppose you have a large amount of inventory at any given time. In that case, you can use barcodes to quickly determine which items are selling well, which ones are not selling, and where there may be opportunities to improve sales.
Another benefit of barcodes is that they allow you to collect data about your customers and their purchasing habits more easily.
This information can be used to improve your marketing efforts, better understand customer needs, and make more targeted decisions about product development and product pricing.
3. Reduce losses due to theft or errors
Barcode systems help reduce losses due to theft or errors by providing a means of tracking inventory.
Scanning items at the POS provides an accurate record of what was sold and when. This information can then be used to reconcile inventory levels, helping prevent stockouts and revenue loss. In addition, barcodes can be used to track individual items as they move through the supply chain, making it easier to identify where errors or losses occur.
By having visibility into these areas, businesses can take steps to correct problems and improve the efficiency of their operations.
Barcode systems can also help reduce losses due to theft, as they provide an audit trail for identifying stolen items. This information can be shared with law enforcement, allowing them to investigate and apprehend suspects more effectively.
Overall, by improving visibility and control over inventory levels, businesses can reduce losses due to theft or errors and improve their bottom line.
4. Improve customer satisfaction
A barcode system can help improve customer satisfaction by ensuring accuracy and timely delivery of orders in several ways:
To start off, a barcode system can reduce errors and inaccuracies in order fulfillment by automating the process of assigning items to orders. This enables businesses to better meet their customers’ expectations for fast, error-free deliveries.
A barcode system can also help improve customer satisfaction by enabling businesses to track inventory levels better and identify opportunities for improving efficiency and reducing costs. For example, a barcode system may detect that an item is out of stock at location A, but plenty of units are still available at location B. As a result, the business can transfer these extra units to location A so they can be used to fulfill customer orders, thereby reducing the chances of delays or disruptions in service.
Finally, a barcode system can help improve customer satisfaction by providing businesses with valuable data that can be used to improve shop floor operations and make better decisions about inventory levels, product mix, and other factors that impact the customer experience.
For instance, companies can use data collected through a barcode system to track customer behavior trends and adjust their operations accordingly. This information can then be used to improve the accuracy of predictions about future customer demand, which can help businesses avoid stockouts and other disruptions that can negatively impact customer satisfaction.
Now that you know the benefits, let’s see how to implement a barcode system for inventory.
How to implement a barcode inventory system for your business?
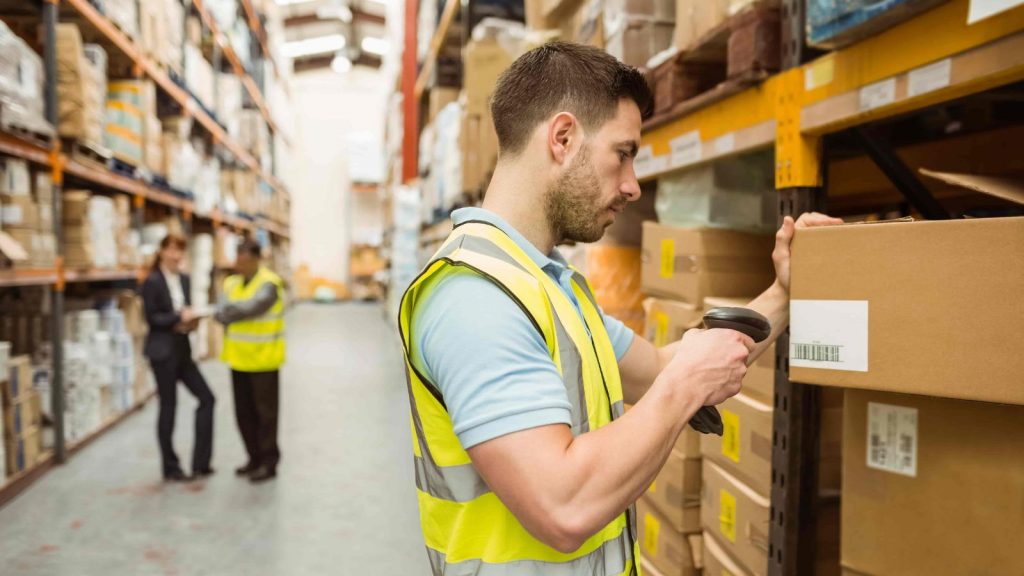
Implementing a barcode system can seem daunting, but these six steps will help you get started.
By planning your system and investing in good technology, you’ll be able to quickly and efficiently manage your inventory moving forward. And with the right system in place, you’ll have more time for what truly matters — growing your business. Whether you need to keep track of limited-edition products or perishable inventory or simply want to streamline your stock tracking process, implementing a barcode system can help simplify things and make your life easier.
So, where should you start?
1. Decide what type of barcode system you need
There are several options available for barcode systems, so it’s important to choose the one that best fits your needs.
A simple scanner and software solution may be all you need if you’re only looking to track inventory levels. But suppose you want to be able to track product location or keep track of more detailed information like expiration dates. In that case, you’ll need a more robust system like barcode inventory management software.
2. Choose the right barcode scanner
Once you know what type of system you need, it’s time to select a suitable scanner.
There are many different scanners on the market, so choosing one that will work well with your chosen software solution and fit your budget is crucial. Not sure where to look? Here is a short list of barcode scanners that can be used with 3rd party inventory barcode systems:
3. Set up your barcode system
Once you have your scanner and software in place, it’s time to set up your system.
This step will vary depending on the type of system you’ve chosen, but in general, you’ll need to create barcodes for each product and then print them out or attach them to your product packaging.
For example, to get set up with Katana’s cloud inventory software, you need to follow these steps:
- Log in
- Under settings, go to Barcodes and enable the type of barcodes you wish to use
- When receiving raw materials or other deliveries, plug in your barcode scanner, activate scanning, and you’re good to go
4. Train your employees on how to use the system
Once your system is set up, it’s essential to train your employees to use it properly.
This is a crucial step for ensuring that your system runs smoothly and efficiently. Depending on the complexity of your system, you may need to provide employees with additional training on an ongoing basis.
5. Test your system regularly
It’s important to test your barcode system regularly to ensure it’s working properly. This step will help you catch any errors or problems to fix them before they cause major issues.
6. Stay organized and keep track of your inventory
Finally, you need to stay organized and keep track of your inventory levels.
This step is especially important if you have a large inventory or sell products with limited shelf lives. You can avoid overstocking or selling expired products by keeping track of your inventory. And if you have a barcode system in place, this task will be much simpler.
And that’s how to set up a barcode inventory system. Next, let’s look at things to consider when looking for a suitable system.
What to consider when choosing a barcode inventory management system?
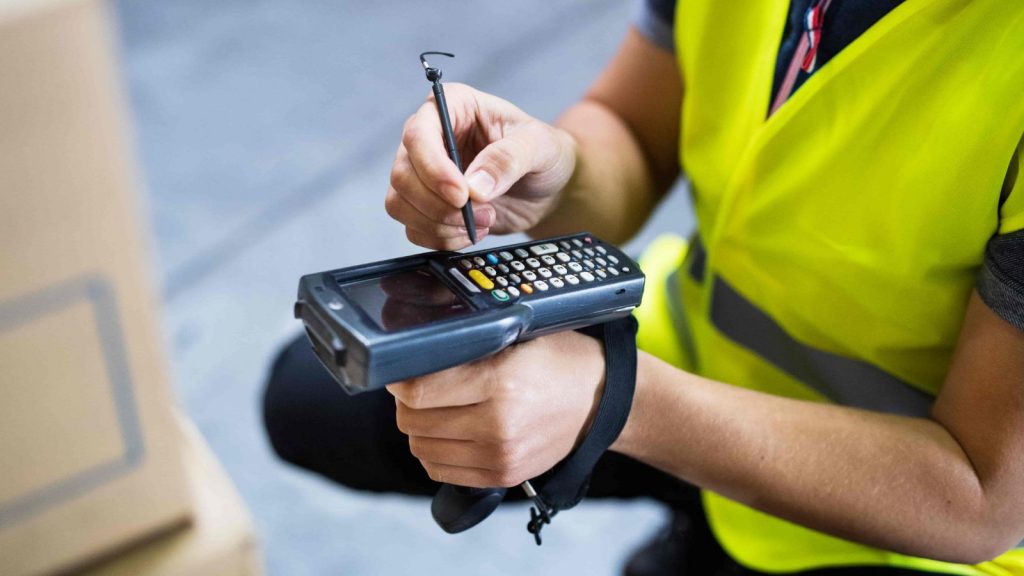
The three things to consider when implementing an inventory barcode system:
- Define your goals
- Account for your software and hardware needs
- Get expert advice
Let’s explore each step in more detail.
1. Define your goals
Before you start using barcodes, take some time to think about what you want to achieve with a barcode inventory system:
- Track stock levels
- Improve customer service
- Reduce shrinkage
Once you know your goals, you can choose the right barcode system for your needs.
2. Account for your software and hardware needs
Barcode systems require software and hardware, so it’s important to consider your needs before investing in a system.
Do you need a handheld scanner for mobile scanning? Will you be printing your labels or using pre-printed labels? Ensure you have all the necessary hardware and software before implementing a barcode system into your business’ workflows.
3. Get expert advice
While it’s possible to implement a barcode system yourself, you will often get better results by consulting with experts in this field.
Experienced barcode consultants can advise on the proper hardware and software for your needs, ensure your system is compliant with industry standards, and troubleshoot any issues that arise during the implementation or use of your barcode inventory system.
By following these tips, you can get the most out of your barcode system and improve efficiency across your organization.
Katana’s barcode inventory system
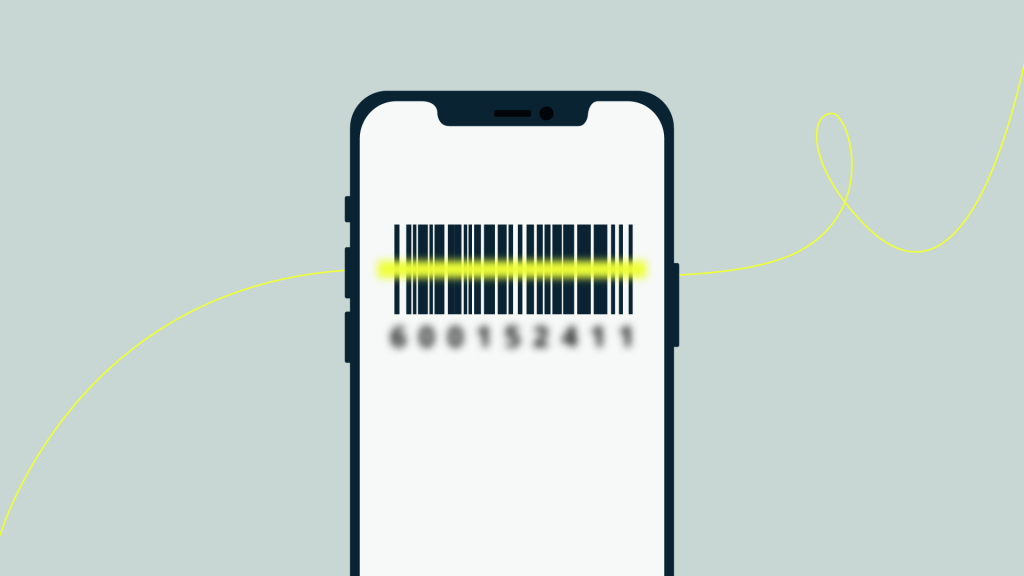
Katana is an all-in-one solution for businesses looking to centralize their entire operation to one intuitive platform.
By automating the process of tracking inventory levels, barcode inventory systems can save you time and money while reducing errors.
Katana’s inventory management software helps companies scan their barcodes to track items moving in and out of stock. When an item is scanned, Katana automatically updates its records to reflect the current quantity on hand. You can easily see when something needs to be reordered, which helps ensure that no items are lost or misplaced.
In addition to being more efficient, barcode inventory systems can also help businesses save money by reducing the time employees spend manually entering data and the number of mistakes that occur during this process.
Katana empowers businesses with all the necessary features needed for:
- Assigning barcodes to inventory items
- Seeing barcode numbers within Katana
- Identifying inventory items using barcodes
If you’re looking for a way to streamline your inventory management system, consider investing in a barcode inventory control system today — you’ll be amazed at how much time and money you can save in the long run.
Barcode inventory system FAQs
How do I create a barcode inventory system?
To create a barcode inventory system, you can follow these steps:
- Decide on the type of barcode you’ll use (like UPC or QR codes)
- Purchase or generate barcodes for each item in your inventory
- Choose a barcode scanning device or app to read these codes
- Select an inventory management software that can integrate with your barcode system, allowing you to track and manage inventory efficiently
What type of barcode is used for inventory?
The most common types of barcodes used for inventory are Universal Product Codes (UPC) and International Article Numbers (EAN). UPCs are widely used in the United States and Canada, while EANs are common internationally.
For more complex needs, Quick Response (QR) codes are used because they can store more information and are easily readable by smartphones.
How do barcodes help with inventory?
Barcodes significantly enhance inventory management efficiency. They allow for quick and accurate tracking of products as they enter and leave the inventory. This helps in maintaining accurate stock levels, reducing manual entry errors, and speeding up processes like restocking, auditing, and order fulfillment.
Barcodes also facilitate better data analysis for inventory optimization.
How does a barcode inventory system work?
A barcode inventory system works by assigning a unique barcode to each item in the inventory. When these barcodes are scanned using a barcode reader or a smartphone app, the information is transmitted to an inventory management software. This software tracks the movement of items, updates stock levels, and provides real-time data on inventory status. This system streamlines operations by automating data entry and providing quick access to inventory information.