How to master multilocation inventory management
Setting up multilocation inventory management is a tough task for many growing businesses. That’s why gathering the right tools and strategies is vital to making sure that operations still run as normal.
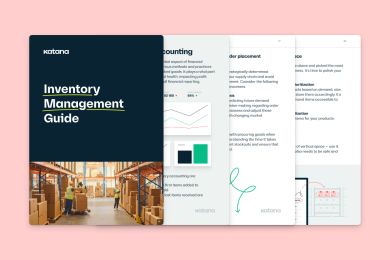
There’s no sweeter sight than the steady growth of your business as you watch the fruits of your labor come to the fore, and your sales reports read as fine as ever.
But there’s no doubt that success brings challenges in itself. And one of the main obstacles to taking your business to the next level will always be a matter of space.
Whether you have decided to take your operation global or even just require extra storage, it’s very likely that, at some point, you will encounter issues with multilocation inventory management.
In other words, you are going to have difficulties managing stock and how it moves around, especially if you distribute manufacturing, too.
The complications can be endless when there is more than one production schedule and stock room to manage. And without the proper tools, you may easily feel that your growth is getting stunted.
Like a flower that’s outgrown its pot, your business will lack the space to grow and risk suffocating without a new pot.
Now, that might seem like a tough hill to climb. But there are methods you can use to lighten the load, and thankfully, there is smart inventory software out there that deals with this precise issue.
But before we get to that, let’s dive into what multilocation inventory management really means and how it applies in the modern world of commercial entrepreneurship.
Table of contents
- What is multilocation inventory management?
- Does your business require multilocation inventory management?
- Why do businesses need multi inventory management?
- Multilocation inventory management complications
- Tips for inventory management in multiple locations
- Multilocation inventory with cloud inventory software
What is multilocation inventory management?
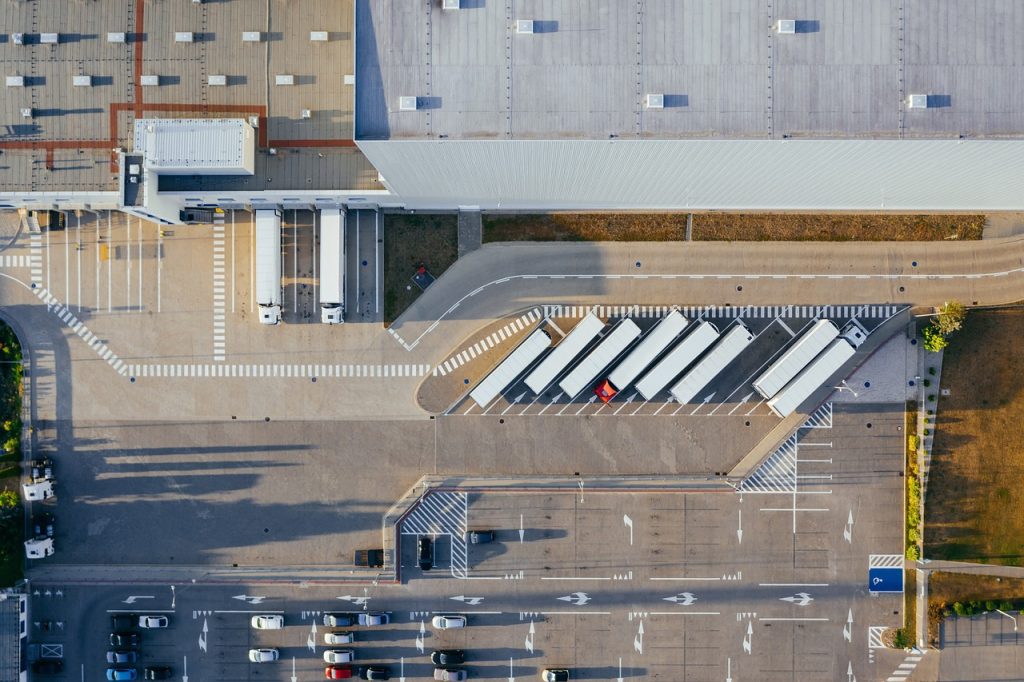
Multilocation inventory management is a strategy to efficiently control and coordinate inventory across various locations, warehouses, or production sites.
Also known as multilocation warehouse management, this approach involves the synchronization of inventory control and order fulfillment to ensure seamless operations despite geographical distribution.
With warehouses scattered across the country, and in some cases worldwide, different challenges arise that threaten to disrupt inventory operations across the entire supply chain.
The objective is to optimize the storage, movement, and utilization of inventory across these diverse locations, ensuring that materials are available where and when they are needed.
Does your business require multilocation inventory management?
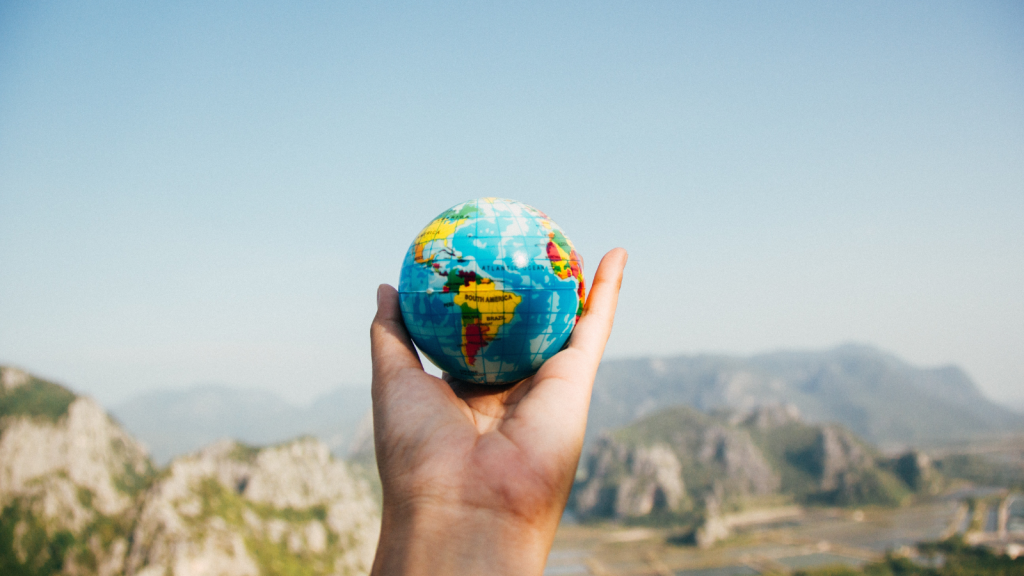
The first step toward enhancing your inventory management involves inspecting your stock operations and determining if adopting a multisite management strategy is necessary.
To find the best solution, the following key factors need to be analyzed.
1. Geographical expansion
Geographical expansion means spreading its operations to different locations, including branches, warehouses, or retail outlets in various regions or countries.
This means dealing with diverse markets, various consumer behavior, and logistical complexities. Each location may have different demand patterns, regulatory requirements, and cultural preferences.
Multilocation inventory management enables businesses to coordinate and control their inventory across all sites.
It involves using specialized inventory software and strategies to keep track of stock levels, streamline order fulfillment, and optimize the movement of goods between locations.
Additionally, it contributes to supply chain resilience by diversifying storage locations, making the business more adaptable to unforeseen issues in specific regions.
2. Logistical challenges
Logistical challenges encompass difficulties associated with managing the movement and storage of goods across various locations.
When a business operates in multiple places, it faces logistical puzzles such as coordinating shipments, optimizing transportation routes, and ensuring timely deliveries.
These challenges are heightened by factors like varying distances between locations, diverse transportation infrastructure, and fluctuations in demand.
Utilizing specialized software and strategies allows businesses to optimize inventory levels, reduce transportation costs, and enhance the overall efficiency of their supply chain.
3. Production complexity
Production complexity refers to the specific challenges manufacturers encounter when operating production facilities in different locations.
This happens because the business has to organize and handle creating products in different places, and each site has its own specific challenges and things to consider when it comes to managing materials and making the products.
For businesses engaged in production, there is a heightened need to synchronize production schedules, manage the flow of materials between all places, and address variations in demand and resource availability.
By utilizing inventory management across multiple locations, businesses can enhance their overall production efficiency.
This approach facilitates seamless coordination between scattered production sites, reduces delays in material availability, and helps maintain consistent quality across all locations.
Why do businesses need multilocation inventory management?
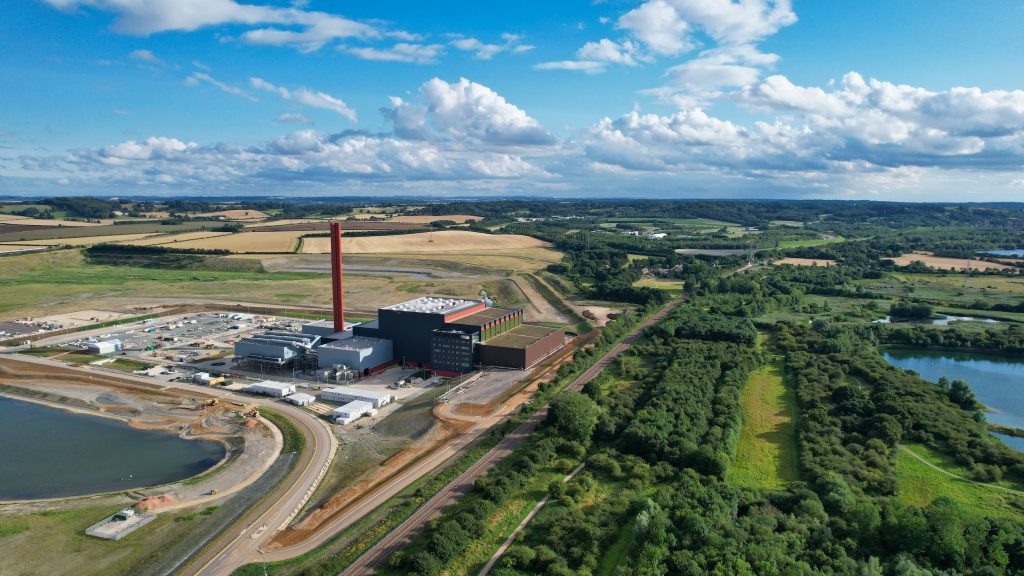
Why do businesses need multilocation inventory management?
Imagine you’re running an online store with all your products stocked in different places. Let’s dive into why this multilocation inventory game is a big deal.
E-commerce
When virtual shelves require constant restocking, managing inventory across multiple locations ensures a smoother and more efficient operation.
Moreover, the e-commerce inventory landscape often involves a complex network of sales channels, suppliers, distributors, and fulfillment centers.
Multilocation management acts as the foundation that ties these elements together and keeps them stable, ensuring a synchronized flow of products from various sources to meet customer demand.
This not only facilitates smoother order fulfillment but also enables businesses to optimize their inventory levels, preventing excess stock that can tie up capital.
Dropshipping
When you sell items without actually keeping them in a warehouse, then that’s called dropshipping.
As efficient as it is having to not worry about stocking the products, there’s a catch – you still need to keep tabs on those invisible goods.
Multilocation management allows you to track products, plan routes, and ship orders directly to the customers’ door, no middleman required.
Manufacturing
If you’re producing your own items to sell, like custom T-shirts or funky gadgets, you’re in the manufacturing game.
That adds a whole new layer to your stock management, including raw materials, supplies, and work-in-progress inventory.
Manufacturers need end-to-end traceability to track the entire lifecycle of a product, ensuring that every component, ingredient, and finished item is accounted for.
This tracking provides insight into the production process while also supporting quality control and compliance with industry regulations.
Pro tip: Calculate cost of goods sold (COGS) with inventory valuation methods and put a value on your remaining inventory levels. Explore the different types of inventory valuation methods your business can use when checking in on your stock levels.
Safe operations
Why bother with all this multilocation wizardry? Its true superpowers are revealed once your operations hit a glitch. It could be a transport hiccup or a wild event like a fire.
With backup spots for your goodies, you’ll minimize the risk of having to cancel orders or running past your planned delivery dates.
It’s also very cost-efficient, eliminating the need for express shipping or other costly last-minute solutions.
Running inventory in multiple locations is a true safety net for your warehouse management when unexpected challenges arise, as they usually do, unexpectedly.
Customer satisfaction
Swift deliveries are crucial for customer satisfaction.
Multilocation inventory management strategically places and routes products, reducing shipping times and elevating the customer experience.
This approach minimizes stockouts, enhances product availability, and ensures accurate order fulfillment. Such benefits enable businesses to adapt swiftly to changing market demands.
With smart multilocation moves, you’re not just avoiding chaos but also getting packages to your buyers faster than a pizza on a Friday night.
Potential to lower costs
On first look, setting up a secondary warehouse might seem counter-intuitive when it comes to reducing costs.
But consider the fact that the costs of transportation and labor can be much higher depending on the location of your warehouse. If you are further from consumers and delivery infrastructure, then there are greater costs for you to incur.
Plus, you can optimize your order fulfillment time and satisfy customers with faster deliveries.
Retail outlet
Many direct-to-consumer brands have found that selling stock in their own retail outlets can bring in a whole new line of customers.
Even staples of this model, such as Away and Glossier, have their own flagship stores.
This also means, though, that they have to start inventory management in multiple locations, even if for just finished goods.
Retailer or reseller inventory
Despite the rise of the direct-to-consumer business model, many businesses still use middlemen to sell part of their inventory.
Most of the time, it’s not needed for them to track inventory in these locations, but it does happen under certain circumstances. For example, if you have a consignment inventory agreement with a reseller, in which case they only pay for the stock after it is sold.
Pro tip: Looking to organize your inventory? Try out our free inventory spreadsheet template to see if it can help you get started.
Multilocation inventory management complications
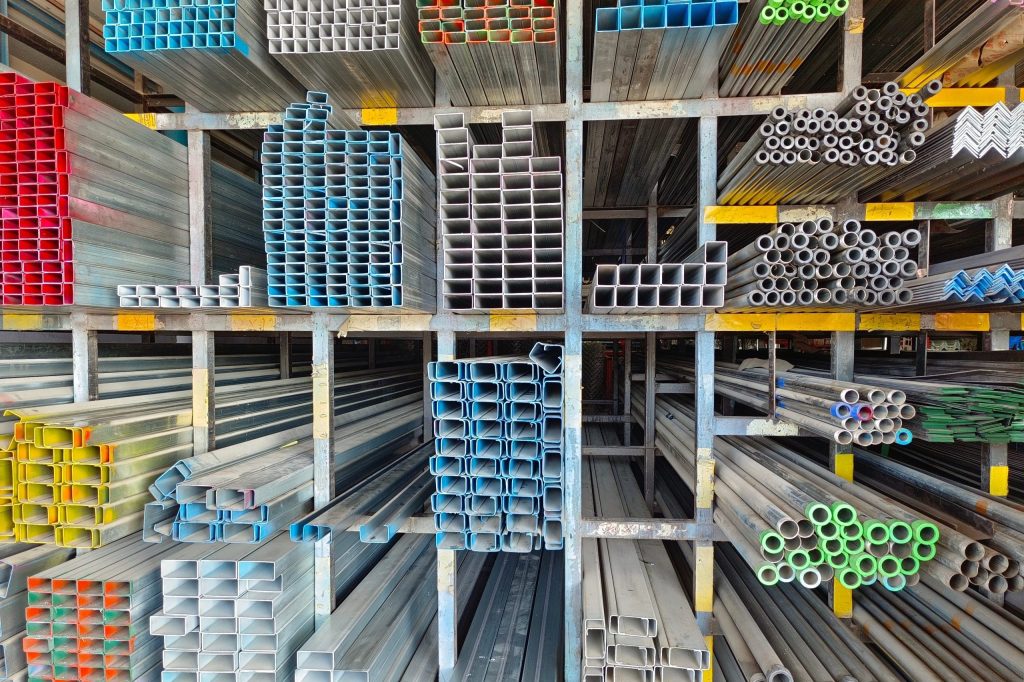
Right, so we know why businesses need inventory management for multiple locations. But what are the challenges that come with this approach?
Unsurprisingly, there are more than a few problems that arise when you split your cozy business up around the land.
1. Stock counting
Maintaining inventory across multiple locations means juggling stock counts in each of your warehouses.
This demands meticulous attention and organization, particularly when materials are in constant motion between sites.
The task involves not only tracking quantities but also ensuring accurate record-keeping amid the dynamic movement of materials.
2. Communication
With operations scattered, effective communication becomes a notable hurdle.
When employees are not physically present in the same location, miscommunication can easily arise.
This poses a risk of bottlenecks in inventory processes and order management, highlighting the need for streamlined communication channels and protocols.
3. Inventory level management
Managing inventory levels becomes a critical challenge, especially for businesses with diverse products and multiple manufacturing sites.
The complexity intensifies when materials stored in one location need to be synchronized with production schedules in another.
This issue requires strategic planning and robust systems, ideally software solutions, to take care of some of the calculations for you.
4. Types of inventory
For manufacturers operating in various locations, the organizational puzzle deepens.
Juggling different types of inventory simultaneously adds layers of complexity.
Materials meant for distinct products may be stored across multiple warehouses, requiring a sophisticated approach to streamline production schedules and maintain seamless operations.
5. Production scheduling
Imagine the intricacies of setting up production schedules while factoring in materials stored in entirely different locations.
This scenario is a reality for businesses managing inventory across multiple sites.
The challenge lies in aligning production timelines with the availability of materials spread across diverse warehouses.
Don’t fret, though.
There are solutions here, some of which are going to make an immediate difference.
Tips for inventory management in multiple locations
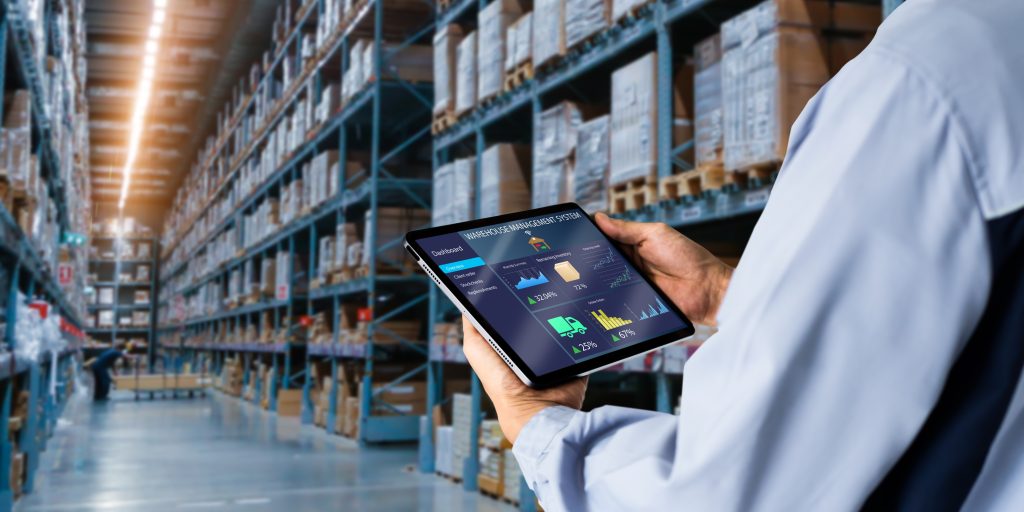
1. Adopt a multilocation inventory management system
The right software can take you a long way when it comes to multilocation inventory management.
It’s important that you look for solutions such as inventory management software that can manage multiple locations, inventory, and production at the same time.
Because as vital as it is to manage stock, there’s no point in the endeavor if you don’t consider how your materials are being used and your orders being fulfilled.
2. Centralize your data
Online solutions such as cloud software provide total control across all your warehouses and supplier locations.
It’s the perfect way to streamline communication, reduce operations costs, and access data. This alignment is particularly vital when dealing with multiple warehouses, as it mitigates the risk of miscommunication, reduces errors, and promotes consistency in operations.
Imagine being able to check your business information from anywhere, whether you’re at home, on a bus, or at the beach. That’s what centralizing data does – it lets you access all your important details as long as you have access to the World Wide Web.
3. Locate warehouses artfully
Don’t underestimate the impact geographical location can have on your business.
You want to position your warehouses as closely as you can to each other whilst also keeping them near consumers. This way, you can save on transportation and logistical costs.
Just be aware that the closer you are to consumers and urban areas, the more likely you are to pay a higher cost of rent, labor, and for producers also manufacturing overheads. Striking the right balance is key here.
4. Plan for demand
Forecasting customer demand is a tough task to undertake, regardless of your industry.
But taking the time to work on demand planning means that you will better be able to optimize your inventory. In which case, there is less chance you will incur carrying costs due to overstocking, a high-risk event with multiple inventory locations.
5. Optimize warehouse layout
The way your warehouses are laid out can have drastic effects on the efficiency of your overall business.
You should take the time to make sure your various material inventory is as close as possible to the appropriate workstations. And keep products that are sold most often close to your shipping area.
In the same way, you should carefully consider which of your warehouses store different stocks. Any unnecessary additional transportation can ultimately delay deliveries to your customers.
Even a detailed map of the warehouse posted at the entrance can help employees gain a quick grasp of where everything is.
5. Establish standards for processes
While taking initiative is good, it becomes problematic when it starts causing disruptions.
Having set standards for processes means that every location completes tasks in a similar way, maintaining quality and making things easier for the next steps.
This avoids redoing work and keeps everything running smoothly across all different locations.
Consistent processes also help team members understand their roles better, ensuring everyone is on the same page and knows exactly what is expected of them.
Additionally, standardized processes help boost efficiency by minimizing errors and promoting a more organized workflow.
When everyone follows established procedures, it fosters a collaborative environment, making it easier to track progress and catch any potential issues early on.
6. Set safety stock
Knowing when to purchase more materials becomes a lot trickier when inventory is spread out. Especially if production also occurs in different places.
As a result, you will have to pay more attention to your stock levels to ensure you don’t run out and cause delayed deliveries.
Ideally, you set an amount of safety stock for each of your items, as well as reorder points to make sure you don’t have to dip into your safety net more than necessary.
Multilocation inventory with cloud inventory software
Katana tracks your entire order fulfillment process, from multilocation inventory management to production and sales. But what’s really great is that you can split your locations up so that they take on these elements accordingly as well.
If a site only holds inventory, then you will have the option to manage stock and purchases, which makes the organization much more straightforward.
Clearly, there are ways that you can manage your multiple sites for inventory without totally losing track.
But there are a lot of details to be managed here.
Materials, finished products, purchase orders, and not to mention the warehouses themselves.
That’s why many businesses make use of software that supports inventory management in multiple locations. These can help automate your stock management and keep track of how items move between warehouses.
Katana Cloud Inventory is an all-in-one solution that can tackle the inventory needs of all your places, in one place.
The system will keep track of quantities of materials and inventory for each of your locations separately. On top of that, whenever an order is fulfilled, the necessary inventory will be reduced automatically.
This means that your inventory for each location is clear to see, in real-time, and in accordance with your scheduled operations.
So, let’s imagine, for example, that materials are running low in one location for a set of sales orders, but you have a surplus in the other warehouse. With Katana, you can quickly make a stock transfer from one location to another and your quantities will be updated automatically.
This way, you can manage your manufacturing business from a single visual platform and eliminate the need for constant tedious calculations altogether.
If you’re more of a visual person then be sure to check out this video explaining Katana’s multilocation features.
But that’s just the start, Katana also offers:
- On-demand access to your costs
- End-to-end traceability across a product’s lifecycle
- Syncing accounting with QuickBooks Online
- Inventory management for raw materials, work-in-progress, and finished goods
- Integration with Shopify, WooCommerce, and other e-commerce platforms
- A way to keep your entire business workflow on a single platform
Embark on a journey towards enhanced multilocation inventory management by implementing Katana. Schedule a demo call today to gain a comprehensive understanding of Katana’s capabilities before making your decision.
Ultimately though, you shouldn’t see multilocation inventory management as a beast that needs taming. We know it might be hard to do, considering the challenges it initially presents.
But rather see it as an opportunity to lower costs, improve efficiency, and, most importantly, grow your business.
Just take your time and use the right tools.
It won’t be long before the struggle is behind you and fresh markets lay ahead.