How to apply manufacturing capacity planning in your business
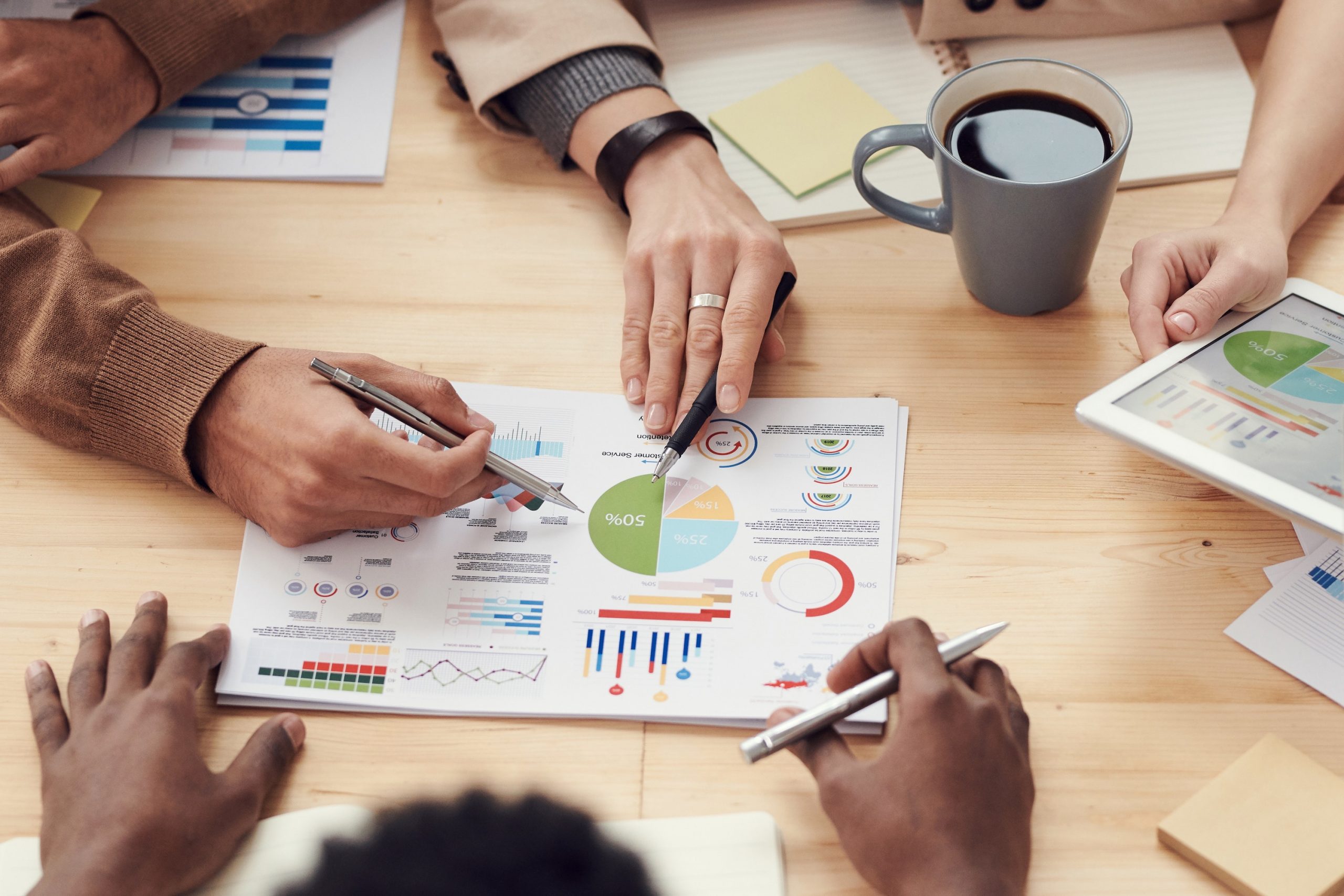
Your analyst crunched the numbers and provided you with a demand forecast. Now, you need to figure out the capacity and devise a plan to ensure your production lines can keep up. This can be a headache when managing your shop floor.
But you can cure those aches by adopting capacity planning into your business, a model that will help you determine the most realistic approach to manufacturing.
In this article, we’ll figure out answers to questions like what is capacity planning in manufacturing, how it works, and how you can get started with it.
What is manufacturing capacity planning?
Manufacturing capacity planning is a method makers use for calculating how much they can realistically produce on their production lines to keep up with forecasted demand. Capacity planning has to consider factors such as:
- Available resources
- Lead times
- Production processes
Your capacity plan can be set to achieve short or long-term goals. Regardless of the period, the main objective of manufacturing capacity planning is to increase your profits and minimize costs.
You can read more about setting goals in the rough cut capacity planning article. But, for now, let’s quickly look at resource planning.
What is resource planning?
Resource planning is the process of managing your resources, such as personnel and machines, and allocating them to projects.
Resource planning also includes analyzing current resource use and making recommendations for how resource use can be optimized. In addition, it involves creating strategies to best utilize the resources at hand in order to reach desired outcomes and goals.
The 3 types of capacity planning in manufacturing
Before starting, you need to be aware of three main types of manufacturing capacity planning. Having a plan in place will ensure you have the right amount of everything you need to produce your products and grow your business.
Workforce capacity planning
Workforce capacity planning means you will ensure that you have enough team members working for the required hours to produce your items. Workforce planning is easier when you have an overview of your shop floor operations, so it is worth investing in a platform that can provide this.
Equipment capacity planning
Equipment capacity planning ensures that you have the right equipment available and that it’s used efficiently to produce and complete your orders. Depending on what you are making, this can be anything from assembly line components to drilling machinery.
Product capacity planning
Product capacity planning makes sure you have enough raw materials and products to complete an order. Proper raw material management is critical to product capacity planning, so confirm that you have suitable systems to track and monitor your materials.
Benefits of production capacity planning
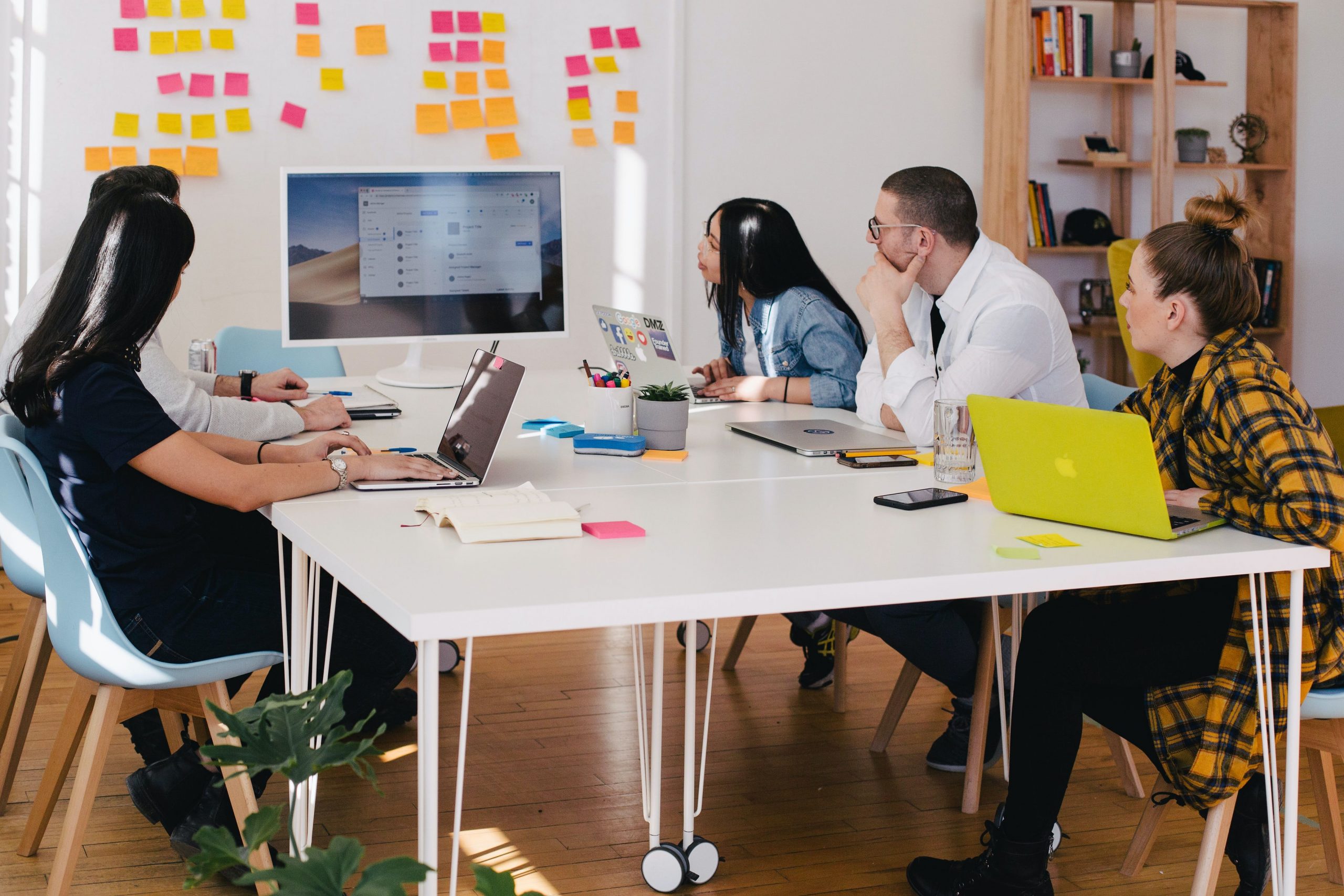
Production capacity planning is an essential tool for organizations to maximize the efficiency of their production, and ensure a smooth workflow. It can help businesses anticipate and plan for any changes in demand, optimize resources, reduce costs, identify bottlenecks, and prevent product shortages. Ultimately, capacity planning in production can improve customer satisfaction by helping businesses meet customer orders on time.
Benefits of production capacity planning include the ability to plan ahead, anticipate future demand, and reduce manufacturing costs. It also enables businesses to identify potential problems early on and implement solutions quickly, allowing them to react swiftly to changes in market conditions or customer needs. Furthermore, it helps optimize resources by ensuring they are used as efficiently as possible.
Capacity planning in production also helps to ensure you have the right people working on a project, and the monetary resources to deliver quality work on time.
Your capacity plan isn’t just a matter of comparing work hours against requirements but helps you to create a healthy workplace with scalability as the focus.
Without a capacity plan, you run the risk of:
- Workers being overworked and scheduled, which will lead to exhaustion and burnout
- Team members’ morale dropping
- The quality of work dropping
- Your manufacturing lead times increasing
Capacity utilization formula
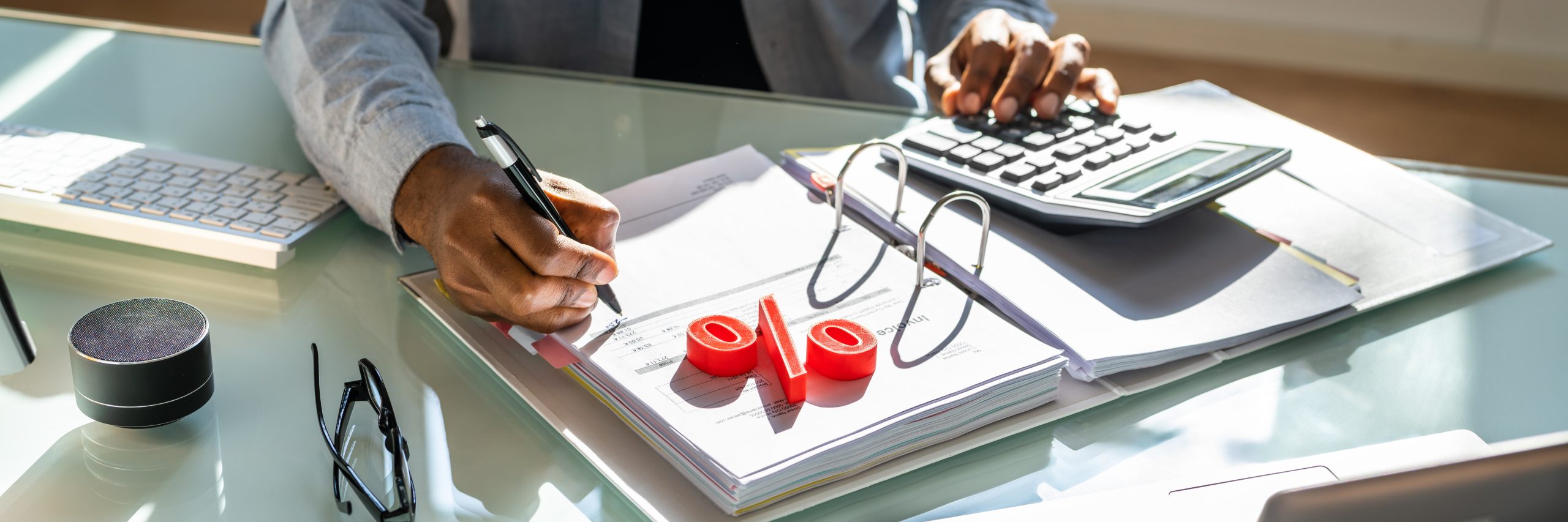
Capacity utilization measures the effectiveness of an organization’s production processes. It is an essential metric for organizations to track, as it helps them understand how efficiently they use their resources to produce goods.
The formula for capacity utilization is:
Capacity utilization = (Actual output / maximum potential output) * 100%
Actual output is the number of goods the organization produces, and maximum potential output is the maximum amount of goods the organization can manufacture with its current resources. Dividing actual output by maximum potential output and multiplying by 100%, we arrive at a percentage representing the organization’s capacity utilization.
For example, let’s say a factory has a maximum potential output of 100 units per day, but it actually manufactures 80 units per day. The capacity utilization for this factory would be calculated as follows:
Capacity utilization = (80 / 100) * 100% = 80%
This tells us that the factory uses 80% of its capacity to produce goods. If the factory were to increase its actual output to 90 units, its capacity utilization would increase to 90%. On the other hand, if the factory were to decrease its actual output to 70 units, its capacity utilization would drop to 70%.
By tracking capacity utilization, organizations can identify opportunities to improve their processes and increase efficiency.
5 best practices for manufacturing capacity planning
As you’ve already gathered, the best way to look at your capacity plan is to remember that often these resources are people. If you’re unable to plan for the human element of manufacturing, you’ll encounter issues.
So, let’s see the five best practices for developing your capacity plan.
1. Tracking time and level of effort
You might be under the impression that completing a task takes 30 minutes, but in reality, it might take up to one and a half hours. If this is the case, you will need to figure out where the discrepancies occur.
Ask team members how long it takes them to usually complete a task, or have them fill in timesheets. This will help you make better forecasts on manufacturing completion times in the future.
2. Identify bottlenecks
Identifying bottlenecks in production and monitoring the amount of work passing through these points can allow you not to overload a workstation or cause a production-stopping problem.
You can use MES software to stay on top of your bottleneck management. A manufacturing execution system can help you with it by allowing you to:
- Monitor production progress
- Reallocate resources to address bottlenecks
- Assign and track tasks on the shop floor
3. Schedule buffers for L&D
According to one survey, 70% of workers believe they haven’t mastered the skills needed for their current jobs.
Learning and development (L&D) shouldn’t be considered an optional perk for your workers or exclusive training for managers. L&D is an integral part of ensuring the delivery of quality products and improving your manufacturing lead time.
Therefore, when you’re putting together your capacity plan, it’s important to leave some time free to schedule L&D sessions for your workers.
4. Calculate your true availability
Besides designing or building products, your employees have all sorts of administrative tasks. Some examples of this could be:
- Checking emails
- Searching for information
- Cleaning the factory and machines
- Even sitting in unproductive meetings
You will need to calculate the amount of time an employee spends on these tasks to determine their true availability when doing your manufacturing capacity planning.
5. Prioritize projects to allocate resources
Finally, prioritizing projects and manufacturing orders is a good practice for developing your capacity plan. The criteria for a priority project can be:
- Time-sensitive orders
- An important opportunity for your business
Finding a tool that can help you prioritize manufacturing orders will allow you to communicate easily with your employees about which tasks need to be completed sooner rather than later.
Capacity planning challenges
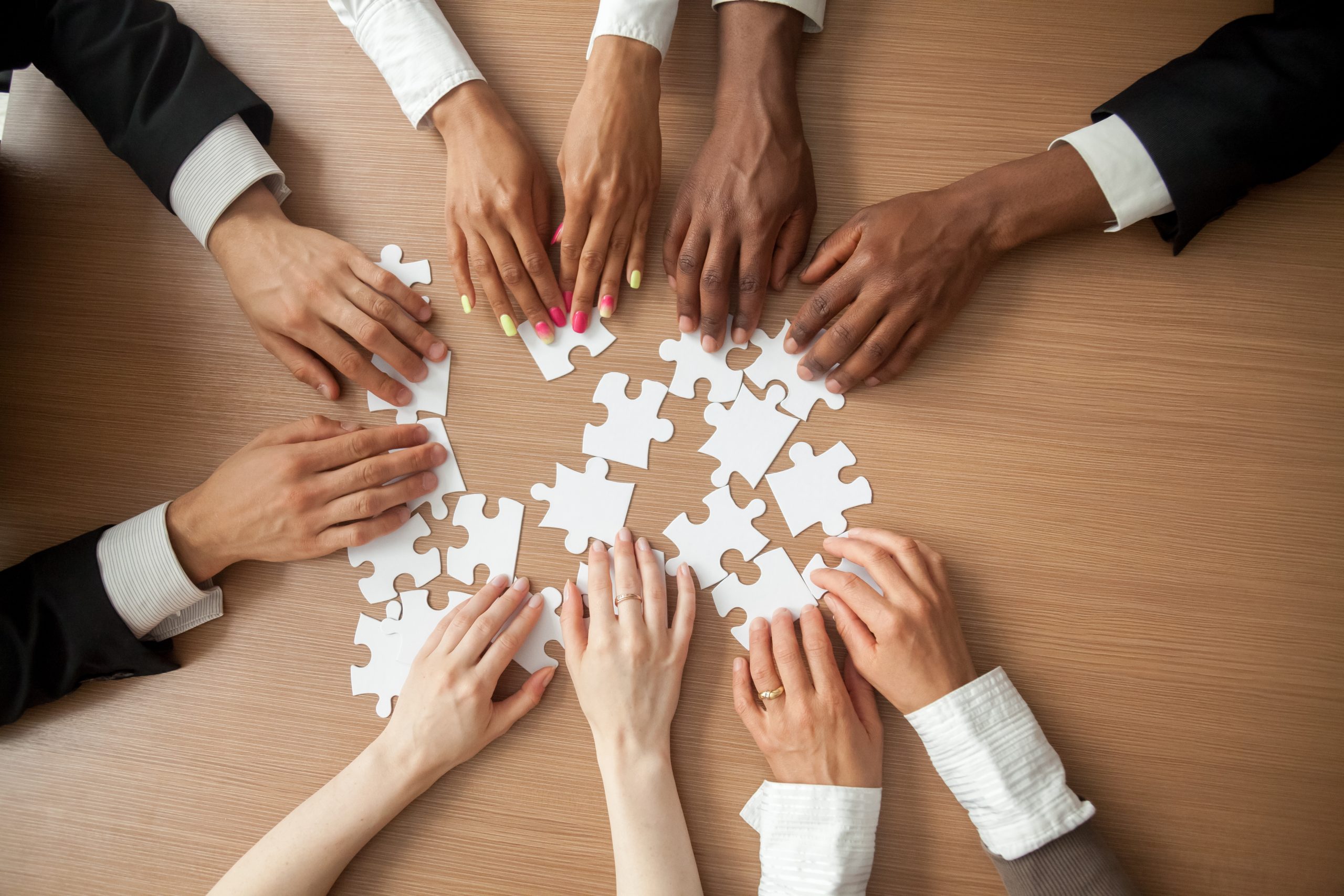
You need to overcome challenges to succeed when working on your production capacity planning. Let’s see the main two hurdles managers must overcome when developing their capacity plans.
Project management maturity
This ties in with what was mentioned about focusing on the skills of your workforce. Your production capacity plan will only be as strong as the abilities of the planner.
The best capacity plans are created in collaboration between managers and team members. Putting together this plan requires experience and flexibility to adapt when things inevitably don’t go to plan.
Data granularity
Your production capacity plan relies heavily on data, such as the performance of your business. However, the more data you collect, the more effort is required to maintain these documents.
When collecting information, decide if you should focus on:
- Organizational level
- Timeframes
- Production or order scheduling
6 recommendations for capacity planning
If you’re ready to get started on the road to developing your capacity plan, you can use the following tips to kick it off:
- Begin by looking into critical resources — You don’t need to jump into the deep end by capturing and analyzing data for every team member. First, start by picking just one or two high-demand resources and investigate their utilization and capacity.
- Look into project or workstation estimates — If working out a capacity plan in manufacturing is something new to you, don’t start by analyzing the individual tasks of resources. Even though that’ll be the eventual goal, just by looking into the performance of one workstation, you’ll start to understand the capacity levels of this area, address that, and move to the next station until you can delve deeper.
- Capture and use data — You need to start using the collected data. Otherwise, if you don’t utilize the data, your workers will eventually stop collecting it for you, as it’ll be a waste of their time.
Want to learn more about how to use data?
Check out the article on manufacturing analytics to learn about the most valuable metrics in production and how you can use these to improve efficiency and maximize profits.
- Communicate — While you set out to record and collect this data, be transparent with your workers. Make them aware that the purpose of this is to improve productivity. Let everyone in the business know what is expected of them and how it all serves to help everyone be more successful.
- Learn how to forecast demand — A great capacity plan depends on how good a person’s forecasting is. Take the time to learn how to do your demand planning, as this information will be vital in understanding how much capacity is needed.
- Don’t begin capacity planning with time tracking — Although time tracking can be helpful, it’s not strictly necessary for a capacity plan. Clock-watching only serves to show what an employee has done with their time and does not imply capacity.
So, that’s everything you need to know about a capacity plan and how to implement it into your business. However, what’s the best software for helping you make these capacity forecasts?
The ultimate platform for manufacturing capacity planning
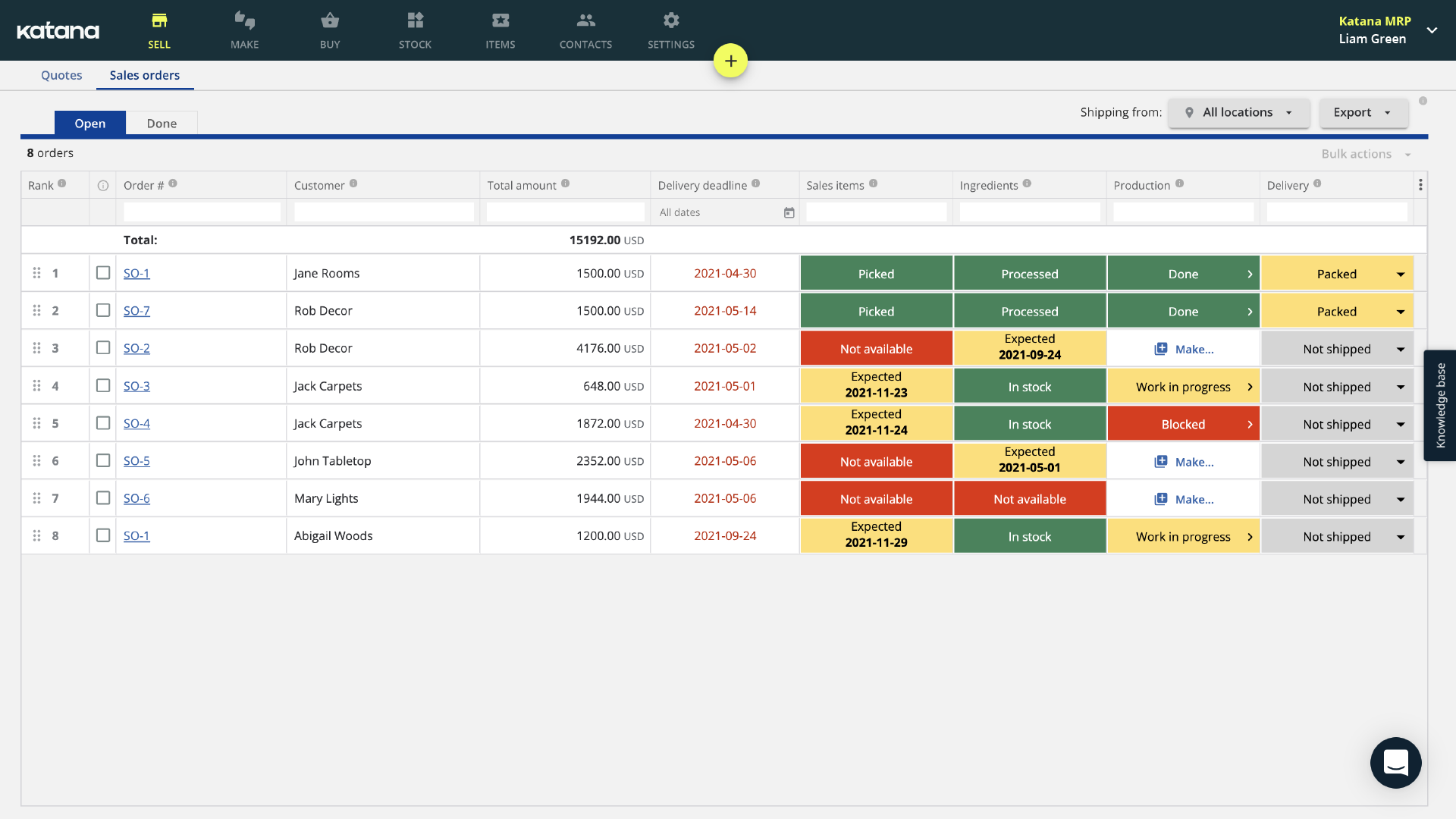
Katana is an easy-to-use manufacturing ERP that equips you with everything needed to help you perform your capacity plan, along with:
- Inventory management
- Production management
- Purchase and sales orders
- Integrations to manage your entire business
Unify all your business tools
Katana integrates seamlessly with your favorite platforms, including QuickBooks Online, Shopify, WooCommerce, Xero, and BigCommerce. By syncing your software with Katana, you can simply manage everything from a central intuitive platform.
In addition, with its robust features, Katana’s intuitive platform makes it easy to:
- Prioritize manufacturing orders
- Manage tasks for employees and receive updates in real time
- Track time to understand capacity limits
- View sales performance
- And much more
To see all the possibilities Katana provides, request a demo today. Give it a go and see for yourself why thousands of makers choose Katana to manage their day manufacturing operations.
Table of contents
Inventory management guide
More on manufacturing
Get visibility over your sales and stock
Wave goodbye to uncertainty by using Katana Cloud Inventory for total inventory control
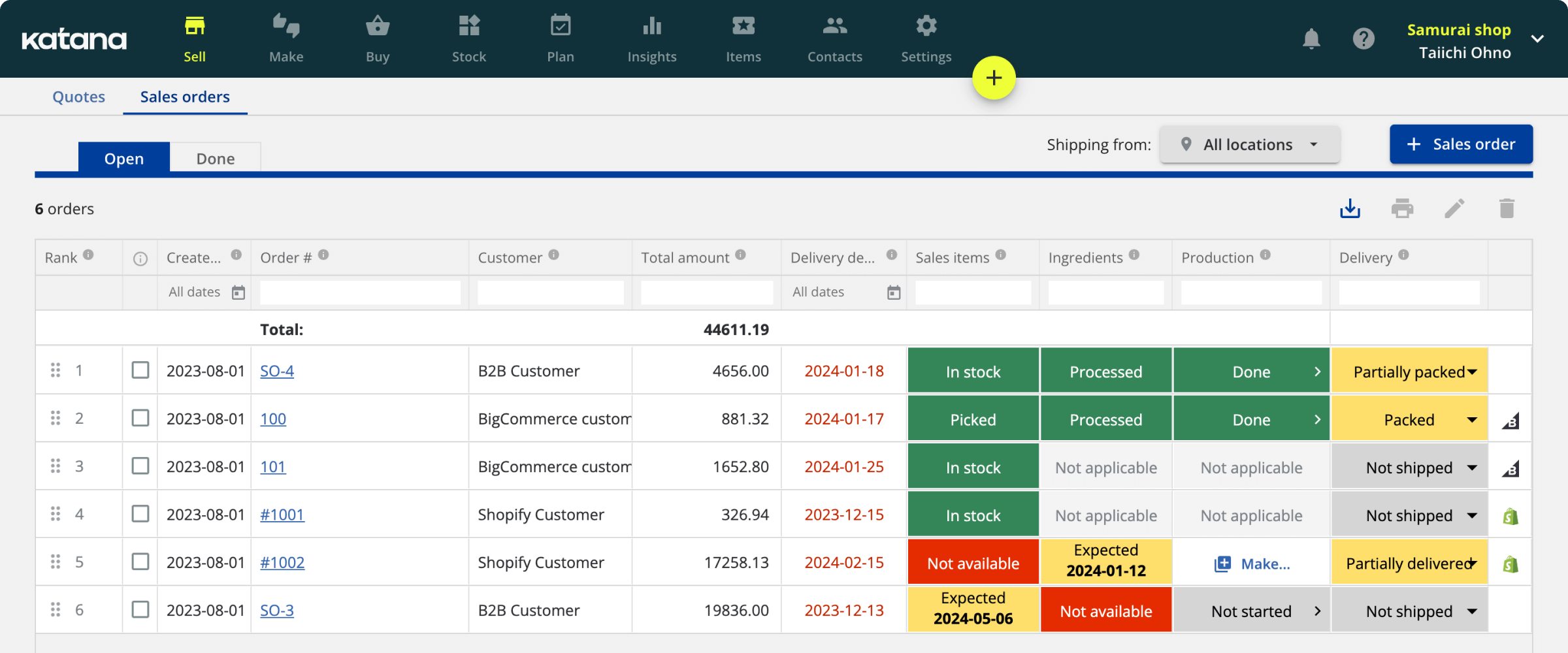