Production planning and scheduling for manufacturing
Production planning and scheduling is essential to increase your manufacturing efficiency. Adjust your production schedule based on inventory, resources, and orders. Learn how with Katana.
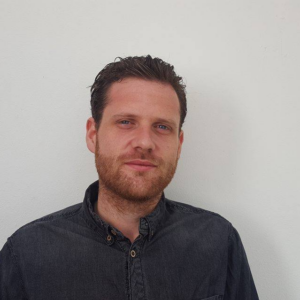
James Humphreys
Production scheduling is essential for growing manufacturing operations to take their production to the next level. If you’re looking to maximize efficiency on your shop floor, you need a way to optimize your production planning and scheduling.
Nowadays, your scaling manufacturing business has many options for finding production planning software explicitly crafted for manufacturers.
This guide will provide you with a comprehensive understanding of production planning and scheduling and how it can help you allocate your resources efficiently and cost-effectively to meet customer orders. So, read on to learn how to improve production scheduling in your scaling manufacturing business.
What is production planning?
Production planning is a process of preparing and planning for manufacturing. A production plan outlines all the steps and methods to ensure the produced goods are manufactured efficiently, on time, and within budget.
You can think of a production plan as a roadmap or strategy that you’ve developed based on the requirement planning of your business before you commit anything to production. These requirements will consider factors like managing your supply chain, raw materials, resources, factories, and warehouses.
Depending on a business’ size and scale of manufacturing, a production manager is responsible for developing a production plan by working closely with shop floor workers, contractors, and different departments within the business.
So, what is the primary task of production planning? Well, there are three that a manufacturer needs to achieve for flawless production planning:
- Complete efficiency when using materials, utilities, and resources
- Reduce manufacturing waste and eliminate excess materials in the purchase management process
- Efficiency utilizing workforce management, the amount of production times required for making goods, and equipment availability
As you can already imagine, your production plan will heavily depend on your manufacturing setup.
However, most manufacturers follow one of two types of planning — make-to-order or make-to-stock.
- Make-to-order — You create manufacturing orders after receiving a customer order. Your production plan will need to anticipate customer orders.
- Make-to-stock — You create manufacturing orders based on expected demand. Your production plan needs to produce a certain inventory level within a specific time period.
Developing a production plan for optimizing flow means identifying what are the most important aspects of your business, for example:
- Supply chain management
- Material requirements planning
- Manufacturing lead time
- Resource capacity planning
Production planning allows managers to create an efficient production process to meet customer and organizational needs.
A great production plan will empower manufacturers to get total control over their production processes. It provides knowledge on what and how long is needed to finish a production run, which allows manufacturers to:
- Better manage their time
- Avoid bottlenecks
- Manage staff
- Create a seamless process flow in manufacturing
Without a proper production plan in place, it’s easy to lose control of your resources and manufacturing — leading to delays, shortages, and increased product costs.
5 types of production planning
Make-to-order and make-to-stock are workflows that will impact how you develop your production plan. Your plan will also be affected by your manufacturing processes. Here are the five main methods of production you can introduce into your business:
1. Job method
The job method, or job shop manufacturing, is often used when manufacturing a single product where custom material processing requirements are needed. For bespoke manufacturing or any production where customization is offered, your production plan will change from product to product. This method is mostly utilized by SMB manufacturers, but larger companies can use it too.
2. Batch production method
The batch production method, or batch manufacturing, produces finished goods in bulk instead of individually or through continuous production. This production process allows manufacturers to closely watch each stage of production to make quick corrections and monitor efficiency. This method is great for food production or for manufacturers who produce items on a large scale.
3. Flow method
The flow method, or discrete manufacturing, is a demand-based manufacturing plan where materials flow from one machine to the next until they become finished goods with little human interaction. This approach to manufacturing requires a standardized workflow and increased quality control to ensure the continuously produced items aren’t defective. This method is great for manufacturers who need to produce a uniform set of items one by one.
4. Process method
Process method, or repetitive manufacturing, is the stereotypical idea people have of manufacturing — assembly lines. This production plan will create finished goods by passing through different machines and processes. Great for manufacturers who need to make a lot of similar products.
5. Mass production method
The mass production method, or continuous manufacturing, is more or less the same approach as the flow method, but on an even larger scale. Manufacturers use this method if uniformity is critical, and they use a standardized process to guarantee that products all look the same. Using the mass production method allows manufacturers to produce many products in a short amount of time.
What is production scheduling?
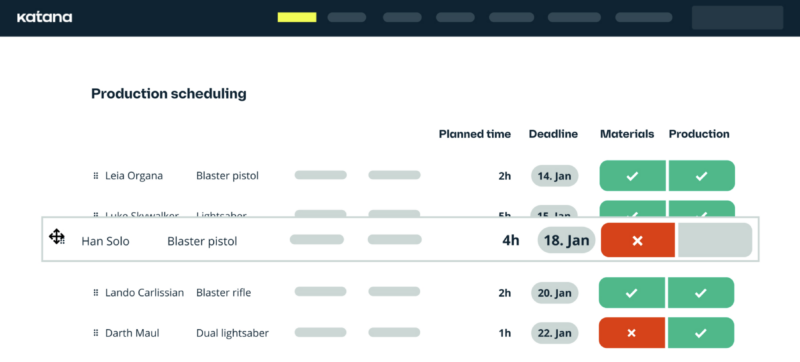
Production scheduling is a vital process that entails the creation of a comprehensive and detailed timetable outlining the specific order and timing of production activities. It involves making critical decisions on when each task or operation should commence and conclude, taking into account resource availability, constraints, and dependencies.
By considering factors such as machine availability, labor capacity, and material availability, production scheduling aims to optimize efficiency and streamline workflow.
This process ensures that production tasks are executed in a coordinated manner, minimizing idle time, maximizing resource utilization, and ultimately facilitating the timely delivery of products.
Effective manufacturing scheduling plays a pivotal role in enhancing productivity, reducing costs, and maintaining a smooth and well-organized production process.
The primary objectives of production scheduling include:
- Sequencing the order of production tasks
- Assigning resources (equipment, labor, etc.) to specific tasks
- Minimizing idle time and maximizing resource utilization
- Adapting to changes in customer demand or unforeseen disruptions
- Ensuring timely delivery of products
What’s the difference between planning and scheduling?
Production planning focuses on the big picture and long-term decisions to ensure that production activities align with the overall business strategy and customer demand. On the other hand, production scheduling focuses on short-term decisions that aim to optimize efficiency, minimize costs, and maintain a smooth workflow within the production process.
Both planning and scheduling are essential for effective production management and meeting customer demands efficiently.
The importance of production planning and scheduling
Production planning and scheduling are crucial aspects of business operations and have significant importance for several reasons:
- Meeting customer demands — Effective manufacturing planning and scheduling ensure timely delivery of products in the required quantities, avoiding stockouts, minimizing lead times, and enhancing customer satisfaction.
- Optimal resource utilization — Proper planning and scheduling enable businesses to allocate resources efficiently, minimizing idle time, reducing costs, and maximizing productivity. This increases operational efficiency and improves resource utilization.
- Cost control — Accurate demand forecasting and efficient scheduling help avoid overproduction, minimize inventory holding costs, reduce setup times, eliminate bottlenecks, and optimize resource use, contributing to cost savings.
- Improved production efficiency — Effective planning streamlines production processes, eliminates inefficiencies, and reduces waste, optimizing production flow, reducing cycle times, and increasing overall efficiency.
- Timely decision-making — Well-defined plans facilitate informed decisions on resource allocation, production priorities, and capacity management, enabling adaptation to changes and ensuring timely production.
- Coordination and collaboration — Manufacturing planning and scheduling involve cooperation between departments, enhancing communication, improving coordination, and achieving a synchronized production process, reducing delays and enhancing operational efficiency.
- Scalability and growth — Well-designed production plans and schedules lay the foundation for handling increased demand, expanding operations, and adapting to market conditions. This helps the business scale and capitalize on growth opportunities.
- Continuous improvement — Monitoring production performance, analyzing data, and evaluating schedules help identify areas for improvement, drive continuous optimization, and maintain a competitive edge.
So, if you want to ensure timely delivery, optimal resource utilization, cost control, improved efficiency, and scalability, you need to have a solid production plan.
5 stages of production planning and scheduling
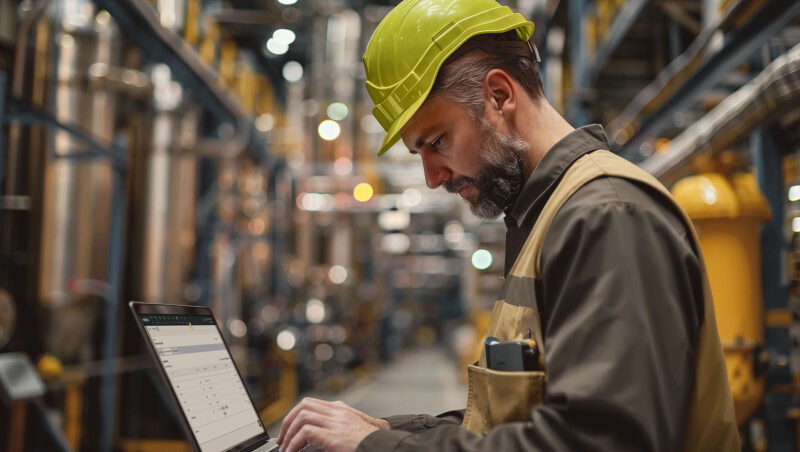
Production planning and scheduling involve a systematic approach to ensure efficient and timely production of goods. The best way to achieve this is by dividing the process into five distinct stages, each serving a specific purpose.
These stages provide a structured framework for organizations to plan, schedule, and control their production processes effectively. Let’s explore each stage in detail.
1. Demand forecasting and capacity planning
The first production planning and scheduling stage involves demand forecasting and capacity planning.
Demand forecasting entails estimating future customer demand based on historical data, market trends, and other relevant factors. It helps organizations determine the expected demand volume and patterns for their products.
To forecast demand, you need to incorporate a variety of data, including:
- Historical sales performance
- Local and national taxes and regulations
- Current manufacturing trends and predictions
- Technological advancements
Learning and understanding your product demand will help you make the best choices when arranging and improving your operations.
You can also use production control software like Katana to forecast demand. Here’s what it would look like.
Once the demand is forecasted, capacity planning comes into play.
It involves evaluating the production capacity and capabilities of the organization to determine if it can meet the projected demand. Factors such as workforce availability, equipment capacity, and facility constraints are taken into account during this stage.
The goal is to align the production capacity with the anticipated demand to avoid underutilization or overburdening of resources.
2. Material planning and procurement
The second stage focuses on inventory control, including material planning and procurement. In this stage, organizations identify the raw materials, components, and resources required for production. The quantities needed are determined based on the manufacturing schedule and demand forecast.
Efficient material planning ensures the timely availability of materials while minimizing inventory costs and the risk of shortages or excess stock.
Establishing strong supplier relationships is essential during this stage to ensure a reliable supply chain. Organizations collaborate with suppliers to coordinate delivery schedules, negotiate pricing, and maintain consistent quality standards.
Effective material planning and procurement help optimize production flow and prevent disruptions in the supply chain.
3. Scheduling and resource allocation
The third stage involves detailed scheduling and resource allocation. It focuses on creating a comprehensive production timeline and sequence of activities to ensure smooth operations.
Scheduling involves assigning tasks to different workstations or production lines, considering factors such as equipment availability, setup times, and dependencies between jobs.
Resource allocation is another crucial aspect of this stage. It entails determining the optimal allocation of labor, equipment, and other resources to specific production tasks. Balancing workloads, considering skill levels, and maximizing resource utilization are key considerations during resource allocation.
The goal is to create an efficient schedule that minimizes idle time, bottlenecks, and unnecessary delays.
4. Production control and monitoring
The fourth stage revolves around production control and monitoring. Once production is underway, it is essential to track work progress, ensure adherence to the planned schedule, and maintain quality standards. Production control is all about monitoring the production process, identifying deviations or bottlenecks, and taking corrective actions as necessary.
Efficient production control relies on real-time data collection, performance measurement, and analysis. It enables organizations to identify issues, make adjustments, and optimize the production flow. This stage also includes quality control measures to ensure the final output meets the required standards and customer expectations.
5. Master production schedules
Once your manufacturing plan looks achievable, you can progress to the next step, producing a master production schedule, the ultimate document for production.
Your master production schedule (MPS) will detail how many items need to be produced within a certain period. Most businesses use manufacturing software to create an MPS that will provide real-time data and allow them to make production changes on the fly.
Effectively controlling and monitoring the production process allows organizations to improve productivity, minimize waste, and ensure timely delivery of products to customers.
Download a production schedule template
Download this free production schedule template for Excel to create an efficient and accurate production plan for your business.
A simple production plan example
For the sake of this example, we’ll keep this enterprise fairly modest. Imagine a small workshop with five artisans making psychedelic T-shirts.
Each artisan works 8 hours a day, from Monday to Friday. They follow a make-to-stock workflow in a job shop setting. It takes 2 hours to produce a single T-shirt.
The maximum capacity of this Funkadelic business is 200 hours.
In this scenario, the annual hippie fest is fast approaching — and looking at your historical data collection — the T-shirt makers expect to see a surge in sales. Last year they were overwhelmed, so this year, they have decided to put together a quick manufacturing plan a week before they expect an increase in demand. They also want to have a safety stock level of 10 for each of their items.
As per their initial plan, they won’t be able to meet production requirements, but they can now use this knowledge to readjust their current production plan. They decide to limit the production of Far Out T-shirts to 40 and Peace T-shirts to 8.
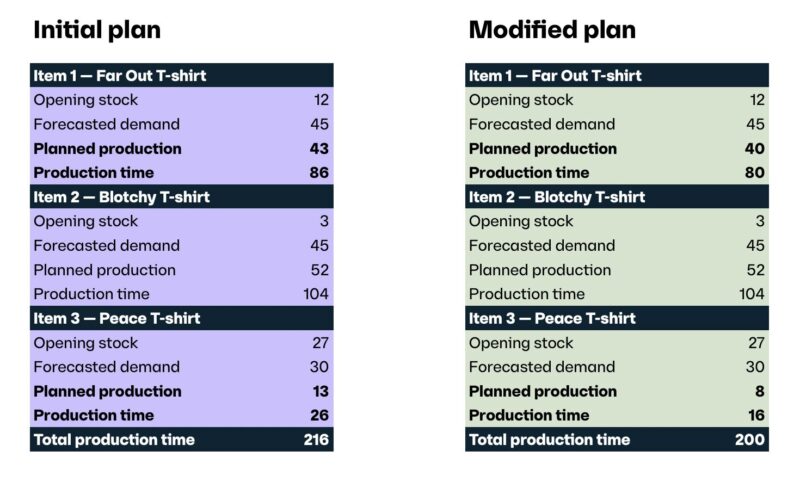
They can still meet the forecasted demand with the modified plan by sacrificing some of the safety stock.
However, this plan puts their operations and resources at 100% capacity. If one of the artisans calls in sick on Wednesday evening, the max capacity for the week falls to 176 hours. When planning production, a rule of thumb is to have 20% free to give yourself wiggle room if a problem occurs.
The key factors to consider when scheduling production
Production planning is vital for any manufacturing business. Even basic products need a clear and defined flow to turn them from raw materials into quality goods. If you don’t follow this flow or your production quality control checklist, your products will surely drop in quality. Without a proper process, your standardized practices will be forgotten.
So, when scheduling the production, what are the key factors to consider?
Crew management
Use your team well.
Your people are a valuable asset to your business. They play a key part in manufacturing process optimization. Make it your business to know your people, including their strengths and weaknesses. This way, you can assign each team member to the most suitable tasks and machines.
If someone is sick or goes on holiday, you have the additional capacity to make up for the temporary loss.
Effective production planning allows you to get the most out of your people and machines. Every team member knows the tasks assigned to them and what their expected output is. Keeping tabs on this process lets you compensate for shortfalls and keep up with high demand.
Running at capacity
Is your workshop constantly running at 100%?
It only takes a minor bump to bring things to a grinding halt. Capacity planning helps to make sure you’re not running at max capacity. If you do receive an unusually large order or two, you will be glad you prepared.
The same goes for your team, as they have enough resources to do their job on time.
Raw materials
Frequent stalls in production planning mean paying team members and machines to stand by.
Integrating a robust MRP or manufacturing ERP software into your business can help ensure you always have the required raw materials available. This means:
- You never have to push back production because of supply order delays or stockouts
- Priority deadlines do not have to be set back due to undersupply
- There’s no need to constantly step over excess raw materials on your shop floor
If done right, warehousing and transport costs won’t skyrocket due to oversupply. As a bonus, every team member always has something to do as they work with your available materials.
Workshop logistics
The logistical flow of each part of your manufacturing process also requires consideration. This may not seem so important, but you would be surprised. Many production lines have come grinding to a halt as one weak link has been placed on the wrong stage.
Pushing machines and people to unsuitable locations can harm efficiency.
Sometimes, what seems like common sense could be harmful to your flow. It takes careful analysis to determine how materials, resources, people, and supplies travel around your shop floor.
It may be that a more efficient layout or order exists for your business. Sometimes a small change can make a world of difference to your production schedule.
Problem-solving
Trial-and-error problem-solving costs your business money through each failed attempt.
Overordering or overproducing is a band-aid solution, as this leads to extra costs or staff burnout. You need effective production tracking software to track your flow and find manufacturing scheduling issues to get to the root of a problem.
Know your manufacturing processes
Understanding manufacturing planning and scheduling allows you to oversee your manufacturing methodically to overcome production issues easily.
Track and manage everything effectively, and it will run like clockwork. Effective manufacturing scheduling makes it easier to do it all by the book — it is set out clearly for your whole team and is available 24/7.
Production planning KPIs
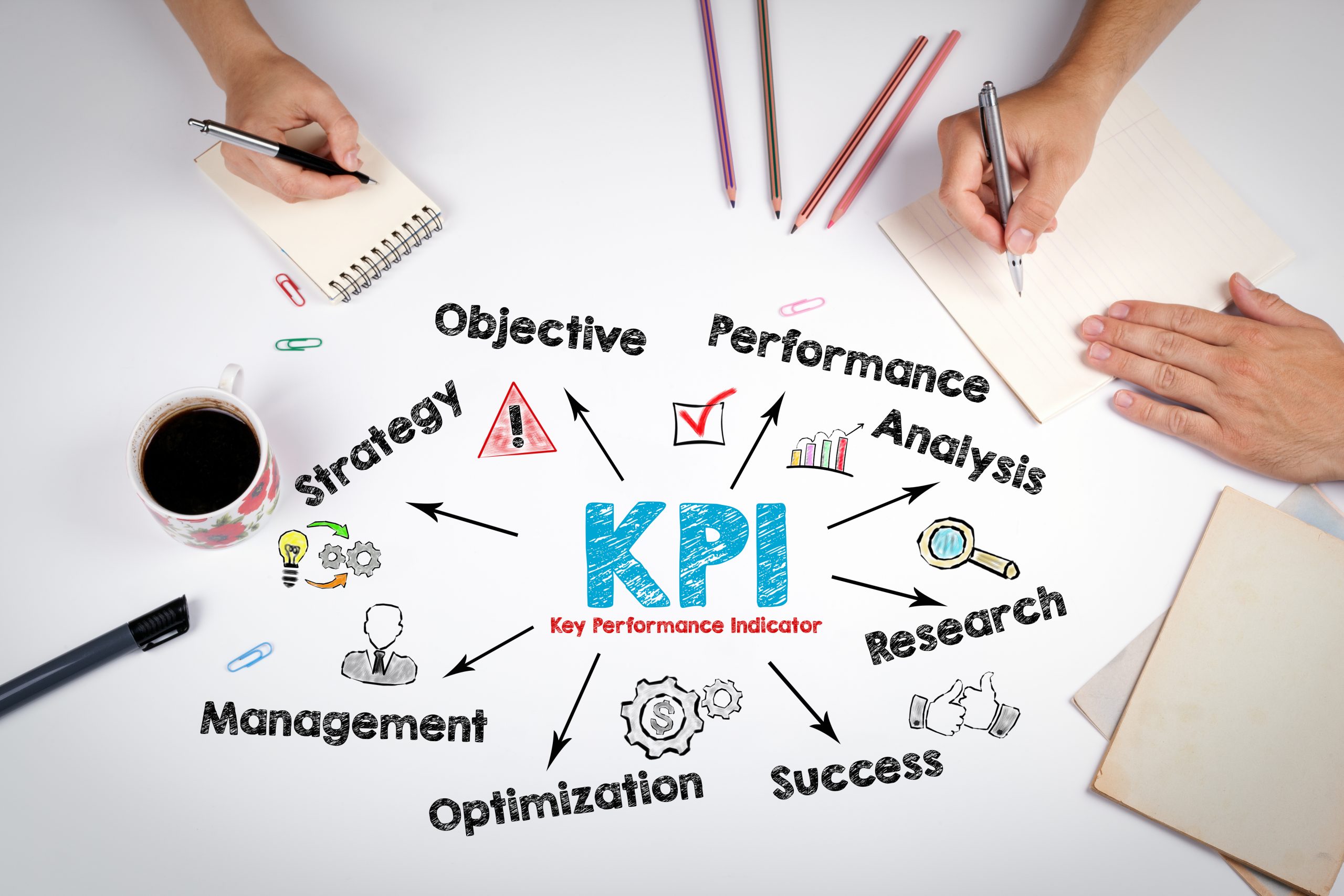
Now you know everything there is to know about putting together your production plan — the next step is understanding how to measure its effectiveness. Here are some production planning KPIs to track to get you started:
- Manufacturing costs — Track how much it costs to produce an item by looking into raw materials, utilities, salaries, rent, etc.
- Capacity utilization rate — You don’t want resources running at max capacity, but you also don’t want machinery or workstations sitting idle.
- Planned production vs. actual hours — This will help you better understand how long it takes to produce an item or uncover any issues that lead to delays on your shop floor.
- Employee utilization (productivity) — The same as your capacity rate. The only difference is that you don’t want to overwork them. Make sure you schedule your human resources reasonably to void burnout.
- Takt time — A lean manufacturing concept that looks into the actual time it takes to produce a single unit of item.
This checklist will guide you in creating your business analytics to observe your production and develop plans to make them even more efficient.
But, as you can tell, doing this is a long and arduous process, and many scaling manufacturers turn to automation to help them with this task.
How to optimize production scheduling
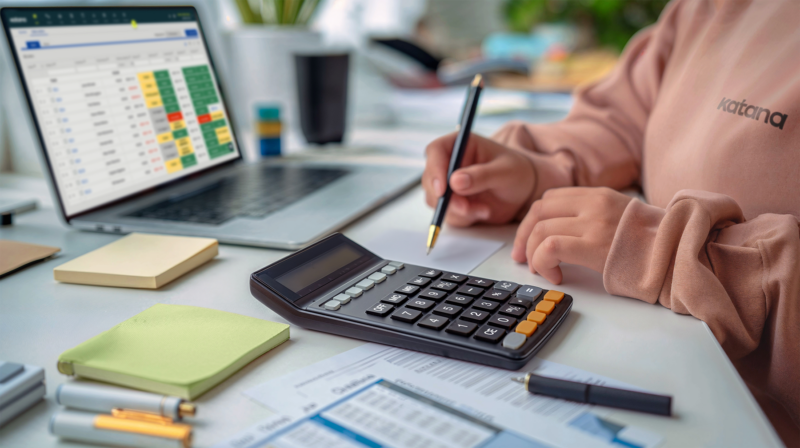
Optimizing production scheduling involves maximizing efficiency, minimizing costs, and ensuring timely delivery of products. Below you’ll find some strategies for optimizing manufacturing scheduling.
Demand-driven scheduling
Incorporate demand-driven scheduling by aligning manufacturing schedules with customer demand. Use accurate demand forecasting to determine the required production volume and adjust schedules accordingly. This approach helps avoid overproduction or underproduction and reduces excess inventory or stockouts.
Utilize advanced scheduling techniques
Employ advanced scheduling techniques such as finite capacity scheduling, just-in-time (JIT) scheduling, or theory of constraints (TOC) to optimize production schedules. These techniques consider capacity constraints, setup times, and dependencies between tasks to create efficient and realistic schedules.
Minimize changeovers and setup times
Reduce changeover and setup times by implementing strategies like single-minute exchange of die (SMED). Streamlining changeover processes allows faster transitions between different product configurations, enabling shorter production runs and increased flexibility.
Implement real-time monitoring
Utilize real-time monitoring systems and production control tools to track progress, identify bottlenecks, and make data-driven decisions. Real-time data provides insights into the actual status of production, enabling prompt adjustments and proactive problem-solving.
Optimize resource allocation
Ensure optimal utilization of resources by assigning tasks based on skill levels, availability, and efficiency. Consider the capabilities and capacities of equipment, machinery, and workforce while allocating resources. Efficient resource allocation minimizes idle time, reduces bottlenecks, and improves overall productivity.
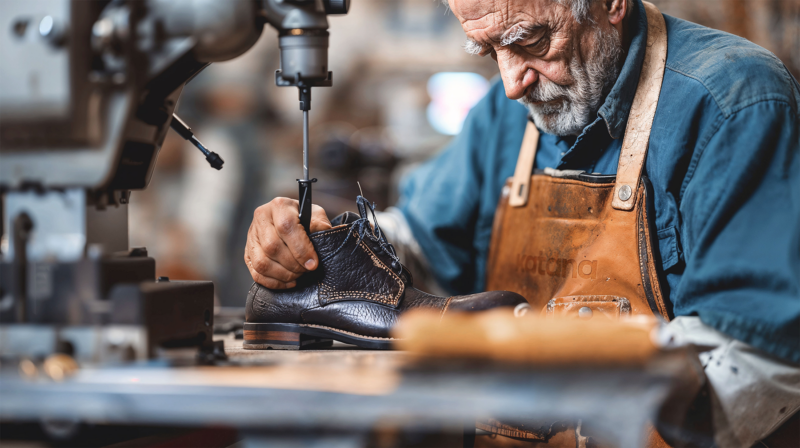
Prioritize critical tasks
Identify critical tasks or processes that significantly impact the overall production timeline. Prioritize these and allocate resources accordingly to ensure timely completion. Focusing on critical tasks minimizes the risk of delays in the entire production process.
Consider production constraints
Take into account any constraints that may affect production scheduling, such as limited capacity, equipment maintenance schedules, or supplier lead times. By incorporating these constraints into the scheduling process, you can avoid scheduling conflicts and optimize production flow.
Implement lean manufacturing principles
Apply lean manufacturing principles such as just-in-time production, continuous flow, and waste reduction techniques to optimize production scheduling. Eliminate non-value-added activities, reduce inventory, and optimize process flows to improve overall efficiency.
Embrace technology
Utilize production scheduling software or manufacturing execution systems (MES) with advanced planning and scheduling capabilities. These tools automate the scheduling process, optimize resource allocation, and provide real-time visibility into production activities, enabling better decision-making and scheduling optimization.
Continuous improvement
Foster a culture of continuous improvement by regularly reviewing and analyzing production schedules, performance metrics, and feedback. Identify areas for improvement, implement changes, and monitor the impact of these adjustments. Continuously striving for optimization ensures ongoing efficiency gains in production scheduling.
These strategies help organizations optimize their production scheduling processes, enhance operational efficiency, minimize costs, and deliver products on time. All that, ultimately, improves customer satisfaction and competitiveness.
Production planning and scheduling mistakes
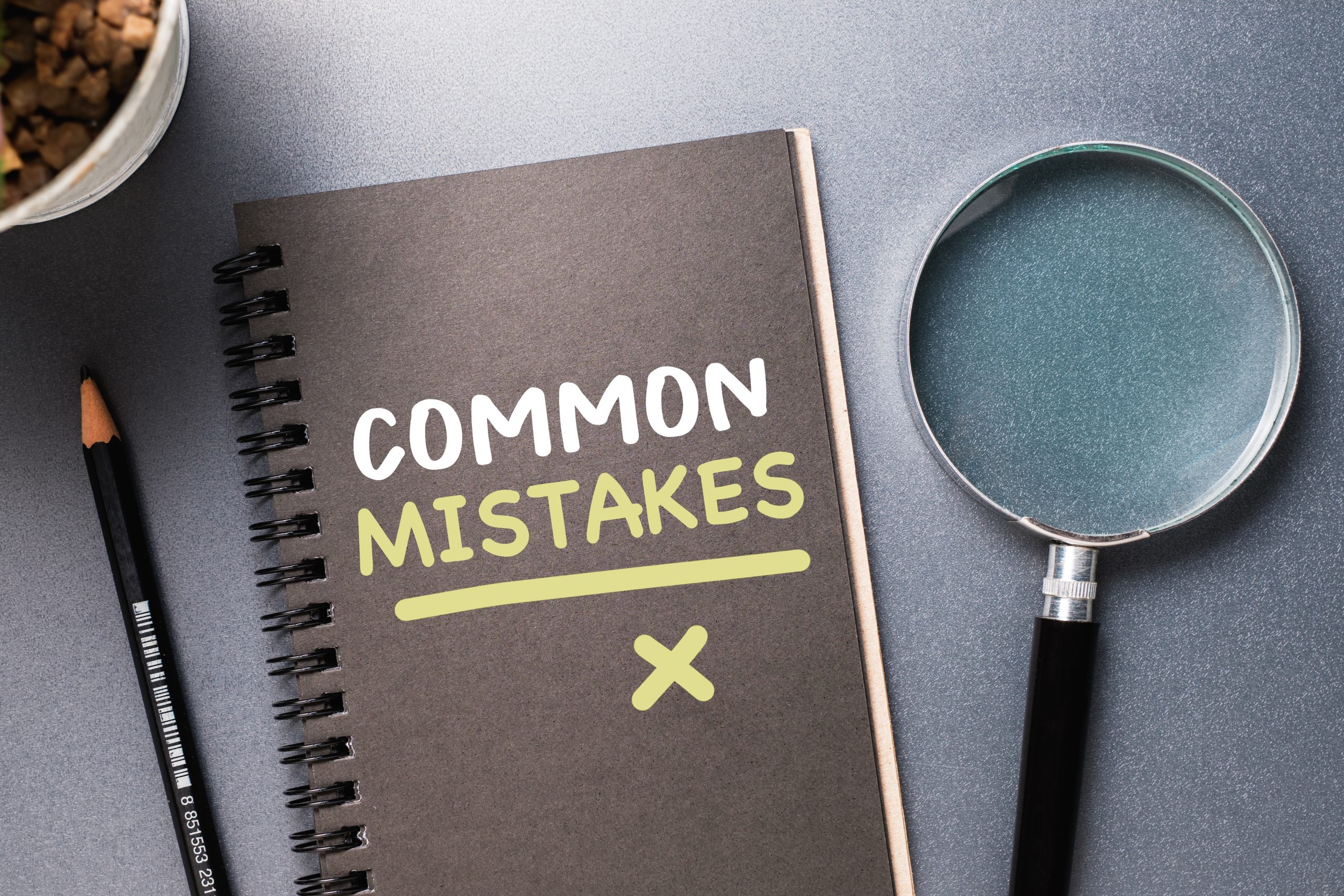
Production planning and scheduling mistakes can lead to inefficiencies, delays, increased costs, and customer dissatisfaction. Let’s review some common mistakes to prepare for when dealing doing manufacturing planning and scheduling.
Inaccurate demand forecasting
Failing to accurately forecast customer demand can result in overproduction or underproduction. Overproduction leads to excess inventory and increased carrying costs, while underproduction can result in stockouts and missed sales opportunities. It is important to gather and analyze relevant data, consider market trends, and collaborate with sales and marketing teams to improve demand forecasting accuracy.
Insufficient capacity planning
Inadequate evaluation of production capacity can lead to resource constraints and bottlenecks. If the production capacity does not align with the forecasted demand, it can result in missed deadlines, backlogs, and delays in fulfilling customer orders. Conducting regular capacity assessments and considering factors such as equipment maintenance, workforce availability, and facility constraints are essential for effective manufacturing capacity planning.
Poor material planning
Inaccurate material planning can cause disruptions in the production process. Insufficient stock of raw materials or components can halt production, while excessive inventory ties up capital and increases storage costs. Utilizing efficient inventory management systems, establishing reliable supplier relationships, and continuously monitoring material requirements are crucial to avoid material planning errors.
CT LAB improves daily operations efficiency by 30% with Katana
“Katana integrates everything, making for effective company-wide resource planning and control.” — Danielle Louw, Production Manager at CT LAB
Inefficient scheduling
Inefficient scheduling can lead to production issues, increased setup times, and idle resources. Poor task sequencing, inadequate consideration of setup times, and neglecting resource availability can result in unnecessary delays and production bottlenecks. Utilizing advanced scheduling techniques, considering the dependencies between tasks, and optimizing resource allocation is vital for efficient scheduling.
Lack of flexibility
Failure to incorporate flexibility in manufacturing planning and scheduling can make it challenging to adapt to unforeseen events or changes in demand. Market fluctuations, machine breakdowns, and supplier delays can disrupt the planned schedule. It is important to build contingency plans, have backup suppliers, and maintain buffer capacity to accommodate unexpected disruptions and maintain operational continuity.
Ignoring feedback and continuous improvement
Neglecting to gather feedback from the production floor, customer feedback, and performance metrics can hinder process improvement.
Regularly reviewing production performance, analyzing data, and actively seeking feedback from relevant stakeholders can help identify areas for improvement and drive continuous optimization in production planning and scheduling.
Lack of communication and collaboration
Poor communication and collaboration among departments can lead to misalignment and delays. Production planning and scheduling require coordination among different teams, including sales, operations, procurement, and logistics.
Clear communication channels, regular cross-functional meetings, and shared visibility of information are essential for effective collaboration and synchronization of activities.
Being aware of these common production planning and scheduling mistakes helps you to prepare for them by adopting best practices. This helps companies enhance their operational efficiency, minimize costs, and improve customer satisfaction by consistently delivering products on time.
Can you use Excel for production planning?
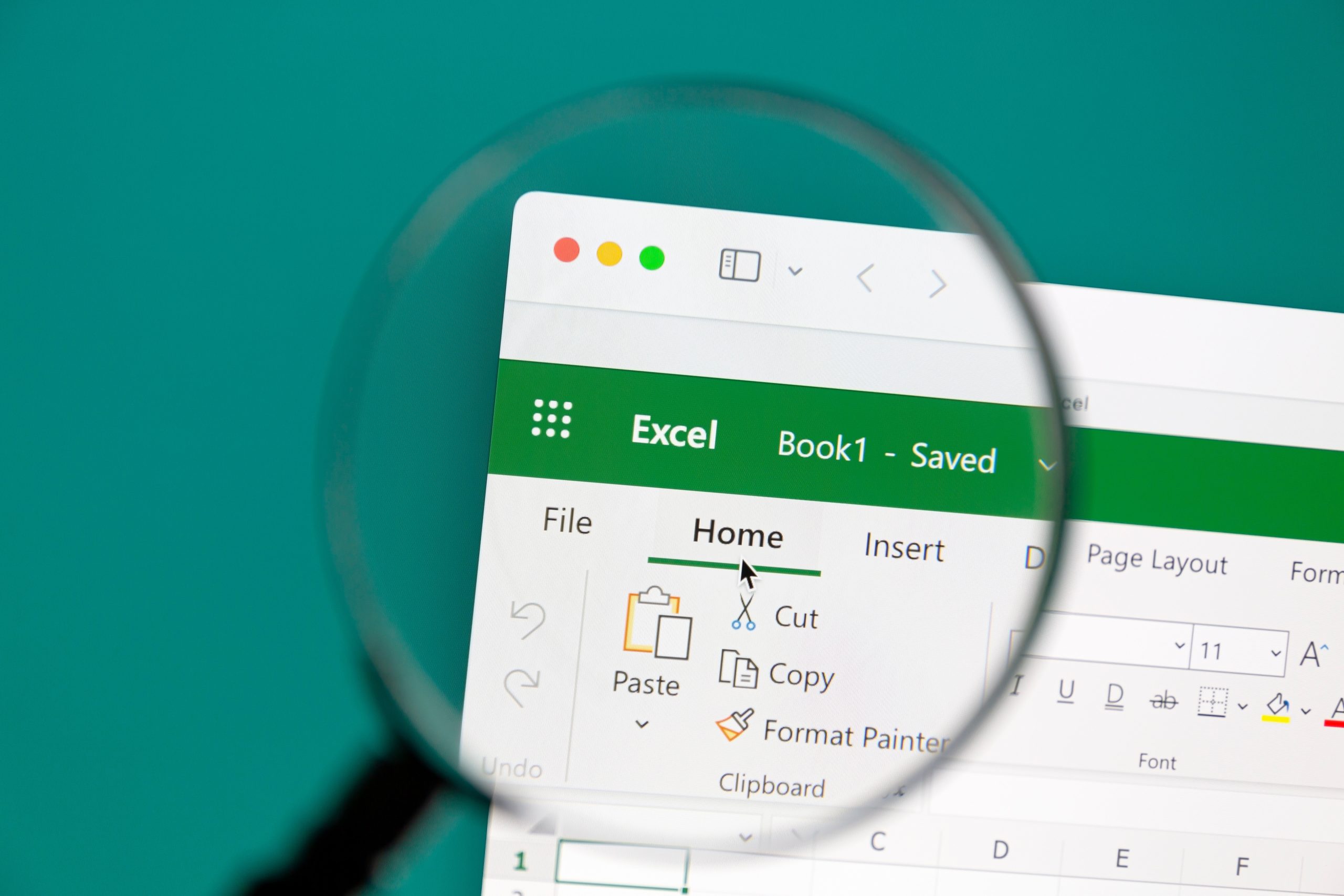
The absence of affordable production planning software has led to many manufacturers using inefficient spreadsheets.
There are three main problems with this approach:
- A lot of manual work — It may be better than doing it with a pen and paper, but Excel is still too labor-intensive.
- Error-prone — They are vulnerable to mistakes that cause confusion, production delays, and business-disrupting problems.
- Static — They do not update automatically. This can lead to delays as changes are not communicated.
Many modern manufacturers are stuck with Excel because they can’t see better options. This is understandable. Most manufacturers do not need the gargantuan flow diagrams and Gantt charts seen in large enterprise software. Shop-bought software like Excel seems like a quick and easy option.
However, it is not powerful enough to use production management effectively. So, what’s the solution?
Production planning and scheduling with Katana
The best way to avoid production planning mistakes and implement different optimization techniques is through software. Katana is a cloud inventory platform that allows you to do all that and more. It offers advanced features with an intuitive interface, so you don’t need a 3-month boot camp to start using it.
Katana takes the heavy lifting off your back and turns tedious paperwork into an easily automated task. Let’s take a look at some of the features Katana offers.
1. Real-time inventory
Track your products and monitor stock movement in real time. To manage your inventory in Katana, open the Stock screen and see the current balance of selected items in the In Stock column.

Based on your actions on the Stock page, Katana makes relevant changes to the inventory count. No more spreadsheets and paperwork — automatic updates will be your new best friend.
2. Reorder points
Create indications to keep stable stock levels and prepare for spikes in demand and supply shortage.
Navigate to the Stock page and see the Reorder point tab.
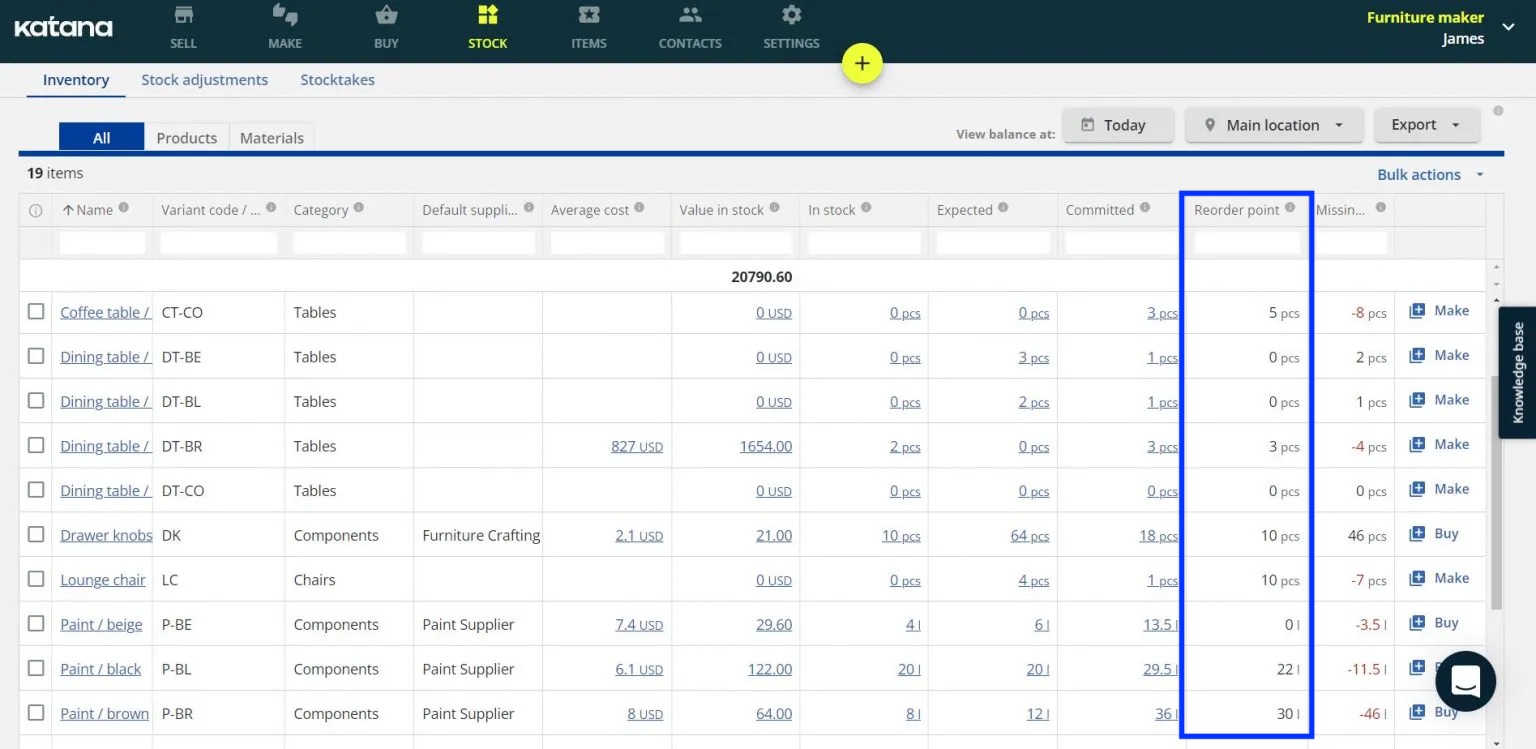
In the MTO business model, the reorder point can be set to zero as production is started after the customer’s request. However, you can set reorder points for your ingredients to make sure you’re ready to begin manufacturing when an order comes in.
In the MTS business model, it’s easier to manage stock levels by setting reorder points to avoid running out of supplies and products.
3. Delivery tracking
Pack and ship your items individually or in bulk. Stock levels will be automatically renewed based on the status of the order.
You can also prioritize orders that you know will have longer delivery times or that need to be delivered faster. It’s a great way to improve your order fulfillment cycle time, and your customers will appreciate the short wait.
If you go to the Sell screen, Sales order tab, and open any sales order, you’ll be able to change the shipping status.

The status can also be changed on the main Sell page under the Sales order tab if you edit it directly in the last column.
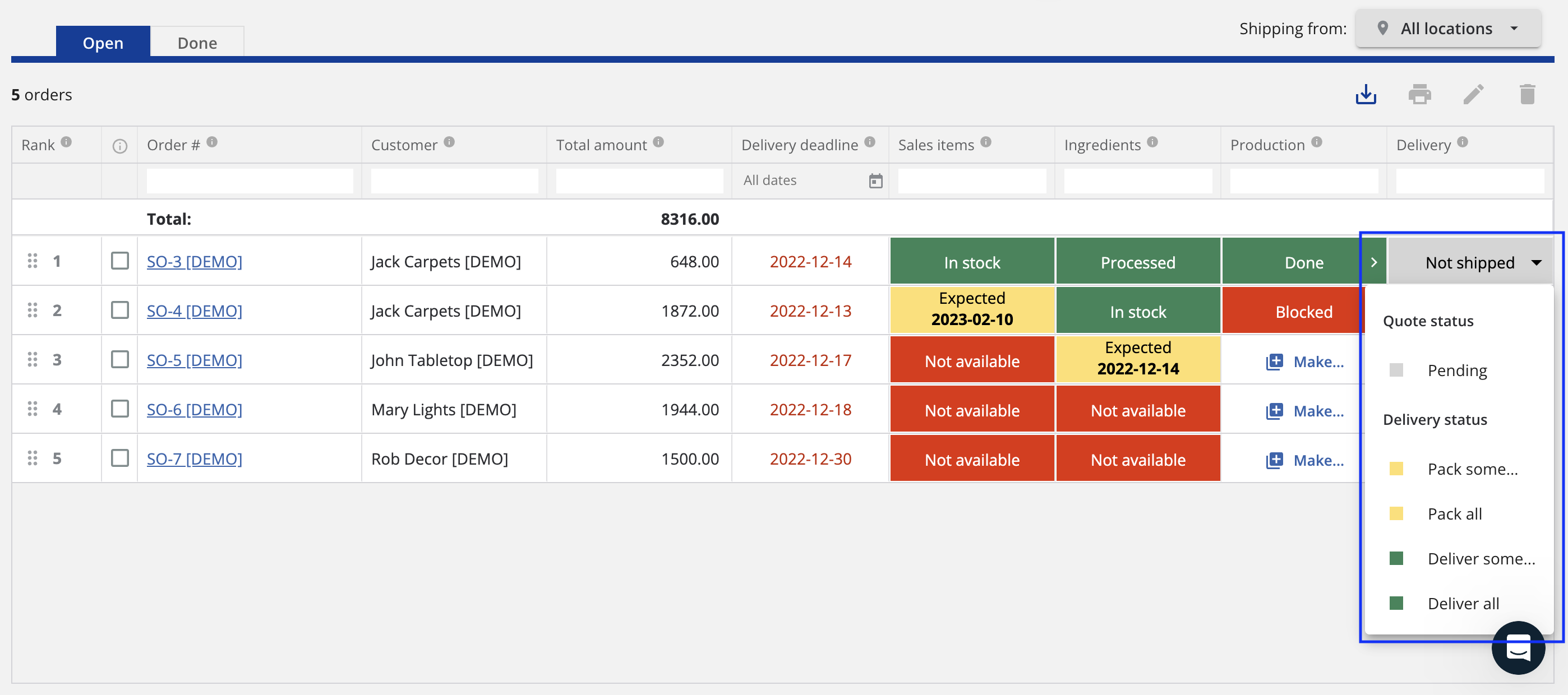
4. Production schedule
Scheduling allows you to prioritize the manufacturing of your most popular products and manage time more efficiently.
You can access scheduling on the Make page in the Schedule tab.
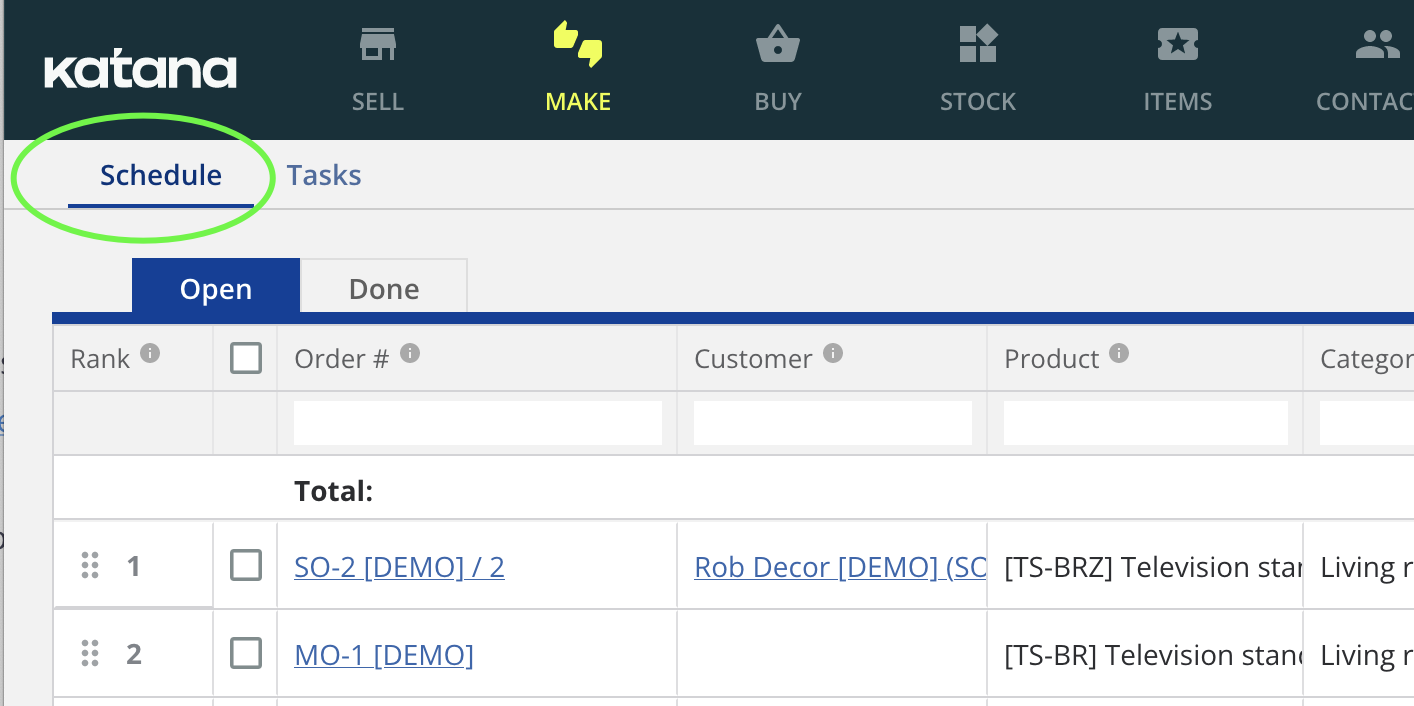
5. Task assignment
Besides schedules, Katana also offers the ability to create tasks and assign them to your shop-level workers (operators). By completing tasks, operators can automatically change the manufacturing status and streamline production without time-consuming paperwork.
Operators can view their assigned tasks in the Shop Floor App, which can be accessed with all smart devices.
Tasks are accessible on the Make page under the Tasks tab. In this view, you can create tasks, change their status, and assign them to your operators.
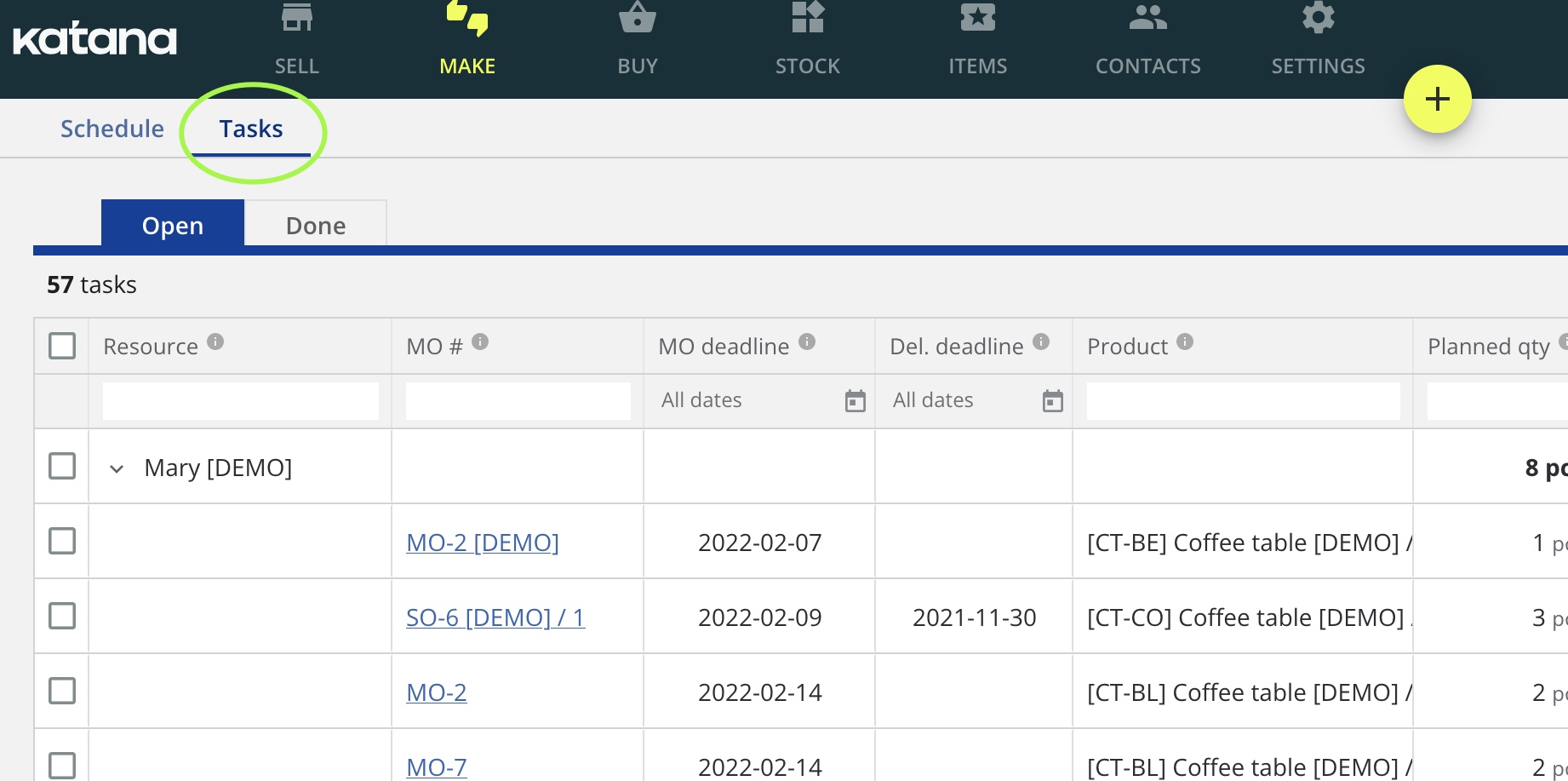
6. Integrations with other helpful tools
Katana has native integrations that can be extremely useful tools for your process of production planning. You can plan out every step of the product lifecycle using integrations such as:
- Accounting tools for keeping your bookkeeping in order: QuickBooks Online and Xero
- Ecommerce platforms to manage your sales: Shopify, WooCommerce, and BigCommerce
- Creating your own workflows with Katana’s open API.
And there you have it — the secrets to a seamless production plan. Now that you know how to plan production, it’s time to put all this knowledge into action and remember the wise (and slightly paraphrased) words of Benjamin Franklin:
“By failing to plan, you’re planning to fail.”
Putting the Pro into Production
Katana helps increase your productivity while eliminating inefficiencies. Request a demo today.
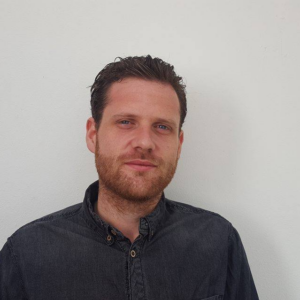
James Humphreys
Table of contents
Get inventory trends, news, and tips every month
Get visibility over your sales and stock
Wave goodbye to uncertainty by using Katana Cloud Inventory for total inventory control
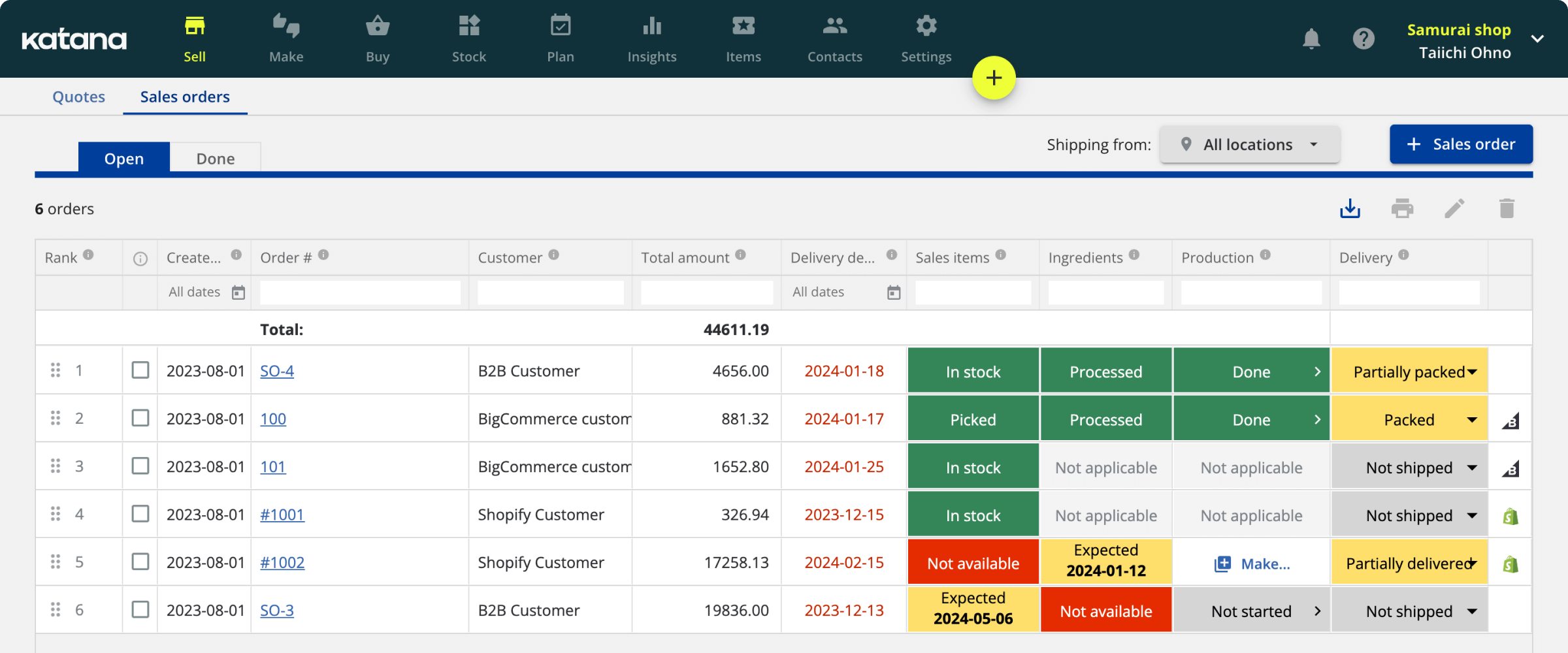