The ultimate inventory management guide
Get the ultimate guide to inventory management
A comprehensive ebook that covers everything you need to know about inventory management.
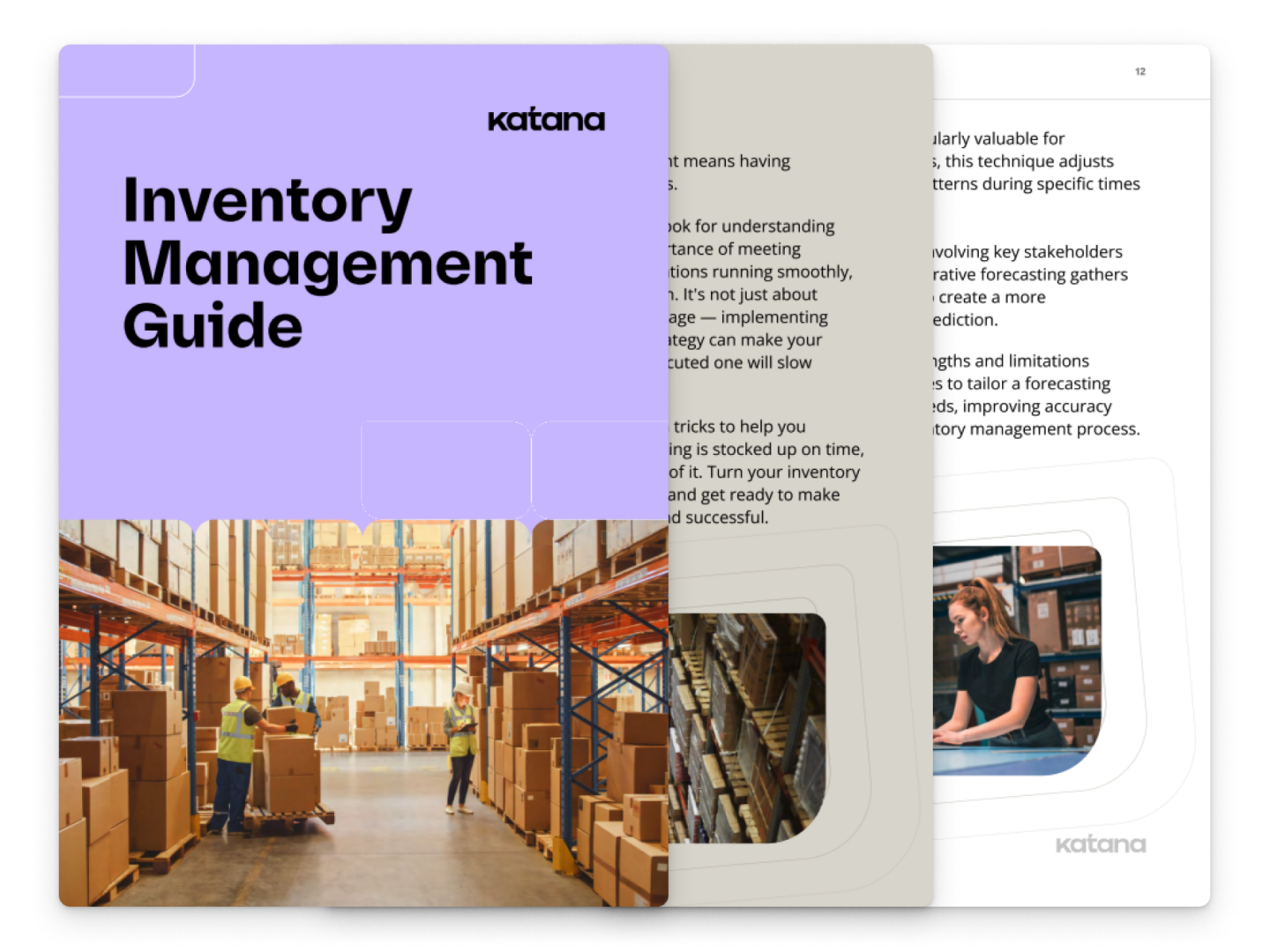
Inventory management is a central part of any business that deals with physical products. Whether you sell ice cream, lug nuts, or handmade vests for spaniels, in one way or another, you will need to manage your inventory. How well you do it will determine your success.
This article contains everything you need to know about inventory management to help you take your inventory game to the next level. If you can master and implement the advice below, you’ll put yourself ahead of the competition in no time.
What is inventory management?
Inventory management is the process of keeping track of all the goods your company has in stock. It’s the science and art of ordering, storing, and using a company’s inventory — the materials, components, and products a business sells or uses to make its finished goods.
Inventory management includes the systems and processes companies use to track their inventory and determine when and how much they need to order to meet customer demand while keeping handling and storage costs minimal.
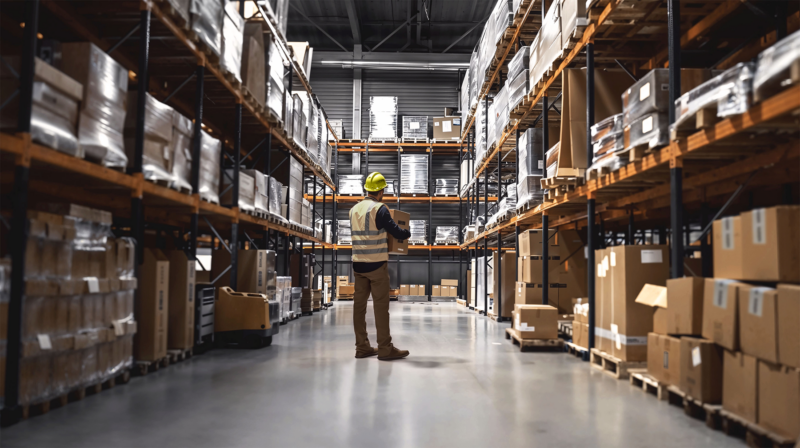
What counts as inventory?
There are many definitions of inventory out there. Some offer an interpretation that refers to inventory as the sum of all items used in your business. This includes anything related to the operations of your business, such as safety or office equipment.
We believe it’s more helpful to think of inventory as the sum of all items used in your business intended for sale.
That means looking at all the bits that go into getting your products made. Regarding materials directly related to your production process, it includes items ready to be sold and items you intend to sell in the future. You could break down the types of inventory into the following:
- Raw materials — Components that can be used to create products
- Work-in-process (WIP) — Items in the process of becoming finished products
- Finished goods — Products that are completed and ready to be sold
- MRO inventory (MRO) — Maintenance, repair, and operations supplies needed to keep production running
Let’s look at the example of making candles. Raw materials would be wax, wicks, and colors. Work-in-progress would be colored or shaped wax. And, of course, the finished good would be a fully formed candle with a wick on top, ready to burn for a cheesy romantic dinner.
Before moving on, let’s quickly review the distinction between inventory and stock. These two terms can often be used interchangeably, but technically, there is a difference. As we mentioned already, inventory encompasses all the bits and pieces from raw materials to finished products, while stock only includes finished goods ready for sale.
Inventory management vs. inventory control
- Inventory control — One part of the broader discipline of inventory management that’s focused on knowing where your inventory is and ensuring it travels to the right place.
- Inventory management — Encompasses the above, and in addition, it’s also the ongoing process of reducing the cost of inventory while maximizing the company’s profits. This includes expenses like carrying costs, inventory processing overheads, and purchasing raw materials.
Why is inventory management important?
There are four common goals of inventory management to keep in mind when coming up with your strategy:
- Improving the accuracy of your production and order fulfillment cycle
- Keeping your inventory organized, using space to its full effect
- Cutting down on waste like inventory carrying costs and transport time
- Saving time and money by improving organization and lowering lead time
You get more out of what you focus on, so place your crosshairs on the positives — read the best resources and look to emulate the companies you admire.
The overall aims of inventory management are universal, but your business will be aligned toward different goals than your neighbor. That definition spells out the end goal that every business owner should have when it comes to inventory management.
Can you hazard a guess as to what it is?
The effects of good inventory management are saving time, money, and resources (including human energy), thus lowering stress levels all-round. However, these are positive side-effects of good practice, not the end goal. The end goal is 100% complete customer satisfaction.
Don’t underestimate the effect customer satisfaction has on your business. Reviews and word of mouth contribute to a reputation, and it’s hard to shake a bad one. Constantly having this goal in mind will make it a lot easier to focus on optimizing your inventory to achieve your business potential.
Inventory management vs. supply chain management
Supply chain management, or SCM, oversees the entire process of producing and delivering goods. It includes everything from sourcing raw materials to delivering the final product to the consumer. SCM involves coordinating suppliers, manufacturers, logistics, and distribution to optimize efficiency and cost-effectiveness.
Inventory management, on the other hand, focuses specifically on controlling and overseeing a company’s inventory. It makes sure that the right amount of inventory is available at the right time to meet demand without incurring excess costs or stockouts.
In short, SCM is broader, covering the entire production and distribution network, while inventory management is a component within that system focused on stock levels.
Read more about supply chain management.
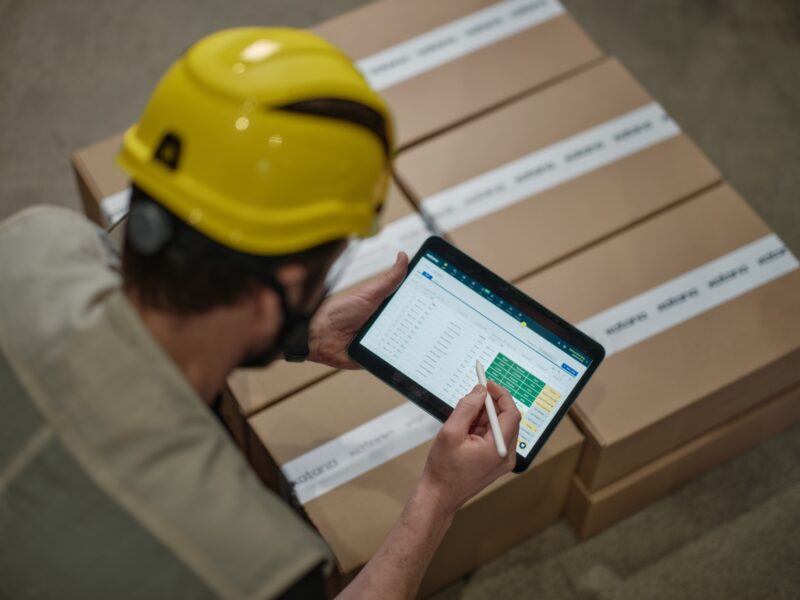
Tips for managing your inventory
There are a lot of moving parts, literally and figuratively, when talking about inventory management. Below you’ll find some tips that help you ensure all these parts move around smoothly in an organized and predictable fashion.
- Prioritize your inventory — Focus on the most valuable items in your inventory. Categorize your stock based on factors like sales frequency, cost, and demand to ensure that high-priority items are always available.
- Track all product information — Keep detailed records of product information, including SKU, barcode data, suppliers, and any relevant specifications. This helps streamline the ordering process and ensures accurate tracking.
- Audit your inventory regularly — Regular audits help identify discrepancies between your records and actual stock levels. This practice prevents issues like overstocking, stockouts, and financial discrepancies.
- Analyze supplier performance — Evaluate your suppliers’ reliability, quality, and delivery times. This allows you to make informed decisions about which suppliers to continue working with and which to replace.
- Practice the 80/20 inventory rule — Apply the Pareto Principle by focusing on the 20% of items that generate 80% of your sales. This approach helps prioritize efforts on the most impactful products.
- Be consistent in stock receiving — Establish standardized procedures for receiving inventory to ensure accuracy. Consistency in checking and recording incoming stock prevents errors and maintains inventory integrity.
- Track sales efficiently — Use sales data to understand which products are performing well and which aren’t. This information helps in making better restocking decisions and optimizing your inventory levels.
- Invest in inventory management technology — Utilize inventory management software to automate tracking, ordering, and reporting processes. This investment can significantly reduce errors and improve efficiency.
- Use tools that integrate with your other solutions — Ensure that your inventory management tools can seamlessly integrate with your other business systems, such as accounting, sales, and shipping platforms. This integration fosters a more cohesive and streamlined workflow.
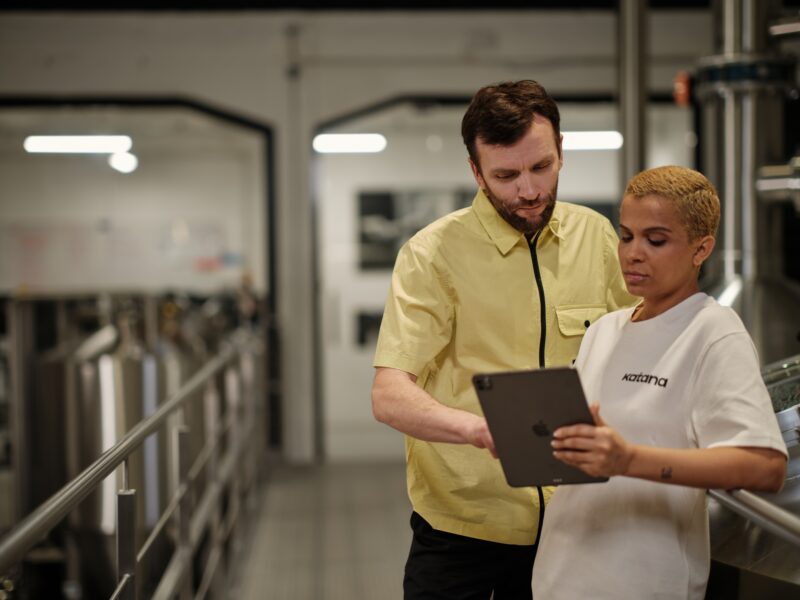
Inventory management techniques and strategies
It’s time to get to grips with the most popular inventory management techniques — the following are widely practiced and are here to stay, so the sooner you get to know them, the better.
Some are so successful that other industries, like software development, have adopted them.
The following principles work regardless of whether you have a small family-run business or aspire to head a multinational company. But one keynote before we start — these methods aren’t in competition or conflict with each other. You don’t have to choose one and ignore the rest.
The optimal approach is to find the most useful aspects of each theory that fits into your business as it stands.
- Periodic inventory management — Involves taking physical counts of inventory at set intervals (daily, weekly, monthly, etc.) without tracking changes in between. This traditional method is less accurate and relies on matching records at each stocktake, which is not sustainable for modern businesses.
- Perpetual inventory management — Continuously updates inventory records whenever stock is moved, or an order is placed, providing real-time accuracy. With modern software, this method reduces time consumption and prevents issues like missing or double-assigned stock.
- Just-in-time (JIT) inventory management — Aims to produce goods exactly when needed to meet demand, minimizing inventory costs and waste. Focuses on eliminating inefficiencies, continuous improvement, customer-centric strategies, and maintaining a balanced work environment.
- ABC inventory management — Categorizes inventory based on sales volume, identifying high-performing items (A) that account for most sales, and low-performing items (C) that contribute less. Helps businesses focus on efficient inventory turnover and consider removing slow-moving products.
- Consignment inventory management — Suppliers retain ownership of inventory until it’s sold to the end customer, reducing risk for vendors and saving on delivery costs. Useful for testing new products without market research, as retailers can return unsold goods.
- Reorder points — Predetermined stock levels that trigger the need to order more inventory, preventing stockouts and overstocking. Helps maintain consistent production schedules and ensures timely fulfillment of customer orders.
Want to know how to calculate your reorder point? Check out this blog post on reorder point formula to find out.
- Safety stock — Extra inventory kept as a buffer against unexpected demand spikes or supply shortages. Ensures timely deliveries and smooth operations, but requires careful calculation to avoid excessive stock holding.
- SKU rationalization — The process of reducing the number of unique products to focus on high-margin and fast-moving items. Involves removing low-performing or similar products to streamline inventory and increase overall revenue.
- Economic order quantity (EOQ) — Calculates the optimal order quantity that minimizes the total costs of ordering and holding inventory. Helps businesses reduce costs by determining the most economical number of units to order at one time.
- Minimum order quantity (MOQ) — Specifies the smallest amount of a product that a supplier is willing to sell, ensuring profitability and efficient production. Buyers must purchase at least this quantity to transact with the supplier.
- FIFO and LIFO — Inventory valuation methods where FIFO (First-In, First-Out) assumes the oldest inventory is sold first, and LIFO (Last-In, First-Out) assumes the newest inventory is sold first. These methods impact cost of goods sold and financial reporting.
- Batch tracking — A system that monitors the movement of goods using batch numbers, enabling traceability from production to sale. Essential for quality control, recalls, and regulatory compliance, ensuring product safety and accountability.
- Demand forecasting—Predicting future customer demand using historical data, market trends, and statistical analysis. Assists in making informed decisions about inventory levels, production planning, and resource allocation.
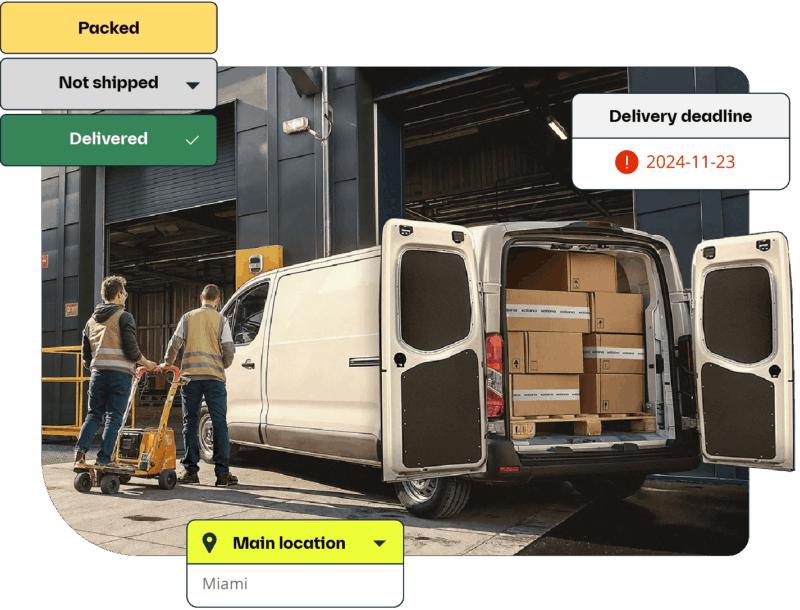
Inventory management challenges
While efficient inventory management seems to be the answer to all the problems a business may face, there are plenty of hardships on the journey to efficiency. Here are some every product business has to deal with.
Handling obsolescence
Handling obsolescence involves managing inventory items that become outdated or obsolete, which can potentially lead to financial losses. It requires proactive strategies like regular reviews and timely markdowns to minimize the impact on profitability.
Managing returns and reverse logistics
Managing returns and reverse logistics entails efficiently processing returned products through restocking, refurbishing, or disposal. Effective reverse logistics can recover value, reduce costs, and maintain customer satisfaction.
Coping with seasonal demand fluctuations
Coping with seasonal demand fluctuations requires adjusting inventory levels to match seasonal variations in demand to avoid overstocking or stockouts. This involves accurate demand forecasting and flexible supply chain management to respond to changing market needs.
Want to prepare for more challenges?
To become a master in fighting issues and tackling hardships like a warehouse superhero, we suggest you read up on the most common inventory management challenges. We’ve gathered the biggest obstacles businesses face in daily stock management and share the best solutions to each issue.
Or, if you want to dive even deeper, then we’ve put together a comprehensive article on supply chain inventory management, including 7 best practices to set yourself apart from the competition.
Implementing technology in inventory management
Inventory management technology is not just a nice-to-have but becomes crucial if you wish to scale efficiently and stay competitive. Implementing advanced technologies can streamline operations, reduce errors, and provide real-time visibility into your inventory. Below, we’ll list some of the key technologies that can transform your inventory management processes.
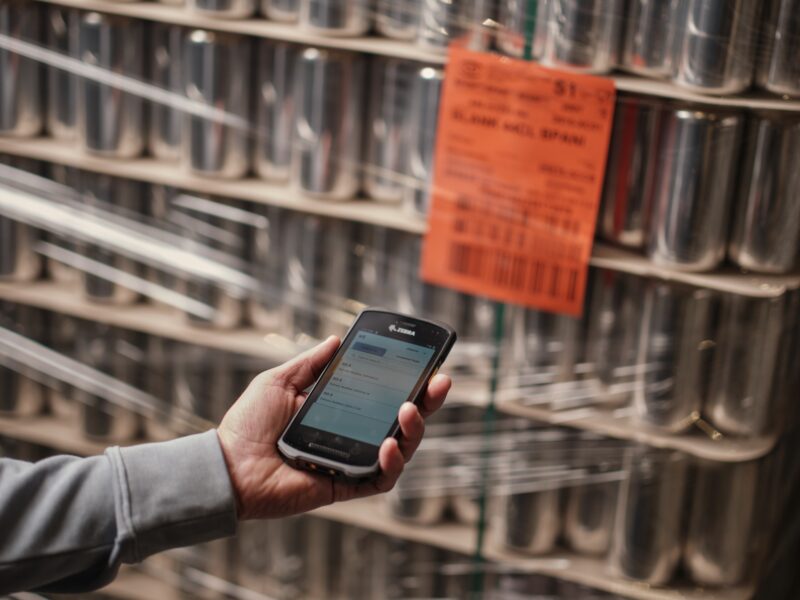
RFID technology
RFID (radio frequency identification) uses radio waves to track products in real time without manual scanning. This technology allows businesses to quickly and accurately monitor inventory movement, making it ideal for large-scale operations with thousands of items.
Barcode systems
Barcode-based inventory management assigns a barcode to each item, which is scanned whenever the item moves into or out of inventory. This system improves accuracy over manual methods and provides real-time updates on stock levels.
IoT in inventory tracking
The internet of things (IoT) integrates smart devices and sensors to provide real-time inventory tracking and data analytics. IoT enables automated monitoring of stock levels, environmental conditions, and equipment status, enhancing supply chain visibility and efficiency.
Demand forecasting and planning
Advanced software tools use historical data, market trends, and statistical models to predict future customer demand. Accurate demand forecasting helps businesses optimize inventory levels, reduce costs, and meet customer needs effectively.
Inventory management systems
When people think of inventory, they often imagine gargantuan warehouses packed to the rafters with cardboard boxes and hundreds of staff scurrying around. But that’s not always the case. In fact, most businesses need only a fraction of that space to store their products and materials.
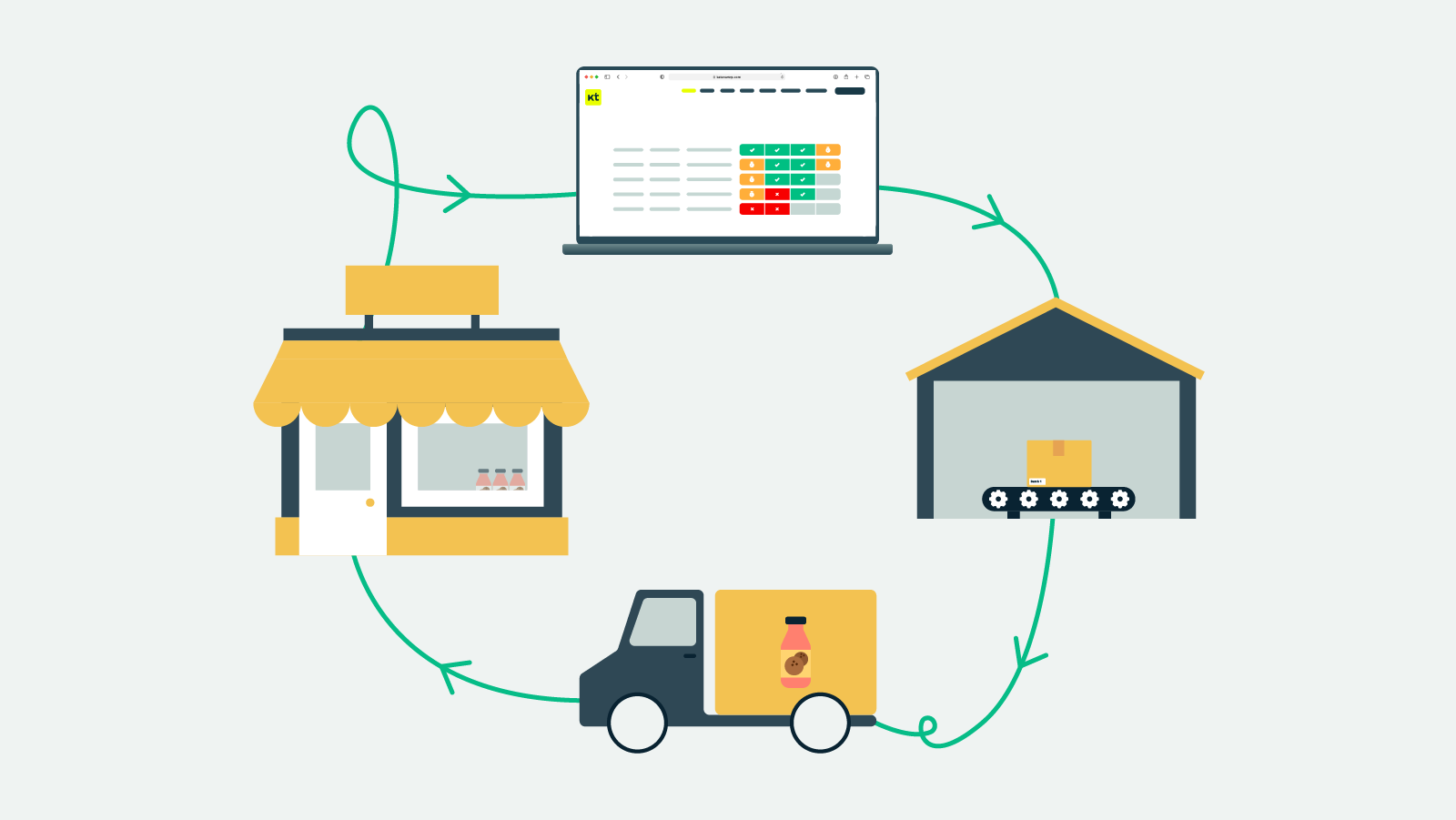
What is an inventory management system?
Inventory management systems are processes and solutions to manage all goods, materials, products, and components owned by a business.
The first port of call, as always, is a pen-and-paper system. This includes written stocktakes and order invoices. Many hobby and micro businesses use this method to manage inventory, if only in part.
But the limitations will be reached very quickly here.
A step up the ladder is using Excel spreadsheets for inventory management. These work fine for a while as long as good practices are followed, like backing up data. Even Formula 1 cars have been built using only an Excel sheet for inventory management.
However, this functionality is restricted. You will have to constantly update a web of spreadsheets to keep your purchases, recipes, raw materials, final products, and sales all in check at the same time.
Sooner or later, problems will occur, regardless of your spreadsheet skills.
The more inventory data added, the more human errors will crop up, which leads us to the final option — real-time inventory management software. These are more robust than spreadsheets and come with functions specifically designed for the purpose of inventory management, so you don’t have to do any tinkering.
What should good inventory management software do?
There’s no doubt that inventory management software is the solution for small and medium-sized companies to optimize their inventory.
The real question here is: How do you pick the right software?
Let’s dig deeper into the features you should look out for when choosing a software system for inventory management.
How to choose an inventory management system?
The main things your inventory management software should be capable of include:
- Storing your entire product portfolio in one place with no need to enter something twice
- Integrating with the most popular business tools for a unified experience
- Using barcode scanners for stocktakes
- Attributing as many variations (size, color, embellishments, etc.) to each product
- Tracking orders from suppliers so you know when stock is expected
- Setting reorder points to avoid stockouts
- Being accessible to you anywhere while still being secure, also known as cloud inventory management
Inventory management software for total inventory control
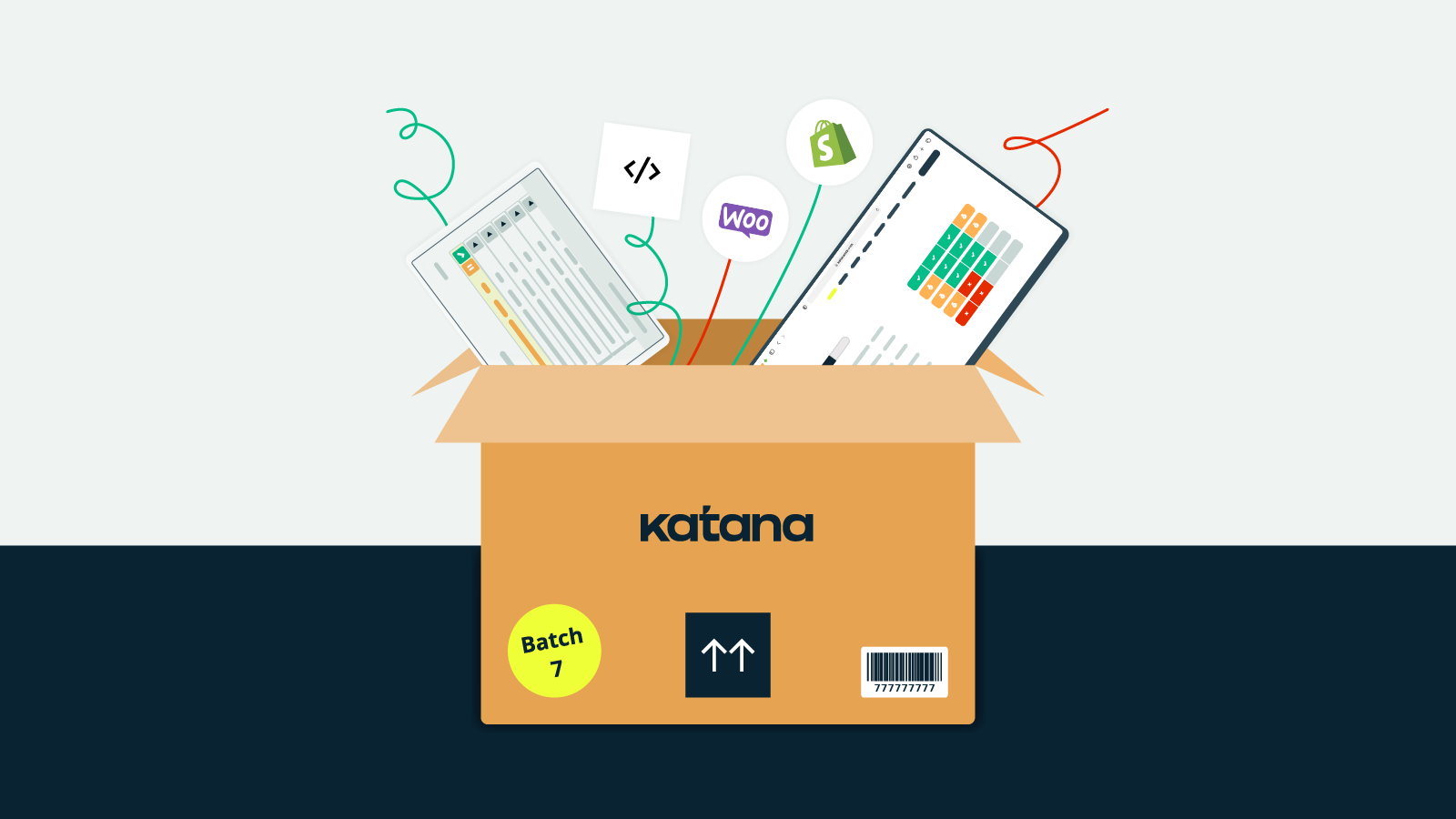
The theory is all well and good, but how does it all pan out when you get to the real thing? Let’s look at Katana’s inventory management software and see how we can implement some of the points we’ve covered.
1. Live inventory management
One of the main problems that businesses encounter when fulfilling their sales orders and scheduling their production is the constant need to check inventory — whether that means going into the stock room or trawling through spreadsheets to see what finished goods and raw materials are available.
Katana’s live inventory management software does all the hard work for you by keeping an up-to-date inventory, which shifts every time a sales order comes in. There’s no need to modify data every time an order comes in because the system does that for you. What’s more, Katana lets you forecast and plan inventory based on accurate sales data, so you’re always prepared to meet the demand.
2. Setting reorder points
Remember these? Katana allows you to set reorder points for each item, so you always know when to make additional products or purchase more materials. You can easily see under the column “Missing/Excess” how close you are to the optimal level of 0. You know you’re in the negative if it’s red and suggests filling up on that item.
Missing/excess = in stock – committed + expected – reorder point
3. Real-time master planning
The real magic with inventory management comes when you consider raw materials. One of the difficulties with production is that different products can share the same materials. This complicates keeping stock because you must track where your materials are used. Katana, however, will keep track of all these so-called “committed” materials so that you never run short.
On top of that, you can prioritize your orders with a simple drag and drop.
So if you have an order you want to get done faster (maybe the customer is a little bit of a VIP), you can just move the order up the line. The software will automatically book your available material stock to higher priority orders. This means that you can easily see what the effects are going to be on all other production orders in a color-coded visual chart. Katana will highlight any resulting delay risks of not getting the customer orders shipped on time.
4. Sales order fulfillment
Having your entire flow from purchasing to sales in one place makes it easy to make decisions and changes. With seamless integrations to the most popular e-commerce platforms, all your sales are synced to Katana, so your inventory doesn’t need to be managed in more than one place.
Every time an order comes in, Katana adjusts your inventory and production line without any extra input needed from your side. You will immediately see whether you have the necessary items in stock or raw materials available to make the products ordered by the customer.
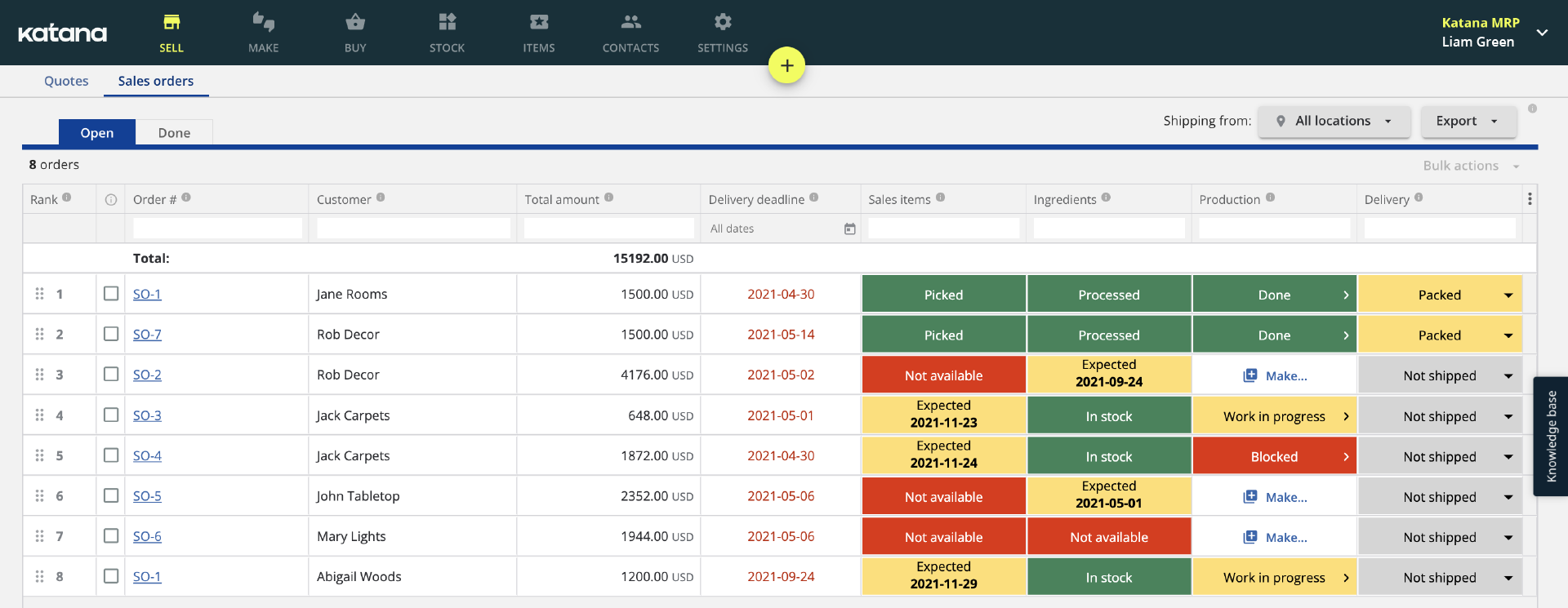
5. Integration with essential business tools
While inventory management is the pillar of any business handling products or materials, there are plenty of other aspects of a business that need tending to. From accounting and sales to reporting and shipping — the right software can speed up processes and take much of the work off your hands.
Katana has numerous integrations to choose from to keep your data and teams in sync. And if you’re using a tool that you can’t imagine parting ways with, there’s a solution for that too.
With our open API, you can build custom flows and create the perfect workspace fitting the specific needs of your business.
So, there you have it, the ultimate guide for inventory management.
No business wants to be spending all their days keeping up with inventory. The whole point of this guide is to show you how to make managing your inventory as streamlined as possible, giving you enough time to grow your business and focus on the things that really matter.
Managing your inventory properly takes a lot of planning, time, and effort, but it can be a breeze with the proper tools in place.
Katana brings together every aspect of your inventory management. Request a demo today to see it in action. Soon enough, managing your inventory will become second nature, and you’ll wonder what all the fuss was about.
Table of contents
Inventory management guide
More on inventory management
Get visibility over your sales and stock
Wave goodbye to uncertainty by using Katana Cloud Inventory for total inventory control
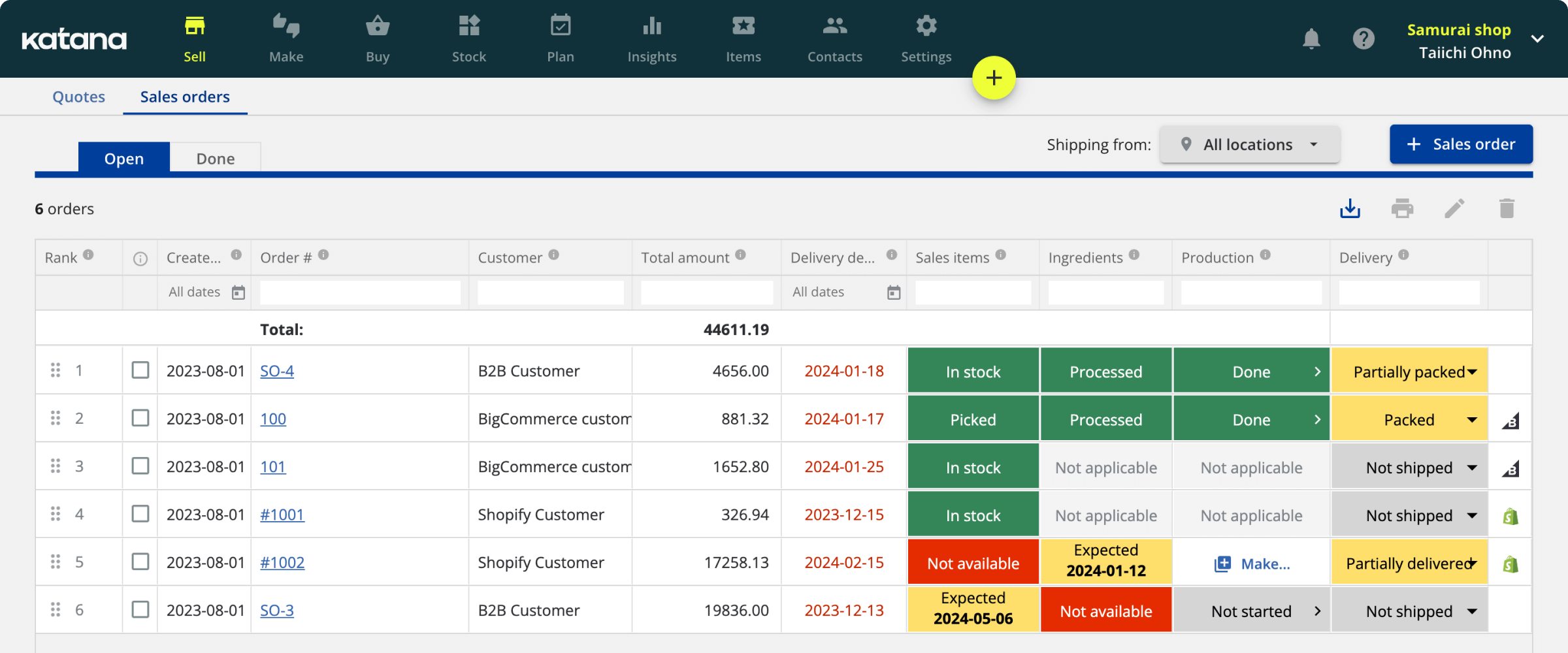
inv-mng-download
Get the ultimate guide to inventory management
Guide sent to your email address. We’ll also send occasional helpful tips, and you can unsubscribe any time. Read our Privacy Policy to learn more.