What is supply chain inventory management?
Supply chain inventory management plays a pivotal role in planning, executing, and controlling across the entire supply chain. It begins from sourcing and extends to product delivery, impacting businesses’ overall functionality and performance. This article explores the significance of inventory management and its effect on overall business performance.

Ioana Neamt
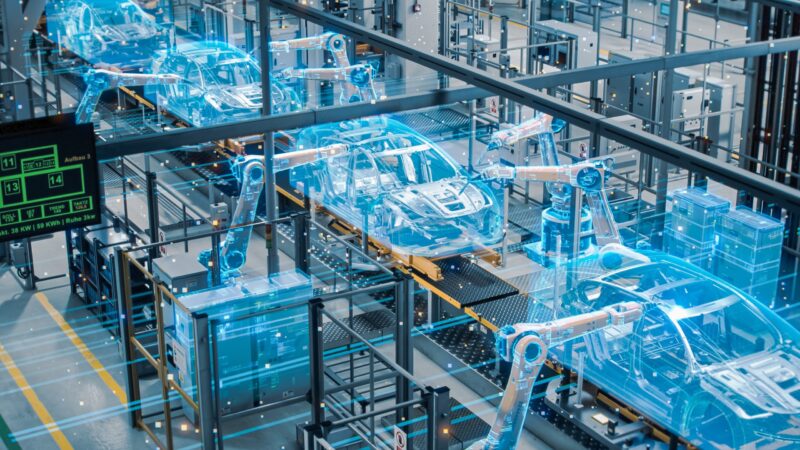
Supply chain inventory management is a strategic process that involves planning, implementing, and controlling the production and delivery of goods or services to the end customer. It focuses on optimizing and coordinating the entirety of supply chain operations, including production planning, scheduling, transportation, order fulfillment, financial transactions, various logistics, and even customer service.
With the supply chain market on the rise and now valued at almost $37.5 billion, the importance of supply chain management (SCM) is more important than ever. Read on to find out what makes inventory management in the supply chain crucial to business success and ultimate client satisfaction.
Why is inventory management in the supply chain important?
The role of inventory management in the supply chain is vital, leading to increased efficiency, visibility, and profitability. Within the supply chain, inventory management prioritizes the flow of goods and materials, focusing on tracking, storing, and distribution.
Simply put, its aim is to maintain optimal stock levels, ensuring the right products are available at the right time and place. This careful supervision of the flow of products and services plays a pivotal role in attaining success, quality, and customer satisfaction.
Supply chain inventory management can improve efficiency and enhance overall performance, but also reduce costs, improve delivery times, and gain a competitive advantage in the market. From sourcing and raw manufacturing of the goods to consumption by the consumer or end-user, inventory management in the supply chain involves three main phases:
- Buying inventory, where initial materials or components are procured and safely transported to the warehouse.
- Maintaining inventory, where inventory is to be strategically stored in the warehouse until needed.
- Selling inventory, where quantities of finalized goods available for sale are controlled. Orders are then dispatched to customers, and profit is observed.
Key components of supply chain inventory management
Supply chain inventory management is a complex process consisting of planning, execution, and control throughout the entire supply chain. Successful and continuous inventory management is key to maintaining coordination and optimization at each stage of the chain. It is important to keep in mind that the process uses a multitude of data, such as serial numbers, product cost, and dates of product movement and storage.
Here are the core aspects of supply chain management.
- Planning — Developing a comprehensive strategy, forecasting demand, setting inventory levels, and formulating production schedules ahead
- Sourcing — Identifying suppliers, negotiating contracts, and managing vendor relationships
- Production — Overseeing the manufacturing process, including scheduling, quality control, and operational optimization
- Inventory management — Supervise stock levels, forecasting demand, and managing order quantities to balance customer needs without excess inventory
- Logistics and transportation — Monitoring the movement of products (with a focus on transportation, warehousing, and distribution) from suppliers to consumers
- Collaboration — Various moving parts across the supply chain means that inventory management requires a coordinated effort between suppliers, manufacturers, distributors, partners, and customers alike
- Information management — Ensuring a seamless flow of information, providing transparency, and fostering data sharing across the entirety of the supply chain
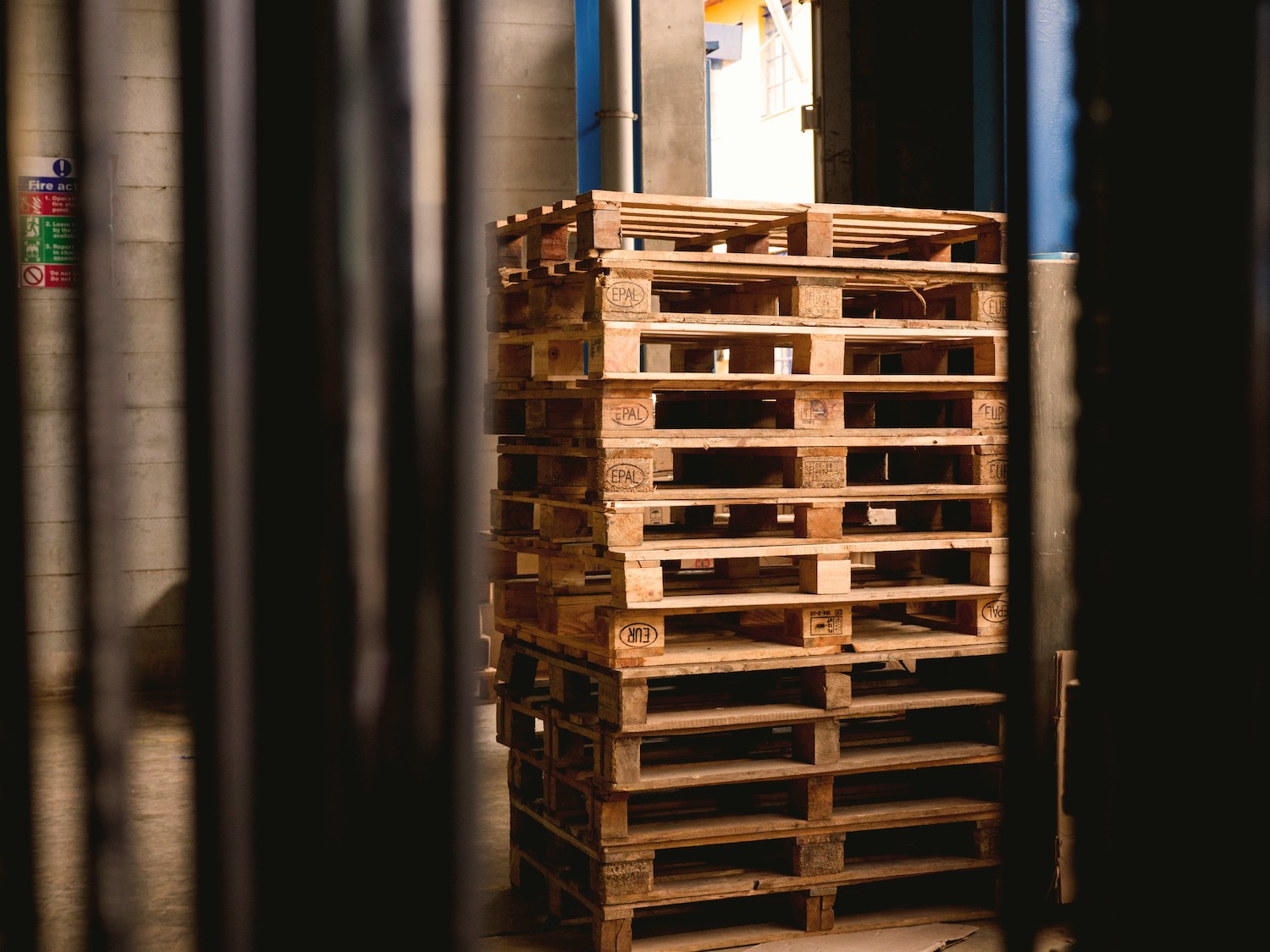
Risks in supply chain inventory management
From sourcing all the way through to product delivery, supply chain management is integral to a company’s overall functioning and performance. But it’s enough for just one of the above core components to fail in order to jeopardize the effective inventory management of the supply chain. On top of this, inventory management can have repercussions when done inadequately or superficially.
The primary challenges of inventory management within the supply chain are linked to uncertainties regarding demand forecasting, supplier reliability, and seasonal market trends.
Here are the main risks of supply chain inventory management:
- Deficient demand forecasting — The balance of future supply and demand relies on correct predictions. A lack of foresight in inventory control poses a significant obstacle that can lead to waste and losses.
- Supplier unreliability — Effective supplier identification and collaboration is a critical facet of supply chain management. An unreliable supplier can negatively affect inventory calculations, lead times, and the movement of goods, as well as generate overall frustration.
- Changing seasonal demands — Low inventory is obviously an issue, but overestimating it can be just as problematic, which is why businesses must avoid the pitfalls of overstocking and understocking. It’s important to observe the market trends that dictate seasonal inventory. A lack of seasonal awareness can lead to financial losses, warehouse inventory management complications, and scheduling conflicts.
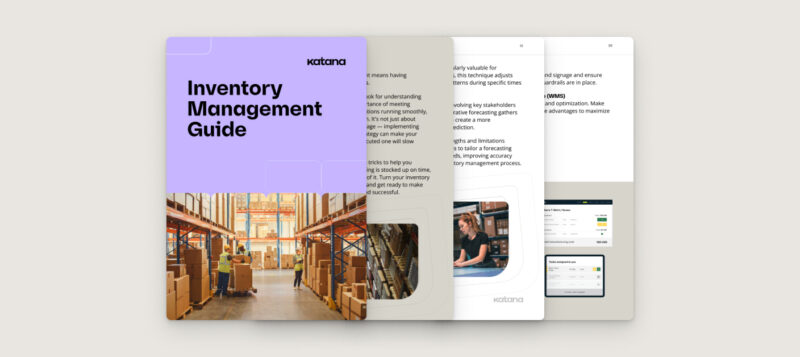
Download the ultimate guide to inventory management
A comprehensive ebook with everything you need to know about inventory management.
Effective inventory management in the supply chain: 7 best practices
Optimizing inventory management in the supply chain is a demanding task that requires careful consideration. When done right, the subsequent benefits include cost reduction, improved lead times, and increased customer satisfaction — which, in turn, will set the business apart in the marketplace.
Adopting the best inventory management strategies is crucial to expediting operations and exercising control over assets and equipment. Here are some of the 7 best practices of supply chain inventory management.
1. Accurate demand forecasting
Effective inventory management can sometimes be reduced to good demand forecasting. Accurate demand forecasting is done by analyzing historical trends and data which can allow businesses to predict the required inventory levels for the future, as well as respond to changing conditions and customer needs. This ensures that products meet customer demand without dealing with overstocking and surplus inventory.
2. Organized inventory classification
Categorizing inventory differs from business to business, and it’s particularly vital to organizations with substantial stock. Whether using the ABC analysis, the 80/20 rule based on profitability, or another system, flexibility and scalability are key. Categorization can be based on location, item type, or other commonalities, ensuring an organized approach that adapts to business growth.
3. Constant inventory monitoring
Regular monitoring helps mitigate risks associated with overstocking and understocking. Conducting consistent audits and monitoring sessions helps ensure that the physical inventory aligns with the reported data. Accurate monitoring can be done in three ways on a need basis:
- Physical inventory counts (stocktakes) for inventory accuracy
- Spot checks for high-volume products
- Cycle counting for periodic audits
4. Maintain a buffer inventory
Buffer inventory, or safety stock, is essential to accommodating supply chain fluctuations and unexpected events. By keeping additional stock, a business can basically manage variations in demand and supply. This strategy helps minimize the risk of unfilled orders by upholding an uninterrupted production pace, even during unforeseen disruptions.
5. Healthy relationship with suppliers
Managing supply chain connections is key to anticipating and solving problems. Many fixes of unforeseen issues lie in the hands of business collaborators — mainly, the suppliers. So it’s imperative to prioritize transparent communication, establish trust, and form long-term relationships with reliable suppliers for market success.
Businesses can take organic collaboration to a new level and use supplier management software that can help centralize supplier info and optimize the process of creating and keeping track of POs with suppliers.
6. Efficient lot tracking
This involves tracing the products through the distribution chain by using batch numbers. Also known as batch tracking, the process is particularly helpful in product recalls and can be done automatically through a lot tracking software.
7. Inventory management systems
Inventory management systems optimize order processes by tracking products through manufacturing, storage, and distribution. This improves efficiency, saving time and money. Additionally, these systems provide enhanced product traceability and detailed performance analysis.
Across every step of the supply chain, inventory managers and overseers should strive to adopt proven strategies, implement systematic approaches, and embrace emerging technologies to ensure accuracy and efficiency.
Effective inventory management is integral to navigating the complexities of supply chain dynamics — and, ultimately, improves delivery times, reduces costs, and enhances consumer satisfaction.
Optimize your supply chain inventory management with Katana
When it comes to effective supply chain inventory management, Katana can be your closest ally, bringing together each facet of your inventory management. Katana provides you with everything you need to organize and streamline your supply chain inventory. It equips you with features like:
- Live inventory management
- Production scheduling
- Real-time insights
- Software integrations
Want to see Katana in action? Request a demo today!

Ioana Neamt
Table of contents
Get inventory trends, news, and tips every month
Get visibility over your sales and stock
Wave goodbye to uncertainty with Katana Cloud Inventory — AI-powered for total inventory control