Catch your runaway costs with manufacturing overhead formula
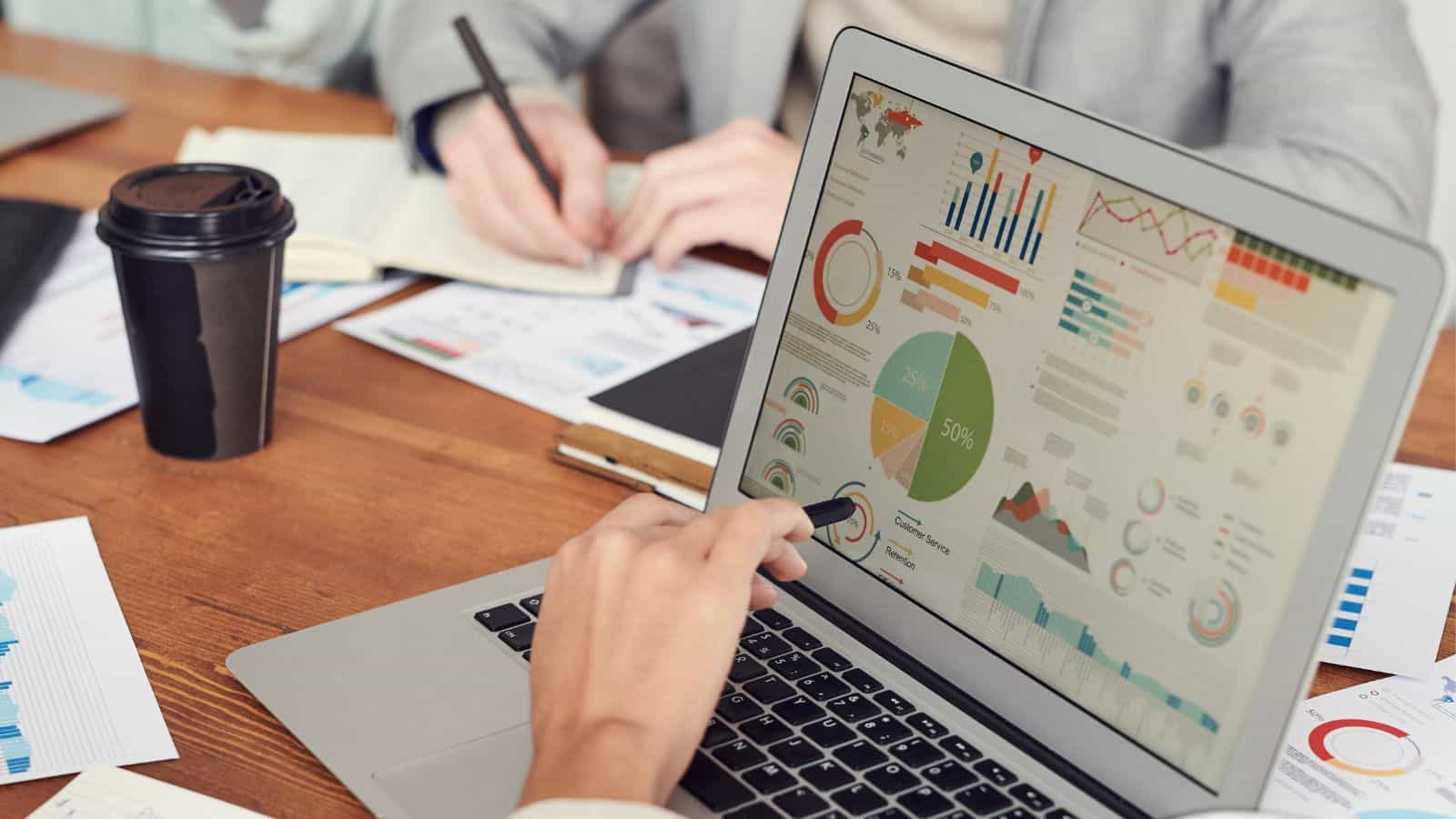
We’ve all checked our bank balances to find them slimmer than expected, thanks to some expenses we don’t always remember. Whether it’s the forgotten Netflix subscriptions or cheeky midday coffee cakes — they all add up.
These hidden costs will keep building up on your statement unless you take the time to reduce the unnecessary ones and take back control. It’s the same thing when running a manufacturing business.
It’s easy for all your little costs for things like cleaning and security to get buried away and forgotten when you’re spending energy on making. This is why learning how to calculate manufacturing overhead can help to resolve this issue and bring to light all the costs you might have lost track of.
This article will explore the importance of manufacturing overhead and how it can help keep your business running efficiently and effectively.
We’ll explore the manufacturing overhead formula, figure out what is manufacturing overhead, why it’s important, and how to calculate it accurately to make the most of your resources.
What is manufacturing overhead?
Manufacturing overhead refers to indirect costs incurred during production, such as utilities, rent, insurance, indirect labor, and materials. These costs are not directly tied to the production of specific goods but are necessary for the overall operation of a manufacturing facility.
Often without these things, you couldn’t run your manufacturing at all. But by breaking down your indirect costs, you can reduce those pesky bills that rarely come to the front of your mind.
It’s a calculation used for accounting purposes, but more importantly, it’s a method to begin to save on unnecessary costs.
Types of manufacturing overhead costs
When you think of what costs you have outside of direct materials, labor, and manufacturing processes, you might be overwhelmed by the thoughts that cross your mind.
There are just so many details that cost your business money, right? So, what does manufacturing overhead consist of?
Well, the first thing to remember here is that we’re just looking at indirect costs related to manufacturing. To get everything right, you may want to read up on what is manufacturing. But, administrative, sales, marketing, and finance expenses aren’t included in manufacturing overhead. Those fall under the umbrella of administrative overhead.
Instead, we can break down manufacturing overhead costs into four sections:
- Indirect labor
- Indirect materials
- Utilities
- Depreciation
Fixed overhead vs. variable manufacturing overhead
- Fixed overhead — Manufacturing costs that do not change with the production volume, such as rent and property taxes
- Variable overhead — Manufacturing costs that vary directly with the volume of production, such as electricity and raw materials
1. Indirect labor
Indirect labor includes the salaries of anyone that works in your workshop but isn’t involved in the manufacturing process.
That means maintenance people, janitors, cleaners, security guards, supervisors, quality control workers, and anyone else that helps keep the ball rolling.
As long as their job indirectly affects your production or production facility, you should include their salary in your manufacturing overhead costs.
It’s already adding up, isn’t it?
2. Indirect materials
Let’s look at some manufacturing overhead cost examples when it comes to materials. It might seem strange to think about, but it makes a lot of sense when you draw it out. Many extra bits and pieces often go into making your product, which wouldn’t stand out on first look.
These could include glue, tape, repair parts, general supplies, cleaning chemicals, and wasted materials.
Estimated vs. applied vs. actual overhead
- Estimated overhead — Anticipated calculation of the total manufacturing overhead costs expected in a given period
- Applied overhead — Overhead costs that have been assigned or allocated to specific products or jobs
- Actual overhead — Total overhead costs that have been incurred during a given period
3. Utilities
This is one of those areas where the costs are almost always inevitable and constant. You’ll have to pay bills wherever the work gets done, right? Rent on the building, water bills, internet, electricity, gas, property tax, and even insurance.
Every business will have its own set of utilities that need to be paid no matter what. Just remember that we’re looking at costs in relation to manufacturing, so your home office bills won’t be counted here.
4. Depreciation
Okay, to be frank, this one is a little bit complicated. But depreciation refers to how much an asset decreases in value over time. This applies to equipment and facilities which are subject to wearing down.
As per GAAP, this has to be measured per product.
We’ll show you an example of how to do this in the next section. But the general takeaway is that your equipment doesn’t last forever, and it’s always costing you something, even if you don’t know it.
Working out an estimate of that is a valuable addition to your manufacturing overhead. Plus, it can be used for tax claims deduction in some instances.
How to calculate manufacturing overhead cost
Small and medium manufacturers need to be extra aware of their manufacturing overhead because the effects of hidden costs are magnified at this scale. Without analyzing the details, your profits might not be as high as you first imagined.
Generally, manufacturing overheads are calculated per product annually. If you’re a small business, it’s going to be useful to do it even more often than that. The effects of your overheads could be quite drastic throughout the year, and you wouldn’t know until you checked. The first thing you need is the formula.
Manufacturing overhead formula
Calculating the manufacturing overhead is very straightforward once you know the indirect costs and the total units produced. All you need is the following manufacturing overhead formula:
Manufacturing overhead = Total indirect costs / total units produced
The thing is, how do we work out these total indirect costs? Well, we go back to the four elements we referred to before. Calculating each of them separately is going to make the whole process a lot easier, but also it means you have numbers for future comparison when you return to your manufacturing overhead.
But let’s look at an example of a skateboard business and see how to find the manufacturing overhead.
Indirect labor
Making skateboards can be a messy affair with so much paint and sawdust everywhere. There’s a cleaner that comes in to sort out all the mess that’s left at the end of the month. That comes to $2,000 a year.
Indirect materials
Lots of bits and pieces get used in the workshop that aren’t necessarily considered as direct costs — tapes for temporary fixes and bleach for cleaning. Not a lot of machinery is needed here, but a jigsaw needs its blade replaced every so often. $500 a year (yes, everything in this dream world happens to come to perfectly round numbers).
Utilities
Unfortunately, you can’t make hundreds of skateboards in your living room. So, you have to pay for workshop rent, bills, taxes, and the whole shebang. In this example, it comes to $12,000 a year.
Depreciation
It’s quite strange to have to calculate how much value is being lost on your assets. Since we’re renting the workshop, there’s no property to account for, but we do have some machinery. If the jigsaw is estimated to last seven years and it costs $1,050, then we could say that the annual depreciation is:
1,050 / 7 = $150
It might seem a little off the wall, but to be fair, this is a legitimate cost to your business. Now that we have all the numbers worked out, we can add them together and get our total indirect costs:
2,000 + 500 + 12,000 + 150 = $14,650 a year
How to find the manufacturing overhead per unit?
You have the total overhead. Now all you have to do is, you guessed it, divide it by the total units produced. In this fantasy skateboard shop, there are 800 skateboards made a year. So, the total manufacturing overhead per unit is:
Manufacturing overhead per unit = Total indirect costs / total units produced = 14,650 / 800 = $18.31
There we have it. Our manufacturing overhead comes to around $18 per skateboard. The accountant is happy, but that seems like quite a lot of extra costs, right?
Now comes the golden question.
How to reduce manufacturing overhead cost
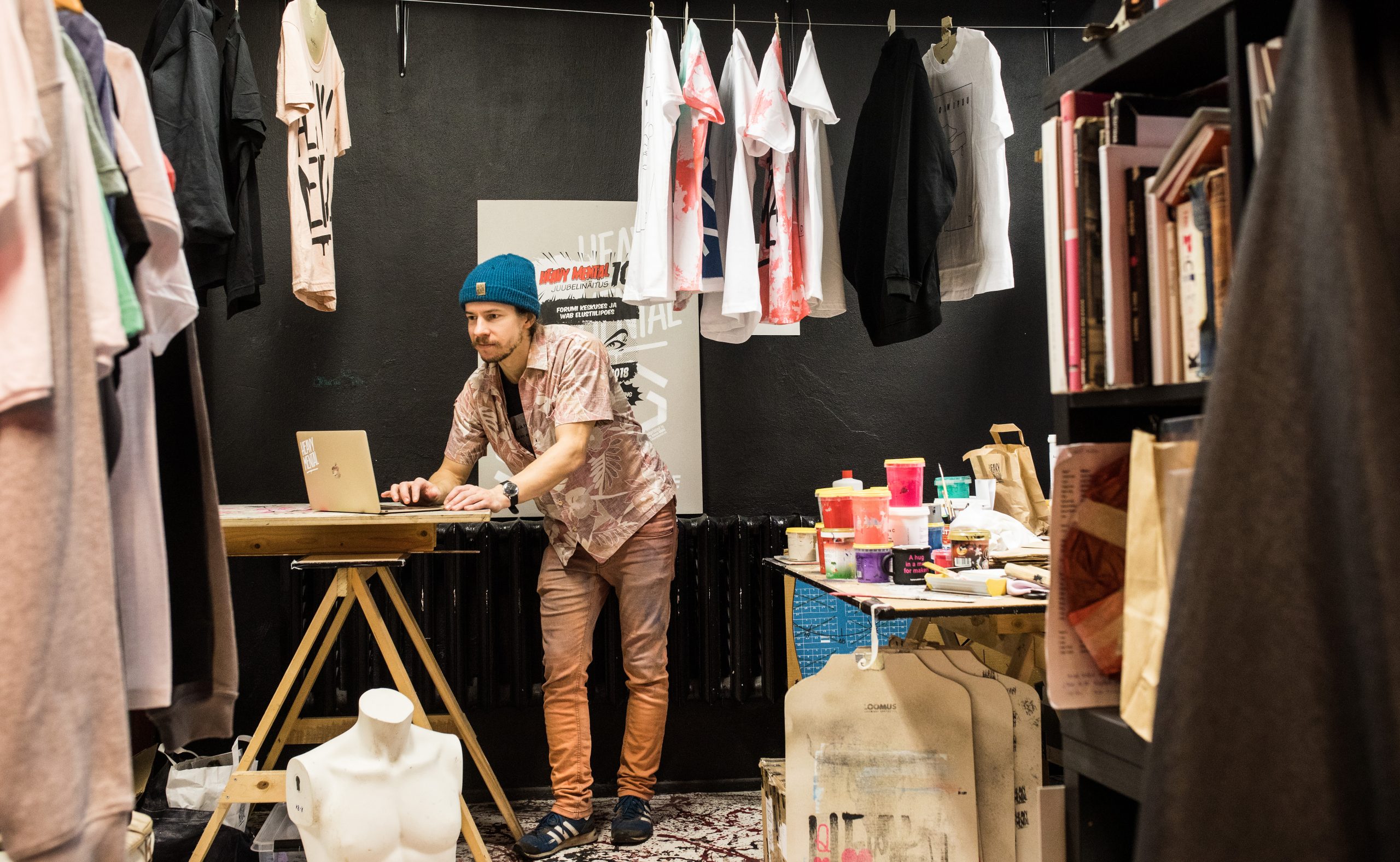
Every business will have a unique set of manufacturing overhead costs, so take the time to consider the ins and outs of your workshop.
We got the numbers down, but what do we do with them?
Well, of course, the aim is to run them down. Every little difference we make here will have positive background effects throughout the year. Here are some tips for hammering down your manufacturing overheads:
- Shop around — You’ll find that not all energy and water suppliers were created equal. You might well be paying more than you should for your utilities, especially if you are taking them all from one place
- Set budgets — Once your indirect costs are worked out, start setting targets for getting them down. If you review these every few months, by the end of the year, you will be surprised at the difference you have made
- Reduce waste — If your materials get broken or damaged, they become indirect materials costs. Try to see where the most significant waste is coming from and tackle your production planning strategy head on
- Clean after yourself — If every worker takes responsibility for their area, the money spent on cleaning can be greatly reduced
- Become more energy efficient — Use energy-saving light bulbs and encourage everyone to be frugal with their water usage. Every drop counts, and mother nature will be pleased too
- Ask around — The best people to help reduce indirect costs are the people spending the most time in your workshop. More than likely, they’ll have some unique ideas for tweaks here and there
- Consult with your accountant — How do you determine manufacturing overhead cost? Well, aside from following the steps, it’s a good idea to talk to your accountant, who knows the law of the land
Cloud inventory software to reduce your overhead costs

Implementing the right software for your needs is usually a good starting point for lowering manufacturing overhead. It’s too easy to overspend on a system beyond your needs and too complex to use.
Katana’s cloud inventory software is designed with the maker’s needs in mind so that you won’t be paying for features you’ll never use. Katana offers you everything a manufacturer needs, including:
-
Inventory management for finished products, raw materials, work-in-progress, MRO
- Seamless integrations with other platforms, for example, QuickBooks Online, Shopify, Xero, WooCommerce, etc.
- Multilocation support
- Katana Insights to easily track sales performance, trends, revenue, profit, and much more
Katana has all the features to monitor and reduce your overhead costs while tackling your direct costs at the same time. That means more control over what you spend your money and resources on.
Request a demo today and see why thousands of manufacturers use Katana to manage their businesses.
Table of contents
Manufacturing guide
More on manufacturing
Get visibility over your sales and stock
Wave goodbye to uncertainty by using Katana Cloud Inventory for total inventory control
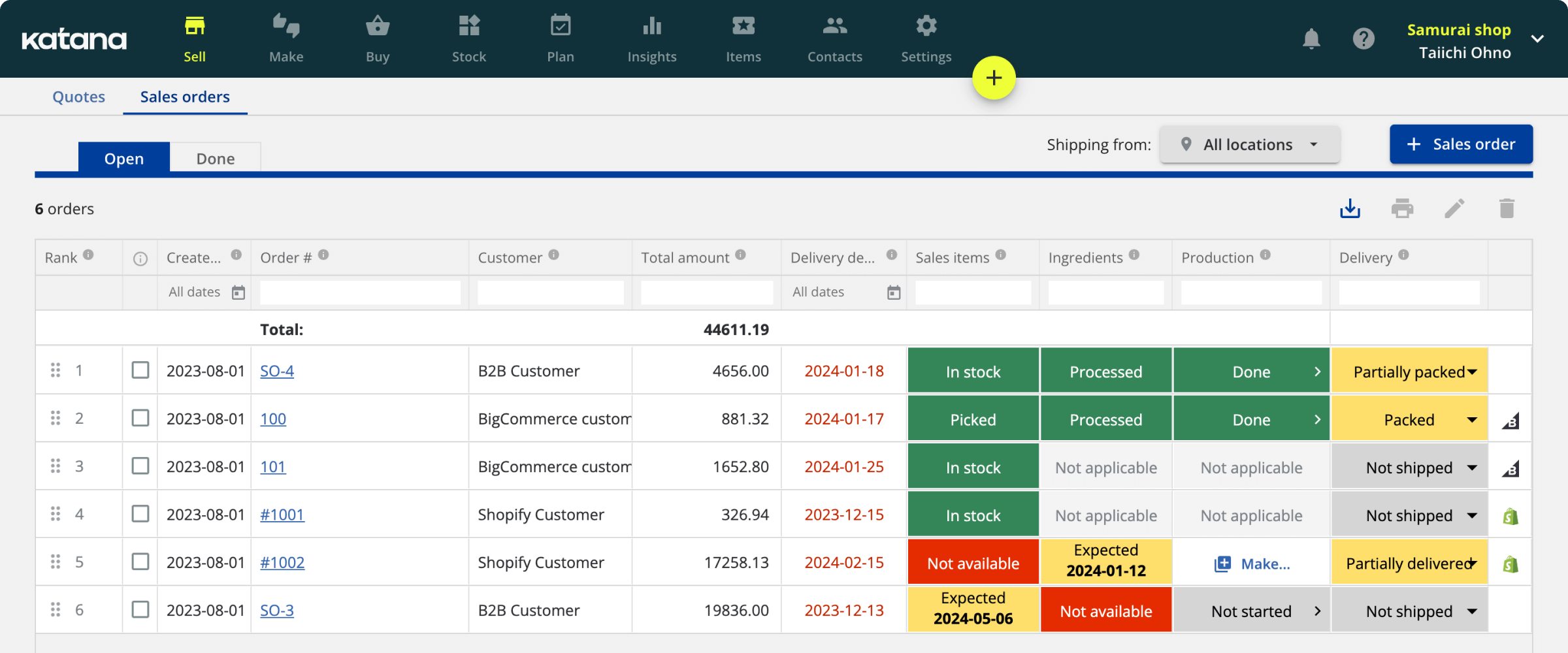