Perpetual inventory system: The best way to track inventory
Which stocktaking method sounds easier to you?
A. Taking a spreadsheet, heading into a warehouse that looks like Hanger 51 from Indian Jones, using your index finger to point between your spreadsheet and an item on the shelf to see what you have in stock — and doing that for every single item you hold?
Or
B. Using software that automates stocktaking and displays the latest quantity?
If you chose option B, you chose the inventory management method that takes advantage of a perpetual inventory system. But what is it, and how does it work? In this article, you’ll learn about perpetual inventory and the formulas it uses to update inventory levels regularly.
Let’s begin.
The thought of another spreadsheet making you sick?
Katana cloud software is a perpetual inventory management system built for manufacturers to centralize sales, production, and accounting to one easy-to-use platform.
What is perpetual inventory?
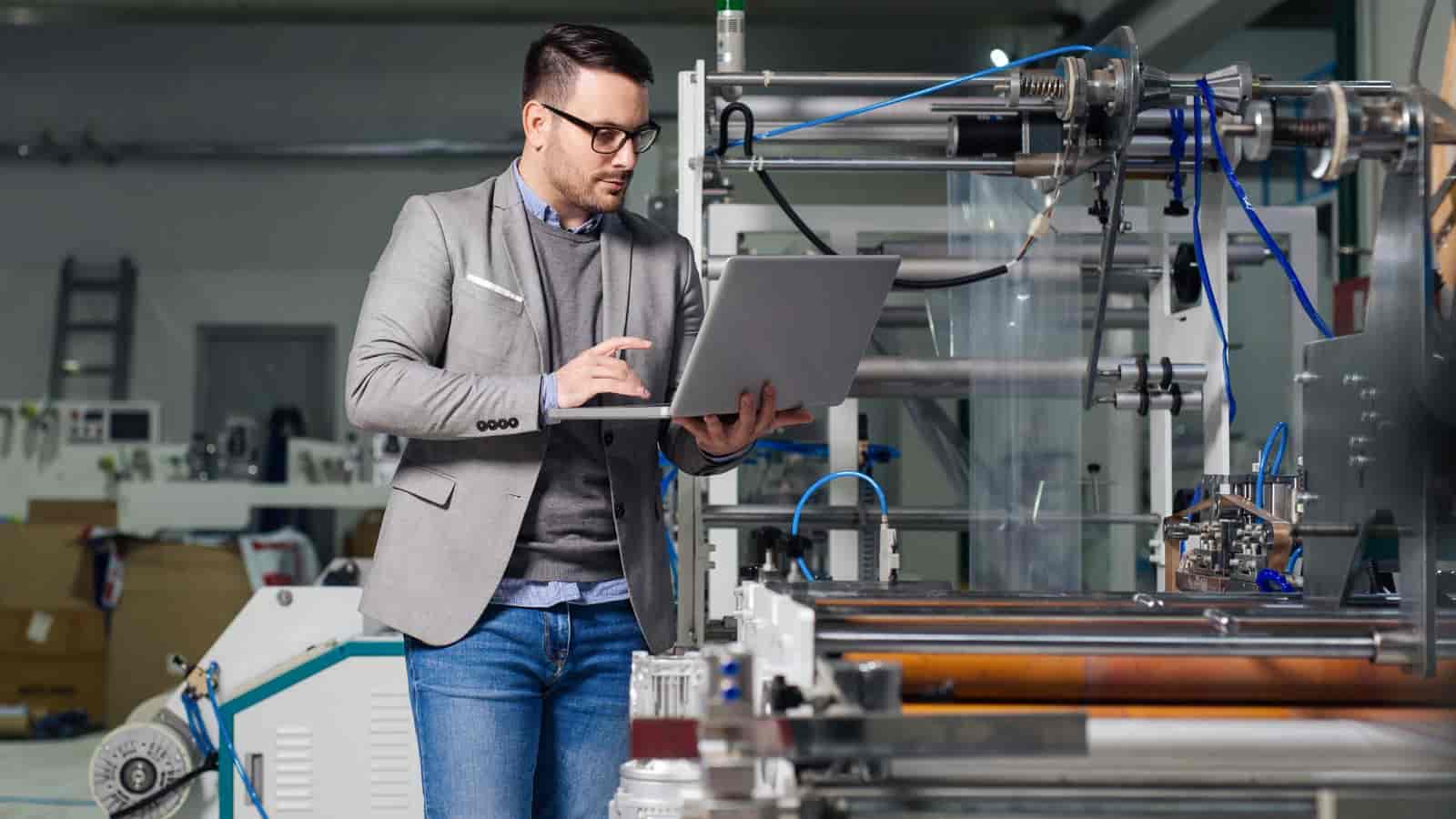
Perpetual inventory is the accounting practice of continuously maintaining inventory records in real time without counting stock levels by hand.
In the words of Biggie Smalls, “If you don’t know, now you know.”
You might not have known the definition of perpetual inventory, but computers, smart devices, automation, and AI have made perpetual inventory management in business and home life fairly commonplace. Take smart fridges — many come with gadgets and gizmos that help you track expiration dates and items inside and outside the fridge (just one of the many examples of perpetual inventory in action). Of course, that’s in theory — in business, perpetually monitoring inventory is a means to track stock accurately and is also important for your bookkeeping.
So, how exactly does a perpetual inventory system work?
What is a perpetual inventory system?
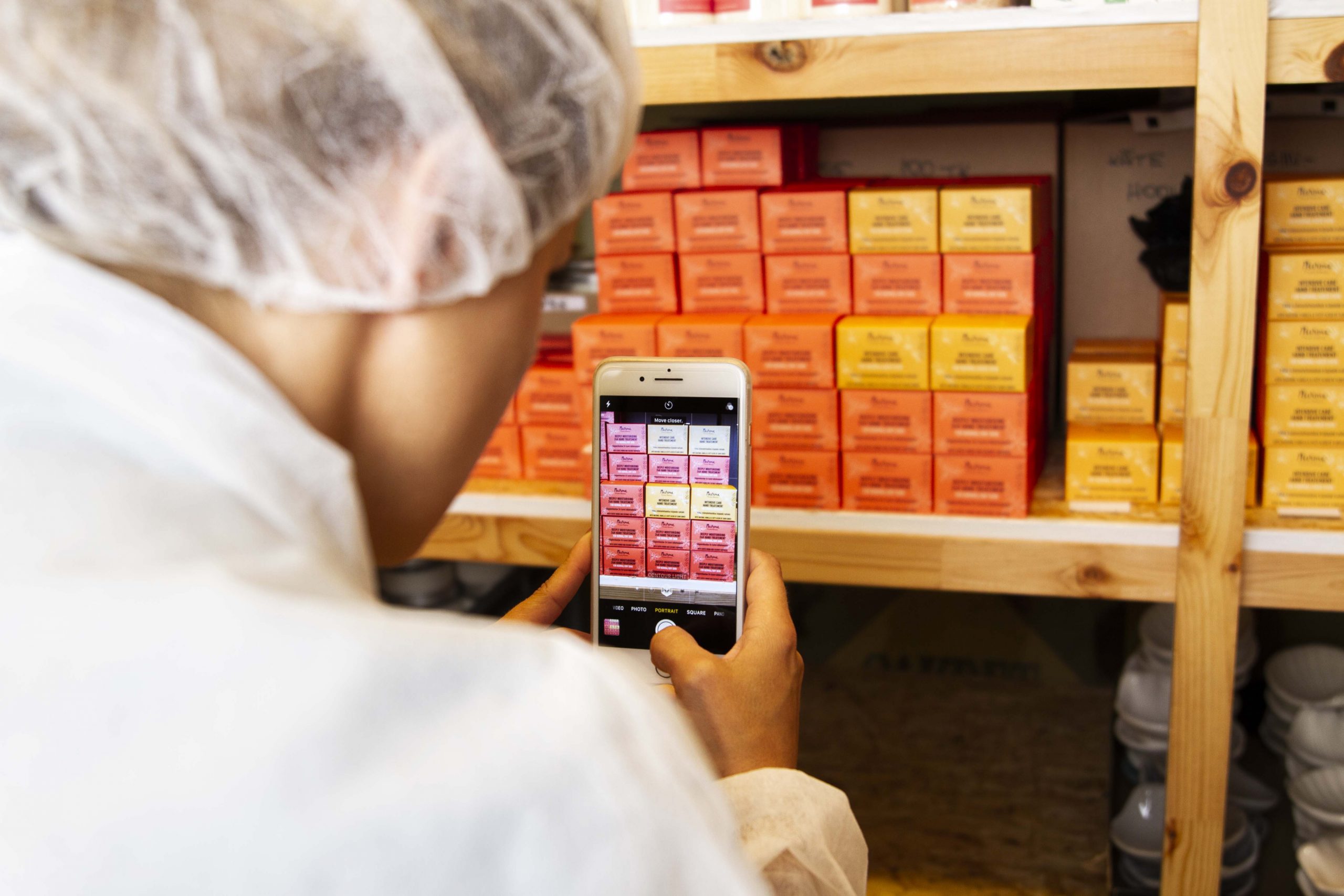
Perpetual inventory systems track the quantity and value of inventory in real time by continuously updating the inventory records with each sale, purchase, and manufacturing order.
It provides an up-to-date and accurate record of the quantity and value of items in stock, which allows for better control and management of inventory levels — ensuring that sufficient stock is available to meet customer demand. In a perpetual inventory system, the cost of goods sold (COGS) is recorded as you go along. This way, you always know how much money you’re making at any given time.
What is the difference between a perpetual inventory and periodic inventory?
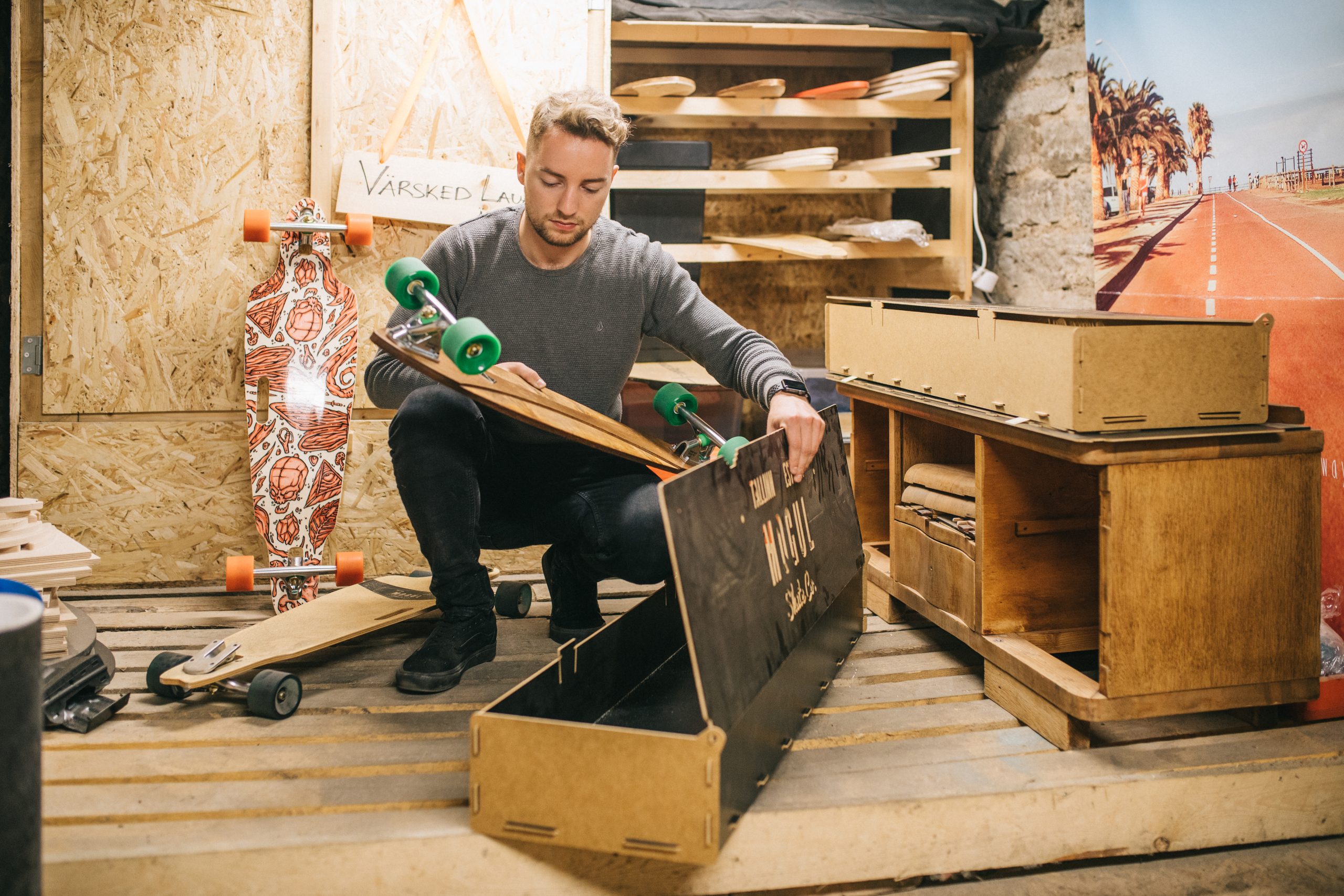
Perpetual inventory and periodic inventory are two methods of tracking and managing inventory.
In a periodic inventory system, the inventory records are updated less frequently, often at the end of an accounting period. The information about the quantity and value of inventory is less accurate and up-to-date, and a physical count of inventory is required to reconcile the records. Periodic inventory is suitable for businesses with lower turnover or those that don’t need real-time inventory information.
Quick breakdown
Perpetual inventory — continuous inventory tracking.
Periodic inventory — physical inventory stocktakes at fixed time intervals.
If you’re wondering if periodic inventory might be more of your business’s speed, then let’s quickly compare the pros and cons of using one over the other.
Advantages and disadvantages of perpetual inventory systems
Now you know the differences, here’s what to expect if you choose the easy street with perpetual inventory or go it rough with a periodic inventory.
Advantages of perpetual inventory systems
- Know exactly what you do and don’t have at any given time
- An accurate balance sheet with the COGS added continuously
- Achieve optimum inventory levels
- Make fast business decisions with up-to-date info
- Easy to spot discrepancies and chances to uncover theft, fraud, and lost goods
Disadvantages of perpetual inventory systems
- If stock is not checked physically at all, then there can be a discrepancy in the inventory
- Software required
Advantages of periodic inventory systems
- Simple application to any inventory
- It doesn’t require any software
- Stock levels are reliable after each inventory take
Disadvantages of periodic inventory systems
- Lack of info on inventory balances between stocktakes can hinder business decisions
- Time-consuming to check stock and then do the math
- Higher chance of theft and fraud due to the absence of continuous checking
- Lost goods can be overlooked and recorded as false sales
- Potentially inaccurate accounts can be very costly
Katana + QuickBooks: automated inventory management and bookkeeping
Katana bridges the gap between operations and bookkeeping by integrating with QuickBooks Online.
Who uses a perpetual inventory system?
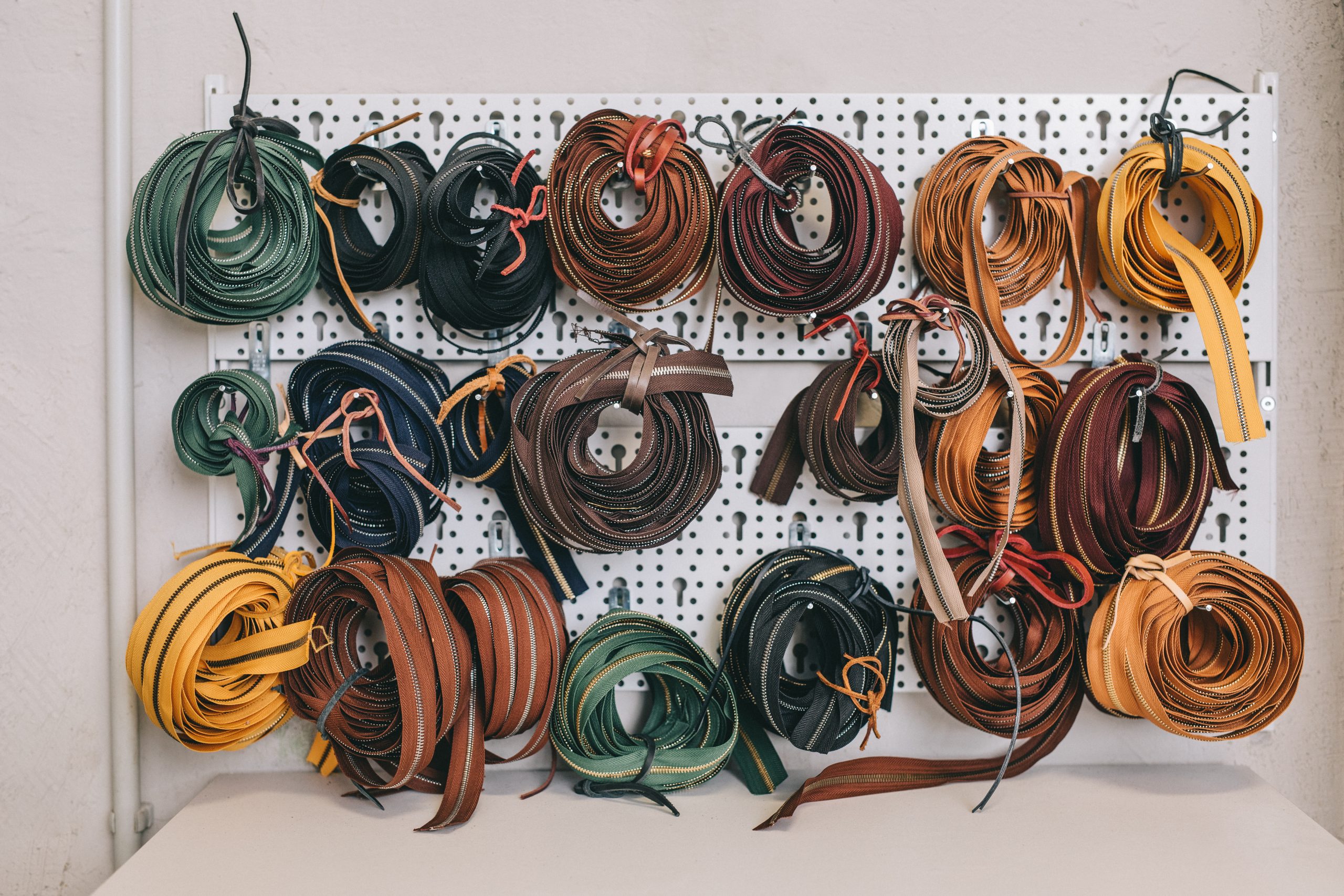
Businesses commonly use a perpetual inventory system with a high volume of inventory transactions, such as:
- Retail stores
- Wholesalers
- Manufacturers
Perpetual inventory systems are also beneficial for businesses that require real-time information about their inventory levels, such as for:
- Inventory control
- Demand forecasting
- Replenishment purposes
A perpetual inventory system allows these businesses to have accurate and up-to-date information about their inventory levels, which helps them make informed decisions about ordering new products, setting safety stock levels, and ensuring that sufficient stock is available to meet customer demand. This system also enables these businesses to avoid stockouts and overstocking, which can lead to inefficiencies, increased costs, and reduced customer satisfaction.
Using a perpetual inventory system can help businesses improve their inventory management processes and increase their operational efficiency and profitability.
How is inventory tracked under a perpetual inventory system?
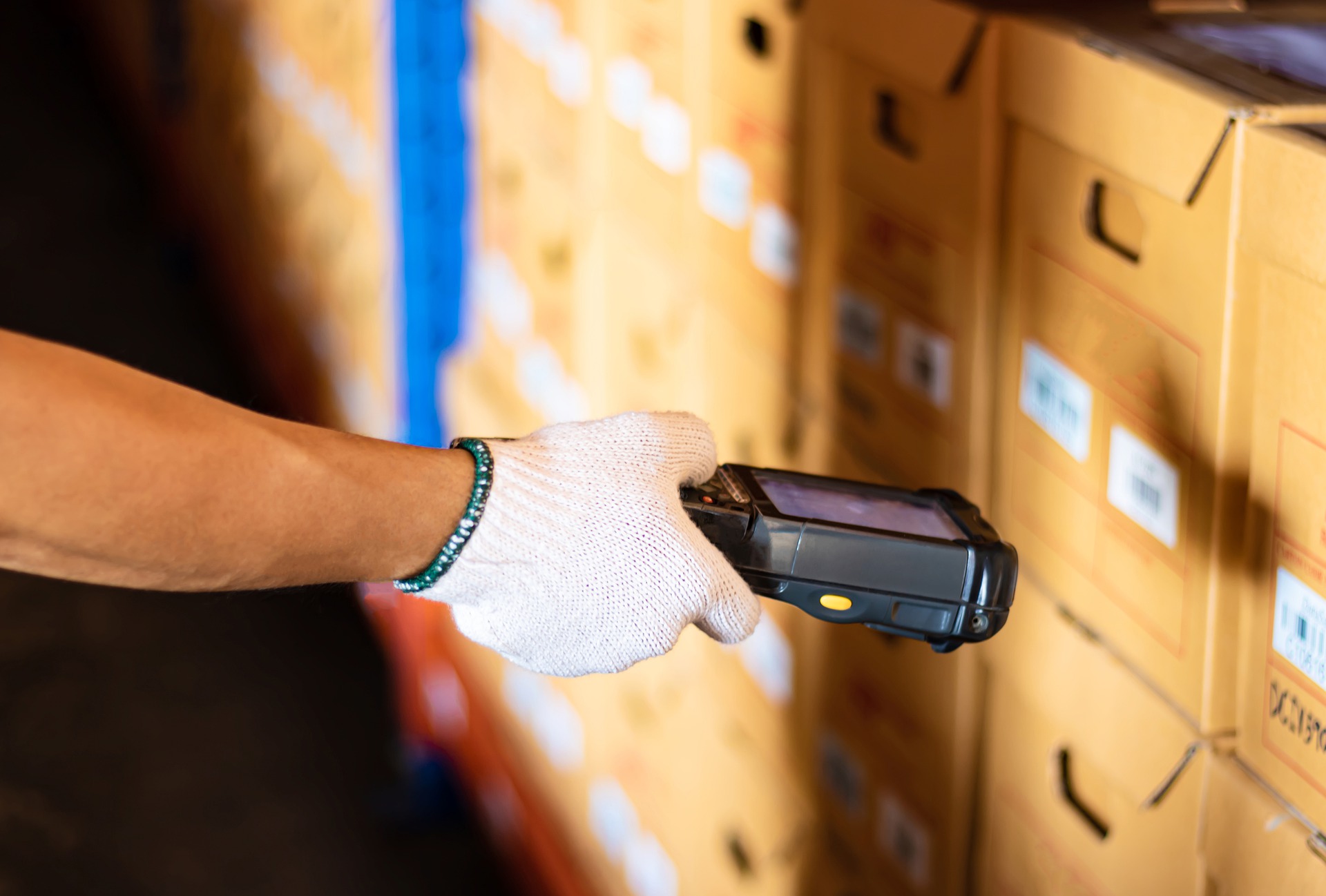
The perpetual inventory system tracks raw materials and finished goods inventory in a manufacturing setting.
Here are the long and short answers to how a perpetual inventory system works:
Long answer:
When raw materials are used in the production process, the system updates the quantity in the inventory records and reduces the value of the remaining supplies. Similarly, when new purchase orders are received, the system increases the quantity of the items in the inventory records and updates the value of the inventory.
When finished goods are manufactured, the system updates the quantity in the inventory records and increases the value of the products. When finished goods are sold, the system reduces the quantity of the sold items in the inventory records and updates the value of the remaining inventory.
Short answer:
Every time an item moves in and out of inventory, the system accurately reflects the latest quantity and value of the remaining items.
But that’s not all.
A perpetual inventory system designed for manufacturing companies can also track the production process, including:
- Production orders
- Work-in-progress inventory
- Inventory in transit
This information can be used to optimize the manufacturing process and ensure that adequate raw materials and finished goods are available to meet customer demand.
Perpetual inventory formulas
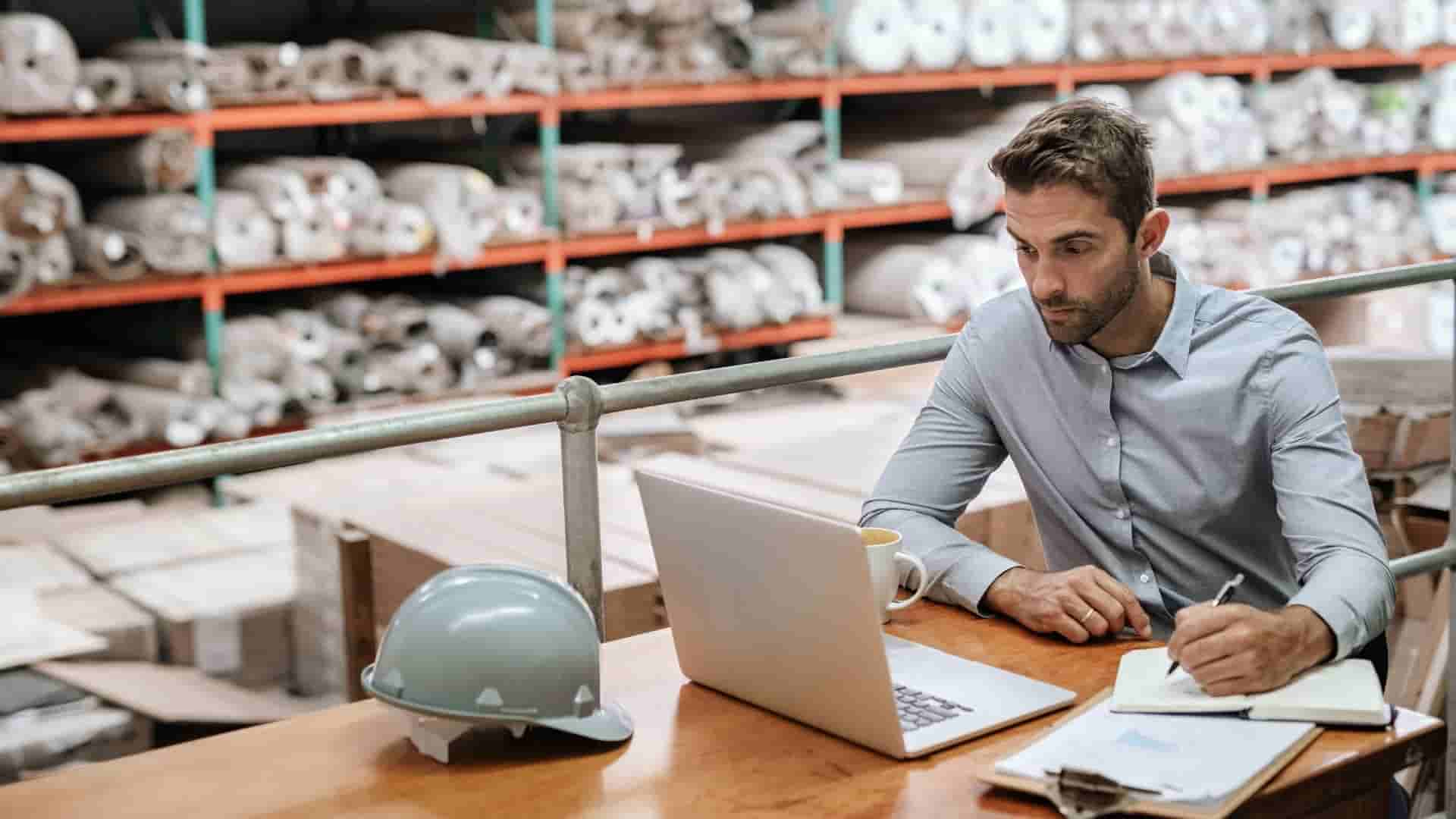
You now know what perpetual inventory is and how it differs from how your great-great-grandfathers used to count inventory. As mentioned, these systems track not only the quantity but also the values. Here are the formulas systems (or workers) use to get these values.
COGS
Knowing the cost of goods is important in any business because it provides valuable information about the cost of producing and selling products and helps businesses make informed decisions about:
- Pricing
- Inventory management
- Profitability
This formula is used to calculate the cost of the products sold during a specific period.
The COGS formula is:
COGS = Beginning Inventory + Purchases – Ending Inventory
Pro tip: learn more about COGS and how to properly use it by checking out this article: Cost of goods sold: a how-to for modern manufacturers.
EOQ
EOQ (economic order quantity) is a formula used in inventory management to determine the optimal order quantity of a product that minimizes the total cost of ordering and carrying inventory. In a perpetual inventory system, the EOQ formula can be used to optimize the ordering process by determining the optimal order quantity of a product based on the following variables:
- Annual demand
- Ordering cost
- Carrying cost
The EOQ formula is:
Q = √[2(DK/H)]
Pro tip: learn more about EOQ and how to properly use it by checking out this article: Economic order quantity (EOQ): balancing cost and demand.
Gross profit margin
The gross profit margin calculates the percentage of each dollar of sales representing gross profit. This metric provides valuable information about a business’s performance, showing how effectively it can generate profit from its sales. You can use the gross profit margin to compare a business’s performance with its competitors and benchmark performance against industry standards.
The gross profit margin formula is:
Gross Profit Margin = Gross Profit / Sales Revenue
There are other techniques manufacturers implement when managing their inventory. But they’re not exactly formulas. Instead, they are inventory valuation methods, which like the formulas, also give you a clearer understanding of your stock levels and value.
Is a perpetual inventory system FIFO or LIFO?
A perpetual inventory system can use either the first-in, first-out (FIFO) method or the last-in, first-out (LIFO) method to determine the COGS and the value of the remaining inventory.
Here’s how both FIFO and LIFO work in perpetual inventory.
What is FIFO perpetual inventory method?
The FIFO perpetual inventory method is a method of valuing inventory and calculating the COGS in which the oldest items in inventory are assumed to be sold first.
In a FIFO system, the COGS is calculated by taking the cost of the oldest items in inventory and subtracting that amount from the total inventory cost. The value of the remaining inventory is then calculated based on the cost of the most recent items purchased.
The FIFO method is commonly used by businesses that sell perishable goods, as it assumes that the oldest items will be sold first, which is often the case with products with a limited shelf life. It also provides a more accurate representation of the actual COGS, as it considers changes in the cost of goods over time.
What is LIFO perpetual inventory method?
The Last-In, First-Out (LIFO) perpetual inventory method is a system for valuing inventory and calculating the COGS in which the most recently acquired items are assumed to be sold first.
In a LIFO system, the COGS is calculated by taking the most recent items in inventory and subtracting that amount from the total cost of the inventory. The value of the remaining inventory is then calculated based on the cost of the oldest items purchased.
The LIFO method is commonly used by businesses that sell durable goods, as it assumes that the most recent items will be sold first, which is often the case with products with a longer shelf life. It also provides a more accurate representation of the COGS in times of rising prices, as it considers the most recent, higher costs.
LIFO is the method of valuing inventory and calculating the COGS in which the most recently acquired items are assumed to be sold first. It is commonly used by businesses that sell durable goods and provides a more accurate representation of the COGS in times of rising prices.
What is the weighted average cost perpetual inventory method?
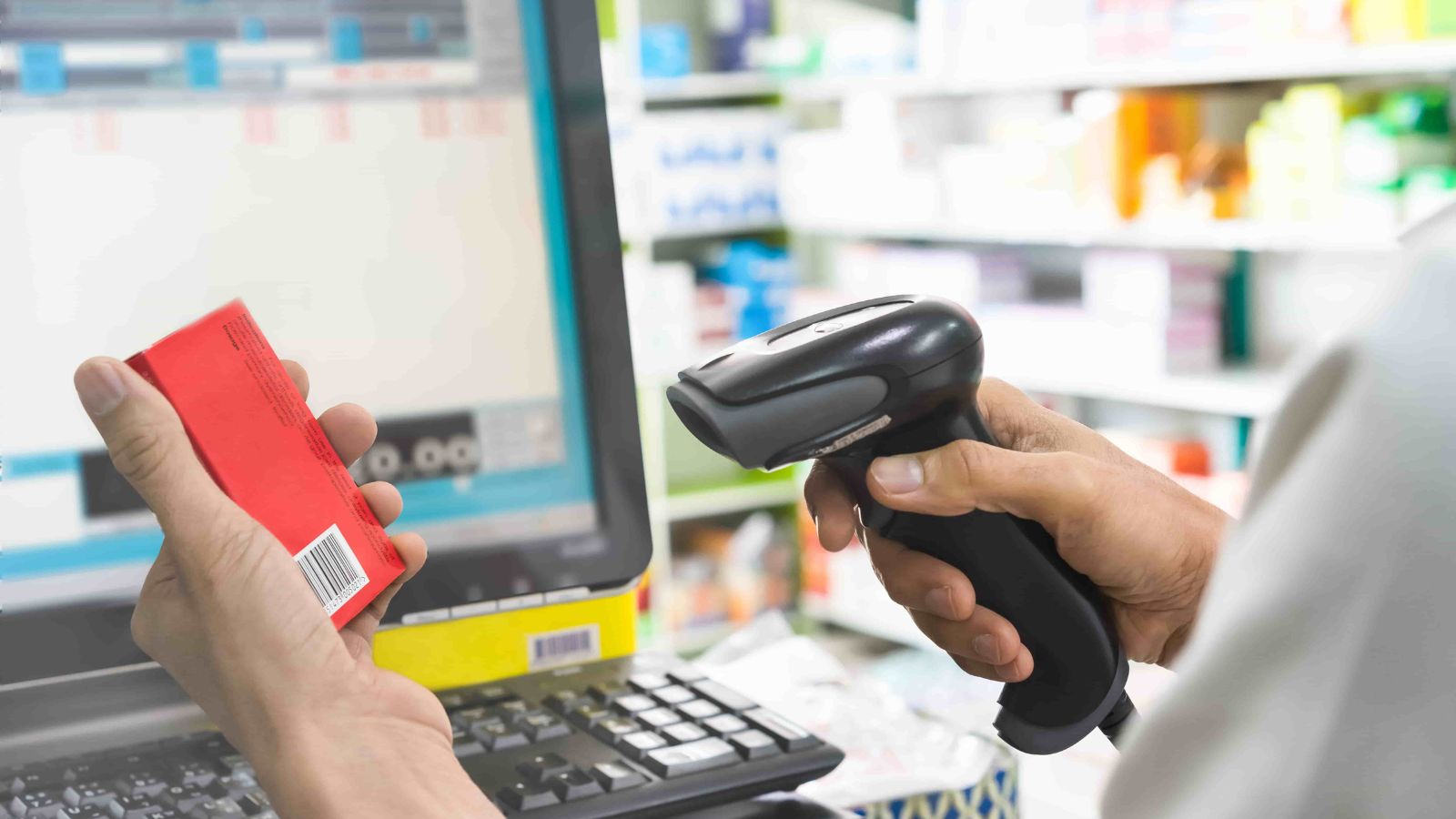
The weighted average cost perpetual inventory method is a technique of valuing inventory and calculating COGS that considers both the quantity and the cost of goods purchased over a certain period.
Under this method, the COGS is calculated by dividing the total cost of all goods purchased during a specific period by the total number of goods purchased. The resulting weighted average cost per unit is then used to value the remaining inventory and calculate the COGS.
The weighted average cost method provides a more accurate representation of the actual COGS, as it considers both the quantity and the cost of goods purchased over a specific period. This method is commonly used by businesses that sell goods with a stable cost, such as non-perishable goods or goods purchased in large quantities.
Examples of perpetual inventory — FIFO, LIFO, and weighted average inventory
FIFO: if a business has 100 units of a product in inventory and the cost per unit varies over time, the COGS for the first 100 units sold would be based on the cost of the oldest 100 units in the inventory, regardless of whether the more recent units cost more or less.
LIFO: if a business has 100 units of a product in inventory and the cost per unit varies over time, the COGS for the first 100 units sold would be based on the cost of the most recent 100 units in the inventory, regardless of whether the older units cost more or less.
Weighted: if a business has purchased 100 units of a product for $5 each and 200 units for $6 each, the weighted average cost per unit would be calculated as follows:
(100 x $5) + (200 x $6) = $1,000 + $1,200 = $2,200
Weighted average cost per unit = $2,200 / (100 + 200) = $2,200 / 300 = $7
Katana cloud inventory management software
Implement real-time inventory management and get complete control over your sales, manufacturing, accounting, shipping, and beyond.
How Katana helps you gain total control over your inventory
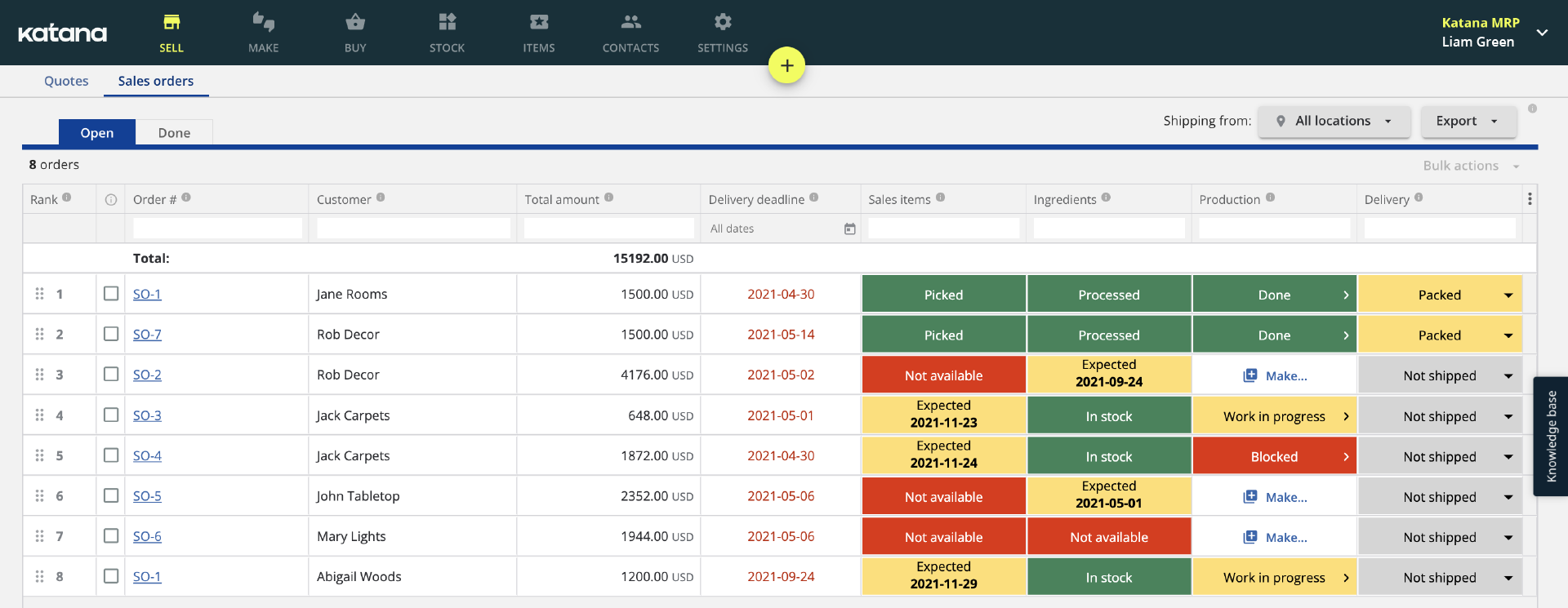
After what probably feels like a very long tangent, perpetual inventory systems are what separates us from the troglodytes (probably).
Just imagine what it was like for cave dwellers in pre-historic times to count their inventory of rocks, “Ug. One. Ug. Two. Ug. Three? Ug. I lost count.” And who can blame them for losing count? There’s a reason you count sheep to fall asleep.
With how far technology has come, there’s no reason to punish yourself, your employees, and your business with this old-world stocktaking method.
Katana cloud inventory software is here to help scaling manufacturers enter a new era in their inventory management. Katana uses the moving average cost (MAC) method and aids any manufacturer regardless of their manufacturing processes — allowing you to get the most current valuation on your inventory levels for each product type.
Katana comes equipped with the following features:
- Real-time master planner — your available raw materials and finished goods are immediately allocated to open orders as soon as they are generated, as Katana tracks your inventory movements in real time
- Live view of inventory and costs — to assist you in understanding your inventory levels after a reporting period, Katana provides a breakdown of manufacturing costs, COGS, and the value of the products still in stock
- Visual and modern interface — quickly browse your entire process, from selling to manufacturing, thanks to the user-friendly interface, giving you a unified perspective of your entire organization
- Integrations — Katana maintains everything in sync and integrates with the top business tools, including QuickBooks Online, Xero, Shopify, and BigCommerce, to name a few. This enables you to manage your company from a single platform
Table of contents
Inventory management guide
More guides from Katana
Get visibility over your sales and stock
Wave goodbye to uncertainty by using Katana Cloud Inventory for total inventory control
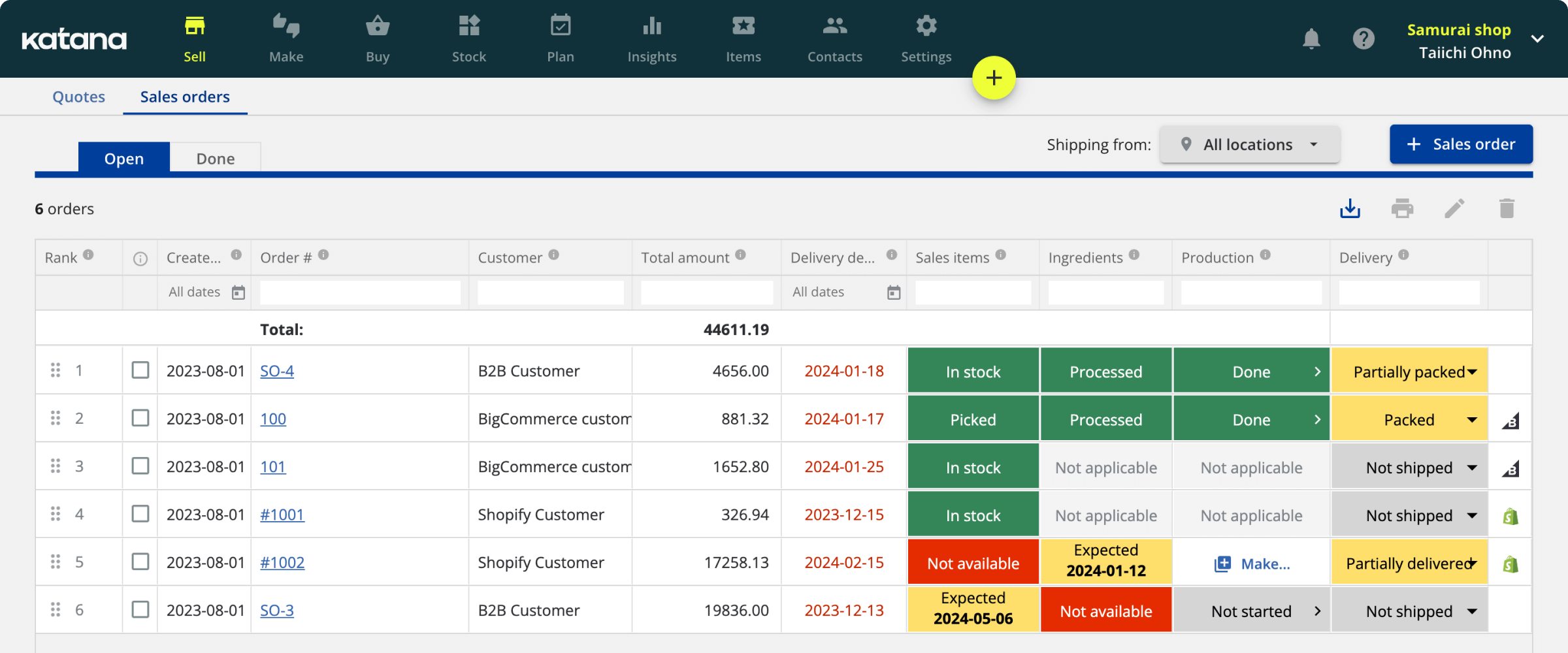