Decoupling inventory: how to keep production moving
Many variables are not under your control when it comes to manufacturing workflows.
A small change in factors such as the supply chain could throw a wrench into the works of your manufacturing business and leave you scrambling for solutions. Building up a decoupling inventory can prevent disruptions and give you enough time to fix the issues. Learn more about decoupling inventory and how it can help you build a resilient business.
Get control over all your different inventory types
Thousands of businesses use Katana cloud inventory software to manage their finished goods, raw inventory and set reorder points to maintain ideal stock levels. See Katana in action.
What is decoupling inventory?
Decoupling inventory effectively decouples (or separates) your business from the supply chain by buffering it from disruptions.
Supply chain issues and machinery breakdowns can be the Achilles heel of just-in-time inventory. Their heavy focus on minimizing inventory on hand can make your business fragile and prone to disruption.
An intuitive solution is to set aside extra raw material and work-in-progress items for some or all stages of your workflow. You could also store equipment and material to fix broken machinery.
For example, let us say you manufacture high-quality bicycles. Your bicycles are fairly complex and require a lot of moving parts. However, for the sake of simplicity, let us say that you require three major sub-parts (subassemblies) to manufacture the bicycles:
- The frames
- The wheels
- The seats
You manufacture the frame and the wheels in-house and easily access the raw material. For your seats however, you depend on an external supplier.
In this case, your business could be throttled by disrupting your access to the seats. A shipment delay or anything going wrong in your supply chain can force you to delay order fulfillment. To manage this risk, you could stock up some seats in your warehouse as a backup. So in case of an unexpected hiccup in your supply, the backup will buy you time to find solutions without interrupting your production. This excess stock of seats that you hold is called your decoupling inventory.
The concept is simple in theory. However, there are plenty of nuances and distinctions to consider before stocking up raw materials for your business.
Advantages of decoupling inventory
- Your business is more resilient against various risk factors
- Supply chain disruptions don’t impact your production adversely
- On-time delivery of your products
- Higher customer loyalty
Disadvantages of decoupling inventory
- Higher overhead to maintain a larger inventory
- Decoupling can be challenging in the case of complex products
The past few years, with their supply chain disruptions and changing geopolitical climates, have forced manufacturing businesses to re-evaluate their JIT production strategies. Increasingly manufacturers are moving away from minimizing the stock they hold and towards shortening their supply chains. Decoupling inventory is an effective tool that can keep your business running in the face of various changes.
Decoupling inventory vs. safety stock
These two are quite similar when it comes to various tools that can be used to build buffers. Although many people use them interchangeably, there is a subtle distinction between them.
Decoupling inventory is used to speak about the stocks you hold to protect yourself against various internal disruptions such as supply issues, machinery breakdown, etc. While safety stock is the excess stock that you hold to protect yourself against changing external variables such as demand fluctuations due to changing customer preferences. These demand fluctuations could end up causing severe disruptions, and this phenomenon is called the bullwhip effect.
So, continuing with our example of bicycle manufacturing, your welding machine breaking down would be an instance of an internal issue. While, a sudden spike in demand for bicycles would be an external factor that could put higher pressure on your production workflow.
Your business needs to be prepared to weather the storm in both cases. In the first case, a solution could be simply having the materials required to fix the machine. The materials that you use in this case would be your decoupling inventory. While in the second case, you could have a buffer of excess bikes stored in your warehouse, which would be your safety stock.
Some subtleties can always be contested. For example, supply chains can be considered external factors, so buffers against changes to this factor could be accounted for with safety stock. However, the key idea is that both the tools have plenty of overlap when it comes to what they help your business achieve – better mitigation of risk factors not under your control.
Decoupling inventory vs. pipeline stock
Modern manufacturing workflows are fairly complex and involve multiple moving parts.
Inevitably, some stock will always be in the pipeline. Be it raw material on its way to your warehouse or finished products on their way to your customers. There will always be some stock in the pipeline. The term used to describe this stock is pipeline stock or pipeline inventory, and as such, it is part and parcel of running a manufacturing business.
Decoupling inventory, however, is optional.
If your business model is based on a make-to-order workflow, in contrast to a make-to-stock workflow, you can run your business without holding any excess stock. A business model like that would just be very risky. Many manufacturing businesses do work without these buffers or safety nets.
The key takeaway is that pipeline stock is an unavoidable artifact of the manufacturing process, and there is plenty of room to optimize it. While decoupling inventory is a choice, you can do without it as well.
Complete and total control of your inventory with Katana
Monitor your item’s move from raw material, WIP, and finished goods inventory. Get complete visibility over your business operations for free.
How cloud software can help with decoupling inventory?
As established earlier, manufacturing workflows can be complex and this makes it tricky to decouple your inventory. There are several factors that you need to weigh when it comes to decoupling inventory.
For instance, if you manufacture food products you cannot stock up on raw materials in excess since they could expire. This would mean that in addition to the manufacturing overheads and handling your business would also have to deal with the waste created due to poor planning. Clearly, estimating how much stock to hold can be challenging.
If you manufacture sophisticated products, like healthcare devices for instance, then the complexity involved in planning the buffers goes up significantly. A cloud solution can help you tame the complexity involved in cases like these.
A cloud inventory platform, like Katana, can help you create multi-level bills of materials (BOM), which means you can create products that are composed of subassemblies. Using the bill of materials feature, you can set up your subassemblies in Katana as a product. Once you have documented the raw materials and components needed to create the subassembly, you can save the configuration. You can then use this subassembly within the BOM structure of your finished goods.
Katana also comes with features such as live inventory management, and purchase order management, that can help you track all your inventory (decoupled and otherwise) and also keep an eye on your inventory pipeline.
Get a demo and find out how thousands of manufacturers use Katana to grow their businesses and manage the complexities of manufacturing.
Table of contents
Inventory management guide
More on inventory management
Get visibility over your sales and stock
Wave goodbye to uncertainty by using Katana Cloud Inventory for total inventory control
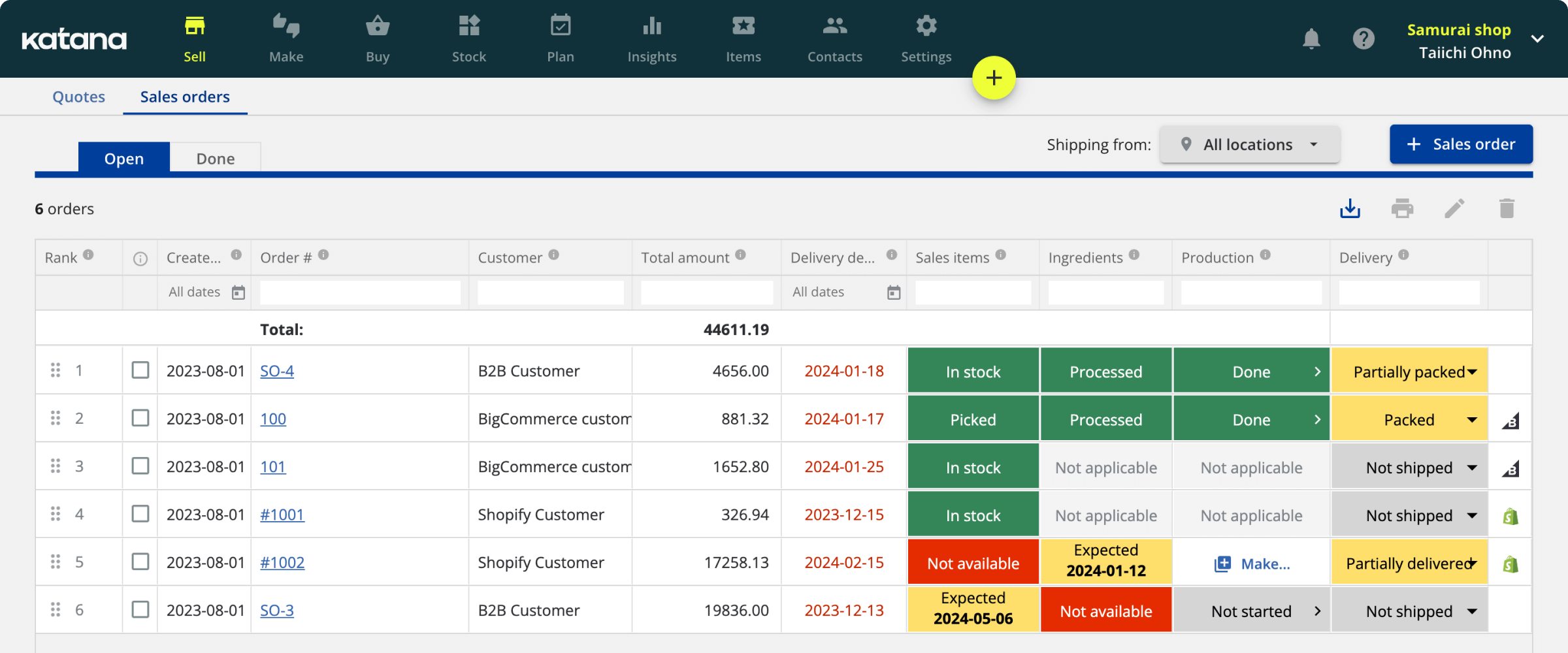