Proper stock replenishment to prevent stockouts
Ambitious manufacturers know that stock replenishment is one of the areas which can make a huge difference in scaling their business. For one, it can just be incredibly time-consuming to manage correctly. Thankfully, there is a way.
Suppose you’re at the coffee machine, ready for a caffeine top-up. Wouldn’t it be great if the coffee cup was always there, filled to the brim?
Well, it’s a dream most manufacturers have with their coffee as much as they do with their stock replenishment. Dreaming their stock room is always in the process of being refreshed and filled for the perfect flow of consumption.
Now, as with most things in life, there’s a good way of doing replenishment of stock, and there’s a bad way. And to make sure you’re managing your stock replenishment properly, you need to take your inventory management seriously. Otherwise, you’ll come up against stockouts and miserable customers or end up ordering too much stock and unnecessarily increasing your carrying costs.
Experts agree that extra inventory costs 18 – 35% of an item’s value for a year — a staggering number to consider. That’s why we’ve come up with this mini guide to make sure you stay on the right path to replenishing stock success.
What is stock replenishment?
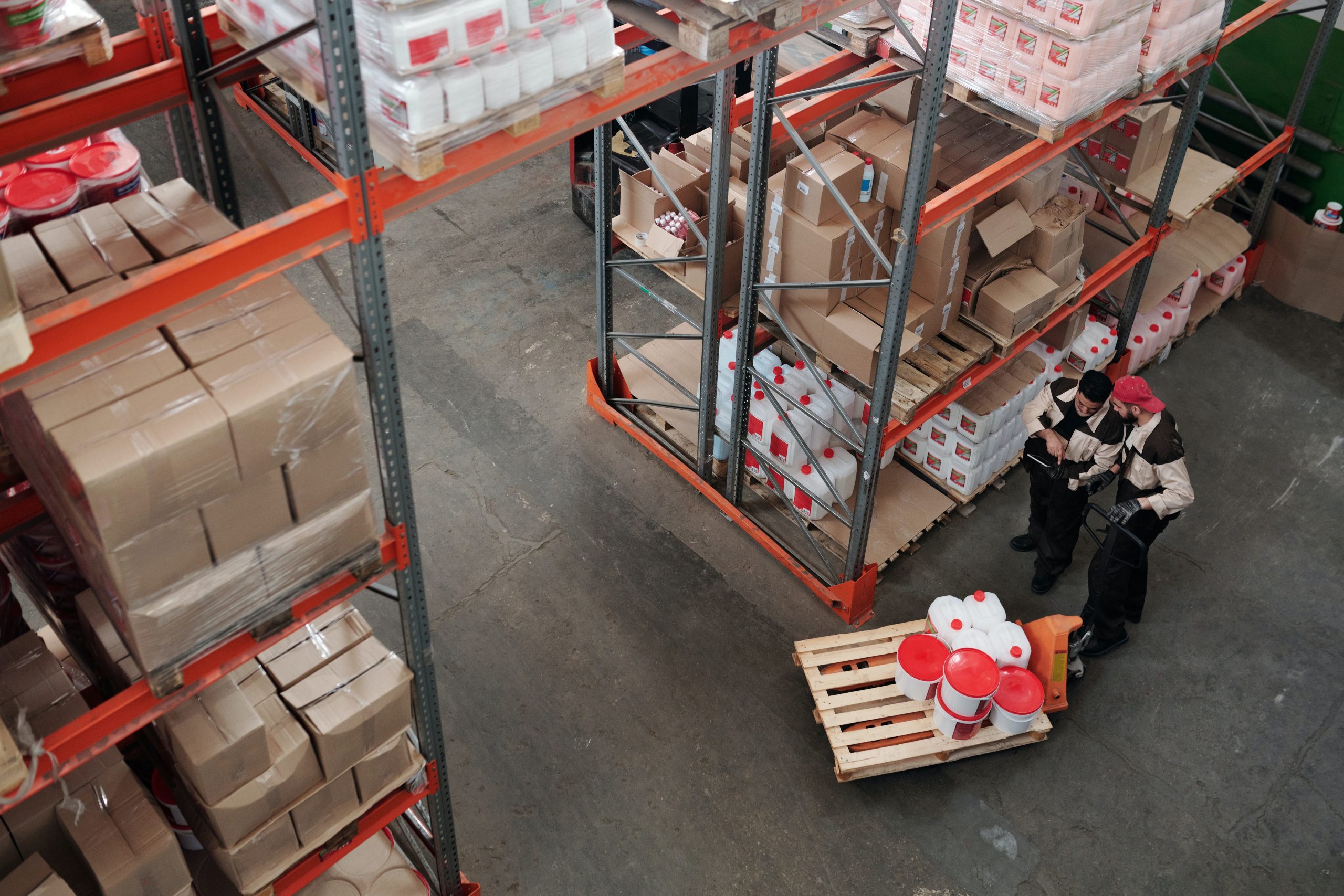
Stock replenishment is the process of reordering materials to meet the demand for your manufacturing and sales orders. That means ensuring you never run out of stock and can deliver to your customers on time.
Manufacturers have been battling inventory levels with spreadsheets and stock replenishment systems for a long time. Thankfully, the dawn of best inventory management software has automated many of the processes enough to allow manufacturers to give up the ancient Excel ways and focus on their products and customers instead.
It’s easy enough to say that stock replenishment is ordering stock to meet demand. But to really gain an understanding, we have to step back and see what that means in terms of the supply chain. Ultimately, your capabilities of keeping stock at optimal levels are affected by many external factors. Your suppliers are as paramount to the process as your own principles.
So yes, stock replenishment is about holding an amount of stock that doesn’t drastically increase your carrying costs while also making sure you never have stockouts. However, it also ensures you have an entire overview of your inventory, from supplier relations to purchase planning and even production scheduling.
You need to build yourself a landscape that covers all of these bases so that your inventory replenishment process becomes part of the natural order of your manufacturing business.
Now thankfully, you won’t be on your own with all this. Modern production management software can automate this for you. It makes sure that you know exactly when to purchase more materials while also ensuring you have materials available for your current manufacturing and sales orders.
But before we get to that, let’s see how we can build the foundations of inventory replenishment right off the bat.
Why is stock replenishment important?
Stock replenishment is a crucial part of any manufacturing business. It’s vital for companies that can’t afford stockouts or excess inventory. An efficient inventory management process reduces the risk of these problems and increases the chances of success.
When done correctly, stock replenishment helps improve customer satisfaction by ensuring that orders are fulfilled on time — that customers never have to wait too long for their orders.
Additionally, it keeps your inventory costs in check as you don’t need to carry large amounts of stock just to make sure you can meet demand. By having just enough supply, you will be able to reduce waste while at the same time making sure you have enough stock to meet customer demands.
Essentially, stock replenishment is key to ensuring smooth and efficient manufacturing processes while simultaneously reducing costs and increasing customer satisfaction.
What are the 3 types of replenishment?
The three main types of inventory replenishment are:
- Reorder point replenishment — This type of replenishment uses a predetermined reorder point based on past sales or forecasts. When the stock level reaches the reorder point, an order is placed with the supplier for additional stock
- Demand replenishment — This replenishment method is based on current and future customer demand. With this method, you only order enough to fill the forecasted demand. It is still essential to have some safety stock
- Periodic replenishment — This type of replenishment occurs when a certain amount of stock is ordered at predetermined intervals, such as weekly, monthly, or quarterly. This method works best for businesses that use seasonal demand cycles and need to adjust their stock levels accordingly
Understanding these different types of replenishment can help you pick out the most suitable strategy for your business, helping you save time, money, and resources.
With the right replenishment method in place, you can be sure that your business is always well stocked with just enough materials to meet customer demands. Proper stock replenishment is essential for any successful manufacturing business — it’s the key to staying competitive in today’s market.
Methods of stock replenishment
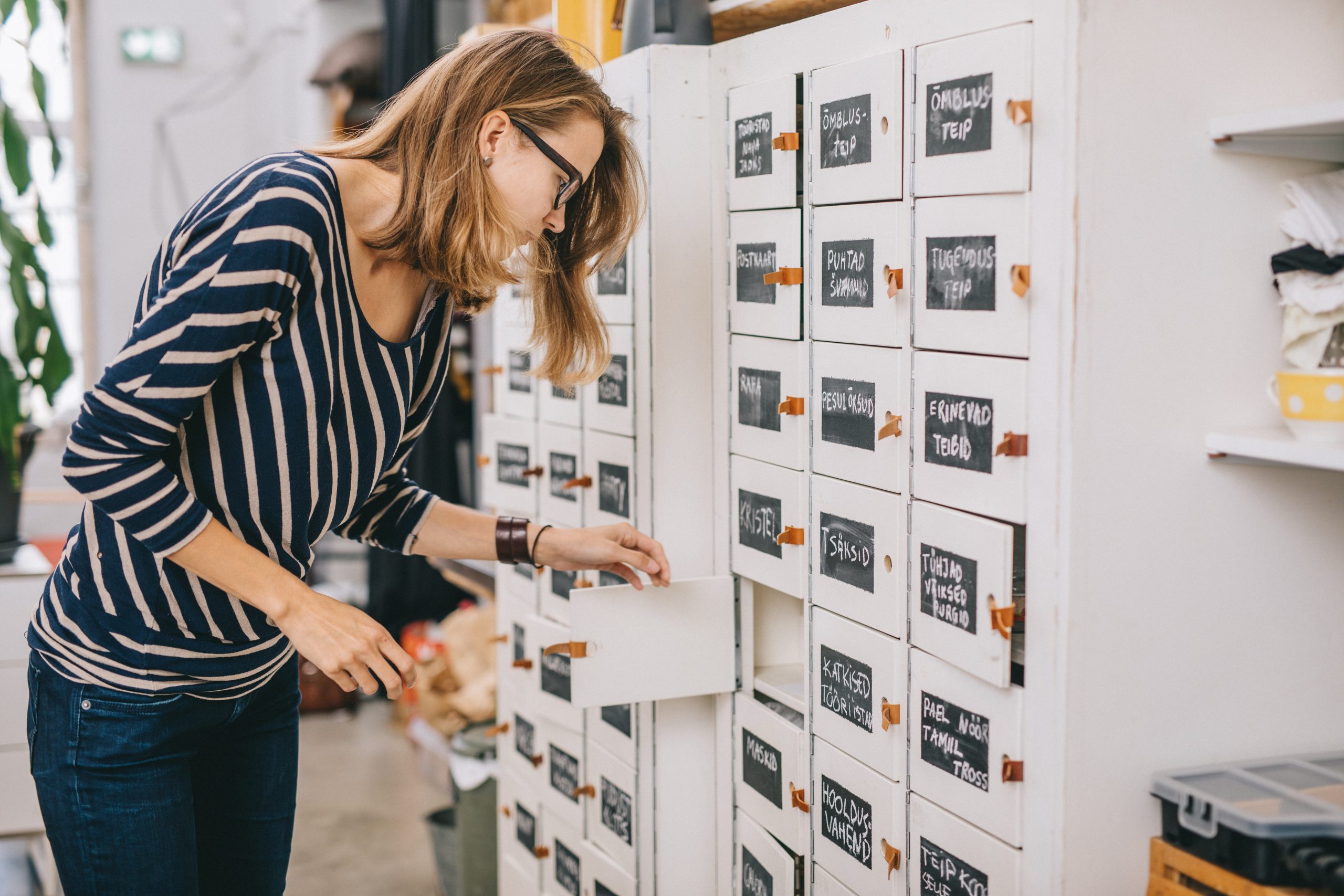
So we know that there are plenty of stock replenishment methods to follow, which is why we have decided to break it down into the main building blocks. These methods of stock replenishment are not necessarily in order of importance, but here is what it boils down to:
- Setting safety stock
- Setting reorder points
- Supplier relations
- Demand planning
- Production planning
Covering these bases will give you a complete outline of when you need to replenish stock.
1. Setting safety stock
Stockouts are not always the most predictable crisis for your manufacturing business.
They can occur due to fluctuating manufacturing lead times, supplier changes, or even a sudden spike in customer demand. You can, of course, try to plan to avoid these situations, but some moments are just simply out of your control.
That’s why it’s always important to have safety stock for your materials and finished products.
Safety stock is the quantity of a particular item that is always there in the background to avoid dreaded stockouts. It’s an emergency fund of inventory that guarantees your customers will always be able to get their products on time.
This is the basic stock replenishment formula you can apply to get your safety stock numbers:
Safety stock = (Max daily usage x max lead time in days) – (avg daily usage x avg lead time in days)
2. Setting reorder points
So, when do you want to be triggering your replenishment orders? Knowing this is a task for your reorder point.
A reorder point is a threshold for each inventory item you do not want to go below, just above your safety stock. The difference between reorder points and safety stock is that your reorder point is designed to make sure you don’t have to dip into that emergency fund of safety stock.
You can think of reorder points as your early warning system while the safety stock is your final line of defense. Reorder point is a metric that will tell you two things:
- When to order more materials from your supplier
- When to manufacture more products from your current raw materials inventory
The reorder point formula looks like this:
Reorder point = (Avg daily usage x avg lead time in days) + safety stock
Once you have your safety stock and reorder points worked out, you know that you should replenish stock every time quantities hit this level.
3. Supplier relations
Now there’s plenty you can do to ensure safety stock is never reached. But not everything is in your control when it comes to replenishment.
Suppliers are the ones who deliver your materials, and not all are created equal. You want to work with suppliers that are reliable with deliveries, offer a good price, and have the best quality materials. The last approach you want to take is a reactive one, where changes only happen when something goes wrong.
4. Demand planning
On some level, your stock replenishment implies a certain level of demand planning. There’s no point in setting safety stock and reorder point levels unless you also understand the context of your particular industry.
You want to look into seasonal spikes in demand in advance so that you can adjust your stock levels accordingly.
Even a simple search on Google Trends for your product keywords will indicate where demand may be moving throughout the year.
5. Production planning
It’s just as important to be aware of your production line when it comes to stock replenishment as it does to your material purchasing.
Because knowing which materials are currently used in manufacturing will let you know how much you really have in the stock room. This way, you can keep an accurate and up-to-date inventory record without relying on constant stocktakes. Good production scheduling software can make a huge difference by simplifying perpetual inventory.
Stock replenishment tips
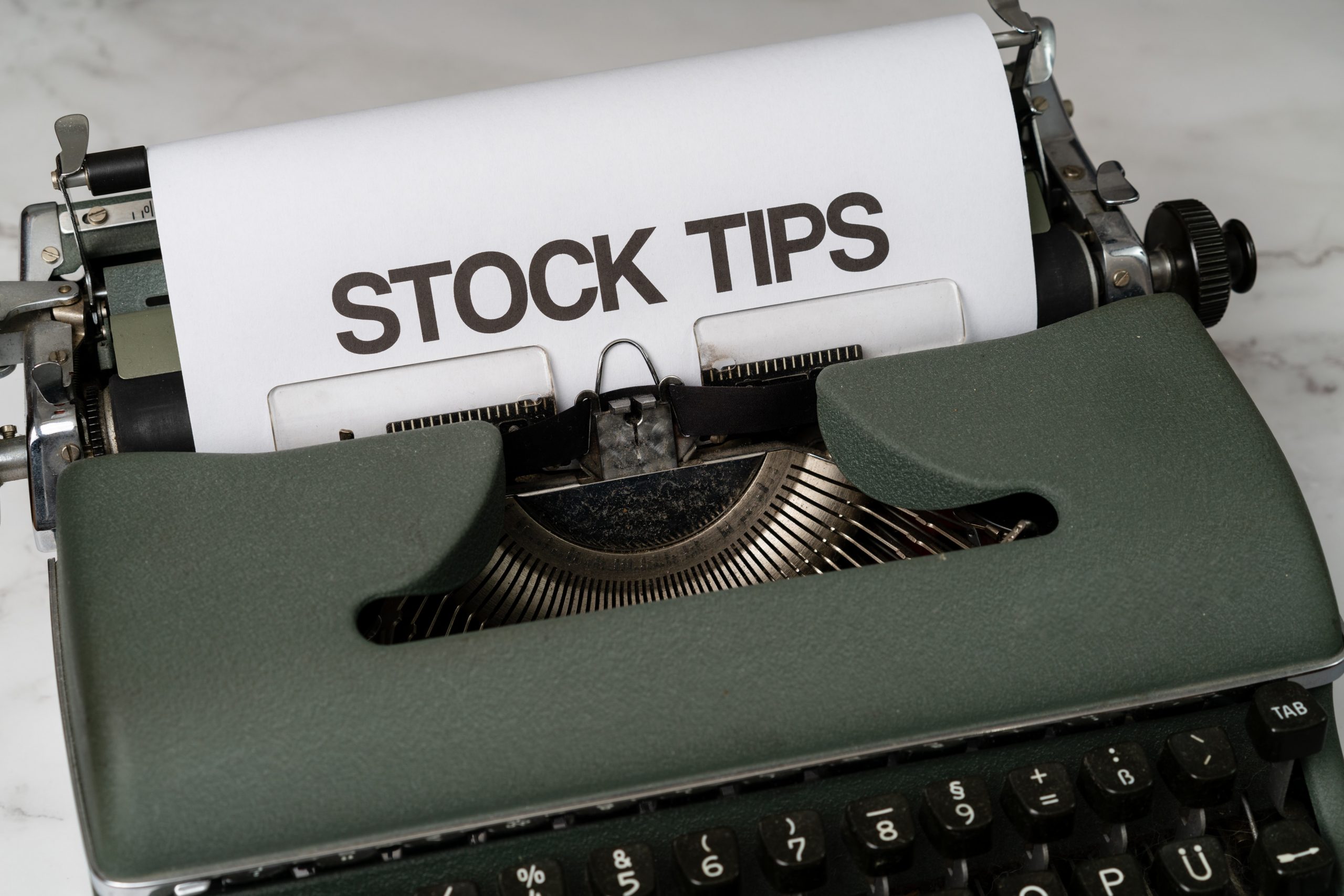
To make it easier to manage stock replenishment, here are a few tips you can use:
- Make sure you are aware of current and future trends in your product industry when it comes to demand forecasting
- Always have a safety stock level to ensure your customers will always be able to get their products on time
- Regularly set reorder points that keep track of inventory levels to avoid being forced into using the emergency fund of safety stock
- Establish strong relationships with suppliers that are reliable and offer materials with good quality and price
- Use a perpetual inventory system with production scheduling software to maintain an up-to-date record of available raw materials and prevent overlap or shortages during manufacturing orders
Improve stock replenishment with Katana
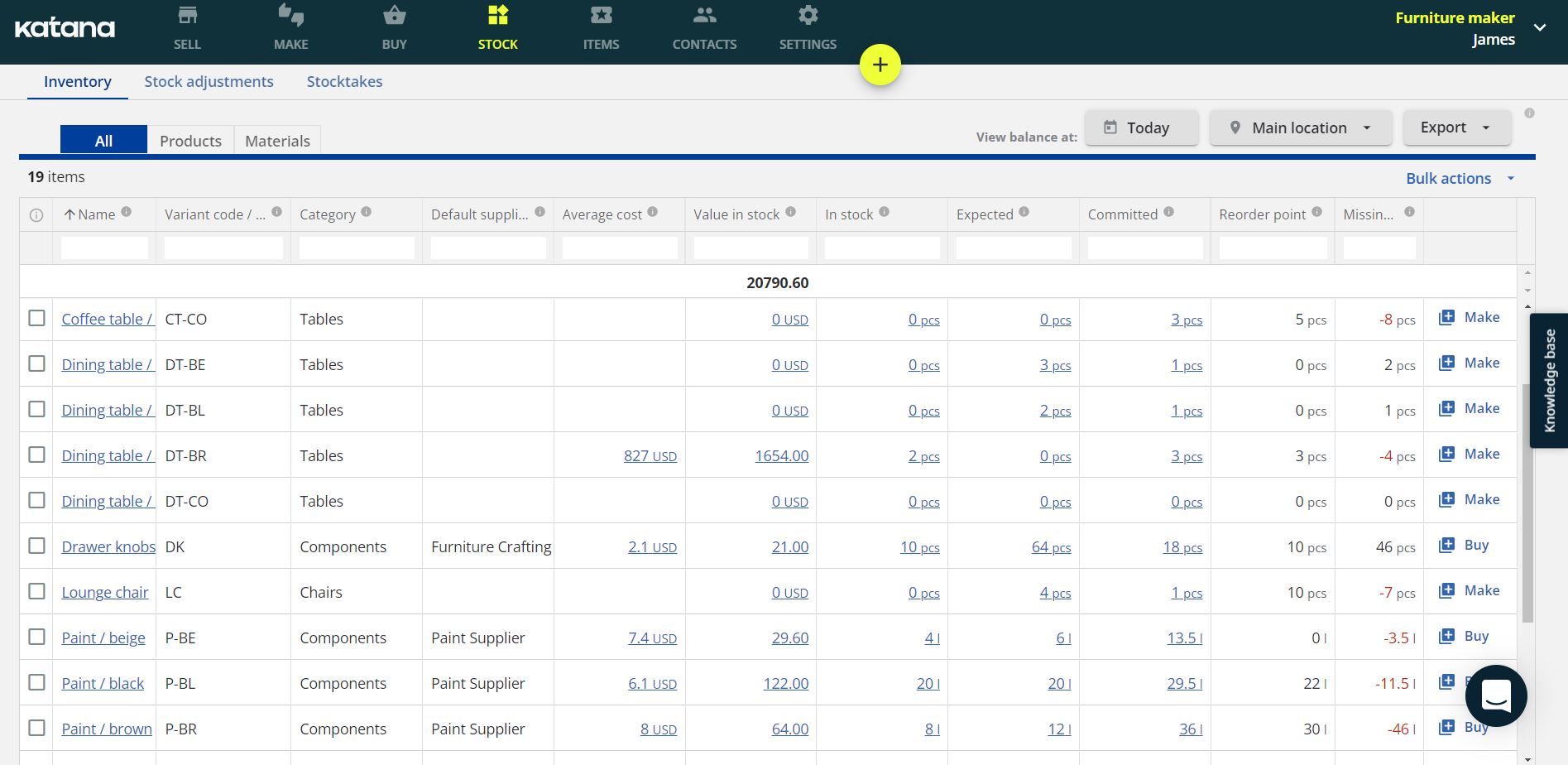
Katana gives you an overview of your stock replenishment by letting you know exactly how far off the optimal inventory levels you are for each item.
You can adjust the reorder points for each item so you know exactly when to make a purchase. The beauty of stock replenishment is that you can ensure you are not spending any more than you have to on excess stock while making sure your customers always get their products on time.
Having elements like reorder points, safety stock, and good supplier relations in place allows you to know exactly when to make those purchasing orders.
Katana automates your inventory management so that you can visually see when your stock goes below reorder points and lets you know how your material availability looks for your sales and manufacturing orders. That’s because raw materials are automatically allocated to orders, so your inventory is always up to date. If you don’t have enough materials for an order, Katana estimates the arrival time, so you can plan accordingly.
Want to see Katana in action?
Book a demo to get all your questions answered regarding Katana’s features, integrations, pricing, and more.
And even cooler than that is the ability to prioritize orders with a simple drag-and-drop feature. Suppose you have a VIP order that needs to be fulfilled fast. You can simply drag it to the top of the list, and that’s it — your production schedule updates and items are reallocated automatically.
The purpose here is that having your stock replenishment automated will mean you can spend less time putting out fires and more time growing your business.
Katana gives you back the time to focus on the vital and often undervalued cogs of your growing manufacturing business, like sales, marketing, product development, and customer experience. Besides its robust inventory management features, Katana also offers:
- On-demand access to your manufacturing costs
- Finished goods and material inventory
- Use as a production scheduling software
- Manufacturing floor-level control
- Sync accounting with your QuickBooks Online and Xero
- Integrate with Shopify, Woocommerce, BigCommerce, and other e-commerce channels
- Plan your material purchasing efficiently
- Ditch inefficient excel spreadsheets forever
- Keep your entire business workflow on a single platform
The takeaway here is that stock replenishment is only one piece of the maddening puzzle that is manufacturing. But ensuring that your inventory levels are always optimal will go a long way to giving you the time you need to focus on growing your business. Like having your coffee constantly balmy and filled to the brim, you’ll be a lot more focused and with one less burden on your mind.
Table of contents
Inventory management guide
More on inventory management
Get visibility over your sales and stock
Wave goodbye to uncertainty by using Katana Cloud Inventory for total inventory control
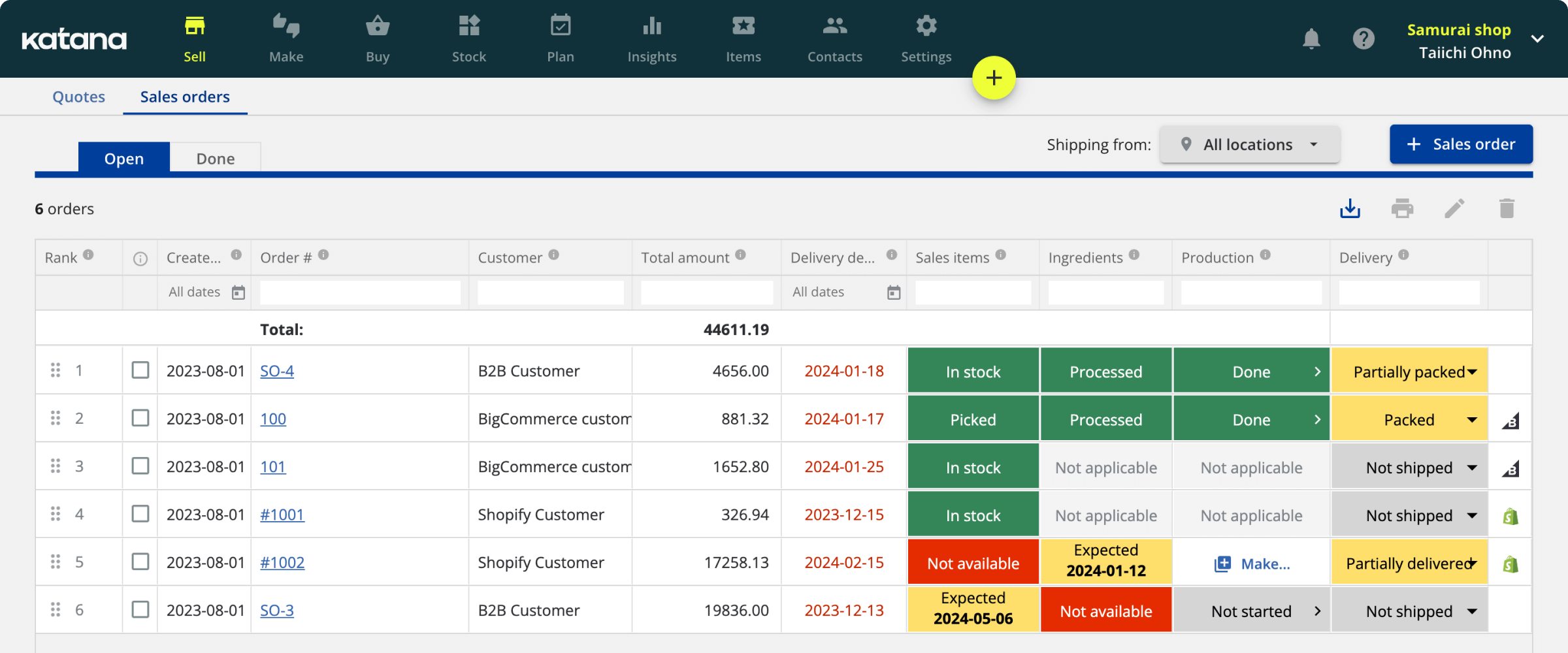