Negative inventory: Get your stock back into positive
Many manufacturers tell you that negative inventory happens often enough, so you may as well embrace it. However, the unfortunate truth is that it’s a sign of bad management. That’s why we’ve looked into negative inventory and how to identify and remove it from your processes.
Regardless of company size, manufacturers need to manage their:
- Administration
- Finances
- Resources
- Production operations
- Sales
- Supply chain
With so many processes to follow, they can’t afford to make any mistakes and risk errors while also trying to meet their production and sales deadlines. This pressure to meet deadlines can lead to mistakes, such as going into negative inventory.
Manufacturers often take a reactive approach and only try to correct negative inventory once it’s brought to their attention instead of stopping the problem from happening in the first place.
However, the longer you put off dealing with your negative inventory, the longer you will be making business decisions based on incorrect information. Negative inventory left unchecked will lead to issues varying in severity, from a minor inconvenience to a problem that stops your entire production.
According to some studies, at any one time, 60% of an inventory record is likely to be wrong and, once corrected, can lead to a 4-8% increase in sales growth.
One of the reasons many manufacturers choose to deal with these problems when they arise is the difficulty of determining what type of negative inventory your business is carrying.
But have no fear! We’ve looked into the problem of negative inventory and put together an article about how you can identify and address it.
What is negative inventory?
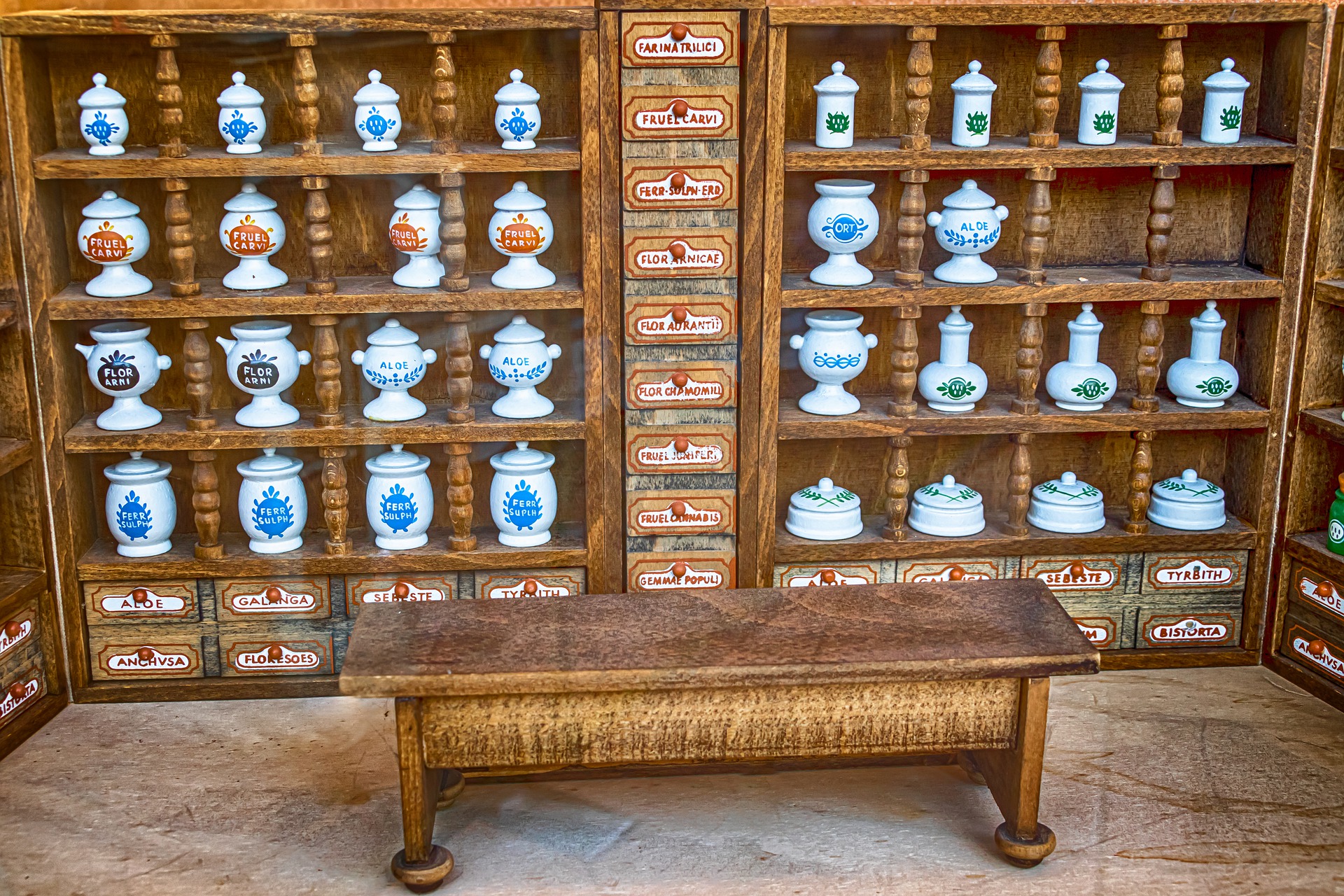
Negative inventory is when a manufacturer’s inventory count suggests that inventory is below zero.
There could be several reasons for negative stock.
Regardless of why, it’s a widespread problem in the manufacturing industry, and some companies even use it as an actual business practice. However, by embracing negative stock, you’re in danger of creating more significant problems for your business, mainly because you’ll make unnecessary decisions, such as ordering more raw materials or starting production, due to inaccurate information.
Ultimately, negative inventory is a sign of poor management when processing sales and manufacturing orders, not a necessary occurrence that manufacturers must face. And if you continue to allow the negative stock to generate in your inventory, you will always be risking:
- Selling items to customers that you don’t have in stock
- Performing a stock transfer with insufficient inventory
- Ordering more materials even though necessary materials are already in production
Knowing the issues is one thing, but the best way to avoid negative inventory is to be proactive and identify what makes negative stock occur.
How does negative inventory occur?
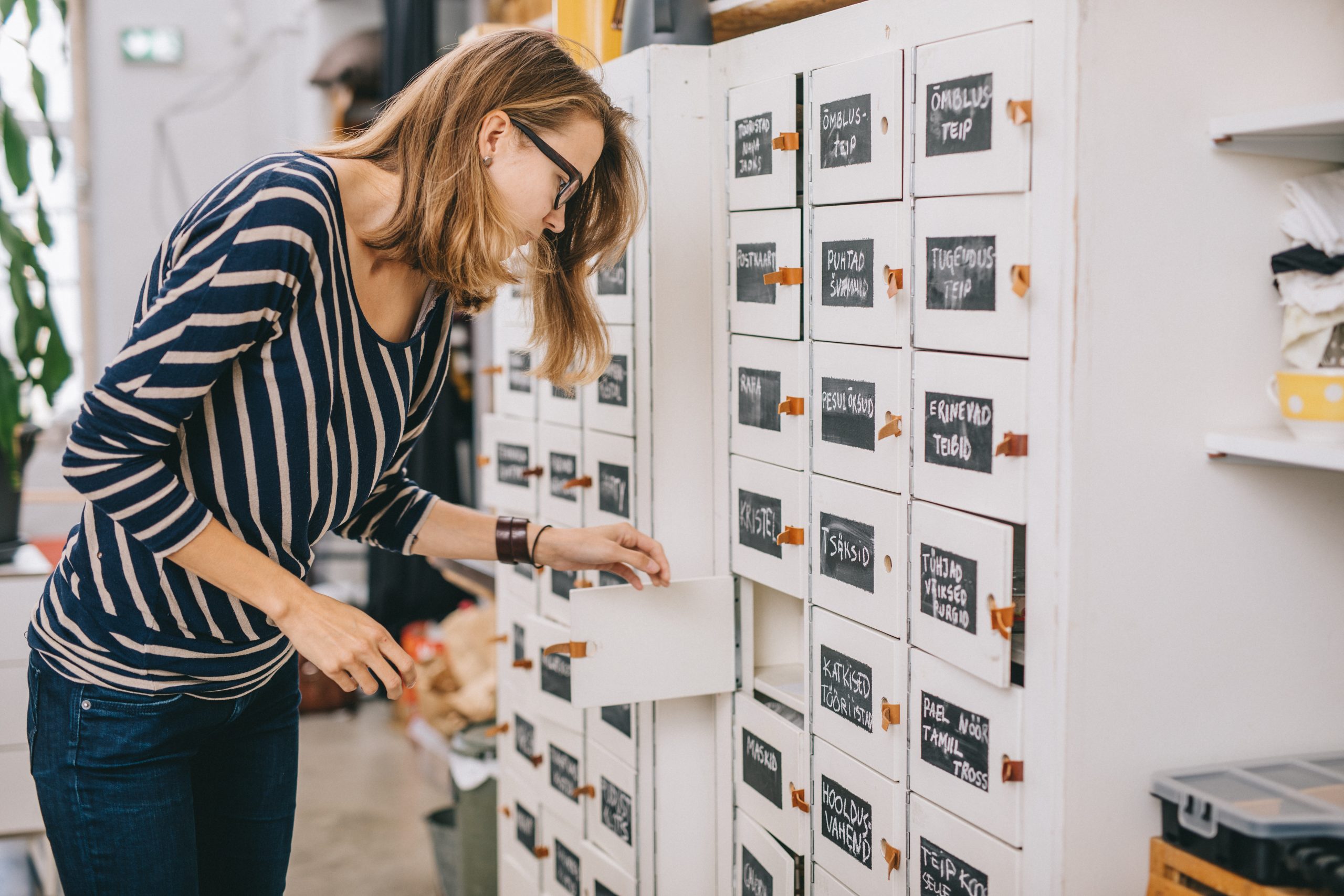
Now that we’ve looked into what is negative inventory, let’s explore how can stock go negative.
Timing
This is probably the most common occurrence when looking into what is negative inventory. An example of a timing issue could be that a customer places an order for a product that’s out of stock, but you go ahead and mark the order as shipped because you know that production for the product will be wrapping up soon.
This issue is probably the easiest to fix because you can make the necessary inventory adjustments once production is complete.
Production
During manufacturing, you need to consider byproducts, scrap amounts, production statistics, and batch tracking. Misunderstanding your manufacturing orders or accidentally creating a duplicate can lead to manufacturing either not enough or too many products.
Inventory at multiple locations
When holding inventory in multiple locations, mistakes like recording a sale from the wrong store can happen. This can make it looks like warehouse A is missing 200 items, while warehouse B has 200 more items than it needs.
Item-level negative stock
Backflushing is the process of generating and completing a manufacturing order (MO) after a batch production has finished so you can update your current inventory levels. Alternatively, an item-level negative stock might appear if there’s a product that you want to make to order (MTO) only when the demand is there.
These are the ways you can end up with negative inventory levels. Now, let’s see how to adjust negative stock and correct these mistakes.
How to fix negative inventory?
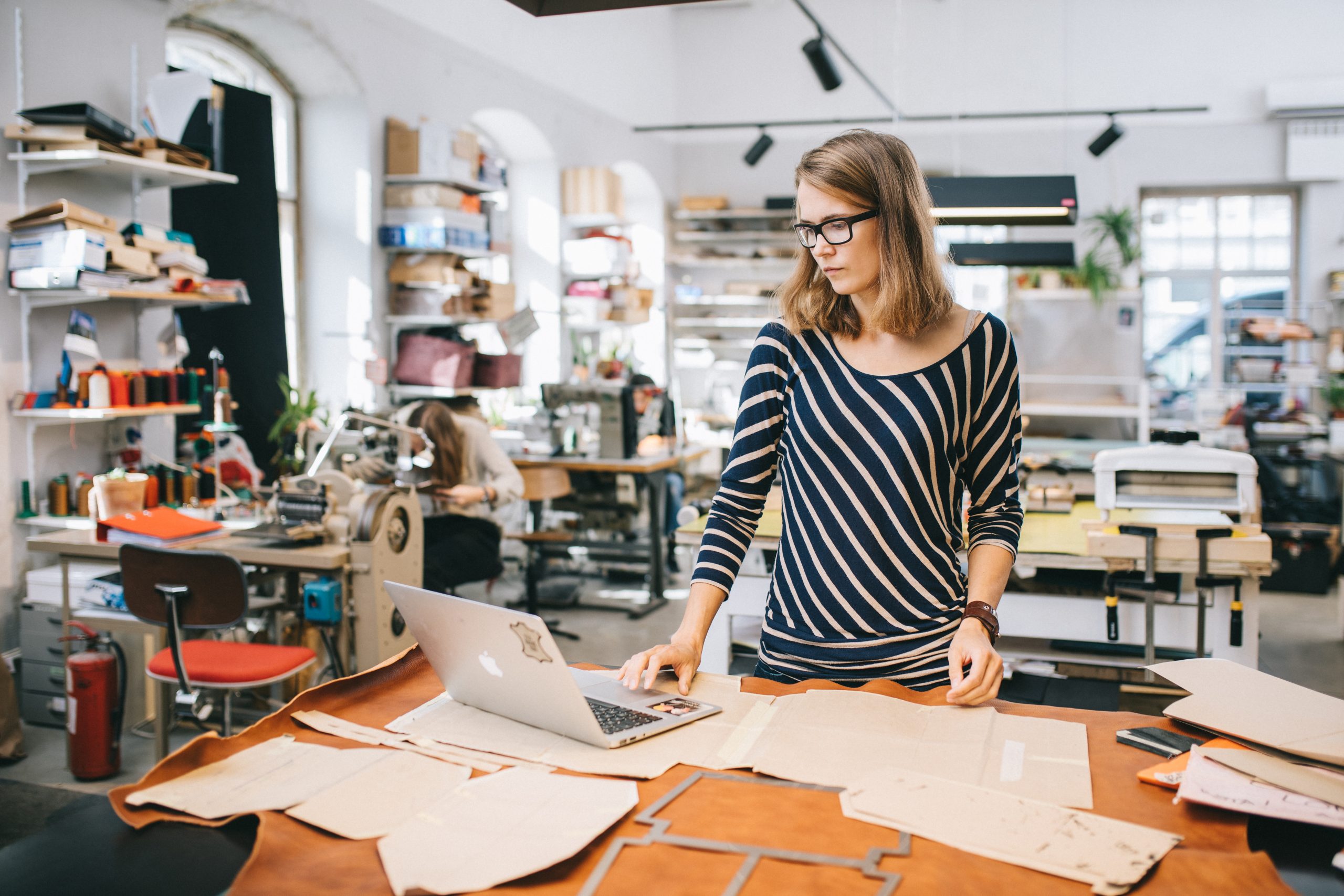
Considering how easily negative stock can form, you’ll be happy to learn that making a negative inventory adjustment is pretty straightforward. Especially when you know what you’re looking for. All you need to do is check your inventory management software reports and locate which products or materials display stock levels below zero.
From here, you can investigate your recent transactions to determine what led to the negative inventory appearing and what type of negative inventory it is.
However, the corrections you’ll make all depend on the type of negative inventory you’ve recorded:
- Time — When correcting, such as marking a product as shipped before production has finished, it’s important not to overstate your amount and remember that missing inventory is still in your stock
- Location — If you made an error while recording a stock transfer, such as inputting the wrong values, the inventory might be at the correct location. It just needs to be accounted for accordingly
- Item-level negative stock — This could be a serious one as it could indicate that there’s a problem with your manufacturing process. You’ll need to identify why your products or materials are coming in as negative stock during production
What are the consequences of not fixing negative inventory?
- Your cost of goods sold (COGS) will be incorrect, giving you improper profits and losses
- Your company capital consists of your current assets minus your current liabilities, meaning if your inventory goes down on the income statement, the working capital will go up
- Mistakes in your accounts payable (AP)
- Bills for your inventory purchases could show up on your income and expense reports
- Incorrect inventory amount on your balance sheet
- Your cash-basis balance sheet will be out of balance
- Your vendor reports will have errors
But, as they say in football (the American one, of course), the best defense is a strong offense. And the same could easily be said about tackling negative inventory. Your best bet to avoid negative inventory is to improve your management practices and implement good cloud inventory software.
Let’s explore what features should a good cloud inventory software have.
Eliminate negative inventory with cloud inventory software
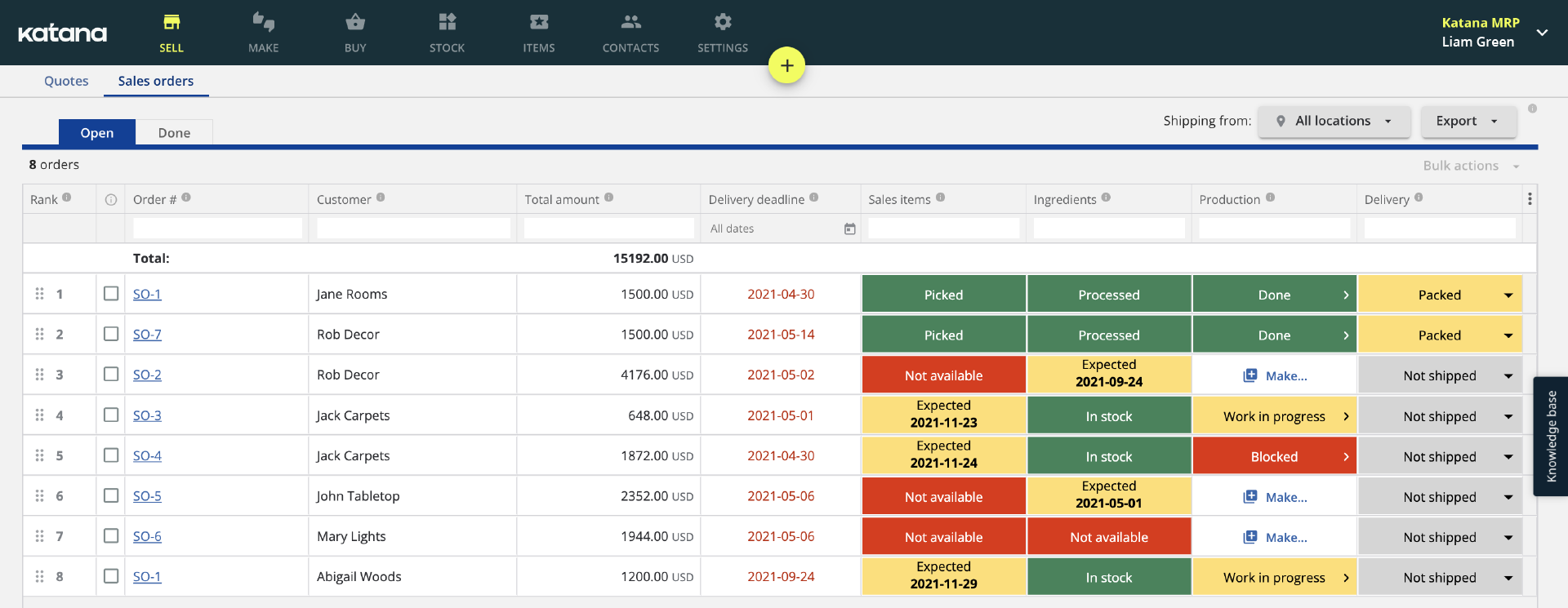
Katana’s cloud inventory platform is built for manufacturers to help them get control over their:
- Manufacturing processes
- Inventory
- Sales
- Supply chain
Check out the video below to see how you can easily fix negative stock in Katana.
But let’s see what other features Katana has that help to make your life easier as a manufacturer.
Real-time master planning
Katana has a unique master planner that tracks your inventory transactions automatically and in real time, giving you an accurate update of your stock levels immediately.
Suppose you create a manufacturing order (MO). Katana will autonomously allocate available material to the open MO, so you immediately know if you have enough resources to begin production or need to order more materials.
Reorder points
You can set a reorder point, and Katana will highlight any products or materials starting to run low. In addition, you can also have safety stock for these unforeseen circumstances, like when materials don’t arrive on time.
Multilocation inventory management
With Katana, you can improve your multilocation inventory management, even if you’re using contract manufacturing. This feature allows you to monitor your inventory levels, regardless of where you store them, and perform stock transfers for products moving between locations.
Remember that this could lead to negative inventory if you make a mistake, so be vigilant when sending and receiving stock.
Centralized sales channels
Many direct-to-consumer (D2C) manufacturers sell from different channels, from brick-and-mortar to e-commerce stores. Katana provides you with a single source of truth so that you can monitor all your channels from one intuitive platform. This includes integrating and synchronizing your favorite e-commerce platforms, like Shopify or WooCommerce, allowing you to manage your sales all from one place.
Integration with accounting software
You can also integrate your accounting software. This is an important feature when it comes to tracking negative inventory. Whether you need to fix negative inventory in QuickBooks Online or Xero, Katana integrates seamlessly with both, making it easy to push all your invoices and bills to your accounting software.
All the tools above can help you avoid generating negative stock and optimize your business by giving you the features to implement lean inventory techniques into your business.
What’s next?
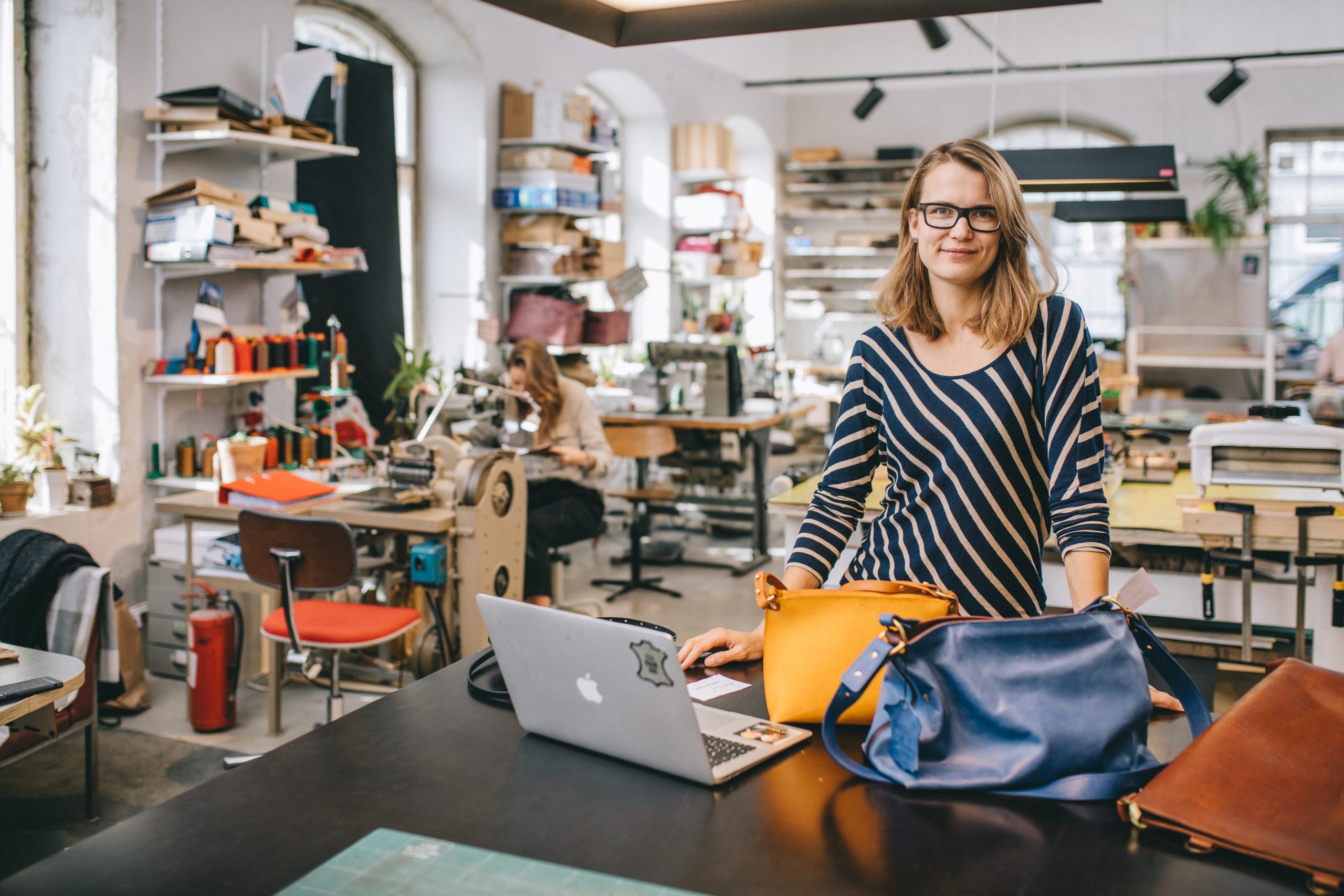
Negative inventory has the potential to cause a lot of issues. But you can nip it in the bud by identifying negative stock as a problem and taking the necessary steps to remove this unwelcome guest from your processes.
How negative inventory will appear on your inventory management software will depend on the platform you’re using. That’s why it’s best to get set up with one that has live updates so you can easily stay on top of your inventory’s movement.
Katana’s cloud inventory platform can provide you with all these convenient features and more. Request a demo and see how Katana can optimize your business processes and help you get rid of that negative stock.
Table of contents
Inventory management guide
More on inventory management
Get visibility over your sales and stock
Wave goodbye to uncertainty by using Katana Cloud Inventory for total inventory control
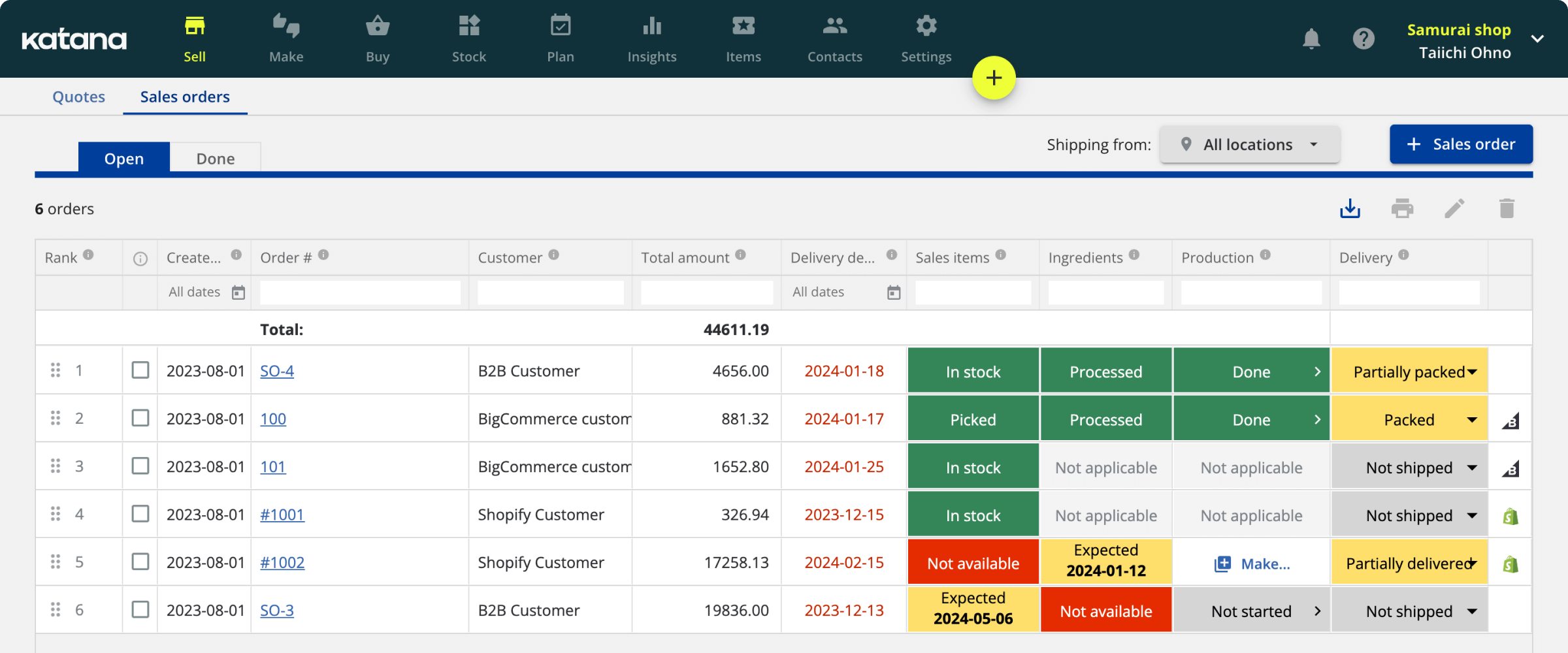