Lean inventory — trimming the fat from your manufacturing
There’s nothing better than a spring clean.
Just getting your home spick-and-span, organized to a tee, from rearranging your cutlery draw to alphabetizing your bookshelf, and then putting your feet up knowing you can relax.
It might not seem like a big deal. But you’ll notice that when you take the time to carefully and logically store items, you’ll save time and energy completing a task — even if that task is making some food or reading a book.
And a factory floor is no different.
That’s why in this article, we’re going to explore lean inventory, the benefits of using the method, and finding the right software to help you bring it all together.
What is lean inventory management?
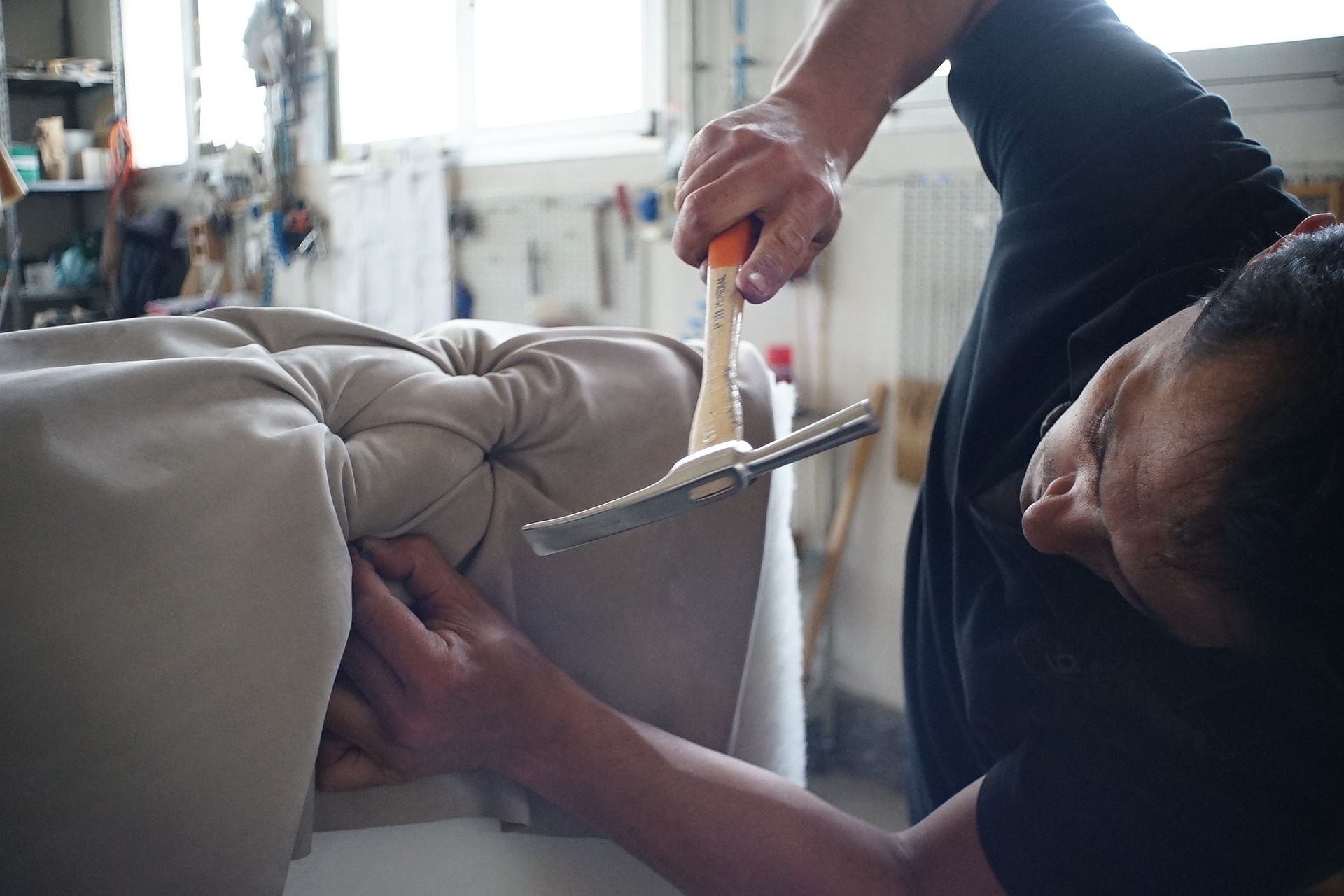
Lean inventory is the process of increasing the value of a company’s stock by identifying and eliminating any waste when handling materials and managing labor and time through the continuous improvement of manufacturing processes. Before manufacturers used lean inventory management, they usually manufactured their goods based on demand planning (or even built and stocked what they believed the customer might want).
However, with lean inventory, the manufacturer identifies and eliminates excess inventory and only stores what they need in a specific time frame.
The practice of storing lean stock originated in Japan, with the simple aim of eliminating ‘Muda’ (for example, eliminating bottlenecks or reducing carrying costs) from the manufacturing process to increase the value of the products produced.
It was famously adopted by Toyota Motor Corporation, which switched to a make-to-order approach and continuously analyzed its production lines to help the company survive a post-war Japanese economy.
Lean manufacturing inventory management can be achieved by:
- Redesigning routing manufacturing
- Removing unnecessary processes from manufacturing
- Rethinking how to keep stock
And that’s the basics to what is lean theory in inventory management. However, the tactic stems from five principles, but what are these lean inventory principles?
Implement lean techniques with Katana
Book a demo with Katana to manage your operations with a real-time inventory system that will help you take your business to the next level.
What are the 5 elements of lean?
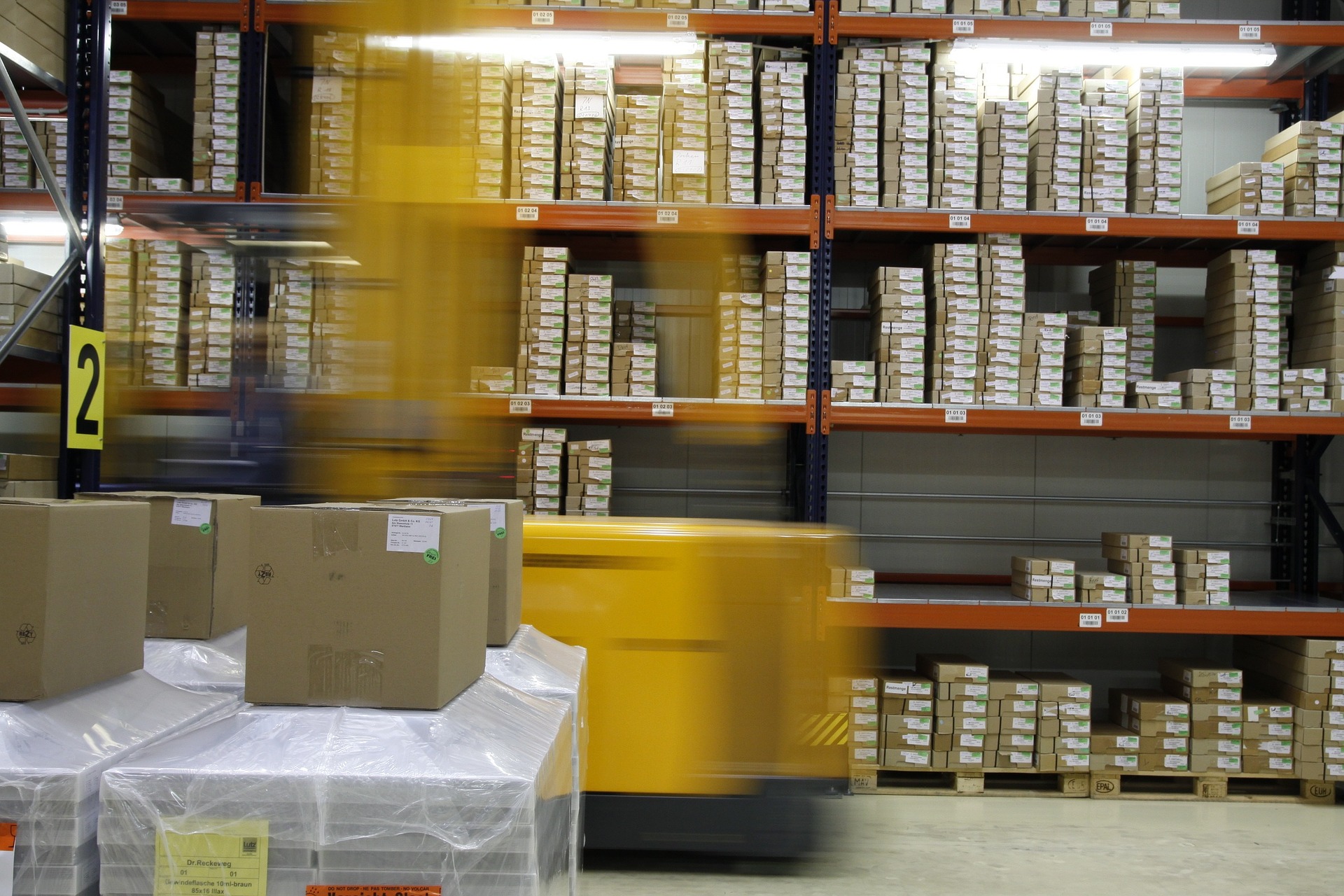
The five lean inventory principles are:
- Value
- Value stream
- Flow
- Pull
- Perfection
These were developed by the renowned engineer and Toyota Production System expert Taiichi Ohno. Let’s explore these principles in more detail.
1. Value
You’ll need to define the value your business will gain from practicing lean management.
Will you be aiming to utilize resources more appropriately? Or are you looking to reduce the amount of inventory you keep on your shelves?
2. Value stream
This is the process of creating or obtaining a product or service. A value stream maps out all the steps and activities that are required for production, from raw materials to finished goods. You need this to identify which process steps are necessary to achieve customer value and which can be discarded.
3. Flow
You’ll need to understand how your inventory flows in your warehouse and apply the lean inventory principles of the five S’s to remove any obstructions to your flow. The five S’s:
- Japanese — Seiri, Seiton, Seiso, Seiketsu, and Shitsuke
- English — Sort, Set in order, Shine, Standardize, and Sustain
Pro tip: Why is inventory considered a waste in a lean inventory system? It’s because keeping inventory raises costs and utilizes resources that provide no value to the customer. So, to truly practice lean inventory management, you will need to get your inventory under control with material requirements planning software.
4. Pull
Now we get to the part of the list that means possibly changing your workflow model.
The only time you should pull your inventory is when a customer places an order. The methodology is to cut down on excess inventory by only beginning production once the demand is there instead of anticipating demand and stocking finished goods.
5. Perfection
This is the most difficult of the lean inventory principles to achieve but also the most crucial one.
The biggest driver behind achieving lean inventory management is to be constantly striving for perfection. You’ll need to continuously refine your inventory management, the quality of your products, its cycle time, your efficiency, and the cost of manufacturing.
It sounds like a lot of work, right?
If you stick it out, you and your customers can expect to reap the lucrative rewards of practicing lean inventory management.
The benefits of using lean inventory
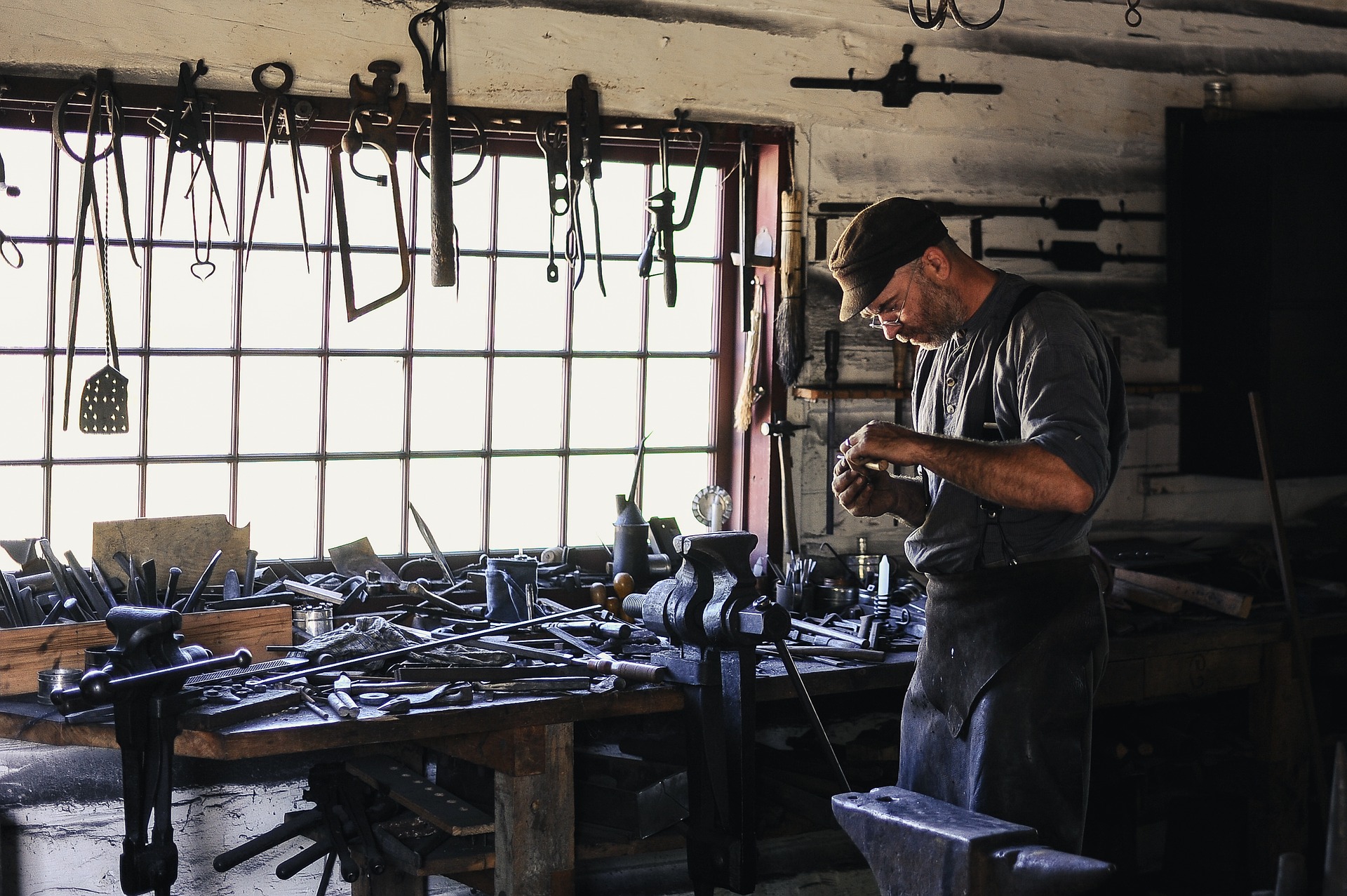
Now that we’ve gone over the basics of lean stock, let’s look at the benefits manufacturers can expect to see if they embark on the journey of lean inventory.
Cost reduction
The main goal of practicing lean inventory is to reduce the amount of waste that your manufacturing processes produce. That means you’ll experience a huge cost reduction since you’ll minimize material waste, lower storage costs, and eliminate losses from dead stock generation.
Fulfillment time
You’ll shorten your manufacturing lead time, get your products out of the door faster, and improve the customer’s experience.
Stock turnover
By taking the just-in-time inventory approach with lean inventory, you’ll be able to have a high inventory turnover rate, which implies good business health.
Eco-friendly
This comes with multiple benefits. Yes, you’ll save money and reduce your carbon footprint. However, manufacturing trends indicate that customers want to shop with businesses trying to help the planet.
So, if you take the lean inventory management approach, you’ll improve your company’s perception among consumers, especially if you highlight your eco-friendly efforts in your branding, marketing, social media, etc.
As you can see, there are a lot of benefits to be had if you adopt lean inventory management. Before you quickly sprint into your factory to make changes, let’s see how you can implement the model into your business.
Pro tip: To really benefit from lean inventory principles, you should also implement lean manufacturing. You can learn all about it from the following article — Lean manufacturing principles to streamline production and eliminate waste
How to use lean inventory in your business?
Admittedly, the following rules for implementation were developed in mind for computers. However, each following point, developed by Steve Bell with Lean IT, is the same you’ll need to follow when implementing lean inventory strategy into your business.
When starting to use lean inventory management, you should:
- Focus on your costs and not the outcomes
- Not hesitate to stop production to deal with any issues. Just have some buffer time scheduled to compensate for stoppages
- Understand the people you work with are your most important resource, so invest in them. Take the time to develop their abilities through mentoring and training
- Know and concentrate on your value streams
- Keep it simple
- Visualize your goal and make the image in your head a real-world thing
- Always put yourself in the shoes of the customer. Only expend resources on something that provides value to the customer
- Be ready for uncertainty and make changes as soon as you need to
If you stick to these eight points, you can surely achieve a lean inventory management system. To make the process as smooth as possible, it’s a good idea to adopt lean manufacturing software.
Katana’s cloud inventory software for lean inventory
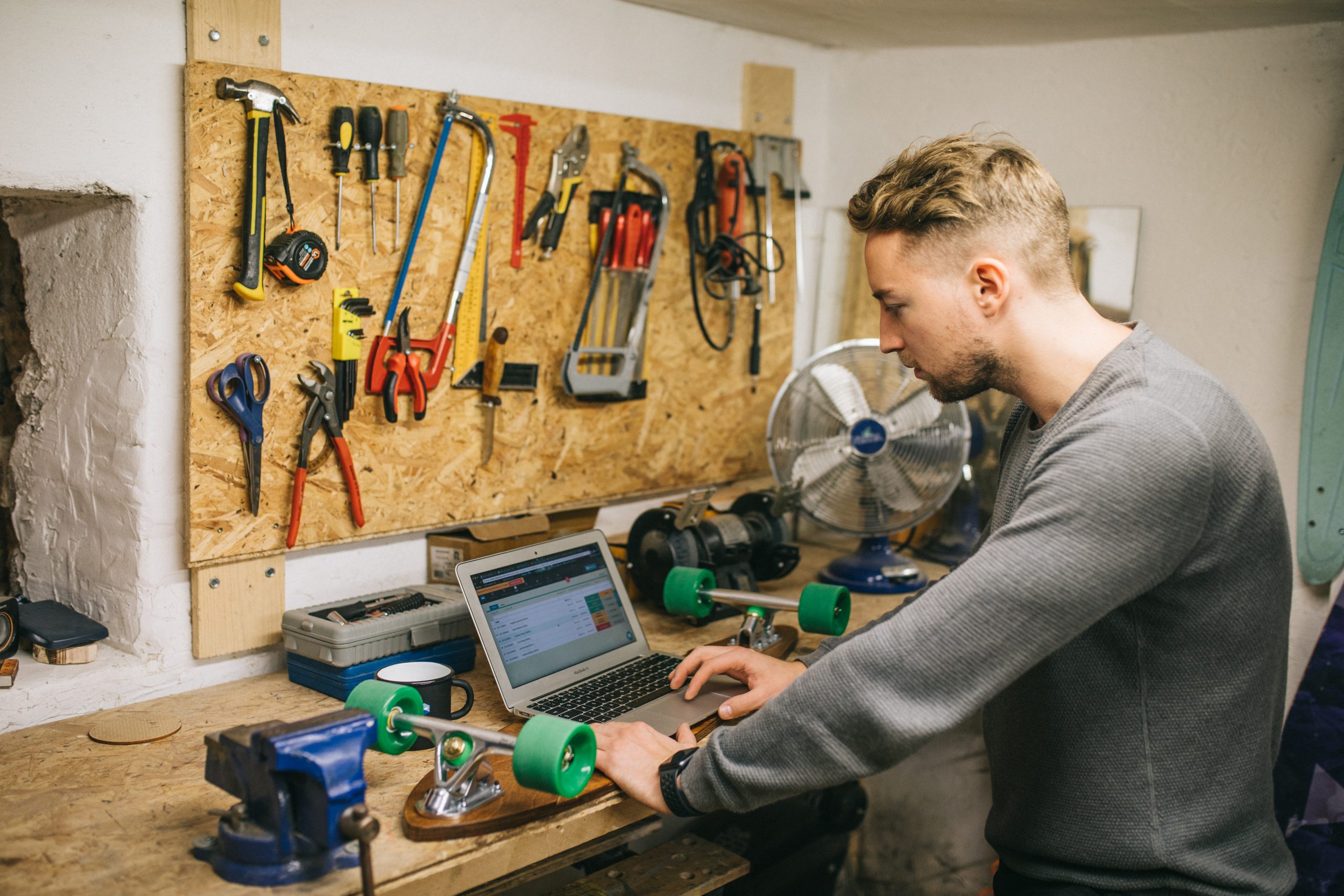
Keeping a lean inventory can be difficult as it’s a continuous process. That’s why it’s essential to find a piece of software that can help you manage this challenging method when running your business.
Katana’s cloud inventory platform has been built to help modern manufacturers achieve a lean inventory workflow. Katana achieves this by offering the following features.
Real-time master planner
Katana’s real-time master planner is perfect for any manufacturer practicing lean inventory management. When a sales order comes in, or a manufacturing order is generated, Katana automatically takes available inventory and allocates it to your orders.
It’s able to do this once you have set up your bill of materials and defined your operations.
Raw material management
Katana automatically tracks your raw materials so you can monitor stock levels in real time and set reorder points to highlight when your inventory levels are starting to dip.
This allows you to discover how much material waste your operations produce and figure out a game plan to reduce that amount or even find ways of utilizing the leftovers.
Priority-based production planning
Finally, Katana automatically schedules production in the order in which manufacturing orders are created. However, assuming you have a VIP order come through, Katana’s nifty drag-and-drop system allows you to prioritize your orders so you can tackle the most important jobs first.
And not only that, Katana will redistribute your resources to fulfill the new workflow as soon as possible.
Katana can effortlessly help you track all the nitty-gritty details with inventory management, making it perfect for green manufacturing. This does not only go together with lean inventory but will bode well with consumers as more shoppers turn to ethical and greener companies.
Implementing lean inventory practices
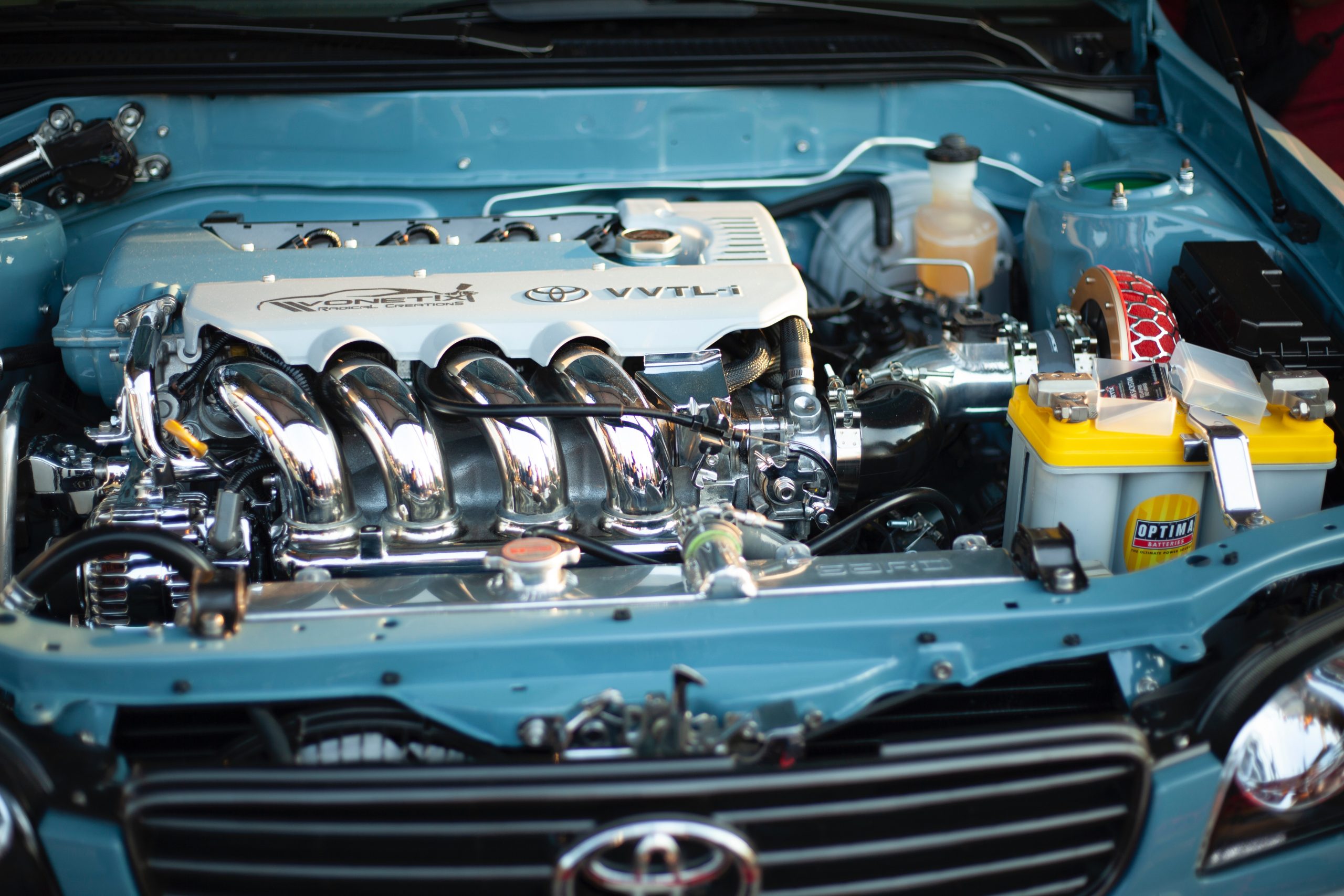
Lean manufacturing inventory, as a rule of thumb, is considered a good form of business practice as it allows manufacturers to figure out how to become more efficient, improve their manufacturing processes and promote an active form of management.
You might be wondering, “When using the lean concepts, all inventory is considered waste?” which is partially true. You need to think of finished goods (and the production of finished goods) as a value. If you have finished goods sitting on a shelf, taking up space and raising costs, it’s not providing any value and is being wasted.
Imagine if a customer asked you what they paid for when they bought the finished product, and you said, “Part of the cost was to cover the fact it’s been sitting in inventory for the past three months,” do you think they’ll see the value in that?
Lean production requires a “push and pull” system of inventory replenishment. You should only start production once a customer has requested the item. However, some safety stock, just in case a large amount of demand comes in, isn’t frowned upon.
Just remember, before you implement lean inventory, ask yourself these questions:
- What is the value you and your customers will gain?
- Is there something that unnecessarily interrupts your workflow?
- Is it possible to pull inventory to satisfy a customer’s needs without compromising those needs or your business?
- Are you proactive to the changes in the market?
- Can you continuously strive for perfection?
The last question is the most important and most difficult. However, lean inventory can be a breeze with a good inventory management system.
Why not find out for yourself? Get started by booking a demo, so you can see firsthand why this software is perfect for anyone going lean and green.
Table of contents
Inventory management guide
More on inventory management
Get visibility over your sales and stock
Wave goodbye to uncertainty by using Katana Cloud Inventory for total inventory control
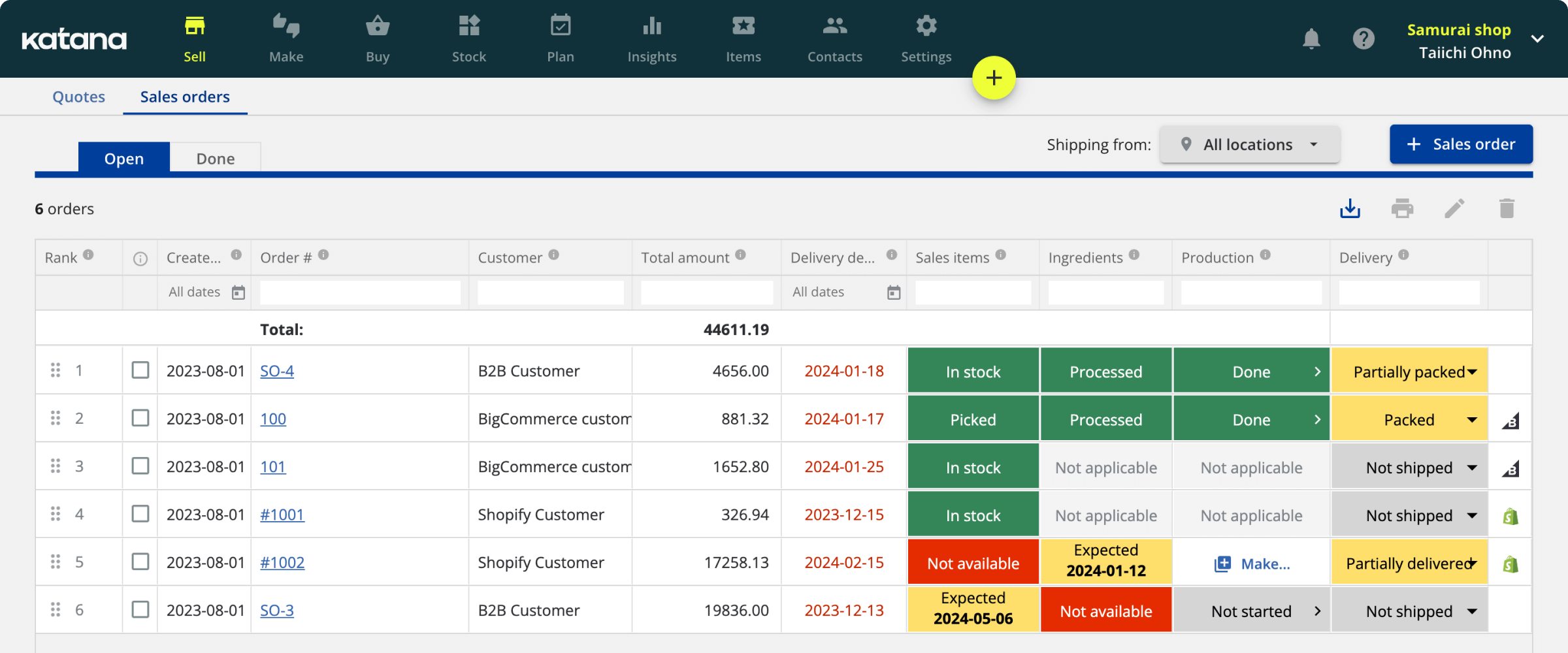