Everything you need to know about finished goods inventory
You’ve finally made it. After months or years of toil, you have a product ready to ship. But, before you can do that, you need to deal with one last thing — inventory.
Creating and managing finished goods inventory can be daunting, but it doesn’t have to be. In this guide, we’ll walk you through everything you need to know about finished goods inventory, from the basics of stock management to how to calculate your inventory value. By the end, you’ll be well on your way to keeping your shelves stocked and your business running smoothly.
So let’s get started!
What is finished goods inventory?
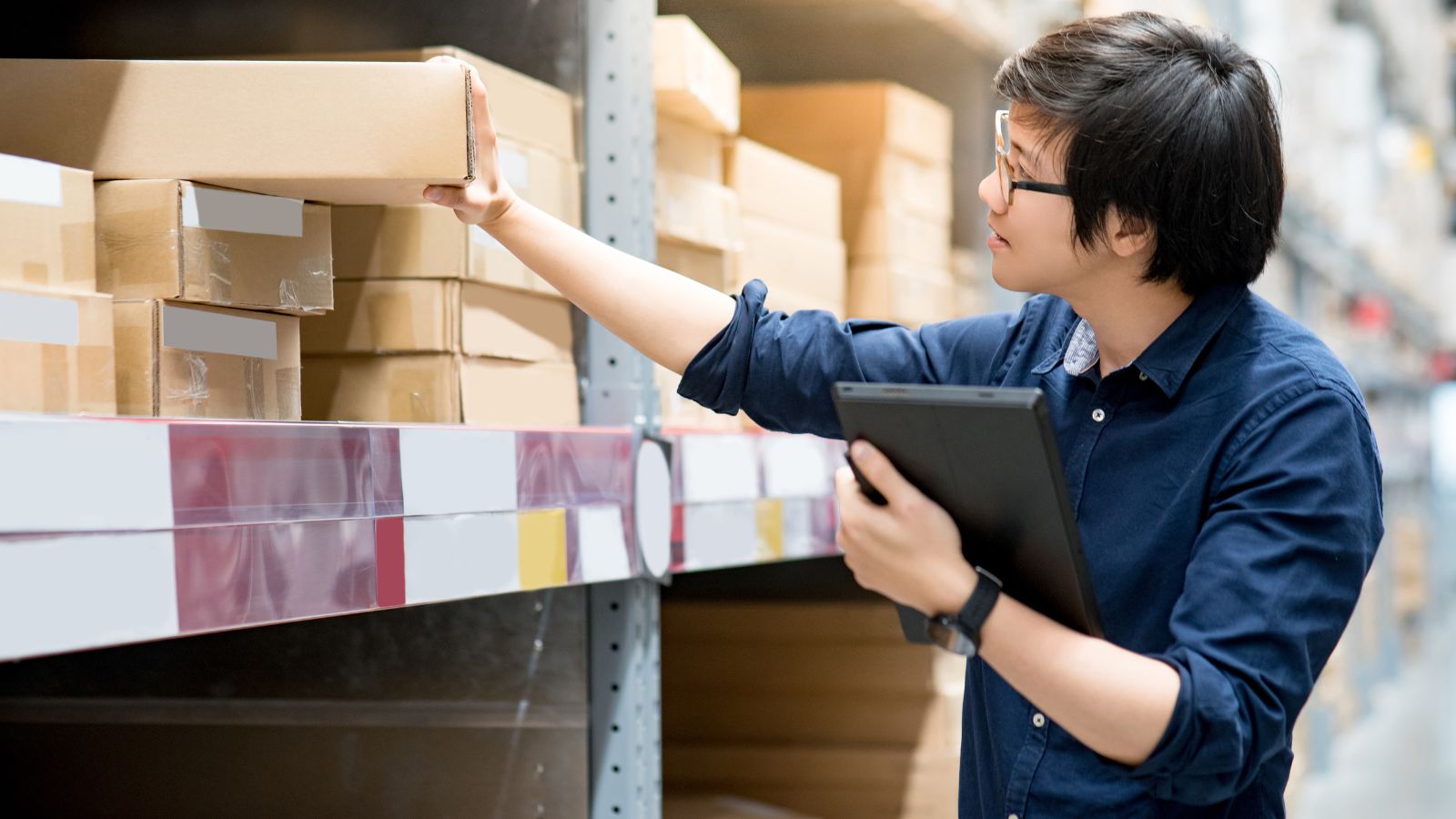
Finished goods inventory (FGI) refers to the stock of products ready to be sold to customers. This includes every complete item in your inventory that does not require further manufacturing or assembly.
As a finished goods inventory example, let’s say you own a clothing boutique. Your apparel inventory contains items that are in finished, wearable condition. On the other hand, raw materials like textile for manufacturing or spools of thread would not be considered finished goods since they can’t be sold as is.
The same goes for work in process (WIP) items, which are products that are partially complete but not yet ready to be sold. WIP items are usually still undergoing some kind of manufacturing or assembly, and as such, they are not considered finished goods.
In order to maintain finished goods inventory, businesses must carefully track both the incoming and outgoing flow of products. This requires the best inventory management software out there, that can handle everything from purchasing and receiving orders to shipping and invoicing customers.
Importance of finished goods inventory
There are a few reasons why finished goods inventory is so important for businesses.
- It provides a buffer against fluctuations in demand — By having finished products on hand, businesses can avoid the costs and disruptions associated with sudden spikes in customer demand.
- It helps you meet customer expectations — Customers today expect faster delivery times than ever before. By keeping finished goods inventory on hand, businesses can ensure that they can meet these expectations and avoid disappointing their customers.
- It allows you to take advantage of economies of scale — Businesses often get a supplier discount when they purchase raw materials in bulk. Having finished goods inventory on hand allows companies to take advantage of these discounts and reduce overall costs.
How to calculate finished goods inventory?
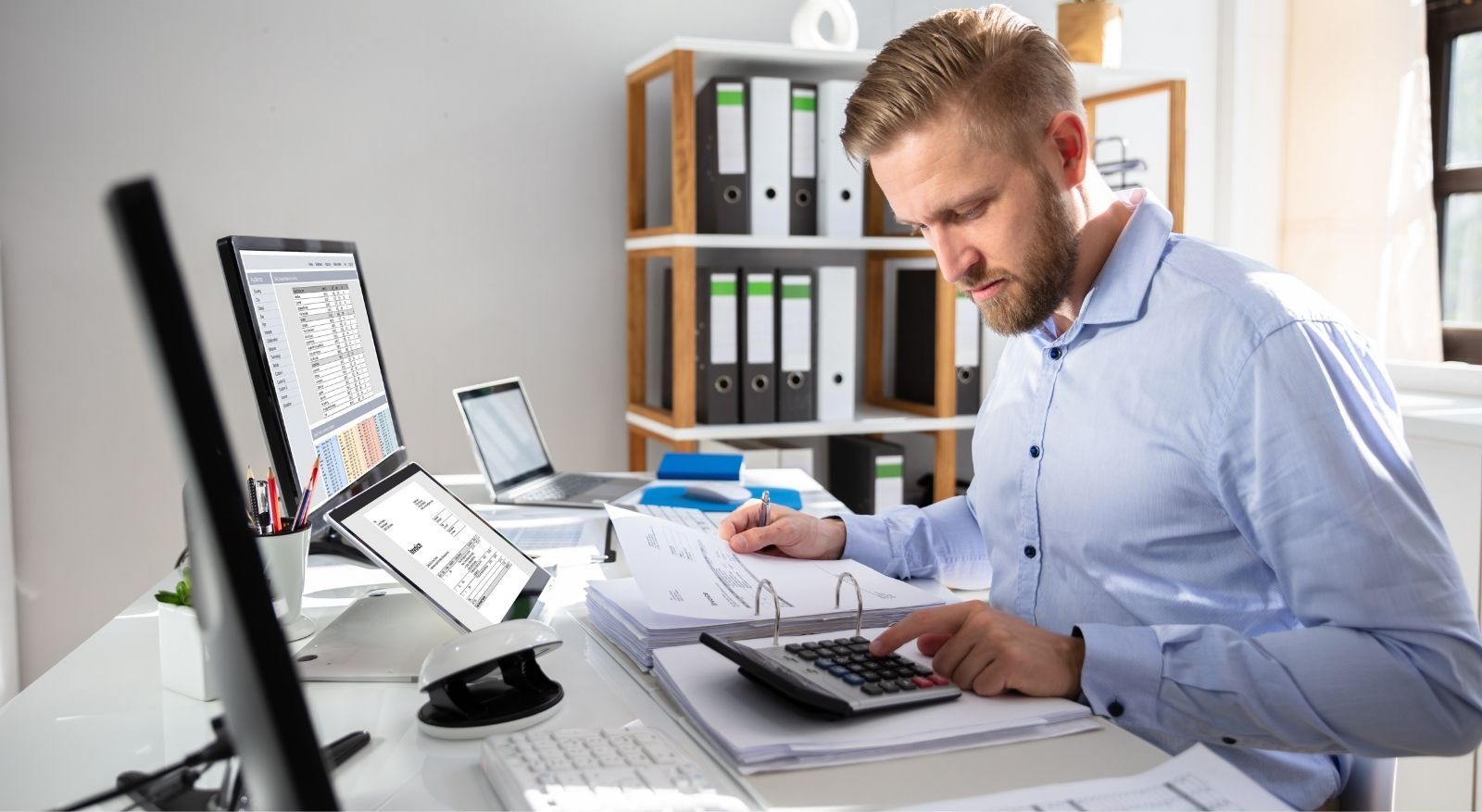
Before we start crunching numbers, let’s quickly go over some terminology we’ll use:
- Beginning finished goods inventory — The stock of finished goods that a business had on hand at the beginning of a period (usually a month)
- Ending finished goods inventory — The stock of finished goods that a business had on hand at the end of a period
- Cost of goods manufactured (COGM) — The total cost of all the raw materials and labor that went into producing the finished product
- Cost of goods sold (COGS) — The total cost of all the finished products that were sold to customers during a period
Now that we’ve got that out of the way, let’s move on to the calculation itself. The finished goods inventory formula is relatively simple:
Ending finished goods inventory = beginning finished goods inventory + COGM – COGS
For example, let’s say that a business started the month with $10,000 worth of finished goods in inventory. During the month, they incurred $15,000 in costs related to manufacturing new products. And finally, they sold $20,000 worth of finished goods to customers. In this case, their ending finished goods inventory would be calculated as follows:
$10,000 + $15,000 – $20,000 = $5,000
So their cost of finished goods inventory for the month would be $5,000.
Of course, this is just a simple example. In reality, businesses usually have a much more complex inventory system with multiple types of raw materials, products, and finished goods. But the basic principle remains the same — businesses can calculate their ending finished goods inventory for any given period by tracking all of the inputs and outputs.
Inventory stages in accounting
The WIP account is used to track the cost of raw materials, labor, and overhead associated with products that are in the process of being manufactured. Once a product is completed and moved to the finished goods inventory, the WIP account is closed out, and the finished goods inventory account is debited for the cost of the goods.
The WIP account is closed out at the end of each accounting period for businesses that use a periodic inventory system. The finished goods inventory account is debited for the cost of goods manufactured during that period.
If a business uses a perpetual inventory system, the WIP account is closed out as each product is completed and moved to the finished goods inventory. In this case, there is no need to close out the WIP account at the end of the accounting period since it is already up-to-date.
While these two systems can be used for calculating finished goods inventory, most businesses prefer to use a perpetual inventory system because it provides more accurate data.
Want to see Katana in action?
Book a demo to get all your questions answered regarding Katana’s features, integrations, pricing, and more.
From raw materials to finished goods
Now that we know, how to calculate finished goods inventory let’s take a closer look at how to get finished goods inventory from raw materials. The inventory goes through three main stages:
-
Raw materials
This is the starting point for all inventory. Raw materials are the unprocessed inputs used to create finished products. They can include everything from steel and plastic sheets to component parts like circuit boards and engines. -
Work in process (WIP)
Once raw materials have been procured, the manufacturing process can start. But the products are not yet finished at this stage — the process is still ongoing. This stage can include things like unassembled furniture, ceramics that haven’t been glazed, or clothes that haven’t been sewn together. -
Finished goods
Once the manufacturing process is complete, the products are ready to be sold to customers. At this point, they’re considered to be finished goods and can be shipped off to the customer.
Managing finished goods inventory
Some businesses use just-in-time (JIT) inventory to minimize finished goods inventory. Just-in-time (JIT) manufacturing is a lean manufacturing technique that helps companies to strike this balance by producing products only as needed. By producing goods only when there is a demand, businesses can avoid the costs associated with holding finished goods inventory.
However, the majority of businesses use some type of inventory management software to track and manage their finished goods inventory.
Micro businesses may be able to get by using spreadsheets and tracking all inventory movements manually, but this can quickly become unmanageable as the business grows. Therefore, most companies dealing with larger inventories use inventory management software like an ERP.
An ERP system is software that helps businesses manage all aspects of their operations, including inventory, manufacturing processes, orders, and much more.
Katana equips businesses with a platform that’s easy to learn and use to take care of all your business needs. Besides the built-in robust inventory management features, Katana offers seamless integrations with your favorite business tools, allowing you to keep everything in sync effortlessly. Give your business the best chance of success. Book a demo now with Katana’s cloud inventory platform.
Table of contents
Inventory management guide
Get visibility over your sales and stock
Wave goodbye to uncertainty by using Katana Cloud Inventory for total inventory control
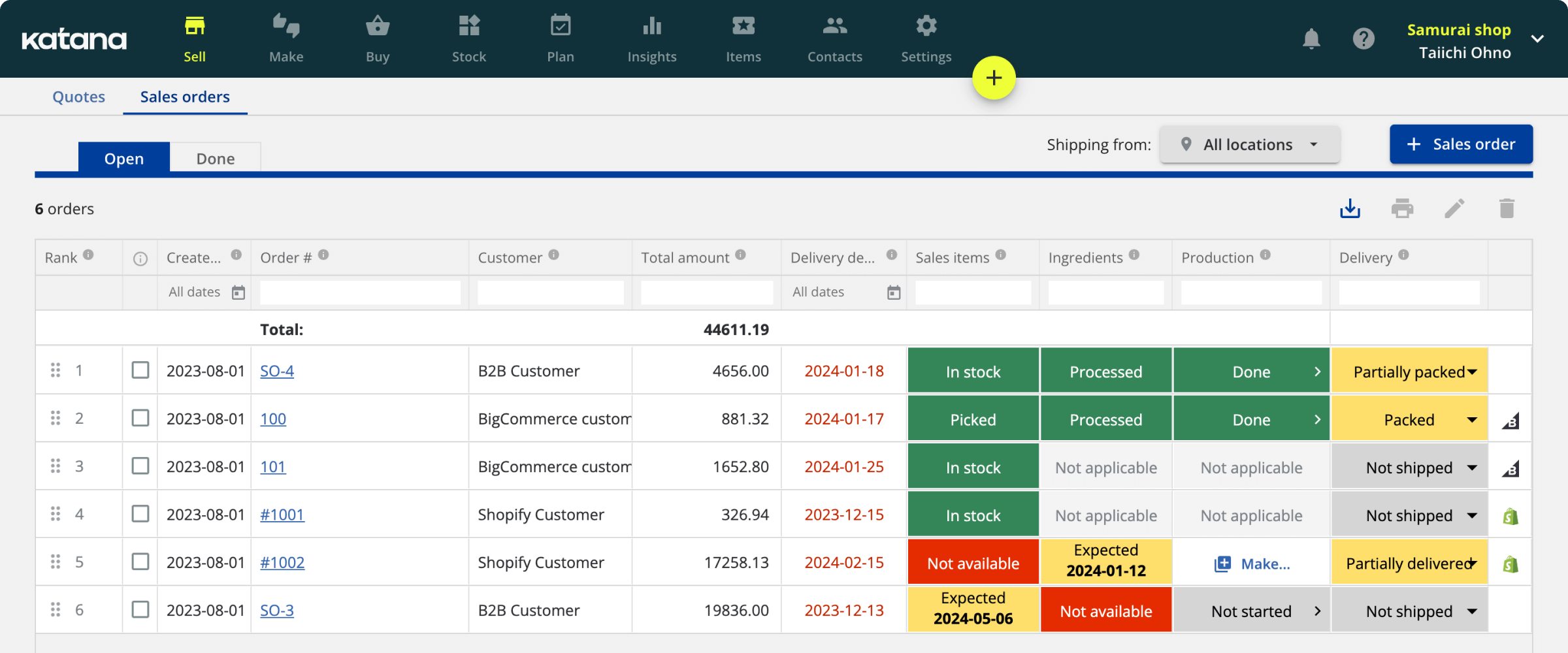