Everything you need to know about the total manufacturing cost formula
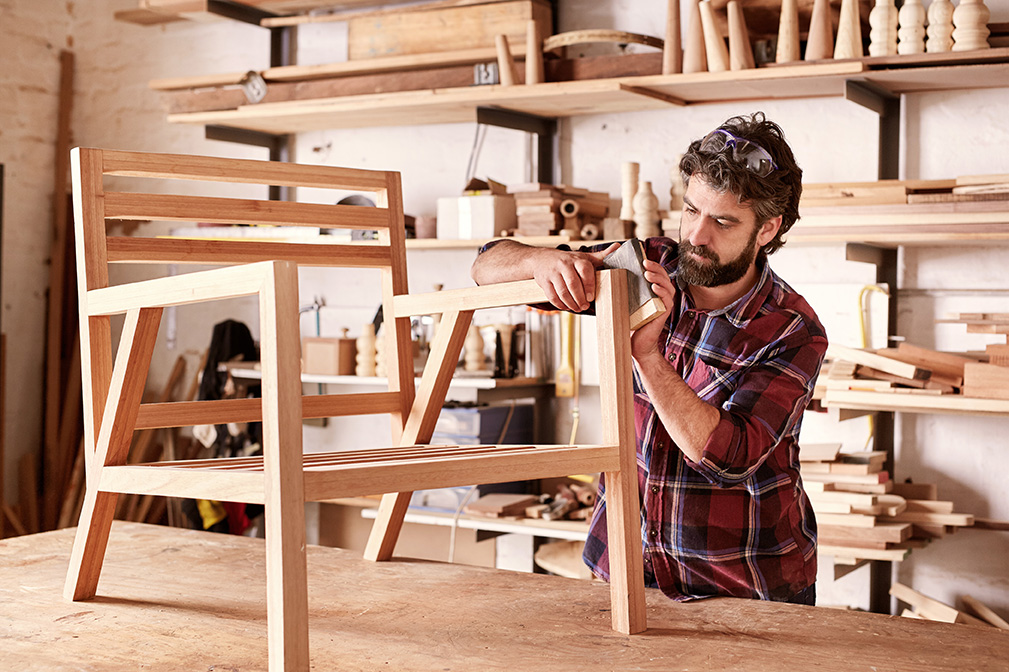
Is knowing and understanding your total manufacturing cost at the top of your to-do list?
It’s not the most glamorous subject. But taking the time to manage it will pay dividends in the long run. You can use it to find out if you are hitting your targets or if your production process is conducive to your desired level of productivity.
The long and short of it is this — if you don’t know your exact costs, how do you know your profit margin?
You could be selling stacks of products, but if your costs are out of control, a lot of hard work is going to waste. It may be a cliché, but it is so for a reason:
“Turnover is vanity. Profit is sanity.
Knowing the value of your current inventory and the cost of goods sold, you can calculate your sales margins.
Maybe there’s room to lean up your manufacturing by cutting down on hidden costs to your business. But how do you know where to start? What are manufacturing expenses beyond basic raw materials? What do you need to do to reduce these costs?
In this guide, we’ll cover everything you need for your total manufacturing cost formula.
Is math not your strong suit?
The art of success is doubling down on your strengths. Let Katana’s cloud platform take care of calculating your total manufacturing costs, so you can stay focused on doing what you do best — manufacturing.
What is total manufacturing cost?
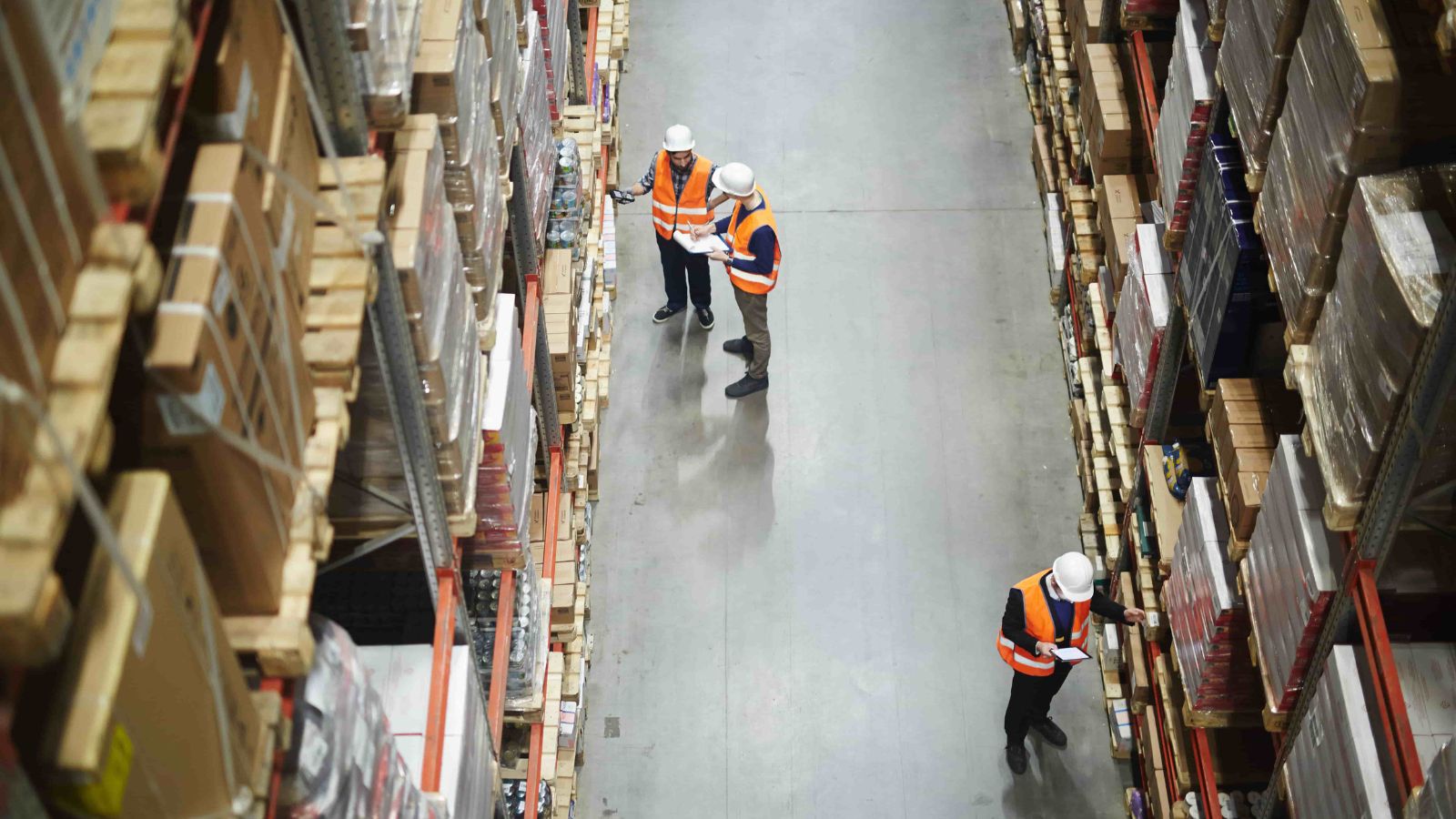
The total manufacturing cost is the sum of expenses associated with all the resources spent while manufacturing your finished goods inventory.
However, calculating and understanding it is not so obvious.
Knowing what each element of your production process costs you is important. You need to understand how to split your total manufacturing cost into its constituent parts.
The first distinction is between the three major costs components of manufacturing a product — these can be direct or indirect. Some things never touch your product but still need to be in your total cost calculation.
That’s right — pretty much everything in your business impacts your costs, even if it seems separate at first glance.
Let’s break this concept down even further.
The three major cost components of manufacturing a product are:
- Direct materials — the primary raw materials that go into the final product
- Direct labor — all staff who have a hand in the refining, assembly, and manufacturing of your products
- Manufacturing overheads — machining, maintenance, and indirect materials and labor in a secondary or support role
What is the difference between direct and indirect manufacturing costs?
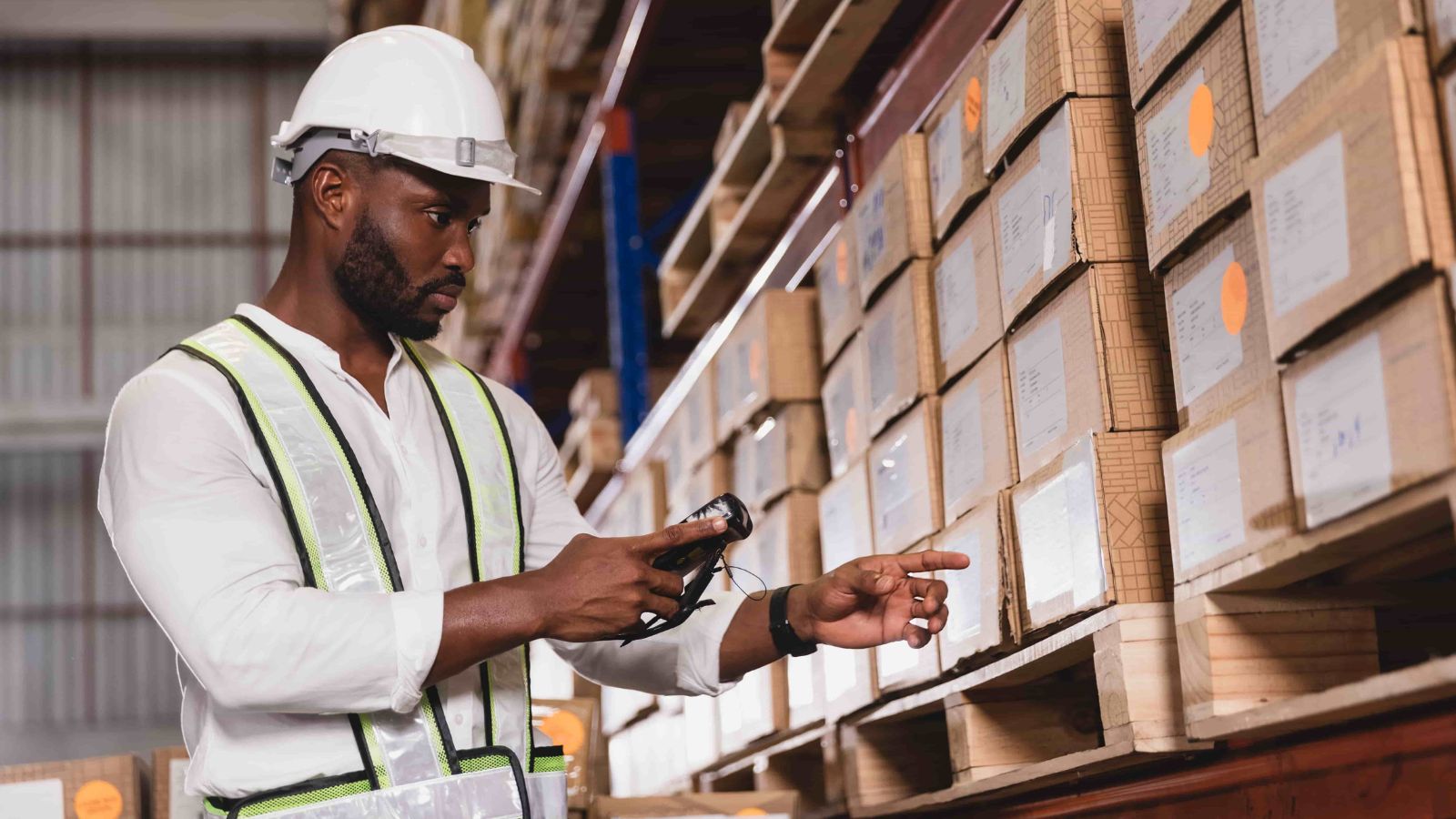
As already explained, your costs will fall into one of two categories.
Direct costs
Direct costs refer to everything spent on the bulk of the manufacturing process. This could be material costs (for example, raw materials) and time costs (staff wages). They must play a physical role in assembly or production for it to be a direct cost.
Be wary.
Some materials and labor are regarded as indirect manufacturing costs (more on that below).
Whatever you do, watch out for counting costs twice by not understanding this.
Indirect cost
These costs in your manufacturing process do not come from raw materials or labor primarily used in manufacturing. This includes:
- Maintenance costs
- Utility bills
- Salary of the non-manufacturing staff
- MRO inventory
As mentioned above, not all the materials consumed by your manufacturing process are regarded as direct costs. For example, nails and glue holding a wooden cabinet are indirect materials called consumables. Don’t forget to add the cost of your consumables to your total manufacturing cost.
One thing to watch out for is the costs that come from depreciation in the value of your raw materials.
If you produce comestibles, your raw materials and finished products in-waiting could spoil. Knowing how much you lose in situations like this is critical to keeping your business afloat. If you know there is wastage in your manufacturing process — you can do something about it.
Hundreds of businesses go into the red every year, and management issues like this are a major cause.
What is the difference between the total cost of manufacturing and the cost of goods sold?
The total cost of manufacturing (TCM) refers to the cost incurred to produce a product, including the cost of materials, labor, and overhead. On the other hand, the cost of goods sold (COGS) only includes the direct costs associated with producing a product, such as the cost of materials and labor. Because COGS excludes indirect costs, it is often used as a more accurate measure of profitability.
What are the benefits of using the total manufacturing cost formula?
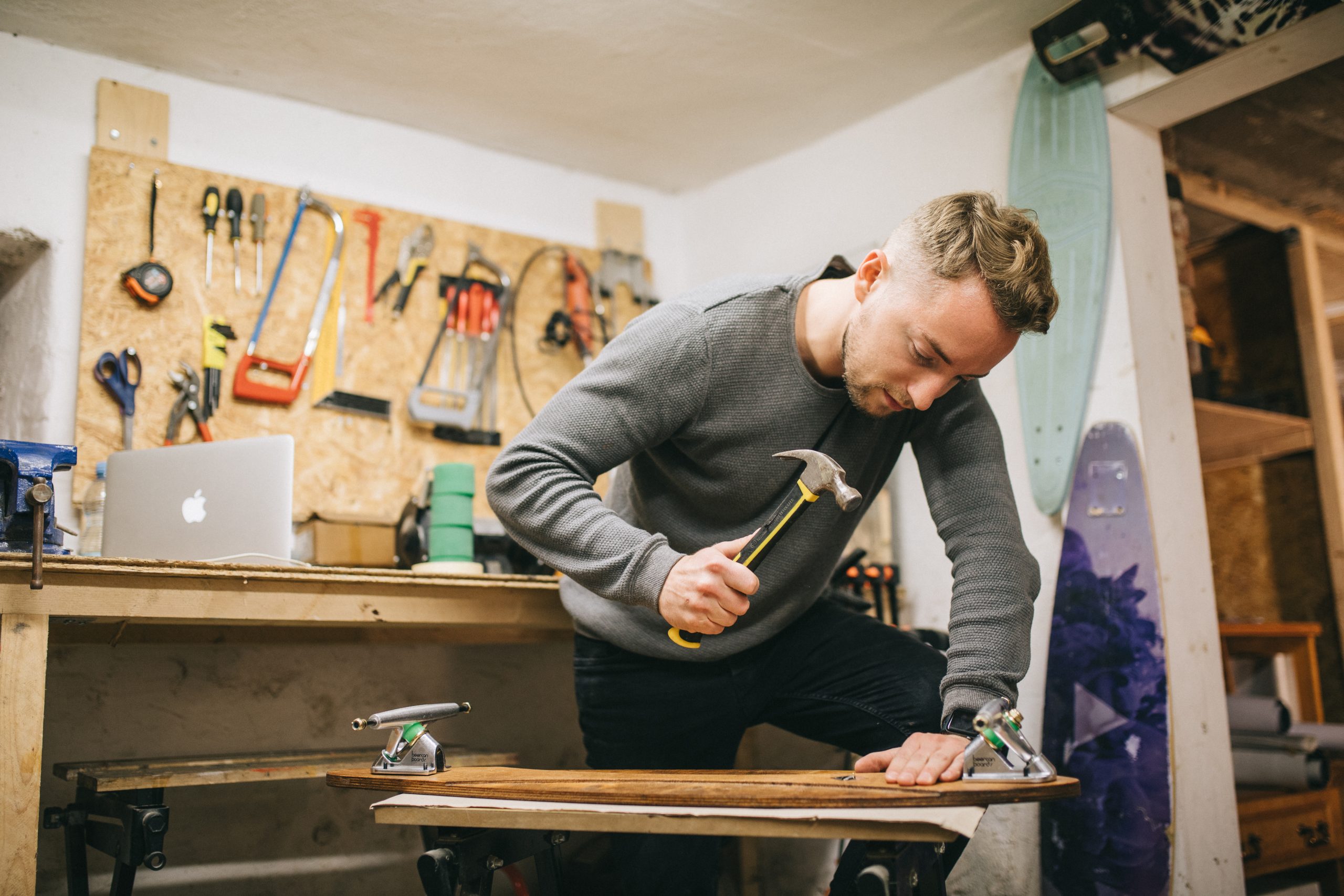
You might be debating whether calculating your total manufacturing cost is even worth the hassle. If you put some time aside and calculate your manufacturing costs, here are five benefits you can expect to reap.
1. Lower costs
When you know the total cost of manufacturing a product, you can find ways to reduce that cost more easily. This can lead to lower prices for consumers and increased profits for businesses.
There are many reasons why lower costs in manufacturing are important. First, lower costs can lead to higher profits for companies. This is because companies can sell their products at a lower price, making them more affordable to consumers. Additionally, lower costs can help companies expand their operations and hire more workers — boosting the economy by creating new jobs and increasing consumer spending.
2. More clarity around financial health
A company’s financial health depends on many factors, including its manufacturing costs. By understanding the total manufacturing cost formula, companies can get a clearer picture of their overall financial situation.
There are many reasons why more clarity around financial health is important. It helps businesses make better decisions about spending and investing.
When businesses have a better understanding of the financial situation of their customers, they can make more informed decisions about spending and investing — leading to increased profits and growth for businesses.
3. Informed decisions around pricing
Knowing the total cost of manufacturing a product can help ensure that products are priced appropriately and that businesses are making a profit.
Detailed product costing is important for informed decision-making around pricing in manufacturing. Product costs are used to calculate the selling price, impacting profitability. Understanding all the factors that contribute to the cost of a product helps managers make better decisions about pricing and other strategic initiatives.
A company that doesn’t understand its product costs clearly may end up selling its products below cost, resulting in losses. On the other hand, a company that prices its products too high may miss out on potential sales and market share. In either case, understanding product costs is essential for making informed pricing decisions.
In addition to profitability, pricing decisions can also impact other strategic objectives, such as market share and customer satisfaction. For example, a company may price its products lower than the competition to gain market share. Or, a company may price its products higher to maximize profits. Whatever the decision, it’s important that it be based on a thorough understanding of product costs and other factors.
4. Less waste
By understanding the total manufacturing cost formula, businesses can identify ways to reduce waste. This can lead to lower costs and a more efficient manufacturing process.
There are many reasons why less waste in manufacturing is important. One reason is that it can help to save costs. When less material is wasted, there is less need to purchase new raw materials, which can save money.
Less waste can also lead to improved production efficiency and quality. This is because when there is less waste, there are fewer opportunities for defects to occur. As a result, products are more likely to pass your production quality control checklist and meet customer expectations. Reducing waste also promotes green manufacturing and environmental sustainability.
5. Insights that drive efficiency
Knowing the total manufacturing cost formula can give you insights into where inefficiencies exist. This can help businesses make changes that lead to a more efficient manufacturing process and lower costs.
If you’re looking to drive efficiency in your manufacturing process, insights are key. You can make changes that streamline the process and improve efficiency by understanding how your manufacturing process works, what areas need improvement, and where bottlenecks exist.
Better insights mean you can save on materials, labor, and other resources by identifying areas where improvements can be made. Sometimes, simply making a few small changes to your routing manufacturing can result in significant savings.
Ultimately, improving efficiency in your manufacturing process is important for ensuring that your products are of the highest quality and meet customer demands promptly.
What you need to calculate your total manufacturing cost formula?
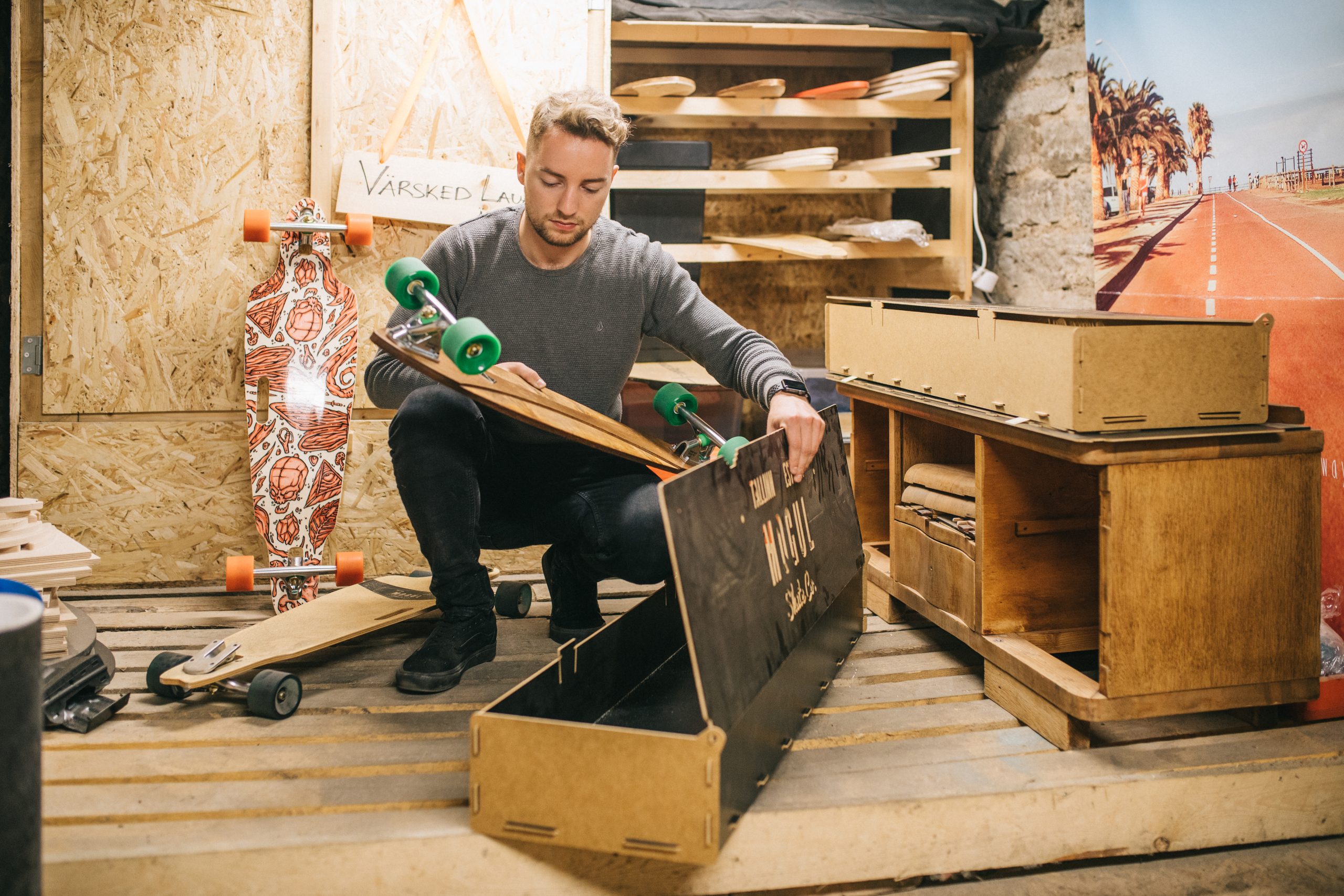
Even though the total manufacturing cost formula is a relatively easy calculation to make, it does require a lot of input from different areas of your business.
And what better way to learn something than jumping into the deep end and learning while on the go? For this to work, we’ll fabricate a scenario, but feel free to use your own business as a replacement for this example. Let’s imagine we’ve been tasked with the responsibility of uncovering the total manufacturing cost of a plucky Portland skateboard manufacturer.
Using what is likely to be consumed during the production of a skateboard, we can identify different manufacturing costs:
- Direct material — the cost of plywood to make the board
- Direct labor — the guys and gals who make and assemble the skateboard
- Manufacturing overhead (Indirect labor) — For example, one manufacturing overhead might include the janitor in the workshop
- Manufacturing overhead (Indirect material) — the masking tape for holding the board in place during molding
- Manufacturing overhead (Other) — includes the costs of running machines like a belt sander or consuming spray paint canisters
- Manufacturing overhead (Other) — the cost of your workshop’s rent and utilities
Now we have some areas of the business which has costs associated with it, we can move onto the formula.
How to find total manufacturing costs
The cost of manufacturing formula is as follows:
MC = Raw materials + direct labor + allocated manufacturing overhead
So, how does this formula work in practice?
Let’s continue with our skateboard manufacturer example. We have identified our direct and indirect manufacturing costs so can apply them to the formula introduced above to understand how to calculate total manufacturing cost.
The direct materials cost for one skateboard is the sum of:
- One deck ($20)
- Two metal trucks ($10)
- Four wheels ($16)
Direct labor could average out to $10 per unit, as they produce several per hour.
Overhead costs include bearings, lubricant, paint, staff, and electricity ($10 per unit).
Raw Materials + Direct Labor + Allocated Manufacturing Overhead
(20 + 10 + 16) + 10 + 10 = 56
This brings your total to $56 for one unit.
Once you have this, you can predict your total costs for a whole day, weeks, and even months production.
Keep track of everything and run the actual total costs against the predicted costs. See if they align at the end of a set time period. This is one way to monitor manufacturing costs.
One thing to remember: as you scale up your manufacturing cost calculation, you need to consider things that don’t scale at the same rate.
This could be:
- Cheaper wholesale prices when ordered in bulk — bring costs down
- Higher maintenance costs for machines — bring costs up
Like every part of your production process, anticipating these changes helps you stay on top of everything.
And there you have it! Everything you need to know to start crunching those numbers and improve your profit margin.
Admittedly, doing these calculations as a startup or as a small manufacturing business. But what happens once you start to grow? Performing this task manually is going to cost you time and money.
So, how exactly do the large-scale manufacturers pull this off?
Want to see Katana in action?
Book a demo to get all your questions answered regarding Katana’s features, integrations, pricing, and more.
Use Katana cloud software to calculate your total manufacturing cost automatically
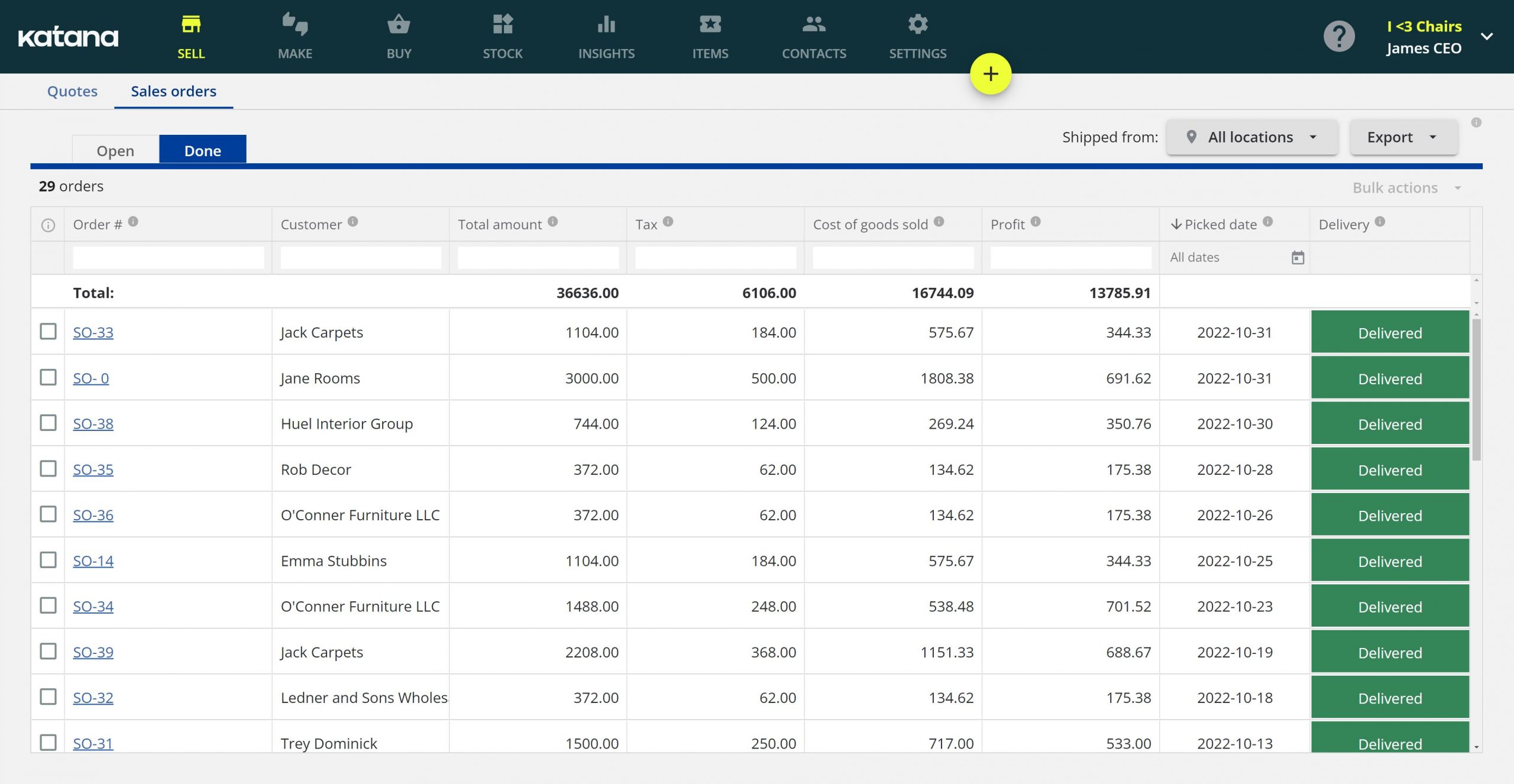
Know every figure in your manufacturing process by using cloud software like Katana.
Katana is a platform giving thousands of manufacturers a live look at their business with an easy-to-use visual platform.
Best of all, by using the information you provide in your bill of materials, Katana automatically calculates the costs of each operation using the moving average cost formula. This means that the value of your inventory is divided by the quantity in stock every time a new purchase is made — your inventory value and actual production costs are continuously and accurately calculated.
See it for yourself — Reach out to our sales team and request a demo.
Table of contents
Manufacturing guide
More essential guides from Katana
Get visibility over your sales and stock
Wave goodbye to uncertainty by using Katana Cloud Inventory for total inventory control
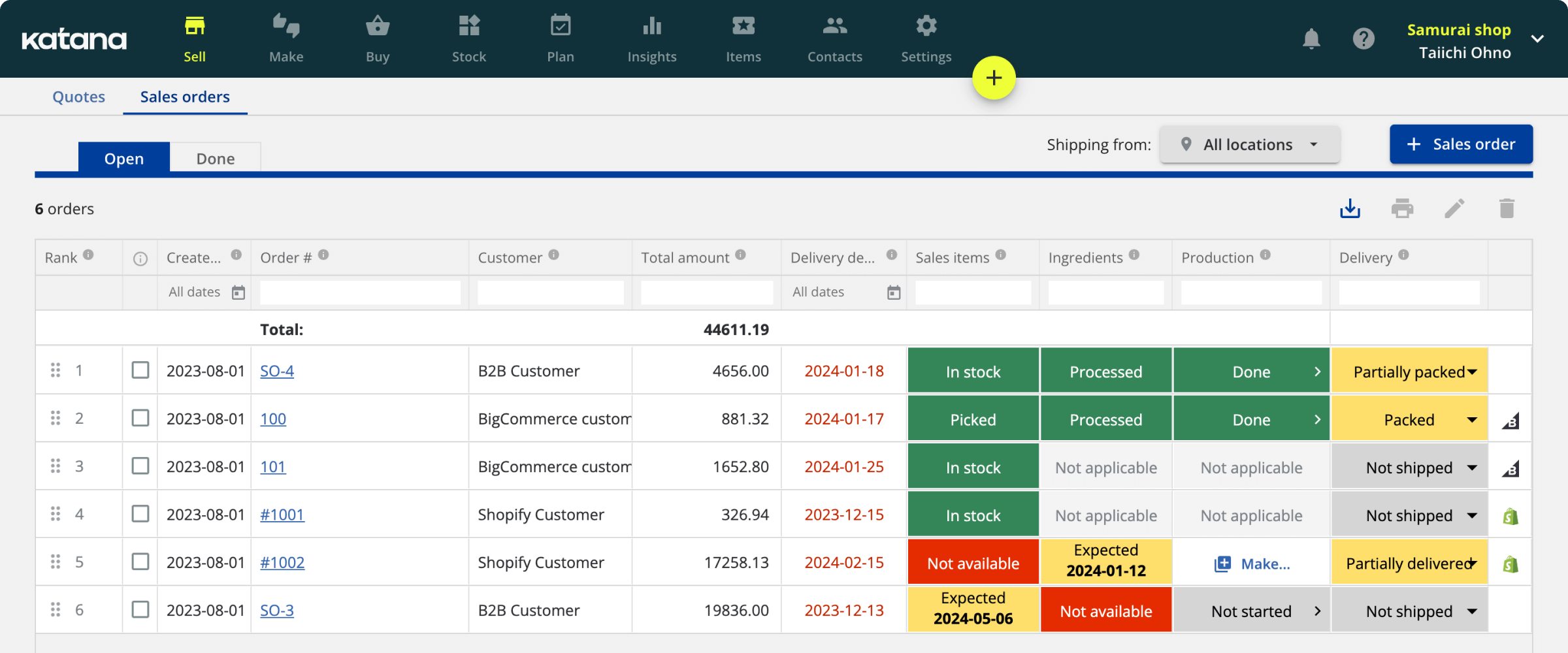