Inventory carrying costs: Slicing the excess waste
Fluctuations in sales can leave you struggling to find a solution for optimizing inventory levels and fulfilling orders. In a situation like this, you might approach your warehouse management with a very simple strategy — keep your shelves full. This may seem like the best solution, but this tactic is counterintuitive and will force you to miss out on opportunity costs in the long run.
Why? Because of inventory carrying costs.
In this article, we’ll figure out what is the carrying cost of inventory and how to calculate it using the inventory carrying cost formula. You’ll also learn tips on reducing these costs and keeping them minimal.
So, let’s get to it.
What is the inventory carrying cost?
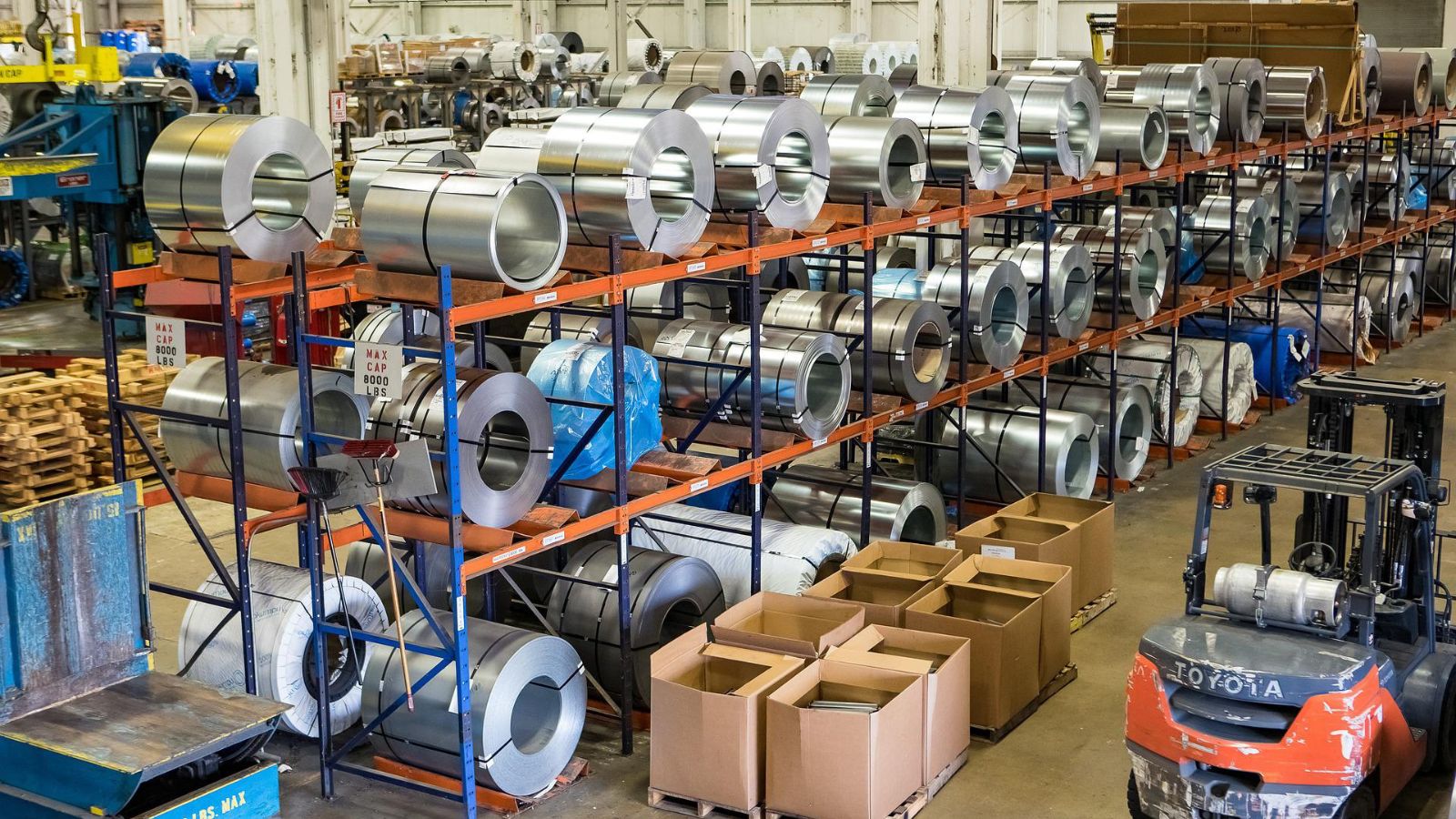
Inventory carrying costs is the total cost of holding inventory for your business, also known as inventory holding cost. Some inventory holding cost examples include:
- Warehouse space and storage rent
- Work hours spent handling inventory
- Transportation costs
- Security costs, including systems and personnel
You know the cost of buying raw materials, but you might not know you are also paying to store and carry them. So, holding inventory that you intend to sell, but have not yet done so, increases your carrying costs. Every business that sells a physical product is subject to these costs.
Every second you have items sitting in your different types of inventory, money continues to leak from your profits and stunt your business’ growth.
Why is calculating the cost of carrying inventory important?
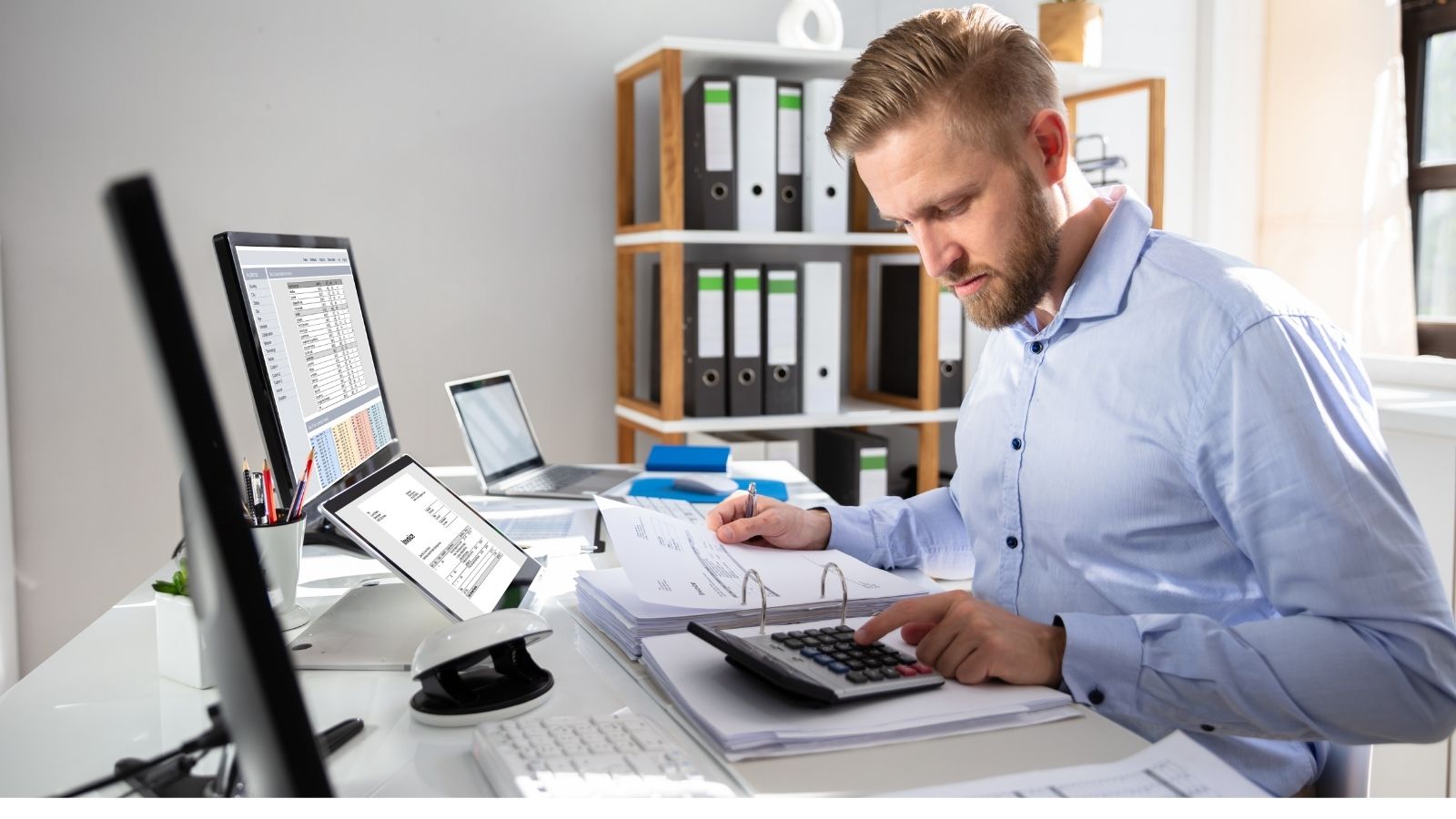
Calculating inventory carrying costs helps businesses determine the optimal level of inventory to maintain. If a company carries too much inventory, it can tie up capital that could be used for other purposes, such as investing in new equipment or expanding the business. Excess inventory can also lead to storage and insurance costs and an increased risk of stock becoming obsolete or perishable.
On the other hand, if a business carries too little inventory, it can lead to stockouts and lost sales. Additionally, the cost of frequently reordering small quantities of merchandise can be higher than the cost of carrying a larger amount.
By calculating the cost of carrying inventory, a business can determine the right balance between having too much and too little inventory, which can help to improve overall efficiency and profitability.
Another important reason for calculating the cost of carrying inventory is that it helps a business understand how inventory costs contribute to the overall cost of goods sold. Carrying cost is a component of the overall inventory cost. By understanding how it fluctuates with changes in inventory levels, production schedules, and suppliers, a business can make more informed decisions that ultimately affect the bottom line.
Pro tip: The costs of carrying inventory do not include the cost of producing your finished goods. While your business retains its inventory during production, you shouldn’t conflate these expenses. To track manufacturing costs, be sure to look into the costs of goods manufactured.
What are the components of inventory carrying costs?
Inventory carrying cost consists of the following components:
- Financing costs
- Capital costs
- Scrapped inventory
- Utilities (rent, gas, electricity, etc.)
- Damage
- Obsolescence and dead stock
- Losses
- Insurance
- Payroll*
*To do with handling and other inventory issues — not labor related to production.
How to calculate inventory carrying costs?
Before you get started with the inventory carrying cost calculator, you need to know all the related expenses. Once you have these on hand, you can start going through the following inventory carrying cost formula to better understand how much holding inventory costs you.
First, you need to calculate the yearly cost of holding inventory:
The yearly cost of holding inventory = Capital costs + service costs + risk costs + space costs
Next, you need to work out your total inventory value:
The total inventory value = Sum of inventory costs x stock of available items
And for the final step, you can divide the results to get the percentage value of your inventory carrying cost:
Inventory carrying cost = Total cost of holding inventory / total value of inventory x 100
Let’s look at an example using the inventory carrying cost calculation for a factory with an inventory value of $85,000 over the past year:
- Cost of capital — $18,000
- Service cost — $4,500
- Inventory risk cost — $4,000
- Storage cost — $3,000
The yearly cost of holding inventory = $18,000 + $4,500 + $4000 + $3,000 = $29,500
Now you have the inventory holding cost. You can divide it by the annual inventory value and multiply it to calculate the percentage of your inventory carrying cost:
Inventory carrying cost = $29,500 / $85,000 x 100 = 35%
In this example, inventory carrying cost calculation shows that 35% of the total inventory costs are from keeping items stocked. But what is the number you should aim for?
The average carrying costs for most manufacturers is between 20% to 30%, though going below 20% means lower expenses for you. Using the inventory carrying cost formula can help you determine your percentage, and if it’s above average, you can start taking action to reduce this figure.
Calculating the carrying costs per square foot
Calculating the cost per square foot of storage is an excellent way to make your total carrying cost more understandable. To do that, you need to know the square footage of your warehouse and your total carrying costs.
Then just divide your total carrying cost by total square feet.
Remember, these costs apply if your excess stock sticks around. If you have inventory not being sold, cut your losses, and get rid of it.
It could be that you are paying for your stock many times over. The items you brought in to get you out of a tight spot could slow your business down. Do the benefits of having lots of spare stock outweigh the ever-increasing costs of housing it?
How to reduce inventory carrying costs?
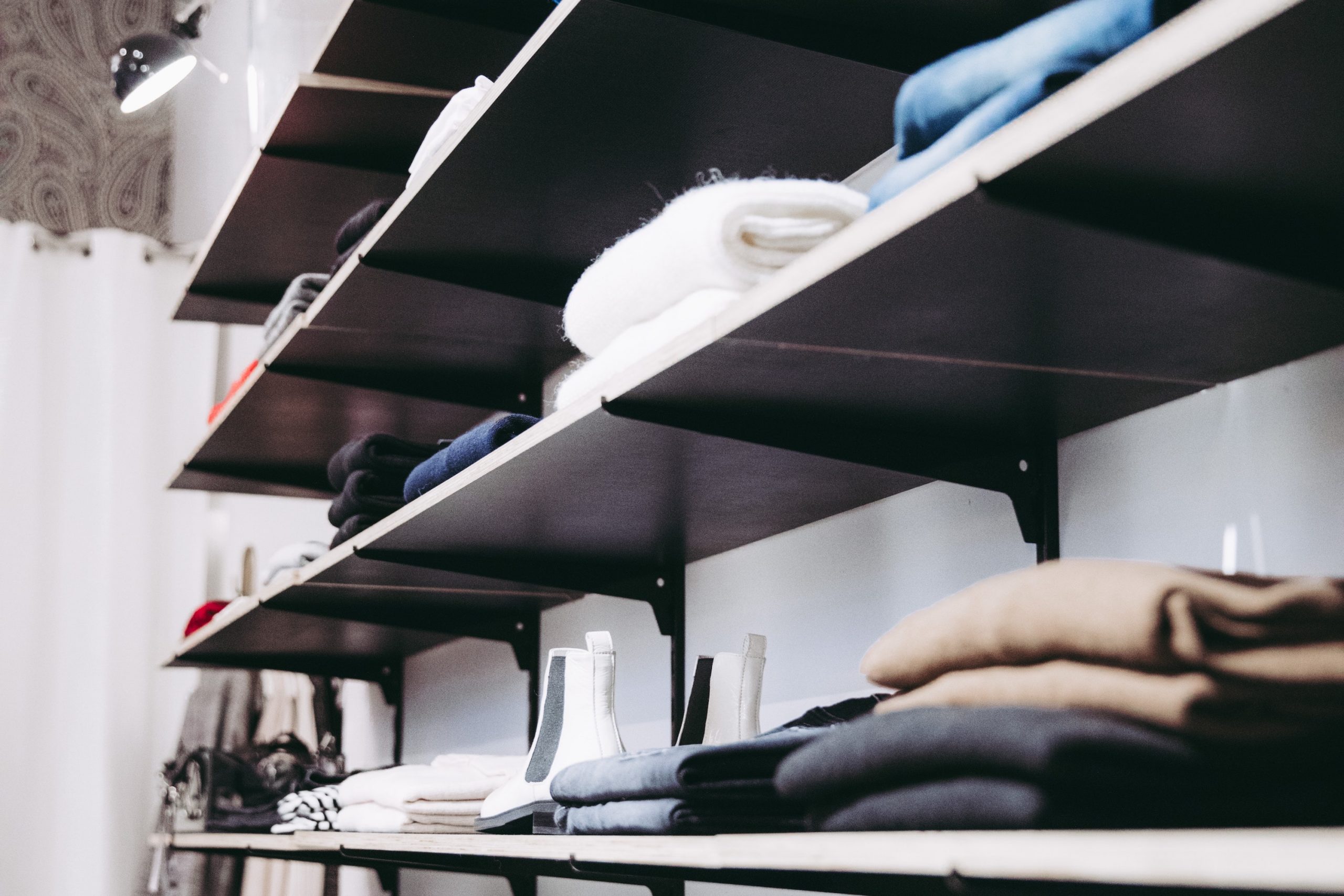
Before we look at ways to reduce inventory holding costs, let’s see if it’s perhaps possible to eliminate these costs altogether.
Is it possible to eliminate carrying costs?
Well, you can try. But no matter how much you sell, you will probably want to keep some stock around for urgent deadlines or samples.
It might be tempting to view all carrying costs as waste, but even lean manufacturing does not mean stripping your business down to its bare bones. It’s all about finding what is optimal for your business:
- If you run an online business, perhaps you don’t need demo stock, but what about safety stock?
- Is your business prepared for eventualities like your machinery or supply chain breaking down?
- Can you keep spare machines on hand, or will you need to rent more?
- Keep some extra stock for emergencies or a second sewing machine?
Sometimes incurring carrying costs could be the cheaper alternative. Every bit of efficiency in manufacturing is gained from some kind of trade-off. This trade-off can come from an upfront cost, which pays off afterward.
How do the masters deal with this?
Avoiding waste is a modern manufacturing principle, coming from the “Kaizen” philosophy which originated in Japan. This was the origin of lean manufacturing, which propelled brands like Toyota to global success. This has evolved into the Agile Scrum Methodology that is suited to scaling manufacturing businesses, as change can be very fluid. Depending on the day’s task, you can pull stuff from one workstation and post it on others.
Because you are running a lean manufacturing business, you can have “sprint” periods for far greater productivity than your normal output.
One downside of this is that it takes time to train staff in these new practices, but considering the benefits down the road, it’s most of the time a smart investment.
Once things get complicated, you can begin integrating an ERP system into your lean manufacturing process. An ERP system can help eliminate waste, improve quality control, and boost efficiency throughout your organization by automating key manufacturing and business processes.
It’s how scaling manufacturers can get one up on large enterprises.
While you may be unable to cut your inventory holding costs down to zero, you can still save cash. So, below you’ll find 5 tips to reduce inventory carrying costs
1. Keep inventory levels up to date
These days, a perpetual inventory system is the only inventory method for scaling businesses.
This inventory management system lets you know exactly how much of everything you have in stock at all times. The more accurate your information, the less time needs to be spent preparing for “what-if” scenarios. Knowing this information takes all the guesswork out of supply orders.
2. Evaluate SKU intensity
Track your sales data to see which product variations are sold as a ratio of how much each is produced.
It could be the case that some of your products sell like hotcakes, and some leave your shop floor rather sluggishly. Once you identify the slow-moving stock, you can focus less on that and more on what is selling. The key is to measure your data effectively with cloud inventory software.
3. Adopt a make-to-order model
One phrase that gets thrown around a lot is economic order quantity (EOQ).
Your EOQ is the optimum stock your business should purchase to reduce annual holding costs as much as possible. However, some of the assumptions it makes are unsuitable for companies. A better compromise is to adopt a just-in-time inventory approach to making orders.
4. Improve your logistics
Are there obstacles in your production process increasing your lead time? They could be physical or procedural. Maybe distance could halt your productivity.
Are you buying materials that take weeks to come into your workshop? Does your staff have to spend valuable minutes locating and retrieving materials? Sometimes shaking up things in your factory can pay off.
5. Adopt the Kaizen philosophy
Make striving for improvement an integral part of your company’s culture:
- How can costs be cut?
- Can something be done quicker?
- Why are my raw materials going on an epic journey rather than coming straight to me?
These are just some of the questions you can ask yourself when evaluating the efficiency of your production line.
You might now be thinking all of this is easier said than done. Well, it might be easier than you expect.
Reducing inventory carrying costs with inventory management software
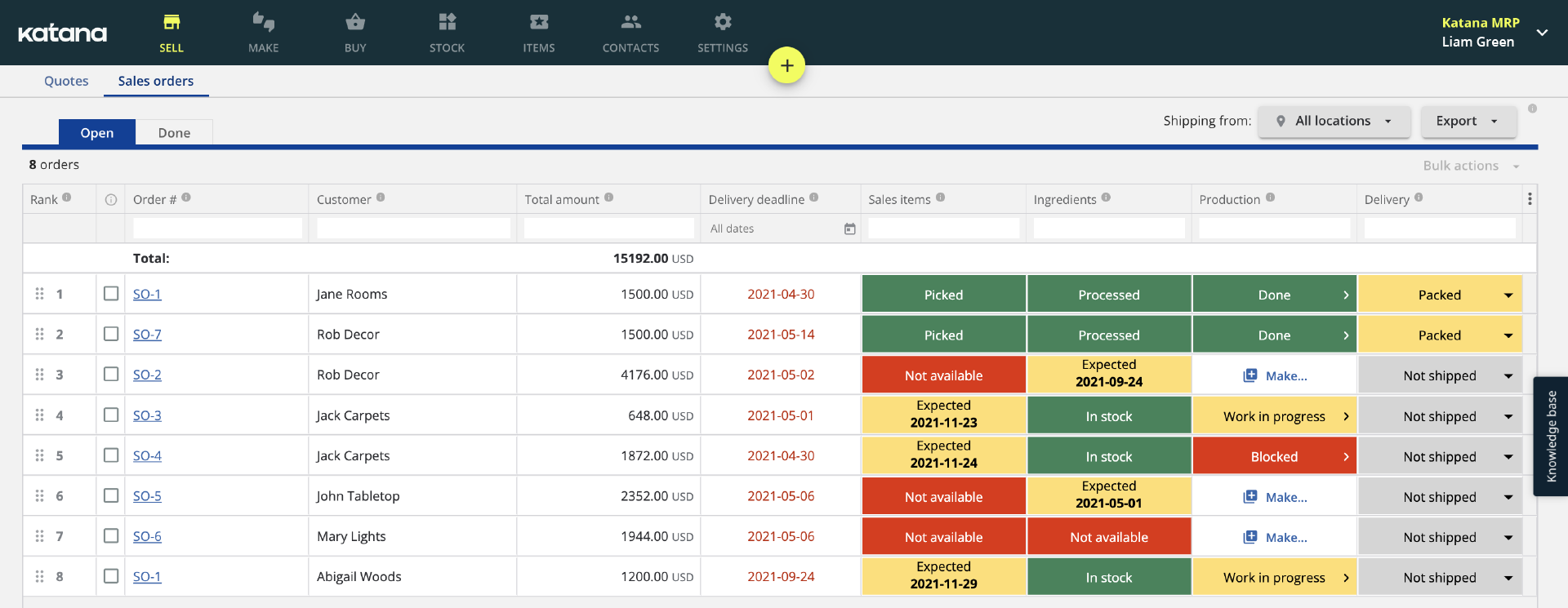
If you really want to get your carrying costs under control, you shouldn’t be relying on doing your inventory carrying cost calculation in Excel. The easiest way to calculate your carrying costs and reduce them is by implementing a manufacturing ERP.
Katana’s cloud inventory software helps streamline inventory management, order fulfillment, manufacturing operations, and other areas of your business, reducing the need for manual intervention and increasing efficiency. All of these factors can contribute to reduced carrying costs over time.
Implementing Katana will help you to reduce carrying costs by:
- Spending fewer man-hours counting and finding stock
- Selling stock before it becomes obsolete
- Getting finished products shipped before these become a loss for your business
In addition, Katana integrates with the best business tools, including:
Integrating your existing software with Katana gives you a unified experience and ensures your data is synced across all platforms.
Get inspired by Samurai discipline and cut costs with Katana — request a demo today!
Table of contents
Inventory management guide
More on inventory management
Get visibility over your sales and stock
Wave goodbye to uncertainty by using Katana Cloud Inventory for total inventory control
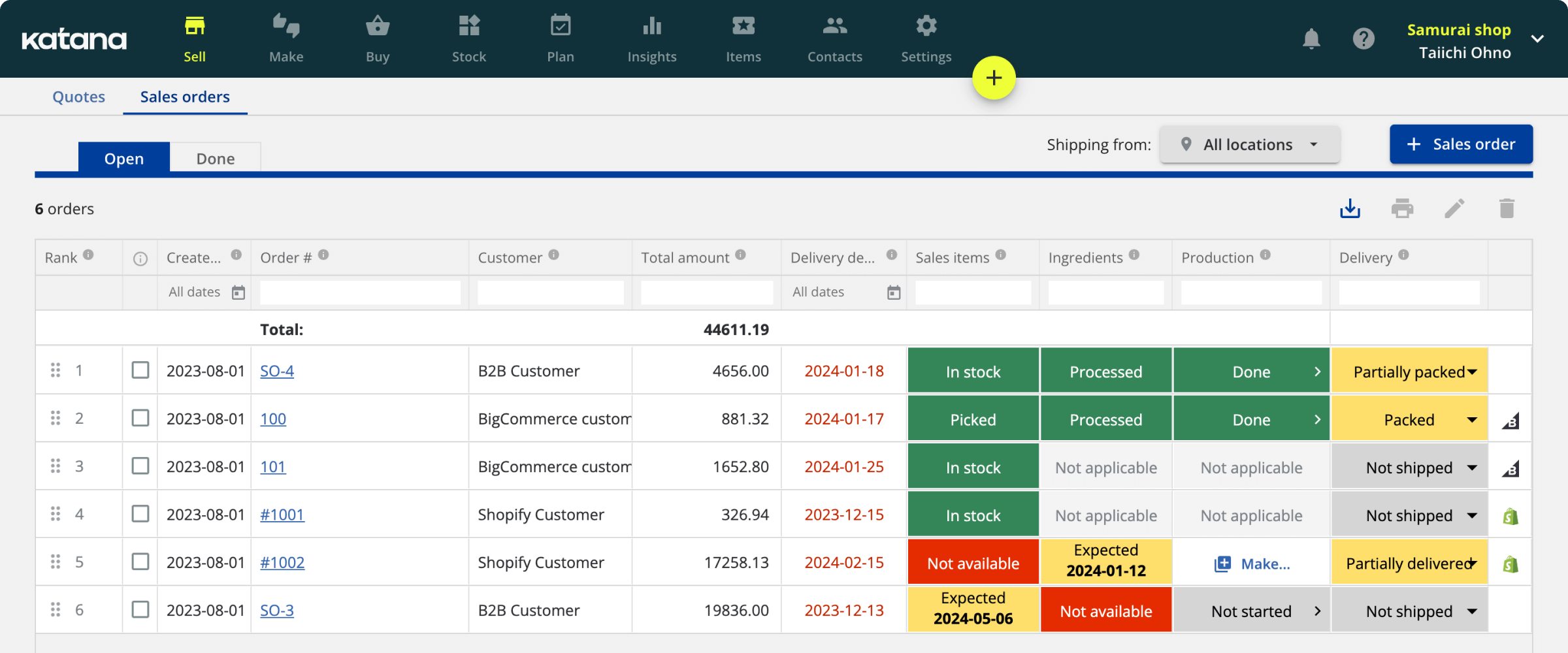