Manufacturing accounting:
A unique approach for a unique sector
As a manufacturing business, you understand the crucial link between a seamless production line and achieving lasting success. The efficient flow of operations, from raw materials to finished products, is vital to meet customer demands and maintain a competitive edge in the industry.
However, the significance of maintaining a firm grip on your financial affairs should not be underestimated.
Effective cost management lies at the core of the manufacturing sector’s financial stability and long-term profitability. By implementing sound strategies and prudent practices, you can optimize financial performance, enhance decision-making processes, and safeguard your business against potential risks.
This blog post will explore a range of indispensable tips and proven strategies specifically tailored to the unique challenges of accounting in manufacturing. Whether you possess years of experience in the field or are just beginning to navigate its complexities, these insights will help you ensure your financial operations run smoothly.
Download the ultimate guide to manufacturing accounting
A comprehensive ebook with everything you need to know about accounting for manufacturers.
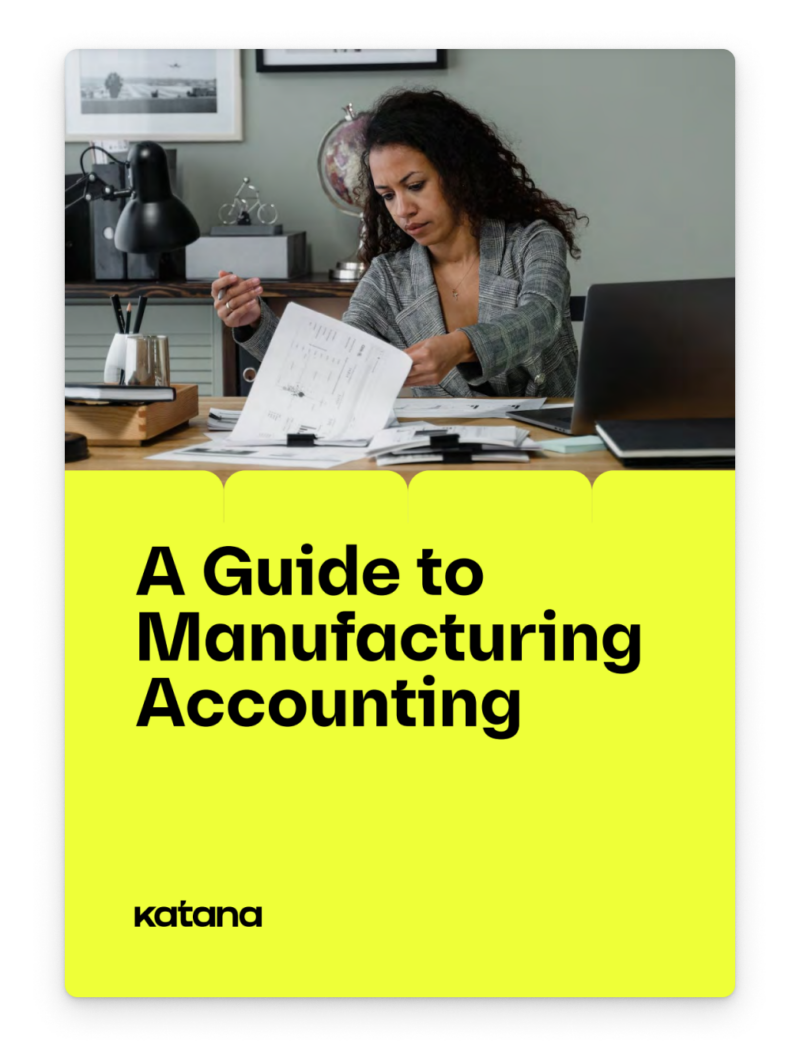
What is manufacturing accounting?
Manufacturing accounting refers to the specialized branch of cost accounting that focuses on the financial management and control of manufacturing operations within a business. It involves the application of accounting principles and practices to accurately track, analyze, and report the financial aspects of the manufacturing process.
In manufacturing accounting, various financial aspects are addressed, including the cost of raw materials, labor, overhead expenses, and inventory valuation. The primary objective is to provide insights into the financial performance and profitability of manufacturing activities, enabling informed decision-making and effective cost management.
Manufacturing accountants are responsible for tasks such as recording production costs, calculating product costs, analyzing variances between expected and actual costs, and providing financial reports tailored to the manufacturing sector. They play a critical role in helping businesses understand the true costs of their products, identifying areas for cost optimization, and ensuring compliance with accounting standards and regulations specific to the manufacturing industry.
By implementing robust manufacturing accounting practices, businesses can gain a comprehensive understanding of their financial performance, make informed decisions to improve efficiency and profitability, and maintain financial transparency throughout the manufacturing process.
What type of accounting is used in manufacturing?
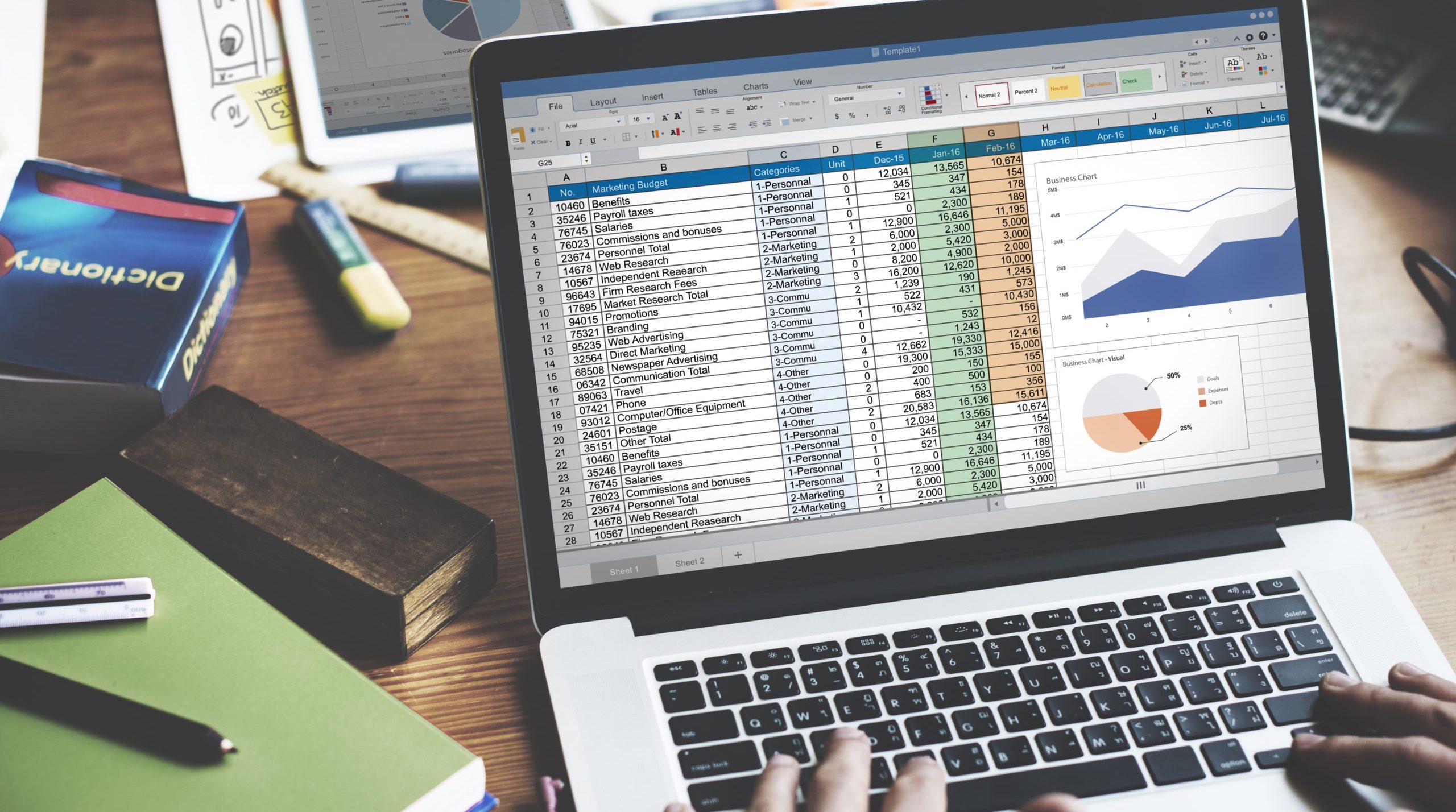
In manufacturing, a distinct form of accounting is employed to meet the specific demands of this industry. Manufacturing accounting entails a dedicated set of requirements, necessitating specialized software and processes to effectively monitor and record production costs associated with each product.
To ensure accuracy and precision, a tailored approach is crucial. This is typically achieved by implementing a double-entry system, which diligently tracks all financial transactions and safeguards against errors or discrepancies.
Within manufacturing accounting, particular emphasis is placed on meticulously tracking and allocating expenditures related to labor, overhead, and other associated costs. By doing so, businesses gain a comprehensive understanding of the financial performance of their manufacturing processes, enabling effective decision-making and proactive cost management.
By employing this tailored approach to manufacturing accounting, businesses can effectively assess and analyze their production costs, identify areas for optimization, and ultimately enhance their financial performance within the dynamic manufacturing landscape.
What is different about accounting for manufacturing costs?
Accounting for manufacturing costs differs from general accounting practices in several key aspects. The distinctive nature of manufacturing operations necessitates specialized approaches and considerations in the accounting process. Here are six more notable differences:
- Cost classification — Manufacturing accounting involves classifying costs into different categories, such as direct materials, direct labor, and manufacturing overhead. These classifications allow for a more accurate assessment of the various components contributing to the overall cost of production.
- Inventory valuation — Manufacturing businesses typically maintain inventories of raw materials, work-in-progress (WIP), and finished goods. Accounting for manufacturing costs requires tracking and valuing these inventories using methods such as the moving average cost or the first-in, first-out (FIFO) method. This enables businesses to determine the true cost of goods sold and the value of remaining inventory.
- Overhead allocation — Manufacturing overhead costs, such as rent, utilities, equipment depreciation, and indirect labor, are distributed across products or production units. This allocation is often based on predetermined cost drivers, such as direct labor hours or machine usage. Accurately assigning overhead costs to products ensures that the full cost of production is accounted for.
- Work-in-progress (WIP) accounting — Manufacturing accounting includes tracking costs associated with products that are still in the production process, known as work-in-progress (WIP). This involves estimating the percentage of completion for each product and allocating the appropriate costs accordingly. WIP accounting provides visibility into the costs incurred at various stages of production.
- Variance analysis — Manufacturing accounting incorporates variance analysis to compare actual costs with standard or budgeted costs. Variances, such as material usage or labor efficiency variances, help identify deviations from expected costs and enable businesses to take corrective actions to control costs and improve operational efficiency.
- Specific industry regulations — Manufacturing businesses must adhere to industry-specific regulations and accounting standards, such as the Generally Accepted Accounting Principles (GAAP) or International Financial Reporting Standards (IFRS), which include specific guidelines for accounting treatment and disclosure of manufacturing-related transactions.
Overall, accounting for manufacturing costs requires a specialized understanding of the unique aspects and complexities of the manufacturing industry. By employing appropriate accounting practices, businesses can accurately track costs, make informed decisions, and effectively manage their financial performance.
Accounting for manufacturers in practice
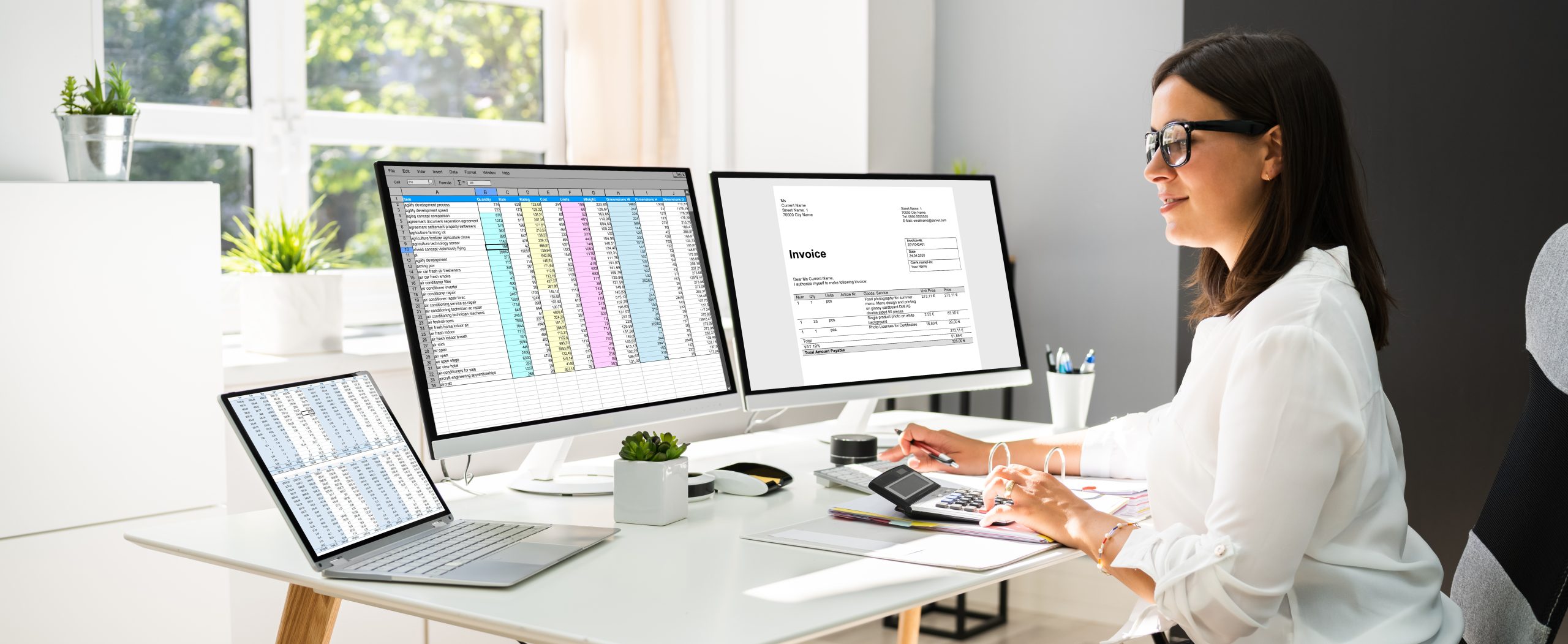
Now that we have gained a deeper understanding of the theoretical foundations of the manufacturing accounting process flow, let’s explore how it functions in real-world scenarios.
Cost accounting
Cost accounting in manufacturing plays a pivotal role, as it involves diligently monitoring the costs associated with producing a specific item. From raw material expenditures to labor and overhead fees, every aspect of cost incurrence is carefully recorded.
By applying inventorial techniques to these costs, businesses can identify areas where spending can be reduced, efficiency can be improved, and profitability can be increased.
Integrated invoicing and billing platforms, such as Xero and QuickBooks Online, offer invaluable support in streamlining costs associated with specific products and batches, ensuring accuracy and efficiency in cost management.
Job costing
Employing job costing enables businesses to assign costs to each production run or batch of products, facilitating a comprehensive tracking of expenditures specific to each job. The resulting data can then be leveraged to make informed pricing decisions, optimize production processes, and allocate resources effectively.
Accounting platforms like Xero and QuickBooks Online provide integrated cost management solutions tailored to manufacturing-specific expenses, encompassing labor, materials, and overhead. This cohesive approach to job costing empowers businesses to gain insights into the true costs associated with each production endeavor.
Inventory management
An integral component of manufacturing accounting lies in efficient inventory management. By carefully overseeing inventory levels, businesses can strike a delicate balance, ensuring they have sufficient raw materials and finished goods to meet customer demand without excessively tying up financial resources in excess inventory.
Effective inventory management not only minimizes disbursement but also enhances operational efficiency and increases profitability. Manufacturing accounting systems offer valuable visibility into key aspects of inventory management, encompassing goods acquisition, stock valuation, and the calculation of moving average costs (MAC). These insights enable businesses to optimize their inventory management strategies and achieve a more streamlined and profitable manufacturing process.
Manufacturing accounting made simple
Book a demo to get all your questions answered regarding Katana’s features, integrations, pricing, and more.
Best practices in manufacturing accounting
Manufacturing accounting is a complex process that requires specialized knowledge and skills. In order to ensure accuracy and efficiency in the process, there are certain best practices that should be followed.
- Automation is key — Automating the process of invoicing, payments, and other financial transactions will help to ensure accuracy and consistency.
- Implement robust inventory control — Keeping track of inventory is crucial in the manufacturing industry, and having a reliable system in place to track and manage inventory is essential.
- Track production costs — Production costs are one of the main expenses associated with the manufacturing process, and they must be tracked and monitored on a regular basis in order to ensure accuracy.
- Utilize data analytics — Data analytics can be used to gain a better understanding of the financial performance of the production methodology and help to make more informed decisions.
Accounting for manufacturing companies becomes significantly more efficient and beneficial when these best practices are followed.
What to look for in manufacturing accounting software
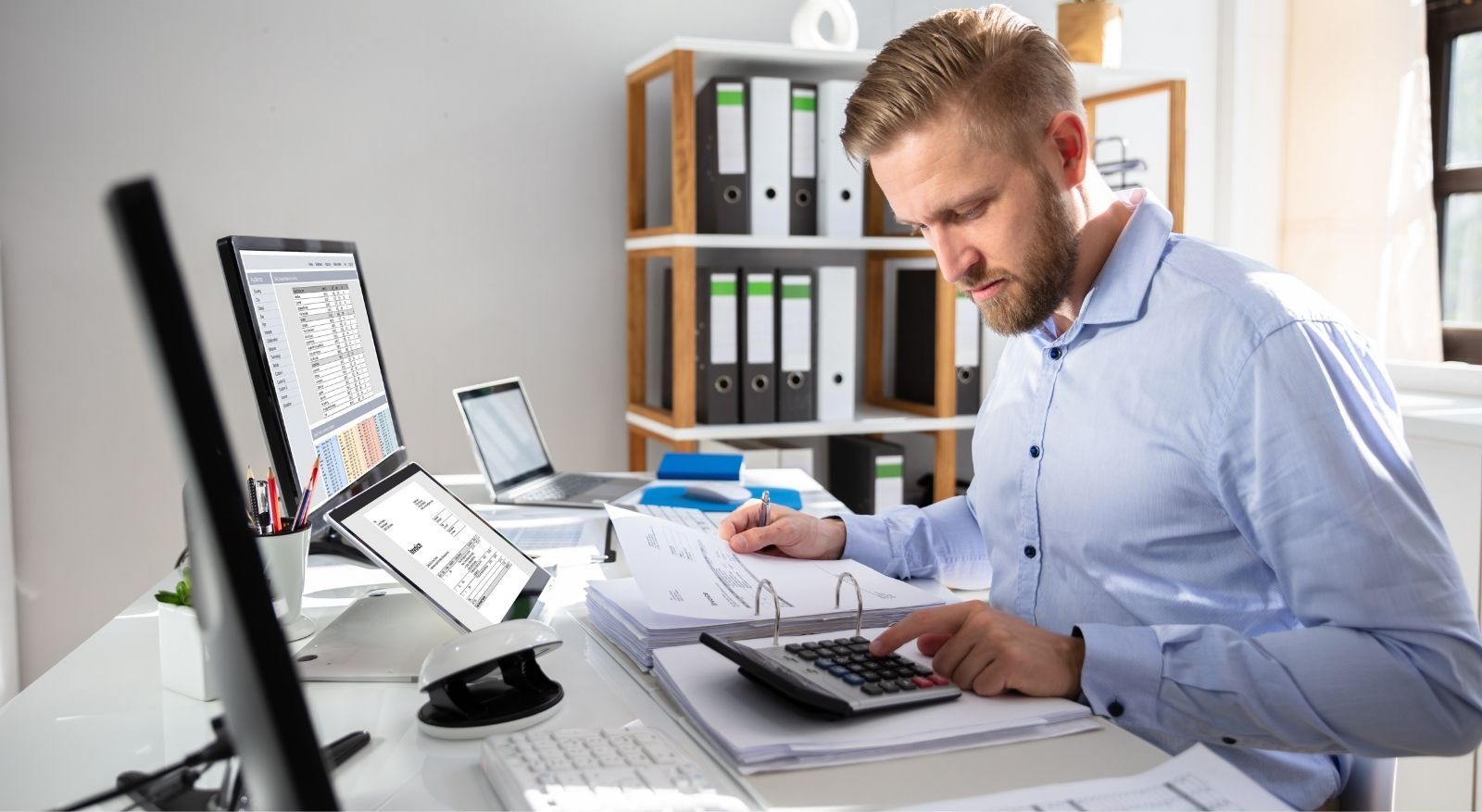
Your manufacturing business is as creative and unique as you are, so it goes without saying your accounting software should be too. Manufacturers will often seek out a modularized all-in-one solution, where every facet of the business, such as inventory, tracking, production, and planning, are combined into one system. These highly extensible systems are known as enterprise resource planning (ERP) platforms.
With numerous options available, selecting the right manufacturing accounting software package can be a daunting task. Moreover, the cost of such software can be substantial, making it crucial to make an informed investment decision.
Let’s explore the essential features that every excellent accounting software for manufacturing should include.
Production cost tracking
An indispensable feature to look for is robust job costing capabilities. This enables you to track both direct and indirect costs associated with producing each unique product or batch. It encompasses expenses related to overhead, labor, and raw materials.
Advanced job costing functionalities empower you to identify areas for cost reduction, enhance productivity, and boost profitability.
Reporting capabilities
The software should have the ability to generate financial reports and provide insightful analysis of production performance. This includes financial statements, production reports, and more.
With robust reporting features, you gain valuable insights into your operations and identify areas for improvement.
Data analytics
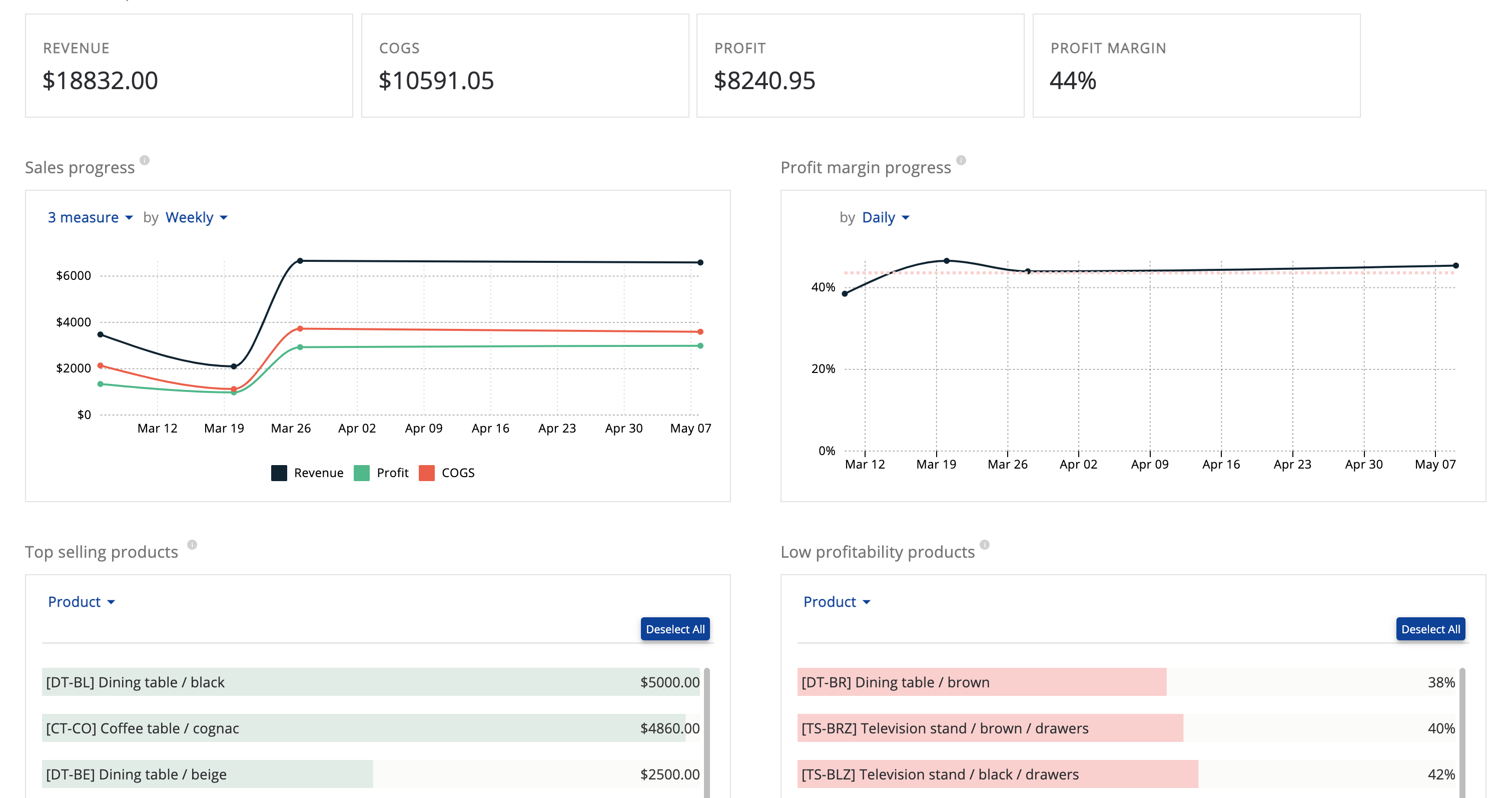
To gain a deeper understanding of manufacturing costs and make informed decisions, the software should incorporate data analytics capabilities. This allows you to analyze data and derive insights into the overall financial position of your business processes.
Inventory control
Good manufacturing accounting software must include powerful inventory management capabilities. This involves effectively managing inventory levels, bills of materials, and the expenses associated with producing specific products or batches.
With proper inventory management, you can ensure a steady supply of materials while keeping expenses under control.
Systems integration
It is crucial to select accounting software that seamlessly integrates with other essential programs, such as inventory management, production scheduling, and invoice generation. Compatibility with existing management tools and databases minimizes the risk of data loss or disruption to ongoing processes. Integration streamlines operations, automates tasks, and enhances overall efficiency.
By integrating your accounting software with Katana’s cloud manufacturing platform, you’ll get all these essential features and more. Get a demo of Katana, and see why thousands of manufacturers trust Katana to manage their entire business. Sign up for a demo today and unlock the power of streamlined manufacturing operations.
Glossary of manufacturing terminology
Finally, manufacturing accounting terminology can be complex, so it’s essential to understand key terms and definitions. Here are some common terms used in the manufacturing industry:
- Material requirements planning (MRP) — A production planning and scheduling system that determines the materials and quantities required to produce a product based on its production schedule and inventory levels.
- Bill of materials (BOM) — A list of all the materials required to produce a product, including raw materials, components, and subassemblies.
- Work-in-progress (WIP) — Inventory that is in the process of being produced but has not yet been completed.
- Cost of goods sold (COGS) — The total cost of producing and selling a product, including direct materials, labor, and overhead costs.
- Job costing — A cost accounting system that tracks the costs associated with producing a specific product or batch of products.
- Moving average cost (MAC) — A cost accounting method that calculates the average cost of inventory over a period of time, which is used to determine the cost of goods sold.
- FIFO and LIFO — First-in-first-out and last-in-first-out are cost accounting methods assuming the first items purchased are the first items sold and the last items purchased are the first items sold, respectively.
- Backflush costing — A cost accounting system that records the cost of producing a product at the time it is completed rather than at each step of the production process.
- Activity-based costing (ABC) — A cost accounting system that assigns costs to specific activities or processes based on their use of resources.
- Enterprise resource planning (ERP) — An integrated software system that manages all aspects of a business, including accounting, inventory management, and production scheduling.
- Just-in-time (JIT) — A production strategy that emphasizes the delivery of products and materials just in time for production in order to minimize inventory costs.
- Total quality management (TQM) — A management philosophy that emphasizes the importance of quality in all aspects of the production process in order to reduce costs and increase customer satisfaction.
Table of contents
Accounting Guide
Readers also liked
Get visibility over your sales and stock
Wave goodbye to uncertainty by using Katana Cloud Inventory for total inventory control
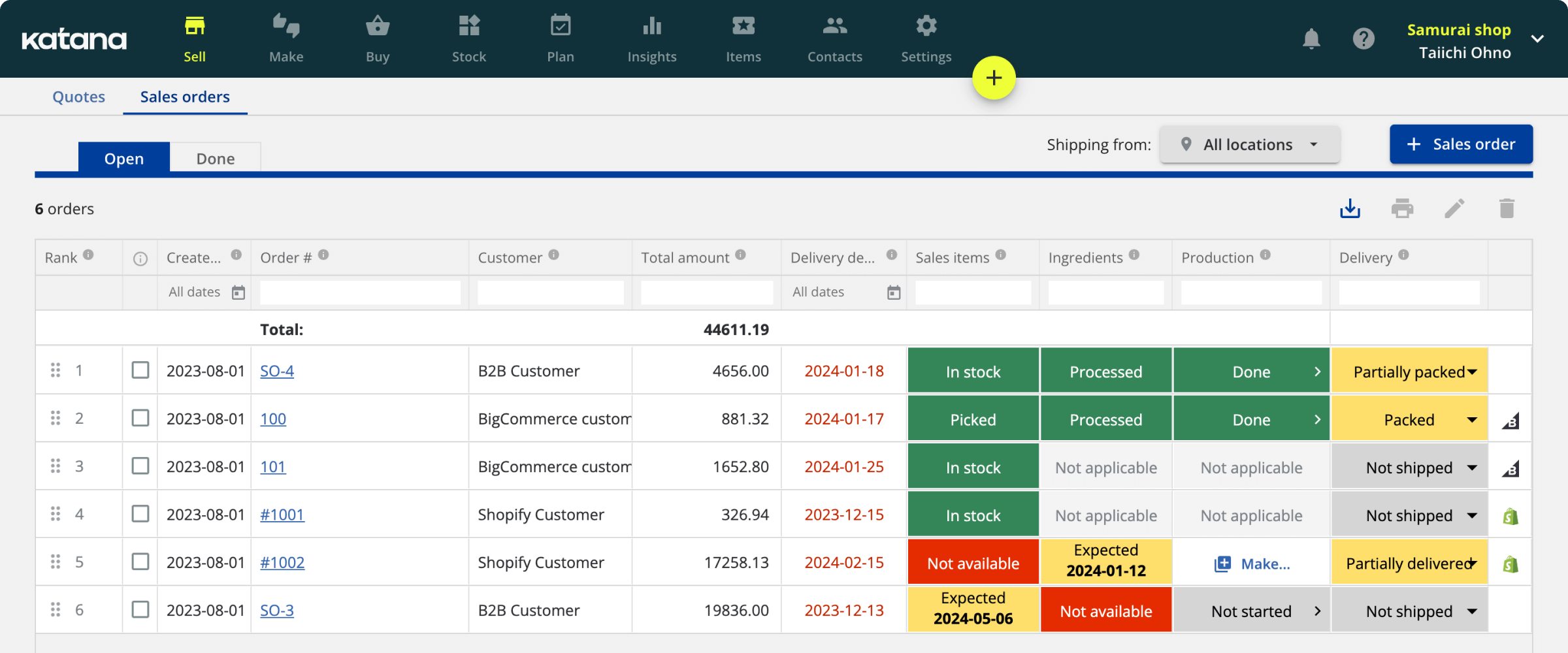