Reorder point formula to maximize sales
Every manufacturing business out there faces questions like:
- How much material do I need to order from my supplier?
- When do I need to place my next supply order?
- When do I generate a new manufacturing order?
If you’re struggling to answer these questions, you can use a reorder point calculation to help you out.
Holding inventory incurs expenses, known as carrying costs. For example, it could be $3 per unit or 15% of an item’s price. So, producing too many finished goods could end up evaporating your profit margin.
This article looks into the reorder point formula, safety stock, and how to calculate it all. It also gives you an Excel formula for inventory reorder points, shows you how to use reorder level formula in Excel, and explores how you can take your order efficiency to the next level with cloud inventory software.
What is a reorder point?
The reorder point, sometimes referred to as ROP, is a stock threshold you don’t want to go below. The ideal inventory reorder point allows for adequate time to make a new order before your stock is depleted. Reorder point is the metric that tells you two essential things:
- When it is the right time to order more materials from your supplier(s)
- When it is the right time to manufacture more products by creating a manufacturing order (MO)
This means your stock will be regulated much better, with fewer interruptions like supply chain breakdowns or production bottlenecks.
Your inventory reorder point levels should cover every item in stock, including all different SKUs. You can link your inventory levels with each product’s bill of materials (BOM) and track it with MRP software.
For example, Katana lets you set reorder points and highlights when you need to order more materials to keep ideal inventory levels.
It’s important to learn how to calculate reorder points because as your business grows and handles more products and SKUs, the more difficult it’s going to be to maintain your ideal stock levels.
Next, let’s look into how to calculate reorder point with the reorder point formula. This doesn’t have to be done by hand — a good cloud inventory software can do it for you to cut back on some admin time.
Reorder point and safety stock
Your safety stock is your trump card in emergencies, but you shouldn’t have to keep dipping into it. The ideal reorder point ensures that your business does not fall below your safety stock levels. If you miss your reorder point and use some safety stock, you need to order even more materials to replace that safety stock once the supply order arrives.
If you don’t, your safety stock will eventually deplete to nothing, and since more orders cost more money, you should try to avoid this.
Therefore, an ideal reorder point is typically a little higher than your safety stock level to factor in delivery time.
But how much higher does it need to be? It depends on your reorder’s average lead time and demand during the lead time. Why is this the case? Well, let’s take a look at these two reasons:
- Delivery time — When you place a new order, it does not arrive at your warehouse immediately. It may take weeks or sometimes even months for the order to be processed and shipped to your desired location
- Material use — During the lead time, you keep using the remaining stock in your warehouse for your manufacturing and sales operations
Therefore, a good reorder point also needs to consider the number of ordered items left in your warehouse by the time the materials arrive. It is essential to take this lead time into account. Otherwise, you run the risk of running out of stock before the reorder arrives. Your reorder point should make production in your business flow, not stop and start.
Setting your reorder point too late defeats its purpose.
Setting it too early means it sits around doing nothing for too long, increasing carrying costs and harming your bottom line. Reorder point calculation formula and safety stock calculation formula are, in a way, two sides of the same coin:
- Safety stock — The amount of inventory a business keeps in the warehouse to protect against spikes in demand or shortages in supply
- Reorder point — The last line of defense before you resort to using safety stock and opening backorders. It keeps your safety stock in reserve for true emergencies only and makes sure that each material you use is reordered in line with its usage
Therefore, you don’t have an overabundance or drought of stock.
You get a perfect balance, safe in knowing you can deal with anything, and keep going. Read on to find out how to use a reorder point formula to set your reorder point.
How to calculate your reorder point?
To calculate your reorder point, you simply need to multiply the average unit sales by the average lead time and include your safety stock levels. Before calculating your reorder point, make sure you know your:
- Average unit sales per day
- The average lead time
- The amount of safety stock you have on hand
Reorder point equation
This is how your reorder point calculation should look on paper:
Reorder point = Average daily usage x average lead time in days + safety stock
Reorder point formula Excel
Below you’ll find an Excel You can calculate your reorder point in an Excel spreadsheet (or a Google sheet or another sheet) with the following reorder point formula:
=SUM(F2+G2)
- Column F — Safety stock
- Column G — Lead time demand
Here is an example of the Excel reorder point calculator:
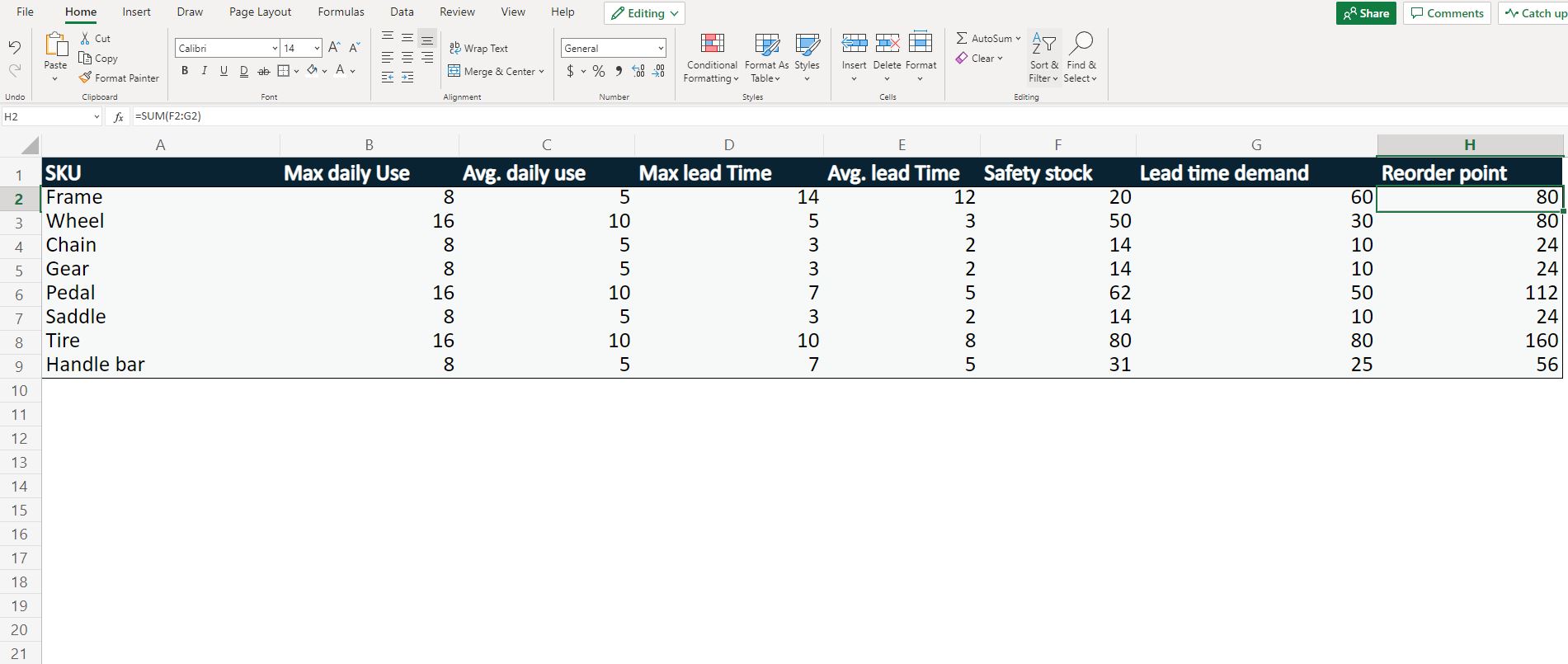
Using this reorder point formula excel template removes the headache of calculating your reorder point yourself.
How to calculate safety stock?
To calculate your safety stock, which should be considered with your reorder point, you need to follow this formula:
Safety stock = (maximum daily usage x maximum lead time in days) – (average daily usage x average lead time in days)
If you want to dive deeper into the topic, you can read more about calculating your safety stock here.
What is the average daily usage?
Depending on what you’re looking into, the average daily usage is the number of raw materials you consume or finished goods you sell in one day.
What is the average lead time in days?
The average lead time in days is how long it takes for your raw materials to be delivered from a supplier or how long it takes you to manufacture a product. The delivery time and manufacturing rate are also part of understanding your manufacturing lead time.
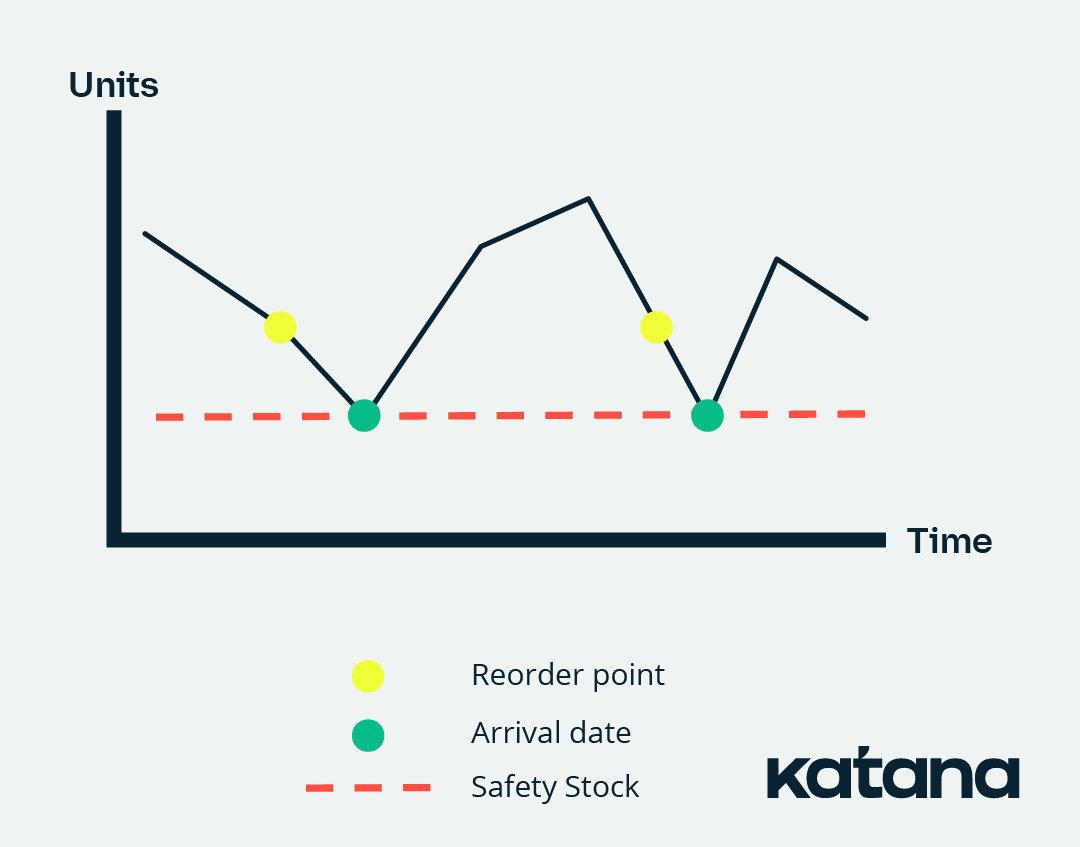
Reorder point formula and safety stock formula combined
Let’s put the reorder point formula to the test and use it in a scenario to get a better understanding. Firstly, just for the recap, the reorder point formula is:
Reorder Point = Average daily usage x average lead time in days + safety stock
So, let’s say you’re a manufacturer that:
- Uses ten units of a specific raw material per day
- Has a resupply or delivery of this raw material that takes seven days to arrive
- Keeps a safety stock level of the raw material at 50 units
Using this information, your reorder point formula is going to look like this:
(10 x 7) + 50 = 120
Using the reorder point formula, you can calculate that your reorder point is 120 units. The moment your inventory levels fall below this number, you will need to place a new order.
Reorder quantity formula
Now you know how and when to order new materials to avoid stock-outs. However, the real question is how much material you have to order to keep your productions running smoothly. One option would be to calculate the economic order quantity (EOQ) but if you’re looking for a quick and easy approach, you can use the reorder quantity formula below:
Reorder quantity for raw materials = Average daily units used x average lead time
Using the example above, a manufacturer who uses ten units of raw material a day and has a delivery time of seven days for a resupply would mean the reorder quantity formula would look like this:
10 x 7 = 70
The reorder quantity formula is going to help you calculate your reorder point formula. The difference between the two is:
- Reorder point — A level when a manufacturer or manager needs to order more inventory
- Reorder quantity — The amount of a particular item that needs to be reordered
EOQ reorder point
EOQ stands for economic reorder quantity and it’s a concept in inventory management that refers to the amount of product that should be ordered to minimize both the cost of holding inventory and the cost of ordering new inventory. So, instead of just looking at lead times and average demand, EOQ also considers costs associated with ordering and holding inventory.
To see how to calculate EOQ reorder point, you can check out the formula below:
EOQ = √[2(annual demand x ordering costs / carrying costs)]
Perfect your order fulfillment with your accurate reorder point policy
When calculating reorder point levels, pay attention to changes in the underlying metrics.
Daily usage and lead time are not carved in stone. Like everything else, they are subject to change, which means your reorder points are too. So, although having an effective reorder point policy means you have freed up more time in your week, you still need to stay on top of things by making new reorder point calculations.
Reorder point levels may increase as your business grows, and they may fluctuate depending on whether you are approaching high or low season.
Therefore, you should recalculate reorder point levels from time to time. A good tip to follow would be to revisit these calculations every three to four months. However, using inefficient spreadsheets can be tedious, time-consuming, and lead to business-critical errors. This is why many manufacturers and managers turn to cloud manufacturing software, like Katana, to help them automate their reorder points.
Reorder faster and more efficiently with Katana’s cloud inventory platform
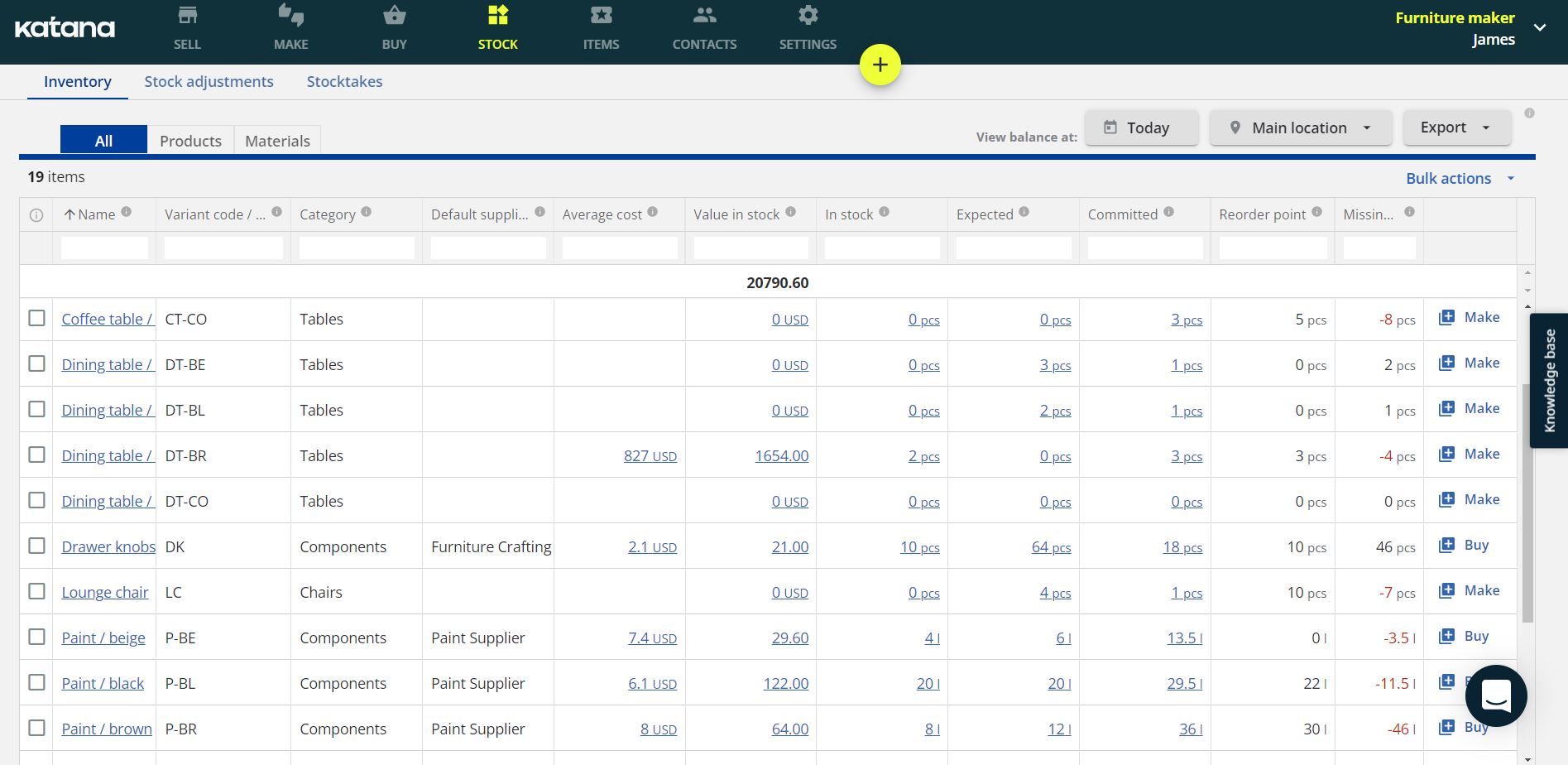
Katana’s cloud inventory software is an all-in-one solution that allows manufacturers to take control of their:
- Inventory management (raw materials, WIP, and finished goods)
- Production planning and scheduling
- Procurement process
Using manufacturing ERP software like Katana allows your company to set reorder points for each raw material and finished product variant under your roof.
Everything is tracked automatically, so you can prevent cognitive overload as your business grows. Increased success and sales demand do not have to become a burden. Katana automatically flags the product and material variants that have dipped below their reorder point, allowing you to identify the areas that require action.
It’s an automatic alarm clock that tells you when you need to place an order, so you never miss a deadline and get your customer wait times to a record low.
This makes setting up and managing your reorder points a breeze. In addition, it will save you time, reduce the chance of human errors, and streamline your entire production process. Request a demo today and see for yourself why thousands of manufacturers use it daily to manage their business.
Table of contents
Inventory management guide
More on inventory management
Get visibility over your sales and stock
Wave goodbye to uncertainty by using Katana Cloud Inventory for total inventory control
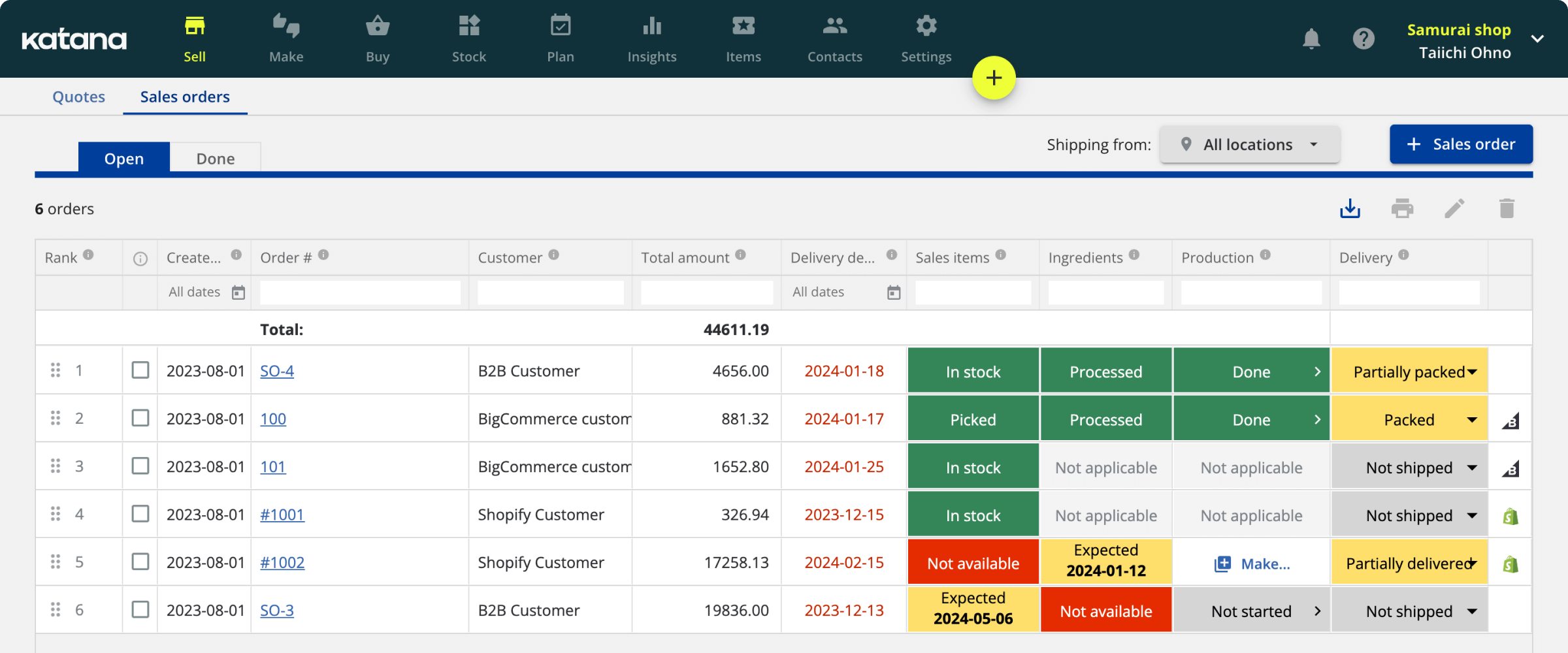