A guide to MRO inventory management
When companies allocate resources to managing inventory, it often focuses on three types. These materials go into products or services (finished goods inventory), components used in the production process (work-in-process inventory), and MRO inventory.
Unfortunately, some small and medium-sized business owners may think, “what does MRO inventory stand for?” That’s a problem many new entrepreneurs face, as they have been hyper-focused on the end product or service and overlook many other things needed to maintain a successful manufacturing process.
Even though it is sometimes overlooked, MRO inventory is still an important part of the resource allocation puzzle, and below, we’ll walk you through everything there is to know about what it is, how to manage it, and some of the current best practices to keep your carrying cost low.
Want to see Katana in action?
Book a demo to get all your questions answered regarding Katana’s features, integrations, pricing, and more.
What is MRO inventory?
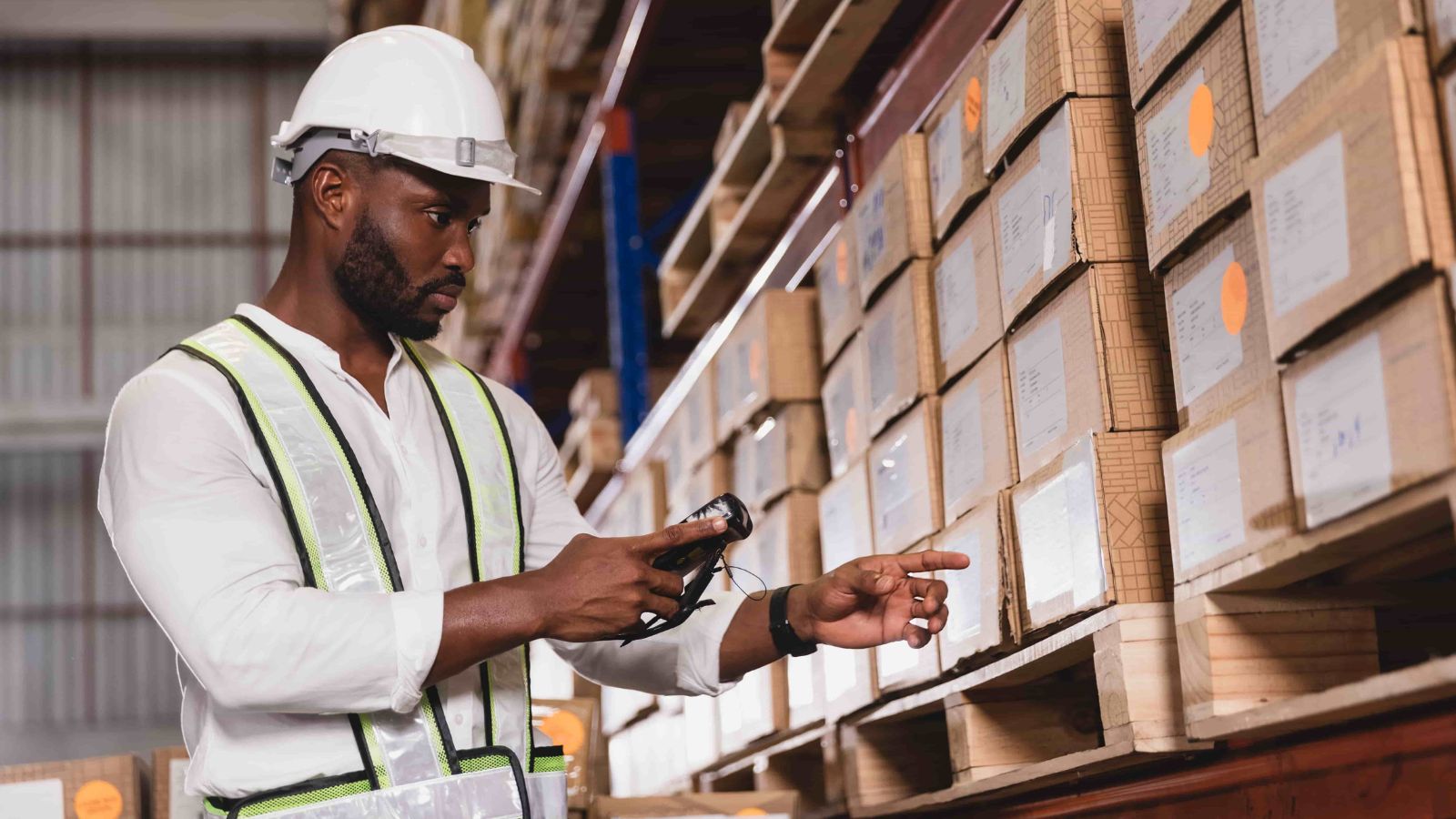
MRO inventory stands for maintenance, repair, and operations inventory. These are the materials and supplies required to keep a production process running but are not considered direct inputs into that process.
That’s the basic MRO inventory definition.
This inventory includes tools, machines, raw materials, office supplies, and other equipment or spare parts. Sometimes, it might refer to the staff required to maintain these things or provide support services.
The key thing to remember is that MRO items are anything that helps keep the process running but is not part of the final product or service.
MRO inventory example
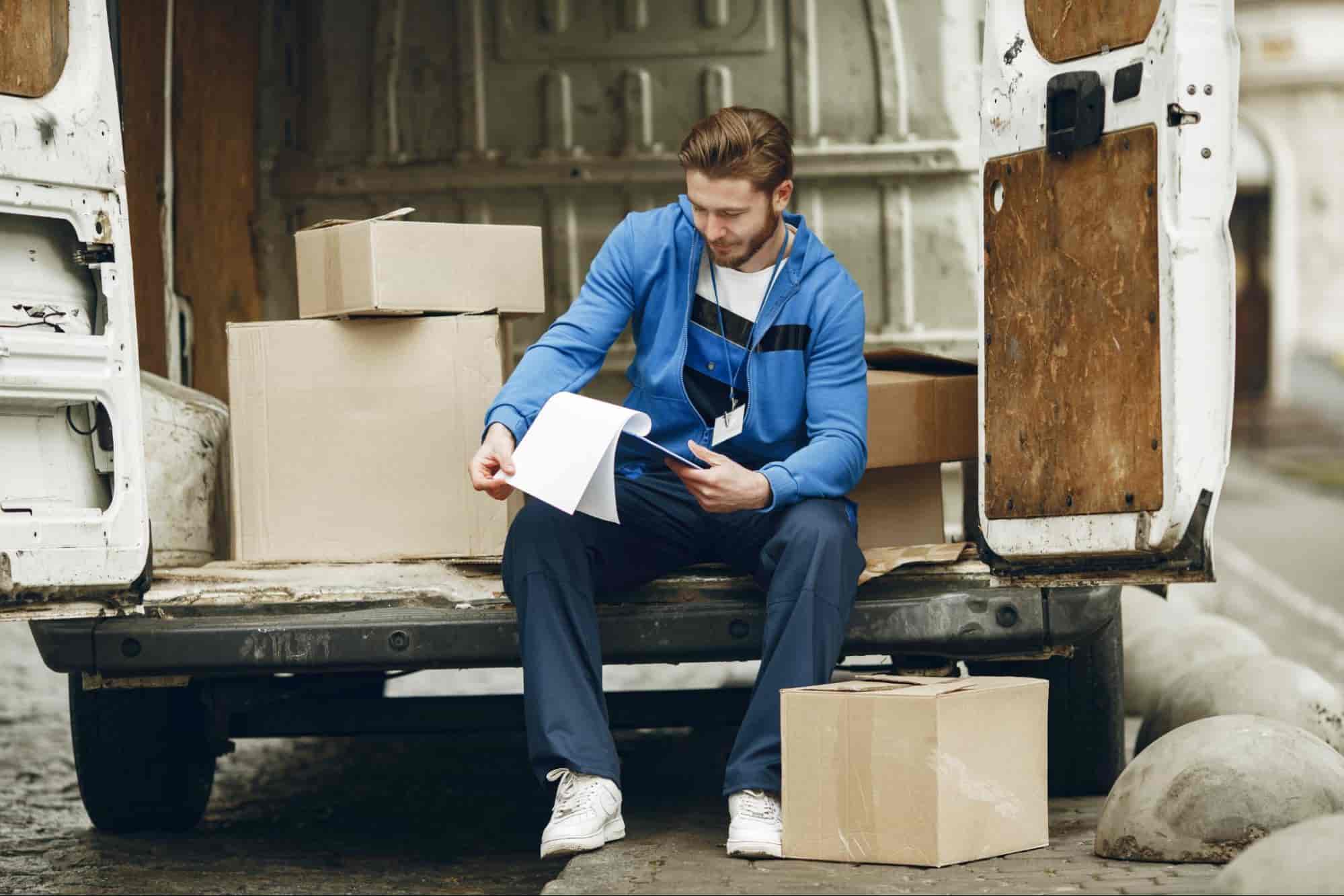
Here’s an example.
At MakeBelievers, our hypothetical company, they produce nightlights and mobiles that are meant to inspire calm dreams in small children. The direct inputs into this process would be the wood, paint, plastic, and other materials that make up the physical product.
The MRO inventory for MakeBelievers might include items like saws and other woodworking tools, ladders and other supplies needed to assemble the mobiles, packaging supplies like boxes or bubble wrap, and materials used in maintenance and repairs. These are necessary to produce the final product but are not part of it.
It also might include:
- The computers and software that help design and sell the products
- The personal protective equipment (PPE) required by line workers
- The furniture in the office where the product is designed
- The vehicles used to transport supplies or finished goods
- The coffee maker in the break room
- The janitorial supplies needed to keep the production plant clean
In each of these cases, these are all things that are necessary for MakeBelievers to function but are not part of the final product. These can seem like small details, but they can add up to a significant chunk of inventory that needs to be managed.
It is also easy to see how poor inventory control can make things messy, causing inefficiencies and higher costs. This is why accurate demand planning, inventory forecasting, and optimization are so important.
What is MRO inventory management?
MRO inventory management is the process of obtaining, storing, tracking, using, and reacquiring the spare parts, tools, machines, and other materials required to maintain a production process. It does not include the materials present in the final product but everything else required to keep the process running.
Many companies find this challenging, as managing MRO inventory is often unplanned and reactive. Reorder points are difficult to set accurately, low seasons can drastically affect what is required, and a lack of safety stock is often held on-site.
This means that it is often not integrated into the overall production management process, which leads to poor inventory analysis.
Additionally, because MRO inventory is not part of the final product, it can be seen as less important and given less attention than other areas of the business. As a result, it is often overlooked or not given the attention it needs to be managed effectively.
This can lead to inefficiencies and waste in the MRO management process, ultimately impacting the bottom line.
Want to see Katana in action?
Book a demo to get all your questions answered regarding Katana’s features, integrations, pricing, and more.
Essential MRO inventory management best practices
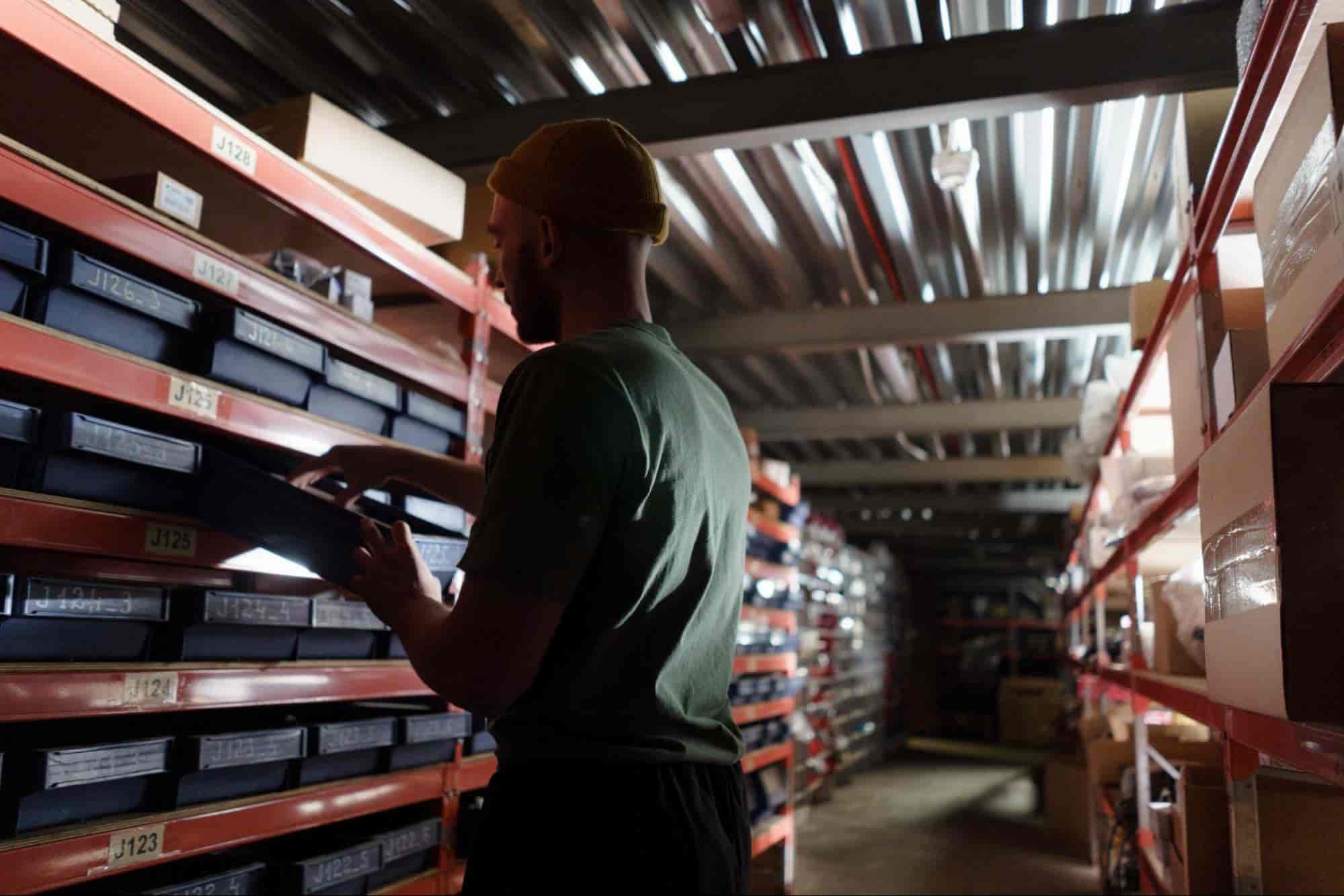
There are four key things to remember when it comes to MRO inventory optimization:
- Integrate MRO inventory into your ERP system — By integrating, you can get a real-time view of what is happening with your production process and make changes accordingly. This will help to improve efficiencies and reduce waste.
- Standardize and centralize MRO inventory — This will help to improve the visibility of what is available and where it is located. This will make it easier to find and use the items when they are needed.
- Implement an MRO inventory management system — MRO inventory management software can help to automate the process and improve accuracy. This will reduce the chances of errors and help to keep costs down.
- Review MRO inventory regularly — This will help to identify any areas that need improvement. This can help to keep costs down and improve the efficiency of the process.
While these are simple steps to follow, the overall question remains — what is a good MRO inventory strategy?
MRO inventory reduction
The first, perhaps more popular MRO strategy, is simply to reduce the amount of MRO inventory a company has. There are several ways to do this, but the most common is to reduce the lead time for ordering new parts or supplies.
This can be done through supplier management to improve turnaround times or streamline ordering and receiving new parts. It can be a challenge, as it requires coordination between different departments within the company, but it can be done.
Increase MRO inventory
MRO stock inventory means more than just having parts on the shelves. To be effective, businesses need to have the right parts, in the right quantities, at the right time. Sometimes, that means carrying more materials in-house than what is necessary for daily production.
The decision to increase inventory levels should not be taken lightly, as it ties up working capital that could be used in other business areas. However, in some cases, it may be the best option to ensure that production can continue without interruption – something that would cause a far greater risk to the health of the business.
Improve your MRO inventory management techniques with Katana
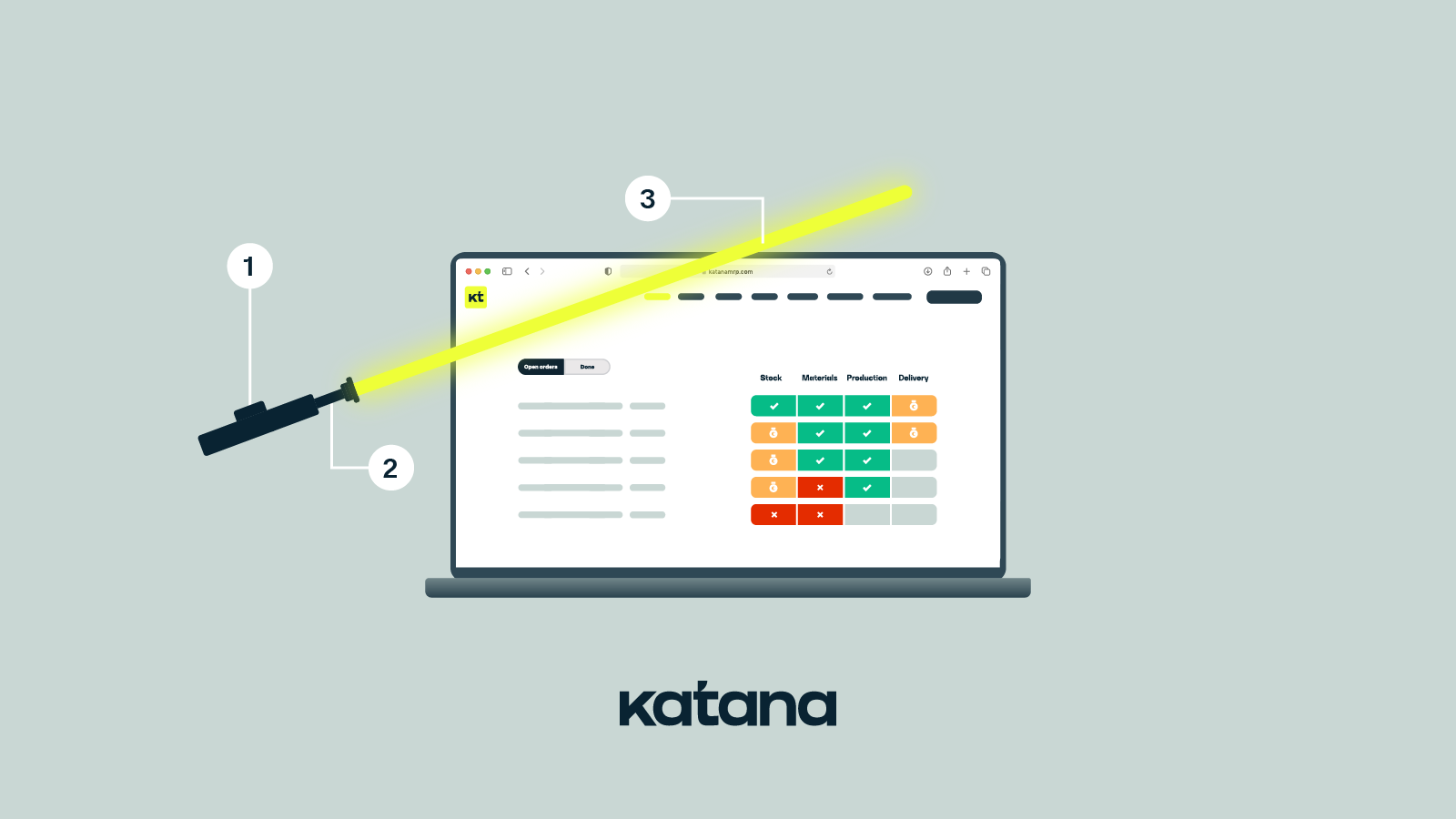
To determine which strategy is best for your business, you’ll need a better understanding of your current state. Katana ERP can give you that by providing full visibility into your MRO materials and the ability to track inventory and manage those items.
Katana connects all of your data into one central location, giving you a complete view of what’s happening with your production process and helping you to identify areas of opportunity.
If your MRO inventory is disconnected and spread out among departments, get a demo of Katana, and you’ll quickly see some easy MRO inventory management solutions.
Table of contents
Inventory management guide
More on inventory management:
Get visibility over your sales and stock
Wave goodbye to uncertainty by using Katana Cloud Inventory for total inventory control
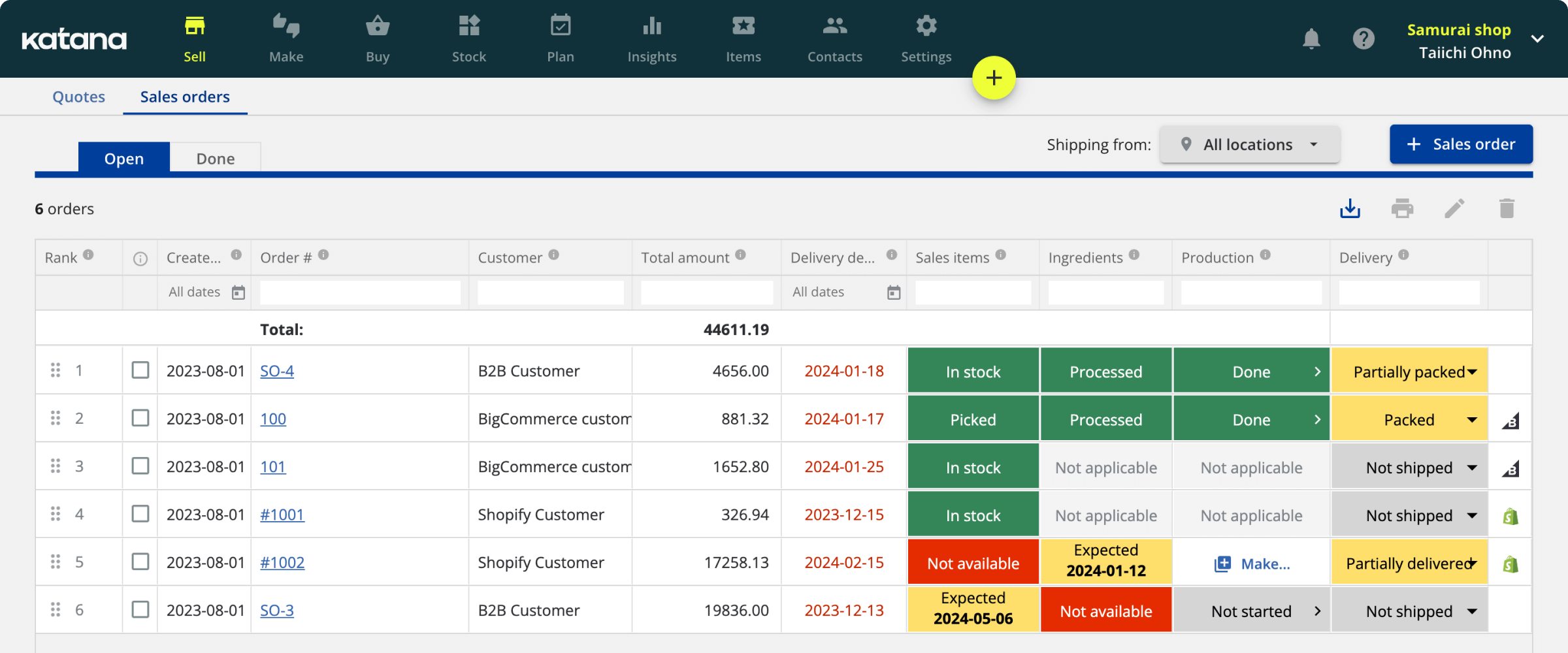