What is a stocktake? The 2024 complete guide
Stocktaking is the process of physically checking stock levels for each product and material you sell to ensure that your data is up-to-date and accurate.
It’s important to have a fine grasp of your stock management to make sure your business can grow. Without knowing what you have and what you’re doing with your inventory levels, there’s no way you can run your business efficiently enough to nurture growth without identifying your stock discrepancy. The stocktaking procedure can be a minefield to navigate without the right tools and a well-thought-out strategy.
That’s why we have explored the world of stocktaking, including how to do a stocktake, the benefits, and the best techniques for maintaining healthy inventory levels.
Discover everything you need to know about stocktaking in this management guide.
What is stocktaking?
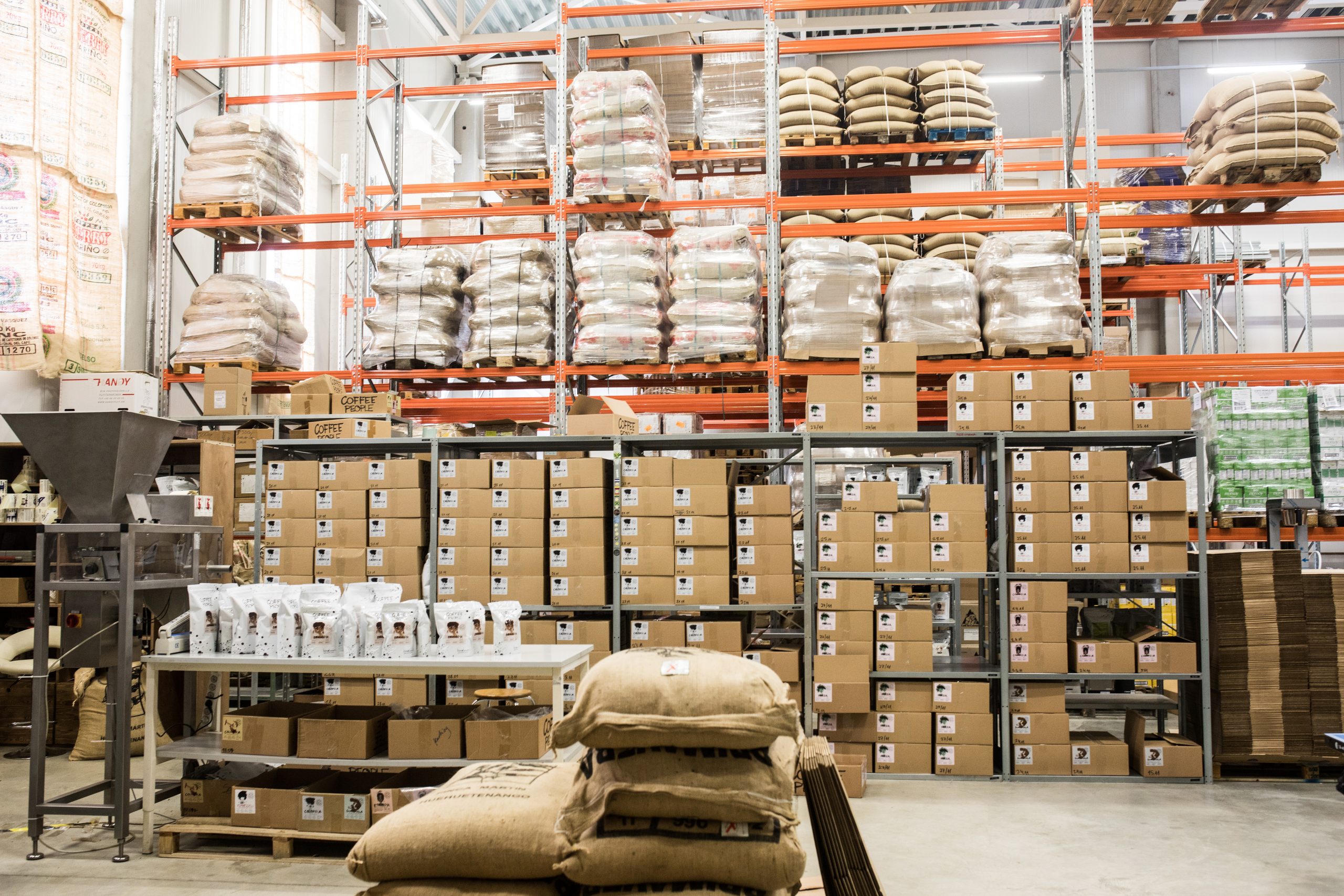
The definition of stocktaking, otherwise known as stock counting or inventory checking, is the act of physically getting verification of the quantities and examining the condition of items held.
Two reasons manufacturers may need to perform a stocktake are to provide an audit of existing stock or uncover stock discrepancy information. However, stocktaking is a major contributing factor to your inventory control, especially as a manufacturer, as your business function optimally relies on successfully managing not just stock but different types of inventory. Now you know what is stocktake, why are they important?
Why are stocktakes important?
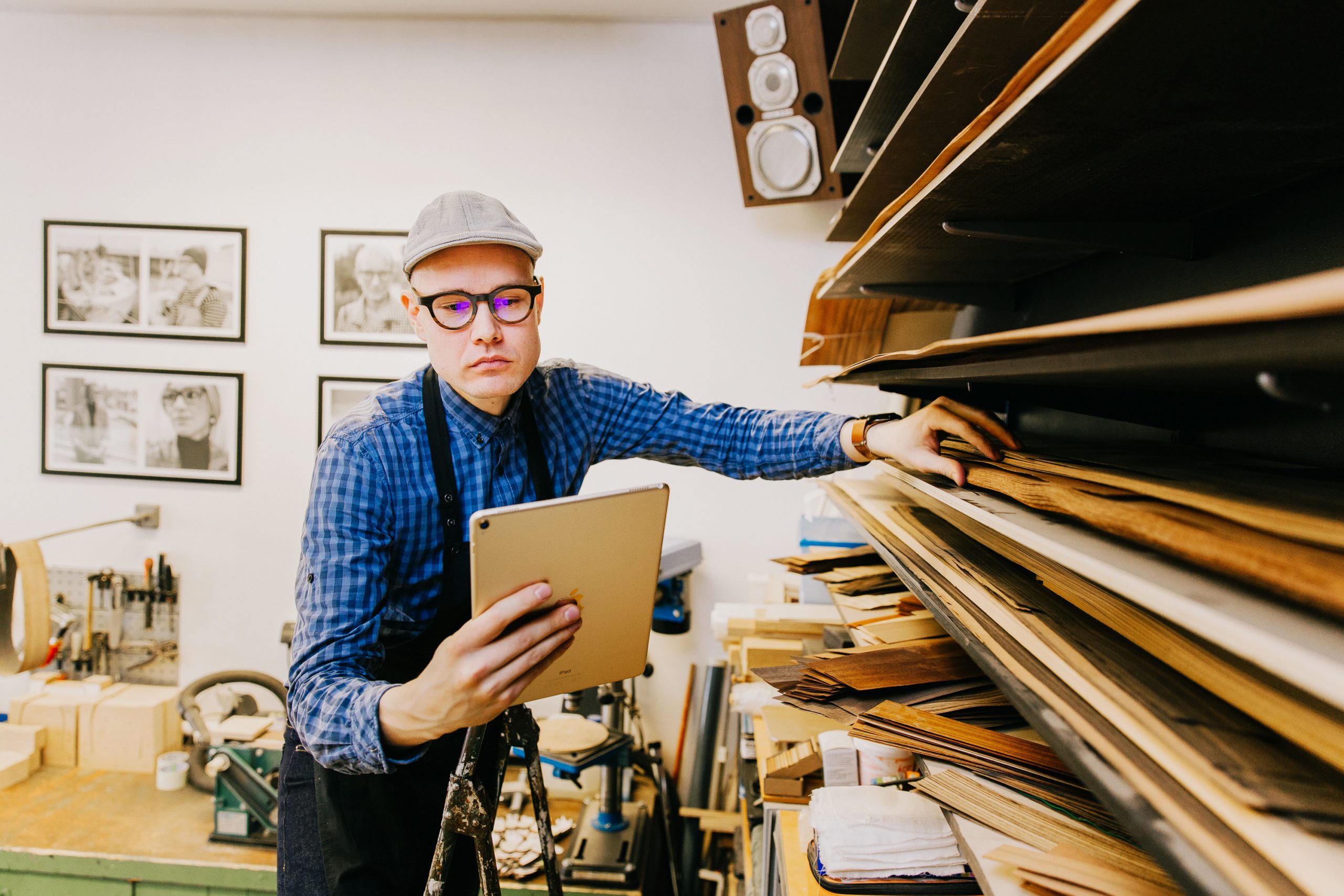
It doesn’t take a lot of self-reflection to realize that stocktaking is necessary for taking care of your manufacturing business.
After all, your inventory — your raw material, components, and subassemblies — is the makeup of everything you use to make and sell your products. Without a strong foundation, you may be setting yourself up to fail. Just imagine that you don’t prioritize your stock management over an extended period.
You might well end up:
- Running out of stock on a product
- Finding yourself with an overflowing stock room that is tying up your cash
- Landing with a pile of dead stock that is no longer usable
- Having a load of unchecked damaged goods on your hand
- Losing sight of potentially beneficial inventory management practices
And these elements can add up fast to create a monster that gets totally out of control.
Imagine that your stock data is so out of sync with reality that you cannot fulfill orders on time without wasting huge resources on overstocking. But hey, not everything is doom and gloom. What you should be keeping your eyes on are the awesome benefits of having a solid stocktaking procedure in place.
Benefits of the stocktakes
Once you start accurately managing your stocktakes, the fruits of your upcoming labor will become clearer.
Here are just some of the many benefits you can expect to find:
1. Keep your inventory up to date
The importance of accurate data cannot be understated.
Maintaining correct inventory data is useful for manufacturing your products. It will also help you make sure you have finished goods in stock waiting to be delivered to customers and that you’re not carrying negative inventory. Without it, your production planning may become obsolete, and even more sadly, your customers might not end up with their products being delivered on time.
That’s why inventory planning software is so important. You can save your business on carrying costs and keep your inventory at optimal efficiency.
2. Uncover stock room issues
There are so many elements that can affect the products and materials which lay in your stockroom.
Poor conditions, damp atmosphere, badly handled boxes, and even theft are just a few. Of course, most of these problems will just be one-off cases that are simply the reality of business. But no doubt optimizing maintenance and security measures can assure you don’t lose any more stock than you have to.
We’re talking humidifiers, advanced locks, handling procedures, that kind of thing.
3. Improve your sales strategies
Nothing cleanses the soul like a good spring clean.
And that’s basically what a stocktake does, except on an even more regular basis (we’ll get to the frequency later). The main point here is that by constantly being in touch with your product stock, you can make a strong visual connection between your sales figures and what’s happening behind the scenes. It won’t take long to realize that one of your pet products is actually doing a lot worse than you thought when you see it on the same shelf week after week.
The opportunity for you to adjust your sales and marketing efforts to suit the supply you already have in stock will then arise.
What is the difference between stock and inventory?
If you’re reading this article so far but you’re scratching your head in confusion, that’s a fair response.
It is confusing.
So, to quickly clarify, the difference between stock and inventory comes down to what it is you actually sell to customers:
- Stock — These are the items that you sell to customers, mostly finished goods. But, if you sell any of your raw materials, components, or subassemblies, then this is classified as stock too
- Inventory — This encompasses everything else, your raw materials inventory and MRO inventory, but still includes your sellable items too
So, if you read inventory management, that’s how you handle all these items in your business. But, your stock refers only to the items you sell to the customers. Now that’s cleared up. The next section should make sense.
Managing inventory to make the most of your stocktake
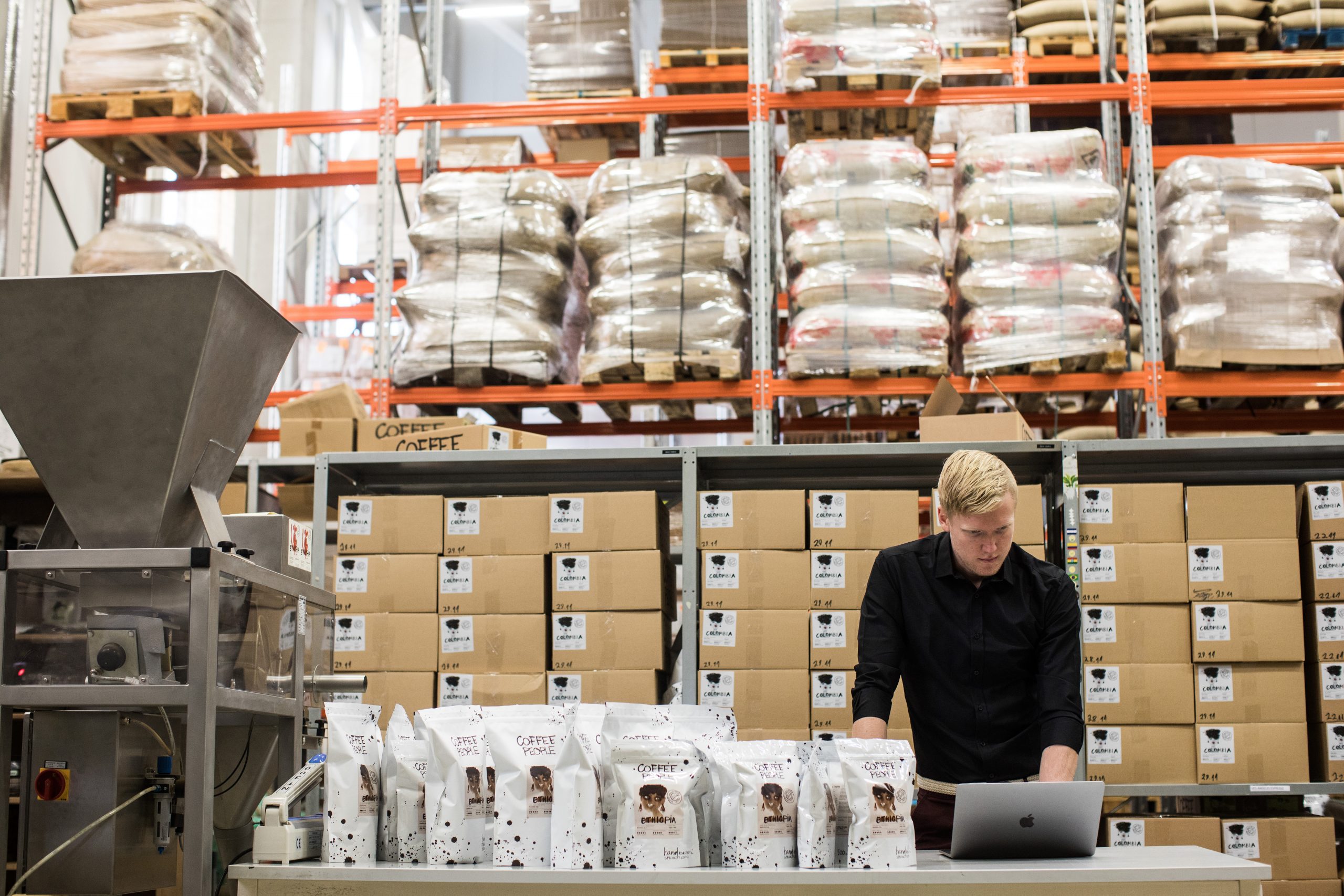
Traditionally, manufacturers and even retailers used periodic inventory management for stocktaking.
This is where you perform stock checks at intervals that could be daily, weekly, or monthly. However, this needs to be done visually and can be extremely time-consuming, depending on how many items you have in your warehouses. This task can take up to an entire day. This disadvantage to periodic inventory management is big enough to drive modern, forward-thinking manufacturers over to perpetual inventory management, but what’s the difference?
- Periodic inventory – Updating inventory at fixed time intervals by physical verification
- Perpetual inventory – The continuous real-time updating of inventory, usually achieved with an inventory management system
You need to look for stocktaking software that can keep your products and materials in sync with your production and sales.
How often should stocktake be done?
The reality is that there is no standard for how many times you should be doing stocktakes, but the truth boils down to:
The more stocktakes, the merrier
There are obvious limits to this mantra, but the point is that you want to have as many updates to your data as you can to ensure that you’re running at your maximum efficiency. There are two general approaches:
- The first is to do a huge annual stocktake, which could involve shutting down your operations and checking everything in one fell swoop
- The second and frankly more beneficial is to be checking your stock regularly throughout the year. Potentially at weekly or monthly intervals
It’s going to be of much more use to keep your records consistently up to date unless your stock room is so tiny that discrepancies are immeasurably rare. The exact interval depends on the length of your product life cycles, but weekly checks are ideal to aim for.
Pro tip: The process becomes much simpler once you have manufacturing ERP software to keep track of your inventory. Especially with software like Katana, you can upload your inventory data with a simple inventory spreadsheet template.
How do you do a stocktake?
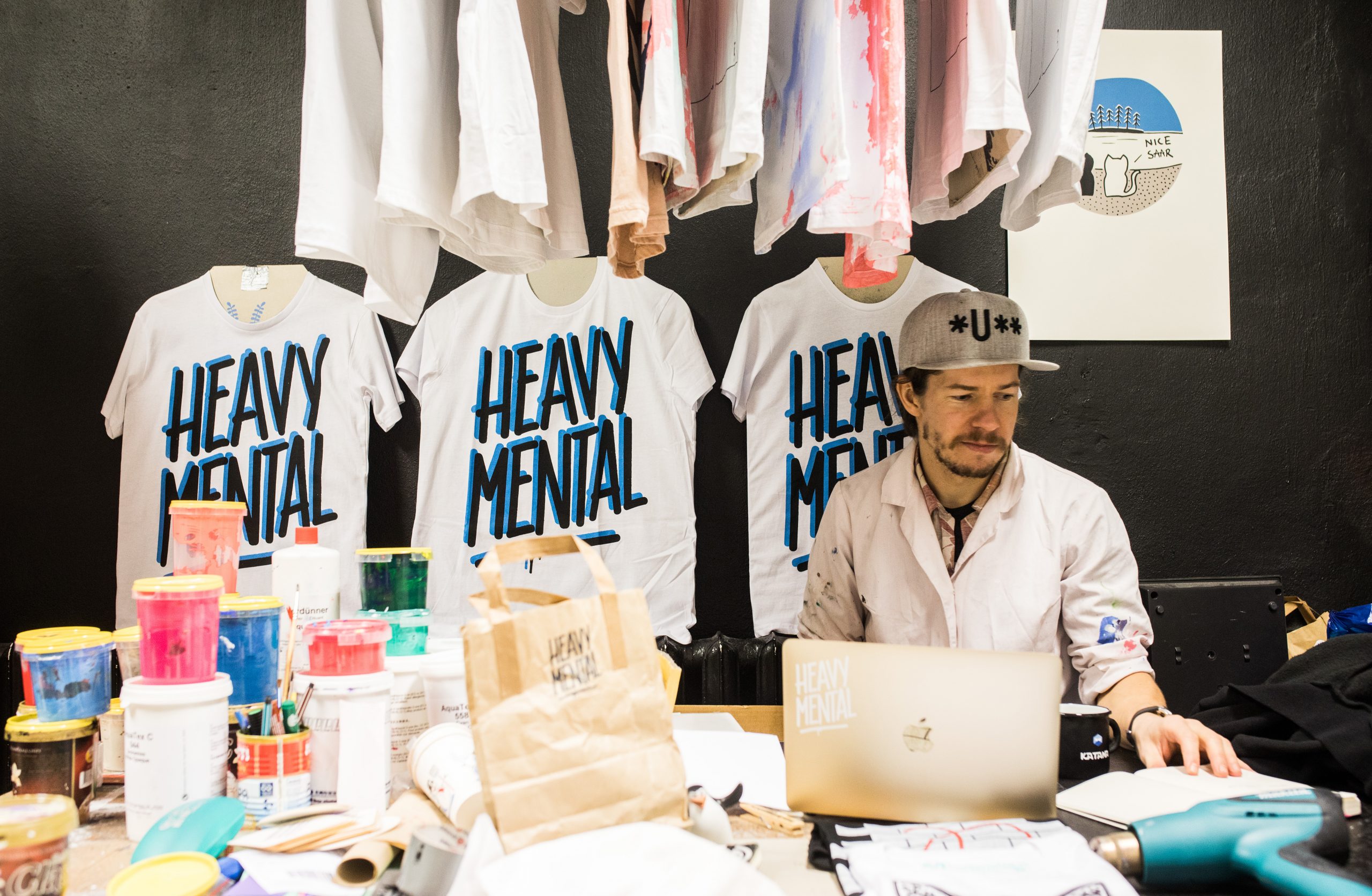
Now, don’t be shocked — just because you aim for stocktakes regularly doesn’t mean you do everything at once.
In fact, this type of stocktaking, also known as cycle counting, is designed to keep your business running as the process is ongoing. So, what is the stocktake process? Well, it’s going to vary for every business, but you can follow these general steps once you have allocated the days and time for your stocktaking:
Before the count
- Pause sales and purchases to avoid incoming and outgoing inventory disrupting your stocktake
- Remove unnecessary distractions by either shutting down operations or performing the stocktake after hours
- Set aside time to resolve discrepancies and solve issues
During the count
- Stocktake all your sellable inventory, even if it’s classed as safety stock, cycle stock
- Make you and your staff record stock levels on the shelf and compare that to figures in your inventory management system
- Take breaks, this task is long and arduous, and it’s easy to make mistakes when overworking yourself
After the count
- Value your inventory correctly, double-check that valuation, and once you’re happy, upload everything to your inventory management system
- Replenish stock items that are running low and analyze the results of your stocktake
- Investigate discrepancies and identify what’s making them occur.
The brilliant thing about getting this right is that it will improve the flow of your shop floor because everyone will be more aware of what is moving in and out of the stockroom once a stocktake has been completed.
Stocktakes with Excel spreadsheets
Using an Excel spreadsheet for stocktake can make the process much easier and more accurate.
To get started, you’ll need to create a template that includes all of your items and their corresponding prices. This is where the stocktake formula comes in handy. The stocktake formula is used to calculate the total value of your inventory at any given time. The formula looks like this:
“=SUM(Stock Price*Quantity)”
This will give you the running total of all items in inventory, allowing you to track how much stock you have on hand easily.
When setting up your spreadsheet for stocktake, be sure to add columns for item names and descriptions, as well as quantity and pricing information. This will make it much easier to locate the items you need when doing your stocktake.
Once everything is set up, you’ll be ready to start keeping track of your inventory with the stocktake formula. Remember to double-check that all information is accurate and up-to-date when running the formula. This will help ensure accuracy in your results and keep you on top of any changes in stock levels or pricing.
Excel spreadsheets can provide an efficient and accurate way to manage your stocktake. Using the stocktake formula makes it easy to keep track of all items in inventory, giving you peace of mind that you’re managing your business resources wisely.
How to improve your stocktaking?
Now you know everything you need about stocktaking and even the steps to follow while performing these duties.
So, what’s the best way to improve this hefty task? Thankfully, some techniques and tools can help you perform this:
Allocate one counter
Considering the amount of information that needs to be gathered and how important it is to avoid making mistakes, it’s best to assign one person to the task. Yes, it might seem unfair as it’s a big task, but it helps avoid mistakes with multiple employees miscommunicating with each other.
Regular stocktakes
The longer stocktaking is put off, the harder it is to possibly remedy any issues that might be found when you do it eventually. Regular stocktakes will allow you to identify:
- Dead stock
- Underperforming products
- The best reorder point for items
Barcode scanning
Physically counting material takes a considerable amount of time. That’s why introducing a barcode scanning system will help you speed up the process and reduce the chance of making a mistake while doing stock counts.
Cloud-based inventory management
Cloud inventory management software allows you and your staff to monitor stock levels on the shop floor or away from the office. All you need to have is an internet connection. The real-time responsiveness of cloud software allows you to keep on top of stock movements and keep up-to-date information on your inventory.
Stocktaking to the next level with Katana’s cloud manufacturing software
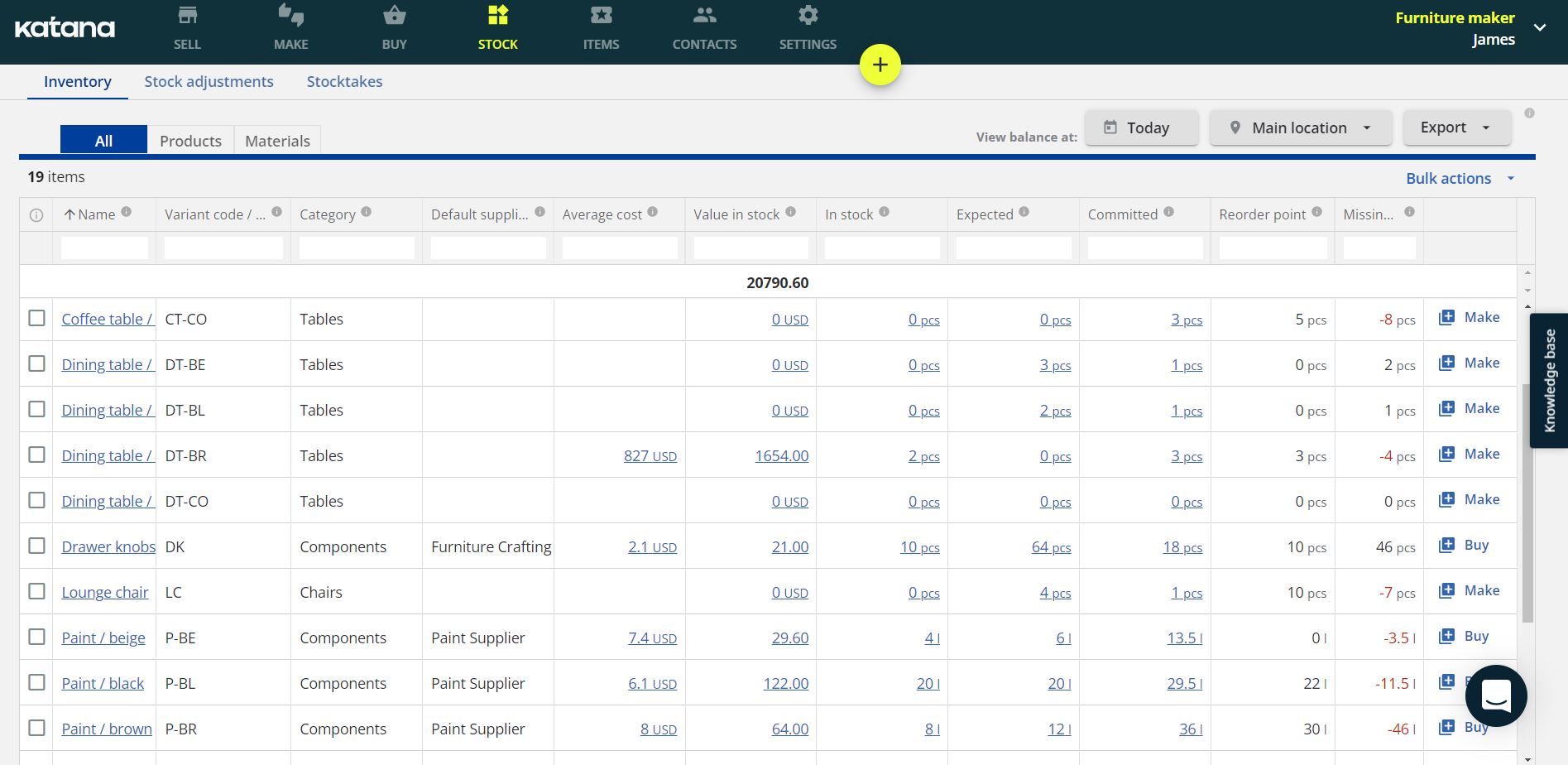
Katana is one of those stocktake solutions that use perpetual inventory management that weaves your sales, manufacturing, and inventory into one seamless workflow.
The stock you keep in Katana is updated automatically in real-time. For many manufacturing businesses, it’s common practice to perform regular stock counts to record stock levels correctly. These counts can come from a stocktake, inventory, or cycle count.
To start a stocktake in Katana, you’ll first need to create a stocktake document for all item variants that have any quantity in stock.
Count the items and update the quantity for each item variant or batch row. You can use a barcode scanner to identify and count item variants or batches — the amount counted will be updated automatically. Once the stocktake status is set as counted, you’ll see a full stocktake report and can review the discrepancies between the quantity in stock and counted quantity.
While your stocktaking is underway, no stock adjustments will be made before the stocktake status is set to Completed.
You can still delete rows that need to be left out from the stock adjustment to recount them. Once done, change the status to Completed. This will automatically create a stock adjustment and update the quantity in stock.
Table of contents
Inventory management guide
More guides from Katana
Get visibility over your sales and stock
Wave goodbye to uncertainty by using Katana Cloud Inventory for total inventory control
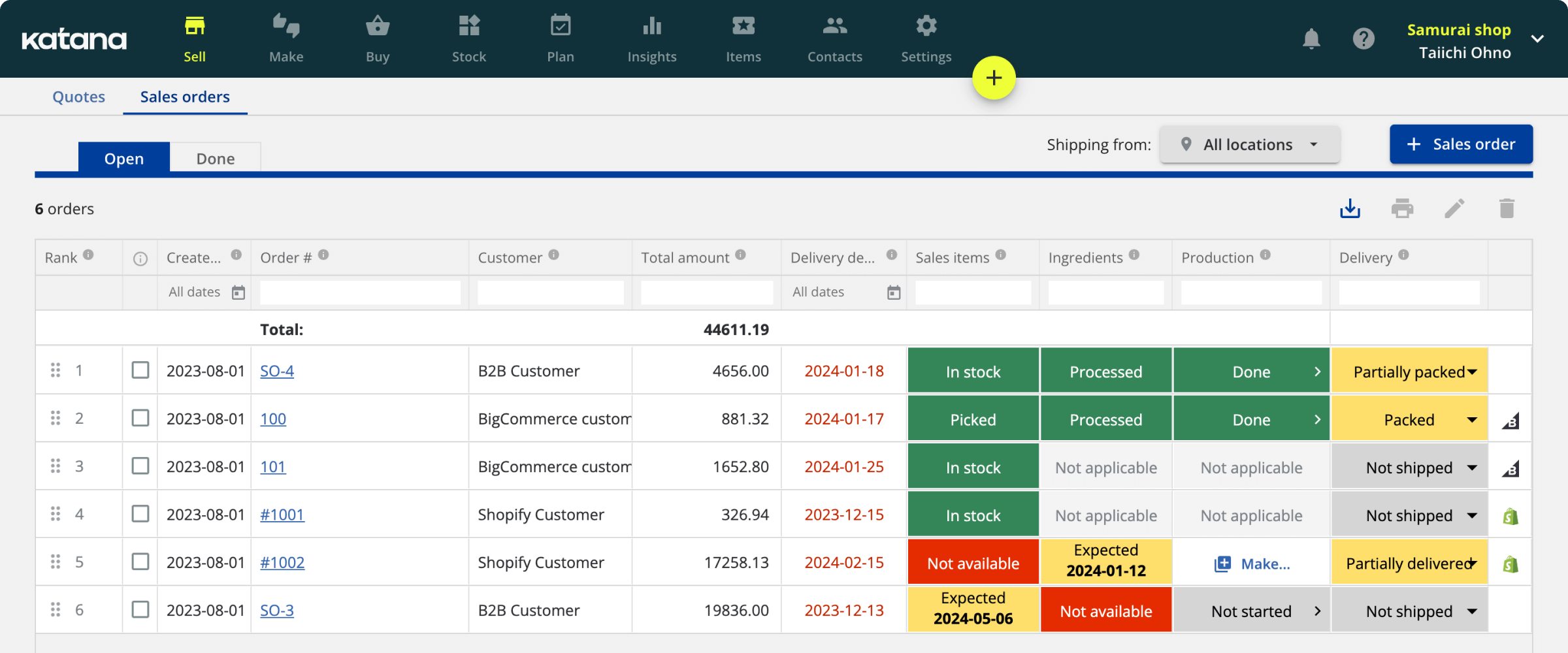