How to calculate pipeline inventory effortlessly
If you’ve ever taken advantage of a pre-sale item, you’ve interacted with pipeline inventory.
Buying a product before it is physically in a brick-and-mortar store, or stocked in an e-commerce warehouse, means you are purchasing a piece of inventory that can’t be calculated as part of normal levels.
In an ideal world — at least for businesses — no piece of inventory would ever be produced before it has already been purchased at the other end. That would be an example of perfect pipeline inventory management.
However, because businesses need to account for things like delays in shipments and changes in customer demand, it’s important to have a handle on how much product is “in the pipeline” at any given time.
Below, we’ll examine:
- What pipeline inventory is
- How to calculate pipeline inventory
- Tips on managing pipeline inventory
- How to integrate software solutions
Let’s head down the pipe.
Live inventory management software for pipeline inventory
Know exactly where all your items are at a moment’s notice with pipeline inventory software purpose-built for businesses tracking multiple inventory types.
What is pipeline stock?
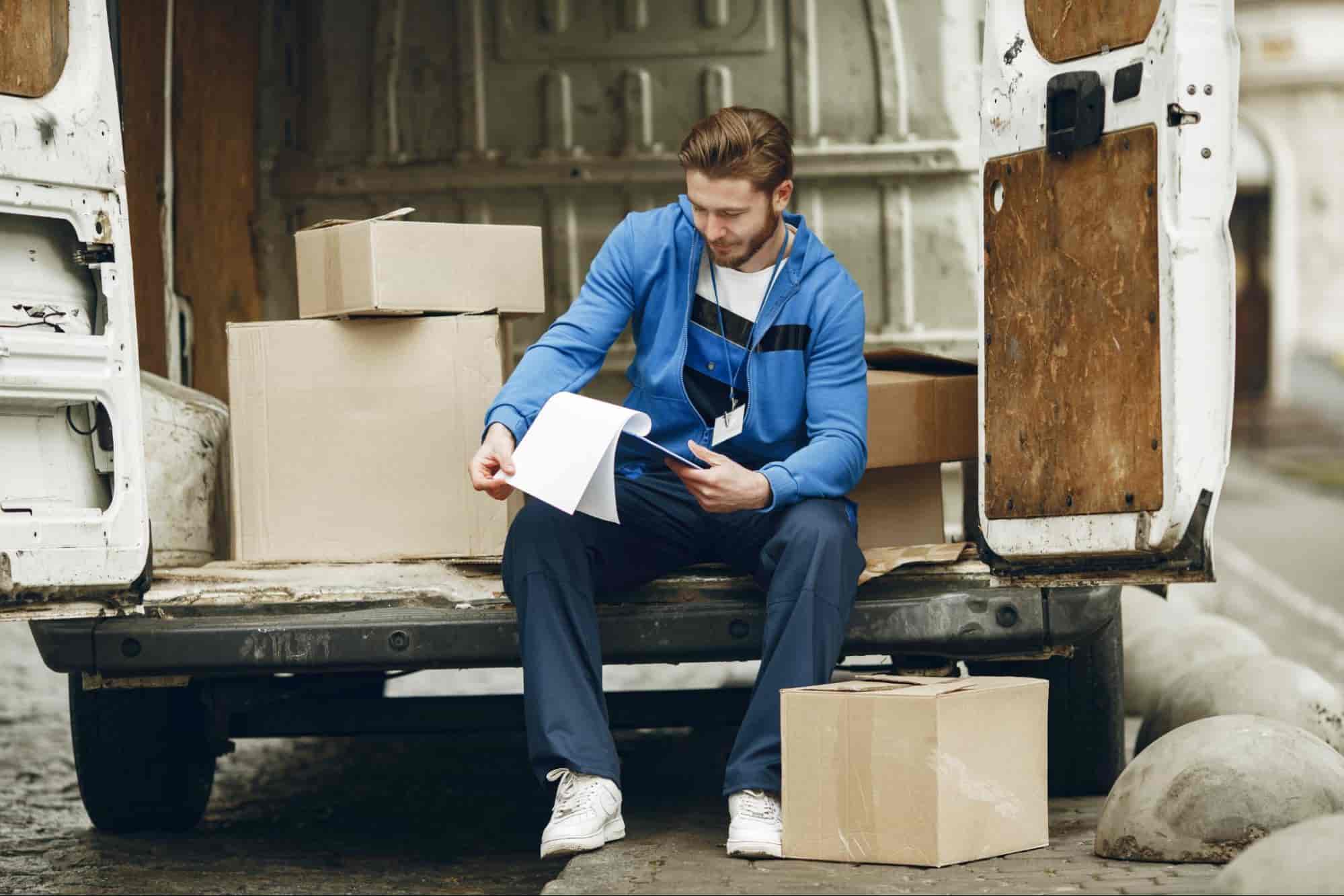
From the moment a business places a purchase order with a supplier until the moment it arrives at the customer’s door, there is a period in which it is considered pipeline inventory. In other words, it’s a product that has been ordered but has not yet arrived at its final destination.
Pipeline inventory can be further broken down into three specific categories:
- In-transit inventory — It has already been shipped from the supplier but has not yet been received by the customer. It’s inventory in the transit pipeline or traveling, and therefore not under the direct control of the business
- Backlogged inventory — This has been ordered by the customer but not yet shipped by the supplier. The order may have been placed weeks or even months ago, and the customer is patiently waiting for it to arrive
- Stock-in-trade inventory — This is a product a business has received from a supplier, sold to a customer, but has not yet been shipped. Like backlogged inventory, stock-in-trade inventory is under the direct control of the business
It is important to note that this applies not just to finished products. It can also apply to intermediary goods and services involved in the manufacturing process.
For example, if a company orders new machines to produce a product but hasn’t yet received them, those machines would be considered still in the inventory pipeline. The same could be said about a service, like if a company orders advertising time but the ads have not yet aired.
Pipeline inventory is also not included in the same way as these other types of inventory that a business owns.
- Safety stock — This is an extra buffer stock that a business holds to protect against stockouts or the situation where they run out of product to sell
- Decoupled inventory — The difference between pipeline inventory and decoupled inventory is that the latter is not customer-facing. In other words, it’s used in the production process, but the customer will never see it
- Dead stock — This is inventory that a business can’t sell for one reason or another. Dead stock is often outdated or no longer relevant to the company’s product line
To calculate pipeline inventory, businesses need to take a different approach that we will explore below.
How to calculate pipeline inventory
The first thing we need to define is manufacturing lead time.
This is the period between when an order is placed and when it is received. It includes the time it takes to produce the product, plus shipping time from the supplier to the customer.
For example, if a company orders new products on Monday and they are delivered on Wednesday, the lead time period would be two days.
We can begin our calculations now that we know what lead time is. The most common way to do this is by using the following pipeline inventory formula:
PI = Lead time × demand
Let’s break down each part of this equation so it is easier to understand:
- Average lead time — As we learned above, this is the period between when an order is placed and when it is received. To calculate average lead time, businesses need to track how long it takes for orders to be filled over a certain time
- Demand rate — This is the number of products customers buy in a given period. Given that this is a demand forecast, it will need to be constantly monitored and updated
Now that we know what each part of the equation means let’s look at a pipeline inventory example.
For this example, let’s say that a company’s shipping chain allows for an average lead time of four days, and their demand rate is 100 products per day. This means that the company must have 400 products in its inventory pipeline to meet customer demand and avoid stockouts.
Tips for managing pipeline inventory
You might think, “That’s an easy formula. What’s the problem?”
The issue is that in the real world, calculating pipeline stock levels is often more difficult than it seems. This is because manufacturing companies need to account for things like delays in shipments and changes in customer demand.
Here are a few tips to help you conduct an accurate inventory analysis and optimize pipeline inventory.
Anticipate changes in demand
One of the most difficult things about managing pipeline stock is that customer demand can change unexpectedly because of things like:
- Seasonality
- Changes in the economy
- New product releases
- Change in manufacturing trends and predictions
Try to anticipate changes in demand as much as possible so that you can adjust your pipeline inventory levels accordingly.
Build a buffer into your lead time
To account for unexpected delays, it’s a good idea to build a buffer into your lead time.
For example, if your lead time is four days, you might want to add an extra day or two to account for potential delays. This will help ensure that you always have enough products in your pipeline to meet customer demand.
However, be careful when implementing this strategy, as too much buffer can lead to unnecessarily high inventory and safety stock levels.
Katana’s cloud inventory software
Cloud inventory software like Katana can help you track your pipeline inventory and more. From partially receiving deliveries and setting reorder points to beat stockouts.
Use software
This is the most effective way of managing all types of inventory, including pipeline inventory and decoupled inventory.
Tracking data manually can be time-consuming and error-prone. Still, with an integrated end-to-end material requirements planning solution like Katana, your inventory levels, lead times, and customer demand can all be synchronized to help keep your pipeline full without any overstock.
With this system in place, you can focus on other areas of your business and be confident that your pipeline is:
- Automatically adjusting to customer demand
- Able to mitigate the risks of stockouts and overstocks
- Reducing the need for manual intervention
It can be challenging to prepare accurately, but managing pipeline inventory can be a breeze with the right software solution.
Table of contents
Inventory management guide
More on inventory management
Get visibility over your sales and stock
Wave goodbye to uncertainty by using Katana Cloud Inventory for total inventory control
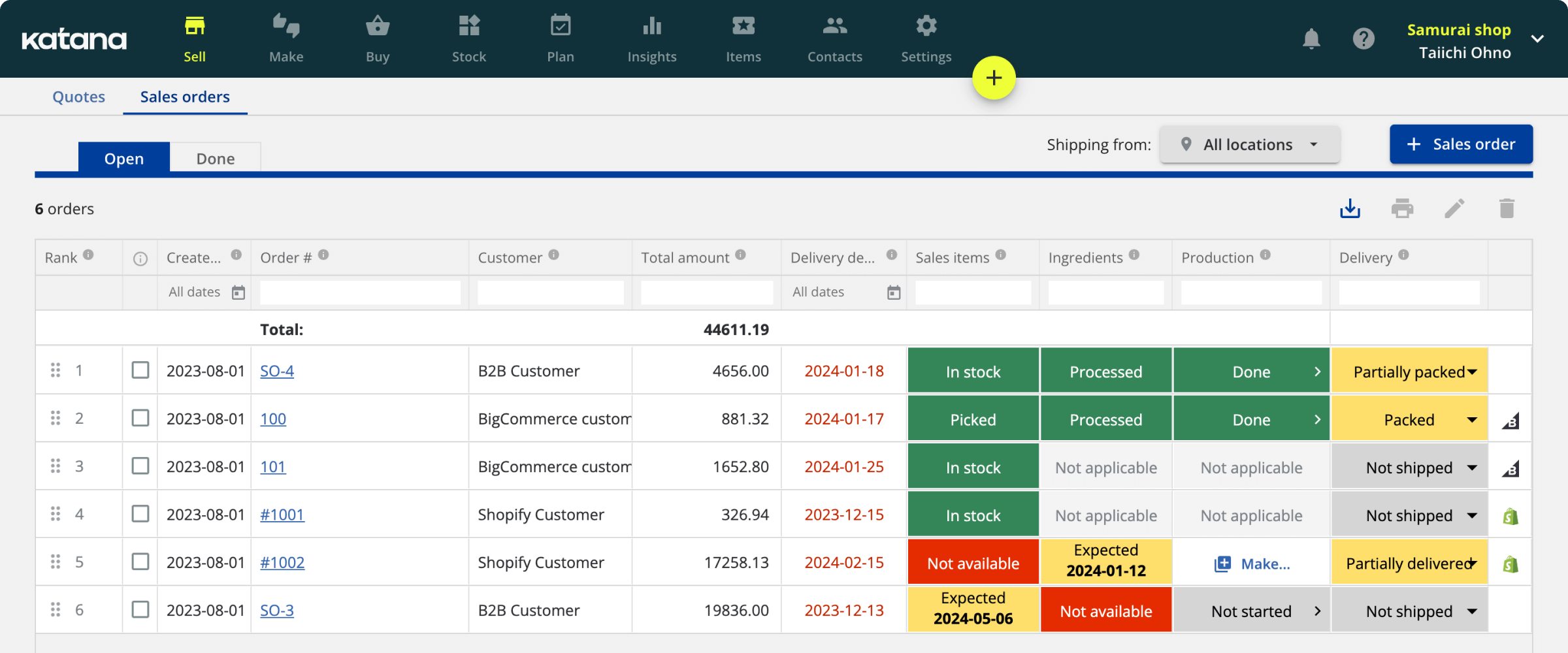