If you use Xero for your accounting, you’ve probably wondered if you can use it to track raw materials. Managing raw material inventory is a critical aspect of various businesses, especially those involved in manufacturing or product-based industries.
While Xero is a powerful accounting software known for its financial management capabilities, it does have limitations when it comes to detailed inventory management, particularly for raw materials.
In this article, we’ll explore these limitations, discuss workarounds for tracking raw materials in Xero, and highlight the importance of utilizing a third-party Xero inventory add-on.
Can you track raw materials with Xero?
The simple answer is no, you can’t use Xero for tracking raw materials. Neither can you use it to track work-in-progress. You can only track the inventory that is bought and sold as a finished product.
There are a few workarounds to track raw materials with Xero, but these will be ineffective if your business needs advanced inventory tracking for:
- High volumes of raw materials and items
- Following a make-to-order (MTO) workflow since you can’t operate at a negative inventory with Xero
- Using bespoke manufacturing
- Monitoring the progress of your production
Xero itself recommends using a specialized app if you need advanced inventory features. So, fixing these issues is as simple as typing “raw material inventory” into the Xero Appstore.
Before we get to the limitations and workarounds, let’s briefly go over tracking raw material in accounting software.
Xero is a fabulous app built specifically to help you manage your business’ bookkeeping. It also comes with basic inventory management features, though these have been catered more to retailers or drop shippers, so it’s missing a lot of essential features for businesses with more advanced inventory needs, like manufacturers.
Let’s move on and see the more specific limitations you can run into when trying to use Xero for raw material tracking.
What are the limitations of Xero raw materials tracking?
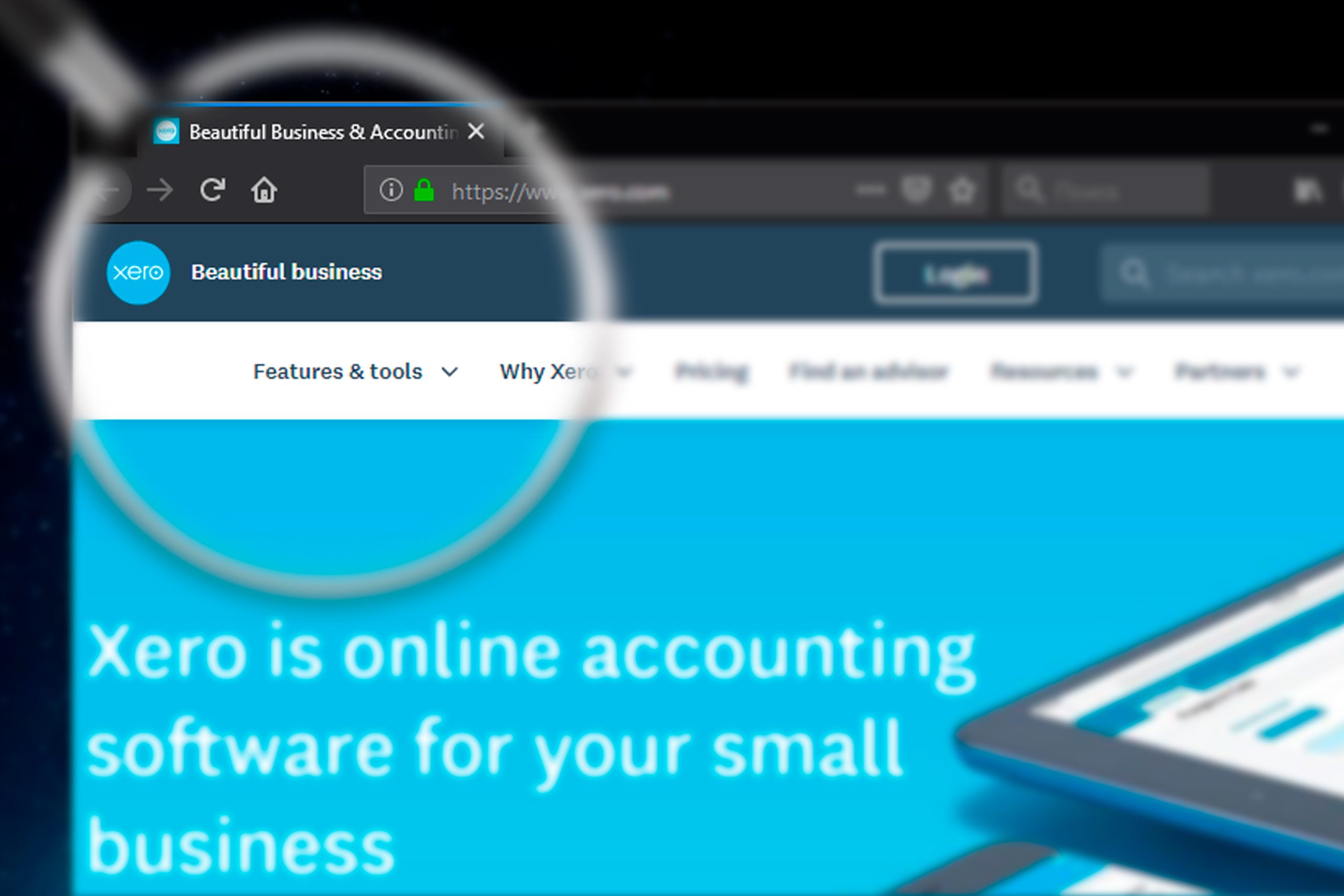
As previously mentioned, there are workarounds to address the absence of features for recording raw material consumption in Xero.
However, before delving into how you can partially utilize Xero for tracking raw materials, it’s crucial to first understand its limitations.
Xero’s inventory management functionality primarily caters to businesses monitoring finished goods inventory. When it comes to tracking other products and raw materials within Xero, you can place them under Untracked Inventory. However, this approach comes with some limitations:
- You can’t track the quantity of these items effectively
- You can’t make updates to these items in your assets account
Not only that, but manufacturers also need to be able to track their production processes and preserve crucial data about the products they make.
It’s not just the absence of Xero’s support for raw materials, the platform also lacks a bill of materials (BOM). This feature is essential for storing the blueprints or specifications required for manufacturing your products. These blueprints play a vital role in calculating the manufacturing costs accurately.
This brings us to another significant concern. In the absence of BOMs or the ability to track raw materials in your accounting, the cost of sales can become distorted. Xero will struggle to account for these essential costs accurately.
These are just a few of the limitations you’ll encounter when attempting to track raw materials in Xero. However, if you’re determined to work with Xero and need to manage the accounting for raw material consumption, below is a workaround to make this process a bit more manageable.
The workaround for tracking raw materials with Xero
Even though there isn’t an actual feature for tracking the consumption of your Xero raw materials, there is technically a way you can do it and even build a pretty basic BOM.
However, this approach is only realistically usable for those who subscribe to make-to-stock (MTS) or assemble-to-order (ATO) workflows. And even then, the costs to assemble products will fluctuate, which Xero, without third-party assistance, won’t be able to automatically compensate for.
Either way, to do that, instead of tracking your finished goods, you buy raw materials and track the quantities and values of those materials.
Essentially, your inventory should be as follows:
- Tracked Inventory — Xero raw materials
- Untracked inventory — Your finished goods
You’ll be able to see how many finished goods you have sold, but it never shows up on your stock-on-hand reports. So, you’ll start by inputting your Xero raw materials or subassemblies with their prices and quantities, for example:
- Bicycle Frame – QTY 6 at $100 each
- Bicycle Gears – QTY 6 at $122 each
- Bicycle Wheel – QTY 12 at $149 each
These expenses will go directly to your balance sheet under Inventory.
Once you sell a finished product, in this instance, a bicycle, the sale will appear in your Profit and Loss, but the Cost of Sales will be missing. To process the cost of sales, you need to make a production invoice to recognize the use of the Xero raw materials.
This setup allows Xero to calculate the average cost of your inventory, even if you buy materials at different prices. However, you will manually need to perform the cost of sales after each sale.
If you want to better understand how to implement this workaround, be sure to check out the video below.
Cloud inventory software for your raw materials
Katana’s cloud inventory platform is the perfect solution for all your inventory needs. It lets you manage raw materials, finished goods, and work-in-progress, and it integrates seamlessly with Xero.
Problems when tracking raw materials with Xero
As you can see, it’s possible to track raw materials in Xero, but the workaround is not ideal. Plus, there are still other issues that you’ll need to overcome, let’s take a look at these now.
1. No WIP tracking
You’re unable to track your manufacturing costs or your work-in-progress automatically. This means you cannot update your accounts until the items are built and dispatched to the customer.
2. No support for make-to-order
The workaround only supports MTS and ATO workflows, meaning that you’re going to have to find or develop another method if you follow an MTO workflow.
3. No multilevel BOMs
As you’ve already seen, it is possible to have a form of BOMs saved on the software, and you’ll even be able to track raw materials. But this is all well and dandy if you’re only making products that don’t require complicated BOMs.
Managing raw material in accounting means you’re sacrificing features such as multilevel BOMs, which are necessary for manufacturers who’re tracking a complicated and diverse inventory.
4. Drains resources
Using the provided workaround for Xero raw material tracking still requires you to manually update inventory (and cost of sales). Therefore this option is not a lot better compared to inefficient Excel spreadsheets, as you need to dedicate time to updating these transactions.
5. No production planning or scheduling
Not being able to track your production and scheduling will take up even more of the resources that you could use to manufacture your products and grow your business.
It might seem like all we’re doing is throwing shade toward Xero. We’re not, Xero is a fantastic tool for managing your finances, and you made (or are making) a wise decision by getting set up with it.
But ultimately, if you’re a manufacturer using it, there are still other features that your business will need, and this is why Xero encourages users to check out the Xero Appstore.
Cloud inventory platform for Xero
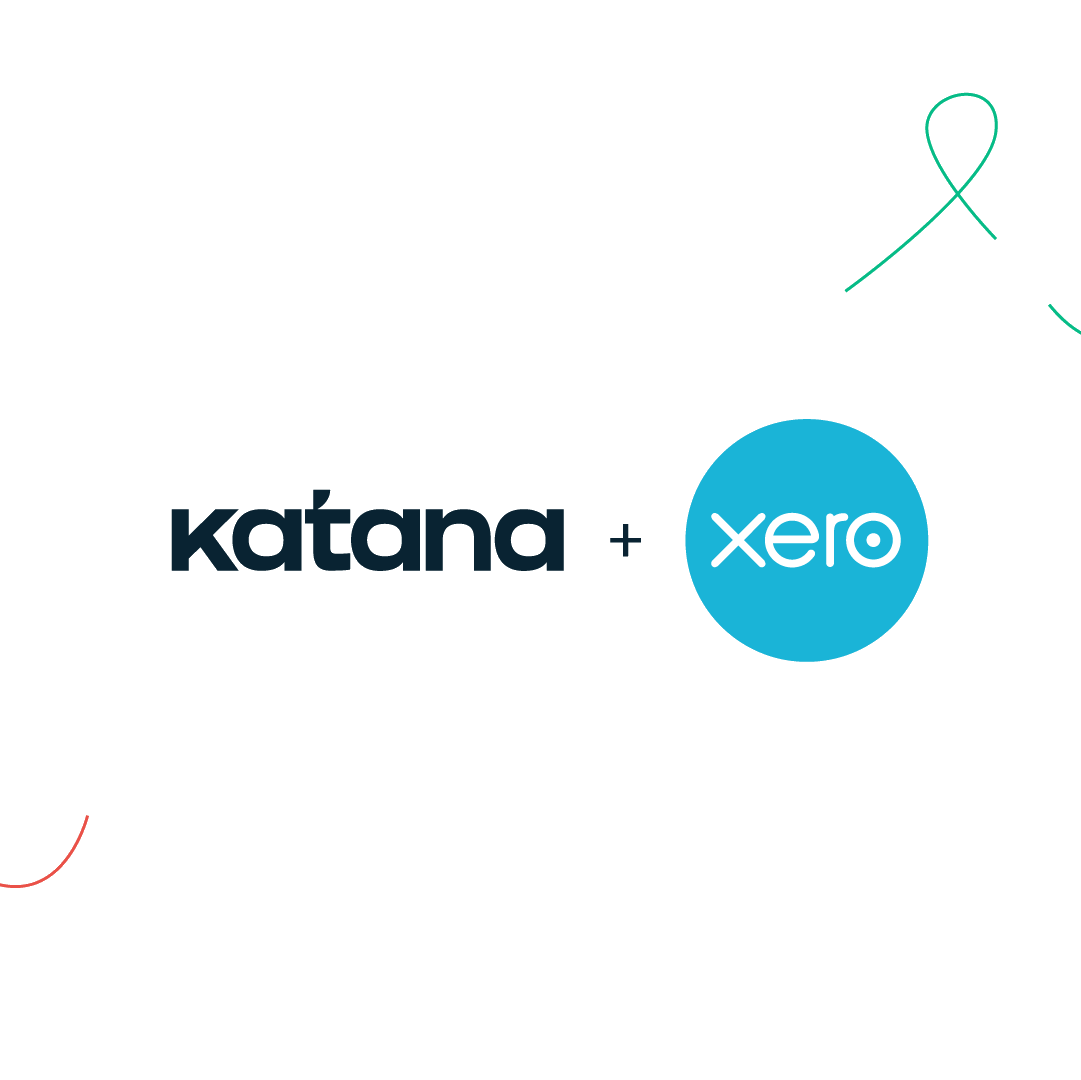
Katana is a cloud inventory platform that seamlessly integrates with Xero, allowing you to centralize your entire business onto an intuitive, visual platform.
With Katana, you can handle all your sales and manufacturing. And once you’ve made a sale or you’ve purchased materials, you can generate your bills and invoices and push them straight to your Xero account to keep track of your finances.
However, Katana can offer so much more besides raw materials tracking. Let’s see some of the benefits in more detail.
Real-time inventory tracking
With Xero, especially using the workaround, you’re not going to have an accurate representation of inventory levels, and you’ll need to perform physical stocktakes more often than you’d perhaps like to.
Katana tracks your finished goods and raw materials in real time, so you always have an accurate overview of your stock levels.
Not only that, but Katana’s real-time master planner takes your finished goods and raw materials and automatically allocates them to your open orders, which will improve your order fulfillment rate since you’ll know immediately if you have the inventory to fulfill your orders on time.
Automatic production scheduling
There’s nothing worse than sweating over getting your production schedule finished, only to have something come up, stop production, and force you to redesign the schedule.
When you generate a manufacturing order, Katana automatically schedules production for you. However, if, for some reason, you need to change your workflow, Katana allows you to easily do so by changing the priority of your orders.
On top of this, the master planner will also redistribute your finished goods and raw materials, so you can stay focused on the shop floor.
Managing BOMs
If you’re a manufacturer who requires a beefier system than what can be offered with the Xero raw materials workaround, then you’ve come to the right place.
Katana allows you to save your BOMs and even create sub-assemblies if you need them, which helps Katana automatically calculate your manufacturing costs and informs the master planner on how to distribute your raw materials to manufacturing orders.
The best part is, if you make different variants/SKUs of a product, Katana will help you generate each possible variation when setting up your BOMs, saving you a lot of time and hassle.
If you want to learn more about how the Katana + Xero integration works, be sure to check out the video below.
So, there you have it, now you’re aware of the limitations when wanting to track raw materials with Xero and the steps you can take to overcome these limitations, be that by using the workaround or taking advantage of third-party software.
If you do decide to look into a third-party Xero ERP integration for raw materials, be sure to check out reputable comparison sites, such as Capterra. Just be sure to find a platform that you can experiment with and request demos, as you don’t want to commit resources to implement software only to realize that it’s not the best fit.
If you wish to see Katana in action and how it will give you total control over your Xero raw materials, you can request a demo here.
Xero raw materials FAQs
Can you track raw materials in Xero?
Xero primarily focuses on financial accounting and inventory management for finished goods. While you can technically track raw materials in Xero by categorizing them as Untracked Inventory, it comes with limitations. You won’t be able to monitor the quantity of these materials accurately, and updating them on your balance sheet can be challenging. Many businesses choose to use third-party Xero inventory add-ons to address these limitations and effectively track raw materials.
Is raw materials inventory an expense?
No, raw materials inventory is not considered an expense on your income statement. Instead, it is recorded as an asset on your balance sheet. Raw materials represent valuable resources that are yet to be transformed into finished products. As you use these materials in your production process, their cost is gradually transferred to the cost of goods sold (COGS) as an expense when the products are sold.
Does Xero have a bill of materials (BOM)?
Xero lacks a native bill of materials (BOM) feature. A bill of materials is a crucial tool for manufacturers as it outlines the components and raw materials required to produce a finished product. While Xero doesn’t offer this feature directly, you can explore third-party integrations and add-ons that integrate with Xero and provide BOM functionality to streamline your manufacturing processes.
Table of contents
Accounting Guide
Readers also liked
Get visibility over your sales and stock
Wave goodbye to uncertainty by using Katana Cloud Inventory for total inventory control
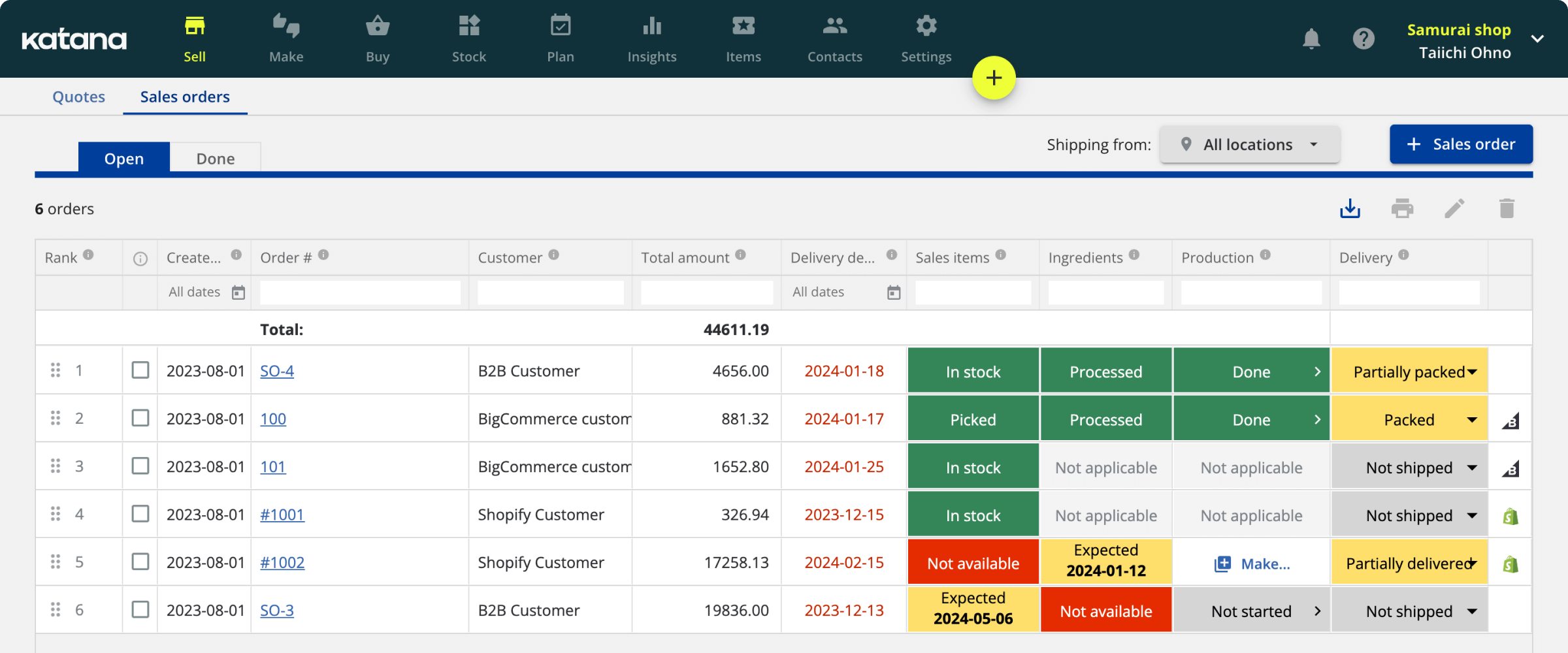