WIP manufacturing: Calculation and cost reduction
Many modern manufacturers have found themselves stuck trying to figure out their WIP manufacturing costs.
Thankfully, there is a formula, and once you have a grasp, it’s going to be easy sailing from there on in. They say it’s the journey that counts, not the destination. And though you might disagree, there can be no doubt that finding the best route is as vital to your success as getting to the destination itself.
In lean manufacturing, that often means zoning in on your WIP manufacturing, aka Work-in-Progress manufacturing.
WIP manufacturing is made up of all the materials, overheads, and labor costs involved in products that are still in the process of production. By analyzing these details, you can lay out a roadmap that allows your manufacturing to become far more efficient while also reducing the costs involved with it. It might sound like a tedious job to take on, but the reality is that improving your WIP manufacturing is going to give you space to grow your business at a greater rate.
Once your processes are in place, it will become second nature to start taking elements like your inventory management of raw materials seriously.
The question is, what is WIP in manufacturing?
WIP manufacturing definition
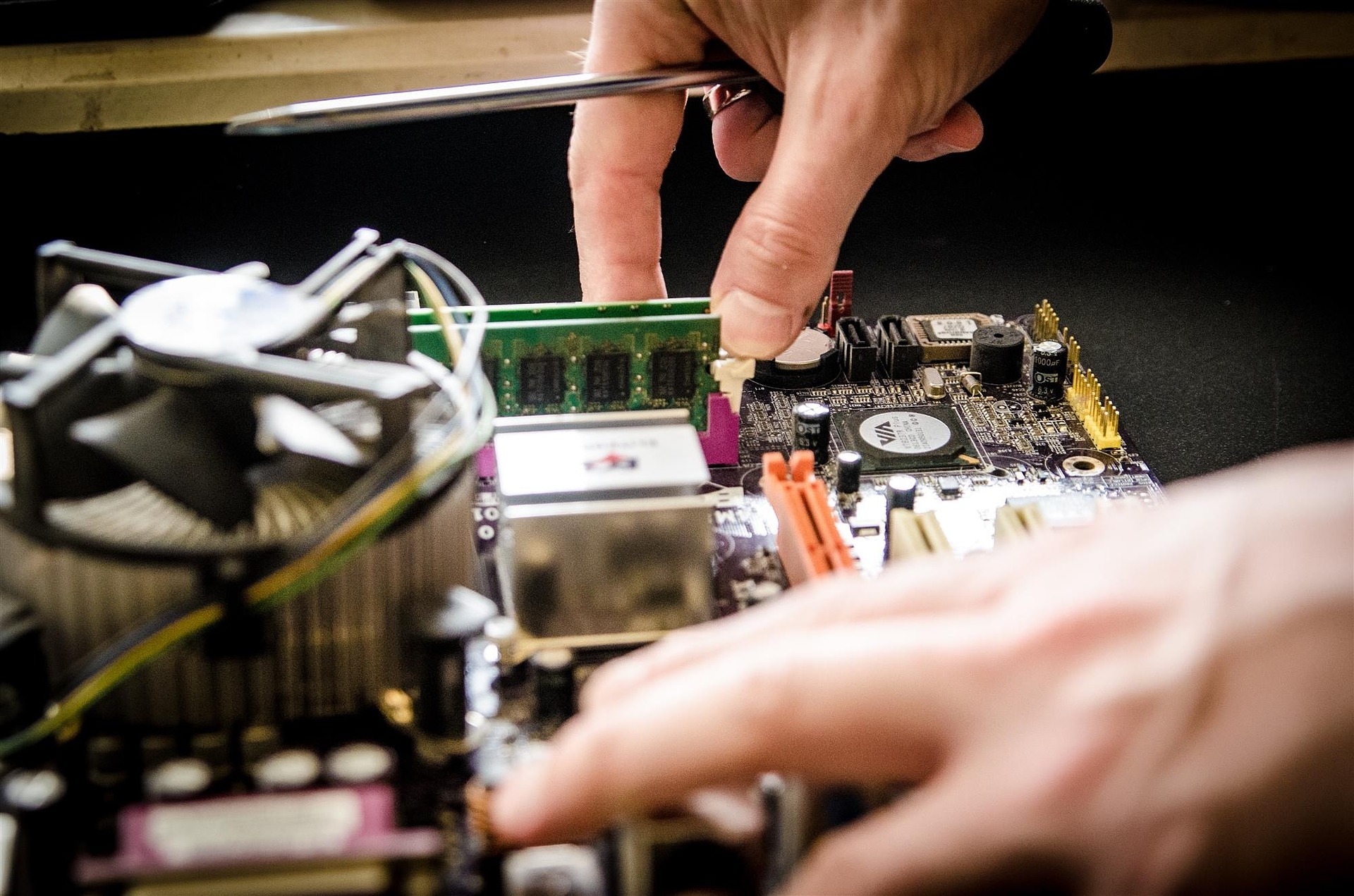
When we look at WIP in manufacturing, we are essentially taking inventory of products that are still in the process of being made.
So, as soon as a raw material is starting to be molded into an assembly item through labor, we can calculate it as WIP. Essentially, we’re looking at the all-important middle ground between material purchasing and landing with finished products.
For example, if you are a maker of good old-fashioned bicycles, you will start by making the saddles, brakes, wheels, frames, handlebars, and gear shifts long before you have the finished product.
Now the costs of all these items, the labor that goes into them, and the manufacturing overheads involved add up to your current inventory assets on your balance sheet. Later they are transferred to your finished goods account and then to your cost of goods sold.
But until they do, they are an area of cost that should be isolated from your finished products. There is a great benefit to doing this, as you will find that a lot of your production bottlenecks and areas for improvement come in WIP manufacturing.
Problems can occur when certain materials are more prone to breaking, for example, or when you simply don’t have a process in place for purchasing materials. We’ll get to the solutions to these problems later.
But first, let’s look at how we can calculate our WIP manufacturing costs.
3 elements of manufacturing WIP
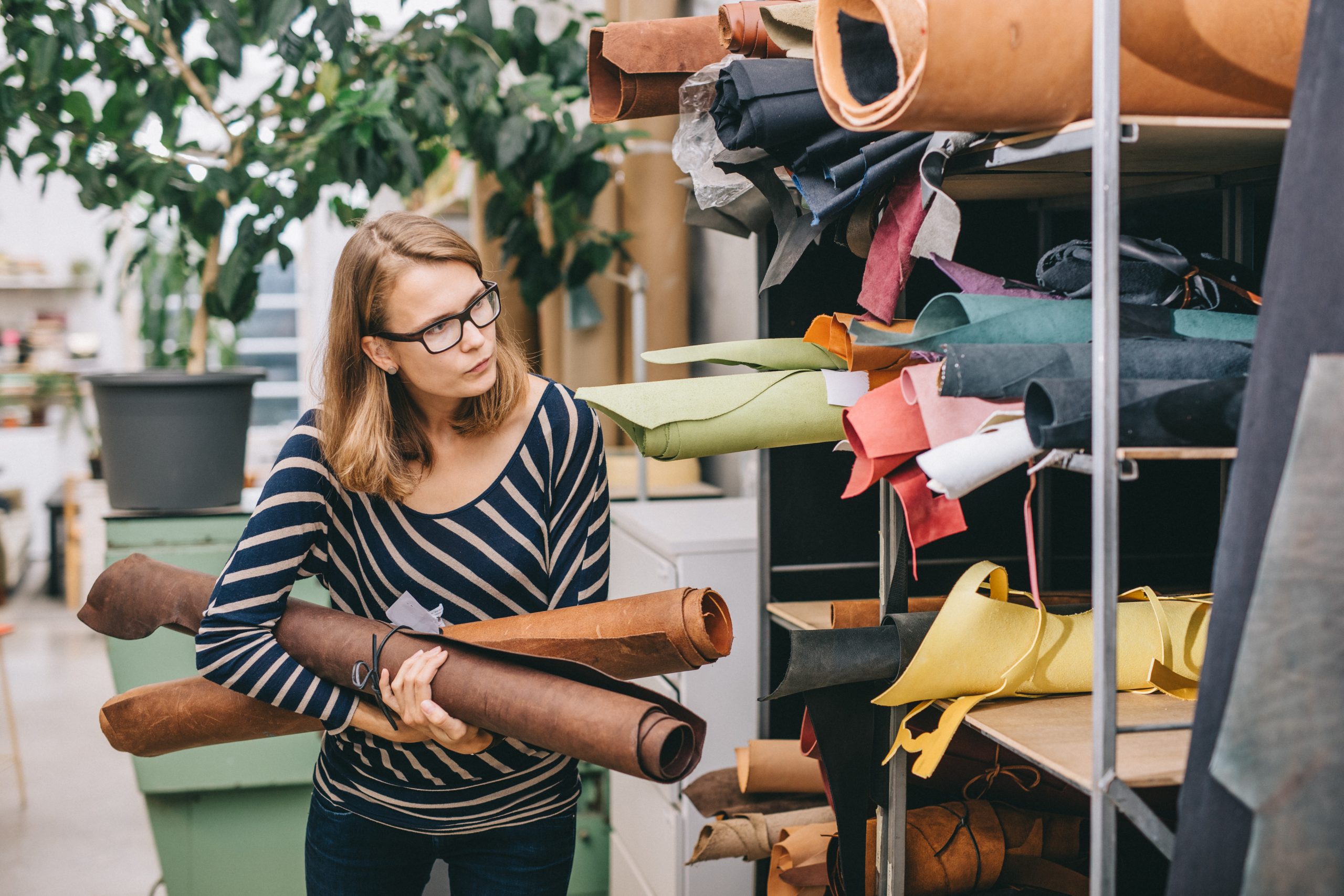
There are a few aspects to keep in mind when calculating and analyzing your WIP manufacturing.
The three elements or components of WIP manufacturing are:
1. Raw Materials
Raw materials are the basic supplies or substances used to manufacture a product. These materials undergo processing and transformation during manufacturing to become finished goods. In the context of WIP manufacturing, raw materials refer to the initial components or inputs that have been partially processed but are not yet in their final form.
2. Labor
Labor refers to the human effort involved in the manufacturing process. This includes the work performed by operators, technicians, assemblers, or other personnel contributing to producing goods. In WIP manufacturing, labor represents the ongoing work and effort put into transforming raw materials into finished products.
3. Overhead Costs
Overhead costs are the indirect expenses incurred during the manufacturing process. These costs are not directly attributable to a specific product but are necessary for the overall operation of the manufacturing facility. They include expenses such as rent, utilities, maintenance, supervision, and other administrative costs. In relation to WIP manufacturing, overhead costs are incurred continuously as production progresses.
These three elements — raw materials, labor, and overhead costs, collectively contribute to the work-in-progress manufacturing process, which involves transforming raw materials into finished products through ongoing labor and the incurrence of overhead expenses.
Examples of WIP inventory

Work-in-Progress inventory consists of partially completed goods or products that are in various stages of the manufacturing process. Here are some examples of WIP inventory across different industries:
1. Manufacturing industry:
- Partially assembled electronic devices, such as smartphones, laptops, or televisions
- Automobiles in various stages of assembly, including chassis, engine, body, and interior components
- Fabricated metal parts undergoing machining or welding processes
- Partially processed food items, such as canned goods or frozen meals
- Textile products, such as partially woven fabric or garments in different stages of production
2. Construction industry:
- Buildings or structures at different stages of construction, including foundations, framing, electrical and plumbing installations, etc
- Road construction projects with partially laid asphalt or concrete
- Multi-story buildings with incomplete floors or unfinished interiors
3. Pharmaceutical industry:
- Medications or drugs in various stages of formulation, packaging, and labeling
- Liquid or powder formulations in the process of being filled into vials or capsules
- Biotechnological products undergoing fermentation or purification processes
4. Food and beverage industry:
- Beverages in different stages of production, such as brewing beer, fermenting wine, or bottling soft drinks
- Baked goods in various stages of preparation, including dough mixing, proofing, or baking
- Canned or packaged food items that have undergone some processing but are not yet fully packaged and labeled
5. Electronics industry:
- Printed circuit boards (PCBs) at different stages of assembly, including component placement and soldering
- Semiconductors undergoing fabrication processes like etching, deposition, and lithography
- Electronic components or subassemblies awaiting integration into final products
These examples illustrate how WIP inventory can be found in various industries, representing products that are still in the process of being manufactured or assembled but are not yet finished and ready for sale.
How to calculate WIP in manufacturing
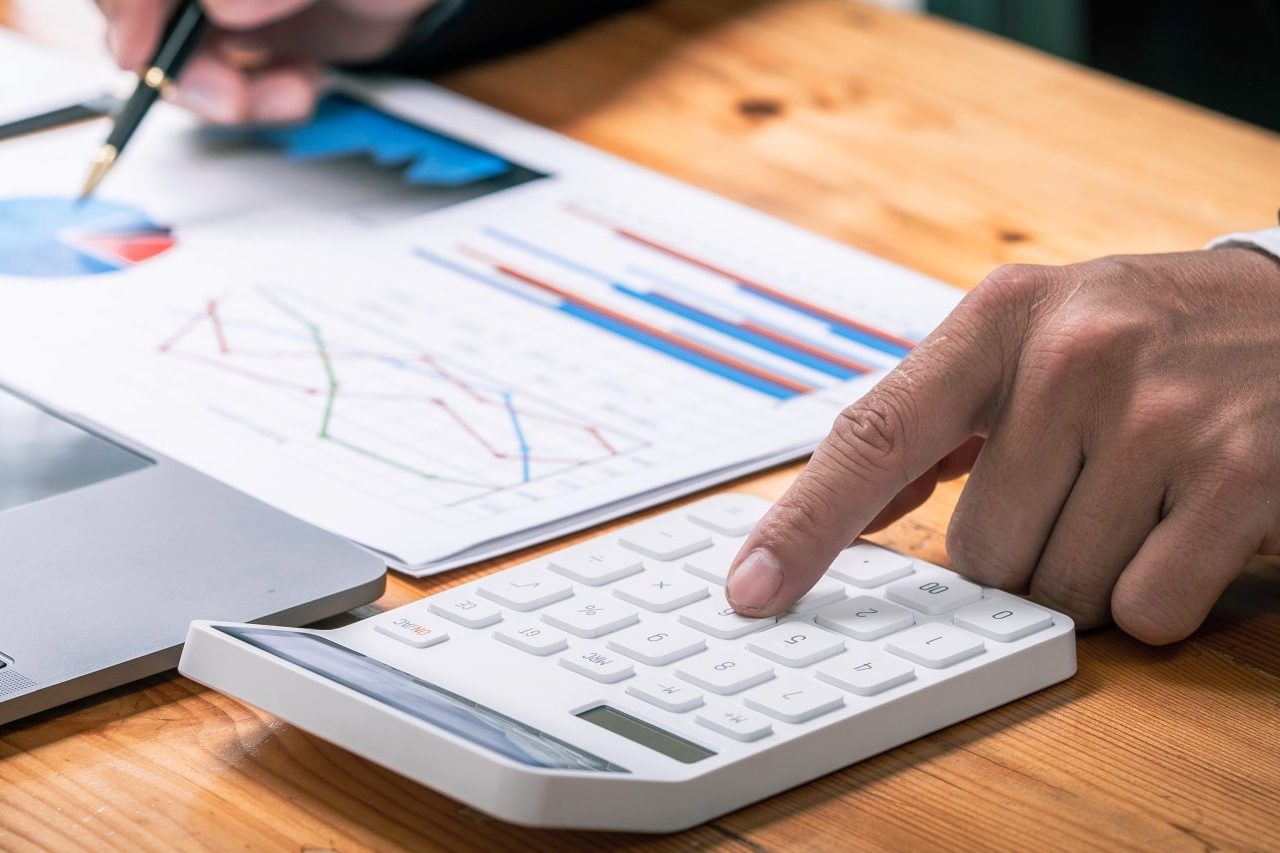
Modern manufacturers like the imaginary guys at our imaginary bike company “Framed” know that focussing on their WIP manufacturing allows them to identify where their production processes are falling short.
Just make sure that you include accurate labor and overhead costs so that you can make the most of this metric.
Alright, so we want to know how to get our numbers straight here. Keep in mind that generally, this calculation is done over a monthly accounting period as well as annually.
The basic formula for your WIP manufacturing is as follows:
WIP = WIP inventory at the beginning of the period + WIP purchased during the period – WIP inventory at the end of the period + labor costs + manufacturing overheads
Now that might seem a bit wordy, but it’s not as bad as it looks at first glance.
If we take our fantasy retro bicycle business as an example, we can get a better look.
So here we have a table that shows the WIP costs over June. This takes care of the first part of our equation before we get to labor costs and manufacturing overheads.
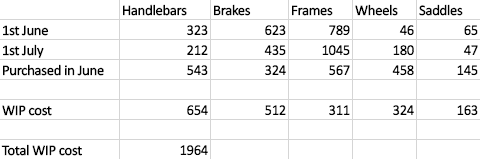
Each assembly item is calculated separately to give the total WIP costs at the end of the month. If we zone in on handlebars, for example, we can see that the business started off with $323 worth of handlebars in June and ended up with $212 worth at the end of the period.
Within this period, $543 worth of handlebar material was purchased, and presumably, much of it was used in production.
323 + 543 – 212 = $654
And once the calculation is done for all the assembly items, we can add them all up to give our total material cost. Here it came to $1964.
Now we just have to add on the labor costs and manufacturing overheads.
For labor costs, we are taking into account any labor that has a direct effect on production. These could be your workers, engineers, welders, or whoever is involved in assembling parts on the production floor.
It’s essential to distinguish between indirect and direct labor costs because indirect labor costs will be accounted for in your manufacturing overheads.
Manufacturing overhead costs include:
- Indirect labor (such as security and cleaning personnel)
- Indirect materials (glues, tapes, repair parts, etc.)
- Utilities (rent, water, gas, electricity, etc.)
- Depreciation (on equipment and machines)
So, let’s fast-forward our calculations and say that our total labor costs came to $1650 for June while manufacturing overheads came to $750. Of course, your business accountant will be very happy if your numbers ever come out this round.
But anyway, now we can use our WIP formula and bring all the pieces together.
WIP = WIP inventory at the beginning of the period + WIP purchased during the period – WIP inventory at the end of the period + labor costs + manufacturing overheads
Therefore:
WIP = 1964 + 1650 + 750 = $4364
And there we have it. The WIP formula is run through, and we have our work-in-progress manufacturing cost for June.
Even more importantly, we have split our costs into materials and assembly items so that we can analyze them further — a great jumping platform for our production scheduling processes.
Because here comes the fun bit, melting our WIP costs down to size.
Reducing WIP manufacturing costs
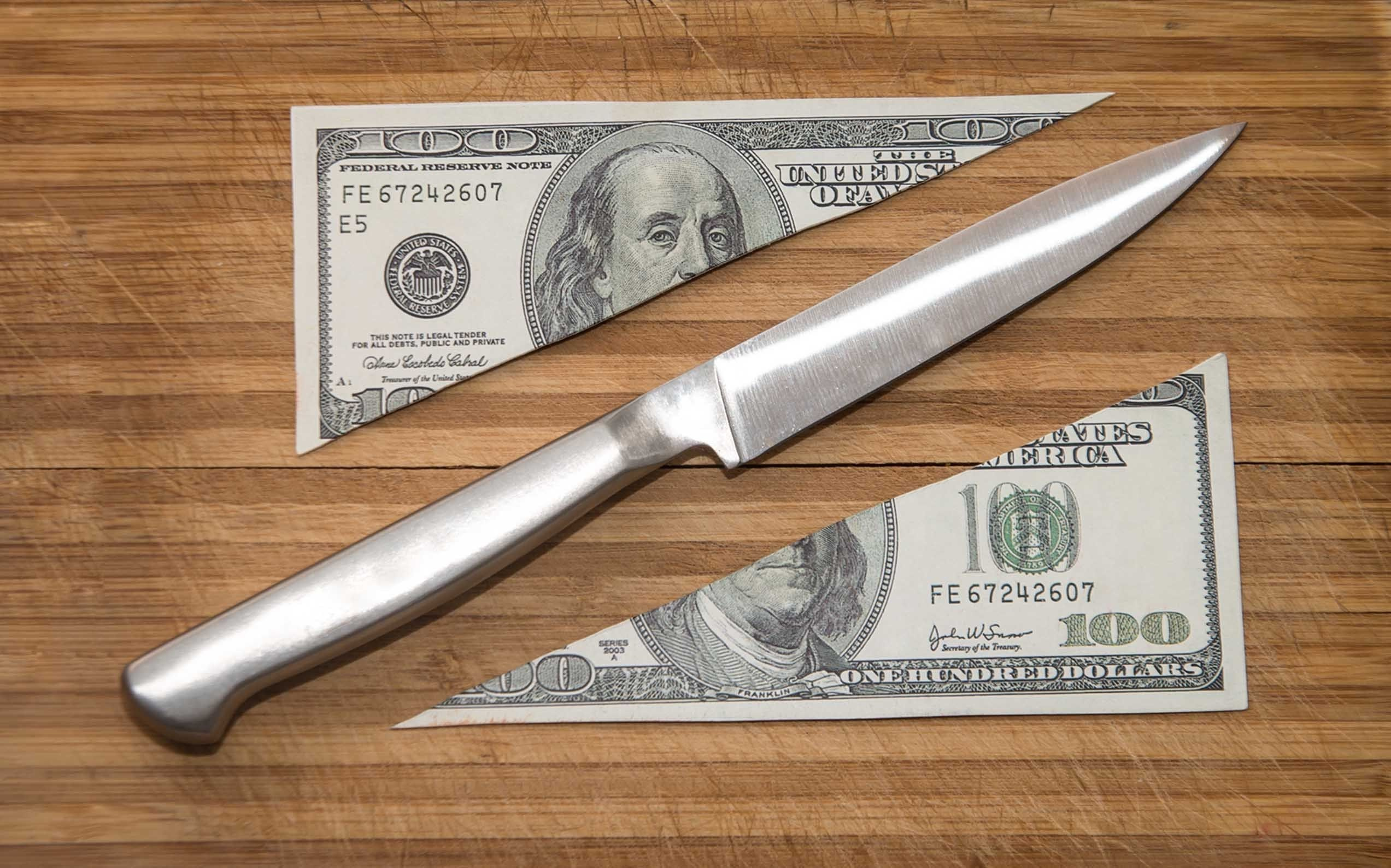
There’s not much point in looking into your WIP manufacturing without analyzing your raw materials inventory. This is the foundation of your production, and optimal material availability is vital to your entire manufacturing business.
Right, so we worked out the cost of our WIP manufacturing. But there’s not much point in doing that unless we also use the numbers to our advantage. That means looking into manufacturing cost reduction and investing in smoother operations.
Because the truth is that many manufacturing businesses’ bottlenecks occur in the production stage where WIP lies.
Here are a few techniques you can use to maximize efficiency through WIP manufacturing.
1. Identify faulty machinery
One of the keys to decreasing your WIP costs is identifying where your bottlenecks occur. And an often overlooked piece of the puzzle is equipment effectiveness and reliability.
If you find that a particular set of items using the same machinery are racking up significant overheads, then you need to look into why that is. It may be that the machine is breaking too many parts and requiring replacement materials.
In this case, you might need to repair or upgrade your machine. It might seem counter-intuitive, but the money and resources you save in the long run will be well worth it.
2. Plan for demand
Properly analyzing your sales forecasts will allow you to implement demand planning strategies and increase your awareness on the manufacturing floor.
Plenty of WIP manufacturing costs are simply a matter of blind planning. But knowing where your high and low seasons start will allow you to set the correct reorder points for your inventory and stay on the lean path to success.
3. Collaborate with your suppliers
Making sure that you are on the same wavelength as your suppliers cannot be underestimated when optimizing your WIP manufacturing. It may seem unrelated, but the fact is that faulty or inappropriate parts can slow down your production processes drastically.
This is an issue that touches even the greatest of mass manufacturers, as it was reported that Ford, General Motors, FCA US, and Nissan collectively would have earned $2 billion more in operating profit had they improved their supplier relations.
In response, you should speak to your suppliers on good terms to establish your mutual needs to the closest degree. Try to be clear about what the purpose of the materials is and how they function as part of your processes.
Using your suppliers’ expertise, you can find suitable materials and get the most out of them.
WIP manufacturing software
WIP production planning doesn’t have to be complex. Book a demo to get all your questions answered regarding Katana’s features, integrations, pricing, and more.
Taking WIP manufacturing to the next level
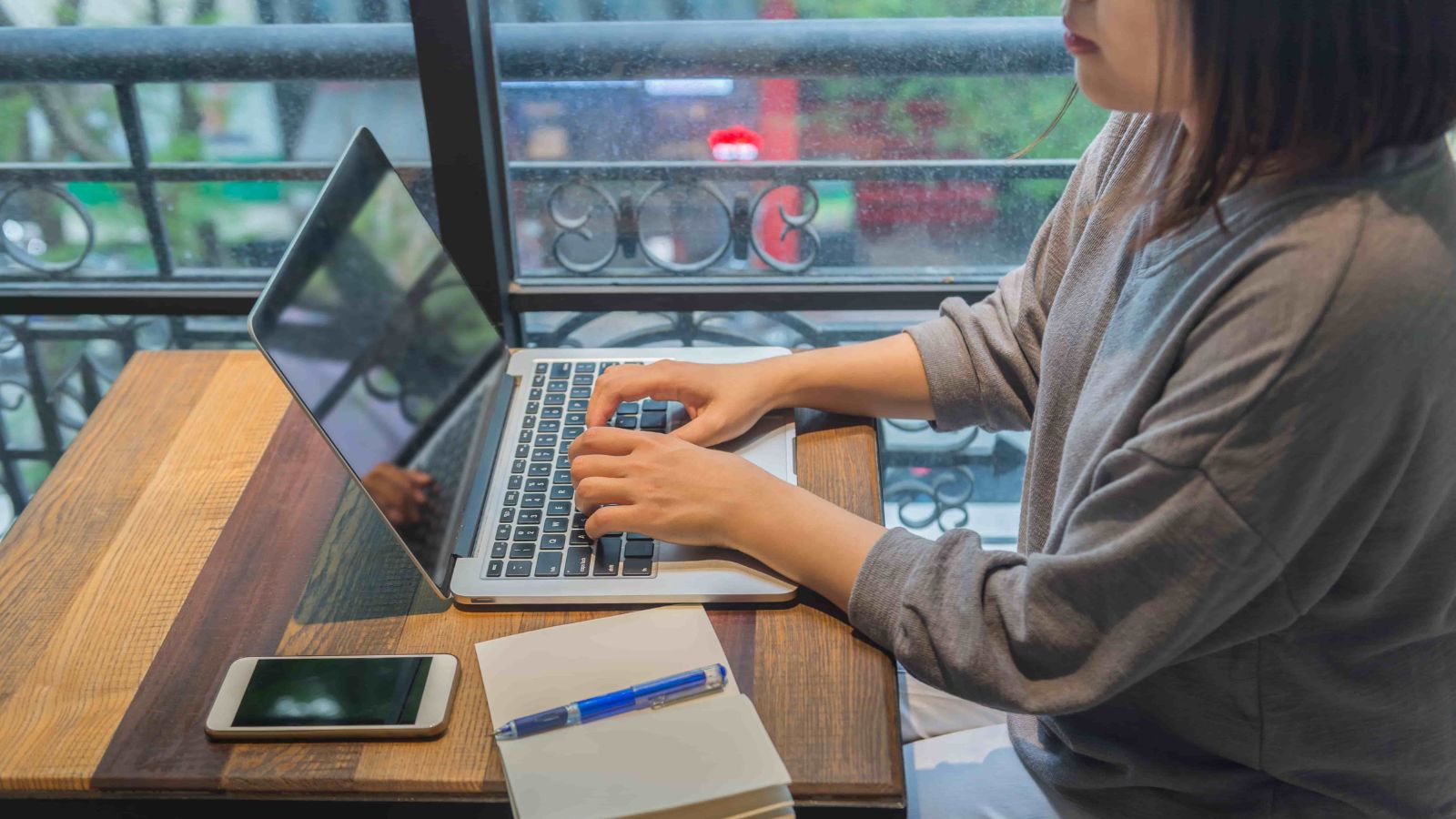
Katana has been designed with a color-coded visual platform so modern manufacturers can have an easy-to-understand overview of their business in real-time. WIP manufacturing is only one cog in the machine, after all.
Your WIP items are made up of an assortment of raw materials. But one of the main problems comes in managing your material availability.
Because as much as we would like to keep materials at optimal levels, it’s rarely that easy. The reasons for it are plenty, and it often comes down to the fact that many products and assembly items are made of the same materials.
That’s why it can be challenging to maintain the correct inventory levels without overstocking and inadvertently increasing your carrying costs.
Using Katana, you can ensure that your material and finished goods inventory are always at optimal levels. The smart master planning engine will commit materials to your manufacturing and sales orders so they never cross over.
This way, your WIP manufacturing is always running smoothly without incurring unnecessary costs.
But Katana isn’t just about keeping your inventory levels on point.
It’s an all-in-one solution that manages your production and sales from a single platform. From start to finish, you can follow your order fulfillment cycles effortlessly so that you can spend your time growing your business.
Here are just a few of the benefits:
- On-demand access to your manufacturing costs
- Finished goods and material inventory
- Use as a production scheduling software
- Integrate and synchronize your favorite platforms, including e-commerce, accounting, reporting, and CRM
- Plan your material purchasing efficiently
- Ditch inefficient Excel spreadsheets forever
- Keep your entire business workflow on a single platform
But ultimately, the takeaway point here is that your WIP manufacturing is not to be taken lightly. The journey your materials take is as vital to the growth of your business as the finished products themselves.
Because by identifying your bottlenecks and reducing your manufacturing costs, you might very well find the road to growth becoming a whole lot clearer.
Table of contents
Accounting Guide
Get visibility over your sales and stock
Wave goodbye to uncertainty by using Katana Cloud Inventory for total inventory control
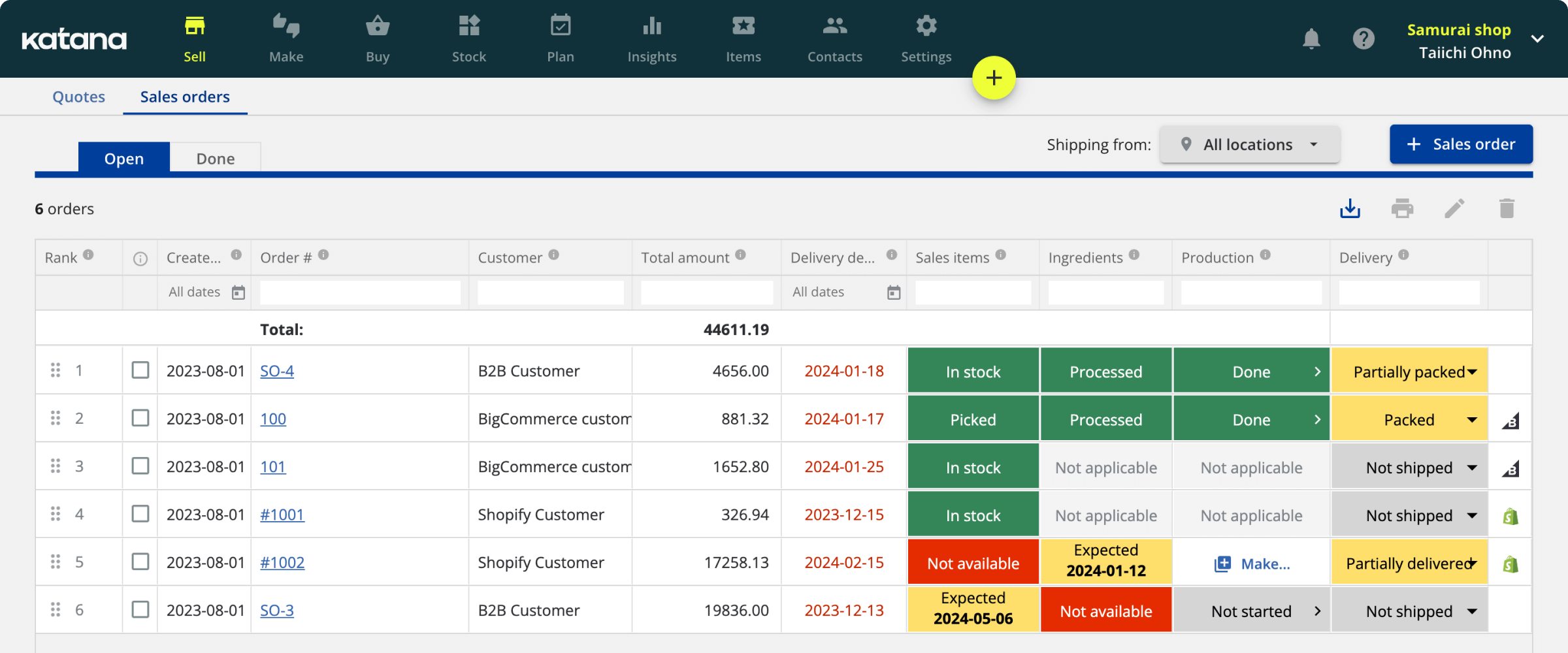