Unlock the possibilities of sheet metal fabrication
Metalworking may not be the most glamorous process, but with the current rise in environmentally friendly and recyclable materials, it’s definitely worth looking into. So put on your safety goggles and crank up the heavy metal — we’re about to dive into the world of sheet metal fabrication!
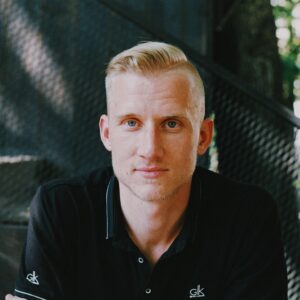
Henry Kivimaa
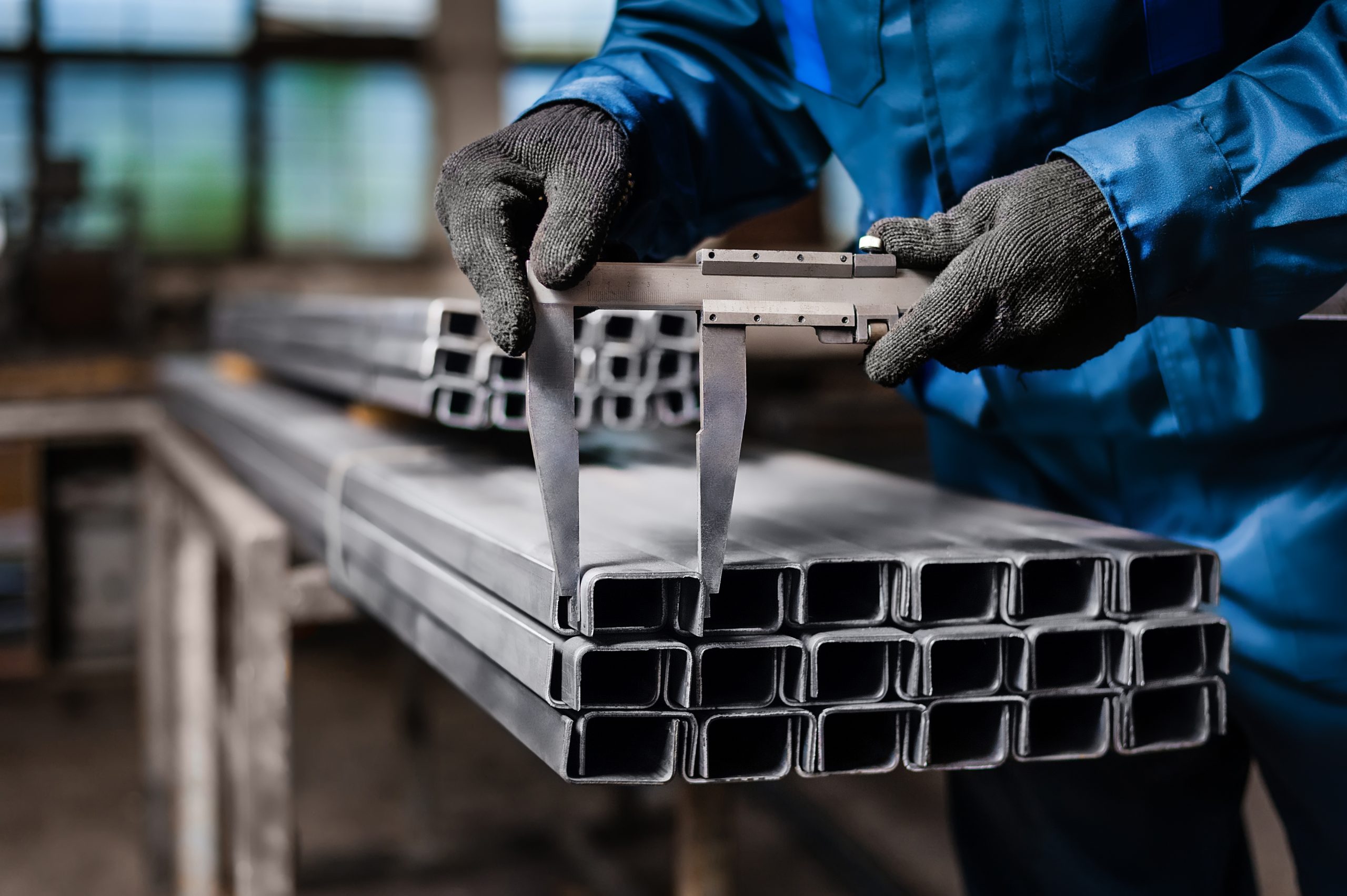
Sheet metal manufacturing may seem like a dull topic. In reality, it’s anything but flat. Sheet metal fabrication is an art honored for centuries, with ancient civilizations using metalworking techniques to create weapons, armor, and tools.
Today, sheet metal fabricators are like modern-day blacksmiths. They take raw materials and transform them into functional products that are used in everyday life.
Sheet metal is a thin, flat piece of metal. It’s typically made from steel, aluminum, brass, or copper and can be found in different thicknesses and sizes.
Overall, sheet metal is a versatile and widely used material and plays a critical role in many industries.
How to manufacture sheet metal?
Sheet metal is manufactured through a process known as sheet metal fabrication. This process involves cutting, bending, and shaping thin sheets of metal to create a variety of products and components.
First, the raw material is cut to the required size using specialized cutting tools such as shears or plasma cutters. Then, the metal is shaped using various bending tools such as brakes, rollers, or press brakes. This step allows for precise bends, curves, and angles to be created in the metal.
Once the metal sheet is cut and shaped, it may undergo additional processes such as different types of welding, punching, or drilling to create specific features or combine multiple pieces. Finally, the finished product may be coated, painted, or treated to enhance its durability or appearance.
Sheet metal fabrication is a complex and precise process that requires skill and specialized equipment to create high-quality sheet metal products.
What is the manufacturing process of steel sheets?
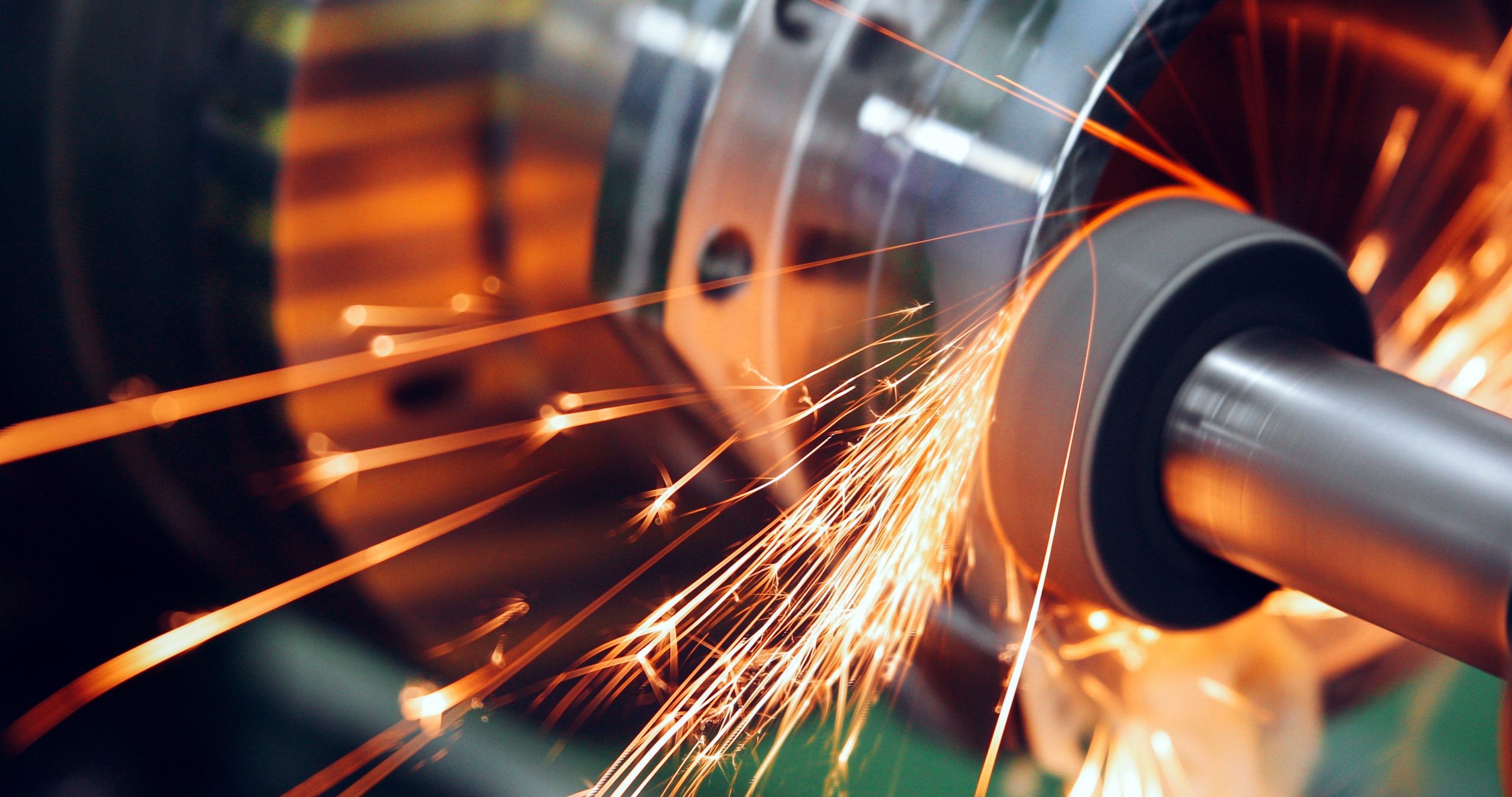
Metal sheet manufacturing transforms metal into thin, flat sheets that can be used for many different applications. This process consists of the following steps.
- Material selection
- Cutting
- Forming
- Annealing
- Finishing
- Quality control
1. Material selection
Material selection is an important step in the sheet metal fabrication process. Choosing a suitable material can significantly impact the finished product’s performance, durability, and cost. Common materials used in sheet metal fabrication include steel, aluminum, copper, brass, and other alloys.
Steel is popular due to its strength, durability, and relatively low cost. It is commonly used in construction, automotive manufacturing, and industrial machinery applications. On the other hand, aluminum is lighter in weight and relatively corrosion-resistant, making it ideal for use in more extreme conditions, such as the aerospace and marine industries. Copper and brass are often chosen for their beautiful visuals and are commonly used in decorative applications.
When selecting a material for sheet metal fabrication, it’s essential to consider the project’s specific needs, such as strengths, corrosion resistance, thermal conductivity, and appearance. By carefully considering the properties and requirements of different materials, sheet metal fabricators can choose the best material for the job and ensure a successful result.
2. Cutting
Cutting is a critical step in sheet metal fabrication and involves removing excess material from a sheet of metal to create the desired shape and size. There are several cutting techniques used in sheet metal fabrication, including:
- Shearing — Specific scissors or blades are used to cut through the metal. Shearing is best suited for straight cuts and can be used on different sheet metal thicknesses.
- Laser cutting — A high-powered laser melts or vaporizes the metal. Laser cutting is precise and can be used to create complex shapes and designs, but it is typically more expensive than other cutting methods.
- Plasma cutting — This involves using a high-temperature plasma arc to melt the metal and create a clean cut. Plasma cutting is fast and effective but may not be as precise as other cutting methods.
- Waterjet cutting — Uses a high-pressure water stream and abrasive particles to cut through the metal. Waterjet cutting is versatile and can be used on a wide range of materials, but it may not be as fast as other cutting methods.
Ultimately, the sheet metal fabrication techniques for cutting depend on the project’s specific requirements. Factors such as the material thickness, desired cut quality, and budget will all influence the choice of cutting method. By carefully selecting the appropriate technique, sheet metal fabricators can ensure a high-quality cut.
3. Forming
Forming is another important process in sheet metal fabrication that involves shaping and bending a sheet of metal to create a desired shape or component. Some forming techniques are:
- Bending — A brake press or similar tool is used to create a bend in the metal. Bending is commonly used to create simple shapes such as L-brackets or U-channels.
- Rolling — The metal sheet is passed through a set of rollers to shape it into a cylinder or cone gradually. Rolling is popular in the manufacturing of tubes or pipes.
- Stretch forming — The metal sheet is stretched over a die to create a desired shape. Stretch forming allows the creation of complex, curved shapes.
- Hydroforming — This involves using hydraulic pressure to press the metal sheet against a die to create a desired shape. Hydroforming is primarily used in the custom metal fabrication of automotive body parts.
The forming method should be based on the desired shape, material thickness, and price range. Choosing the appropriate forming technique ensures a successful end result.
4. Annealing
Annealing is a process used in sheet metal fabrication to soften the metal and make it easier to mold. The metal is heated up to a temperature below its recrystallization point and then cooled down slowly, during which it rearranges its crystal structure. The slow cooling process helps relieve internal stresses in the metal, making it less brittle and easier to work with.
In addition to improving formability, annealing can also be used to improve the overall quality of the metal. The slow cooling process helps refine the structure of the metal, making it more uniform and consistent. This results in a stronger, more durable final product.
Overall, annealing can help improve the quality of the metal and make it more malleable. By heating and cooling the metal in a controlled way, fabricators produce high-quality sheet metal parts that can endure the manufacturing process as well as future use.
5. Finishing
Sheet metal finishing means applying various techniques on metal sheets to improve their appearance, functionality, and durability. Some standard sheet metal finishing techniques include:
- Deburring — Sharp edges, burrs, and rough spots are removed from the sheet metal surface to ensure that it is safe to handle and does not damage other components during assembly.
- Grinding and sanding — Using abrasives to smooth out rough surfaces and prepare the metal for painting or coating.
- Painting and coating — A layer of paint, powder coat, or other protective coating is applied to the sheet metal surface to improve its appearance and protect it from corrosion.
- Polishing — This technique uses abrasive compounds to buff the sheet metal surface to a high shine, giving it a glossy finish.
- Plating — A thin layer of metal, such as chrome or nickel, is applied to the metal surface to improve its appearance and resistance to corrosion.
- Anodizing — An electrolytic process to create a protective oxide layer on the surface of the sheet metal, to further improve its resistance and strength.
Overall, sheet metal finishing is used to improve the look and quality of the surface of the metal and, when done correctly, ensures long-lasting effects on the final products.
6. Quality control
Manufacturing quality control helps ensure the final product meets the required specifications and standards. There are several steps involved in the quality control process for sheet metal fabrication, including:
- Material inspection — The incoming raw materials are inspected to ensure meeting the predetermined specifications, including size, thickness, and material composition.
- Design and engineering review — Design and engineering drawings are checked to confirm their accuracy and ensure that the pieces can be effectively manufactured.
- Production monitoring — The production process is monitored closely to ensure the parts are manufactured according to the requirements. This also means that any defects or deviations from the specifications are identified and corrected as soon as possible.
- Final inspection — Finished parts are inspected to make sure they meet the specifications and quality standards before being shipped to the customer.
For the quality control process to be effective, it’s essential to have a well-trained and experienced team of quality control professionals who are familiar with the industry standards and have the necessary skills and tools to perform the required inspections and tests. Investing in good production quality control checklists, teams, and procedures guarantees successful manufacturing and high customer satisfaction.
What are the benefits of sheet metal fabrication?
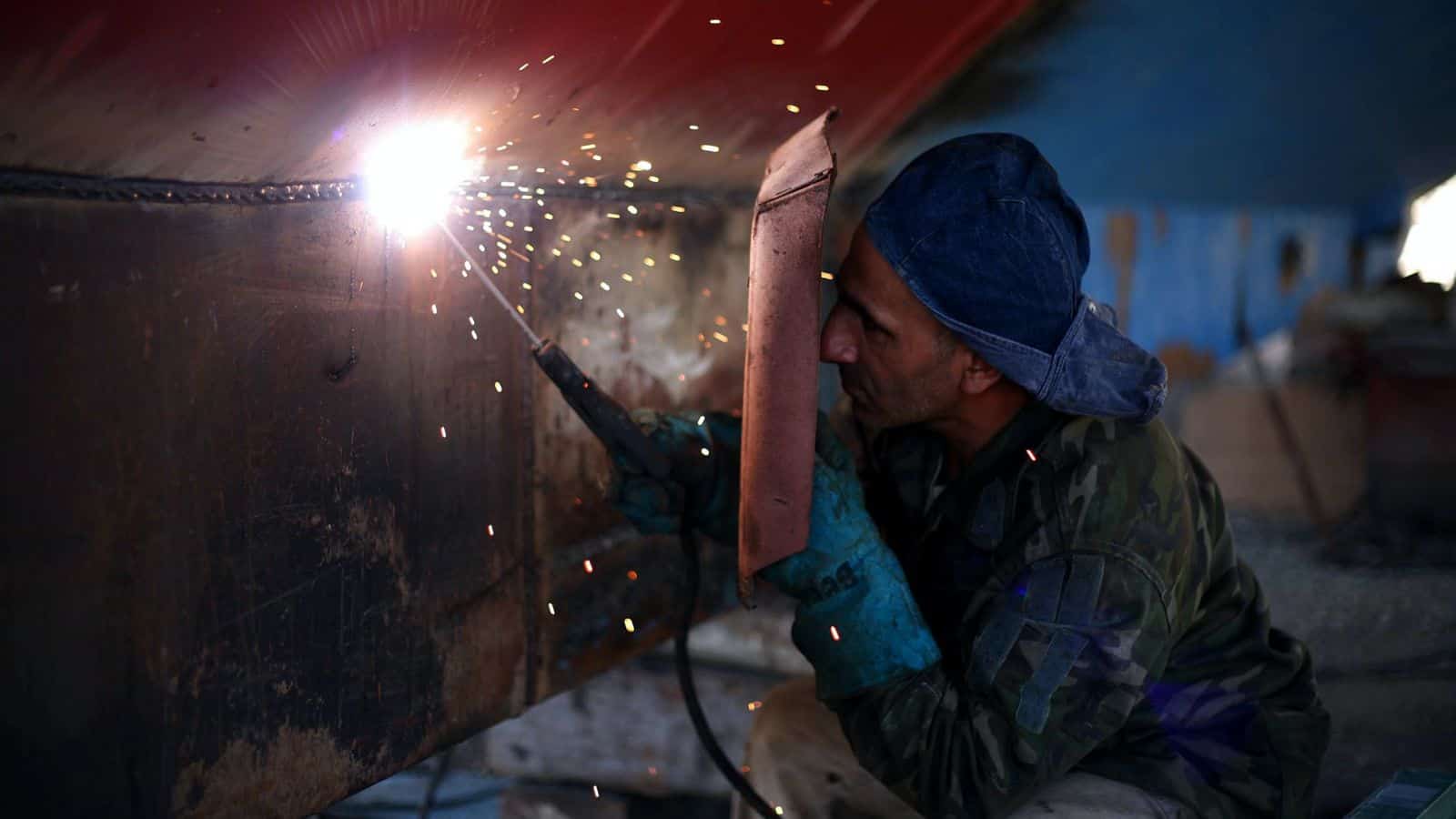
Sheet metal’s benefits are acknowledged in many industries, including automotive, aerospace, building materials, and technology. Sheet metal fabrication is an efficient way to manufacture high-quality metal components in large quantities.
It has many advantages that make it a common choice for a wide range of products. Some of the benefits include:
- Strength and durability — Sheet metal is known for being robust, making it a reliable material for numerous functions. When processed properly, it can withstand high temperatures, pressure, and environmental conditions without losing shape or breaking down.
- Versatility — Sheet metal can be formed into any shape and size. It can be cut, bent, punched, stamped, and welded to create more complex parts and components.
- Cost-effective — Compared to other materials, such as plastics or composites, sheet metal is relatively cost-effective, making it an ideal choice for many industries.
- Easy to work with — Sheet metal is easy to work with, allowing for efficient and precise manufacturing processes. It withstands extreme conditions inside and outside the factory and requires no special treatment.
- Recyclable — Sheet metal is highly recyclable, making it an eco-friendly choice for those aiming to get into green manufacturing. It can be recycled by melting and reprocessing to create new products, reducing waste and environmental impact.
How to learn sheet metal fabrication?
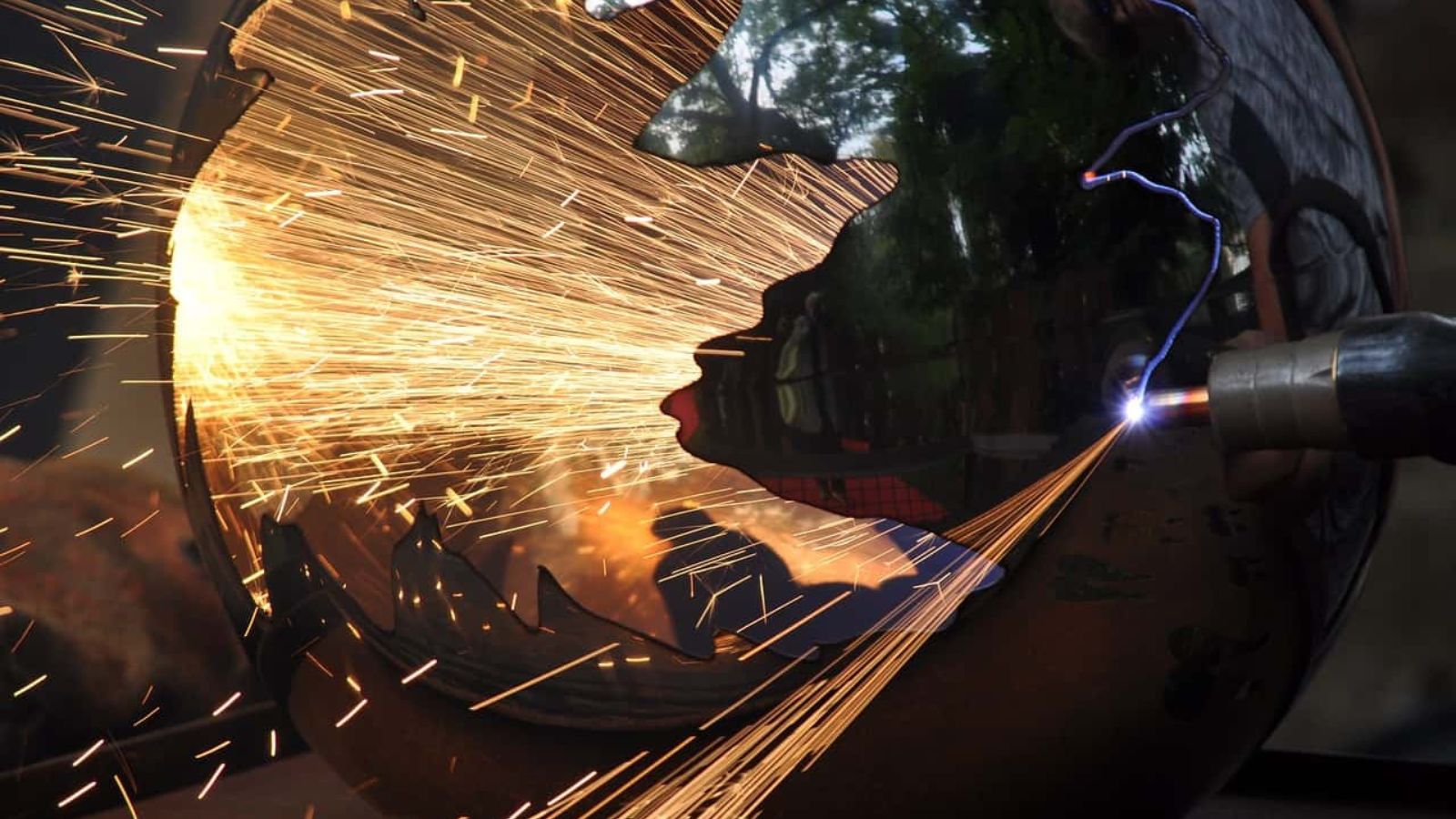
Learning how to fabricate sheet metal involves combining theoretical knowledge and practical experience. There are many ways to gain both.
Learn the theoretical knowledge
Start by learning the basics of sheet metal fabrication, including the different types of materials, manufacturing processes, and safety procedures. You can take courses, read books, or watch online videos to understand the principles of sheet metal fabrication.
Learn from experienced professionals
Find sheet metal fabricators who have experience and can mentor and guide you in the learning process. You can shadow them, ask questions, and observe their techniques to learn manufacturing best practices from those who have already gathered all the necessary knowledge.
Practice on your own
Set up a small workshop with basic tools and equipment, and start practicing sheet metal fabrication techniques on your own. Start with simple projects and gradually work your way up to more complex ones.
Once you’re confident in your skills, you could start a small manufacturing business from your workshop. Practice makes perfect, they say, so why not gather experience welding and selling your products to earn some money on the side to support your new hobby?
Attend workshops and training programs
Many manufacturers, trade organizations, and community colleges host workshops and courses. Attending these will be an excellent way to learn advanced techniques and gain practical experience from experts.
Network with other fabricators
Attend industry events, join online forums, and network with other fabricators to learn about the latest manufacturing trends and techniques in sheet metal fabrication. This will also help with finding contacts for future business endeavors and cooperation.
Get certified
Consider getting certified by a recognized certification body to demonstrate your proficiency in sheet metal fabrication. While your work will speak for itself, being certified creates a trustworthy image that your partners and customers will appreciate.
How can Katana help with sheet metal fabrication?
Katana is a cloud inventory software that can help businesses iron out the details of their manufacturing, from supplies to shipping. With its wide range of automation and features, Katana provides real-time visibility and control over the entire production process.
Production planning
Plan your production schedules based on customer orders and available resources, such as materials, budget, and workforce. Create tasks for shop-level workers — or operators, as they are called in Katana — and give them access to the Shop Floor App, where they can view and complete their assignments via any smart device.
Inventory management
Live inventory management, from raw materials to finished goods, allows manufacturers to keep track of their stock levels and reorder materials when needed. Set reorder points to remind you to restock low supplies before running out.
Traceability
Katana provides traceability of the entire production process, including the raw materials used and labor hours spent on each step. Batch and lot tracking allows tracing each product’s lifecycle — from raw material to retail.
Real-time data
Diving into real-time data allows manufacturers to monitor their progress and adjust as needed to optimize their production process. Insights on all aspects of the business help put together a detailed manufacturing analysis to support its further growth.
Integrations
Put together a custom workflow to meet the specific needs of your business. Katana has several built-in integrations to fill your requirements, including bookkeeping, automation, and e-commerce tools. If some area of your business still needs particular attention, feel free to connect to other software using Katana’s open API.
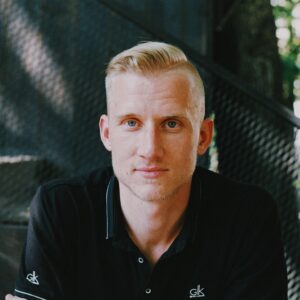
Henry Kivimaa
Table of contents
Get inventory trends, news, and tips every month
Get visibility over your sales and stock
Wave goodbye to uncertainty with Katana Cloud Inventory — AI-powered for total inventory control