15 expert practices for retail inventory management
The perfection of your retail inventory management is critical. In this article, you learn what is retail inventory management and the best 15 practices you can follow to optimize your business.
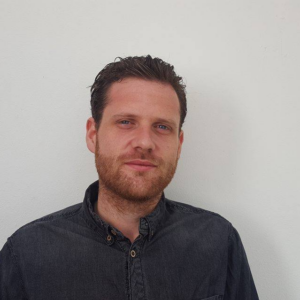
James Humphreys
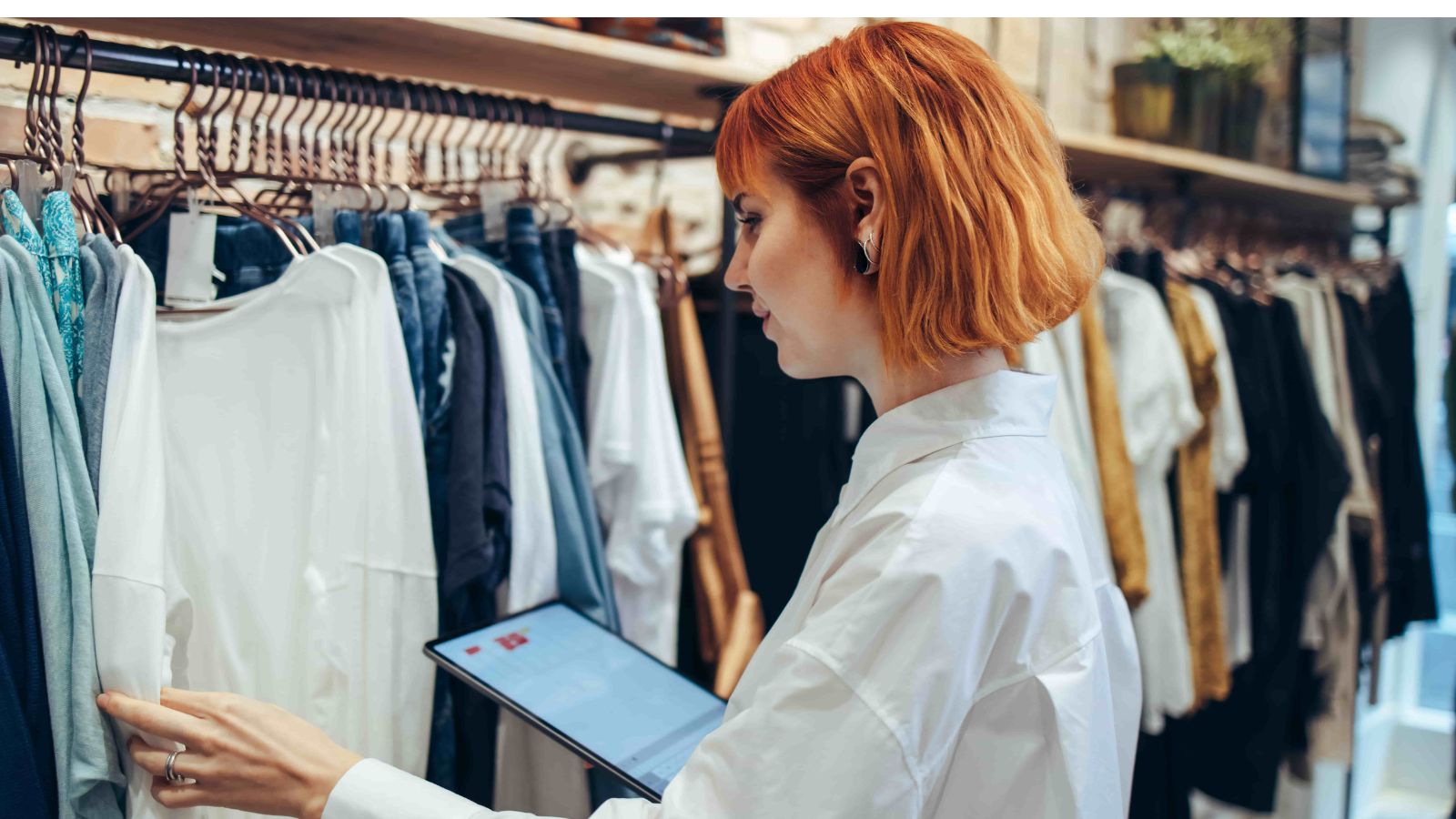
In retail, there’s one crucial element of your company that can make the difference between your business thriving or surviving.
Neglecting to optimize your retail inventory management, especially in businesses that also have to juggle production, spells certain doom for you. Your inventory is the lifeline of your business. If not properly managed, your it will hemorrhage money, items, and sales, and all that you’ve worked hard to build will perish.
However, this fate is easily avoidable.
We’ve put together this article exploring store inventory management in retail and the practices you can follow to optimize how you and your staff handle inventory.
What is retail inventory management?
Retail inventory management is organizing and tracking a store’s merchandise.
This includes everything from:
- Purchase management and stock-taking
- Displaying and selling products
- Inventory management
Knowing what is store inventory management in retail, is essential for any business that sells products.
It helps you keep track of your inventory levels, ensure that you have enough merchandise on hand to meet customer demand, and avoid running out of popular items. Businesses can use several different methods to manage their inventory, including:
- Barcoding and scanning systems
- Electronic data interchange (EDI)
- Warehouse management systems (WMS)
- Cloud inventory management software
Whichever system you choose, it’s important to ensure that it’s easy to use and fits your store’s specific needs. Now you know what is inventory management in retail. How exactly does it work?
How does retail inventory management work?
Retail inventory management is critical to the success of any retail business.
Get it wrong, and you’ll be significantly disappointing your customers.
Good inventory management ensures that a business has the right stock level to meet customer demand while also avoiding excessive levels of stock that can tie up valuable resources. Several different methods can be used to manage inventory, including:
- First-in, first-out (FIFO)
- Last-in, first-out (LIFO)
- Economic order quantity (EOQ)
- Just-in-time (JIT)
What is first-in, first-out (FIFO) in retail inventory management?
First-in, first-out (FIFO) is a retail inventory management system in which the first items to arrive are also the first items to be sold.
This system is often used in perishable goods industries, such as grocery stores, where it is important to keep track of expiration dates. FIFO can also be used in non-perishable goods industries, such as clothing stores, to ensure that older inventory is sold before newer inventory arrives. There are several benefits to using a FIFO system:
- It helps avoid stockouts of popular items since the newest products are always being made available first
- It can help reduce waste and dead stock since outdated products are less likely to sit on shelves for long periods without being sold
- It can help businesses avoid inventory shortages and provide better inventory control over costs under certain circumstances
However, there are some drawbacks to using a FIFO system as well:
- It may not be the best option for products where freshness is not a priority — since older items are often disposed of before they expire, this can lead to unnecessary waste
- In high-demand or low-supply periods, newer inventory may sell faster than needed and force businesses to restock more frequently than necessary
- This system does not account for trends that could impact how quickly different products sell and may not always be ideal for all businesses
There are several live inventory management systems available to businesses, and the best option will vary depending on the products being sold, the size of the business, and other factors.
First-in, first-out (FIFO) is a popular option for many businesses, but it is not always the best choice. Carefully consider all options before choosing an inventory management system to ensure that it is the best fit for your business.
What is last-in, first-out (LIFO) in retail inventory management?
Last-in, first-out (LIFO) is a method that accounts for inventory that records the most recently produced items as sold first.
This method is often used in retail stores and other businesses because it helps reduce the burden of accounting for rapidly changing inventories. When using LIFO retail inventory management, businesses keep track of each inventory item’s cost price and sell price. The business then sells its newest stock at the lowest prices and gradually increases selling prices up until it has sold off old stock that has reached its lower limits.
There are several benefits associated with using LIFO retail inventory management, including:
- Quickly reducing the amount of work involved in managing rapidly changing inventory levels
- Allowing businesses to offer lower prices on popular or high-demand items
- Helping businesses keep track of their inventory carrying costs more easily and accurately
As with any business process, there are also some potential drawbacks associated with using LIFO retail inventory management, including:
- Potential difficulties in adjusting selling prices due to rapidly changing market trends
- Risk of low profits if selling prices aren’t able to be increased quickly enough when new stock is added to the inventory
Overall, many businesses find that LIFO retail inventory management benefits far outweigh its potential drawbacks, so it remains an important tool for managing a growing and changing inventory.
Pro tip: To learn more about the different inventory techniques, their benefits, and how to implement them in your stock management, check out our article on inventory management methods.
What is economic order quantity (EOQ) in retail inventory management?
In retail inventory management, economic order quantity (EOQ) is the order quantity a company should make for its inventory given:
- Production cost
- Demand rate
- Other variables
The goal of EOQ is to minimize the total cost of inventory, including both the cost of holding inventory and the cost of ordering new inventory.
To calculate EOQ, companies need to know their annual demand, lead time, carrying costs, and ordering costs. Once these variables are known, the EOQ formula can be used to determine the optimal order quantity.
The EOQ formula is:
EOQ = √(2*D*C/H)
where:
D = Annual demand
C = Ordering cost
H = Holding cost
The EOQ formula can be used to minimize the total cost of inventory, which is the sum of the holding cost and the ordering cost.
To find the minimum total inventory cost, companies need to optimize their ordering quantity and order frequency. The EOQ model is a helpful tool for retail inventory management, but it has some limitations:
- It assumes that demand is constant, which may not be realistic
- It assumes that lead time and carrying costs are known and constant, which also may not be realistic
- It does not consider other factors, such as transportation costs or taxes
Despite these limitations, the EOQ model can still be a helpful tool for retail inventory management.
What is just in time (JIT) in retail inventory management?
Just-in-time inventory management in retail is a method of managing goods and raw materials in your retail store and shop floor.
JIT relies on the principle that suppliers should receive goods just in time to fulfill an order. In other words, retailers only receive goods when they need them and never more than what is necessary to fill current orders.
There are several benefits to using a JIT approach to inventory management. First, it can help you reduce wasteful spending on storage space or equipment for holding excessive amounts of stock. In addition, JIT allows for faster delivery times for customers and decreased costs associated with lost sales due to out-of-stock items.
Finally, this type of inventory strategy also leaves room for more frequent and accurate stock-taking, which can help identify potential issues with your product range sooner.
If you’re thinking of implementing a JIT inventory management system in your retail business, it’s important to partner with a supplier who is experienced in this type of approach. They can help you put the necessary systems and processes in place to ensure your business runs as smoothly and efficiently as possible. A JIT inventory approach can help your business thrive in today’s fast-paced retail environment with the right partner.
Now you know what is store inventory management in retail, the methods for managing stocks, and their own advantages and disadvantages.
The best method for a particular business will depend on:
- The type of goods being stocked
- The level of customer demand
- The resources available to the business
To make sure that inventory is managed effectively, businesses need to have systems and processes in place to track stock levels and keep accurate records — this can be done manually or with the help of specialized purchase order software.
Good retail inventory management is essential to the success of any retail business. By putting in place effective systems and processes, businesses can ensure that they have the right level of stock to meet customer demand while also avoiding excessive levels of stock that can tie up valuable resources. If you’re thinking of starting a retail business, it’s important to consider your approach to inventory management from the very beginning.
By doing your research and choosing the right systems and processes for your business, you’ll be well to achieve success in this competitive space.
Get a demo
Inventory management doesn’t need to be complicated. See what Katana’s inventory software can do and see why thousands of businesses made the switch.
Best practices for becoming an expert in retail inventory management
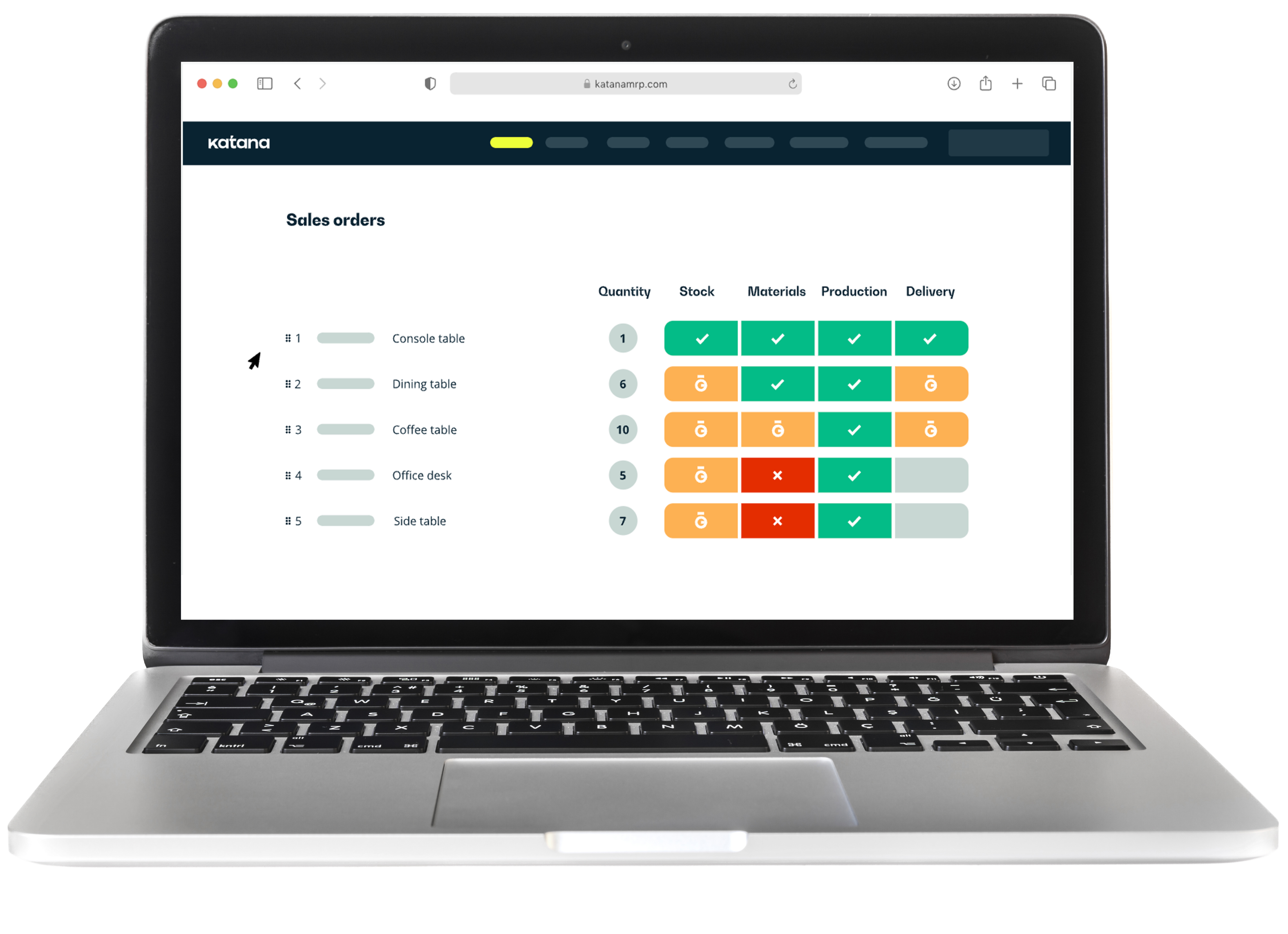
Inventory management is an essential part of running a successful retail business.
It’s important to have a solid strategy to avoid overselling, stocking out, and keeping track of your inventory levels.
But what are the best practices for effective inventory management? Here are 15 expert practices to get you started on the road to improving retail inventory management:
1. Analyze data
Analyze your sales data thoroughly when forecasting future demand for each product you sell, taking into consideration the following:
- Seasonality
- Available inventory
- Pricing changes
- Competitors’ offerings
- Just about any factor that might affect customers’ buying patterns.
This will help ensure your inventory levels stay consistent with customer demand.
Data analysis is critical in retail inventory management for several reasons.
First, understanding past sales trends helps retailers forecast future demand and plan their inventory accordingly. This prevents overstocking, which can tie up capital and result in markdowns or understocking, leading to lost sales. Second, data analysis can help retailers identify opportunities to improve their inventory turnover and, ultimately, their profitability.
For example, if a retailer notices that certain items are selling slowly, they may adjust their order quantities or shelf placement accordingly.
Finally, data analysis can help retailers track and predict changes in customer behavior, such as seasonal shopping patterns — this information can be used to inform marketing and promotional strategies.
2. Implement software
Use software or apps to keep track of inventory levels on hand.
This will give you real-time updates and help you decide about ordering more stock or changing prices to move items faster. As a retailer, it is crucial to have an effective inventory management system in place to keep track of your stock and ensure that you can meet customer demand. There are many benefits to implementing software in retail inventory management, including:
- Improved accuracy — Ensure that your inventory records are always up-to-date by using the software. This ensures that you are not wasting time and resources tracking down misplaced or inaccurate inventory records. Instead, you can focus your efforts on growing your business and meeting customer demand
- Improved efficiency — When all of your inventory information is kept in one place, it is much easier to manage your stock efficiently. This means that you can quickly and easily reorder inventory when it is needed or return items to suppliers when they are no longer required
- Reduced costs — By implementing software in your retail inventory management system, you can significantly reduce costs related to managing stock, such as labor costs associated with tracking down missing items or inaccurate records. By automating many administrative tasks, you can reduce your reliance on manual processes and free up time and resources to focus on growing your business
3. Prioritize products
When restocking your store, order bigger quantities than usual for popular items likely to sell out quickly.
Then set price changes to take effect at different times for each product to maximize sales and minimize losses from unsold stock.
When it comes to retail inventory management, one of the most important things to keep in mind is the need to prioritize selling products. This is because the goal of any business is to make a profit. To do that, retailers need to ensure that they are selling as many products as possible.
While there are many different ways to prioritize selling products, one of the most effective approaches is to look at customer demand.
Specifically, businesses should identify and satisfy their customers’ needs. This can be done by leveraging data analytics tools such as sales forecasting models, inventory valuation methods, and inventory optimization techniques. Businesses will help increase their bottom line while also providing a better experience for their customers.
4. Investigate the bottom line
Constantly evaluate metrics like gross margin, shipping costs, receipts per square foot, and other profitability factors — then use these insights to adjust prices so they’re just right.
Investigating the bottom line of retail inventory management is an important task for many reasons:
- It allows businesses to optimize their inventory levels and improve profitability
- It helps managers identify trends in customer demand that can be used to make better purchasing decisions in the future with tools such as purchase order software
- It can give retailers a more accurate understanding of the state of their business and allow them to make strategic changes as needed
5. Demand planning
Increase your forecasting accuracy by using data from multichannel retailers when estimating future demand for each product.
There are many benefits of improving demand planning in retail inventory management. Perhaps most importantly, it can help to ensure that stock levels are maintained at an optimal level. This can minimize the risk of both stockouts and excess inventory, which can negatively impact the business.
Additionally, effective demand planning can help to improve customer satisfaction levels by ensuring that products are available when needed.
It can also help improve operational efficiency and reduce costs by reducing the need for manual intervention and increasing planning accuracy. Ultimately, improving demand planning can positively impact the bottom line.
6. Audit inventory movements
Regularly evaluate your inventory levels and adjust them to stay consistent with actual sales activity.
If you notice that a certain product is consistently selling faster than anticipated, it might be time to increase its order quantity. In contrast, if you’re consistently seeing less demand for a particular item than expected, consider decreasing the order quantity or discontinuing it completely. Auditing inventory movements is critical in retail inventory management for several reasons.
First, it helps to ensure that inventory levels are accurate and up-to-date. This is important for both operational and financial planning purposes. Second, auditing can help identify potential issues or problems with the way inventory is being managed. This can help to improve inventory management processes and procedures.
Finally, auditing helps provide transparency and accountability in the inventory management process.
This is important for both internal and external stakeholders.
Overall, there are several benefits to auditing inventory movements in retail inventory management. By ensuring that inventory levels are accurate and up-to-date, improving inventory management procedures, and providing transparency and accountability, organizations can better manage their inventories and ensure that they remain cost-effective and profitable.
7. Data mining
Use data mining techniques to find correlations between different factors (like client demographics, profit margins, and location) to make better predictions about future sales trends across all of your stores — then tweak your inventory management strategy accordingly.
Data mining plays an important role in retail inventory management. By understanding consumer buying patterns, retailers can more effectively manage their stock levels and make better decisions about pricing, promotions, and product assortments. Data mining can help retailers identify trends and optimize their inventories to match customer demand.
In addition, data mining can help retailers forecast customer demand more accurately, which can help them maintain adequate stock levels and prevent out-of-stocks.
This can reduce the costs associated with lost sales and reduce logistics and storage expenses.
Data mining is a powerful tool that helps retailers manage their inventories more effectively and improve their bottom line.
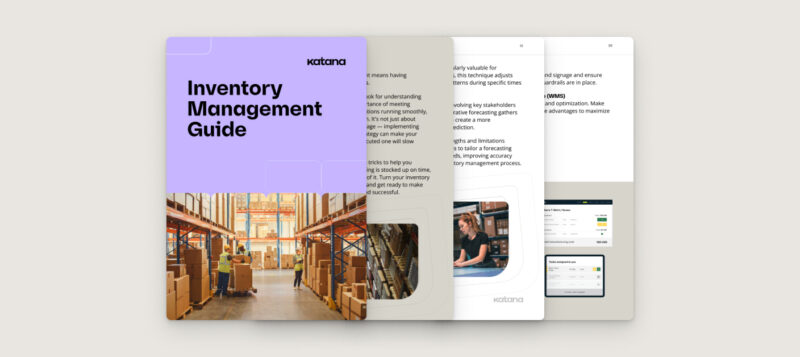
Download the ultimate guide to inventory management
A comprehensive ebook with everything you need to know about inventory management.
8. Scheduling
Ensure you have enough staff, so customers don’t have to wait in long lines. This will help increase sales by making the shopping experience more pleasant and convenient.
There are several reasons why it is important to improve scheduling in retail inventory management.
Some of the key benefits include improved efficiency, reduced costs, and better customer service.
First, retailers can become more efficient by improving their inventory planning. This involves ensuring that the right amount of stock is available while also reducing the amount of time needed to process and fulfill orders. In addition, retailers can use scheduling to manage their inventories better, ensuring that they have the right products in stock.
Second, improving scheduling can help to reduce costs associated with inventory management. This includes both the costs of holding excess inventory and responding to customer orders quickly. By utilizing an effective scheduling system, retailers can minimize the costs associated with managing their inventories and ensure that they can always respond quickly to customer demand.
Finally, improving scheduling can help to improve overall customer service.
When customers place orders, retailers need to be able to fulfill these orders quickly and efficiently. By utilizing an effective master production scheduling system, retailers who manufacture their own products can ensure that their customers are always happy with the products and services.
In addition, retailers who improve their scheduling systems can also provide their customers with better customer service overall, as they will be able to respond more quickly to customer inquiries and concerns.
9. Separate your inventories
Your order management for e-commerce inventory should be separate from your physical locations.
This is crucial so you don’t end up overstocking one channel while running out of stock on the other – which could result in lost revenue if you’re unable to meet customer demand promptly.
There are several key reasons why it is important to keep your inventories separate in retail inventory management. Perhaps the most important reason is to prevent stockouts. If you have one big inventory, it is very easy to lose track of what you have in stock and what you need to restock.
With multilocation inventory management, you can more easily track your inventory levels and ensure that you always have the items that your customers need.
Manufacturing retailers will be able to make better decisions about what materials to order or goods to manufacture in batches and what items to stock in smaller quantities, based on which items are selling well at different times. This can help you save money and be more efficient with your inventory management processes.
Another important reason to separate your inventories is to ensure that you have an accurate record of the value of all of your items at any given time.
Having a full record of your inventory value can help you make better decisions about how to use, order, or manufacture specific items.
It can also help you keep track of your inventory levels for tax purposes. If you have a large inventory, it can be difficult to accurately value all of your items if they are all stored together. However, if you keep your inventories separate, you can more easily calculate the value of each item and keep track of your overall inventory value.
Finally, keeping your inventories separate can also help you keep track of your inventory levels for customer service purposes.
If you have a large inventory, it can be difficult for your customer service representatives to keep track of what items you have in stock and what items you need to restock. However, with separate inventory, your customer service team can more easily access stock records and make sure that you have the items your customers need.
This can help you provide better customer service and improve your overall satisfaction levels.
By following these best practices for separate inventories, you can improve the efficiency and effectiveness of your retail operations.
10. Use data from sales channels for better predictions
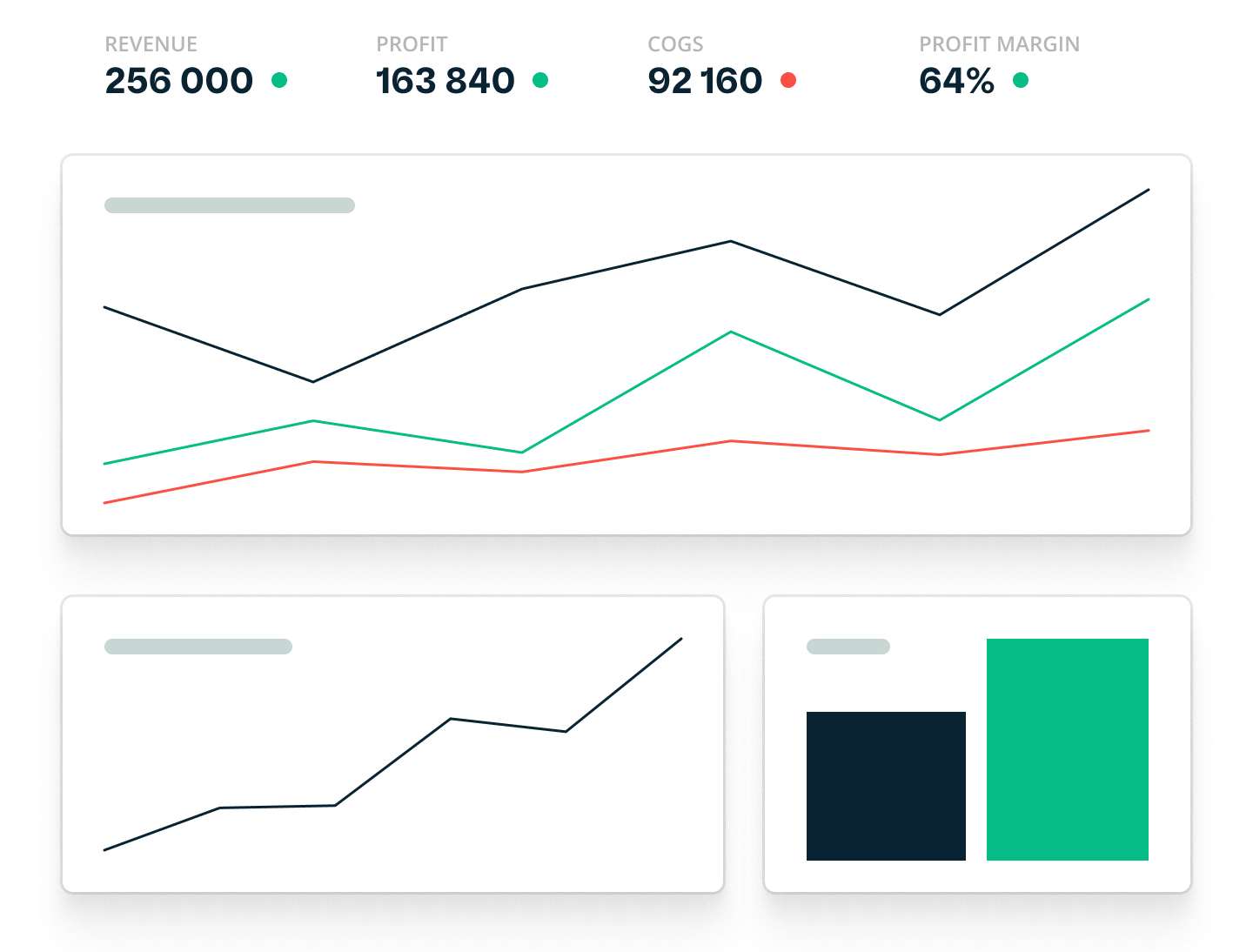
Whenever possible, use data from multiple sales channels, like:
- Shopify POS system
- Receipts from customers who buy online and pick up in-store
- Data collected at a brick-and-mortar location
Gathering this data will help improve the accuracy of your forecasts for each product you sell.
The use of sales channel data is an important factor in retail inventory management, as it can provide valuable insights into consumer trends and preferences. This data can be used to create more accurate predictions about future demand for particular products, which can then inform decisions about how much inventory should be kept on hand at any given time. Having this information can help retailers avoid stockouts and overages, negatively impacting the bottom line.
Sales data from retail channels can provide a wealth of information that can be used to improve predictions about future demand for products.
This data can help retailers better understand consumer trends and preferences, which can then be used to inform decisions about inventory levels. Having accurate information about future demand can help retailers avoid stockouts and overages, which can hurt the bottom line.
By using data from sales channels, retail inventory management can be more effective and efficient, leading to better outcomes for businesses and consumers alike.
11. Embrace technology
Take advantage of technology to make the ordering process as efficient as possible.
Use mobile apps that enable staff to place orders right on their phones, for example, or invest in an inventory management system that automatically flows information about sales trends and customer demand into your purchasing decisions.
Technology is always evolving, and retailers need to be proactive in adopting new technologies to stay ahead of the competition.
Not only does this help them keep up with the latest trends, but it also allows them to streamline their operations and improve their bottom line. One area where this is especially important is inventory management. There are several benefits to embracing technology in inventory management, including:
- Greater efficiency and accuracy
- Improved inventory forecasting
- Faster response times and improved customer service
- Greater visibility and control
- Reduced shrinkage
12. JIT inventory management
Consider using ‘just-in-time’ sourcing strategies to reduce the excess stock you end up with — especially if most of your products are perishable or quickly go out of style, like products made in an electronics manufacturing process.
This means buying goods from suppliers just before you need them — instead of stocking up well in advance — then shipping them directly to stores when necessary.
As previously stated, just-in-time (JIT) inventory management is a system where inventory is delivered as needed, and production is timed to meet customer demand. This system can be used in any business, but it is especially beneficial for companies that have high inventory turnover rates, such as retail stores.
There are several benefits of using JIT inventory management in retail inventory management.
Perhaps the most important benefit is that it can help to reduce inventory carrying costs. Carrying costs are associated with storing and managing inventory, and they can add up quickly. By reducing the amount of inventory that a company has on hand, JIT inventory management can help to reduce these carrying costs.
13. Partnerships
Partner with other companies that specialize in handling fulfillment and reverse logistics, so you can outsource tasks like reordering stock and processing returns as easily as possible.
Partnerships help to ensure that merchandise is properly distributed throughout the store. This helps keep shelves stocked and organized and prevents customer frustration due to empty shelves or out-of-stock items.
In addition, partnerships can help to improve communication between retailers and suppliers. This communication can help to ensure that retailers can order the correct amount of merchandise and that suppliers can provide retailers with accurate information about their products.
Katana + integrations = success
Looking for software to partner up with? Check out our integrations page and find the most suitable tools to help take care of all aspects of your business.
14. Staff training
Train staff to go through your inventory periodically — perhaps once per week or month — to identify slow-moving products that are just taking up space on the store shelves.
Then either discontinue selling them or offer special deals to make them more appealing to customers.
15. Perform regular stock takes
Conduct regular inventory counts to capture discrepancies between what your POS systems are reporting versus what’s actually in stock.
This will ensure that inventory level adjustments are as accurate as possible, minimizing losses from unused stock and maximizing sales for each product you sell.
Stocktaking is an important part of inventory management in retail businesses. Stocktaking allows retailers to track their inventory levels and ensure adequate stock on hand. In addition, regular stock takes help retailers to identify any discrepancies or theft that may be occurring within their stores, enabling them to take action to prevent further losses.
Furthermore, stocktaking allows retailers to plan their restocking and ordering activities more effectively, helping them to reduce inventory costs and improve cash flow.
Overall, regular stock takes plays a vital role in the success of retail businesses by providing them with valuable insights into their inventory levels and enabling them to make smarter decisions regarding their inventory management practices.
Looking for software to optimize your retail inventory management?
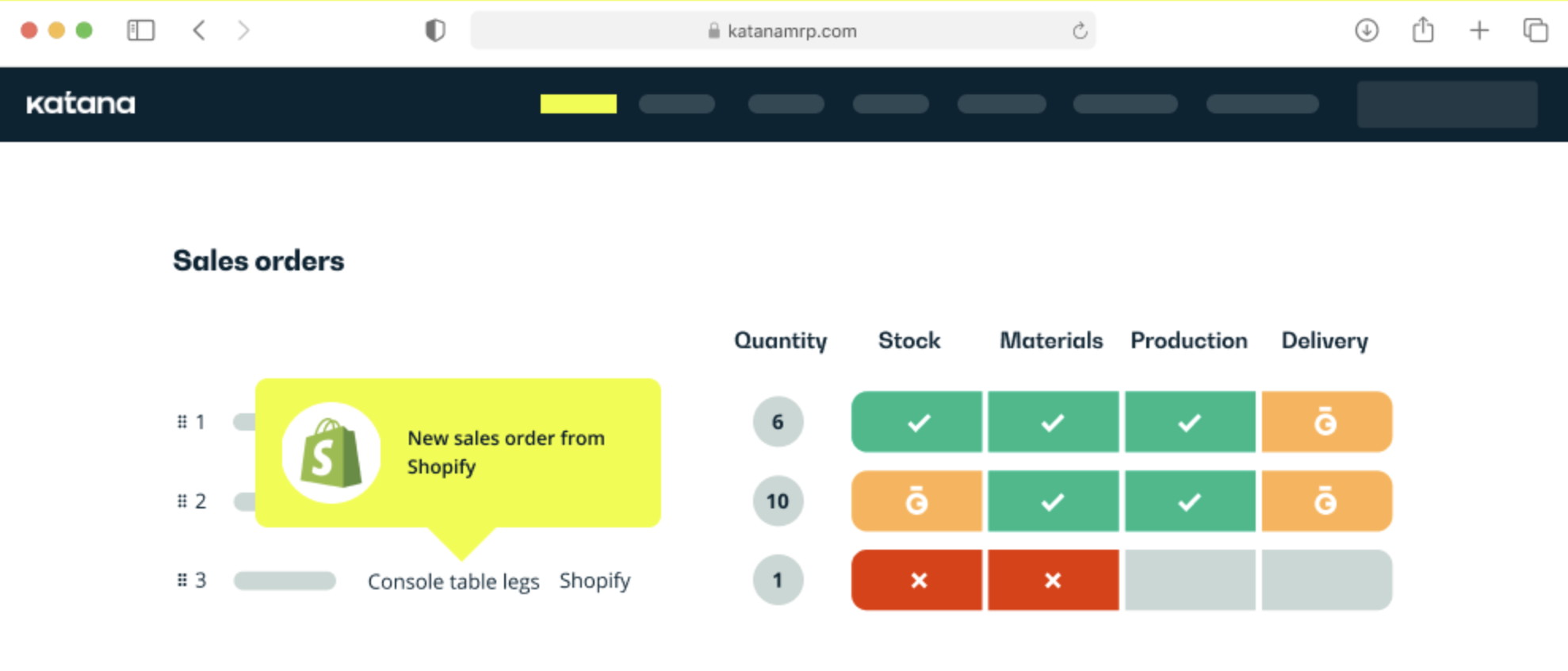
When it comes to inventory management for retailers, there are a few key considerations:
- You need to be able to track stock levels across multiple stores and warehouses
- You need to be able to manage sales orders and purchases from a single platform
- You need a solution that can help you solve stock issues quickly and efficiently
Katana’s retail inventory management software helps with these considerations. With Katana, you can view your:
- Stock levels
- Sales and manufacturing orders
- Purchasing data
You can also use Katana to create and manage multiple warehouses and store locations. Plus, Katana’s built-in real-time stock management features can help you solve any stock issues that may arise on the fly. With Katana’s intuitive yet easy-to-use user interface, it’s a breeze to manage your inventory and keep track of sales orders and purchasing data.
So what are you waiting for? Sign up for a Katana demo, and see how it can help you optimize your inventory management processes.
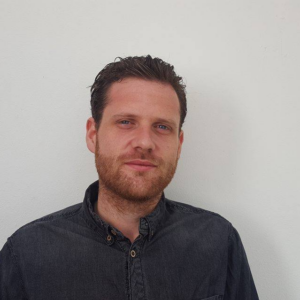
James Humphreys
Table of contents
Get inventory trends, news, and tips every month
Get visibility over your sales and stock
Wave goodbye to uncertainty with Katana Cloud Inventory — AI-powered for total inventory control