Inventory costing: How to choose the right method
Inventory costing may sound like a dry and serious topic, so we’ve decided to make it juicy and fun with a cup of lemonade, using that as an example to help explain the concept of inventory costing.
Imagine being a kid and running a lemonade stand. You’ve got a pitcher of lemonade, a stack of cups, and a big bag of lemons. You know that the lemons and cups cost money, and you want to ensure you’re charging enough for each cup of lemonade to cover the costs while also making a profit.
But how do you figure out how much each cup costs to make? That’s where inventory costing comes in.
What is inventory costing?
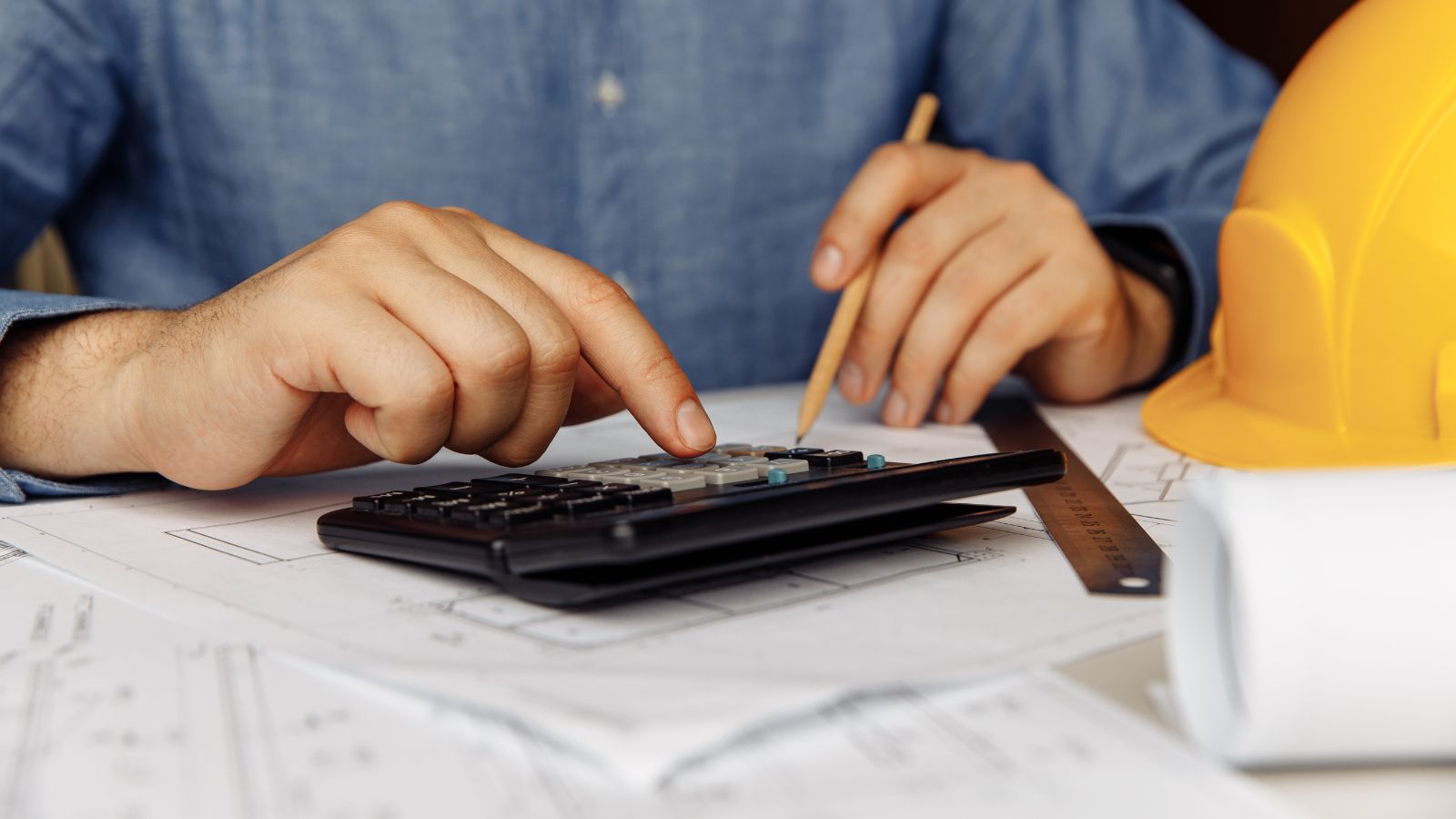
Inventory costing is an accounting process that helps businesses determine the value of their inventory.
It involves calculating the cost of each item in a company’s stock, including raw materials, labor, and other expenses related to inventory management, including production, purchasing, and carrying costs. Inventory costs can also include shipping and handling fees, storage costs such as rent or utilities for warehouse space, insurance, taxes, and any other expenses incurred to get the inventory ready for sale.
This information is then used to determine the total value of a company’s inventory, which is essential for accurate financial reporting, tax purposes, and decision-making. Inventory costing is a common way to calculate the overall success of a supply chain, determining whether the current processes are working as smoothly and efficiently as expected.
What’s the difference between cost of goods sold vs. inventory costs?
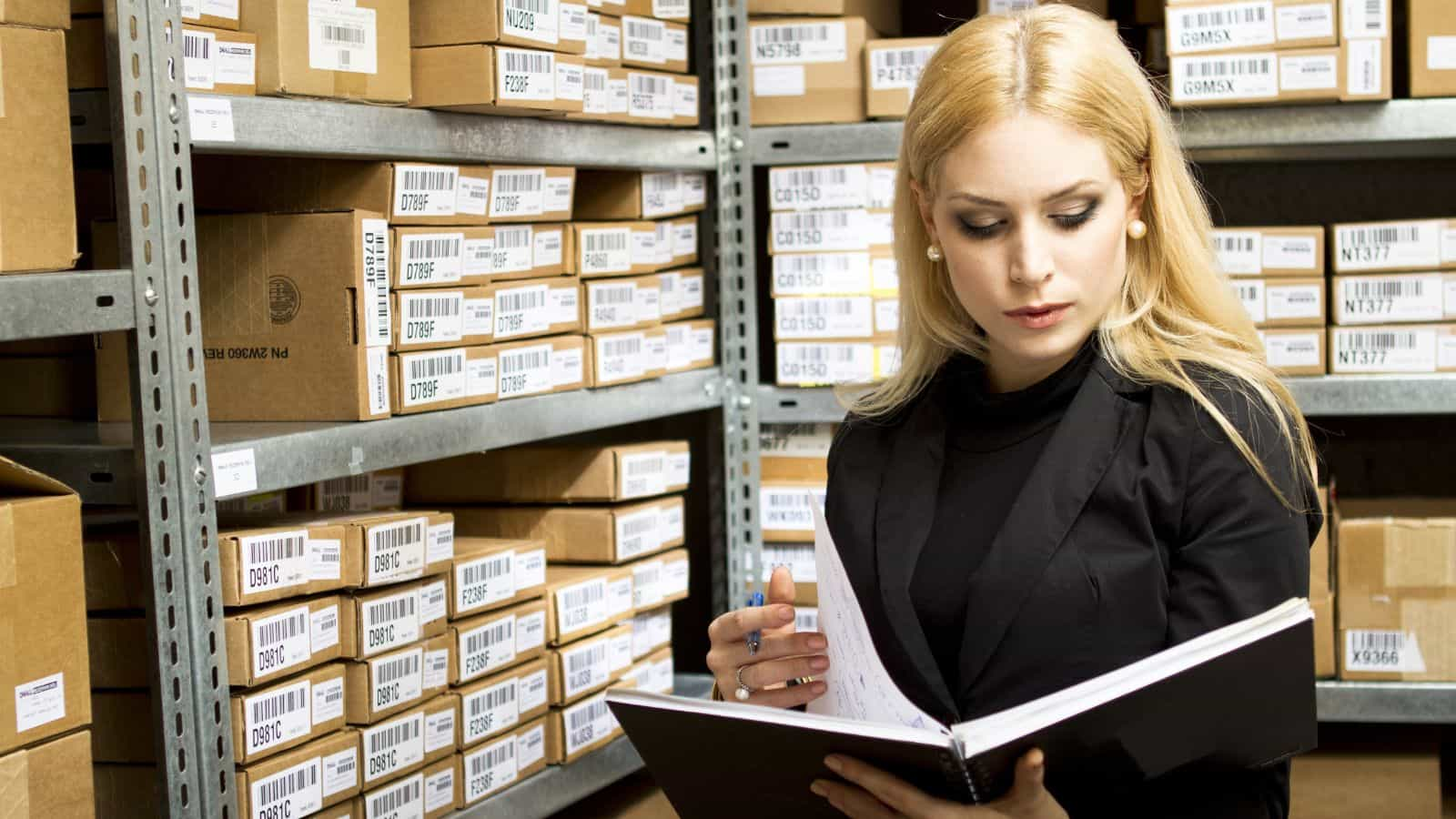
Cost of goods sold and inventory costs are two important accounting terms that relate to the expenses involved in producing and selling goods. Here’s a brief explanation of the difference between these two costs.
Cost of goods sold (COGS)
COGS is an important metric for businesses, as it helps them determine their gross profit margin.
COGS refers to the direct costs associated with producing or purchasing goods that a company sells during a specific time. These include the cost of materials, labor, and other related manufacturing costs.
COGS is calculated using a simple formula, adding the cost of the inventory you had at the beginning of the period to the total price of the merchandise you purchased during this time, then subtracting the cost of products you have left at the end of the period.
COGS = start inventory + purchases during the period – ending inventory
Example of COGS calculation
Suppose you own a store that sells T-shirts and need to calculate a month’s COGS.
At the beginning of the month, you had 100 shirts in your inventory that you bought for $10 each, making a total of $1000 start inventory. During the month, you purchased 200 more for $12 a piece, bringing your purchases to $2,400. At the end of the month, you have 50 left in your inventory, which means $600 worth of T-shirts.
Using the COGS formula, you can calculate the cost of the T-shirts you sold during the month as follows:
COGS = $1,000 (beginning inventory) + $2,400 (purchases during the month) – $600 (ending inventory) = $2,800
This means that the cost of the T-shirts you sold during the month was $2,800.
Inventory costs
Inventory costs are the expenses associated with holding and managing a company’s inventory.
These costs can include all expenses for acquiring, storing, and maintaining inventory and any losses due to spoilage or theft. Inventory costs are typically calculated per unit and are included in a company’s financial statements as an asset.
These costs are relevant regardless of whether the inventory is sold or not, whereas COGS can only be calculated after sales have happened and it is reported under expenses.
What are the most common inventory costing methods?
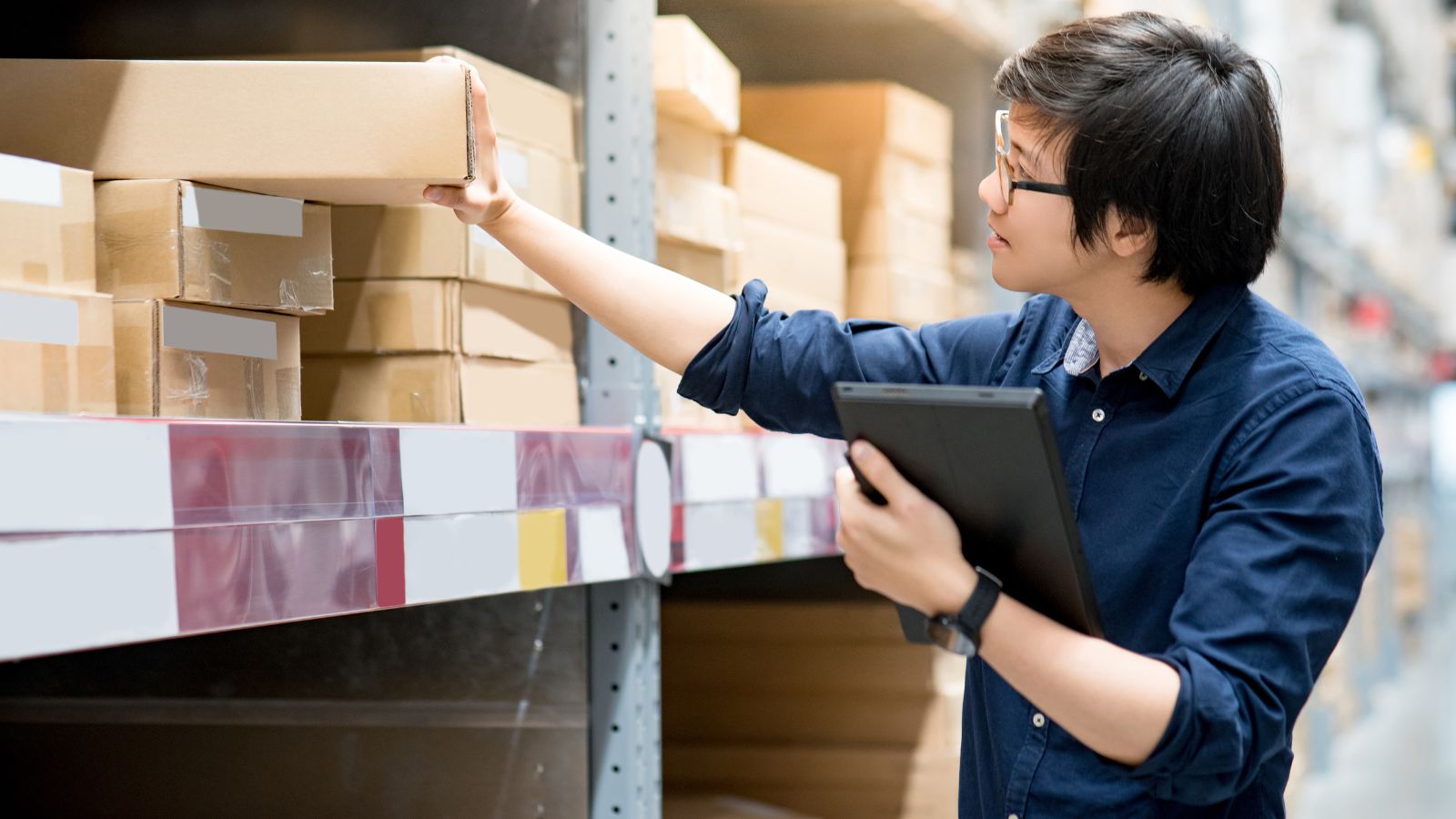
There are several methods of inventory costing, each with advantages and disadvantages. Choosing an inventory cost approach will have a significant impact on the company’s finances. Here are the four most common inventory costing methods, also approved by Generally Accepted Accounting Principles (GAAP).
1. First-in, first-out (FIFO)
FIFO is an inventory costing method that assumes the first items purchased are also the first items sold.
Under this method, the COGS is based on the cost of the oldest items in inventory, while the cost of the newest items is used to calculate the ending inventory. This method can result in a more accurate reflection of the current inventory cost, as the price of the oldest items may be lower than that of newer items.
FIFO is commonly used by businesses with perishable or time-sensitive products, such as food and beverage, pharmaceuticals, or electronics.
For example, in the food and beverage industry, businesses may use FIFO to ensure that older items with a closer expiry date are sold first, reducing the risk of waste and spoilage. Similarly, in the pharmaceutical industry, where medications may have expiry dates, FIFO can help ensure that older stock is sold first to avoid waste and maintain the product’s effectiveness.
FIFO can also be useful for businesses that experience regular price increases, as it allows them to sell the older lower-cost items first, resulting in lower COGS and higher gross profit.
2. Last-in, first-out (LIFO)
In LIFO, the main principle is that the most recently acquired items are sold first.
The COGS value is based on the cost of the newest items in inventory, while the cost of the oldest goods is used to calculate the ending inventory. This method allows businesses to assign the higher-cost items to be sold first, resulting in a higher COGS but lower taxable income.
LIFO is often used by businesses in industries such as oil and gas, where prices are highly volatile and change frequently, mostly increasing.
The method can also benefit businesses with goods that follow consumer trends. This impacts industries such as electronics or fashion, where the most recently acquired items are likely to be the most relevant and valuable.
However, LIFO can also present challenges, particularly during times of inflation.
Because LIFO assumes that the most recently acquired items are sold first, it can result in a mismatch between COGS and purchasing replacement inventory. This can lead to lower profits and higher taxes, as COGS is based on older and cheaper items, while replacement inventory costs are based on newer, higher-cost goods.
Note: LIFO is actually banned by the International Financial Reporting Standards (IFRS), and many countries, including Canada, India, Japan, Russia, and members of the European Union, don’t use this method. However, as it is approved by GAAP, the United States haven’t banned LIFO, and it is a legal method of inventory cost accounting.
3. Specific identification method
The specific identification method tracks the actual cost of each individual item in inventory.
This method is often used for products that are unique, high-priced, or have a low turnover rate. For example, a luxury accessories store has a diamond necklace in their jewelry inventory that they purchased for $10,000. If the store sells the necklace for $15,000, COGS would be recorded as $10,000, resulting in a gross profit of $5,000.
This method can be particularly useful for businesses that sell customized or unique products, as it allows them to accurately track COGS for each item separately.
However, the specific identification method can be more time-consuming and complex than other inventory costing methods because it requires tracking the cost of each individual item in inventory. This can be difficult for businesses with a large number of items or fast-selling products.
4. Weighted average cost
Weighted average cost takes the average price of all the items in inventory to determine COGS. This method assigns an average cost per unit to all goods in stock, regardless of the purchase date.
Example of weighted average cost calculation
Let’s say a company has 100 units of a product in inventory. 50 units were purchased for $5 each, and the other 50 for $10 each. The weighted average cost per unit would be calculated as follows:
(50 x $5) + (50 x $10) = $750
$750 / 100 units = $7.50 per unit
This means that COGS for 20 units sold would be:
20 units x $7.50 per unit = $150
This method is often used by companies with large amounts of inventory that have a similar cost. For example, grocery stores may use the weighted average cost method to calculate COGS for items like milk or eggs, which have a similar price per unit.
In addition, this method can be useful for businesses that experience frequent price fluctuations. As an example, a company that sells electronics may use weighted average cost to avoid fluctuations in COGS due to changes in the price of components and raw materials.
Weighted average inventory costing or average cost inventory method?
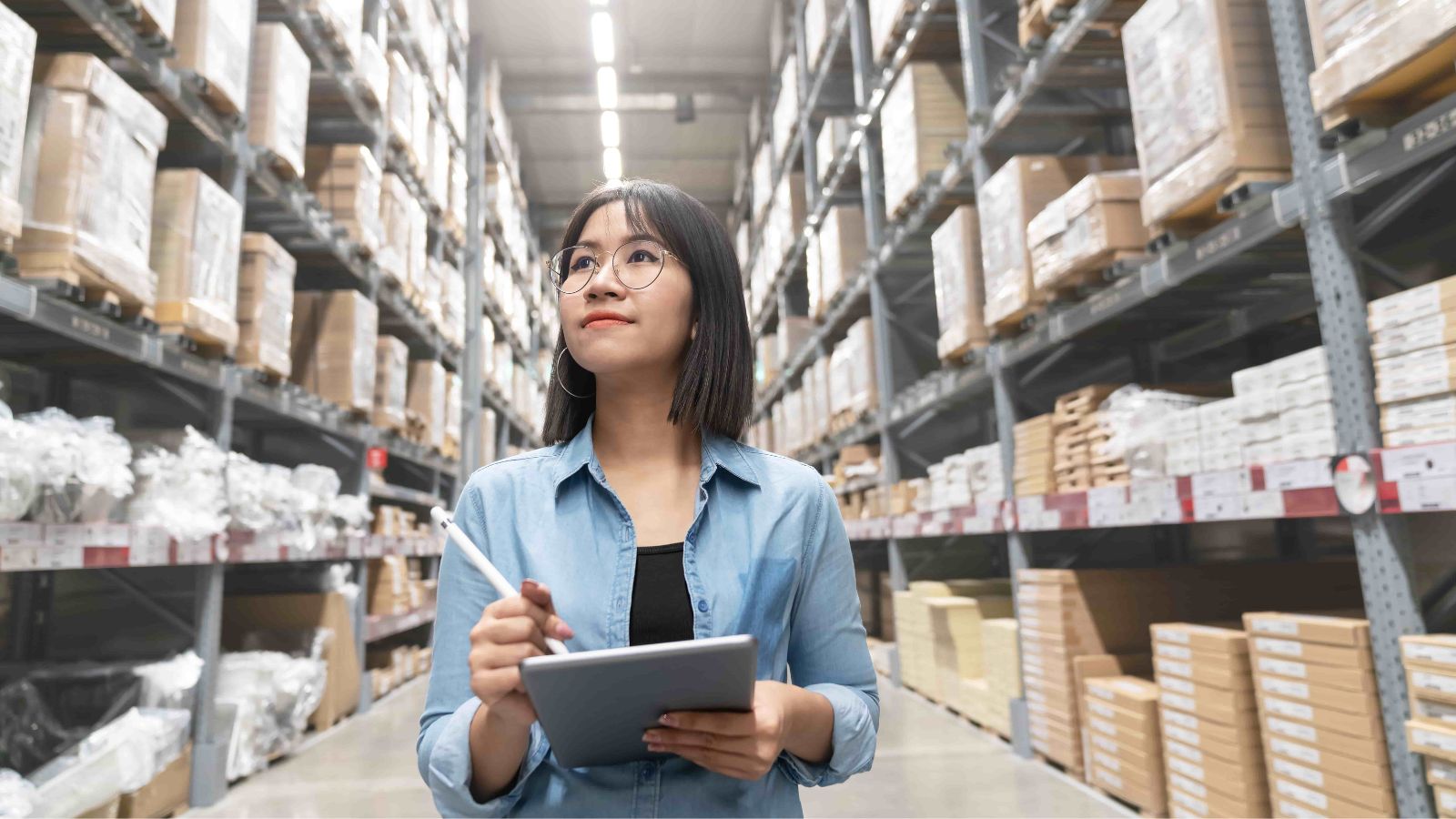
You might have seen the phrase average cost inventory method thrown around here and there.
Sounding an awful lot like weighted average inventory costing, it has gotten many people confused about what is the difference between the two. While the terms are often used interchangeably, there is a key difference in how these methods approach inventory costing.
The average cost method is quite self-explanatory, meaning that it calculates the average cost of all items in inventory, regardless of the quantity. This method is simpler and faster than the weighted average cost method but doesn’t always provide as much accuracy in terms of COGS and ending inventory.
On the other hand, the weighted average cost method takes into account the quantity of each item, thereby providing a more accurate reflection of COGS and ending inventory.
Therefore, when choosing between the average cost method and the weighted average cost method, it’s important to consider the size and complexity of your inventory.
The weighted average cost method may be more beneficial if you have a large inventory with many different items and quantities. However, if your stock volumes are smaller, the average cost method may be sufficient and easier to manage.
How to choose an inventory cost accounting method?
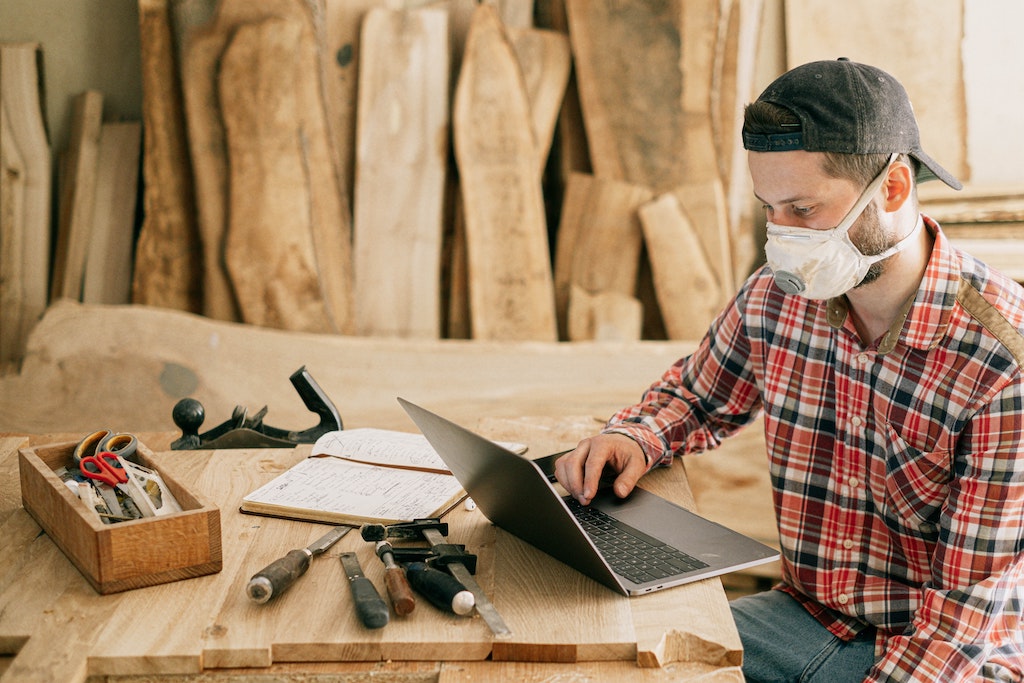
Choosing an inventory cost accounting method is an important decision that will impact a company in the long run. Here are some key points to consider when selecting an inventory cost accounting method.
Nature of the business
Consider the nature of your business and the type of inventory you carry.
If your inventory items are perishable or have a limited shelf life, the FIFO method may be the best option. If your goods are non-perishable or have a long shelf life, the LIFO method may be more appropriate. If you’re a small business with many customized and unique items, you might even look into the specific identification method.
Sales and purchasing patterns
Consider the patterns of your sales and purchases.
If your inventory levels fluctuate significantly and you make frequent purchases, the weighted average cost method may be a good choice. If you rarely reorder your goods and experience price increases over time, the LIFO method may be better suited to your needs.
Tax implications
Consider the tax implications of each method.
For example, LIFO may result in lower taxable income during periods of inflation, while FIFO may result in lower taxable income in deflation. It is highly recommended to consult with a tax professional to determine which method is most suitable for your business.
Accounting software and record-keeping
Consider your accounting software and record-keeping practices.
Some accounting methods may be complex and require more detailed records, while others are simpler and easier to manage. Ensure your accounting software can handle your chosen method and that you have the resources to keep tabs accurately.
Industry standards
Consider industry standards and regulatory requirements.
Some industries may have specific inventory cost accounting methods that are commonly used or required by regulators. It is essential to research these standards and requirements before selecting a method.
Katana Cloud Inventory Platform for managing inventory cost accounting
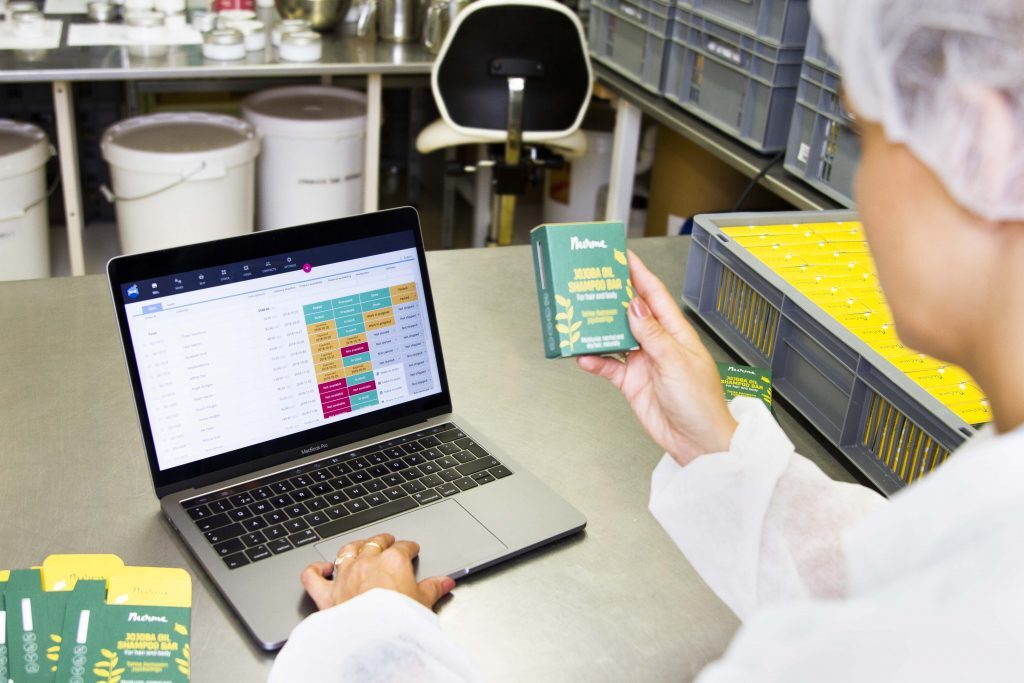
Katana is a cloud-based manufacturing platform used by thousands of manufacturers for managing their production and all other business-related operations.
Real-time inventory tracking
Katana provides live updates on your stock levels, so you always know how much inventory you have on hand — including everything from raw materials to finished goods. Having a real-time overview of your stock helps you make informed decisions about when to reorder materials or products and can help prevent stockouts or overstocking. You can even set reorder points to avoid the panic of running low on supplies.
COGS tracking
Katana allows you to track your COGS per product to see how much it costs to produce each item. This helps you understand your profitability and identify areas where you can cut costs or improve efficiency. It can also help you determine if the selected inventory cost accounting method works for you or if you need to consider switching to another approach.
Financial insights
Katana provides a range of reports, including balance sheets, income statements, and cash flow statements. A thorough inventory analysis helps you track your business finances and identify areas to improve profitability.
Integrations
Katana has partnered with many platforms to create an all-in-one solution to fit any manufacturing business. Choose from our list of integrations for e-commerce, accounting, shipping, and automation, or build your own workspace with Katana’s open API.
And that is all about inventory costing for today. Now that you’ve learned all there is to know about managing your lemons and cups, go open the best lemonade stand on the block. To see how Katana can help you to succeed, reach out to our sales team and request a demo.
Table of contents
Accounting Guide
More on inventory costing
Get visibility over your sales and stock
Wave goodbye to uncertainty by using Katana Cloud Inventory for total inventory control
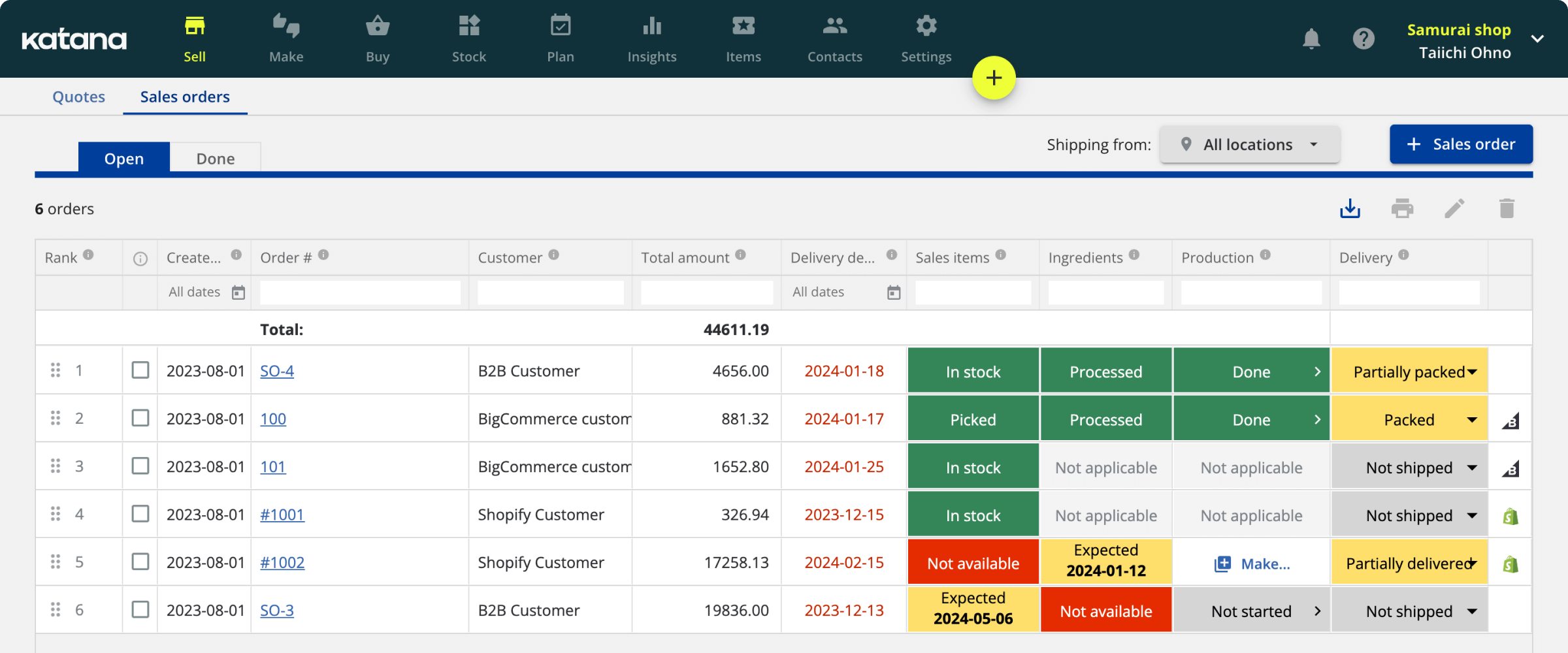