Common types of welding for manufacturers
Welding is the process of joining two pieces of metal together. But there are many types of welding to achieve this. In this article, you can learn about all the different types and the benefits of using them.
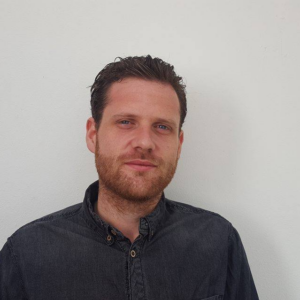
James Humphreys
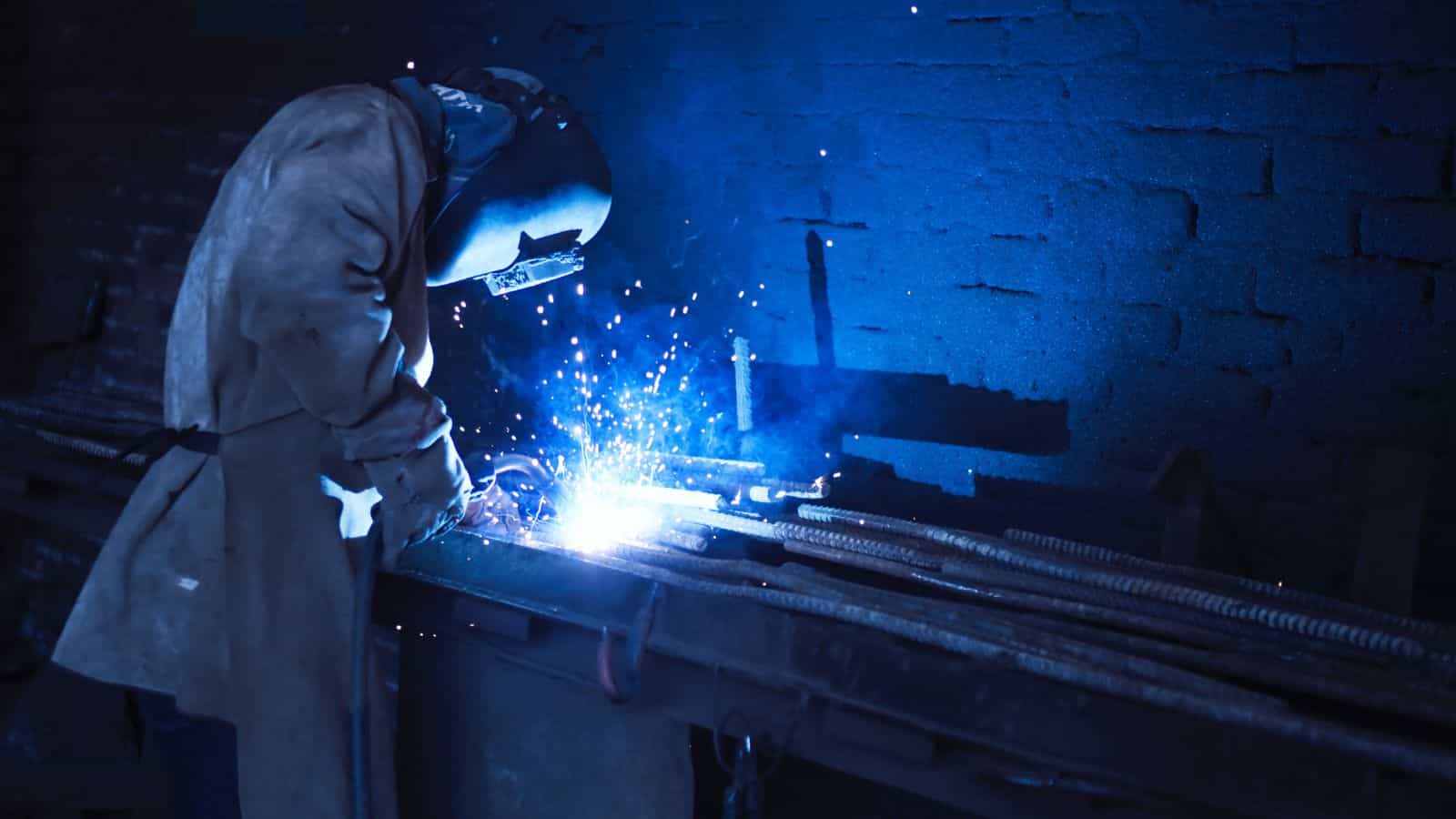
Welding is the process of joining two metals.
It is an important step in manufacturing our phones, laptops, and vehicles. It is also a process that requires varying levels of skill and precision depending on the type of welding and type of welder that is required.
There are many different types of welding, each with its advantages and disadvantages. We have compiled a comprehensive list for you to review before choosing which method is best for your company’s welding project.
Without further ado, here is a list of welding types explained.
Download the manufacturing ebook for small manufacturers
Learn how to organize and scale your manufacturing.
What are the different types of welding?
We can categorize all types of welding as either fusion or solid-state welding.
Fusion welding is the most common type of welding that joins two metals by melting them together. It includes arc welding, resistance welding, oxyfuel welding, and more.
Solid-state welding joins two metals without melting or fillers. It includes diffusion welding, friction welding, ultrasonic welding, and explosive welding.
The type of welding that you require will depend on your project’s needs.
Try metal fabrication software for free
Know at a moment’s notice if you have all the necessary resources or if raw materials are running low the second a manufacturing order is created.
Fusion welding
Here are four categories of fusion welding processes.
1. Arc welding
Arc welding is the most common type of welding process. It is a fusion welding process and is used for welding various types of metals, including aluminum, stainless steel, and carbon steel. The process involves using an electric arc to create heat that melts two pieces of metal together.
Five common types of welds using arcs include:
- Shielded Metal Arc Welding (SMAW) — More portable than other kinds of welding. This includes a consumable electrode. However, it is less efficient and requires more welders to be employed
- Gas Metal Arc Welding (GMAW) — Also involving a consumable electrode, GMAW is a simple form of welding that can easily be performed by new types of welders. No slag build-up and higher deposition rate than SMAW — Metal Inert Gas (MIG) or CO2 welding
- Gas Tungsten Arc Welding (GTAW) — This process is also commonly known as Tungsten (Wolfram) Inert Gas (TIG) Welding. It can be completed with or without filler metal. Although the process is slower and more expensive than others, it yields high-quality welds
- Flux-Cored Arc Welding (FCAW) — Similar to SMAW, FCAW uses heat generated by an electric arc to fuse base metal in the weld joint. However, FCAW is a cheaper alternative because it does not require a separate shielding gas tank. This process is perfect for welding metals that are rusted or contaminated
- Plasma Arc Welding (PAW) — In PAW, the arc has a very deep penetrating ability into the metals welded, and the fusion takes place in a very narrow part of the joint. This process is well suited for welding metals that are difficult to weld using other methods
2. Resistance welding
Resistance welding requires heat and pressure to accomplish coalescence. Five of the most commonly known types of welds in this category include:
- Spot welding — Spot welding is a type of resistance welding that fuses overlapping metal sheets at specific points. Various types of welders commonly use spot welding for high-volume projects like manufacturing lines for constructing steel cars
- Seam welding — Seam welding is a type of resistance welding in which a rotating wheel moves along the length of two abutting metal sheets, fusing them as it rotates. Many types of welders are used on projects that require long, continuous welds, such as in shipbuilding
- Butt welding — Butt welding is a type of resistance welding in which two pieces of metal are placed against each other end-to-end and then fused. Many types of welders use butt welding in pipefitting and the automotive and energy industries.
- Flash butt welding — Flash butt welding is similar to butt welding except that arc flashes are produced at the joining ends of metal to melt them before applying heavy pressure to join them. This process is commonly used to weld tubes and rods in steel industries
- Projection welding — Projection welding is similar to spot welding but without an electrode to concentrate heat. Projection welding is often used in joining thicker materials and is very efficient compared to spot welding. Multiple welds can be made at the same time when multiple projections are present
3. Oxy-fuel welding
Oxyfuel welding requires a combination of oxygen and various fuels to produce a flame to melt the base metal and filler rod. Oxygen is most commonly combined with either acetylene or other fuels, including hydrogen, coal gas, or liquified petroleum gas:
- Oxy-acetylene welding — Oxy-acetylene welding is the most widely used oxyfuel welding. It is used to join different ferrous and non-ferrous metals, generally of 3mm thickness and below. This technique is very difficult to master, so it is typically used by seasoned welders
- Oxy-hydrogen welding — Hydrogen has a lower flame temperature, so oxy-hydrogen welding welds metals with a lower melting point. This welding process is very slow, but it also is convenient, safe, and environmentally friendly compared to other types of welding
Some materials that are exclusively used in oxy-fuel welding include:
- Cylinders — Steel pressurized cylinders contain oxygen and fuel gas
- Regulators — Control the flow of gas
- Safety valves — Keep the flow of gas going in one direction. They also reduce the possibility of a flashback
- Torches — Control the flame
- Hoses — A nonporous hose moves oxygen and fuel gas to the torch
4. Other fusion welding processes
Few fusion processes do not require a current or resistance. Two such processes include:
- Electroslag welding — This type of welding is similar to electro-gas welding, but no arc is used
- Thermit welding — With origins from 1900, this is a fusion welding process that combines Al powder and iron oxide through a chemical heating process to join thick, heavy, and irregularly shaped materials. It is used in railroad repair cracks in ingot and large frames and shafts
Complete control with steel fabrication estimating software
Get a clear view of your sheet metal and steel projects within Katana — increase production and decrease admin time.
Solid-state welding
Solid-state welding processes require no external heat or filler metal, and materials stay in a solid state throughout the entire welding process. These processes also require different types of welder machines.
Here are four types of welding processes that maintain materials in a solid state.
4. Diffusion welding
Diffusion welding is a process in which the atoms of two pieces of metal combine under high pressure and temperature. This high pressure starts diffusion between the surfaces of welding plates.
This method can join similar and dissimilar metals and is commonly used in the aerospace industry. It also is less prone to plastic distortion than other welding processes. However, it is also a time-consuming process that is difficult to use for mass production.
5. Friction welding
Friction welding is a solid-state welding process that uses friction between two surfaces to be joined to generate heat. This heat melts the surfaces, which creates a weld.
There are several types of welding using friction, which include:
- Continuous induced friction welding
- Inertia friction welding
- Linear friction welding
- Linear vibration welding
- Friction surfacing
Friction welding can produce high-quality welds quickly, requiring fewer supplementary materials, less time, and less skill than other types of welding. However, the cost of setting up a friction welding system is very expensive.
6. Ultrasonic welding
Ultrasonic welding is a solid-state welding process that uses high-frequency sound waves to create heat and melt the metals being joined.
All ultrasonic welding systems will include:
- A press, usually with a pneumatic or electric drive — Assembles the parts under pressure
- A nest, anvil, or fixture — These parts are placed and allow a high-frequency vibration to be directed to the interfaces
- An ultrasonic stack — This is composed of a converter or piezoelectric transducer, an optional booster, and a horn tuned to resonate at the same ultrasonic frequency (typically 15, 20, 30, 35, or 40 kHz)
- A controller — Controls the movement of the press and flow of the ultrasonic energy
Ultrasonic welding is useful in industries that use thermoplastics and materials like polypropylene. Using this method is very quick, safe, and reliable. However, it can only be used for smaller materials (joints cannot be larger than 150mm), and the cost of setting up an ultrasonic welding system is also very expensive.
7. Explosive Welding
Explosive welding is a solid-state welding process that uses a controlled, explosive charge to create enough energy to weld two pieces of metal together.
This welding process is mainly used for cladding processes and is suitable for nearly all kinds of metals and alloys. It is very time-efficient, making it suitable for mass production. However, it is also a high-energy process that can be dangerous if not done correctly.
How to weld together your workflow
Do you have a collection of welders blinded by confusion on the shop floor? Create, assign, and monitor tasks with a clear communication channel with Katana’s Shop Floor App.
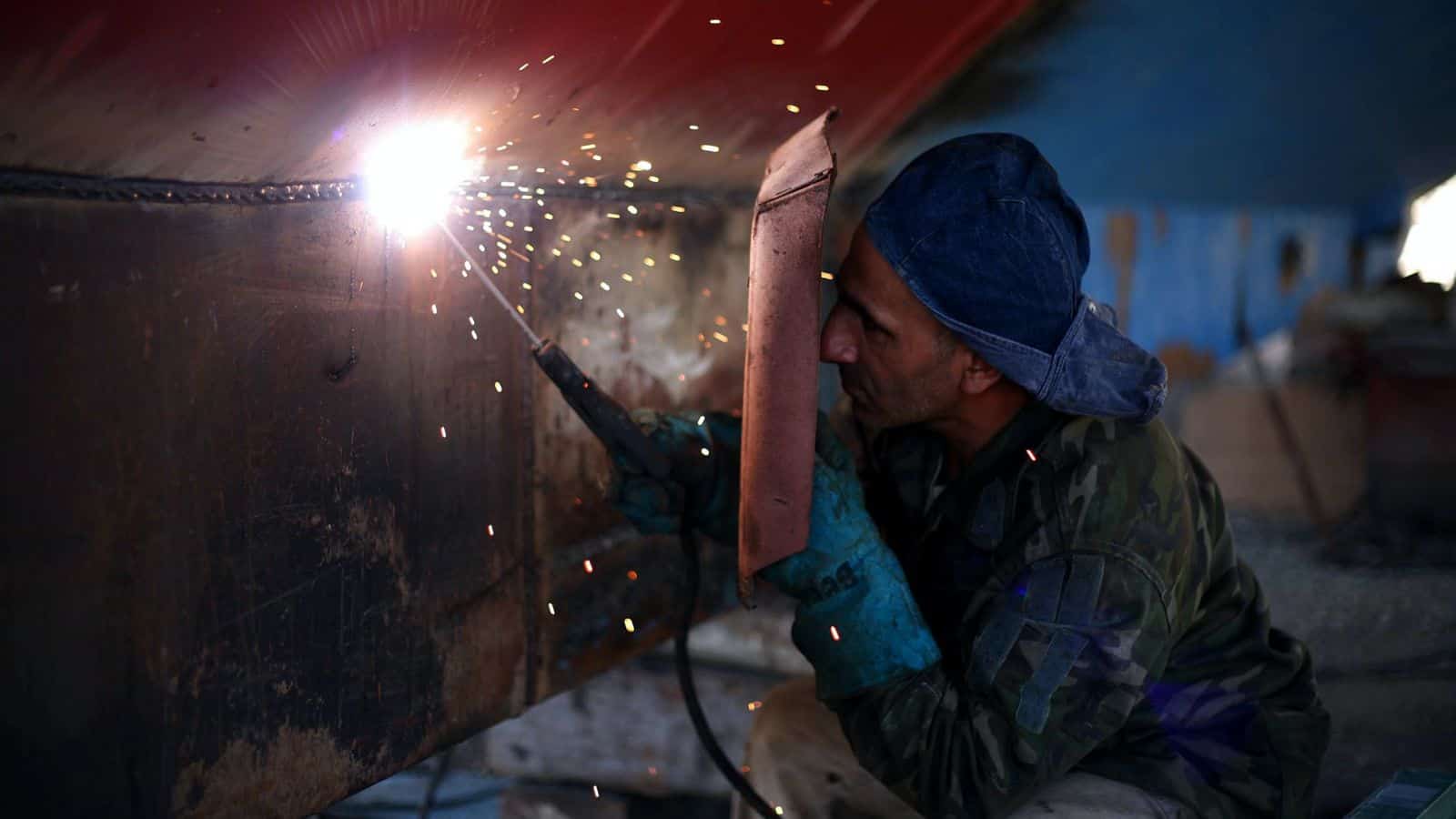
Food for thought while you look for the perfect welding technique
There is no such thing as a perfect type of welding, but each has its advantages and disadvantages. Some projects will require fusion welding, while others will be more suited for solid-state welding.
The key is to select the right method for the job at hand, considering the metals being joined, the thickness of those metals, and the environment in which the welding will take place, among other factors.
Hopefully, this post has given you a basic understanding of the types of welding that will help you in your next welding project. Good luck!
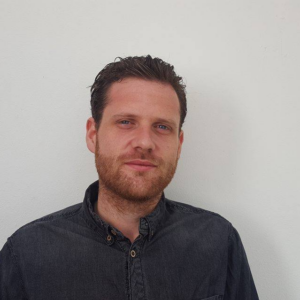
James Humphreys
Table of contents
Get inventory trends, news, and tips every month
Get visibility over your sales and stock
Wave goodbye to uncertainty with Katana Cloud Inventory — AI-powered for total inventory control