OEM vs. ODM: which is right for your business?
Manufacturing jargon can sometimes feel like reading a bowl of alphabet soup. So buckle up for a ride through the world of ODM vs. OEM to explore the exciting world of manufacturing strategies.
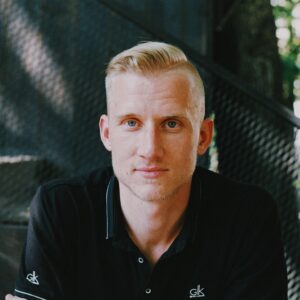
Henry Kivimaa
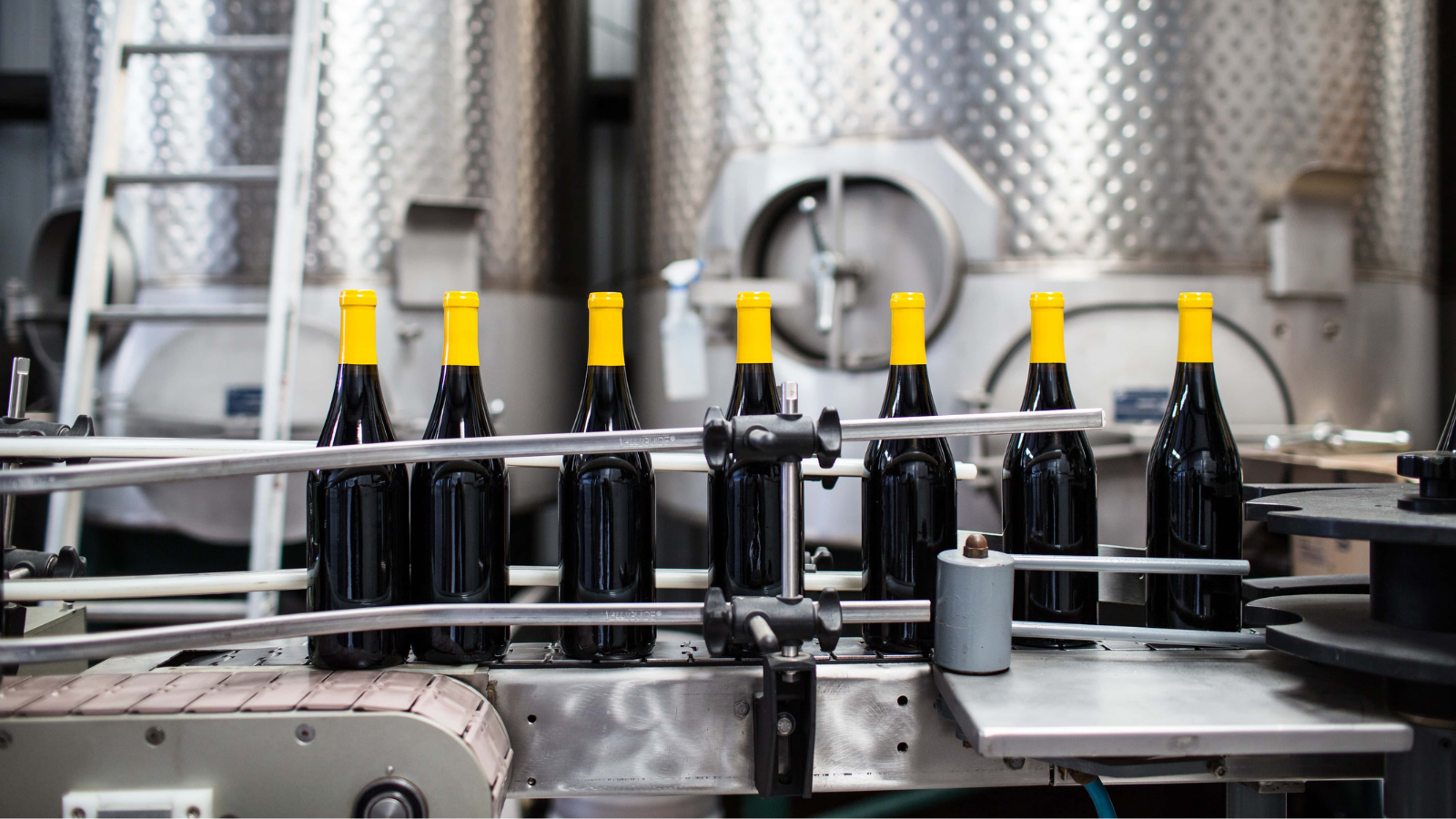
Manufacturing is just the tip of the production iceberg. Before that, a whole world of design goes into creating unique products. Depending on your business, you might be doing your own design or using preexisting designs. It’s like choosing between baking a cake from scratch or using a mix from the store. Both can be delicious, but one requires a little more creativity and effort.
There are distinct names for these different business models: OEM and ODM. They might sound like some elaborate spy code or illegal party drugs, but they do belong to the manufacturing industry:
- OEM stands for Original Equipment Manufacturer
- ODM means Original Design Manufacturer
But what endless manufacturing possibilities lie behind those words?
The difference between OEM and ODM
OEM means a company designs and develops a product but often outsources manufacturing to a third-party company. The third-party manufacturer then creates the product under the brand name of the company that designed it. In other words, the company that developed the product doesn’t actually manufacture it itself. Instead, they focus on product design, marketing, and sales.
Examples of OEM
One of the biggest OEM companies is Apple. They design their own products but outsource manufacturing to Foxconn, a Taiwanese electronics company that also creates components for HP and Dell. While Apple designs its products in-house, manufacturing is outsourced to Foxconn to save on costs and effort, with the rights to the design and finished goods still belonging to Apple.
The ODM approach involves the manufacturer not only producing the items but also designing them from scratch. In this case, the manufacturer is responsible for the entire product development process, from design to production. The company that hires the ODM manufacturer will then sell the product under its own brand name.
Examples of ODM
A big ODM industry is smart devices. Companies such as Qualcomm produce microchips for smartphones and tablets that they design and manufacture themselves. Then big electronics companies like Sony and Motorola buy their goods, possibly relabel them and use them in their own products. While Sony and Motorola now own these specific chips, the intellectual ownership of the product design is still Qualcomm’s.
To conclude, the main difference between OEM and ODM is that with OEM, the company that designed the product outsources the manufacturing, while with ODM, the manufacturer produces and designs the product.
OEM vs. ODM vs. CM
Aside from OEM and ODM, there’s another manufacturing model that deserves mentioning — contract manufacturing (CM). When comparing OEMs vs. contract manufacturing, the difference is in the offered service and the level of input. While with OEMs, the manufacturers often work with buyers in the design stage to be on the same page, a CM is precisely what the name suggests, a company hired to complete the manufacturing process.
What are OEM and ODM services?
OEM and ODM services can be offered in a variety of industries, including electronics, consumer goods, and health devices. Both services provide advantages to businesses, as they save money on production costs while offering high-quality products. Here are some examples of the services provided by each.
OEM services
OEMs typically focus on manufacturing and assembly services, with some also offering troubleshooting and product service for the manufactured components.
Services offered by OEMs include:
- Production of products according to the specifications provided by the brand company
- Manufacturing and assembly of products
- Quality control and testing of products
- Packaging and labeling of products
- Shipping and logistics services
- After-sales support and customer service
ODM services
ODMs offer a more comprehensive range of services, as they are involved in the entire product development and manufacturing process.
Services offered by ODMs are mainly similar to OEM services but also include the following:
- Design and development of products
- Prototyping and testing of products
- Customization of products based on client specifications
Which is right for my manufacturing business?
Choosing the perfect manufacturing model for your company is challenging and shouldn’t be taken lightly. You know your business and its specific needs and processes, so there is no one-size-fits-all solution. One isn’t generally better than the other, but one could offer more benefits to your business. Here are some key points you may want to consider when deciding on a manufacturing model.
Design expertise
If your business has strong design capabilities and can create unique and innovative products, then ODM may be your better option. On the other hand, if you lack design expertise and need products to be made to your specific requirements, OEM may be a better fit.
Cost considerations
ODM products are generally less expensive to produce, as the manufacturer has already invested in design and tooling. If manufacturing cost is a significant factor for your business, then ODM may be the better option.
Brand identity
If you want to build a strong manufacturing brand identity and market your products as your own, OEM may be the best solution for your business. However, ODM may be a better fit if you are willing to sell products under the manufacturer’s brand and focus on delivering quality products at a lower cost.
Industry and market requirements
Some industries and markets require specific certifications or compliance with regulations. If your products require particular certificates and standards, OEM may be the better option, as you can outsource to a manufacturer who has already taken the time to get certified.
How can Katana help manage your manufacturing?
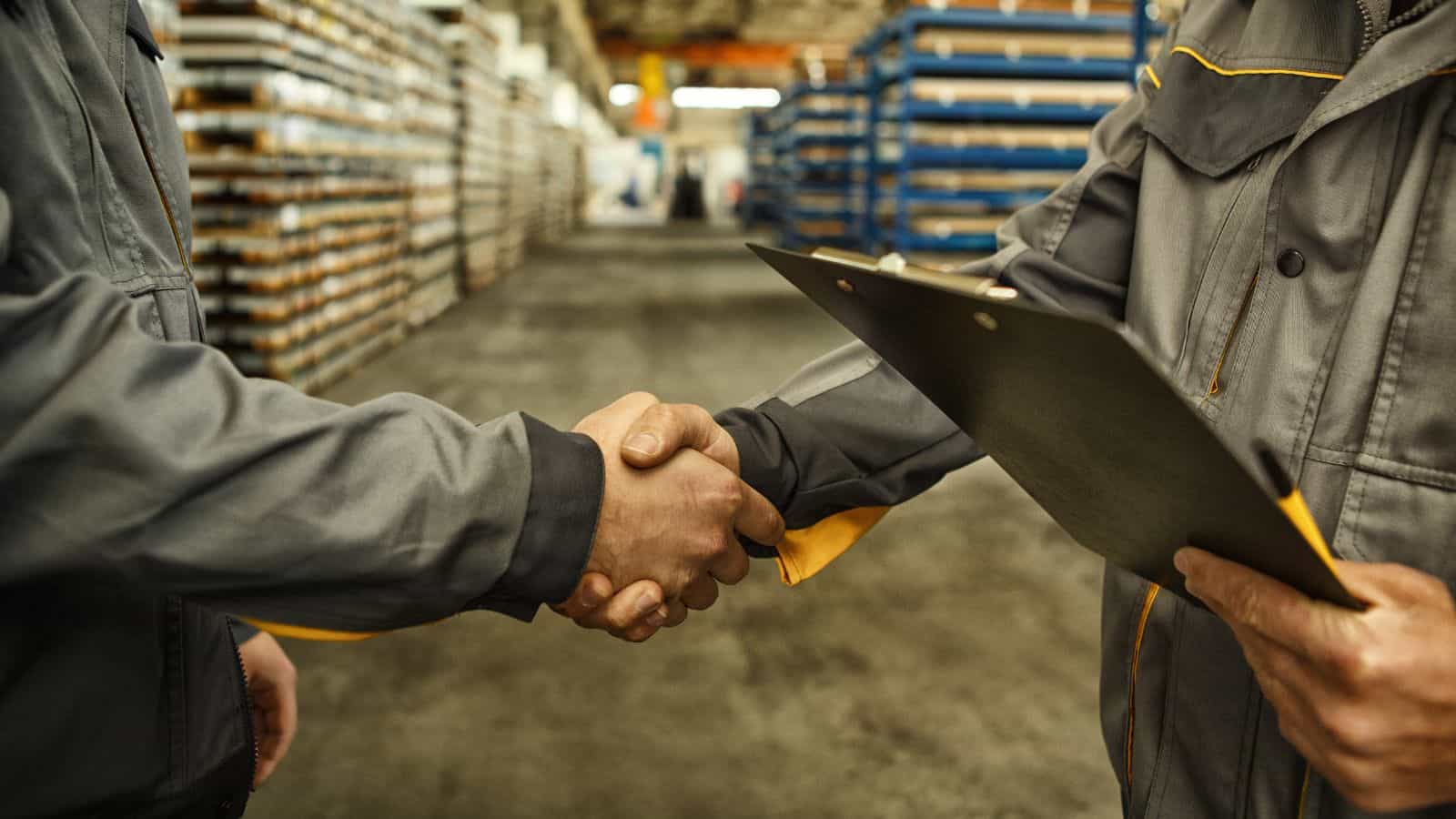
Katana is a cloud-based production planning and inventory management software for small and medium-sized manufacturers, including ODM, OEM, and CM businesses. Whether you create your own products from scratch or outsource your manufacturing, in both cases, there are many areas of the business to oversee.
Inventory management
One of the most essential features of Katana is its inventory management capabilities. It allows manufacturers to track their inventory levels in real time, including raw materials, work-in-progress, and finished goods. This can help OEMs and ODMs optimize inventory levels and reduce waste and stockouts.
Outsourced Purchase Orders (OPO)
Outsourcing refers to sending some or all of your purchase orders to be fulfilled by a contract manufacturer outside your own business. Outsourcing can be useful for companies that don’t have the capacity to produce goods in-house or need to access specialized equipment or skills. We’ve even put together a video series explaining OPOs and how they work in Katana.
Production planning and scheduling
Katana allows manufacturers to schedule production, create and manage manufacturing orders, assign tasks to employees, and track the progress of each assignment. Shop-level workers can access their tasks in the Shop Floor App, where they can view and edit them, triggering changes in inventory levels and production operations. This way, manufacturers can streamline their production processes and eliminate inefficiencies.
Bill of materials management
Using Katana, manufacturers can create and manage bills of materials for their products. This can help ODMs ensure they have the necessary raw materials and components to manufacture their products, and OEMs keep track of their supplies and parts.
Live data and insights
Katana provides users with real-time information and manufacturing analytics about their production processes. With this feature, manufacturers can track sales, monitor the progress of production orders, and identify areas where to optimize their operations to reduce manufacturing waste and increase efficiency. The data and insights feature also includes customizable dashboards and reports, which allow users to visualize their data and highlight the statistics most essential to their business.
Integration with other software
With Katana’s open API, users can integrate with other software tools, such as accounting software, e-commerce platforms, and CRM systems, to fulfill their specific business needs. There are also many existing integrations to build a custom workspace and create personalized workflows.
Maximize your business potential with Katana
Book a demo to get all your questions answered regarding Katana’s features, integrations, pricing, and more.
And there you have it.
Now that you know the difference between OEMs and ODMs, it’s time to start skyrocketing your manufacturing business with Katana and also impress your friends at your next dinner party with all this new knowledge. Just don’t blame us if they start asking you to design and manufacture their products.
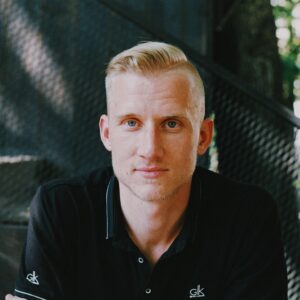
Henry Kivimaa
Table of contents
Get inventory trends, news, and tips every month
Get visibility over your sales and stock
Wave goodbye to uncertainty with Katana Cloud Inventory — AI-powered for total inventory control