Perishable inventory: The best tools for expiry date tracking
Working with perishable inventory can be tricky Here’s everything you need to know about shelf-life management, from the benefits of doing it right to the tools manufacturers need.
Team Katana
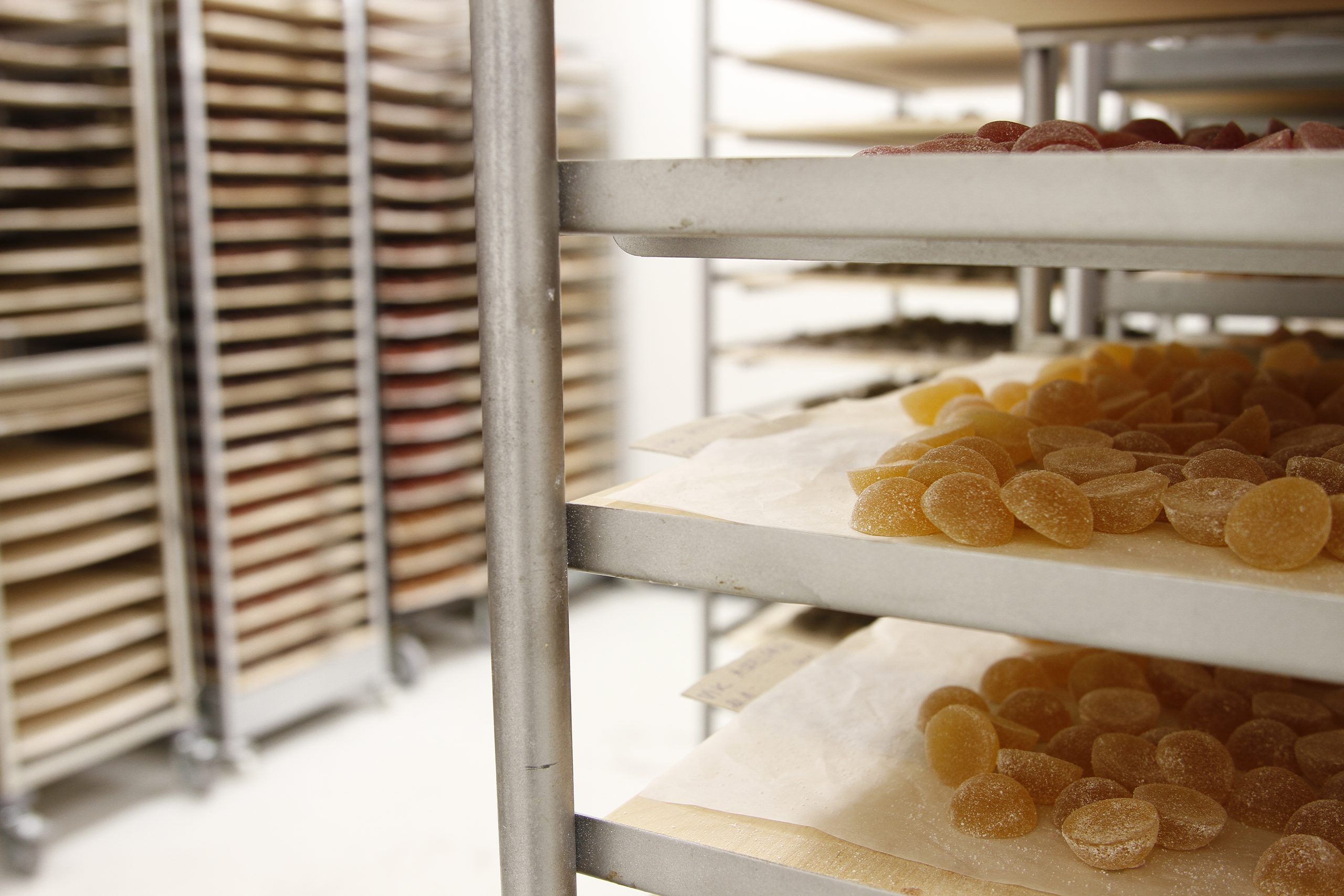
If you’re working with perishable goods, tracking your raw materials and products is essential. In this article, we’re going to look at the tools you can use, and the benefits of adopting them into your business, and how to monitor shelf-life management as a manufacturer.
Download the ultimate guide to inventory management
A comprehensive ebook with everything you need to know about inventory management.
What is perishable inventory in manufacturing?
Perishable inventory includes raw materials and finished products that lose their value over time and eventually become worthless. When you think of perishable inventory, you’re probably thinking of products from the following industries:
These industries work with products and ingredients that expire, but perishable inventory also applies to technological products. For example, rapid advancements in computer processing technology mean that the components inside your computer also become obsolete after a certain period of time.
Pro tip:
You can always adopt a manufacturing ERP system to track your perishable inventory. But before doing that, take a look at our free guide to improving your inventory management processes to make the most of the software you choose.
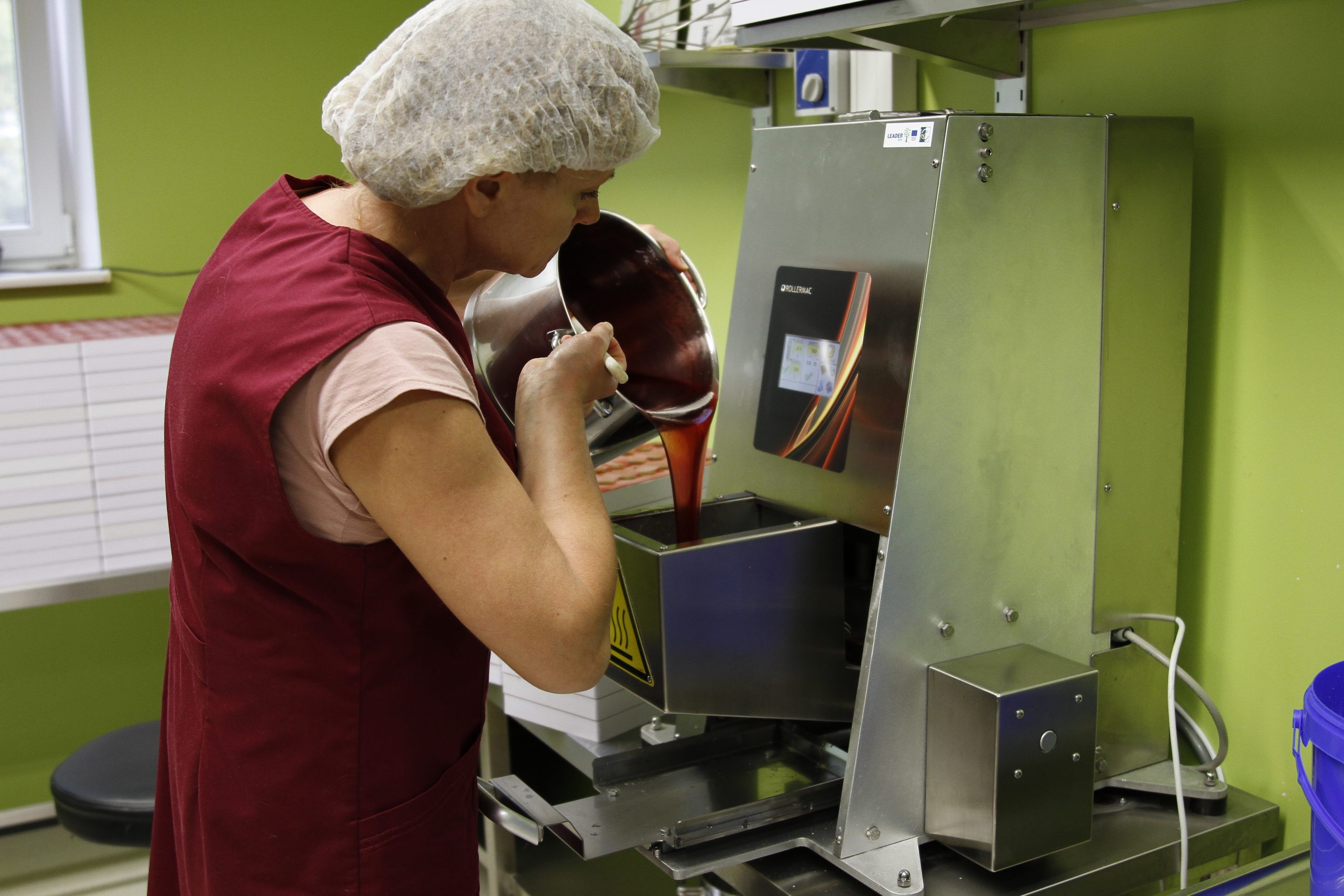
The importance of tracking your perishable inventory
The main reason for tracking your perishables, like food inventory and cosmetics inventory, is to ensure you won’t sell expired products.
Improved perishable inventory tracking allows you to manufacture and distribute your food products at the right time and in the right quantities based on your demand. When done right, the benefits of implementing the right tracking for your perishable inventory include:
- Optimal inventory levels
- Greater profits
- Better cash flow
- Happier customers
- Fewer recalls
What’s more, based on recent manufacturing trends and predictions, customers are not only becoming more conscious of where their products come from but are switching to online shopping. In fact, 70% of customers will be doing their grocery shopping online by 2024, making optimizing your shelf life management processes more important than ever.
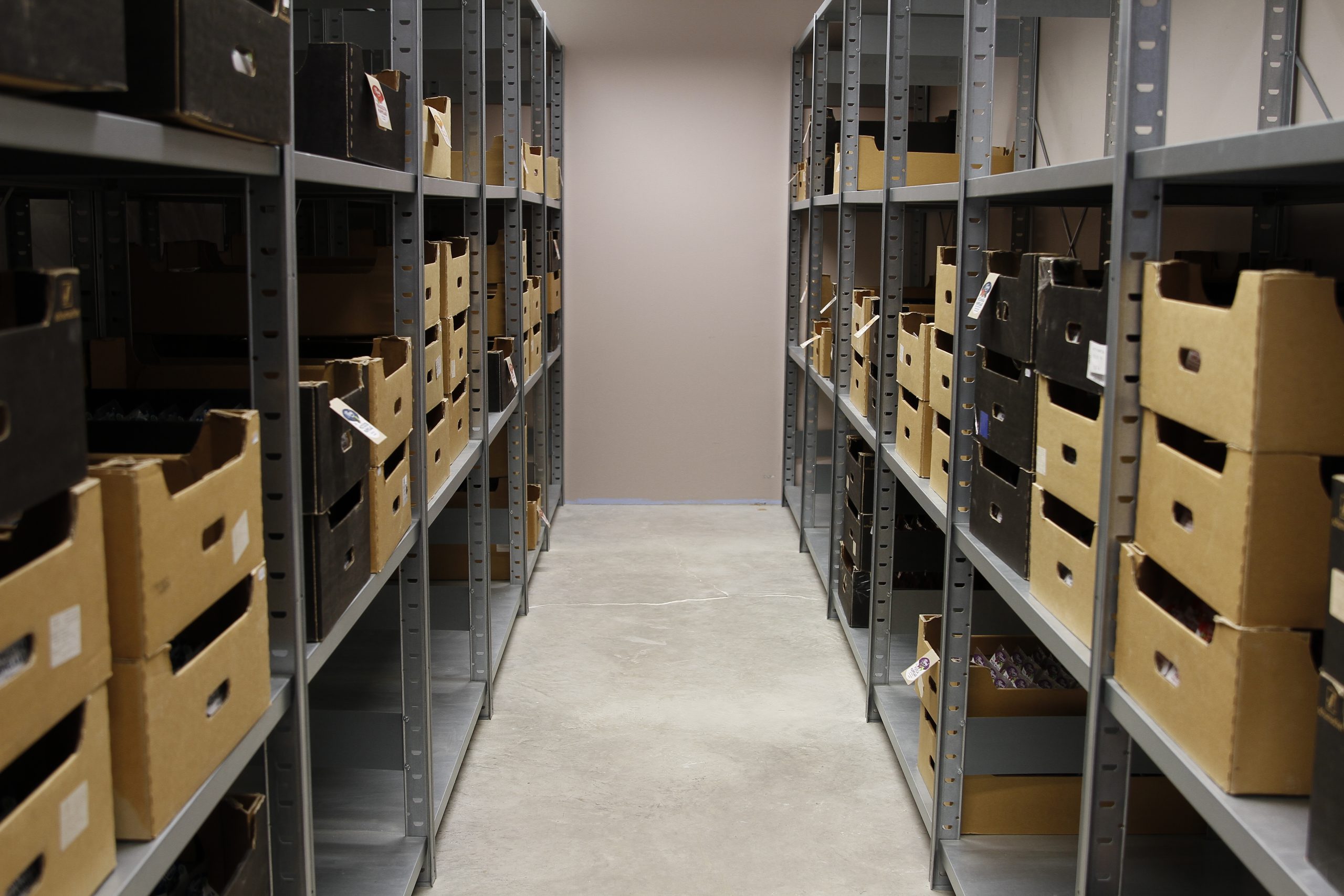
How to monitor shelf life management
In this chapter, we’re going to look into the different techniques and processes you can implement to get more control over how you monitor shelf life management.
1. First expired, first out (FEFO)
FEFO is the process of selling your perishable inventory, starting with the products that are closest to their expiry date. FEFO allows you to ensure the expiration date for a product isn’t reached before it’s delivered to the customer or spoils within your inventory.
By adopting the FEFO method, you can:
- Ensure that raw materials and products remain fresh
- Reduce the amount of inventory that expires on your shelf
- Save on labor costs by reducing the number of spot checks you need to perform
Note — there is another similar shelf life management method called first in, first out (FIFO), which allows you to ship inventory before it becomes outdated, like with computer components, as mentioned earlier.
2. Traditional spreadsheets
Regardless of which method you choose to follow, you’re going to need a system to help you track your inventory. If you’re small and willing to put in the extra manual work, inventory tracking can be done via spreadsheets.
However, this is going to require meticulous monitoring of your inventory, and you’ll need to create templates and documents to:
- Outline procedures
- Perform checks
- Record sign-offs
Since spreadsheets are inefficient for inventory management in the long term, you’ll need to balance your perishable inventory tracking efforts with techniques for tracking your inventory. This can be as simple as identifying expiry dates once you receive items and clearly labeling them with colored stickers so you can visually identify stock arrival times.
3. Manage your suppliers
Managing your suppliers is probably the simplest way to get fresher ingredients. Find suppliers who can best deliver on getting items to you sooner and alternative suppliers should anything go wrong with your supply chain.
Other tips for managing suppliers include:
- Negotiating better terms
- Being active with pre-receipt quality checks to improve the quality of your finished goods
It is always recommended to stay in contact with your suppliers to identify any issues that might come up in the future, like running out of stock, so you can make a plan B and maintain your optimal perishable inventory levels.
4. Sell short-dated products
Your priority when handling perishable inventory is to have your products out the door and with the customer before the expiration date. This allows you to save on carrying costs and still deliver a quality product to your customer. If you find yourself in a position where products are going to spoil soon, try:
- Directly communicating with customers
- Offering discounts
- Inventory kitting
Selling at a loss is always better than completely disposing of your inventory.
5. Implementing software
Finally, the best way you can improve how to monitor shelf life management is to introduce software into your business, like a batch inventory management system. Inventory management systems that can track your perishable inventory are going to be essential, especially for manufacturers who need to track a large number of items.
With software implemented for perishable inventory tracking, you’ll be able to monitor your inventory, manufacturing, and other departments from a visual dashboard, while also taking advantage of:
- Batch or lot number tracking
- Product traceability
- Product recall processes
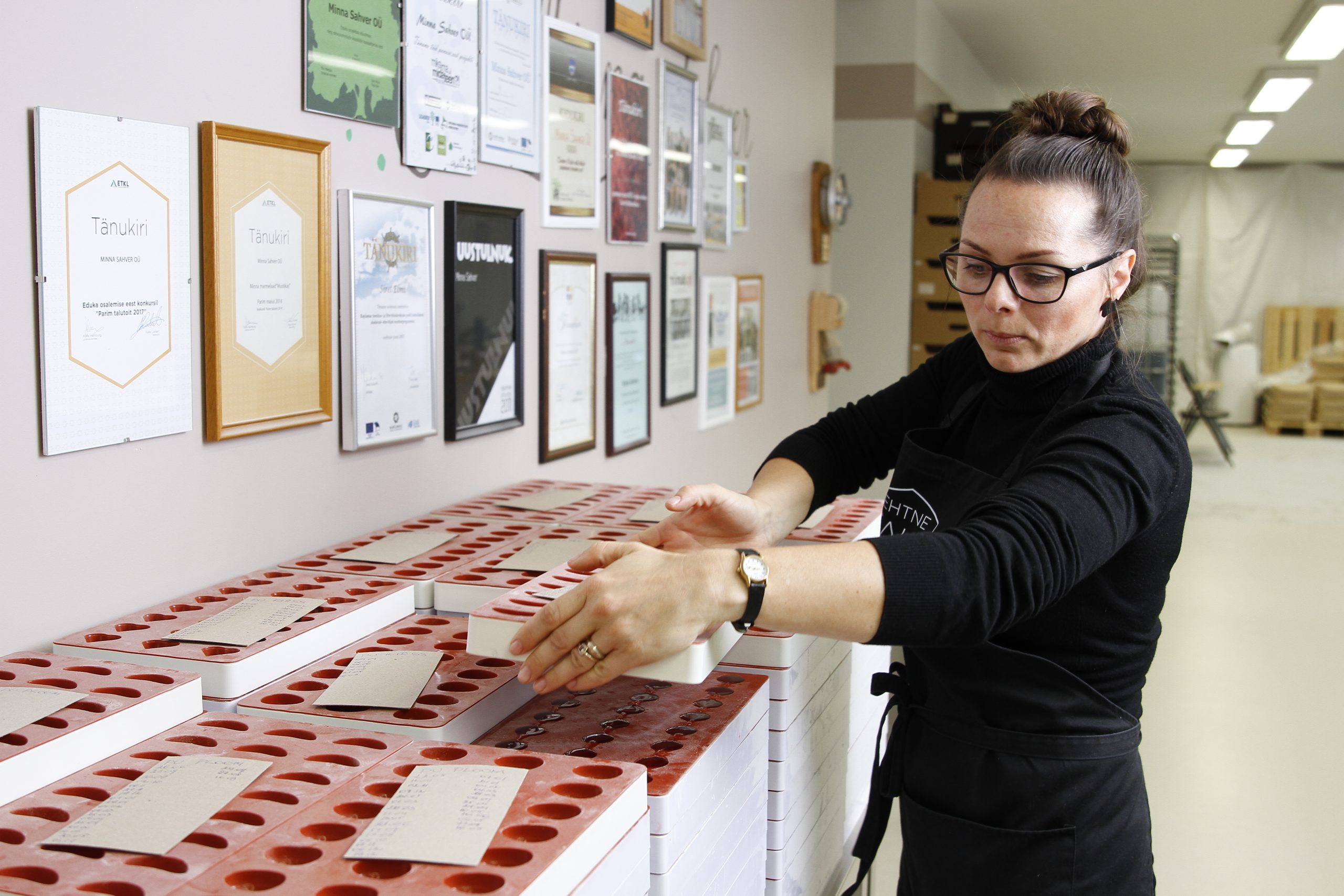
The benefits of implementing an inventory shelf life management system
Once you’ve got yourself set up with an inventory management system, here is a list of benefits you can expect to find:
1. Demand classification
Using software for inventory shelf life management is going to help you make the best possible predictions on future demand with real-time analytics, greatly improving your demand planning.
Monitoring your entire inventory from one dashboard can allow you to see which products are moving the fastest, which are at risk of becoming dead stock, and if some inventory performs better during different periods of the year. Just remember, to get the most out of your demand planning to:
- Set your limits and group forecasts logically
- Take into consideration your resources when demand planning
- Set clear goals
2. Batch numbers
A perishable inventory management solution will allow you to use batch numbers during production, so you can easily trace your product’s current location — ne that within your shop floor or somewhere else along the supply chain.
The purpose of using batch numbers in your manufacturing process is to:
- Conduct fast and easy product recalls
- Ensure expiration date tracking
- Improve relationships with suppliers by having accountability
- Differentiate your products if they appear similar but using different processes (for example, a baker can make cakes with or without eggs)
3. Improved inventory management
Improving your inventory management is one thing, but as a manufacturer with perishable inventory, you need a system that can monitor all different types of inventory. Most cloud-based manufacturing software often comes with barcode scanning functions and allows you to track, in real-time, different inventory types, allowing you to improve:
- Raw material inventory management
- Work-in-progress (WIP) inventory management
- Finished goods inventory management
By having more control over your perishable inventory management, you’ll be able to reduce manufacturing costs and improve your production process by knowing exactly where your inventory is and any areas in your business where problems occur.
4. Safety stock and reorder points
A good perishable inventory management system will give you the tools to set up safety stock and reorder points, so you can maintain ideal stock levels that’ll allow you to quickly react to a spike in demand or a stock adjustment from items spoiling.
Your safety stock will be your buffer, so that means you’ll carry an X number of items, and when your stock levels start to dip, you’ll still have items in your inventory when you purchase more or manufacture more finished goods.
And setting reorder points in your perishable inventory management system will notify you when you start to dip into your buffer.
5. Improved manufacturing lead time
Using the right perishable inventory management system is going to reduce your manufacturing lead time. With the help of the right tool, you and your team will know what needs to be done and when, as well as:
- Optimize production planning and scheduling
- Store your bill of materials (BOMs)
- Define operations
- Automate manufacturing cost calculations
Outlook for the perishable goods industry
Despite the prices for perishable goods increasing around the globe, there was a significant price decrease for some items. The price for 308 SKUs (36.3%) decreased — with 13.6% of the reduced pricing occurring between 5 to 20%.
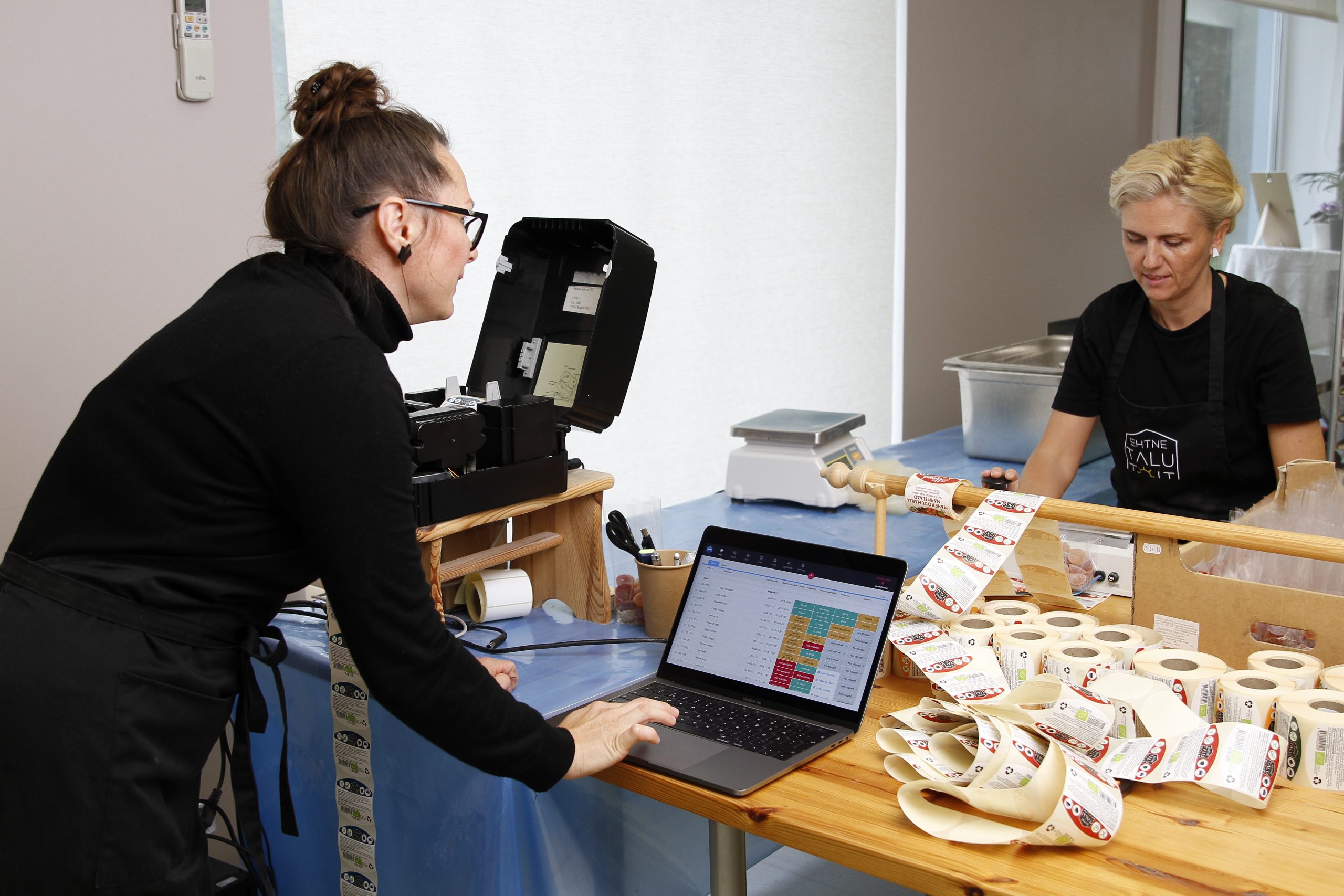
Get full traceability with cloud inventory software for perishable inventory
Katana’s cloud inventory software helps thousands of businesses get a live look at their inventory, production, sales, and more. Perishable inventory management is significantly easier to track with features designed to give you total visibility and control, including:
- Batch or lot number tracking
- Expiration and best-before-date tracking
- Product recall processes
And there you have it — everything you need to know about implementing an inventory shelf-life management system into your business. If you’d like to learn more about perishable inventory management systems like Katana, check out our features.
Team Katana
Table of contents
Get inventory trends, news, and tips every month
Get visibility over your sales and stock
Wave goodbye to uncertainty with Katana Cloud Inventory — AI-powered for total inventory control