Operations in manufacturing: How to stay in control
Perfecting how you manage your operations in manufacturing is a surefire way to success. Read how to optimize your shop floor with this article.
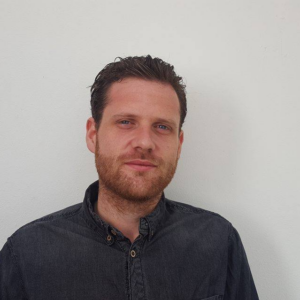
James Humphreys
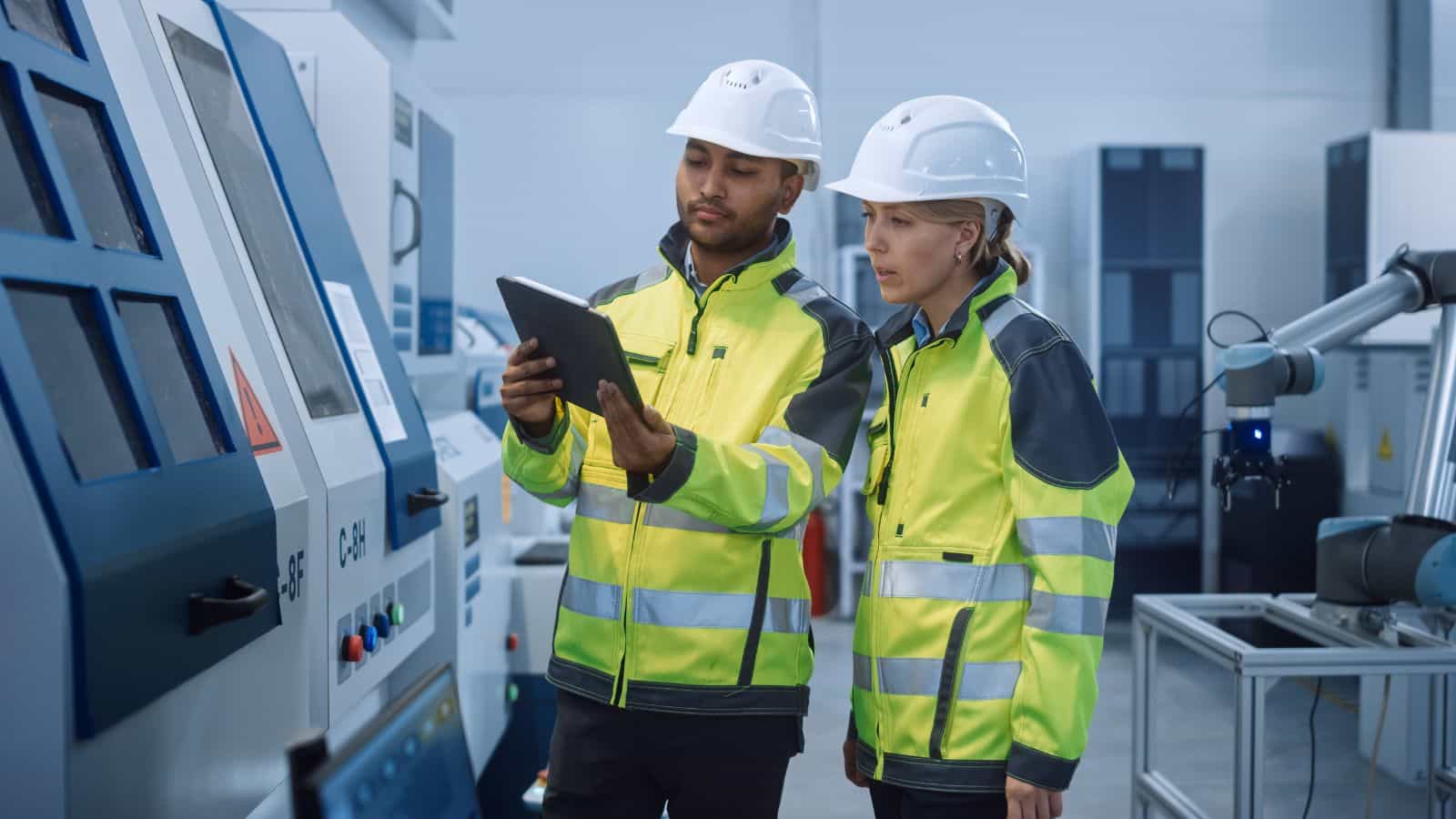
Designing a quality product is a big part of starting a manufacturing company, but it isn’t everything.
Even with the best idea in the world, you’ll still struggle to create a profitable business without the right person (or people) managing your operations.
There needs to be an overseer in the various operations in manufacturing, constant communication between the factory floor and office staff, and a focus on efficiency to maintain profitability.
Operations are the department concerned with these things.
It’s about ensuring that the products are being made correctly, on time, and within budget. To do this, operations managers need to deeply understand the manufacturing process and identify areas where improvements can be made.
It’s more than just adjusting on the fly.
The best operations teams will be proactive in their approach, always looking for ways to streamline the process and make it more efficient. This might mean automating certain tasks or implementing new technologies that can help to speed up production without sacrificing quality.
Below, we’ll examine the definition of manufacturing operations management, its responsibility, and some best practices that will set you up for success.
Taking control of operations and beyond
Katana is an all-in-one tool that helps you manage your entire workflow, from purchases to operations and shipping. Want to fine-tune your whole business by using just Katana?
What are operations in manufacturing?
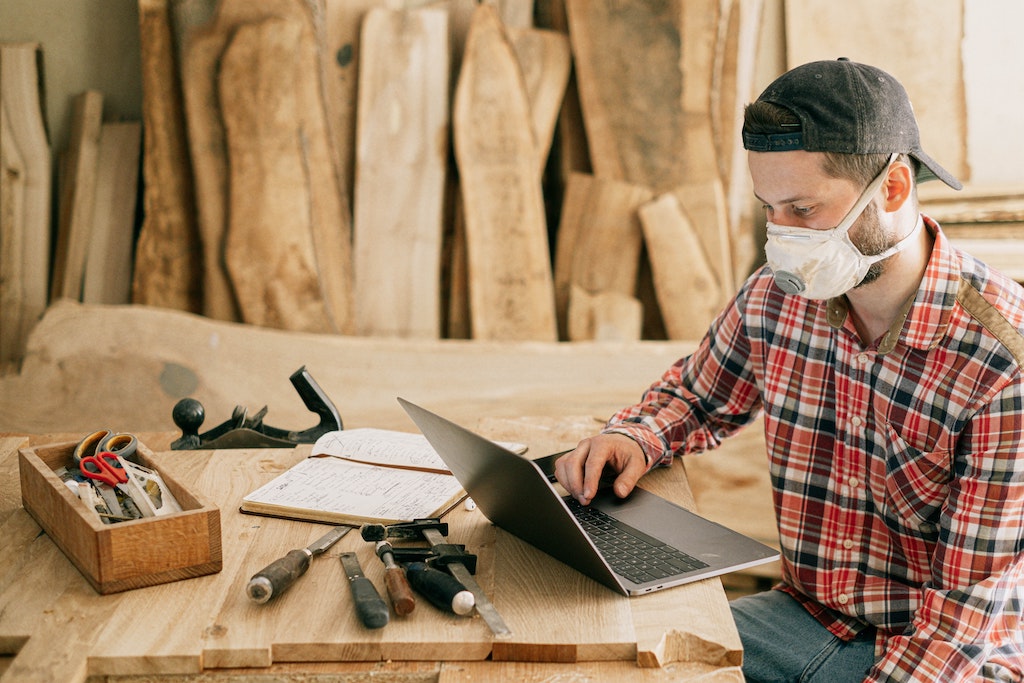
Operations in manufacturing are the process responsible for the creation and delivery of a company’s products or services. It includes everything from the sourcing of raw materials to the assembly of finished products, as well as any other steps in between.
The goal of operations is to do all of this as efficiently and effectively as possible while maintaining a high-quality level. The balancing act between craftsmanship and profit margins is one that every company struggles with, but it’s especially important in manufacturing.
That’s because the costs associated with production are often much higher than in other industries. There’s a lot of expensive equipment and machinery involved, and the process is often more labor-intensive than others. For these reasons, even small efficiency improvements can greatly impact the bottom line.
What is the difference between production and manufacturing?
Production is the process of creating or obtaining items, while manufacturing is the process of creating those items. Production can refer to anything from farming to mining to construction, while manufacturing specifically refers to creating products in a factory setting. Confused? Check out this guide on production vs. manufacturing to learn more.
Benefits of a strong manufacturing operation system
Many benefits can come from effectively managing your operations in manufacturing. Perhaps the most obvious is that it can help to reduce costs and increase profits.
When done well, operations management can also lead to:
- Improved communication
- Greater efficiency and productivity
- Increased flexibility and agility
- Reduced waste and scrap
- A more engaged workforce
In today’s competitive marketplace, these are all vital ingredients for success. Take the last point, for instance. Employee engagement can have a drastic impact on a company’s bottom line.
One study found that disengaged employees cost American companies up to $550 billion every year. Finding a way to inspire and engage your team can greatly impact your business.
The benefits of managing your operations in manufacturing are interconnected. For example, improving communication can directly impact employee engagement, which in turn can lead to increased productivity.
The best managers will be able to weave a web of improvements that amplify each other and lead to real, tangible results for the business.
What is manufacturing operations management (MOM) responsible for?
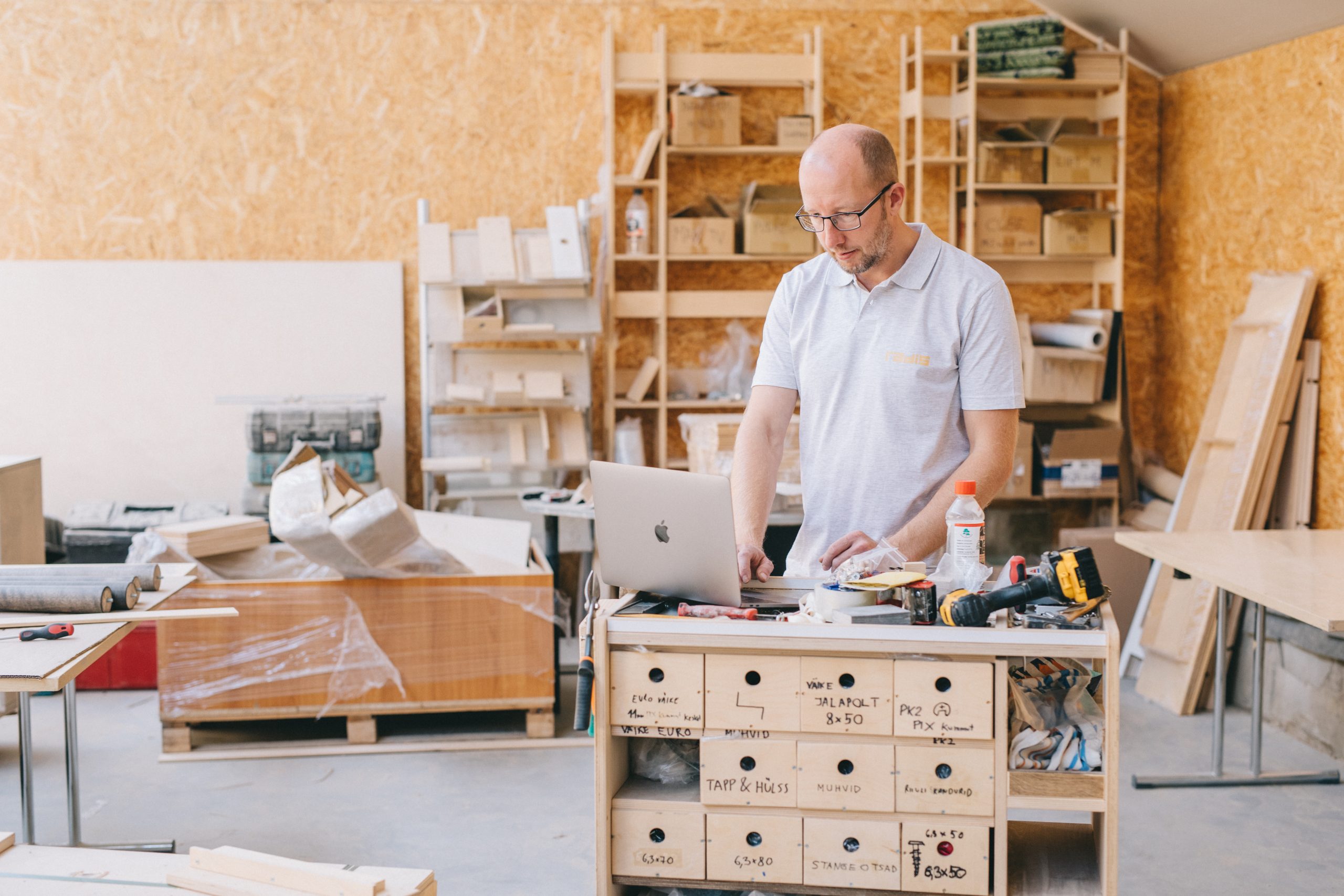
MOM, or manufacturing operations management, is a term used to describe the software systems and processes responsible for managing the production process. It includes everything from materials management to quality control and can be broken down into four main stages.
Planning
Before diving headlong into the production process, a careful plan is essential. The goal of the planning stage is to develop a roadmap that can be followed to ensure that the final product meets all the requirements.
This is not as simple as just saying, “we’re going to make a 5×5 box.” It needs to include things like what type of wood will be used, how many nails are required, and how long it will take to complete the task. All of these details need to be considered before production can begin.
A successful production plan will feature:
- End goals — What are you trying to achieve?
- Detailed task lists — What needs to be done to make this happen?
- Realistic estimates — How long will each task take, and how much will it cost?
- Contingencies — What will you do when something goes wrong?
Without one, it will be difficult to monitor progress, make adjustments, or even know if you’re on track to meet your targets.
Scheduling
Knowing exactly who will be responsible for each task and when it needs to be completed is crucial for operations in manufacturing businesses. This includes the workers on the factory floor, office staff, support personnel, and anyone else who might be involved in the process.
The scheduling stage of MOM is about creating a timeline that can be followed to ensure that everyone is aware of their responsibilities and knows when things need to be done. This might include daily or weekly production meetings to review progress, as well as more detailed scheduling for individual tasks.
It’s important to note that the schedule should be flexible enough to accommodate changes. This might mean built-in buffer time for each task or the ability to reassign workers to different areas if something goes wrong quickly. The goal is to avoid disruptions in the production process, which can lead to delays and increased costs.
If working with an overseas contract manufacturer, the scheduling phase can be extremely challenging. Time differences, cultural differences, and language barriers can all lead to communication problems. It’s important to work with a partner that you trust and have a good relationship with to avoid these issues.
Execution
Now’s the time to put all that preparation to work.
The product is created in the execution stage, and it’s important to have a well-oiled machine if you want things to run smoothly. This includes having the right tools and equipment, as well as trained personnel who know how to use them.
It’s also crucial to have systems in place to track progress and identify any issues that might arise. This might include quality control measures, as well as regular check-ins with team members to ensure that everyone is on track.
In the execution stage, things can start to go off the rails, so it’s important to be prepared for anything. Have a plan in place for what to do if something goes wrong, and be sure to communicate it to everyone involved. That way, you can avoid costly delays or rework.
Control
Once the production process has started and you are comfortable with your scheduled timelines, it’s time for the most critical part of MOM — control.
This is where you will monitor progress and ensure everything is going according to plan.
This stage can be broken down into two main areas:
- Quality control
- Schedule compliance
Quality control
Are your products meeting the standards that you set?
This is where quality control comes in. There are several ways to ensure that your inventory is up to snuff, but it’s important to have a system in place that can catch any issues early on. That way, you can make the necessary adjustments before it’s too late.
One way to do this is to perform regular inspections at different points in the production process. This could be done by an independent third party or by your team. Either way, it’s important to have someone check in on things to ensure everything is being done according to specifications.
Another way to keep tabs on quality is through customer feedback. This can be gathered in several ways, but one of the most effective is through post-purchase surveys. These can help you to identify any issues that might not be apparent during the production process.
It’s also important to have systems in place to track defects. This data can be used to identify areas of improvement in the production process. By keeping track of these things, you can ensure that your products are always meeting the highest standards.
Schedule compliance
You will also need to track progress against your schedule. This will help you to identify any potential delays and take steps to get things back on track. It’s also important to compare actual results against your estimates so that you can fine-tune your process for future projects.
One tool that can be helpful here is earned value management (EVM). This technique can be used to measure progress and calculate the value of work that has been completed. EVM can be a bit complex, but many software applications can help to automate the process.
Live production scheduling software
Become unstoppable with Katana, which gives you the tools to create and monitor operations in real time. Did something happen that disrupted production? Simply reprioritize your workflow, and Katana will automatically redistribute resources to open orders.
Best practices in manufacturing operations
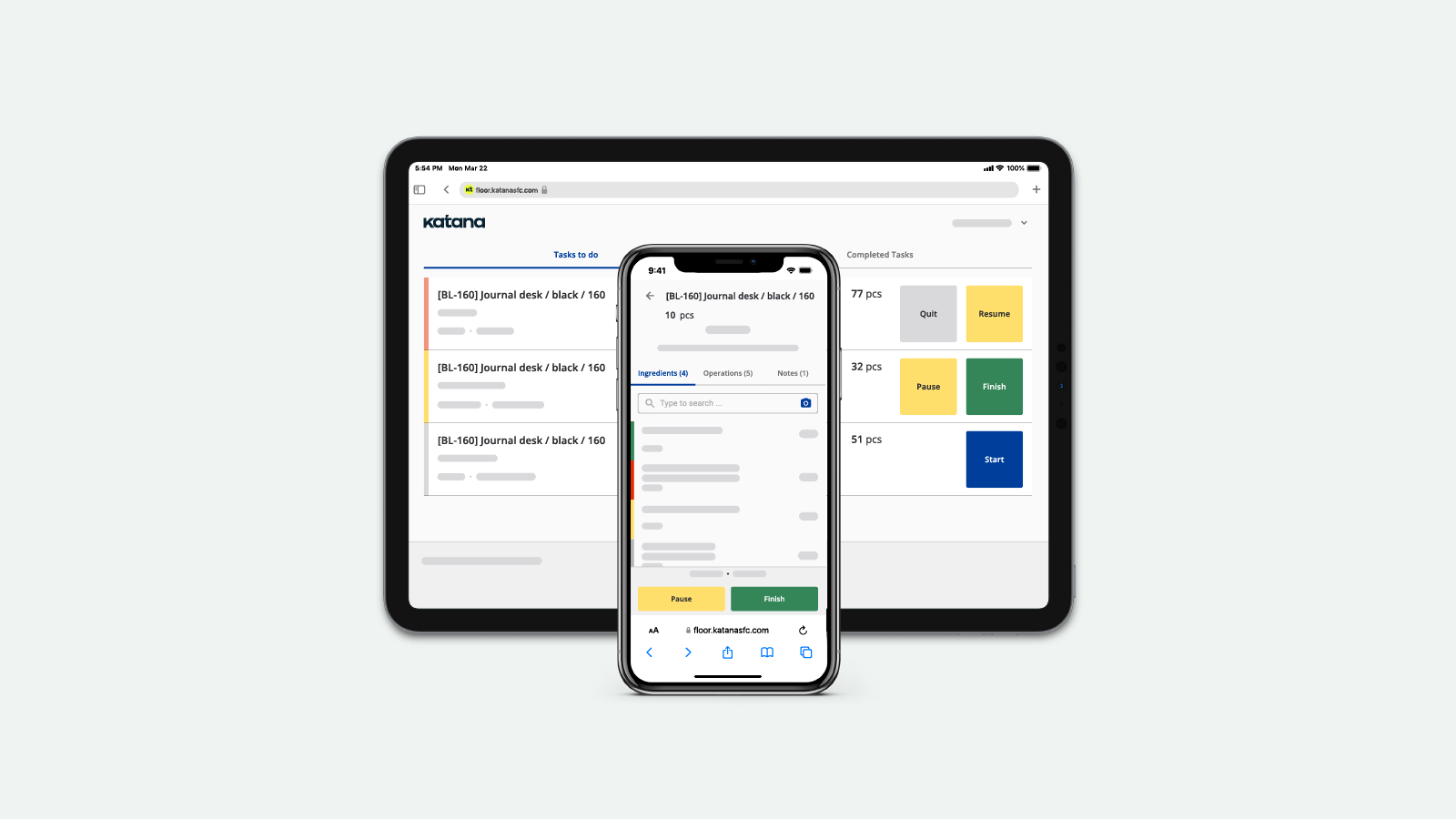
Importantly, these four stages of MOM are not always sequential.
You will need to ping-pong back and forth while being flexible enough to quickly make changes to any part of the system as needed.
For example, if you’re in the middle of execution and realize that you’re missing a key piece of equipment, you’ll need to quickly adapt and go back to the planning stage to find a solution.
Or if your supply chain is disrupted during the control phase, you’ll need to adjust your schedule to make sure you still have the proper inventory for your upcoming demand forecast.
One of the best ways to stay on top of things is with Katana’s Shop Floor App, which is meant to improve communication between operations managers and the production team by:
- Automatically clearing individual task lists
- Updating live production status, by linking directly from the app to Katana
- Limiting wasted resources with paperless manufacturing orders and memos
- Focusing individual access to only the sections that apply to each employee
By creating Operator accounts for each necessary team member, you can allow your staff to log in to Katana and access their task list from any device.
ERP (enterprise resource planning) software will give you a real-time view of your manufacturing process from start to finish. That way, you can quickly see where things are going wrong and make the necessary changes to get back on track. Get a demo and get your operations team firing on all cylinders!
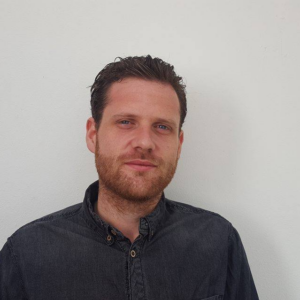
James Humphreys
Table of contents
Get inventory trends, news, and tips every month
Get visibility over your sales and stock
Wave goodbye to uncertainty with Katana Cloud Inventory — AI-powered for total inventory control