Your guide to warehouse inventory management
Warehouse inventory management is a crucial aspect of supply chain efficiency. This article will walk you through it all, from the basics to the detailed know-how needed in daily operations. We’ll also shed light on the intricacies of warehouse inventory management systems and arm you with actionable tips you can start to apply today.

Ioana Neamt
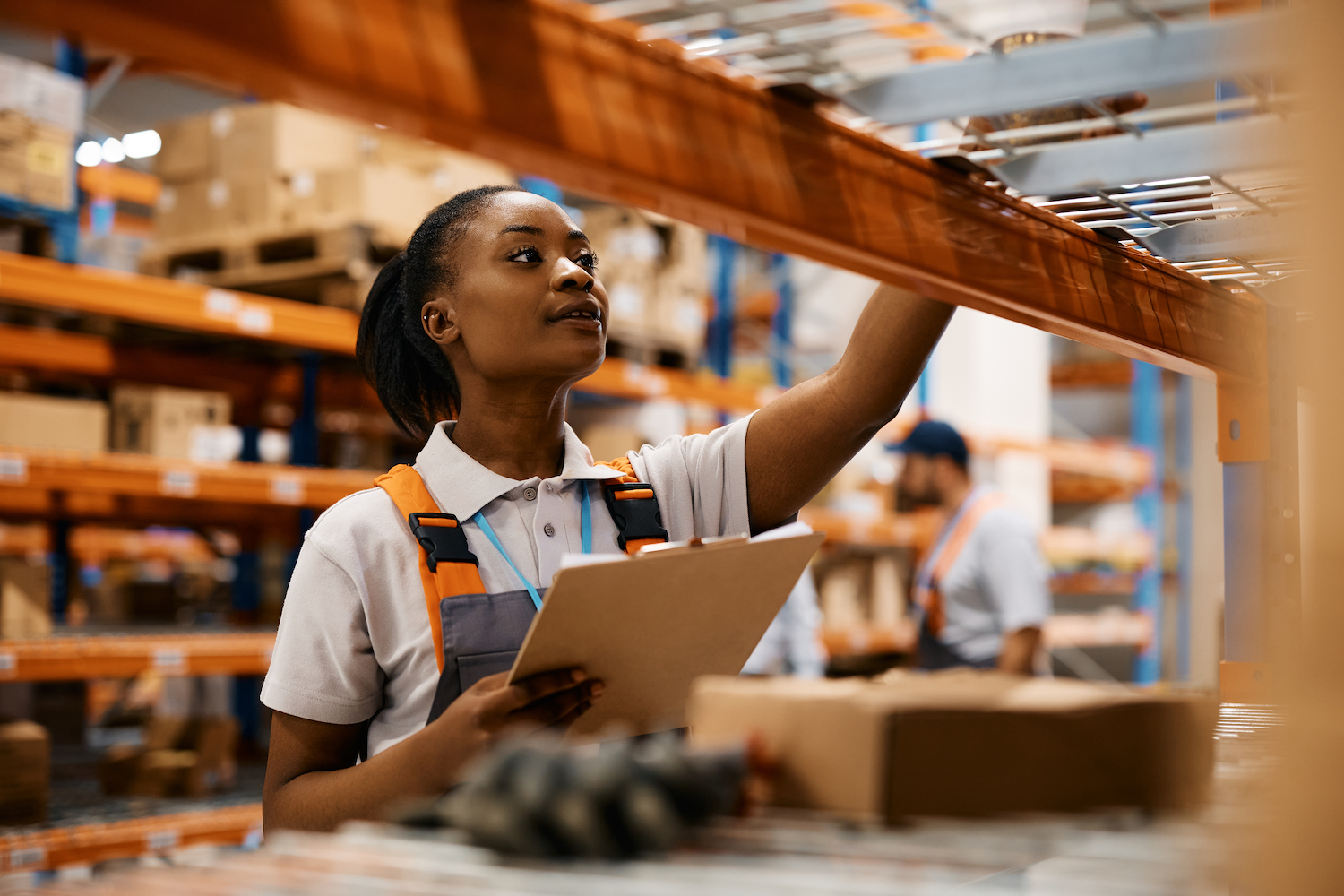
How well you manage your inventory dictates how smoothly your e-commerce business operates, with a direct impact on your bottom line. Effective warehouse inventory management is the only way to ensure you always maintain optimal stock levels and keep your storage costs to a minimum, even as your business grows.
However, perhaps its indirect effect is even more important — keeping on top of warehouse inventory management guarantees you can consistently deliver products promptly. In turn, this boosts customer satisfaction and retention rate, which will inevitably have their say when you calculate your profits.
Optimizing warehouse inventory management is an ongoing, ever-present challenge. The best strategy can look radically different, not only from one industry to another, but it may vary widely even between businesses in the same field, throughout different growth phases, or even seasonally.
However, that’s not to say there aren’t any generally valid points to keep in mind as you figure out your own inventory management strategy. This guide is here to help you with exactly that.
Understanding warehouse inventory management
Warehouse inventory management is a collective term that encompasses your visibility of storage and inventory movement within a warehouse facility. It’s the sum of a wide range of tasks, including receiving goods, maintaining inventory levels, tracking stock locations, ensuring product quality, processing orders, and even managing warehouse staff.
In other words, the goal of warehouse inventory management is to optimize inventory levels, minimize storage costs, and ensure efficient order fulfillment to meet customer demand. Consequently, it’s essential for keeping your supply chains in check, reducing costs, and enhancing customer satisfaction.
Warehouse inventory management is usually the job of a warehouse inventory manager who may act on their own or lead an internal team, but the task can also be outsourced to a third party, depending on the size and nature of the operations. In either case, these specialists often rely on software systems and AI technologies to help with the calculations and tracking.
Inventory management vs. warehouse management: key nuances
Before we get down to the nitty-gritty of warehouse inventory management, we must clear up some of the confusion around the terminology. The industry differentiates two separate facets of managing stock:
- Inventory management — Activities related to forecasting business trends and managing stock according to the expected demand. The term normally covers business-level decision-making. In this context, inventory includes not only the finished products in storage but also the goods already in storefronts, as well as raw materials and parts still in the manufacturing phase.
- Warehouse management — Inventory handling processes and related tasks within a warehouse or storage facility. It also involves optimizing stock storage for smooth operations, as well as picking and packing tasks. Warehouse management is also responsible for minimizing waste, for example, by prioritizing stock with the closest expiration date.
In a nutshell, inventory management is a high-level overview of everything that has to do with stock, from the point of acquisition to the point of sale. Meanwhile, warehouse management is all about the details of running an efficient warehouse, focused solely on the handling of finished products until they go out of storage.
Download the ultimate guide to inventory management
A comprehensive ebook with everything you need to know about inventory management.
Why it matters — The benefits of warehouse inventory management
Bluntly put, having no warehouse inventory management in place is like having a lid on your business’ potential. However, having a substandard one is not much better, as it can also wreak havoc on your entire supply chain, affecting everything from logistics costs and employee morale to fulfillment accuracy, shipping times, and customer satisfaction.
So, when saying benefits, we don’t mean reasons why it’s a good idea to do warehouse inventory management in the first place — that goes without saying. Rather, it’s about why you should constantly improve it and make sure it’s always ready to accommodate growth. With that said, these are some of the results you can expect in return for your efforts:
- Improved order fulfillment accuracy — Accurate inventory tracking helps prevent stockouts and overstocks, so you can make sure customer orders are fulfilled promptly and correctly, minimizing complaints and lost clients.
- Quicker deliveries — Timely shipments and deliveries are crucial for customer satisfaction, and effective inventory management is essential for achieving this. Accurate inventory levels and streamlined fulfillment processes ensure that orders reach your customers promptly and increase the chances of them coming back for more of your products.
- Lower costs — Effective inventory management practices can significantly reduce storage costs, preventing losses due to overstocking, expiration, or damage. Similarly, accurate inventory tracking reduces the risk of running out of stock when you need it the most, which can hurt your sales and affect your bottom line.
- Higher staff productivity — Optimizing processes and implementing sound warehouse automation empowers your staff to focus more on strategy, unlocking new avenues for growth, and less on repetitive tasks.
- More good reviews — Checking all the boxes above gets you closer to higher customer satisfaction and loyalty with each step. Satisfied customers are more likely to return for repeat business and recommend the company to others, boosting your brand’s reputation and driving sales growth.
Demystifying warehouse inventory management systems
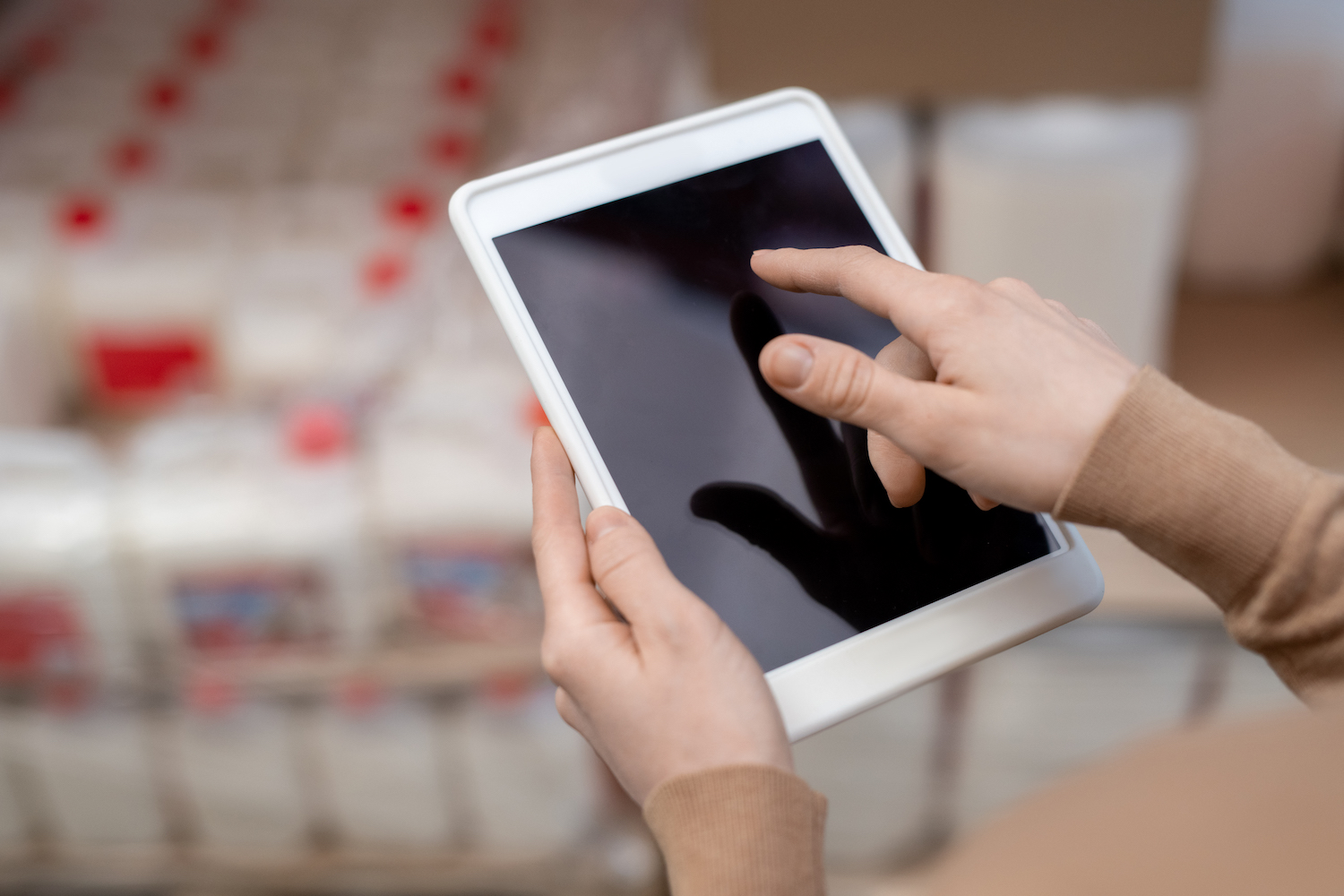
Warehouse inventory management systems, or WMSs, are software solutions designed to help you efficiently track and manage the storage and movement of stock within your warehouses. These often provide a suite of features and functionalities that help streamline inventory control processes, thus enhancing overall operational efficiency. These are some of the key features many WMS solutions offer and their benefits:
- Inventory tracking — A warehouse inventory management system’s base functionalities are providing real-time visibility into inventory levels, helping locate items within the warehouse, and tracking stock movements throughout the supply chain. This minimizes the risk of stockouts and overstocks and helps you maintain control over your inventory.
- Order management — WMS systems facilitate order processing and fulfillment and optimize picking, packing, and shipping procedures. A streamlined order processing and fulfillment ensures deliveries arrive to the right clients and unlocks faster shipping times, boosting customer satisfaction along the way.
- Reduced labor costs — WMS systems can automate repetitive tasks and streamline processes, reducing labor costs and improving employee productivity.
- Warehouse layout optimization — Beyond helping order processing, warehouse management systems also help you find the best warehouse layout and storage strategies for your business and maximize picking efficiency. On top of ergonomics, this can further reduce your operational costs.
- Automated replenishment — Inventory replenishment processes can be automated using warehouse management systems. These systems can trigger reorder points based on predefined stock levels and demand forecasts, helping maintain inventory levels with little to no manual intervention.
- Reporting and analytics — WMS systems generate comprehensive reports and provide data analytics insights so you can identify trends, make informed decisions regarding inventory replenishment, pricing strategies, and promotional activities, and keep improving your inventory management practices.
- Integration with enterprise resource planning systems — Although most warehouse inventory management software is available as a standalone solution, many WMS systems on the market support integration with broader enterprise resource planning solutions. This adds another layer of scalability to your warehouse management framework and provides a holistic view of inventory management across the entire supply chain.
State of Inventory Management: A Review of Rising Costs
Businesses worldwide have faced challenges from supply chain volatility and may continue to experience hardships going into 2024. Download the report and see how omnichannel selling has helped Katana customers increase sales orders despite economic uncertainty.
Choosing the right warehouse inventory management system
The choice of the ideal WMS for your application depends on factors such as business size, inventory volume, industry requirements, and budget considerations. You should carefully evaluate your specific needs and assess the features and capabilities of different WMS solutions before you make the call.
We already mentioned that warehouse inventory management is often split into two separate disciplines: warehouse management and inventory management. WMS systems branch off in a similar fashion.
Inventory management systems (IMS)
IMSs focus on tracking the movement and status of inventory throughout your warehouse and supply chain. They provide visibility into stock levels, incoming and outgoing orders, and historical sales data. IMSs can be simple spreadsheets or sophisticated software systems that integrate with point-of-sale platforms and warehouses.
Key features:
- Tracking incoming orders, stock levels, and outgoing orders
- Forecast inventory needs based on customer demand and sales data
- Generate alerts and notifications for cycle counts
In summary, inventory management software covers the acquisition, tracking, and shipping of products. It ensures you are always aware of the location of your products in real time, and you also have a reliable log if you ever want to retrace any steps.
Warehouse management systems (WMS)
WMSs extend beyond inventory tracking to manage the entire warehouse operation. They provide features for employee management, picking, packing, shipping, and warehouse layout optimization. WMSs help minimize disruptions, automate processes, and improve overall warehouse efficiency.
Key features:
- Track employee movements and productivity
- Optimize picking, packing, and shipping processes
- Manage warehouse layout and storage strategies
While inventory management systems focus primarily on tracking inventory levels and movement, warehouse management systems offer broader functionalities that extend beyond inventory control. They provide comprehensive tracking of various metrics throughout the warehouse, including employee movements and order fulfillment processes.
Inventory tracking is certainly an integral part of most warehouse management systems, but it is typically not their primary function.
Which one is right for your business?
While IMS focuses on inventory control, WMS encompasses broader warehouse operations, particularly in multilocation scenarios. A WMS provides advanced features for managing inventory across multiple locations and centralized storage facilities.
A WMS is more suitable if you have employees and multiple storage locations to manage or need help locating inventory items. However, if you primarily need to manage and track your inventory supply chain, an IMS should be sufficient.
7 best practices for effective warehouse inventory management
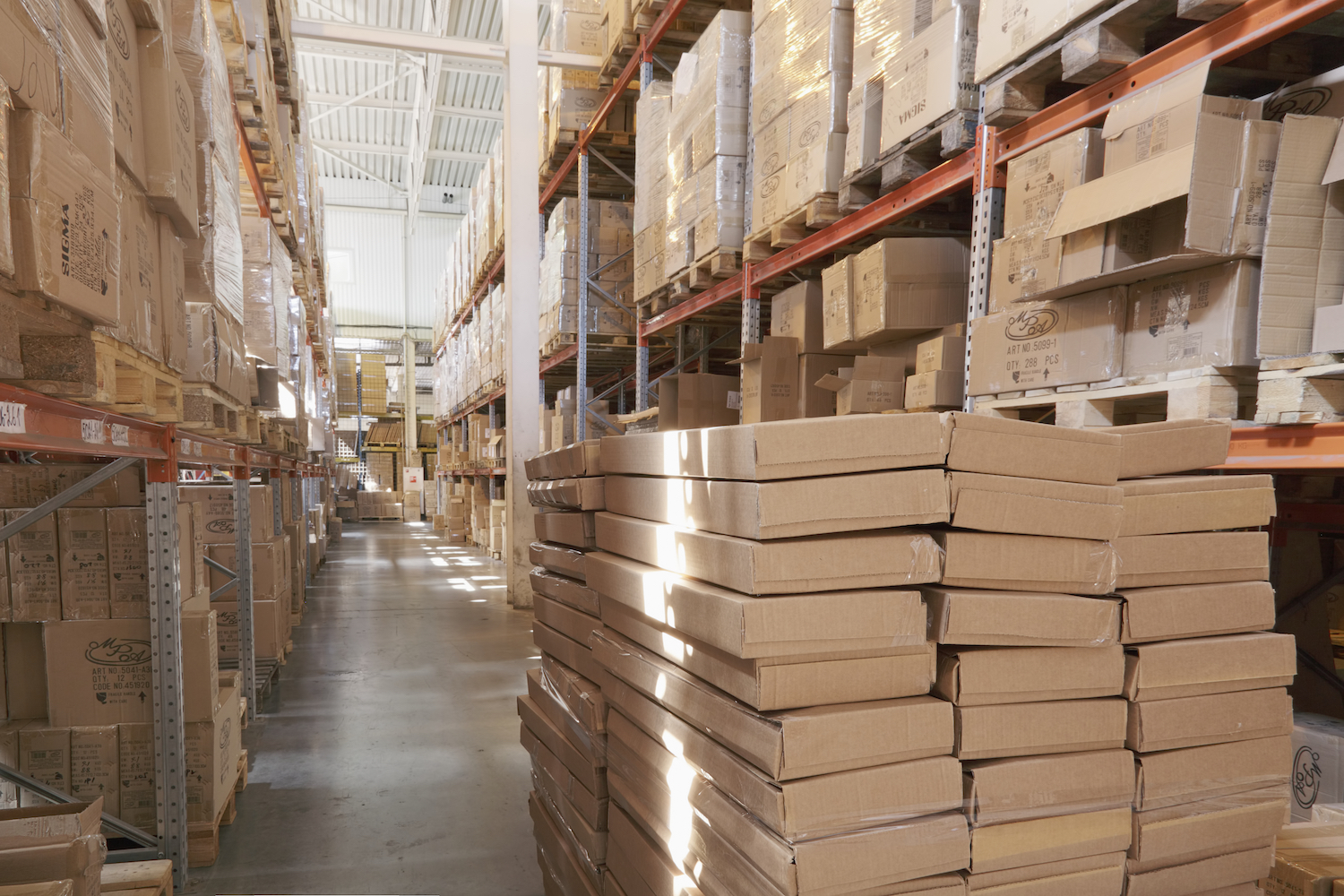
This section explores the best practices that contribute to the efficient organization, tracking, and control of inventory within a warehouse setting, ultimately enhancing overall logistical efficiency.
1. Hire a warehouse manager and empower your workforce
Efficient warehouse management starts with appointing a qualified warehouse manager who possesses extensive experience in operating a similar warehouse. This individual will oversee the day-to-day operations, ensuring inventory levels meet customer demand, goods are received and shipped on schedule, and warehouse space is utilized effectively.
Empowering your warehouse workforce is equally important for achieving efficiency and accuracy. Encourage feedback from your team to identify areas for improvement and implement automation tools to streamline tasks. This will free up your employees’ time to focus on finding innovative ways to enhance warehouse operations.
2. Prioritize your stock — Adopt the 80/20 rule
Effective inventory management hinges on prioritizing stock items and implementing standardized procedures for receiving and handling stock.
The 80/20 rule, also known as the Pareto Principle, highlights the importance of identifying and focusing on the 20% of inventory items that generate 80% of your profit. This prioritization allows for better allocation of resources and attention, ensuring that your most valuable stock is managed effectively.
Additionally, developing a consistent approach to receiving and handling stock minimizes discrepancies and ensures accurate inventory tracking. By implementing these strategies, you can optimize your inventory management practices and achieve greater profitability.
3. Design your warehouse for efficiency
An efficient warehouse layout is crucial for optimizing operations and maximizing productivity. The key to achieving an efficient layout is to consider the movement of goods, product accessibility, and space utilization.
- Prioritize high-value and high-transaction-volume items by placing them closer to the shipping and packing areas. Also, organize your inventory based on demand, seasonality, or product characteristics. This will minimize travel time for warehouse workers, expedite order fulfillment, and make it easier for warehouse personnel to locate items quickly and efficiently.
- Utilize vertical space effectively by considering the use of racking systems and vertical lift modules (VLMs). These solutions allow you to store a large inventory in a compact footprint and provide easy access to products.
- Regularly review your warehouse layout to ensure it aligns with current business needs and adapts to changes in inventory or product mix. By optimizing your warehouse layout, you can significantly improve efficiency, reduce labor costs, and enhance overall productivity.
4. Implement a WMS — Embrace automation and eliminate manual tasks
Warehouse inventory management software streamlines inventory tasks and provides stock updates whenever needed. With proper scanning and cataloging of items, warehouse inventory management software accurately tracks stock levels and locations. Cloud-based software is especially well-suited for applications where you need real-time analytics.
WMS also provides features for inventory optimization — for example, setting low-stock alerts will ensure you never run out of stock while avoiding a potential overstocking problem too. Taking the same idea further, many WMS solutions even have the capability to automatically reorder products when your stock drops to a certain level.
Speaking of reorder points, you can also rely on the software’s capabilities to help determine optimal stock levels.
Keep in mind that the alternative, manual tasks, are not only time-consuming but also prone to human error. Automated solutions can help you count and manage your warehouse inventory quicker, more accurately, and with less effort. These include:
- Warehouse drones
- Sensors
- Wearable devices
- RFID tags
Furthermore, mobile devices like tablets and handheld scanners also help reduce paper consumption — on top of their efficiency, accuracy, and ease of use. All of this means that your staff can drop the mind-numbing tasks and focus on what they’re best at.
5. Forecast smarter — Anticipate demand and thrive in busy seasons
Demand forecasting is a critical tool for warehouse managers to anticipate demand fluctuations and ensure optimal inventory levels.
By analyzing historical sales data, identifying trends, and considering seasonal patterns, demand forecasting can help you prepare for busy seasons and take full advantage of upswings in sales. Demand forecasting also helps you identify slow-moving items and optimize storage costs.
6. Safeguard your inventory — Regularize cycle counting and inspections
Ensure inventory accuracy and prevent stockouts by implementing regular cycle counting and inspections. Cycle counting involves periodically counting a portion of your inventory to identify discrepancies, while inspections involve observing warehouse operations to identify potential issues that could lead to inventory losses or safety hazards.
Additionally, regular audits can provide a comprehensive overview of your inventory status and help you identify areas for improvement. The frequency of these checks can vary based on inventory value and importance.
7. Embrace innovation and stay ahead of the curve
Embrace a culture of continuous improvement in your warehouse operations to enhance efficiency, productivity, and safety. This involves regularly reviewing processes, identifying areas for improvement, and implementing new strategies to optimize warehouse management.
Stay updated with the latest technology advancements in the warehouse industry. Explore innovative solutions like mobile applications, automation tools, and sensor-based systems to automate tasks, improve safety, and maintain optimal storage conditions.
Planning for the future involves anticipating customer needs and preparing for business growth. By understanding demand trends and proactively expanding inventory management capabilities, you can adapt to changing market conditions and seize opportunities for expansion.
Untangle the warehouse inventory management web with Katana
Start streamlining your warehouse inventory management operations today with Katana’s cloud-based software solution that enables you to oversee and manage your entire setup in one place. Get a real-time overview of your stock levels, inventory needs, and more, with Katana. Get in touch with us to request a demo and see Katana in action!

Ioana Neamt
Table of contents
Get inventory trends, news, and tips every month
Get visibility over your sales and stock
Wave goodbye to uncertainty with Katana Cloud Inventory — AI-powered for total inventory control