Stay at the top of your game with manufacturing process improvement
“Change is the only constant” — a key principle to follow in production industries, not only because it is essential to expect change, but also to understand how you can best position your operations to ensure that change works in your favor. The best way to do that is through continuous improvement of your manufacturing process.

Ioana Neamt
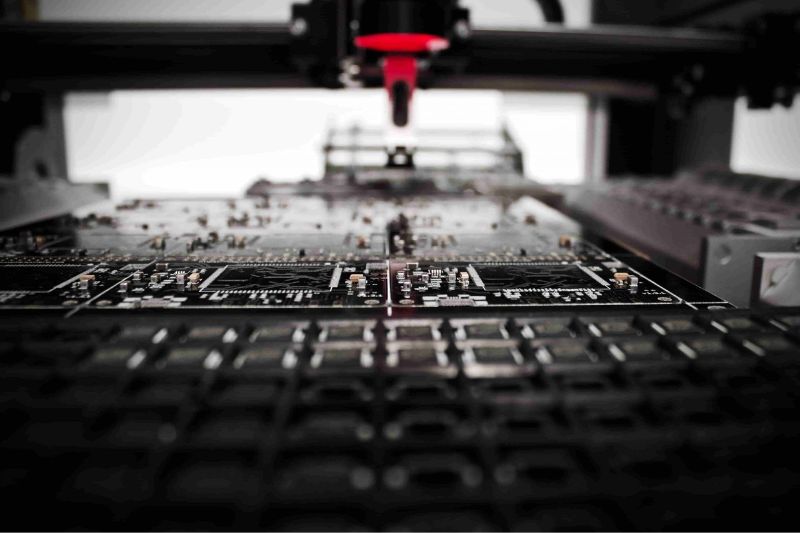
Even if probably all of us swore that we wouldn’t need math for anything when we grew up, we still got the idea stuck in our minds that the quickest way from point A to point B is a straight line. However, things are not as stripped back as that saying may lead us to believe. First, we need to know where and what point A and point B are. And, while we have since learned that math is certainly essential to many things, it is also important to understand that the line of progress in the real world is rarely ever straight.
In fact, we find that a lot of the time, progress is about looping back, analyzing, and accounting for mistakes or miscalculations.
Progress happens when we correct courses using that new information. Growth happens when we continually review our process in the interest of improving. This is as true of businesses as it is of people. In the manufacturing industry, continuous improvement is an essential element of sustainable success.
What is manufacturing process improvement?
Think of it as getting and keeping your ducks in a row. It refers to an ongoing effort to identify and eliminate anything that translates to waste, inefficiencies, and errors in your manufacturing process.
The goal is to achieve an ever more efficient, productive, and profitable manufacturing operation. Thankfully, you don’t have to do it alone or keep score yourself — there are several tools available to help you understand the key steps of a process, measure performance, and make changes to improve it.
Why is process improvement important in manufacturing?
To put it simply, it is better to stay ready than to have to get ready. In the fast-paced economic landscape, the most successful businesses are those that are ready to adapt.
- Enhance productivity
- Reduce costs
- Improve quality
- Boost customer satisfaction
- Respond well to changes
- Ensure employee safety
1. Enhance productivity and efficiency
By identifying and eliminating inefficiencies in the production process, manufacturers can reduce waste and downtime. When you optimize, you also make it easier for your employees to work more effectively. Achieving faster turnaround times and more efficient use of resources can help you reduce the time it takes to get your products to market. In industries where lead times are critical, this can give you a competitive advantage.
2. Reduce costs
Eliminating waste and improving efficiency are essential to reducing costs in manufacturing. Improving your manufacturing process correctly can translate to savings on materials, labor, energy, and maintenance.
3. Improve quality and consistency
Process improvement in manufacturing can also help you improve the quality of your product. Identify and correct defects as early as possible in the production process to achieve better quality control. This will minimize rework and increase the consistency with which you deliver high quality to your customers.
4. Boost customer satisfaction
Process improvement in manufacturing is also essential in earning higher customer satisfaction, loyalty, and repeat business. Consistently delivering high-quality products on time and within budget is guaranteed to create a positive experience for your customers.
5. Adapt to change
In today’s dynamic market, we see customer demands changing relatively rapidly, technology advancing in leaps and bounds, and regulatory requirements following suit. Continuous process improvement keeps manufacturers nimble and more easily able to adapt when needed.
6. Ensure employee safety, engagement, and empowerment
Employees who are actively involved in process improvement initiatives will feel valued and engaged. A good understanding of the manufacturing process, appropriate training, and participation in process improvement can increase the safety in your workplace. What’s more, it can help boost morale, motivation, and overall job satisfaction.
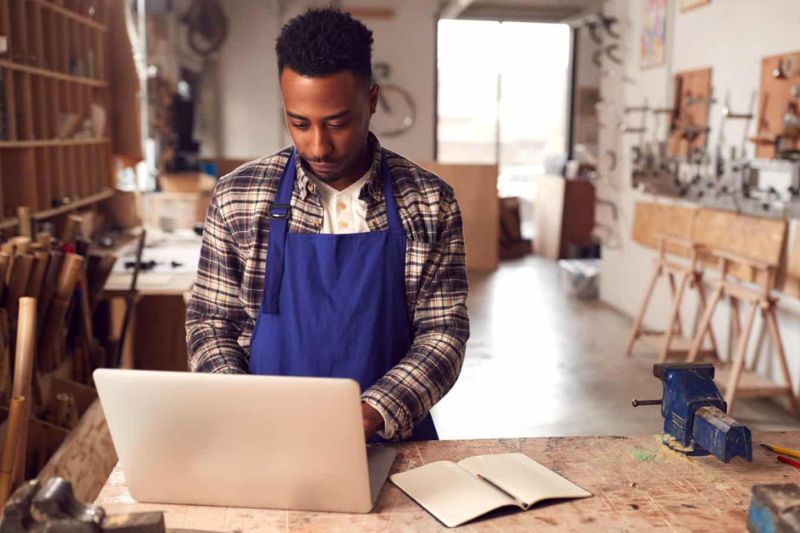
Manufacturing process improvement examples
There are several tools and strategies to approach the improvement of your manufacturing process, most of which operate under the principles of a philosophy called lean manufacturing.
Basically, you find and do away with as many “wasteful” steps and practices as possible in order to achieve a fluid production process. There are eight main types of “waste” that lean manufacturing process improvement requires that you focus on:
- Defects
- Overprocessing
- Overproduction
- Process delays (waiting)
- Surplus inventory
- Unnecessary motion
- Unnecessary transportation
- Underutilized talent
Below, you’ll find a short list of some of the most popular approaches to tackle them.
Kanban
This is a visual workflow technique that is designed to help identify bottlenecks and improve efficiency.
Using visual cues to mark the progress status of a task, the Kanban method allows you to better manage your production line. By encouraging workers to limit the tasks that can be in progress at any one time, this method pushes teams to identify and resolve problems as they arise — continuous improvement for a more streamlined flow of work.
Learn more about how to simplify workflow and boost productivity with our in-depth guide on Kanban for manufacturing.
5S
This methodology is about getting and staying organized. Employ this strategy to create a clean and efficient work environment — identify what is the optimal place for everything so that you maximize productivity and output. The five “S” stand for the five core principles it follows:
- Sort — Separate the necessary from the unnecessary
- Set in order — Arrange necessary items in a logical and easy-to-reach position for their intended purpose
- Shine — Keep the workplace clean and tidy
- Standardize — Establish clear procedures for maintaining a clean and well-organized workplace
- Sustain — Make it a strong habit to maintain a clean and organized work environment
Ways to implement this strategy include having a labeling system to identify and categorize items and conducting regular audits to identify and address any clutter issues.
Kaizen
Similar to the two methods presented above, Kaizen is a Japanese work philosophy. It refers to continuous improvement that focuses on making small, incremental changes to any process, and it relies on employee participation and empowerment to drive improvement efforts. Here are three steps you can take to implement the Kaizen method:
- Establish a culture that recognizes and rewards improvement efforts
- Encourage employees to submit and discuss improvement suggestions, no matter how small
- Hold regular kaizen discussions — daily, weekly, or whatever frequency works best for your operations — that facilitate the identification and implementation of improvements
Six Sigma
This is one of the most popular techniques used to implement quality control in manufacturing. It refers to a set of quality and process improvement techniques that focus on reducing the number of defects below a certain threshold.
Developed in the 1980s at Motorola, this method involves the structured use of statistical tools to reduce or eliminate defects, variation, and waste from the manufacturing process.
As popularized at Motorola, the Six Sigma implementation standard was the ability of a company to manufacture its products within a specification of 3.4 defects per million units — a high standard of output quality consistency, which can result in lasting customer appreciation for your business.
Overall equipment effectiveness
You can employ the OEE performance method to improve the productivity and efficiency of your production process. This strategy helps you maximize the output of equipment and processes while also taking into account the quality of the final result. Practical steps you can take to track and improve overall equipment effectiveness in manufacturing include the following:
- Make sure that your equipment is well maintained to minimize breakdowns and improve its availability
- Keep your staff well-trained on best practices to ensure that both your workers and your machines operate safely and at maximum efficiency
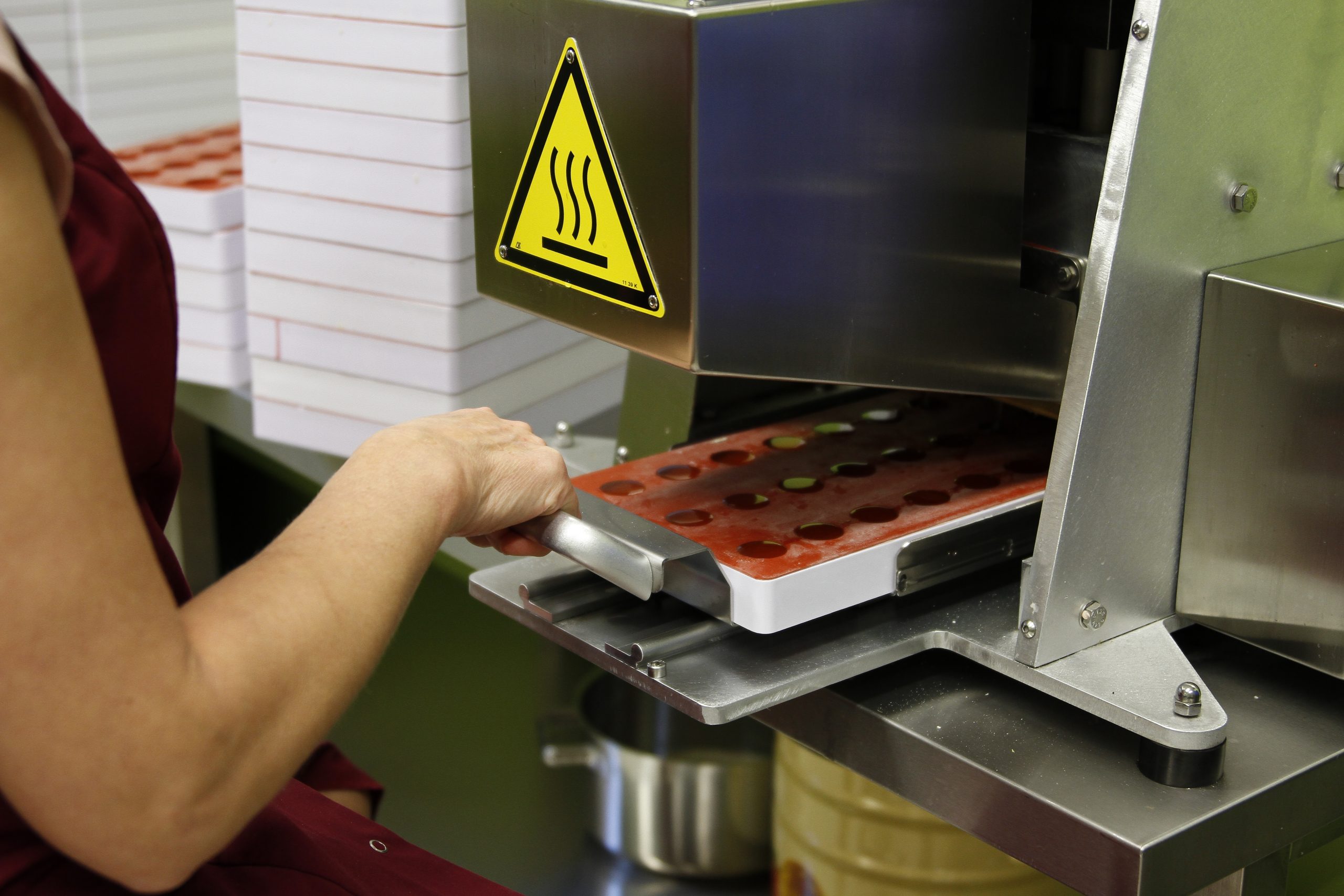
Tackle manufacturing process improvement with Katana
Work smarter, not harder — Katana is cloud inventory software with advanced manufacturing features. Katana makes it easy for you to oversee your entire process from order purchasing to sales, refine the production process, maintain optimal inventory, gain real-time shop floor insights to keep people and products moving, and more.
- Track your inventory in real time through all production phases, from raw materials to finished goods
- Make and refine production plans and schedules that are well-tailored to work with your resource availability and meet your business needs
- Optimize workflows to maximize productivity with the Shop Floor App. This software allows you to track progress and resources, as well as keep your teams aligned and well-supplied to avoid production delays
- Streamline your operations through seamless integration with e-commerce, accounting, reporting, and CRM platforms.
Ready to see Katana in action? Get in touch with us, and let’s see how we can help.
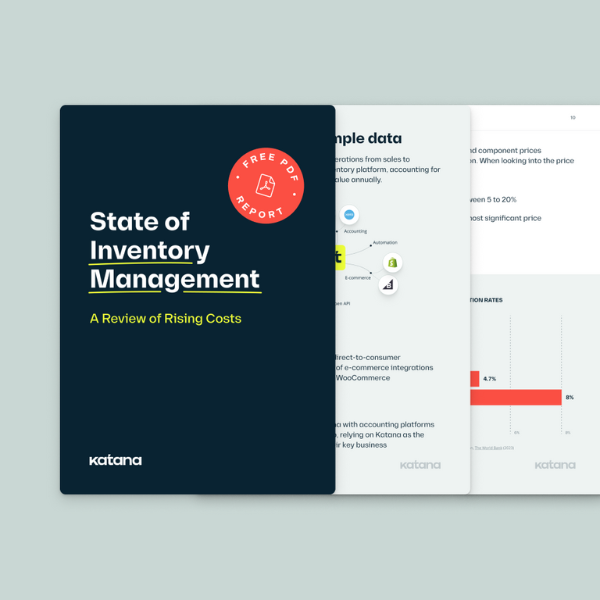
State of Inventory Management
Download a report based on data from real businesses using Katana to explore key trends and actionable insights to help you navigate an uncertain 2024.

Ioana Neamt
Table of contents
Get inventory trends, news, and tips every month
Get visibility over your sales and stock
Wave goodbye to uncertainty by using Katana Cloud Inventory for total inventory control
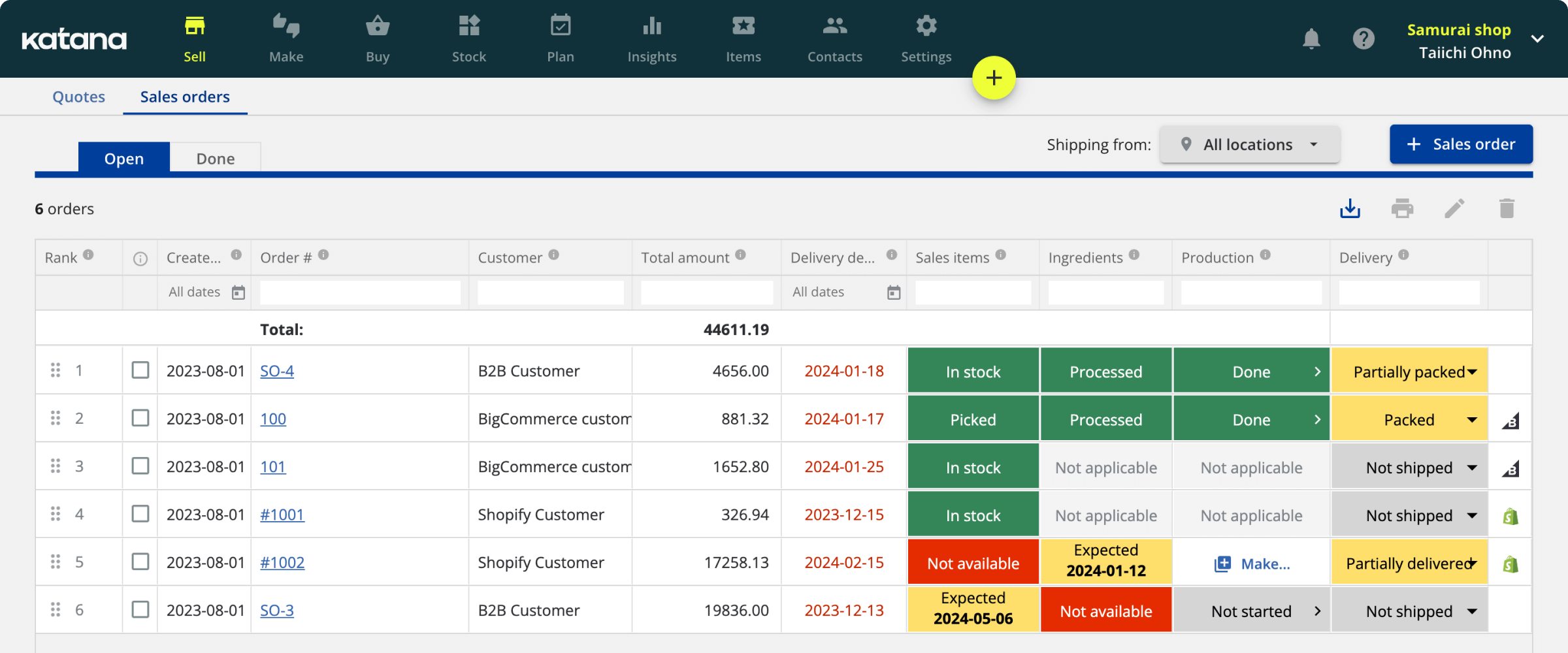