Warehouse bin location best practices

Ioana Neamt

Warehouse bins are the smallest units of storage space within any logistics operation, and as we all know, the devil is in the details. They’re meant to simplify inventory management processes, but to reach their full potential, your warehouse bin storage system must form an integral part of your daily operations. But do you really need such a complex system, and if so, how do you set it up for success and keep it running like a well-oiled machine?
This guide will lead you through the benefits of warehouse bin location management, what it looks like in the flesh, as well as the nitty-gritty of labeling your bins and keeping track of where all your products are stored. But first, the why.
Do I really need warehouse bin location management?
The short answer is yes. The long answer is also yes, unless you run a microbusiness with very slow-moving inventory and you want to keep it that way indefinitely or you want to outsource your warehousing and fulfillment to third-party logistics.
But even if you’re a solo entrepreneur and your logistics center is your dad’s garage, once sales pick up, it’s just a matter of time until chaos creeps in and you end up spending more time looking for misplaced stuff than making money. And then we’re back to the short answer.
The benefits of warehouse bin location management
Without a warehouse location system, retailers usually store products in logical groups or categories, just like your dad used to do in his garage. Everyday tools within reach, heavy stuff on the floor, and junk that will come in handy one day out of sight. But out of sight is out of mind, which is the recipe for lost items, picking errors, delays, and customers asking for the manager.
- Ultimate transparency for all — Storing and finding each item is always logged, making not only everyday work but even onboarding new warehouse staff quick and easy.
- Sharper inventory accuracy — The same log you use for bin location management helps keep track of your inventory in real time, helping prevent stockouts and overstock.
- Faster order fulfillment — Streamlined picking routes mean orders fly out the door on time, keeping customers happy and boosting your service level.
- Fewer picking errors — Misidentifications become the exception instead of the rule. Accurate bin locations lead to accurate picks, minimizing returns and rework.
- Amplified warehouse productivity — Time is money, and time spent searching is money being lost. Accurate bin location logging helps your team get more done in less time.
In a nutshell, then, optimized bin management boosts accuracy and productivity and therefore, your bottom line.
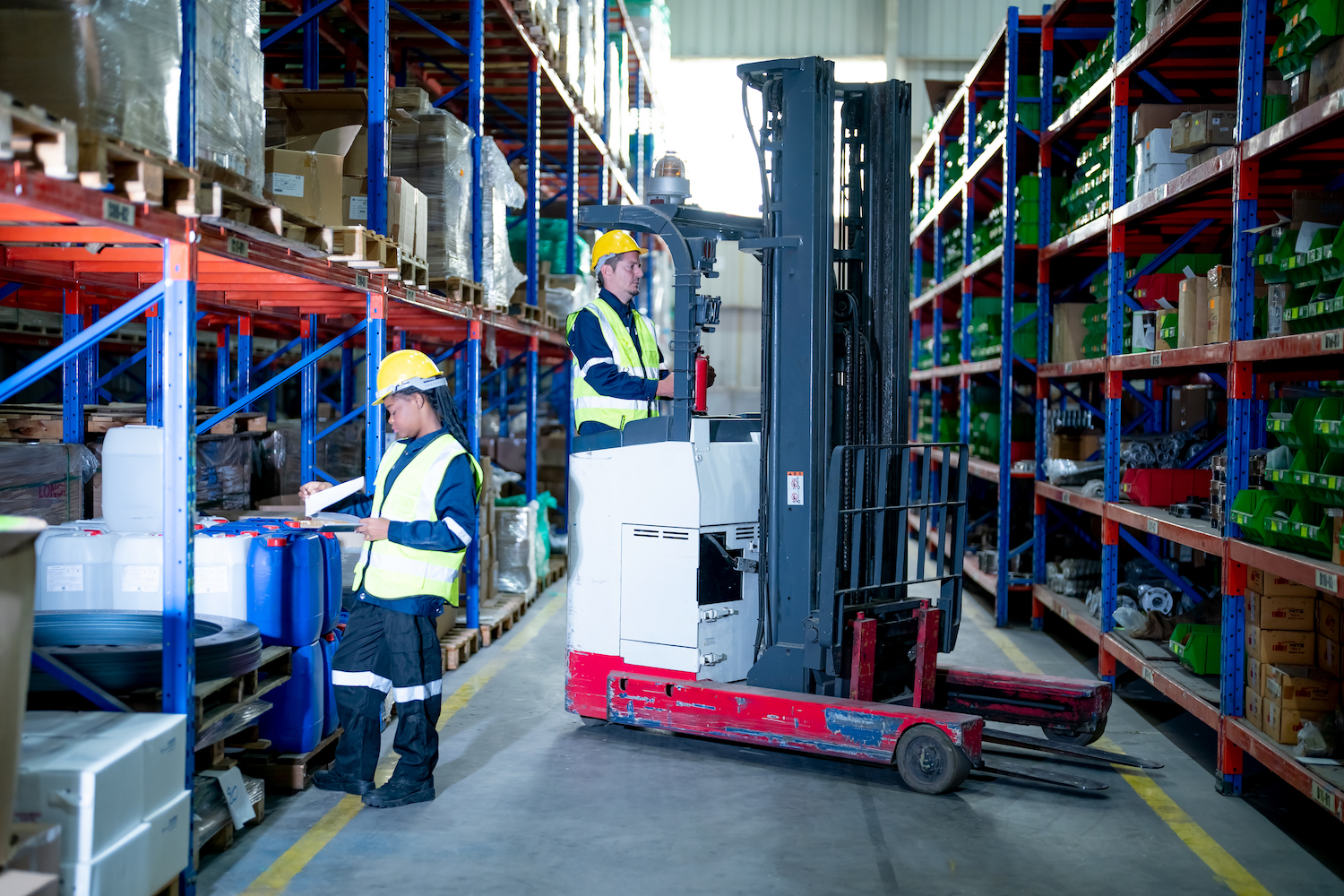
What a warehouse bin location system looks like
Efficient work is impossible without a well-thought-out framework, and the basis of your bin location management system is a logical naming convention for all subunits so that you can assign codes to each bin and make them easy to find. You can have as many layers as you need, but a typical warehouse location format includes 5 levels.
- Imagine your warehouse divided into sections. These are your zones, and each zone groups items based on shared characteristics like size, temperature needs, or activity (e.g., picking, packing).
- Each zone has aisles, these are your staff’s highways. The space between them depends on your product size, picking equipment, and overall flow.
- Aisles intersect, and each intersection represents the end of a rack or bay.
- Once you’re at a rack, you can start thinking in three dimensions. Each shelf or level offers another layer for your inventory.
- Finally, the bin is your smallest storage unit, the treasure chest holding your individual items.
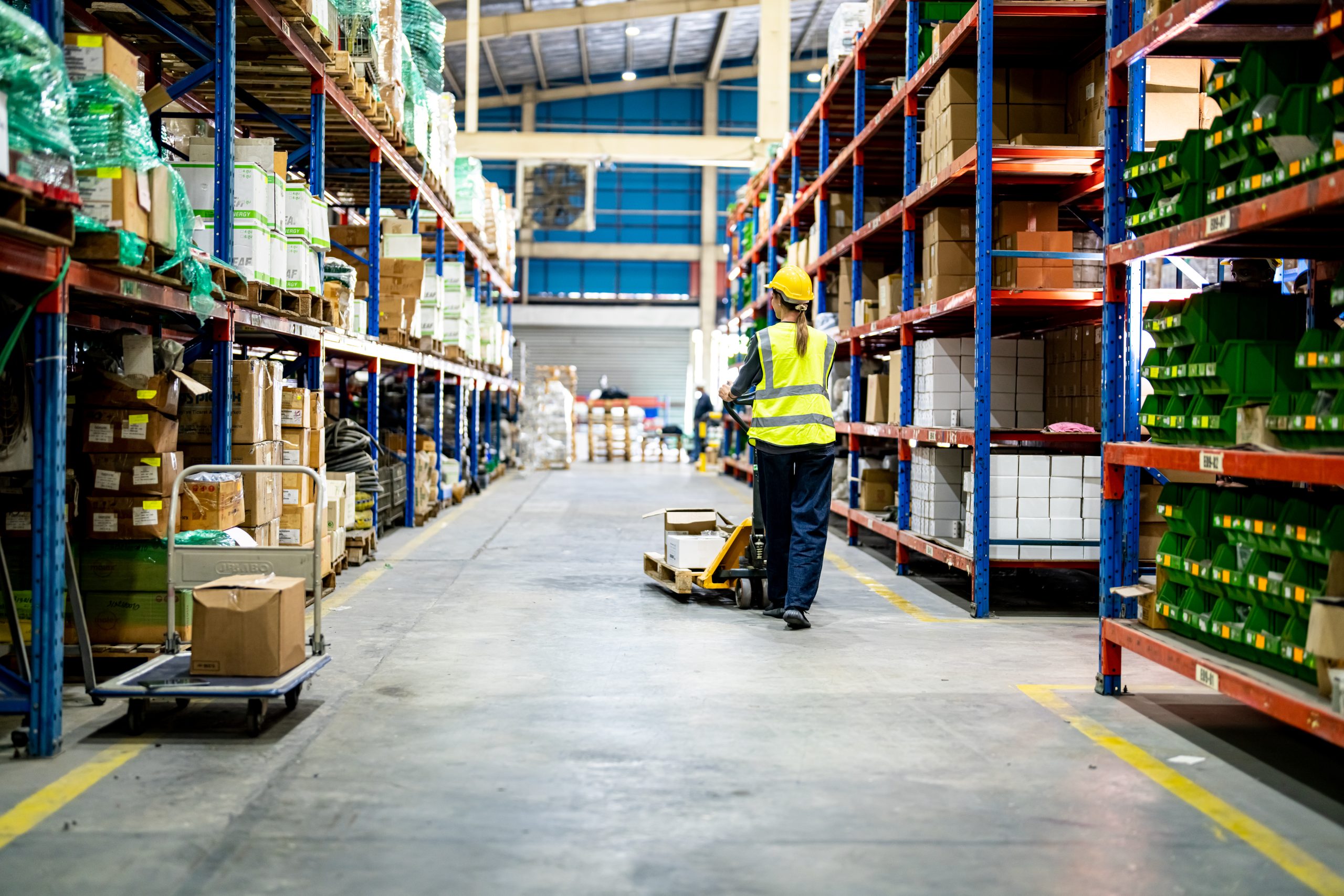
Naming convention — The short code that tells the whole story
There are many ways to come up with codes for each bin, but the simplest is to assign a letter or number to all your storage levels and put them end-to-end, moving from the highest to the lowest level.
Say a customer ordered a six-pack of bottled craft beer. Because it’s perishable (and delicious), but it’s also heavy, fragile, and sensitive to heat, it’s one of your fast-moving items. So, it makes sense to store it in a zone not too far from the packing and loading area but in an aisle that’s not too close to the loading dock, where it might be exposed to fluctuating temperatures and sunlight. It’s also heavy and fragile, so it should be on a lower shelf.
Therefore, zone A, aisle #3, and shelf #1 should be perfect. Since you use a first-in, first-out inventory method for perishable goods, your system will remind you that the oldest batch of craft beer was stored in bin #6, so your code will look like this: A-03-01-06.
These item coordinates are, therefore, unique to that bin. All you have to do is log what you store in there upon receiving it and update the log whenever you take out a six-pack or decide to store a different product in it.
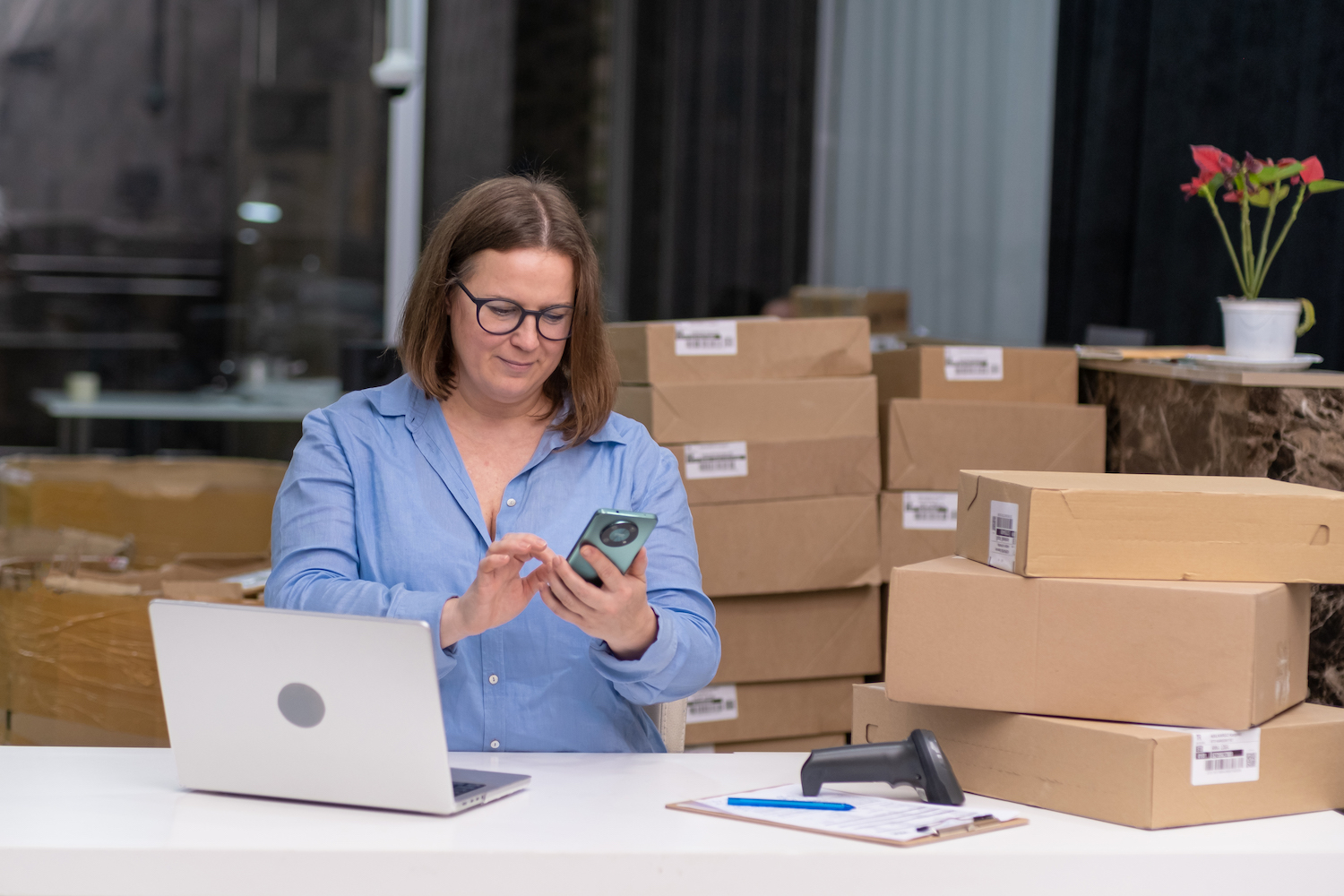
Warehouse bin labeling best practices
- Prioritize clarity — Standardized labeling is the be-all and end-all of bin location systems. Avoid confusion with a clear and consistent system.
- Use electronic tools — Consider barcode or RFID technology for fast scanning and automated data entry, reducing lag and human error.
- Keep the logic simple — Your employees must be able to find items and log any action, even if the barcode gets damaged. Keep the codes as simple as possible.
- Simplify your labels — Labels must be concise, clear, and legible. They must have all the information pickers need and none of what that they don’t.
- Make them eye-catching and durable — Use contrasting colors and place your labels at eye level wherever possible. It’s also a good idea to weatherproof materials so they’re easily visible and can withstand wear and tear.
- Do regular checkups — Inspect labels regularly and replace damaged or faded ones immediately to maintain accuracy.
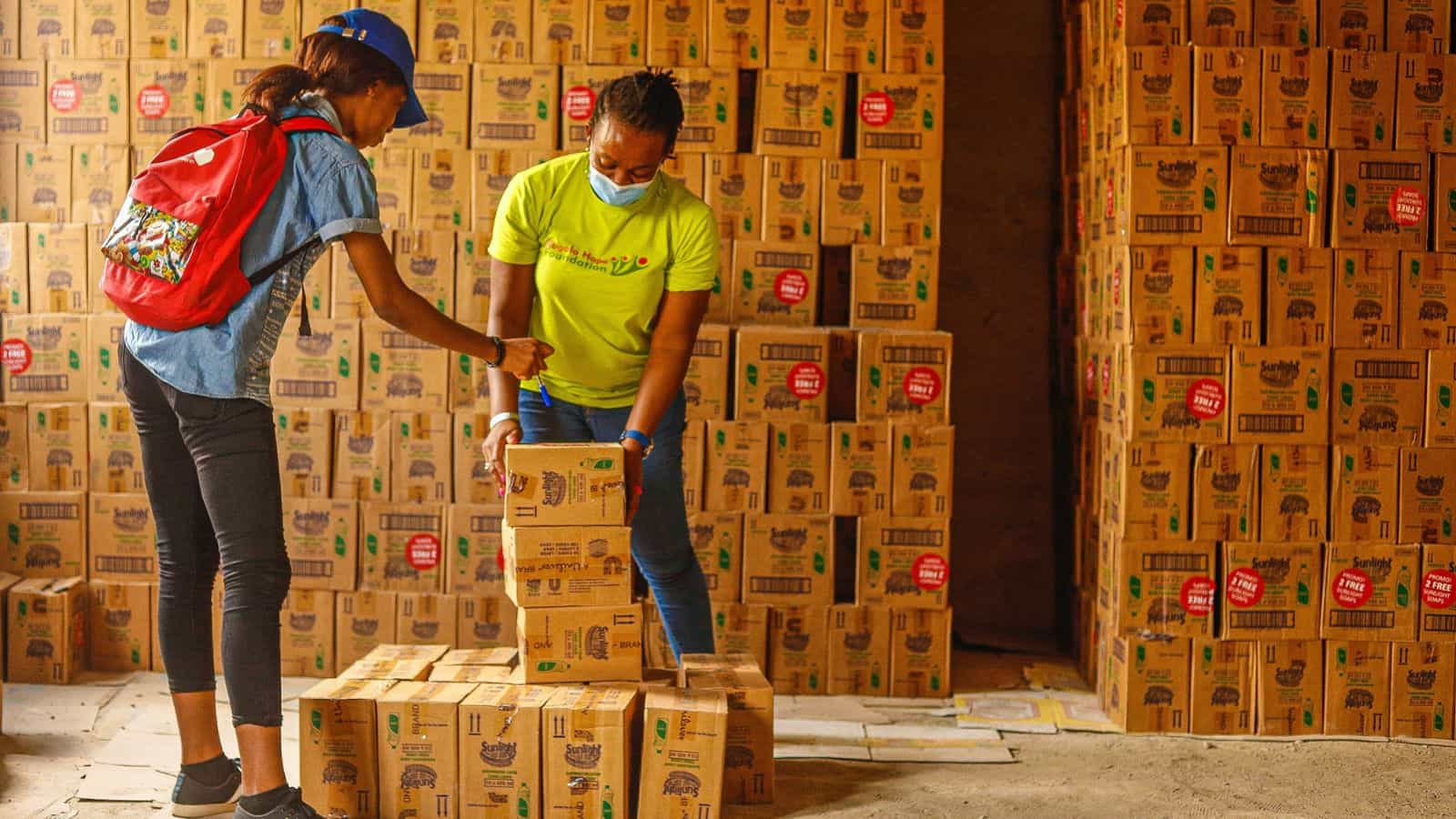
How Katana helps manage your warehouse bin location system
Optimizing your warehouse bin location system is not a one-time effort but an ongoing process. The right inventory management software can help implement the warehouse bin location best practices we discussed above and unlock efficiency, accuracy, and a competitive edge in today’s demanding marketplace.
Katana empowers you to optimize bin locations, print labels, track inventory levels and expiration dates seamlessly using barcodes and serial numbers, and verify your stock with ease in real time. Below are just some of the benefits that await:
- Reduce errors and avoid unnecessary spending — Improved visibility for accurate, efficient receiving and stock counting
- Organize effortlessly — Assign bins, track batches, and find items instantly
- Centralize operations — Print custom labels and manage everything in one place
- Take fulfillment to the next level — Streamline picking and packing with the new warehouse app
Get in touch with us to learn more about Katana and start reaping the rewards!

Ioana Neamt
Table of contents
Get inventory trends, news, and tips every month
Get visibility over your sales and stock
Wave goodbye to uncertainty with Katana Cloud Inventory — AI-powered for total inventory control