Order routing — what, why, and how?
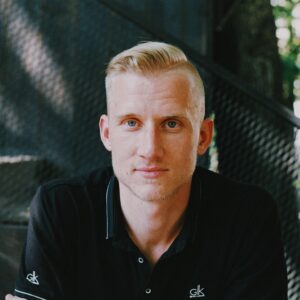
Henry Kivimaa
Efficient order routing is the backbone of high-quality service. The best time to receive an order is now, the next best time is as soon as possible. In this article, we explore how order routing can help you save money while increasing sales and customer satisfaction.

Visualizing the lifecycle of a product, from the warehouse shelves to your doorstep, doesn’t require a very vivid imagination.
The goods are grabbed off a shelf, put on a truck, and eventually, delivered to you. Nothing too complicated, one would guess.
Although the process seems simple and straightforward, there are some nuances that fulfillment teams need to know and follow. Cutting corners can come at a high cost, literally.
What is order routing?
Order routing is the process of ensuring the safe and fast movement of products from the warehouse to the buyer’s doorstep.
It’s essentially a roadmap with written directions and guidelines for the fulfillment team to follow to save resources on the journey and make the shipment process as effective as possible.
Overview of the process
As an example, let’s look at a made-up order.
John Smith needs a new laptop. He purchases one online to save himself the trouble of driving to a store. He receives an email confirming his order, with the order number and estimated delivery date.
The store automatically forwards the order to an order management system (OMS) and starts processing it.
The OMS checks the inventory levels of his selected laptop across all warehouses. Using predefined rules and algorithms, the OMS decides on the best fulfillment center to process the order. This decision is based on factors like inventory levels, John Smith’s location, and transportation options and costs.
The order is forwarded to the suitable fulfillment center, where the warehouse team starts processing it. They pick the laptop from storage, pack it securely, and prepare it for shipping.
The package is handed over to a shipping carrier. John Smith receives an email confirming the shipment of his order along with a tracking number to follow his delivery in real time. The shipping carrier transports the package to John Smith’s house.
After receiving his package, John Smith receives another email confirming the delivery of his goods, thanking him for choosing this online store for his purchase and asking him to leave feedback on the order process.
John Smith is happy with the speedy delivery and his new laptop, so he recommends the store to his friends and keeps it in mind the next time he needs to buy something.
The steps of order routing
Let’s go over order routing and its processes once more, one by one.
- Order placement – John Smith places an order for a laptop
- Order confirmation – John Smith receives an email confirmation
- Order processing – The order is added to an OMS to start processing it
- Inventory check – OMS checks inventory levels
- Routing decision – OMS selects the best fulfillment center
- Order fulfillment – The warehouse team picks, packs, and prepares the laptop for shipping
- Shipping and tracking – A shipment is created and John receives tracking information
- In transit – The shipping carrier transports the package from the fulfillment center to John’s location
- Delivery – The laptop arrives at John’s doorstep
Rules for order routing
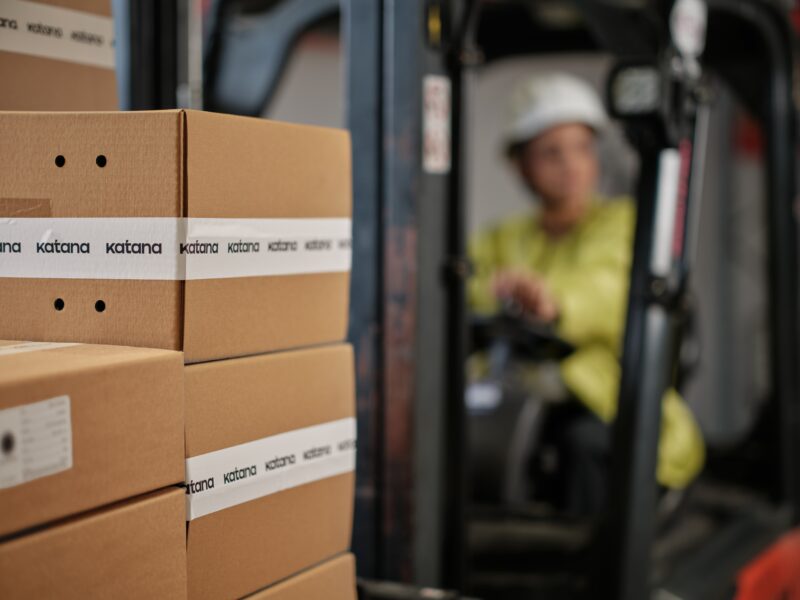
As mentioned above, your OMS uses algorithms and rules to determine the best location and route for order fulfillment.
This means that the system creates a scenario in which you process and ship the order in the most optimal, effective, and cost-efficient way. Let’s look at the the most common routing rules.
Proximity to customer
Prioritizing fulfillment centers closest to the customer’s delivery address helps minimize shipping time and costs, improve delivery speed, and increase customer satisfaction.
Shorter shipping distances also mean fewer carbon emissions during transportation, contributing to a more sustainable supply chain. For environmentally conscious customers, this is a huge green flag.
Inventory availability
Routing orders to locations with sufficient stock of the requested items ensures speedy order fulfillment.
Shipping orders from locations where the items are already available can reduce the risk of delays, backorders, and stockouts. This rule also helps balance inventory across multiple locations, making better use of available and reducing overstock at any specific location.
Cost efficiency
Select fulfillment options that minimize the overall costs of processing and delivering orders.
This practice helps reduce the expenses of shipping, fulfillment center operations, and inventory handling while meeting delivery expectations. In return, lower costs contribute to higher profit margins, allowing you to reinvest in other areas or offer better prices.
You could also offer free shipping, which would give you a competitive edge over your competitors.
Operational capacity
Distributing orders based on the workload and available resources, fulfillment centers can prevent bottlenecks and delays.
By leveraging underutilized centers, you can ensure that none of your locations are overwhelmed and that all teams can work at maximum efficiency. Avoiding overload also acts as a quality guarantee, as all locations can still maintain high standards in their operations.
Service level agreements (SLAs)
Agree on standards and commitments regarding the quality and time of service and stick to them.
This can include metrics such as delivery lead time, order accuracy, and customer support responsiveness. These metrics are a competitive advantage, as customers are more likely to choose businesses that guarantee good quality and timely delivery.
SLAs show accountability and benchmarks for performance, which will help you measure and improve your operational efficiency. If the set standards aren’t met, responsible teams will have to better their processes, and customers may be entitled to compensation.
Types of order routing systems
As with all business operations, software solutions have been created to speed up the process, automate mundane tasks, and use computers to do all the calculations and routing for you.
Let’s go over the most common techniques used for routing orders.
1. Geographic order routing system
Geographic routing prioritizes the customer’s location and proximity to a fulfillment center as the primary routing rule. This system is ideal for businesses with multiple fulfillment centers scattered across different locations.
While this technique doesn’t always consider other routing rules and can be less effective for those with unevenly distributed inventory, it is relatively simple to implement and manage and a great way to reduce transportation costs.
2. Inventory-based order routing system
As the name suggests, the main rule for routing orders in this system is the availability of products in fulfillment centers. Its goal is to prevent stockouts and backorders by fulfilling orders from locations with the highest stock levels.
Inventory-based routing may not be the most cost-efficient solution, but it helps balance stock levels across all your locations and reduces the risk of delays due to inventory shortage.
3. Capacity-based order routing system
Routing orders based on capacity means prioritizing the operational power of fulfillment centers. This system is preferred by businesses that focus on their overall operational efficiency.
Although capacity-based routing doesn’t prioritize cost and is more dependent on real-time data, it does help you balance workload across multiple fulfillment centers, preventing bottlenecks and improving overall efficiency in all your locations.
4. Time-sensitive order routing system
When the main goal is to cut down on delivery time, it’s called time-sensitive order routing. This system ensures that urgent orders or express deliveries are prioritized and fulfilled in the fastest available location.
Speedy delivery often comes with higher shipping costs and requires immaculate tracking of shipments, but it’s a clear advantage over competitors and a great way to guarantee customer satisfaction.
5. Rule-based order routing system
Rule-based systems use one or more predetermined rules to determine the best fulfillment center for an order. These can include any of the previously mentioned routing rules.
This system is relatively static and does not offer the flexibility of other systems. However, it is the easiest one to set up and manage and can be customized to determine the rules best suited to your business needs.
6. Hybrid order routing system
Hybrid systems combine multiple routing techniques and approaches, creating a more flexible and optimized solution for each business. This can mean balancing multiple factors or simply using the most suitable elements of each system.
Hybrid routing is more complex and requires advanced technology to manage, but it makes up for the difficult implementation by being highly flexible and adaptable. It’s suitable for larger operations, allowing them to optimize for multiple rules at the same time.
7. Algorithmic order routing system
Algorithmic systems use advanced algorithms and optimization to make the best routing decisions. They are designed to adjust automatically based on real-time data and considering multiple criteria.
It is the most complex routing system, requiring sophisticated technology and expertise to implement and manage. This makes the implementation process quite expensive and time-consuming.
The upside is the flexibility and dynamic routing it offers its users. An algorithmic system can optimize for multiple factors simultaneously and use machine learning to improve its algorithms over time.
Businesses to look up to
It’s always useful to learn from the best of the best, so let’s take a quick look at industry leaders with excellent order-routing strategies.
Amazon
The retail giant uses algorithmic routing to optimize their shipping cost, speed, and operational capacity.
With more than 175 fulfillment centers worldwide, routing is a crucial element of their operations. The multitude of locations brings the products closer to the customers but also complicates the routing process even more.
Amazon uses advanced machine learning algorithms to predict demand and make routing decisions based on current conditions as well as historical data. Their systems heavily rely on continuous data analysis, which helps them quickly adapt to changing conditions such as demand fluctuations, inventory levels, or logistics disruptions.
And it’s obviously working, as they efficiently handle massive volumes of orders every day, even during peak holiday periods, and can offer same-day or next-day delivery to many shoppers.
Walmart
Walmart utilizes a combination of geographic and inventory-based routing. This combo ensures efficient and timely delivery from its distribution centers and stores.
Orders are routed to the nearest distribution center or store with enough ordered items in stock. Even for online orders, Walmart often uses its physical stores as pick-up locations to use their store inventory to speed up order fulfillment.
This also simplifies the return process for buyers who, upon receipt, realize that the ordered goods aren’t a good fit or don’t meet their expectations.
Zara
Zara uses inventory and capacity-based routing to balance stock levels across its locations, ensuring high availability and fast replenishment.
The apparel brand centralizes all its inventory and operations, forecasts demand at individual stores as well as regions, and routes orders based on the capacity of fulfillment centers. Its biggest priority is speedy and dynamic inventory movements to keep stores always stocked with the latest trends while avoiding overstocking.
These practices ensure that Zara always runs on optimal resources and that customers always have access to the most popular products.
3 tips for better order routing
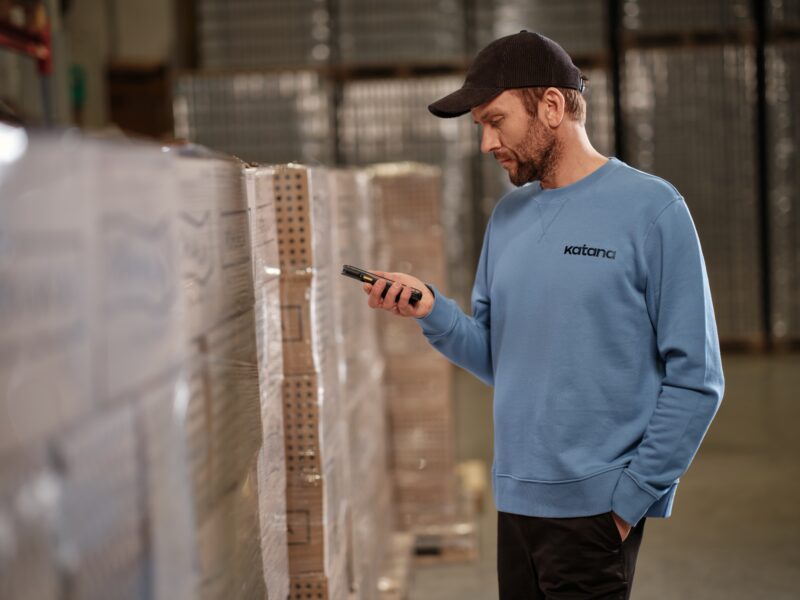
Every business is different, which means that there are no one-size-fits-all solutions. However, some techniques and hacks can help streamline your order-routing process, freeing up time for more critical tasks.
1. Barcode scanning
The adoption of barcode scanning in logistics in the 1980s and 1990s drastically improved inventory management and order accuracy.
The fear of complicated implementation has planted a seed of doubt into the minds of many business operators, essentially slowing down their potential success and growth. However, with the right software and technology, barcode implementation doesn’t have to be a headache but an investment.
Barcode scanning is an easy way to improve efficiency and accuracy in your operations, eliminating the risk of manual errors. It also speeds up your inventory transactions by automatically updating inventory levels upon receiving or shipping goods.
Many software solutions are already equipped to generate different types of barcodes for your products, import your existing labels, and integrate them into your inventory and order management software.
2. AI and machine learning
Aside from algorithms, there are other ways that computers can impress us with their advanced ability to speed up order routing.
AI-driven software allows you to analyze large datasets and make real-time decisions in the blink of an eye. Using additional machine learning models, you can continue to improve your routing efficiency based on past and potential future data.
AI can also immediately consider all possible shipping options and select the most cost-effective way to fulfill orders. Machine learning allows you to go through all these options, create routes, and select carriers to help you reduce shipping costs without compromising delivery times.
Machine learning can also analyze customer behavior and data, provide personalized recommendations, build marketing strategies, and thereby increase sales.
3. Warehouse layout
One way to optimize fulfillment is to optimize the fulfillment centers and warehouses themselves.
A strategic warehouse layout helps workers locate items more quickly, speeding up fulfillment and saving your workers unnecessary steps throughout the day. Logical layouts also facilitate better coordination between teams and processes such as picking, packing, and shipping.
One easy way of improvement is placing popular items in easily accessible locations like eye level or the front of the warehouse. If you know these items move often, make it easier for your staff to pick them up. Similar to this strategy, you could also employ the ABC inventory method, categorizing your items in categories based on importance and popularity.
Remember to continuously seek improvement by following your most important key performance indicators (KPIs), like pick time or order accuracy. These metrics can give you a clear overview of how effectively your warehouse operates and what could be improved. Also, be open to feedback from the warehouse staff — they are the people most affected by the layout on a daily basis, making their suggestions the most valuable.
Warehouse mistakes to avoid
Warehousing isn’t an easy task, and we don’t want you to learn it the hard way. So here are 11 warehouse mistakes, what they could cost you, and how to avoid them altogether.
Use cases for routing orders
The essence of order routing should be clear to you now, but each use case is unique.
The practices and processes vary based on the goals and priorities of a business and what it wishes to focus on in order fulfillment. Whether it’s maximizing speed, minimizing costs, or enhancing customer satisfaction — the order routing approach must be tailored to the business.
Ecommerce platforms
Ecommerce platforms like Shopify or BigCommerce need to fulfill a high volume of orders and ensure quick delivery to the buyer while keeping shipping costs minimal.
Order routing lets them direct orders to the nearest fulfillment center with available stock. It also takes into consideration factors like inventory levels, customer location, and shipping costs to find the optimal location for order fulfillment.
Retail chains
Big retail chains, like Walmart mentioned above, must juggle inventory across not only physical stores but also online channels and ensure products are available wherever customers choose to shop.
For them, the best solution is to integrate in-store inventory with online orders. Many have implemented a “ship from store” model, meaning that orders are routed to the nearest retail location with the ordered goods in stock. This guarantees a quick delivery time for the buyer, often within the same day.
Manufacturers
The biggest challenge for manufacturers lies in syncing production with order fulfillment, minimizing inventory holding costs, and meeting delivery deadlines.
One solution is to implement order routing systems that integrate with supply chain and manufacturing software. Another is to route orders based on production schedules, inventory levels, and delivery requirements.
Often, manufacturers who are also involved in selling their products opt for the just-in-time model to reduce inventory costs and prevent production delays.
Food delivery
Food delivery is the most time-critical service, with delivery times not calculated in days or hours but often just minutes.
Drivers have to be allocated to orders in real time to ensure that food is delivered to customers while it’s still hot and fresh. Food delivery services like DoorDash and Uber Eats use algorithms to assign deliveries to the closest available driver while taking into consideration factors like traffic, driver availability, and the location of the restaurant, customer, and driver.
Pharmaceuticals
The pharmaceutical industry requires strict compliance with regulations and standards.
Precise order routing ensures that medications are delivered to the right location on time, using the necessary precautions and correct means of transportation. A more rigid order routing system like rule-based routing is a great fit here, as there are requirements that can’t be compromised. Factors such as inventory levels, regulations, and the critical nature of medications should be the top priorities. After these are optimized, other rules can be considered.
Order routing in Katana
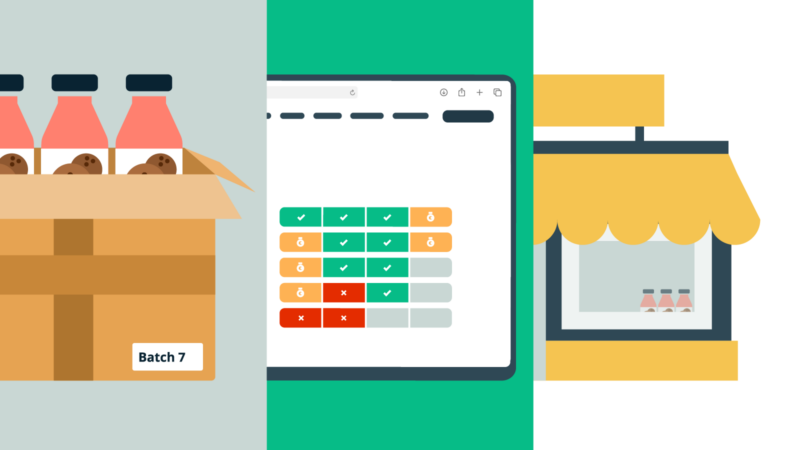
The best way to pave the road to a struggle-free order routing journey is to employ a reliable order management system.
Katana is a powerful cloud platform designed to optimize inventory, order, and production management. Here are some of the most beneficial features that Katana offers to streamline your order routing and other business-critical processes.
Real-time inventory management
Katana provides live visibility into your inventory across all your locations.
Keep stock levels up to date and route orders efficiently based on real-time inventory data. Prevent stockouts and overstocking by assigning orders to the best-equipped fulfillment centers.
Multichannel order management
Integrate Katana with your sales channels, including ecommerce platforms, retail stores, and wholesale.
Katana centralizes your order management and makes it easier to track and fulfill orders from multiple sources. A unified view of all your orders allows for more efficient routing and fulfillment and gives you the data necessary to find areas of improvement in your routing process.
Production management
Katana offers specialized production planning and scheduling tools that can easily be integrated with order management features.
Align your production with order fulfillment needs and ensure timely delivery to your customers. Optimize your supply chain by routing orders to production facilities with the necessary resources to meet delivery deadlines.
Demand planning and forecasting
Predict customer demands with Katana’s advanced planning and forecasting tools.
Katana helps you plan for future inventory needs by analyzing current sales data and past trends. Stay stocked, avoid delivery delays, and streamline your supply chain according to customer behavior.
Custom workflows
Use integrations to build a workspace that meets the specific requirements of your business.
Some tasks that Katana offers integrations for include:
- Accounting tools like QuickBooks Online and Xero
- Ecommerce like Shopify, WooCommerce, and BigCommerce
- Custom workflows using Katana’s open API
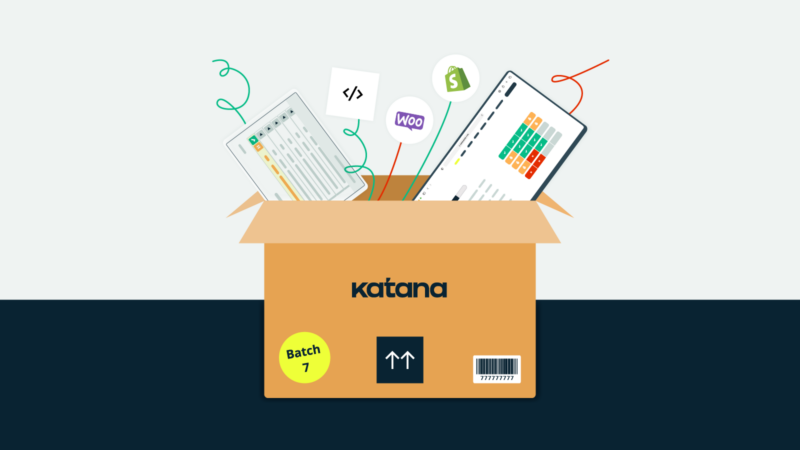
So, there you have it – order routing, what it is, and how it works.
If you feel like an all-encompassing software solution such as Katana could benefit your business, whether you need it to simplify your order routing or any other business aspect, then don’t be a stranger. Sign up for a free demo call and discuss your needs with one of our experts.
Or, if you still have some doubts, take an interactive tour of the platform and see for yourself how intuitive and user-friendly Katana really is. Until next time!
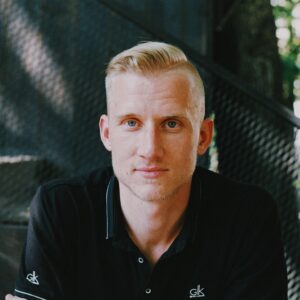
Henry Kivimaa
Table of contents
Get inventory trends, news, and tips every month
Get visibility over your sales and stock
Wave goodbye to uncertainty with Katana Cloud Inventory — AI-powered for total inventory control