How to calculate the cost of goods manufactured
Goods manufactured refer to products produced by a company or manufacturer through a series of processes, using raw materials, components, and labor, to create finished products for consumers or other businesses.
The cost of goods manufactured (COGM) is an important metric, especially for manufacturing businesses, because it can affect profitability, which is the ultimate goal of any business.
What is the cost of goods manufactured (COGM)?
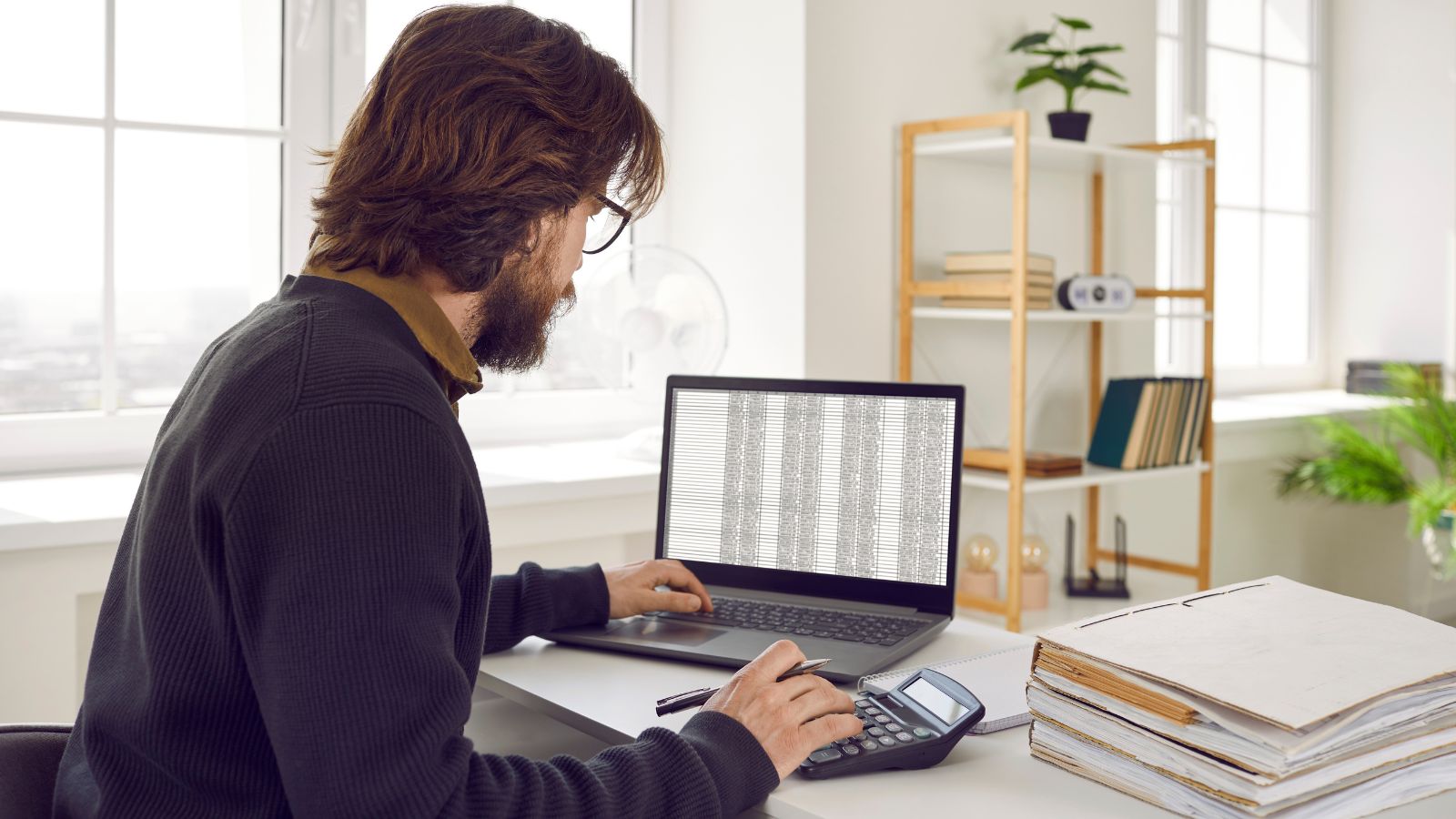
The cost of goods manufactured (COGM) refers to all the costs involved in producing a product, including direct labor, indirect labor, raw materials, and overhead costs.
COGM is a useful accounting metric because it can be used to measure the performance of production and manufacturing costs with target costs. It determines the profit margin and other costs related to manufacturing or selling products, so knowing this number is crucial for any business owner or manager.
How to calculate the cost of goods manufactured?
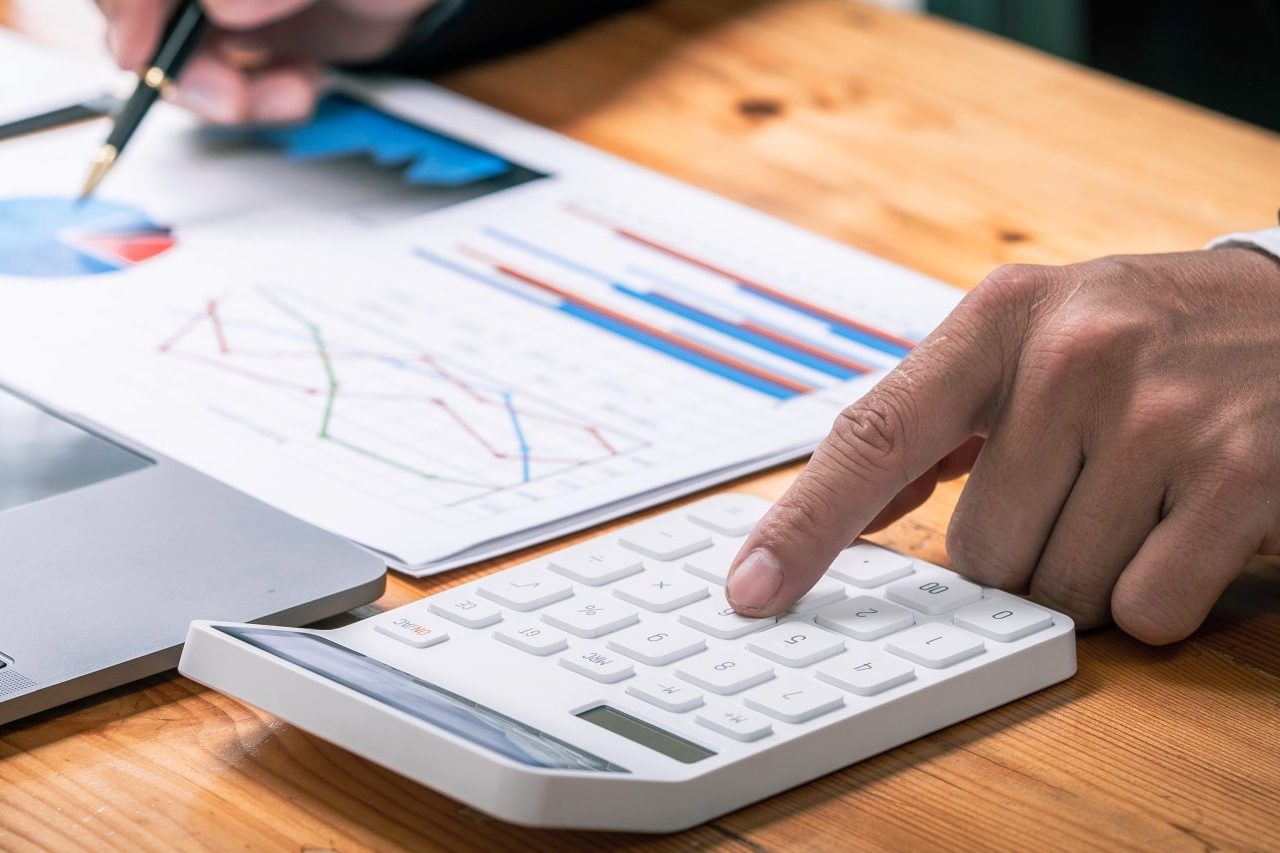
Figuring out how to find the cost of goods manufactured, you’ll want to break it down into three components:
- Direct material costs
- Direct labor costs
- Overhead costs
Materials cost money when you buy them, so you know exactly how much is being used.
Labor is easier because it’s paid for regularly as salaries each month.
Overhead costs can be harder to track because they may not be as directly related to the production process as materials or labor are.
This can include examples such as:
- Utilities — Electricity used in running machines, insurance paid on machinery, freight charges incurred, etc.
- Factory and warehouse rent
- Depreciation of machines (or equipment)
The cost of goods manufactured formula
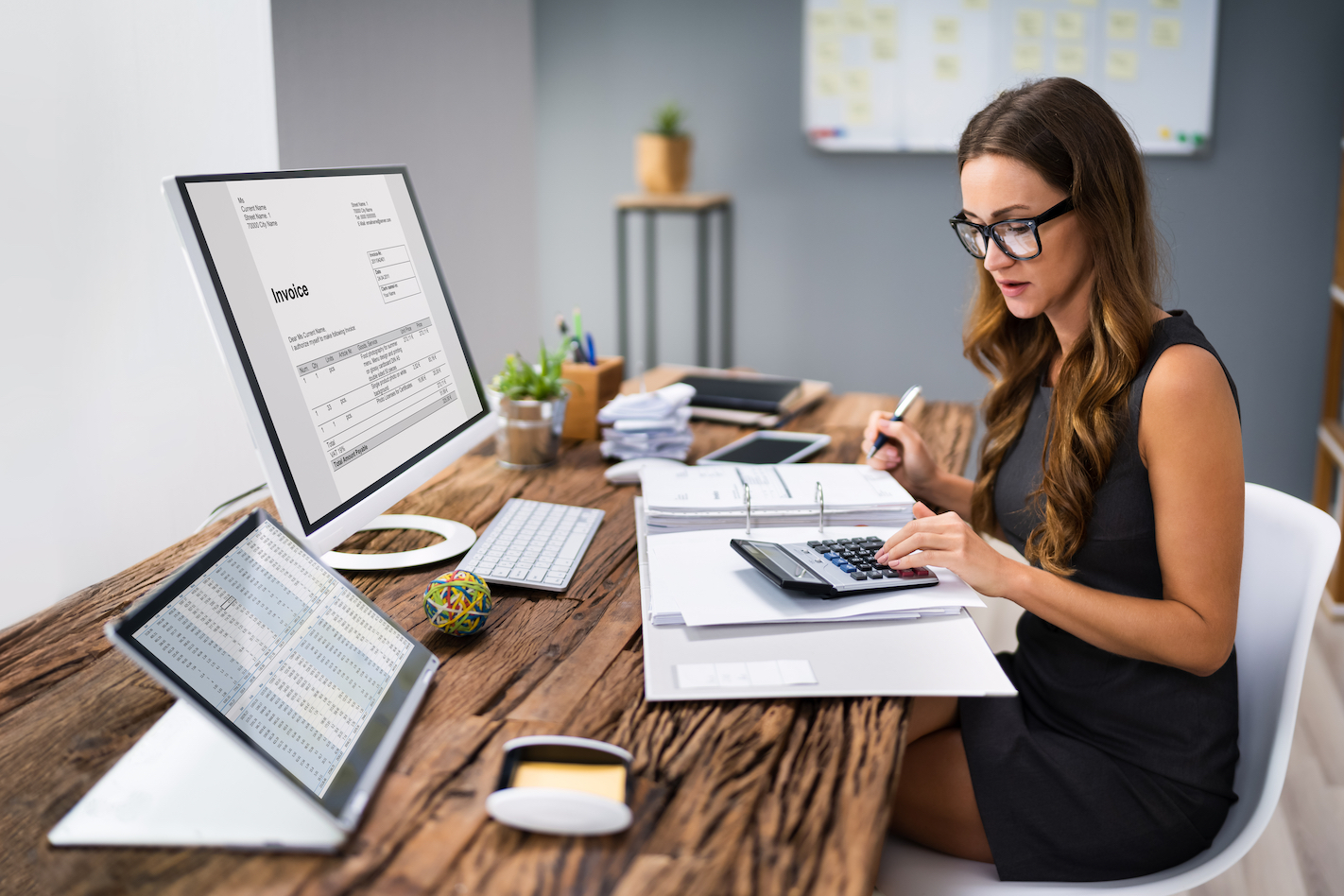
The cost of goods manufactured can easily be calculated with the following formula:
COGM = Beginning inventory + Costs incurred during production — Ending inventory
You add the value of raw materials and work-in-progress inventory at the start of the period to all the costs of making products during the period and subtract the value of inventory at the end of the period.
The resulting answer is the cost of goods manufactured, which represents the total amount paid for direct materials and labor costs associated with manufacturing your products. This number can be used to compare actual and planned manufacturing costs.
The COGM formula can be calculated manually or automatically using cloud manufacturing software like Katana.
Why is understanding COGM important?
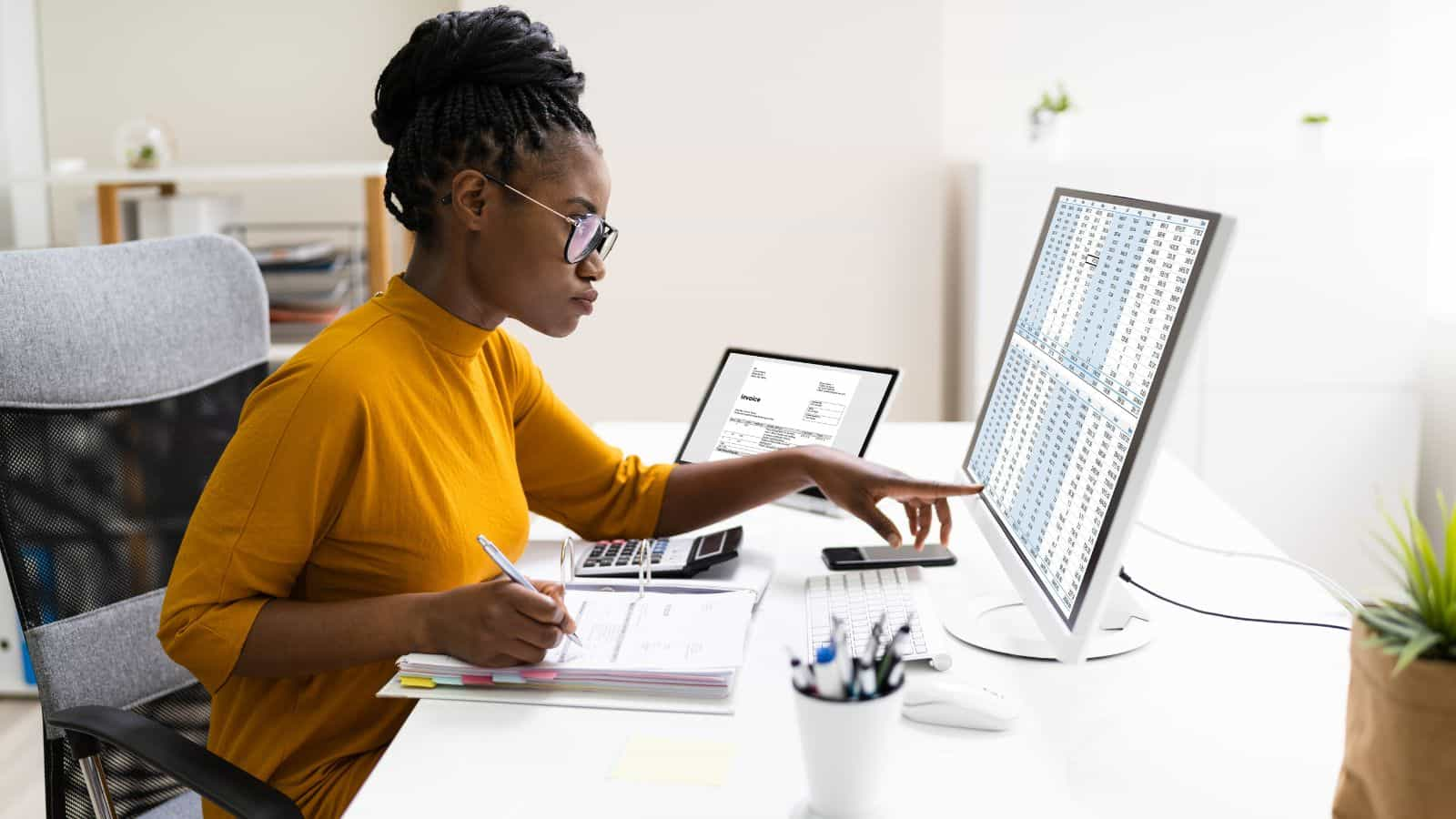
As a manufacturer, your survival depends on profitability.
Your profitability depends on identifying all sources of costs, and your inventory is the core part of your costs. You can stay on top of your costs by understanding, measuring, and tracking COGM.
Without knowing COGM, it’s almost impossible for a manufacturer to reduce manufacturing costs and improve profitability.
Financial analysts and business managers use COGM to determine whether a company’s products are profitable enough to continue selling or if they need to change elements of the supply chain to lower those costs.
An example of calculating COGM
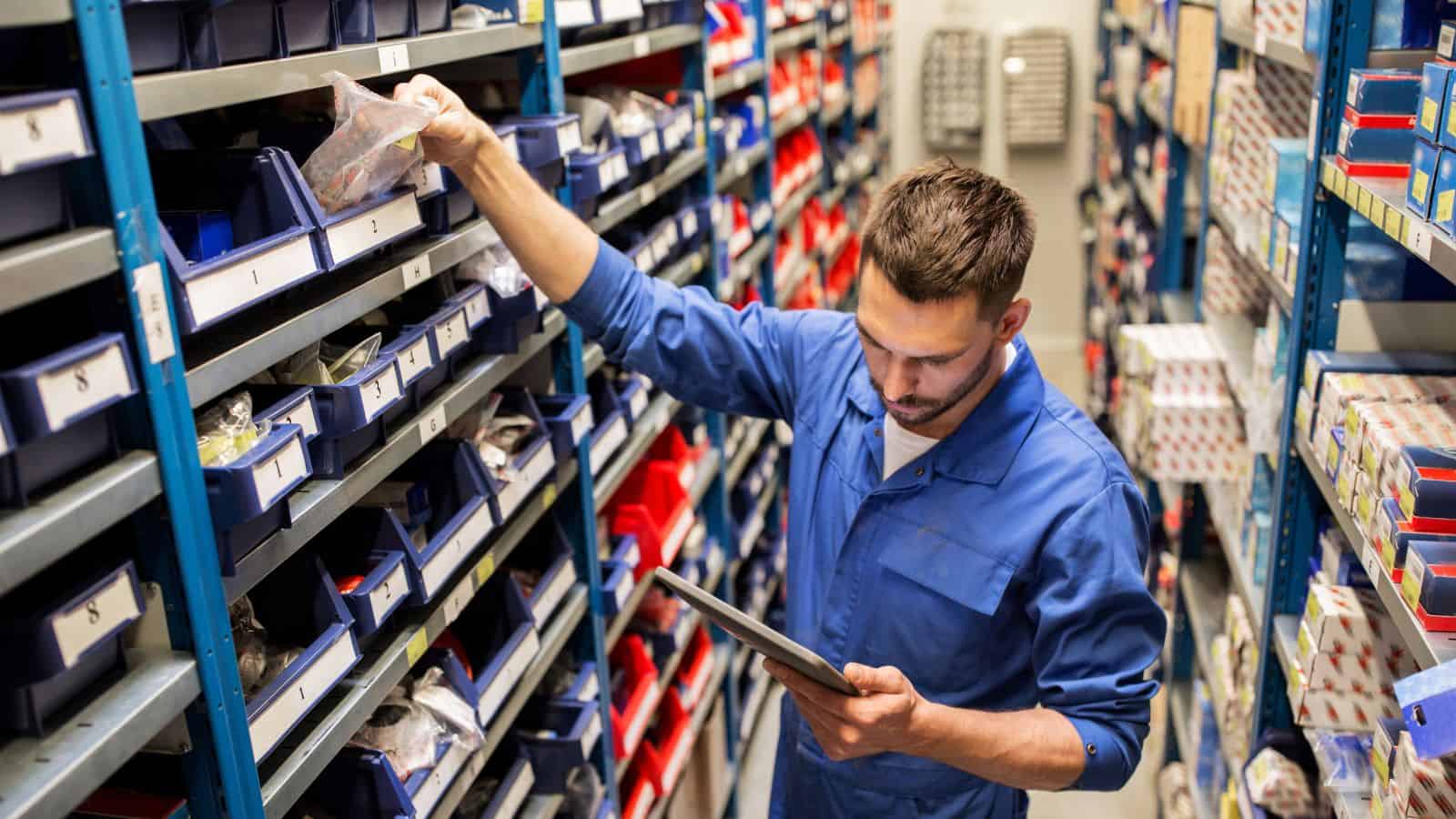
To perform the COGM calculation, identify the three important calculation parts.
Beginning inventory
You need to determine the number of finished goods on hand at the end of the previous month. Next, you add all raw materials purchased during that same period. Finally, you subtract any ending work-in-progress (WIP).
Beginning Inventory = Finished goods + Purchases — Ending WIP
Costs incurred during production
Here is a list of the different production costs to help you perform your calculations:
- Material costs — Track during the purchase
- Labor costs — Track at the time of invoice payment
- Depreciation of machines — This cost can vary widely, depending on how long your company has been in business and what kind of equipment you have. For example, if your company has been around for 30 years and uses equipment purchased back then, deprecation may be an increasing expense.
- Factory rent — Depends entirely upon location and other factors specific to each situation
- Utilities — Electricity bills are easily determined based on kilowatt usage over time. Still, heating/air conditioning bills can be trickier because sometimes businesses use their generators instead of paying someone else for heat/cooling services.
Ending inventory
Since you already have the beginning inventory, subtract that amount from the total sales for the period to get your ending inventory.
This is a simplified example:
Ending inventory = Beginning inventory + Purchases — Total sales
Now that you have the beginning inventory, ending inventory, and costs incurred during production, you can calculate the COGM using the COGM equation:
COGM = Beginning inventory + Costs incurred during production — Ending inventory
COGM vs. COGS
COGM is the total cost of making products for sale.
The cost of goods sold (COGS) is the actual expenses related to producing those products.
COGM does not include marketing or distribution costs — it only includes direct labor, materials, and factory overhead costs associated with producing finished goods inventory. On the other hand, COGS is an accounting term used to describe the total amount spent on producing a product before it’s sold.
For example, if you purchase $1000 worth of raw materials but don’t sell them until six months later, you would recognize that $1000 expense in your books as the cost of goods sold.
COGM vs. TMC
Total manufacturing cost (TMC) is the total cost of all the materials and labor that go into making products for sale.
While COGM calculations include:
- Direct material costs
- Indirect material costs
- Direct labor costs
- Factory overhead (indirect labor and fixed expenses),
TMC calculations only include direct material costs because they do not include indirect material or factory overhead expenses.
Save time and money by automating your processes
Get automatic manufacturing cost calculations with Katana, including live inventory management, real-time production planning, and more essential manufacturing features.
Using cloud manufacturing software for COGM calculation and tracking
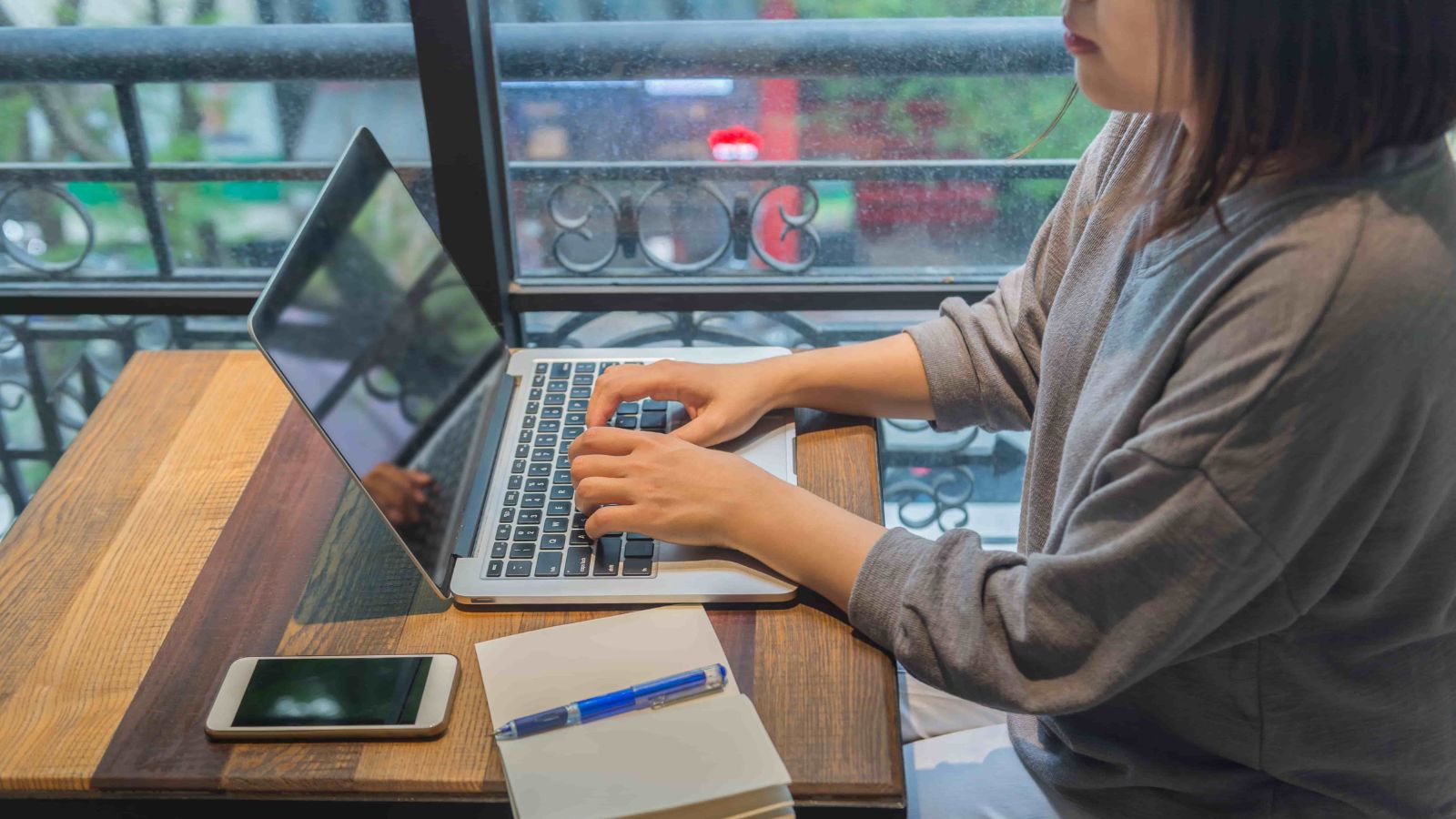
As a manufacturer, you need to have a solid system for calculating COGM.
If you don’t, you could lose money or even go out of business because of miscalculations and inaccurate information. Luckily, some tools make it easy to calculate COGM and keep track of the results.
Cloud manufacturing software such as Katana allows businesses to use data from their operations to calculate COGM and other vital figures like inventory value and sales revenue.
Cloud manufacturing systems can help track COGM by keeping track of raw materials as they pass through each stage of production and into the finished goods inventory.
This means that when it comes to managing your manufacturing accounting, all those numbers will already be there and ready to go.
Keeping your finances and bookkeeping up to date
COGM is a significant concern for companies that produce goods.
If your COGM is higher than your selling price, then you aren’t making a profit on each item sold — and this can be bad news for your business. If you don’t know how much COGM you have, you won’t be able to make informed decisions about pricing or product development.
Making sense of COGM and having efficient systems to measure and track them is critical to your survival as a manufacturing business.
Cost of goods manufactured FAQ:
Does COGS include the cost of goods manufactured?
Yes, the cost of goods sold typically includes the cost of goods manufactured.
COGS is a financial accounting measure representing the direct costs of producing and selling goods.
It includes costs such as:
- Materials used
- Direct labor
- Factory overheads
- Utilities
- Equipment depreciation
COGM, on the other hand, is a gauge of the manufacturing costs during a specific time period. This includes costs for labor, materials, and manufacturing overhead.
What is not included in COGS?
Certain expenses are not included in the cost of goods sold, while these costs are still associated with producing and selling goods.
Here are some examples of expenses that are not included in COGS:
- Selling, general, and administrative expenses (SG&A) — These costs, such as salaries and marketing costs, are essential for the general running of the business even though they are not directly tied to the production process.
- Research and development (R&D) expenses — R&D expenses are costs incurred to develop new products or improve existing products. These costs are not included in COGS because they do not relate to the production of goods.
- Interest and other financing costs — These expenses relate to the cost of borrowing money and are not directly related to production.
- Income taxes — Income taxes are not included in COGS because they are not a direct cost of producing or selling goods.
In summary, COGS includes only the direct costs related to the production and sale of goods and excludes other expenses that aren’t directly related to the production process.
What is an example of a COGM?
Here’s an example of how to calculate COGM:
Let’s say a manufacturer produces 10,000 units of a product during a month, and the following costs were incurred during the production process:
- Raw materials used: $30,000
- Direct labor cost: $20,000
- Factory overheads: $10,000
To calculate the COGM, you would add up these costs to get the total cost of goods manufactured:
COGM = Raw materials used + Direct labor cost + Factory overheads
COGM = $30,000 + $20,000 + $10,000 COGM = $60,000
So in this example, the cost of goods manufactured is $60,000 for the month.
Remember that this is merely an illustration and that the precise COGM costs may change based on the business and the product being produced. The COGM only calculates the cost of goods sold for a certain period.
What are indirect materials in COGM?
Indirect materials are supplies used in the production process, but that cannot be directly linked to a particular good or production unit. Indirect materials are often included in the factory overhead costs in the cost of goods manufactured (COGM) calculation.
Examples of indirect materials may include items such as:
- Machine lubricants
- Cleaning supplies
- Small tools used in manufacturing
Still, their usage is not directly tied to a specific product. These materials do not directly impact the final product but are necessary to keep the manufacturing process running smoothly.
Direct materials, such as steel used to construct automobile frames or fabric in clothing manufacturing, may be easily linked to a particular product or unit of production.
In COGM, the computation of factory overheads and indirect production expenses can often include:
- Rent
- Utilities
- Depreciation
- Indirect materials, if there are any
The predetermined overhead rate, determined based on the predicted overhead expenses and the anticipated number of units to be produced, is used to assign factory overheads to each production unit.
Is COGM on the income statement?
COGM is not typically reported on the income statement.
However, COGS is usually reported on the income statement.
To determine COGS, start with the beginning finished goods inventory, add the cost of the products produced throughout the period, and then deduct the ending finished goods inventory. The result is the price of the goods sold over the specified period.
So while COGM is not reported on the income statement, it is used to calculate COGS, which is included in the income statement.
Table of contents
Accounting Guide
Get visibility over your sales and stock
Wave goodbye to uncertainty by using Katana Cloud Inventory for total inventory control
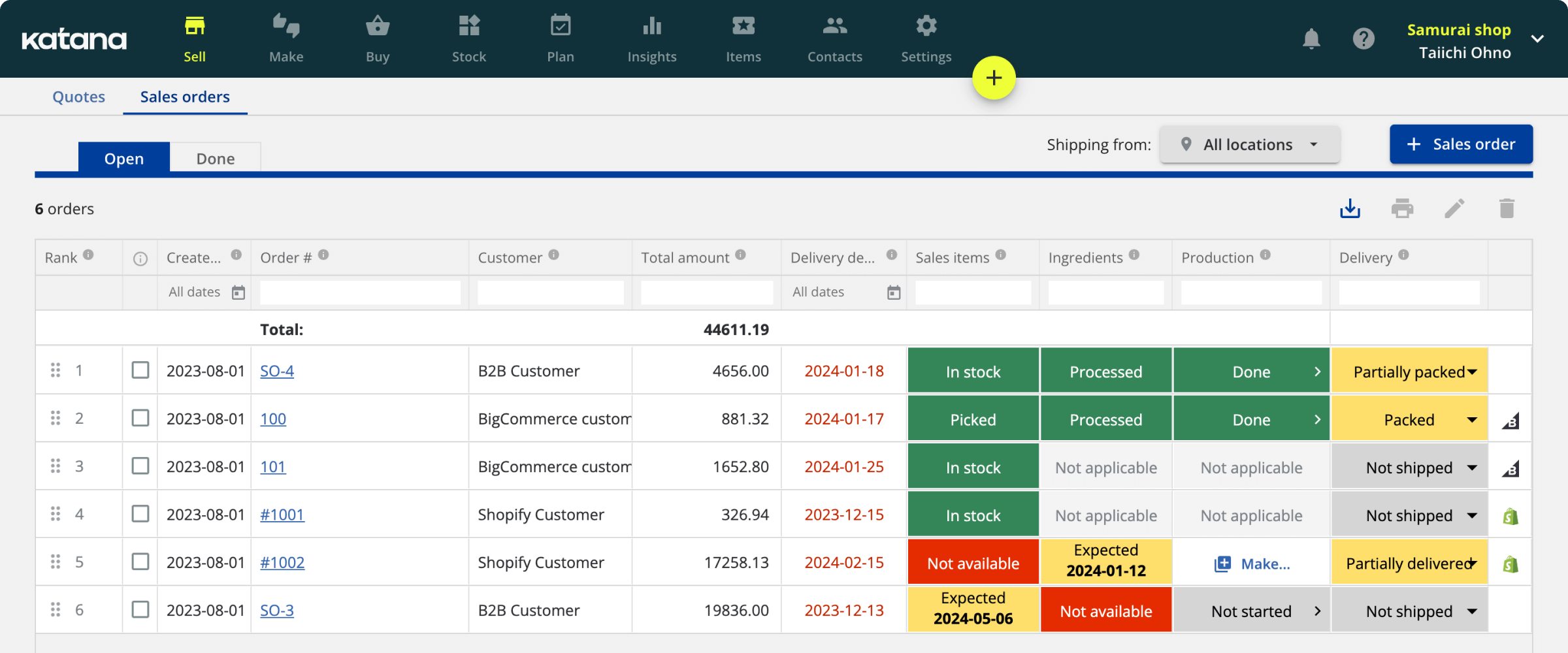