Engineer to order (ETO): Finding a unique fit
Engineer to order is a way of manufacturing where a product is designed, produced and delivered once an order is made. Read all about the ETO workflow below.
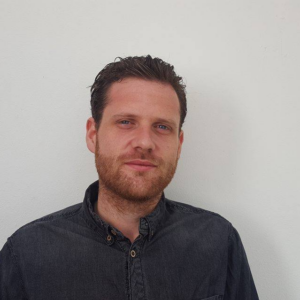
James Humphreys
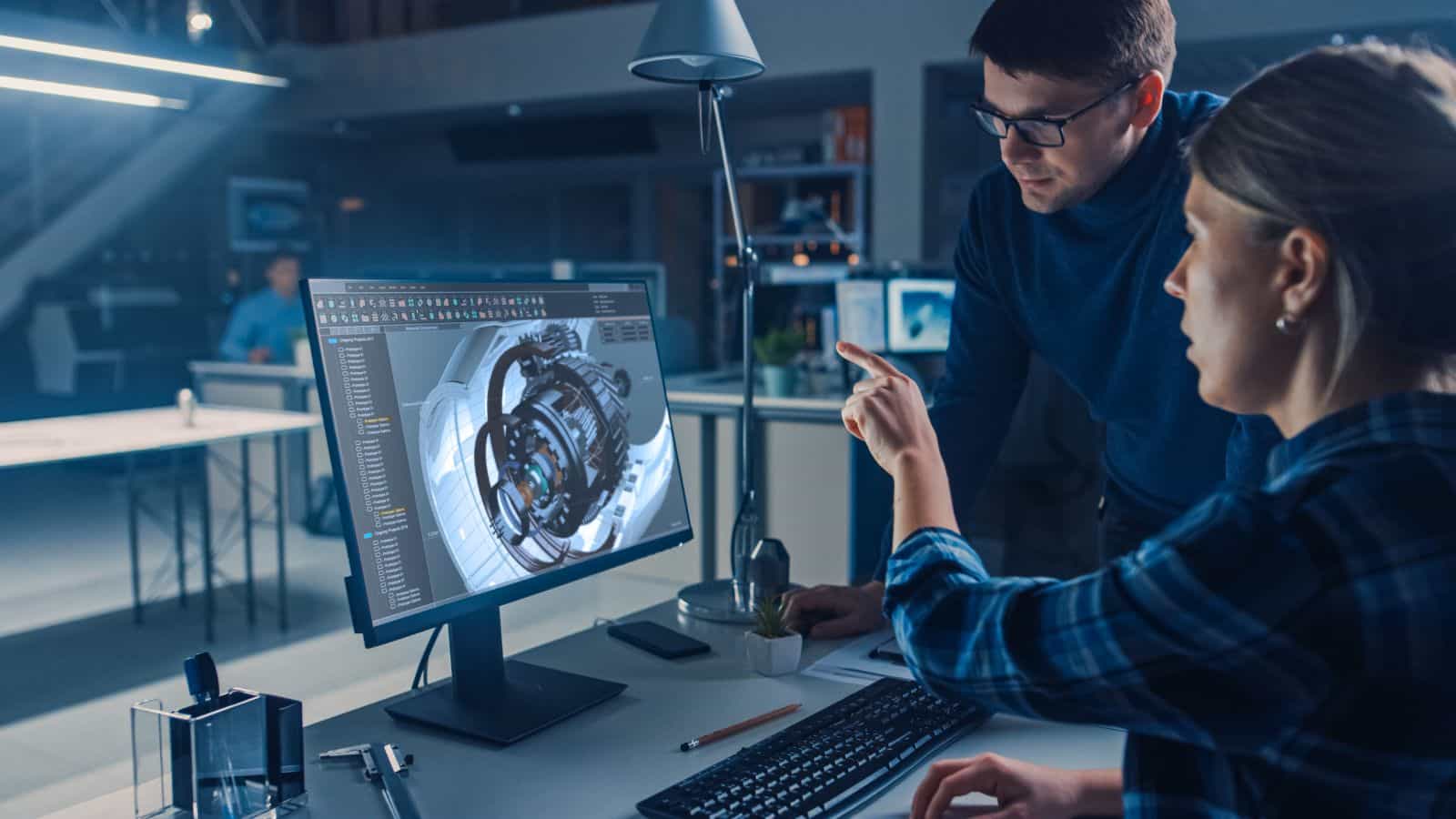
Generally, manufacturing companies design a product meant to solve a problem faced by many customers worldwide.
They optimize production processes to lower costs, trying to secure the largest market possible. While this may be the typical business model, it is not the only one. In contrast, an engineer to order (ETO) company designs unique solutions for specific customer needs.
This can be a one-off product or a small batch of products produced to the same specification. The key characteristic is that each ETO product is different from the next and usually cannot be produced without significant engineering input.
Below, we will take a closer look at the ETO process, how it differs from traditional manufacturing techniques, some of the most famous examples, and how to implement it in your own business using software.
Engineer to order made easy
Katana’s cloud inventory platform gives businesses the tools to manage different inventory types, so you can support make-to-stock and engineer-to-order workflows simultaneously.
What is engineer to order?
Engineer to order manufacturing is a process in which products are conceived, designed, and produced to meet the specific requirements of individual customers. In other words, each product is unique, and the designing process begins after the customer has placed an order.
While this may be a new concept for some, it is quite similar to some more familiar items, like the way custom cars or bespoke items like suits are made.
In both cases, the customer provides specifications, and the manufacturer is able to customize products that meet those requirements specifically without preconceived notions of what the customer wants.
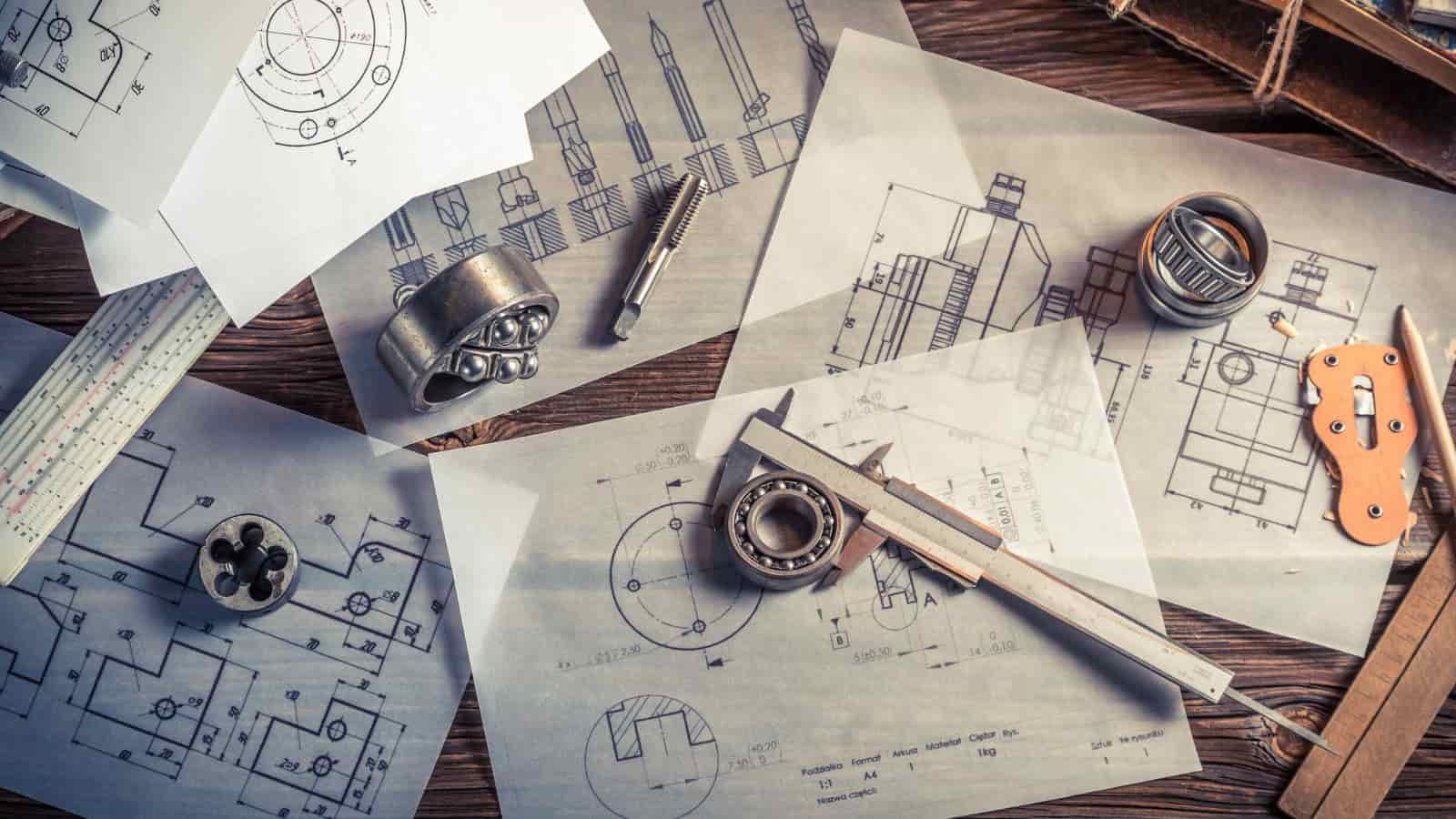
Engineer to order vs make to order
Engineer to order and make to order are often conflated, but there is a big distinction between the two.
In make-to-order manufacturing, a fixed design is created before any customer orders are placed. The manufacturer then produces the product to the same specification for each customer that places an order.
With an engineer to order manufacturing solution, on the other hand, the product is not designed until after a customer places an order. This means that each product produced is unique and tailored specifically to the customer’s requirements.
It is important to note that engineer to order does not necessarily mean that the finished product is made completely from scratch each time.
In many cases, ETO manufacturers will have a base product or platform that can be modified to meet the customer’s specific needs.
This modular approach helps reduce lead times and costs while providing a fully customized solution for complex products.
Engineer to order vs configure to order
Similarly, in a configure-to-order system, the customer chooses from a range of existing design options that have been pre-determined by the manufacturer.
The options might be things like size, color, or material, and they are configured into a product that is then produced to meet the customer’s specifications.
In an engineer to order system, on the other hand, the customer’s requirements are used to generate a completely new product design. This means that the options available to the customer are not pre-determined, and any pre-existing constraints do not restrict the final product.
Engineer to order examples
It may be difficult to visualize how this process can be used in manufacturing. Let’s take a look at some examples.
Frontline Fire & Rescue
One of the most common engineer to order product examples is emergency vehicles, especially fire trucks.
While some standard fire trucks are used in most jurisdictions, each one still needs to be customized to meet the specific needs of the fire department it will be serving. For example, in terms of size, features, and capacity, a fire truck designed for use in a rural area will be very different from one meant for use in an urban area.
This process begins with a consultation between the fire department and the manufacturer to understand their specific needs. Once these have been established, the team gets to work engineering and manufacturing a truck that meets those requirements.
Frontline Fire & Rescue, for instance, has created custom hazmat incident control trailers, underground fire pumps, and mobile command units, among other things.
APAC HVAC
Heating, ventilation, and air conditioning (HVAC) systems are also among the best engineer to order success stories.
While there are some standard HVAC units available on the market, most commercial buildings require a custom system to function properly. This is because each building is different in terms of size, layout, and climate control needs.
APAC HVAC is one of these engineer to order companies and has created custom systems for a wide variety of clients, including hospitals, office buildings, and factories.
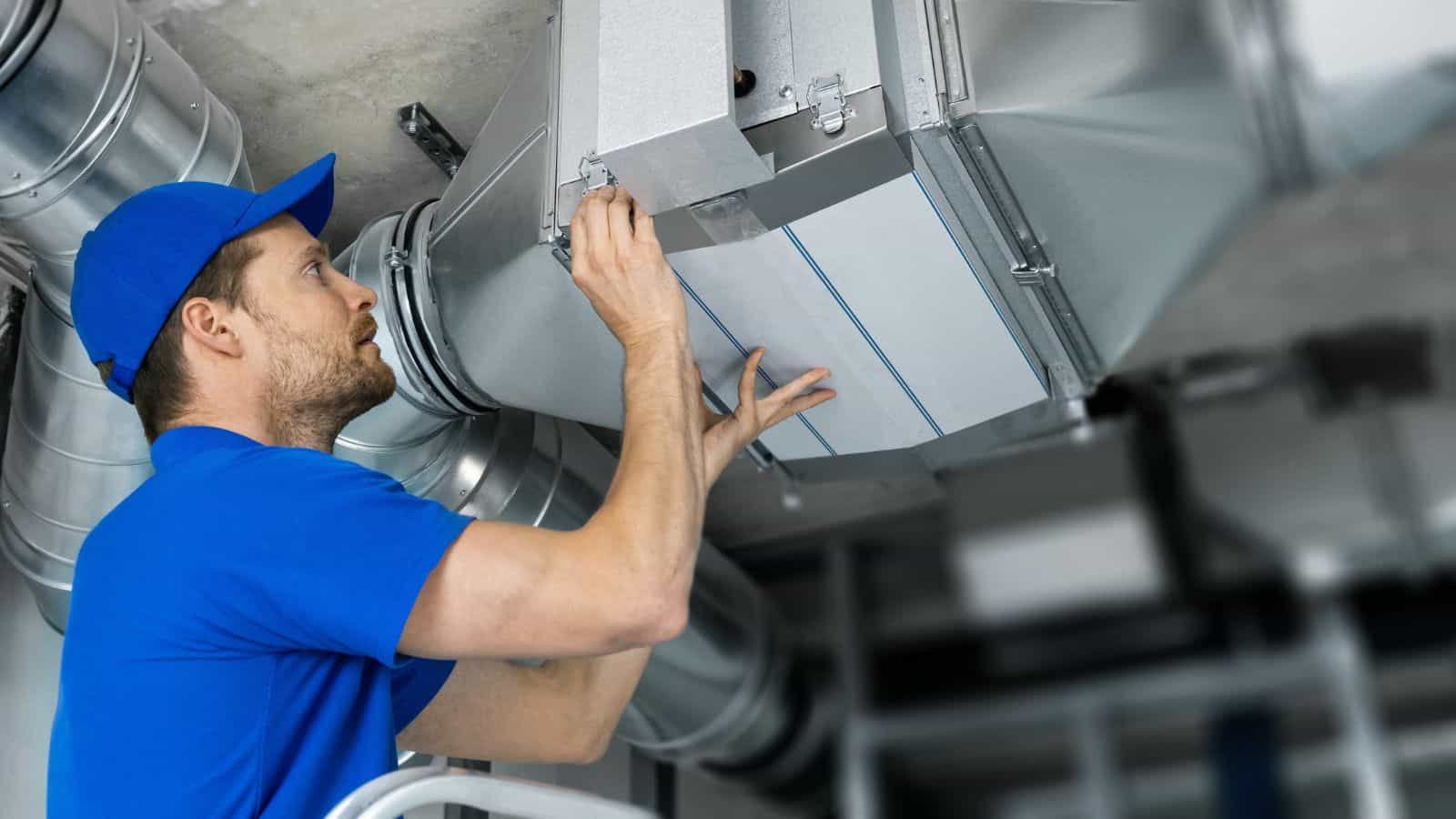
Amiga Engineering
Defense and aerospace manufacturing represents perhaps the widest range of engineer to order process examples, as each project is generally one-of-a-kind.
Amiga Engineering creates completely bespoke designs of 3D-printed parts for the aerospace, defense, and medical industries, among others.
For each customer, Amiga engineers will consider the specific materials, loads, and operating conditions that the part will need to endure. They will then create a design that meets those requirements using 3D CAD automation software.
Once the design is complete, and customer approval has been received, it is sent to production, where it is printed using one of Amiga’s additive manufacturing processes.
This example highlights how ETO processes can be used in conjunction with new technologies like 3D printing to create parts that would otherwise be impossible to manufacture using traditional techniques and give companies a competitive advantage.
Katana’s cloud inventory software
Join thousands of companies using Katana to manage their entire business, from inventory to purchases to production and beyond.
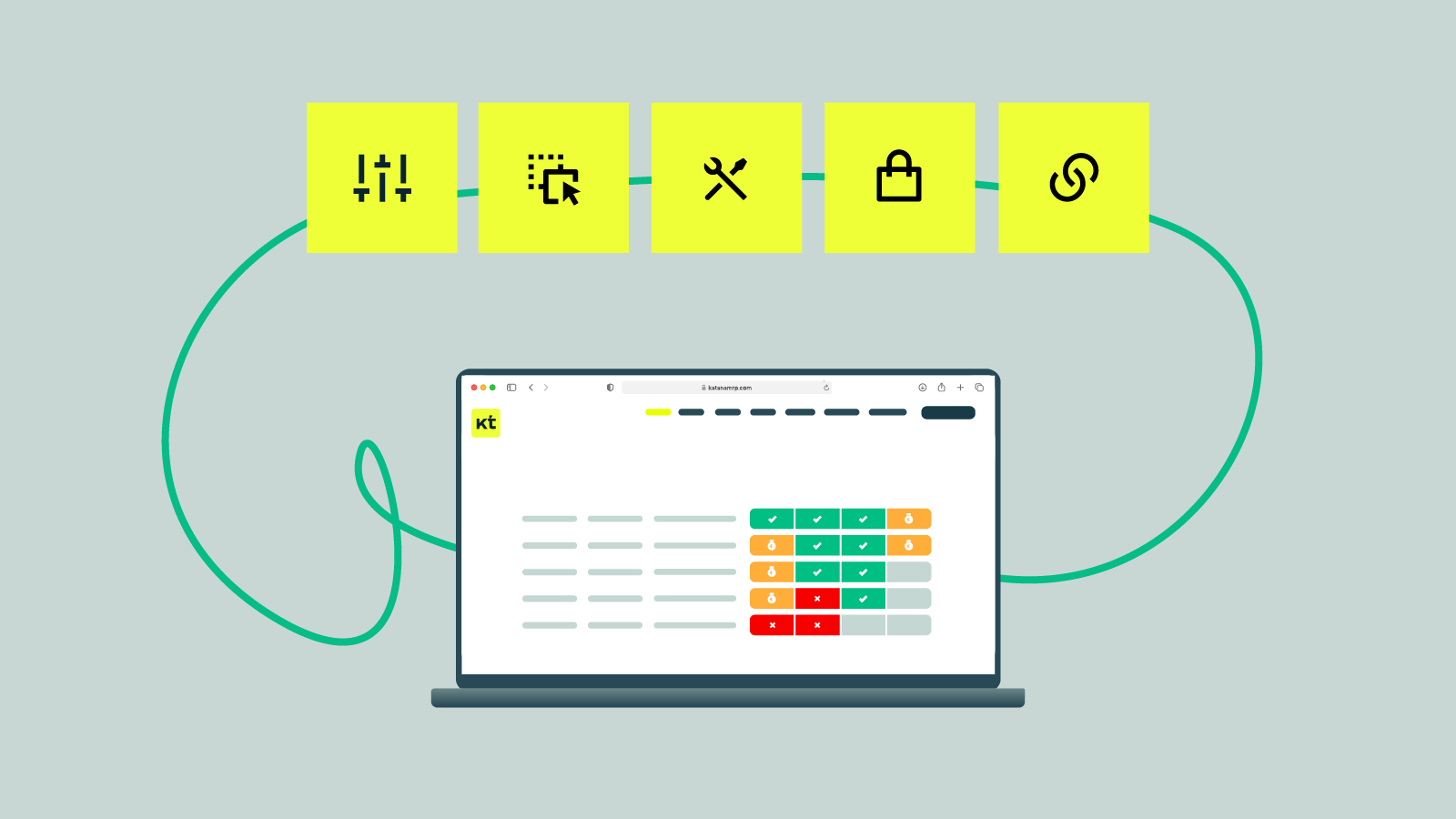
How Katana can help you manage an engineer to order workflow
With Katana, you can manage your ETO process from start to finish.
The engineer to order ERP software gives you visibility and control over every aspect of your business, from quoting and designing straight through to production and delivery.
Katana also helps you to streamline your operations, reducing the time and cost of production. Flexible manufacturing scheduling tools ensure that each job is scheduled according to its requirements, meaning that there are no delays or disruptions in the workshop.
What’s more, Katanais fully scalable, so you can grow your business without having to worry about outgrowing your software.
If you’re looking for engineer to order manufacturing software that will help you to optimize your operations and increase efficiency, then Katana is a perfect choice.
Get a demo to see how Katana’s ERP system can help you streamline your engineer to order process flow.
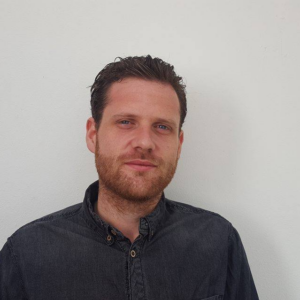
James Humphreys
Table of contents
Get inventory trends, news, and tips every month
Get visibility over your sales and stock
Wave goodbye to uncertainty by using Katana Cloud Inventory for total inventory control
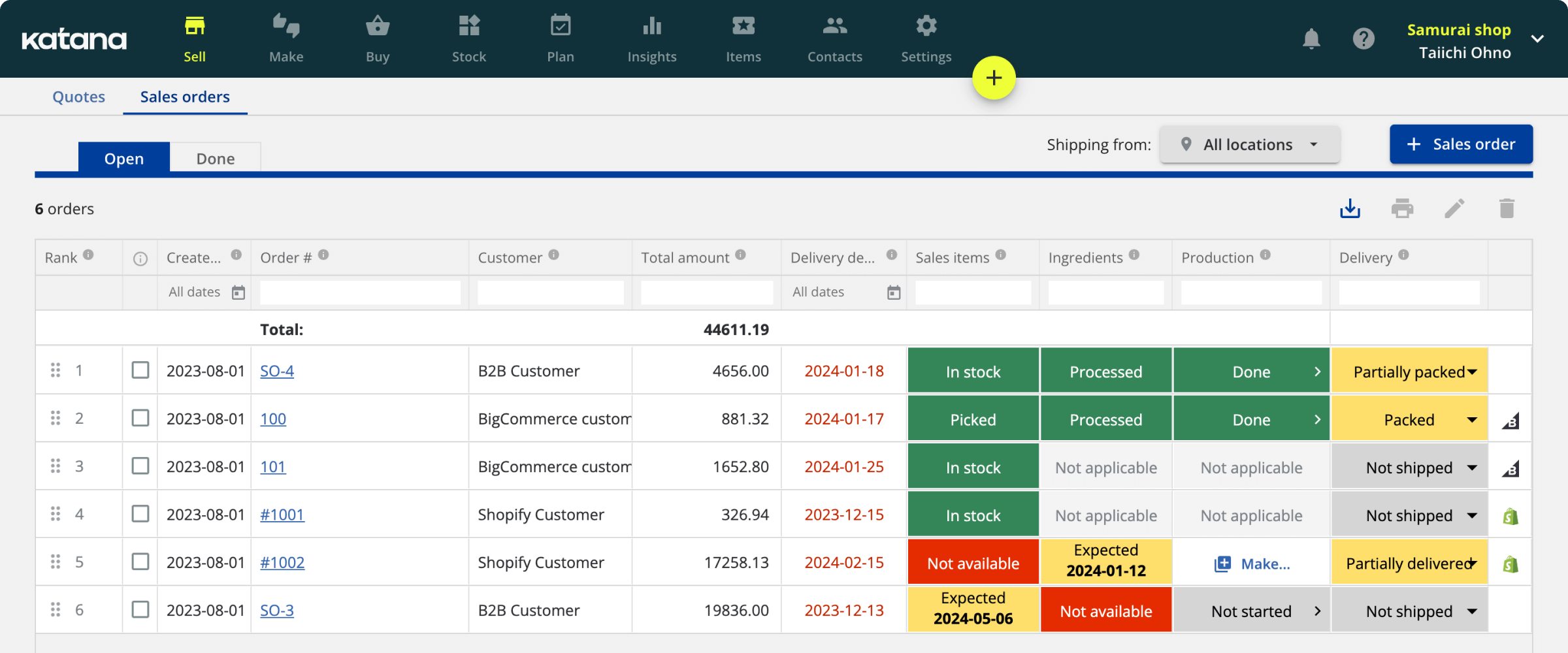