Routing manufacturing: mapping your production
Routing manufacturing maps the journey of your products throughout the manufacturing process. Discover the importance of routing manufacturing.
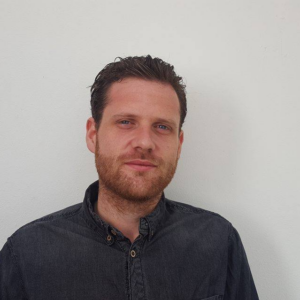
James Humphreys
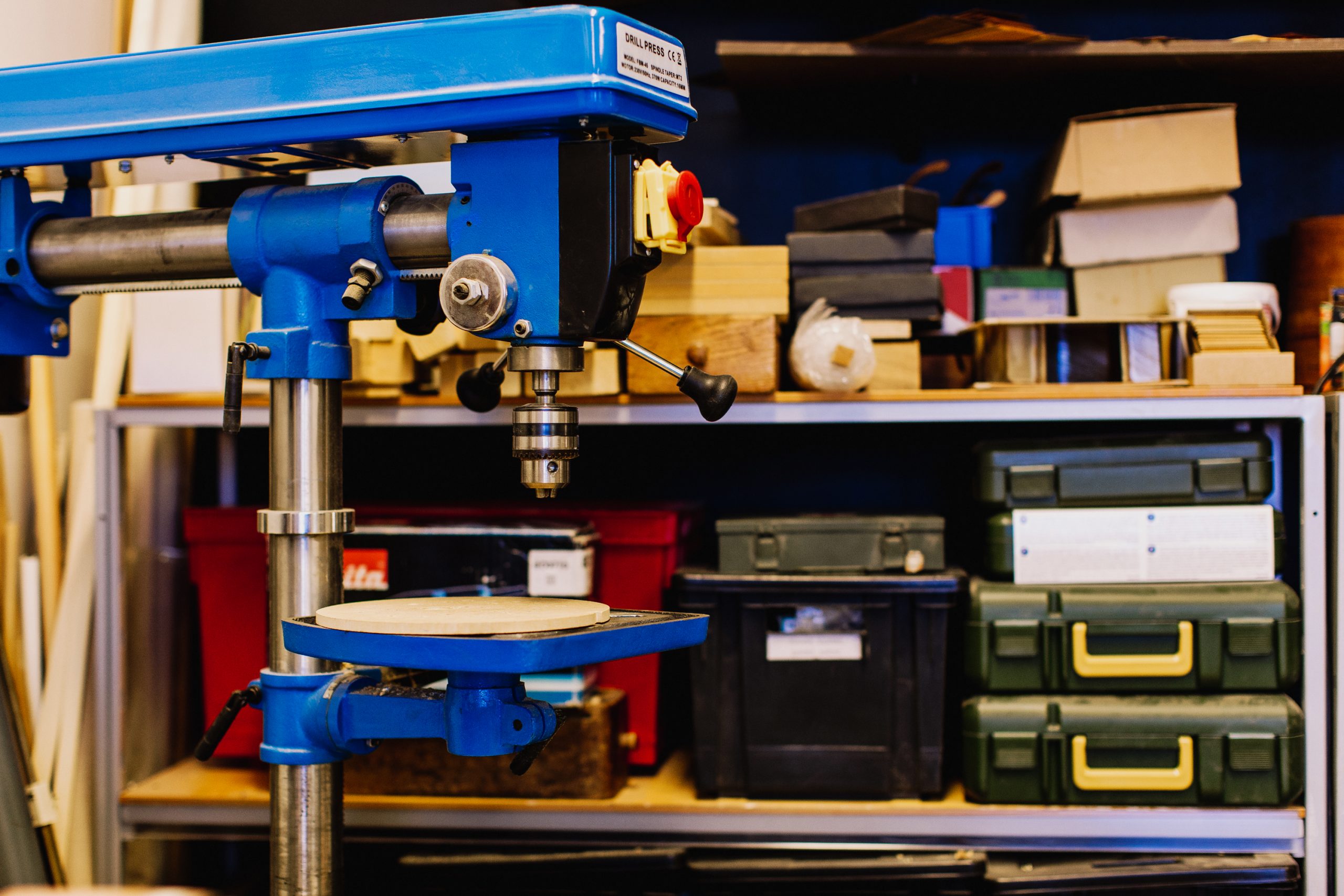
Imagine you’re a bus station manager.
You have 20 buses, each of which visits 5 out of the 100 bus stops in the city.
However, the routes aren’t established, and the buses aren’t numbered.
It will be impossible to avoid delays as you’ll be struggling with the logistics of getting the buses to their correct stops in the correct order.
This is similar to if you’re a manufacturer who makes customized goods.
Your products and the orders will require different processes. Without routing manufacturing, it’s going to be difficult to move your product from one process to the next.
You’re probably wondering, “What is routing manufacturing, and how do I do it?”
In this article, we’ll look into routing and how you implement it to achieve a smooth, uninterrupted flow for your products as you manufacture them.
Let’s begin.
Perfect your manufacturing route
Identify bottlenecks and easily make improvements to your manufacturing workflow like thousands of other businesses with Katana Cloud Inventory software.
What is routing in manufacturing?
Routing manufacturing, sometimes referred to as production routings, is the route to be followed during each step of the manufacturing process when transforming components and raw materials into a finished product.
Routings show the production flow that needs to be achieved. This can be done in one or more facilities or sent to an external vendor for specialized tasks. A task is an action that is performed to make the product. For example, the steps could go in an order such as:
- Cutting material
- Painting
- Assembly
- Packaging
Routing details the steps needed to take and, in the order, they need to be completed to create your product.
Along with this, the routing highlights the materials and equipment/workstations that will be used to manufacture an item, all derived from a product’s bill of materials. For a simpler explanation:
Routing = lists of tasks needed for a manufacturing process used to make a product
The same routing can be used for multiple products if it has a similar process. Also, a product may go through one process more than once before moving on to the next stage. If this is the case, the number of cycles must be specified in routing manufacturing.
So, determining your routing in operations management will help you understand the path and sequence of operations needed to be completed on a product as it passes from one process to another.
But what’s the purpose?
The aim of routing manufacturing is to establish the optimum sequence of operations at the lowest cost and complete it in the quickest amount of time. Routing manufacturing does not mean that you can take any shortcuts. You still have to review your production quality control checklist to maintain the highest quality.
Routing is an important base for organizing your business as it defines the manufacturing method.
When figuring out your routings, consider:
- The tasks that need to be carried out to manufacture an item
- The work centers (where production activities are performed) in which these tasks are carried out
- The sequence in which a product passes through the processes
Once you’ve completed this, you’ll have your routing document applied to each product you manufacture. This lists all production operations and processes, in chronological order, that take place to complete the final product.
Primarily, routing manufacturing will provide grounds for scheduling and measuring the capacity of production resources.
What is an example of routing in manufacturing?
To breakdown the definition of routing in manufacturing further, here’s what a typical manufacturing example looks like for a business that builds its own bicycles:
- Frame welding — the first step in the routing process for a bicycle might be frame welding. This involves joining the various frame components together using welding equipment.
- Frame painting — once the frame is welded, it might be sent to a paint booth for painting. The painting process might include several steps, such as sanding, priming, and applying multiple coats of paint.
- Wheel assembly — the next step might be wheel assembly. This involves attaching the spokes to the rims, mounting the tires, and attaching the wheels to the frame.
- Gear assembly — once the wheels are attached, gear assembly might be next. This involves installing the gears and derailleur onto the frame and attaching the chain.
- Final assembly — the final step might be the final assembly. This involves attaching the bicycle’s handlebars, seat, pedals, and other finishing touches.
Quality control checks might be performed throughout the routing process at each step to ensure that the product meets the required standards.
For example, welds might be inspected for strength, the paint might be checked for evenness and durability, and gears might be tested for smoothness and accuracy. By carefully planning and optimizing the routing process, manufacturers can ensure the production process is efficient, effective, and high-quality.
What is process route modeling?
Process route modeling typically involves using flowcharts or diagrams to represent the process flow. A symbol or shape represents each step in the process, and the arrows between the symbols indicate the sequence of steps. The model may also include information on the inputs, outputs, and resources required for each step in the process.
Routing in production planning and control
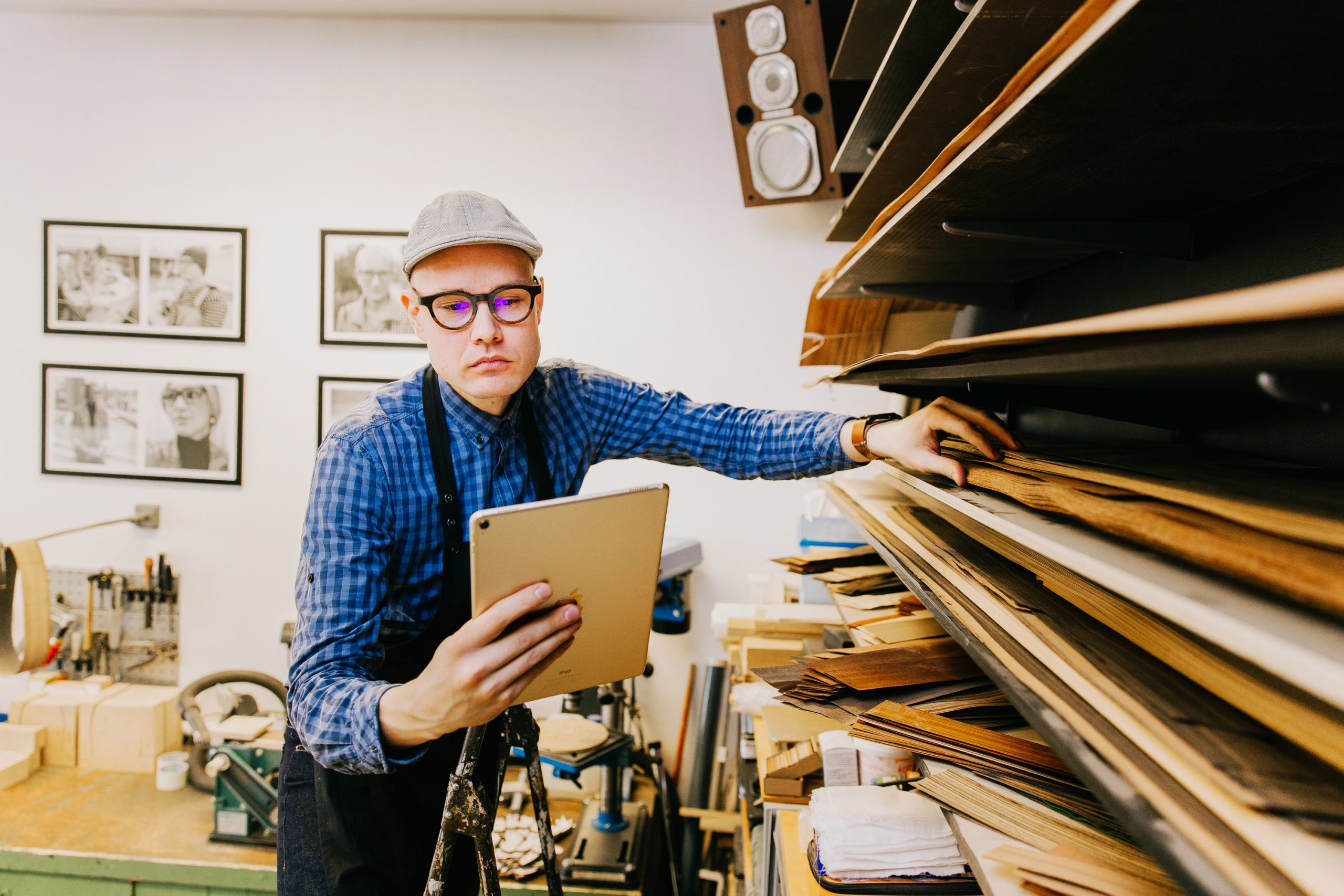
Production routing means as soon as a manufacturing order is generated, you and your employees will know immediately what tasks need to be carried out at what work centers, significantly cutting down your manufacturing lead times.
This will vary depending on what type of manufacturing business you operate. For larger companies that use repetitive manufacturing, the products are standardized, so no managerial effort is really needed since the products go through one movement.
However, the quaint, proud, and scaling manufacturers will need to establish routes as their highly customized items whizzing all around the shop floor.
Routing a production order requires:
- The information on the product being manufactured
- Details of each relevant operation
- The set-up time
- The standard time is needed to finish the production
The routing procedure consists of six points:
1. Make and buy decision
You’ll need to decide which parts and components are to be made by yourself or bought in. You decide this by price comparison, availability of resources, if you have the appropriate tools, and whether the materials and machines are available.
2. Bill of materials
Your bill of materials determines the materials required for production. Using a BOM means procuring the relevant material and components before production starts.
3. Preparation of route sheet
This is where you’ll need to look at operations and pair them with a sequence to manufacture the product. This establishes the operations needed to process a product, listing them in their sequence on the route or operations sheet.
4. Lot size determination
This is where you determine the capacity that can be produced at one location. However, “If the product is to be produced to fulfill the consumer requirements, the question to determine the lot size does not arise.” This is mainly a concern for businesses that use a continuous or repetitive manufacturing workflow.
5. The scrap factor
You’ll need to estimate the amount of scrap produced during the manufacturing process. As we know, all the components produced at various workstations do not meet the required standards, and those that do not pass inspection will be neglected as scrap.
Scrap may be produced at one point during the manufacturing process or progressively. You’ll need to determine these points and take the appropriate action to deal with the buildup called a scrap factor. Normally this is decided from previous experience, and you’ll need to direct resources to remove scrap to avoid bogging down machines.
6. Provide necessary information and forms
As you probably know, manufacturing and business management can be dull and bureaucratic.
Unfortunately, your routing manufacturing is no different. You’ll need to have your manufacturing orders, job tickets, inspection tickets, move orders, tool tickets, and equipment tickets.
However, for businesses with around 2 to 15 employees, this might not be necessary. Although, it’s a good practice to have your floor-level management to this high standard of the organization to avoid bottlenecks and backlogs.
As you can see, preparing routing in production requires a mental sweat. But once you have taken the time to do this, you’ll be able to reap the benefits.
Advantages of production routing
- Effective utilization of available resources
- Reduction in production costs
- Quality improvement occurs
- The productivity of the system improves
- Provides a basis for loading scheduling
For a production routing example, let’s use a business that manufactures customized wooden glasses. They have their routing manufacturing planned out might look something like this in action:
Task 1
Design — As per the customer’s specifications
Task 2
Preparation of material and cutting — Getting everything ready
Task 3
Shaping — Setting the shape of the glasses into the desired final shape
Task 4
Varnishing (‘X’ number of cycles) — Varnishing the glasses, so they keep their shape. This has to be done several times
Task 5
The final product — The final touches are made on the glasses
Task 6
Packaging — The glasses are packaged and ready for delivery
Task 7
Shipping — The glasses are shipped off to the customer
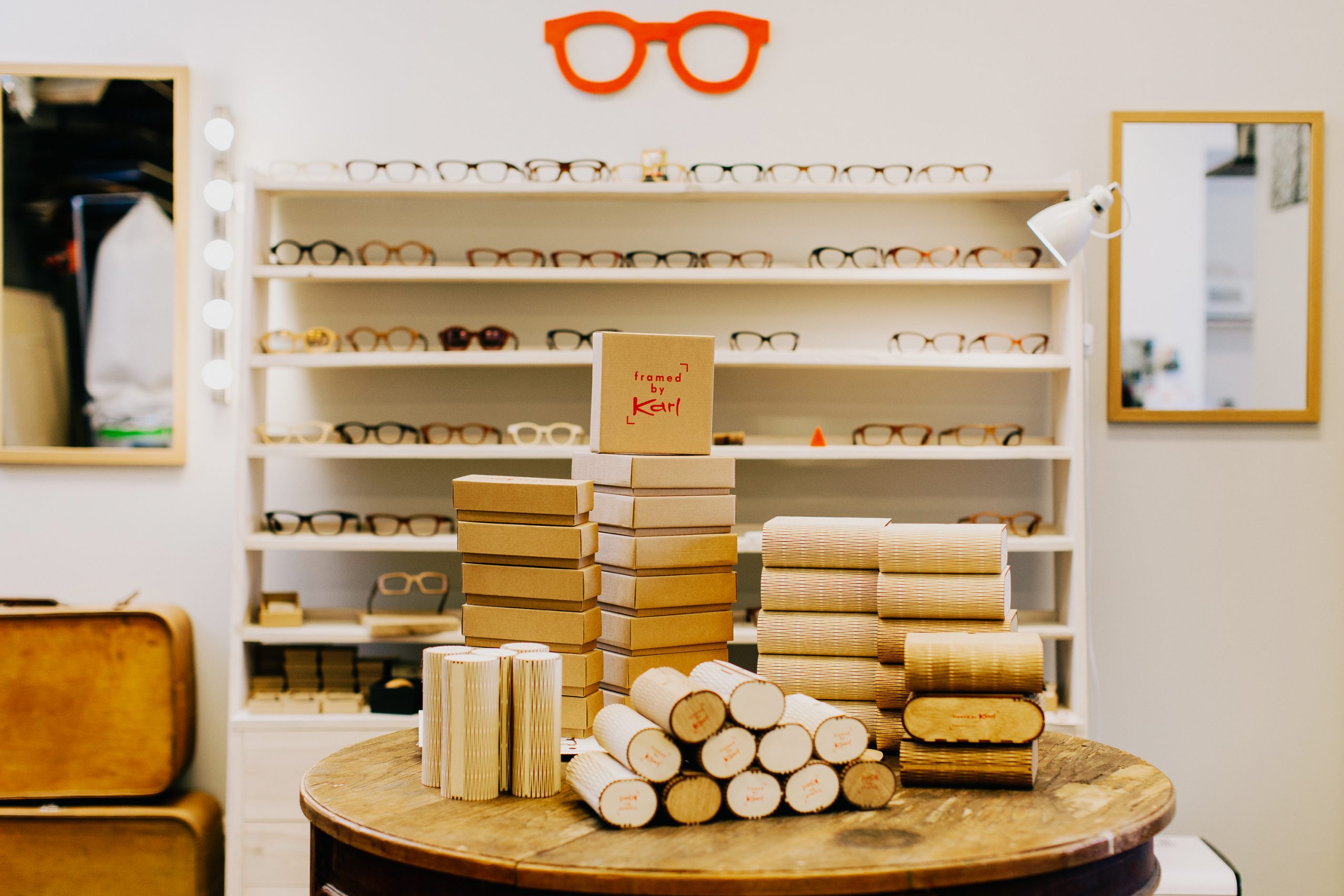
The production routing example shows that the final stages of manufacturing your products will be packaging and shipment. However, without planning the route beforehand, getting to this stage will be delayed by your items getting lost on the shop floor.
If you’d like to see the sequence and task list in more detail, our investigation into the job shop manufacturing workflow should satisfy you. We’d recommend this to any business manufacturer, as this will be how your business will operate.
Pro tip: Routing manufacturing determines how your product gets from A to B on your shop floor, but you still need to calculate manufacturing lead times and figure out a master production schedule. Check out this huge breakdown of what is manufacturing to maximize your business’s performance.
How to use routing manufacturing in Katana
Katana cloud manufacturing software is specifically developed for SMB manufacturers looking to grow their businesses.
It helps you do this with features such as:
1. Live inventory management
Automatically updates and saves inventory movement in real time, helping you manage:
- Raw materials
- Finished goods
- Work-in-progress (WIP)
2. Streamlined floor-level management
Easily manage resources with a nifty drag-and-drop system to prioritize those important orders.
3. Integrations with your favorite tools
Access your e-commerce orders or generate an invoice for your accounting software, all from one platform.
You don’t have to overload yourself with more work by working out your routing manufacturing within Excel or on some other paper-based system.
Routing in production can be made so much simpler by integrating cloud-based manufacturing software into your business. Production Operations lets you see what tasks must be performed, and you can easily reassign your resources to fulfill these.
Essentially, to translate everything into the language of Katana, this is where you can complete your routing manufacturing within the software. Saving you the hassle of having to draft and maintain different schedules with the cumbersome Excel program.
Routing in production planning and control with Katana allows you to easily monitor your floor-level staff as you can see what tasks are not started, in progress, or completed.
Want to see for yourself? Request a demo today to see exactly how Katana can benefit your business and get all your questions answered.
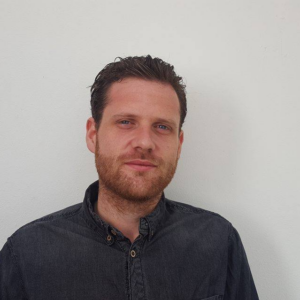
James Humphreys
Table of contents
Get inventory trends, news, and tips every month
Get visibility over your sales and stock
Wave goodbye to uncertainty with Katana Cloud Inventory — AI-powered for total inventory control