What is a bill of materials (BOM)?
A bill of materials is an essential part of the manufacturing process. Here we look at why that is and how growing manufacturers can best use BOMs.
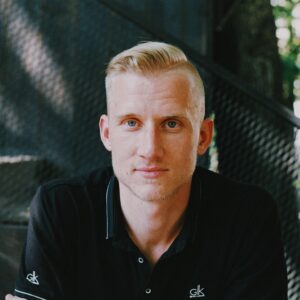
Henry Kivimaa
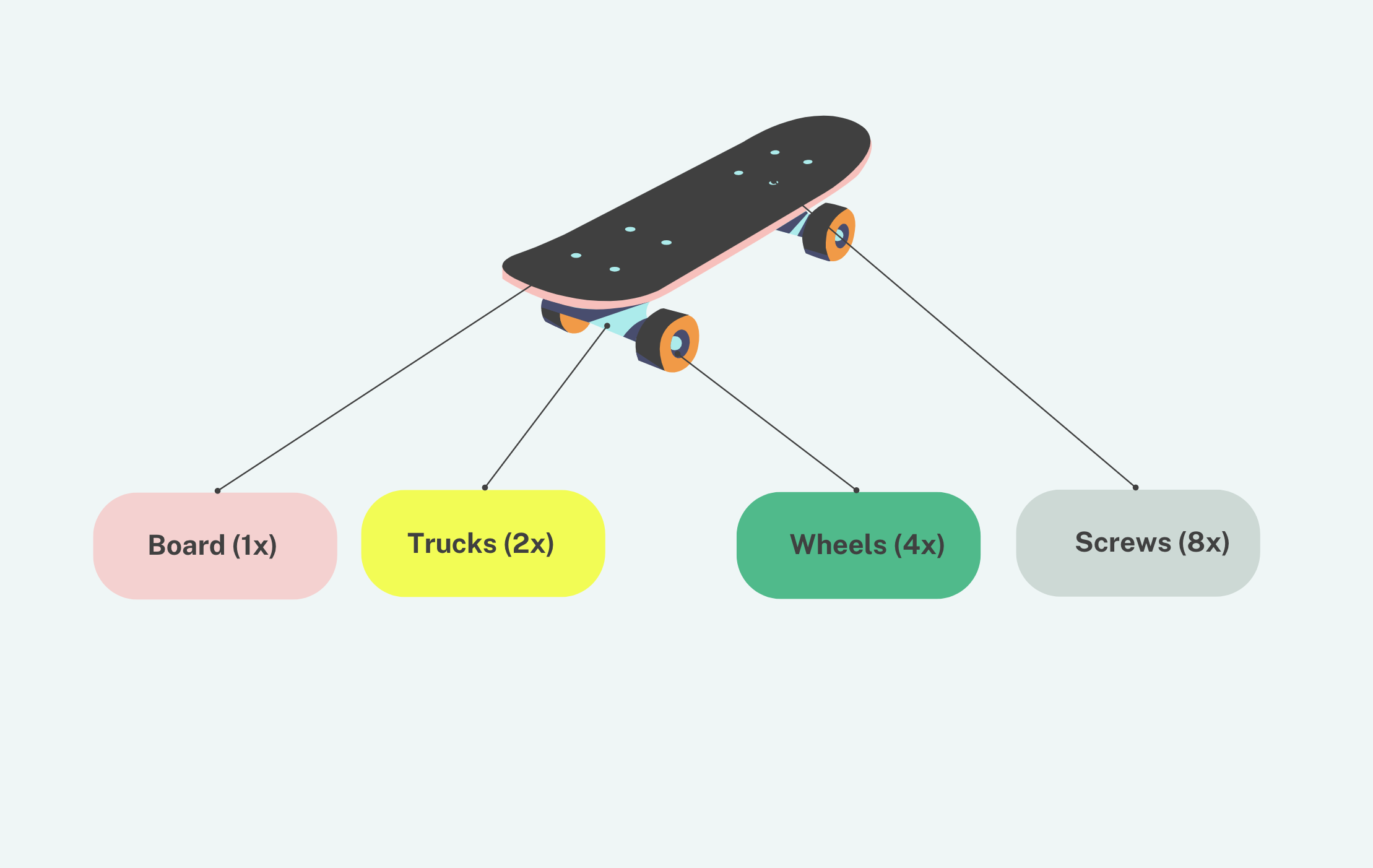
If you’ve ever bought an item from IKEA’s wide selection of furniture inventory or played with Legos, you know that your best bet to start using the item pictured on the box is to follow the instructions and assemble it accordingly.
However, if you’re like most men, you first try assembling these things without even knowing that the manual exists. After an hour or two of furious manufacturing, you step back and notice that the item resembles nothing like what’s on the box.
If you’re lucky, maybe you accidentally created something you need anyway. But more than likely, you must take this construction apart, admit defeat, and look for the instruction manual.
The moral of the story is that instruction manuals are pretty handy, and using them does not mean you’ve been defeated. Even manufacturers who push out hundreds of products have such manuals. They just call them by a different name — a bill of materials (BOM) or a product recipe.
This article will explore the ins and outs of bills of materials, look at what is BOM in manufacturing, how to make a BOM, and what you need to know about a bill of materials management.
What is a bill of materials?
A bill of materials (BOM) is a comprehensive, structured list of raw materials, subassemblies, intermediate assemblies, subcomponents, parts, and the quantities needed to manufacture a product. It has various applications and is sometimes referred to as a production recipe, assembly list, or component list.
It typically includes information about the quantities of each item needed, as well as information about the specifications and quality requirements for each item.
A BOM serves as a reference document for manufacturers and suppliers, enabling them to manage their inventory and production processes efficiently. It is an essential component of the manufacturing process, providing a clear outline of all the components required to build a product and helping to ensure that the finished product meets the required quality standards.
BOMs can be used in a variety of industries, from manufacturing and construction to software development and engineering.
Regardless of where your business operates in the manufacturing industry, all manufacturers get started by creating their BOMs.
Single vs. multilevel bill of materials
A bill of materials is a vital document for production management, ordering replacements, and performing maintenance on your products. It allows businesses to manage purchases and reduces the possibility of errors. When it comes to the structure, there are two types of BOMs:
- Single-level bill of materials
- Multilevel bill of materials
Single-level bill of materials
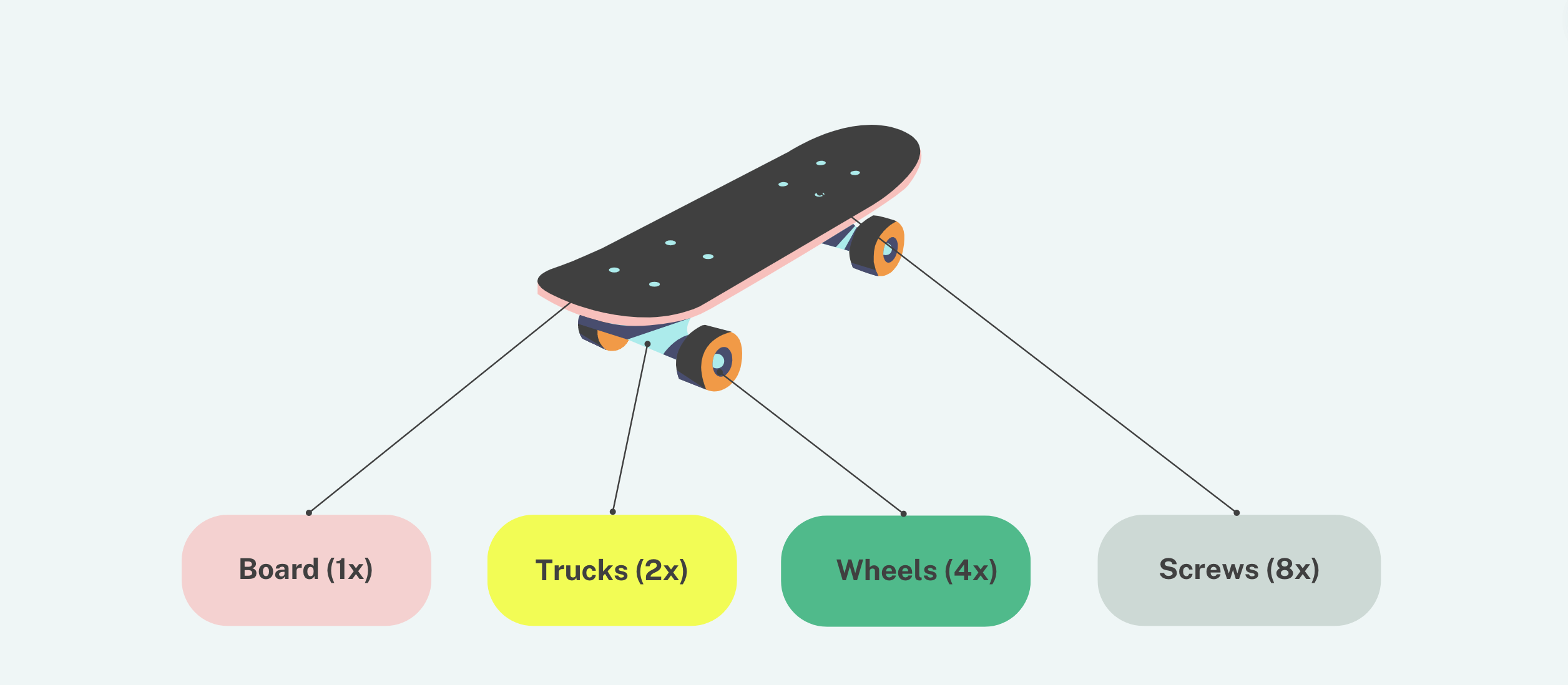
A single-level bill of materials structure is a simple list of parts to produce a product. It consists of only one level in components, assemblies, and materials.
Although simplicity can sometimes be best, a single-level BOM may not be suitable for more complex products.
One critical factor to consider is that if an issue arises with a product, such as a quality concern, you cannot identify which material in the production process needs to be replaced or amended.
You can still use a single-level BOM for more complex products as well, but it may be harder to follow since it’s missing the hierarchical structure.
Let’s move on and see what a multilevel BOM looks like.
Multilevel bill of materials
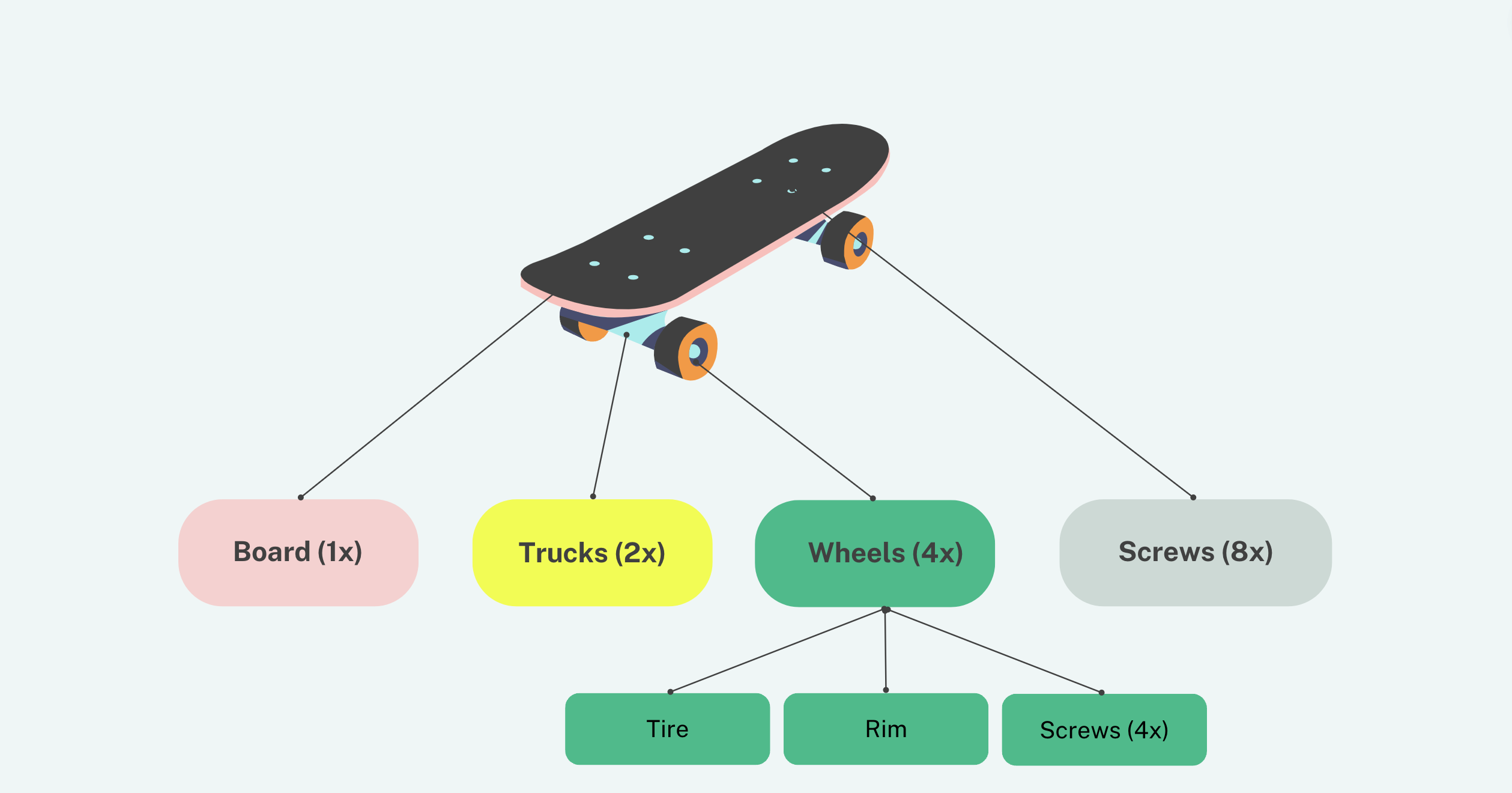
A multilevel BOM, also called an indented BOM, is an intricate bill of materials that lists the components, assemblies, and parts required to make a product.
The structure of a multilevel BOM resembles a family tree and maps out all components and subassemblies of a product. Each BOM level will detail all the components that are directly or indirectly used in producing a parent item.
It provides a display of all items that are in parent-children relationships. When an item is a subcomponent, for example, all its components, including finished parts and raw materials, are also exhibited.
It’s similar to a single-level BOM but provides a greater layer of detail and specificity on all parts involved in the production of the product.
Intuitive BOM software
Katana’s inventory platform lets you create and manage your BOMs, giving you a clear overview of all your materials and processes. Get a demo to see it in action, or read more to learn about the specific features.
Types of BOMs
There isn’t a one-size-fits-all when it comes to a bill of materials. There are many types of BOMs to choose from, so it helps to understand your options. Here’s a quick overview of different types to help you decide your business needs.
Manufacturing bill of materials (MBOM)
A manufacturing bill of materials displays the materials, assemblies, and subassemblies that are required to produce a finished product. It applies to the production process before the completion of the finished goods.
Engineering bill of materials (EBOM)
An engineering bill of materials is different from a manufacturing BOM, as it defines the design of a finished product. It is often created based on a computer-aided design or CAD drawing as part of product lifecycle management.
Configurable bill of materials (CBOM)
A configurable bill of materials is a form of BOM used by industries with multiple options and highly configurable products.
The CBOM is used to dynamically create products that a company sells, so they can easily be molded and shaped. The CBOM structure’s benefit is that it reduces the work effort needed to maintain product structures.
The configurable BOM is most frequently driven by configurator software. The development of the CBOM is dependent on having a modular BOM structure in place.
Modular BOM
BOMs that describe the subassemblies are referred to as modular BOMs.
Modular BOM structure provides the assemblies/subsystems that can be selected to configure an end item. So, this structure requires modular BOM as well.
The main reason modular BOMs are used is that maintaining the BOM is much simpler (given that the assembly list of the product is long and complex, and maintenance does not require a complete overhaul of the BOM each time).
Can you manage your BOMs with Excel?
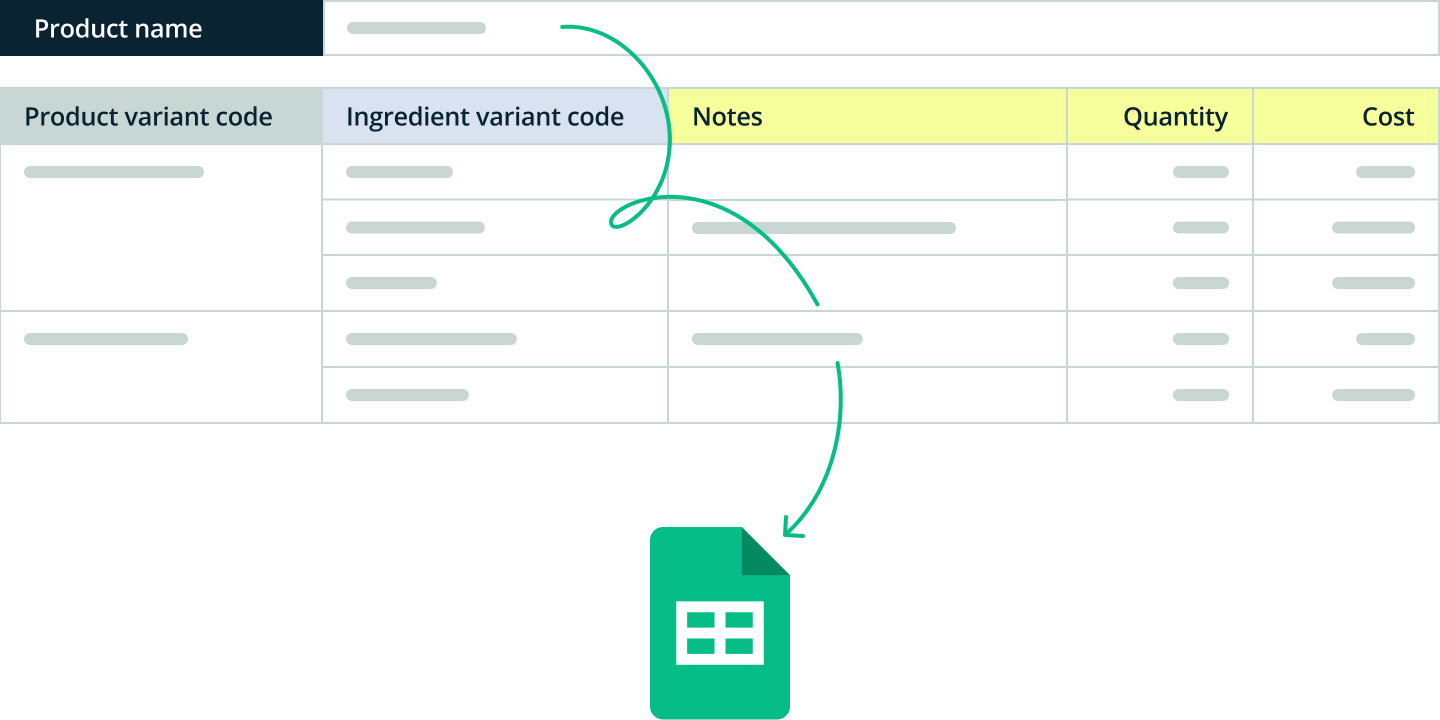
A spreadsheet may seem like the obvious choice to manage your bill of materials, but is it the best? Let’s take a look at some challenges when using Excel for your bill of materials management process.
1. Prone to errors
From copy/paste errors to more complex macro and script issues. BOMs kept in inefficient Excel spreadsheets can easily be plagued with problems and must be constantly updated manually, which will take up much of your resources. Not only does it waste time, but it can also mean that key business decisions are made based on inaccurate data.
2. Difficult to add variants
It is difficult to add in your potential product variants. When a product has multiple variants, it can be complicated to manage in Excel as the number of resolved BOMs will grow exponentially with the number of variants, quickly becoming impossible to manage.
3. Calculating costs and quantities
Calculating totals in Excel may seem simple, and it is for flat or single-level BOMs. However, when dealing with multilevel BOMs, it is more complicated.
Calculating costs and quantities for multilevel BOMs requires extensive setups and complex formulas. This takes valuable time away from other important tasks, and with increased complexity, it can result in errors.
4. Creating a multilevel (indented) BOM is complicated
Creating a multilevel BOM in Excel is not impossible but can be complicated. You need to find a way to indicate a hierarchy level across parts and subassemblies. The reason that this is so difficult is that:
- It’s easy to make mistakes when adding or removing parts from your existing multilevel BOM. For example, are you inserting the new value in the right places, or if removing a subassembly, have you accidentally deleted all the associated parts as well? Small mistakes can lead to huge errors if you make a business decision based on incorrect data.
- The sorting function in Excel is incredibly useful, but it can also cause major problems. For example, sorting columns can mess up your key columns and delay your production process.
- When manufacturing various products, they will often use the same parts. Managing multiple instances of a part across products across different levels of the BOM hierarchy can cause serious issues in Excel. For example, if you update the part number for a part for one product, will all instances of the part in the BOM be updated?
As you can see, there is a lot to think about when using Excel to manage your BOMs. Let’s move on and see if specialized software can help you manage BOMs.
Free Excel BOM template
If a simple BOM Excel template is all you need, you can download one for free by clicking the download button.
How to make a BOM in Katana
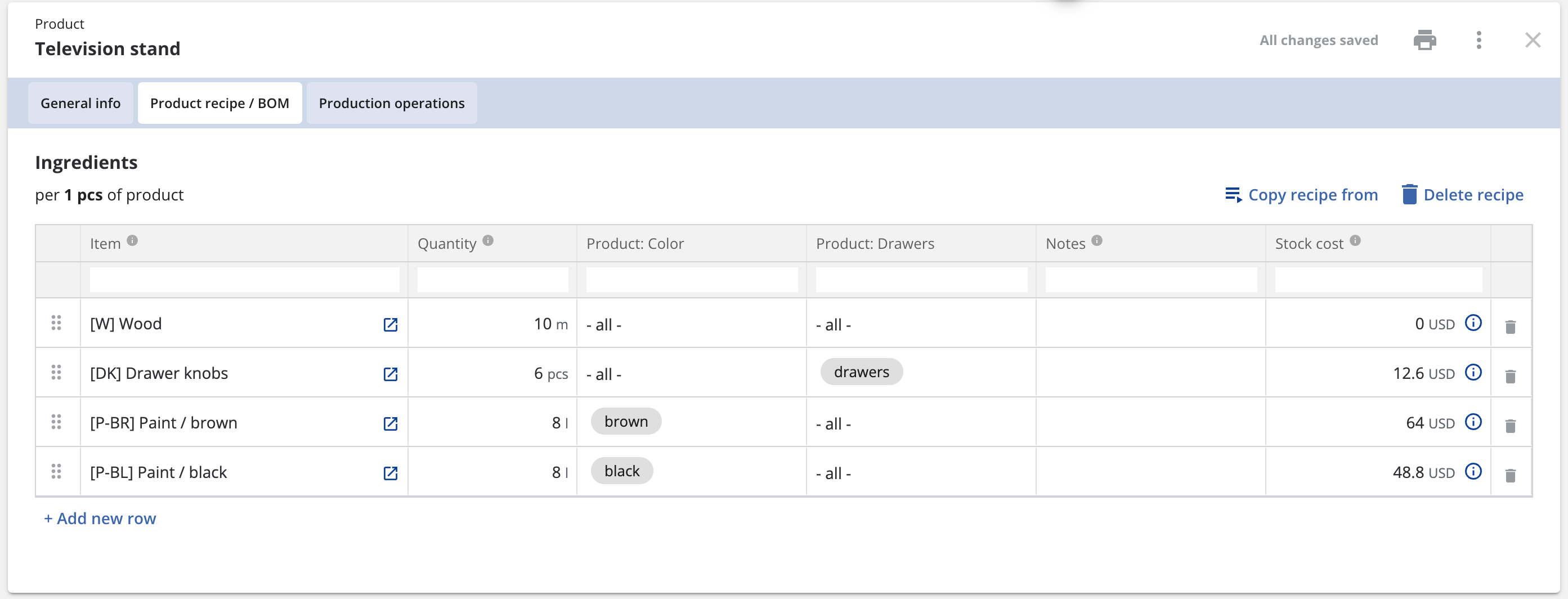
Here’s how to create a bill of materials in Katana using the following parameters:
1. Item
Every material, ingredient, or subassembly should have a unique name in your bill of materials. Katana also displays the item’s SKU, making it easy to distinguish between different materials.
2. Quantity and units of measure
The quantity of each material needed to produce a product must be specified. This allows the bill of materials to be an accurate purchasing asset and help establish safety stock and reorder points.
The units of measure are specified when each item is created, so Katana adds that to the BOM automatically when you enter the quantity.
3. Product color
Specifying the product color will help to ensure there are no errors made by those using the bill of materials to create the finished product, especially if you have a lot of color variants.
4. Description and notes
The bill of materials should include a clear, informative description of the material for those involved in the production process. You should also include any additional information needed for someone to understand the BOM clearly.
5. Stock cost
Katana fills in the stock cost automatically based on the quantity you entered before, making it easy to track the costs.
To make your manufacturing process even more effective, you may want to enrich the BOM structure with additional information in the comments. Here are some options you can add:
- Lead time — The time between the initiation and completion of an assembly process
- Scrap factor — The percentage of components and/or materials ruined during manufacturing operations
- Quality criteria — Upfront defined measurable tests and test results to confirm that the quality objectives of an assembly process have been met and the production quality control checklist followed
- Done criteria — An upfront agreement of assembly steps and tasks that need to be completed to complete the assembly process
- Roll-up cost — Calculates the standard cost based on the BOM and routings of assembling the product
To get a more detailed overview of Katana’s bill of materials feature, have a look at the video below:
Bill of materials example
Understanding the varying complexities and types of bills of materials available to you can sometimes seem overwhelming and leave you wondering where to begin.
So, here’s a basic bill of materials example to show how you can get started. Let’s go with making wooden doors, simple enough.
The first thing is to list the items that go into making a door. You need:
- Door panel
- Handle
- Hinges
- Latch
Okay, I guess we’re done then. Time to go home?
Well, not quite yet, there are a few more steps to go through. And the next is to determine how much of each item we need.
- Door panel (1x unit)
- Handle (1x unit)
- Hinges (2x unit)
- Latch (1x unit)
Brilliant, we know what we need and how much of it.
Next up: how much does it cost?
- Door panel (1x unit) $20
- Handle (1x unit) $6
- Hinges (2x unit) $2
- Latch (1x unit) $2
Total cost: $30
So, that’s about as simple as a bill of materials, or product recipe, as you will ever find.
It’s not too hard to imagine how it could become more complex. If, for example, we offered different door handles, it would make sense to build a configurable BOM.
But that should give an idea of how it works, so you can start building your own BOMs.
Benefits of BOM manufacturing
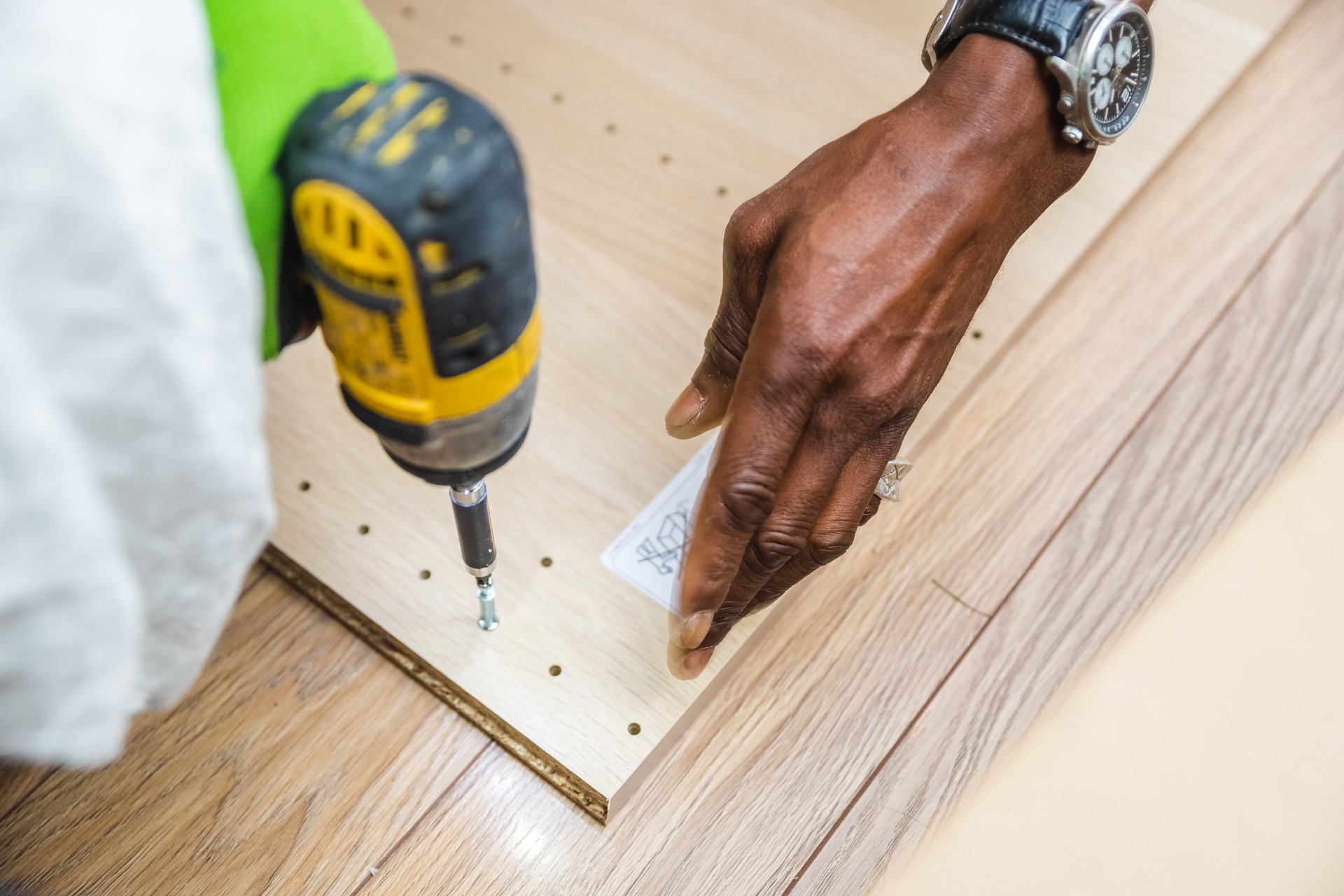
The benefits of having BOMs in manufacturing can be a lot more widespread than just on the end product itself.
Always available
A clear list of materials, quantities, and inventories ensures you won’t run out of materials. By using BOMs, your inventory management software can remind you when stocks are low so that you can replenish as necessary. This can massively reduce delayed deliveries to customers.
In time
Knowing the required inventory levels, the process involved, and the time it takes to manufacture, results in timely and predictable delivery processes. By knowing how everything functions at every step along the way, you can ensure that each step happens on time when needed.
With better planning comes more accurate knowledge of how much time a job will take, which feeds back into the BOM. This allows your team to cost up jobs and orders more effectively, making you more profit.
It’s a beautiful self-refining cycle.
Less waste
Another reason a BOM is essential in manufacturing is its ability to help reduce waste.
A lot of waste comes from excess inventory itself. You are tying up resources that could be put to use and keeping unusable products. It’s throwing away money through inventory carrying costs.
With BOMs, you know what is needed, and by bringing in the right parts efficiently, you aren’t left with excess inventory.
In the end, you are left with product recipes that constantly self-improve. And at the same time, this helps keep your stock at optimal levels.
Bill of materials software
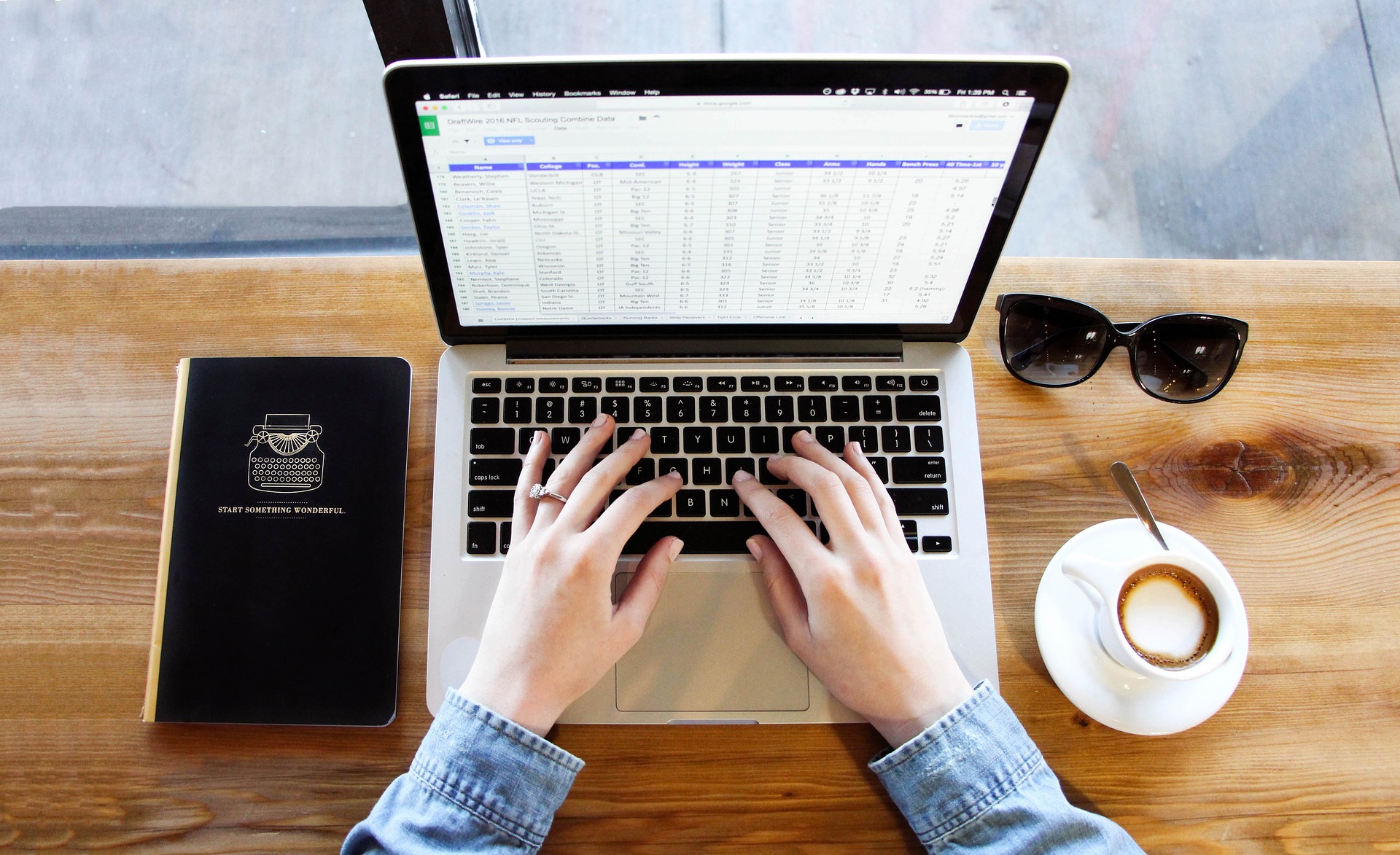
As you saw above — you can use spreadsheets for your BOMs, but there will be certain limitations and challenges you need to deal with.
It would make a lot more sense if you could have a bill of materials software that made everything seamless, wouldn’t it?
Well, you’re in luck — Katana’s cloud inventory software embeds your BOMs in your entire workflow. That means you can see all your BOMs, inventory, sales, and production on a single platform.
Katana integrates with the best business tools like QuickBooks Online and Shopify, giving you a unified experience and eliminating the need to transfer information between platforms manually.
Reach out to our sales team to book a demo and see Katana in action.
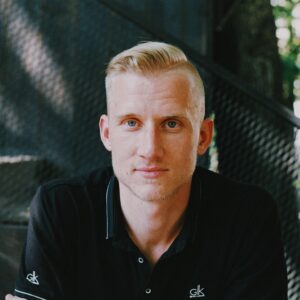
Henry Kivimaa
Table of contents
bom-template
Download a free bill of materials template
This template is a great starting point for creating a BOM that works for you.
Get inventory trends, news, and tips every month
Get visibility over your sales and stock
Wave goodbye to uncertainty with Katana Cloud Inventory — AI-powered for total inventory control