Optimizing Xero tracked inventory for batch and expiry tracking
The issues with the lack of features for Xero tracked inventory and expiry dates can be solved, with the use of 3rd party manufacturing software.
Team Katana
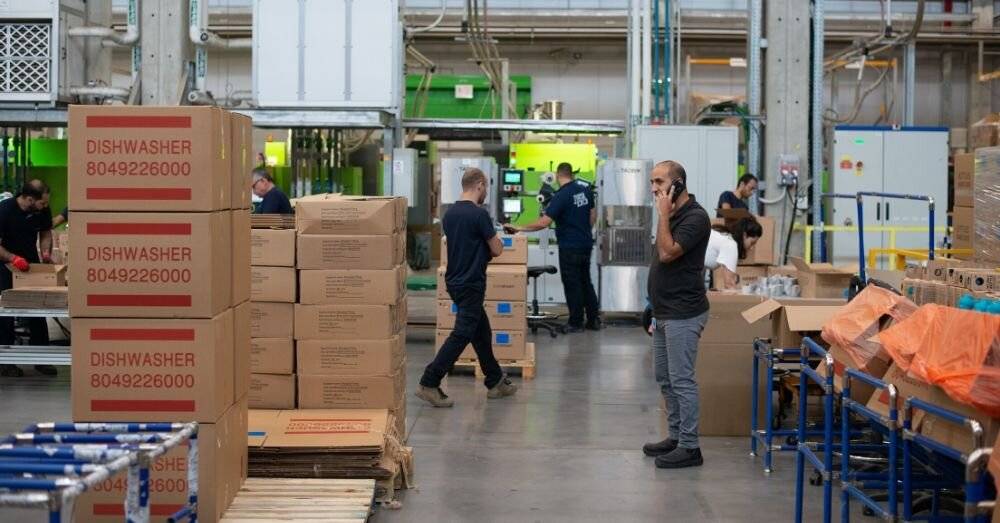
Manufacturers using Xero will quickly realize there are some limitations with using it to monitor batch production. That’s why we put together this article on Xero tracked inventory, the issues, and the solutions to optimize your manufacturing with it.
Batch (sometimes referred to as lot) and expiry tracking is a system for grouping and monitoring a set of stock, and monitoring the expiration date of the items.
It’s a good rule of thumb to have these tracking processes in place, but for manufacturers, with perishable inventory, it’s an essential requirement as it’ll help them:
- Avoid spoilage
- Trace defective items back to its original batch
- Enable product recalls
But, the big enchilada, can Xero tracked inventory also manage batch and expiry tracking?
In this article, we’re going to look into if the Xero inventory expiration date tracking features are up-to-speed for modern manufacturing, and how to optimize your batch tracking with the software.
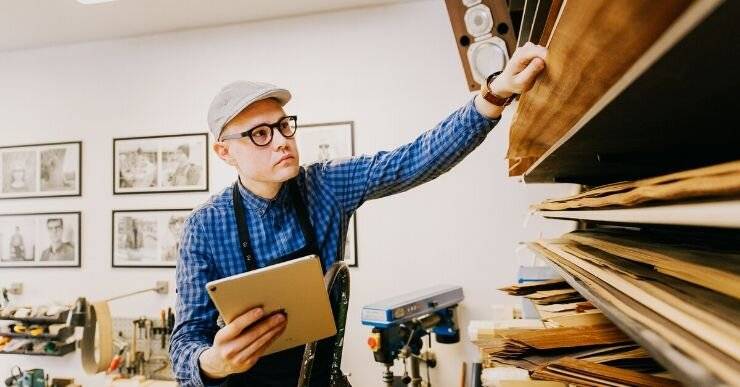
Xero inventory management
Xero comes equipped with inventory management features, which is what attracts so many manufacturers to the software since it kills two birds with one stone by having software that can help them get control over their:
- Manufacturing
- Finances
Sounds too good to be true, right? Well, there is a pretty substantial catch.
Xero is a fantastic tool for helping you keep your bookkeeping accurate and up to date in real-time. But, for manufacturers, it’s missing advanced features needed for running your business.
The inventory features are split into two parts:
- Xero tracked inventory
- Xero untracked inventory
Xero tracked inventory automatically updates inventory levels of your goods sold, and tracks the associated costs.
But, untracked inventory, which is the items you don’t sell (and services you provide) aren’t automatically monitored.
You can still track the price, notes, and tax rates for these items. But you can’t set stock levels for untracked items.
And being able to track the conversion of raw material to finished goods is essential for manufacturers.
In a nutshell, that’s how Xero inventory management works, but you can check out this video below if you want to know more about the system:
Pro tip: Inventory management is important for manufacturers, especially when you have to handle different inventory types simultaneously. A good rule of thumb is to perfect your shelf-life management, which will help you optimize your inventory space.
Now, let’s look into the issues of Xero tracked inventory, and how you can get it to work for you as a manufacturer.
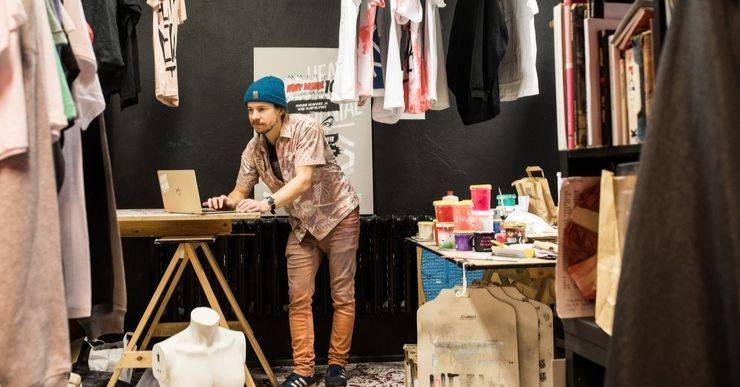
Xero tracked inventory and its limitations for manufacturers
Xero is certainly a good choice for manufacturers looking to get set up with accounting software. But the only way you’ll be able to get the most out of using Xero is to understand its limitations.
So, let’s look into features manufacturers need, why they’re important, and if it works in Xero:
Xero inventory expiration tracking
Expiry tracking is the process of monitoring your inventory’s shelf life to avoid items spoiling.
It’s something that’s needed by manufacturers in food production and those who need to use cosmetics formulation production software. But, improved Xero tracked inventory is also useful for industries that handle things like technology (since items will eventually become outdated).
By using an inventory expiration tracking system or a barcode scanning software, you can track the expiry dates of your inventory, so you can take the appropriate actions before your items turn bad, and you have to sell them at a discount, or worse, dispose of them.
But, the big question, is there a Xero inventory expiration tracking system? Unfortunately, no.
That doesn’t mean you should burn bridges with Xero, as they do have the Xero App Store where you can find a Xero inventory add-on that can integrate with your account and give you the inventory expiration features you need.
Xero batch and lot tracking
A batch and lot tracking system allows you to monitor a group (batch) of products that were made using the same materials and manufacturing processes, as they make their way along your supply chain.
A Xero tracked inventory batch system will allow you to track your item’s movements forward and backward along this supply chain too.
This means by using a batch number, you’ll be able to identify where the item came from, where it’s located now, and where it will end up.
A Xero tracked inventory batch system will also help you:
- Track the expiration date of items
- Trace spoiled or defective items back to its batch
- Allow you to implement a product recall process
- Be legally compliant with legislation for your industry
Xero tracked inventory only goes as far as helping you monitor some of the inventory you sell, and manufacturers need to be able to track all items in their inventory.
And once again, the best way to get Xero inventory expiration date and batch tracking are to visit the Appstore and get yourself set up with a batch inventory management system that can integrate with your account and bridge the feature gap.
A batch inventory management system will allow you to:
- Perform product recalls quickly and effortlessly
- Streamline expiry tracking
- Improve your relationship with suppliers
- Make fewer mistakes by ditching manual tracking
The purpose of getting set-up with Xero is to have the best tools on the market for tracking your finances.
However, to take advantage of Xero inventory expiration date tracking, you’re going to need to look into a 3rd party integration that’s designed to help manufacturers get more control over their production.
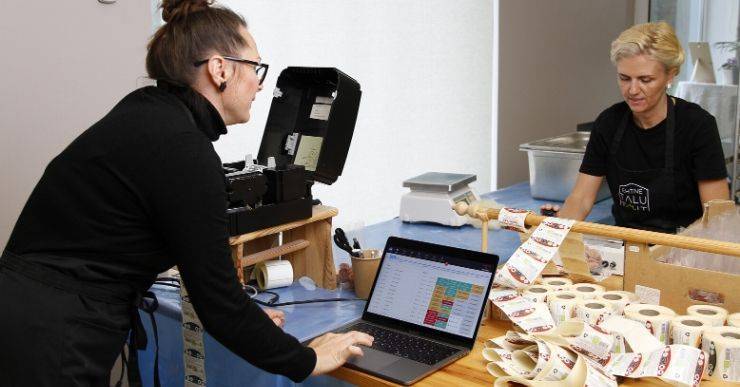
The solution to xero inventory expiration date tracking
Without using 3rd party integrations, Xero tracked inventory will only record the quantities of available items you have to sell.
If you’re just getting started with Xero and need to set up stock levels, you can easily import your opening balances using an Excel file.
Once you’re finished setting up and using Xero tracked inventory, your stock levels will automatically increase and decrease as you buy (make) and sell products, unless you make adjustments to an item’s balance.
Xero tracked inventory will calculate the value of the items you have in stock and include this on your balance sheet report.
If you happen to trade items, the inventory balance updates. Otherwise, when you sell items, the sale is recorded as a cost of goods sold (COGS).
You can learn more about Xero tracked inventory over on TV.Xero, but this is about as far as the software goes when it comes to helping manufacturers.
That’s why Xero themselves suggest manufacturers check out the Appstore for product traceability solutions that will help them:
- Operate at negative inventory. Which is useful for those who record sales as complete before finishing production or dispatching the product
- Allow you to follow your own workflow and give you greater inventory control
- Track and monitor the consumption of raw materials and sub-assemblies into finished goods
- Buy and sell items in different currencies without manually updating;
- Save purchase order receipts
- Track more than 4,000 inventory items at one time
But, with so many options to choose from when improving your Xero inventory expiration date tracking, where do you even begin?
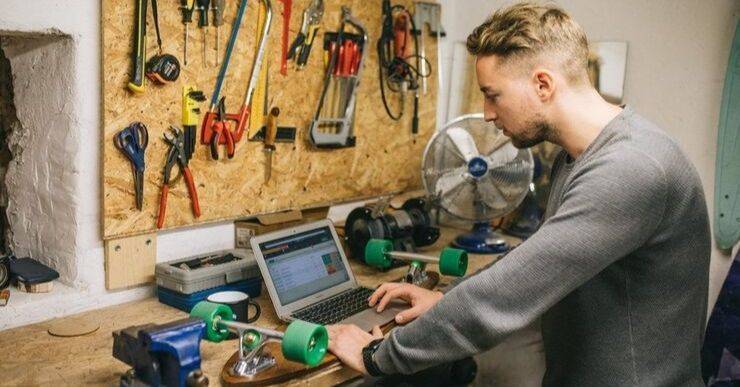
Using Cloud Inventory Software for Xero inventory expiration date tracking
Katana cloud inventory software is an Xero ERP integration built by manufacturers for direct-to-consumer (D2C) manufacturers looking to bridge the gap between their sales, manufacturing, and finances.
With this integration, you can unlock the full potential of Xero inventory expiration date tracking with:
- The track expiration feature
- Tools to trace defective or spoiled items back to batch
- Everything you need for fast and easy product recalls
Not only will you be able to get more control over Xero inventory expiration date tracking, but Katana can also centralize your business and help you manage with:
The Auto-Booking System
It’s easy to get overwhelmed when trying to fulfill sales and manufacturing orders. That’s why we have the auto-booking system, that takes available items, and automatically allocates them to open orders, so you know immediately if you’re able to:
- Fulfill orders
- Need to manufacture more products
- Order more raw materials
Prioritized Production Planning
Stop stressing over putting together your master production schedule with Katana’s intuitive automatic scheduling system. When you’re generating manufacturing orders, Katana automatically schedules it to production in the order they’re created.
However, if you need to prioritize an order, our nifty drag-and-drop system lets you change the schedule, and Katana will redistribute allocated materials and recalculate deadlines.
Reorder Points
In Katana, you can improve your Xero tracked inventory with reorder points, which will allow you to set up safety stock in your business. Once your inventory dips below this point, Katana will highlight the quantity, so you know it’s time to manufacture or order more items.
Conclusion
And there we have it, everything you need to know about Xero inventory expiration date tracking, and how you can optimize your batch manufacturing.
But, to quickly summarize, when looking for a 3rd party integration for your Xero tracking inventory, you’re going to need:
- Real-time analytics
- Reorder points
- Automated manufacturing of your workflow from quoting to ordering to billing to shipping
- Multilocation inventory management
- Integration of your point of sales software
- Tools for demand planning
- Batch and expiry dates and lot tracking
- To manage returns and exchanges
- To make notes on manufacturing orders
- Integration with your e-commerce platforms such as Shopify and WooCommerce
- Automated finished goods and raw materials management
- Features to help you scale your business
Katana Cloud Inventory Software can help you in all these areas. If you don’t have an account yet and want to see how Katana can automate your Xero tracked inventory, request a demo today.
And that’s all we have for today! We hope you enjoyed this article. If you have any questions, feel free to comment below, shoot us a message on our social media pages or pop us an email, and we’ll be more than happy to answer them.
And until next time, happy manufacturing.
Team Katana
Table of contents
Get inventory trends, news, and tips every month
Get visibility over your sales and stock
Wave goodbye to uncertainty with Katana Cloud Inventory — AI-powered for total inventory control