What is traceability and how to implement in manufacturing?
Product traceability will help optimize your production lines and is a legal requirement for some businesses. But what is it, and how do you implement it?
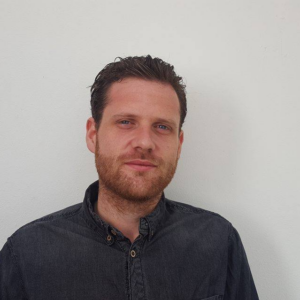
James Humphreys
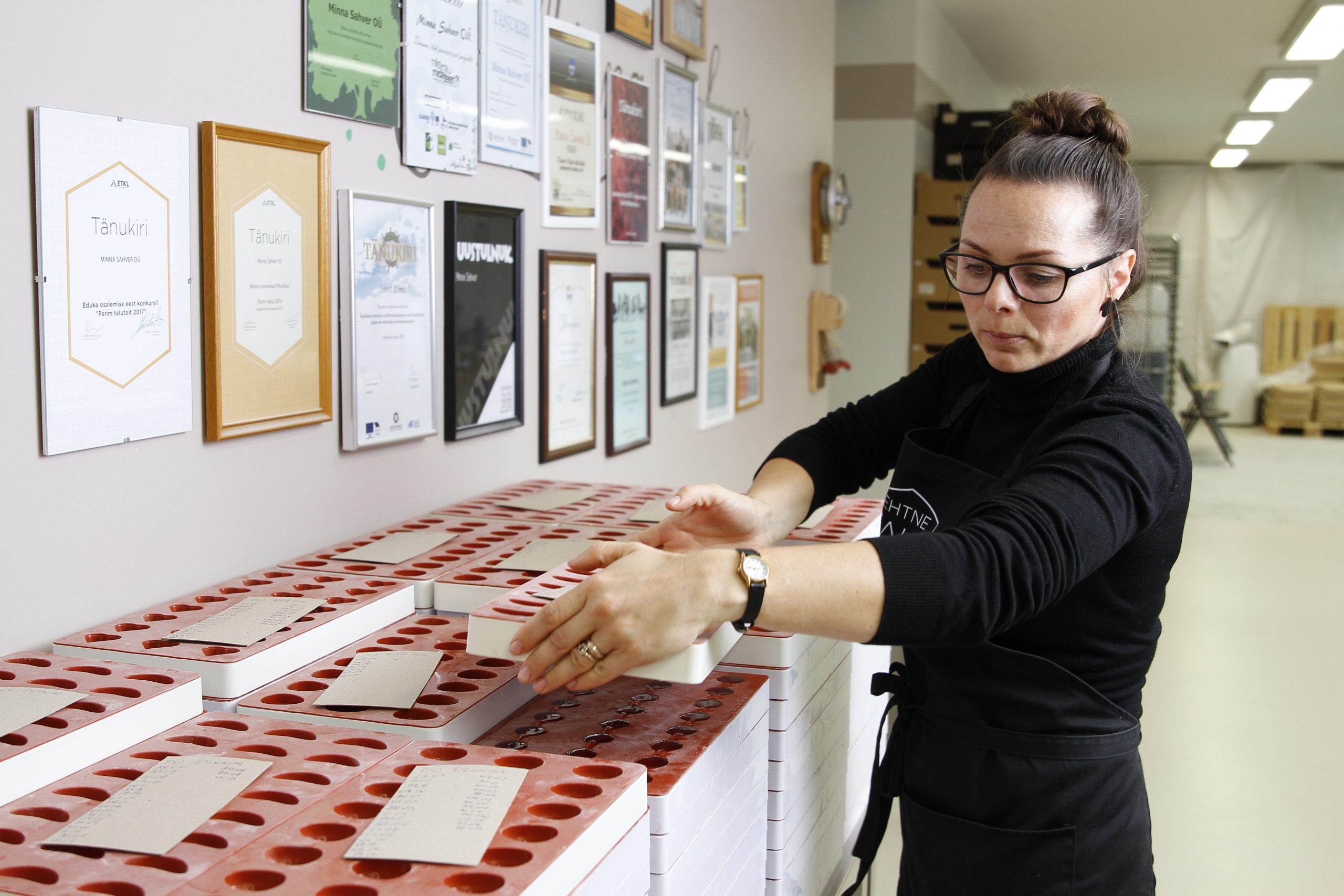
Product traceability allows you to track your inventory movements from end-to-end, meaning you can track products to where they were shipped, or back through their operational steps.
In this article, we’re going to look into traceability in manufacturing, why it’s important, the benefits, and how you can implement it.
Download the definitive guide to batch production
Download our free ebook guide on batch production to learn more about the benefits, workflows, and software you need to get started.
What is traceability in manufacturing?
Traceability is the procedure of tracking (and documenting) all your raw materials, parts, and finished goods throughout your manufacturing process.
The term itself is coined together from “Trace” and “Ability” and is used to describe the ability to track products by all manufacturing industries, but is most often used in industries dealing with perishable goods, like cosmetics or food inventory.
Having a traceability program for manufacturing in place will allow you to find historical information on a product, such as:
- Suppliers
- Items
- Inspection notes
- Manufacturing details
- Time spent at each workstation
- Distributors
There are two perspectives when it comes to product traceability:
Chain traceability
This is forward and backward product traceability. Meaning manufacturers can track products from raw material to the distributor.
And the distributors or consumers can understand where the product came from.
Internal traceability
Product traceability with a limited scope, such as monitoring one specific part of the supply chain.
For example, if you use outsource manufacturing, the information you receive about their components is an internal traceability program.
What is end-to-end traceability?
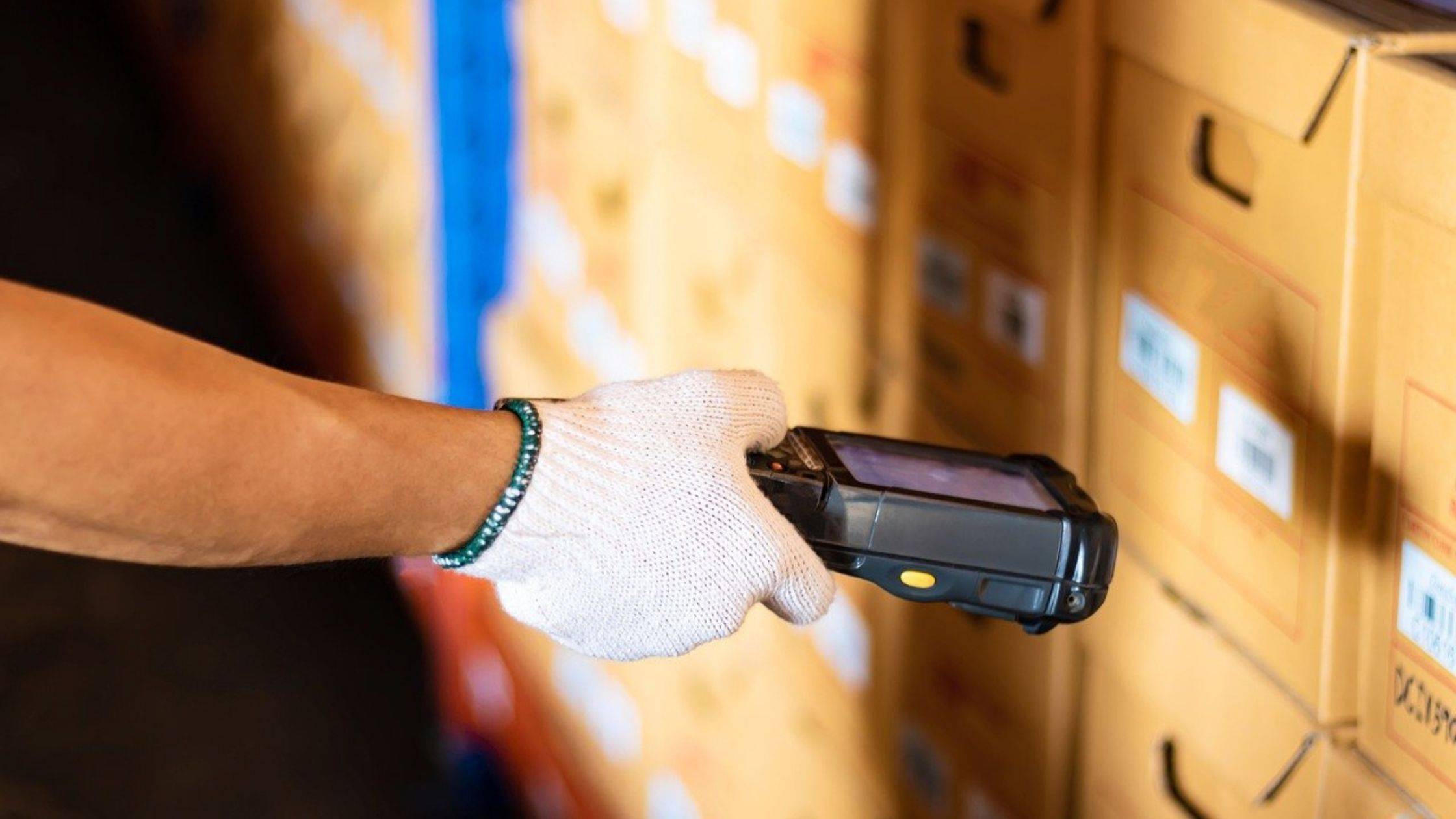
End-to-end traceability is the ability to track and trace every piece of material throughout the manufacturing process.
This record-keeping ensures that each component can be traced back to its original source, making it easier to identify any issues that may arise. End-to-end traceability is a key component of quality control and assurance and is often required by government agencies and industry organizations. In some cases, manufacturers may also be required to provide end-to-end traceability data to their customers.
End-to-end traceability can be achieved through:
- Barcode scanning inventory management systems
- RFID inventory management software
- Other unique identification methods
These identifiers are attached to each component as it moves through the manufacturing process.
As each component is assembled into a finished product, its identifier is recorded. This record can then help track a product through the supply chain and into the hands of the customer. End-to-end traceability offers many benefits for manufacturers, including improved quality control, decreased product defects, and reduced liability.
By having a complete record of every component in a product, manufacturers can more easily identify and fix any issues that may arise.
End-to-end traceability can also help manufacturers meet customer expectations and comply with industry regulations.
Katana Cloud Inventory
Katana supports thousands of businesses with batch tracking, barcode scanning, expiry date tracking, and more. Schedule a free demo call with our team and see Katana in action.
Why is product traceability in manufacturing important to implement?
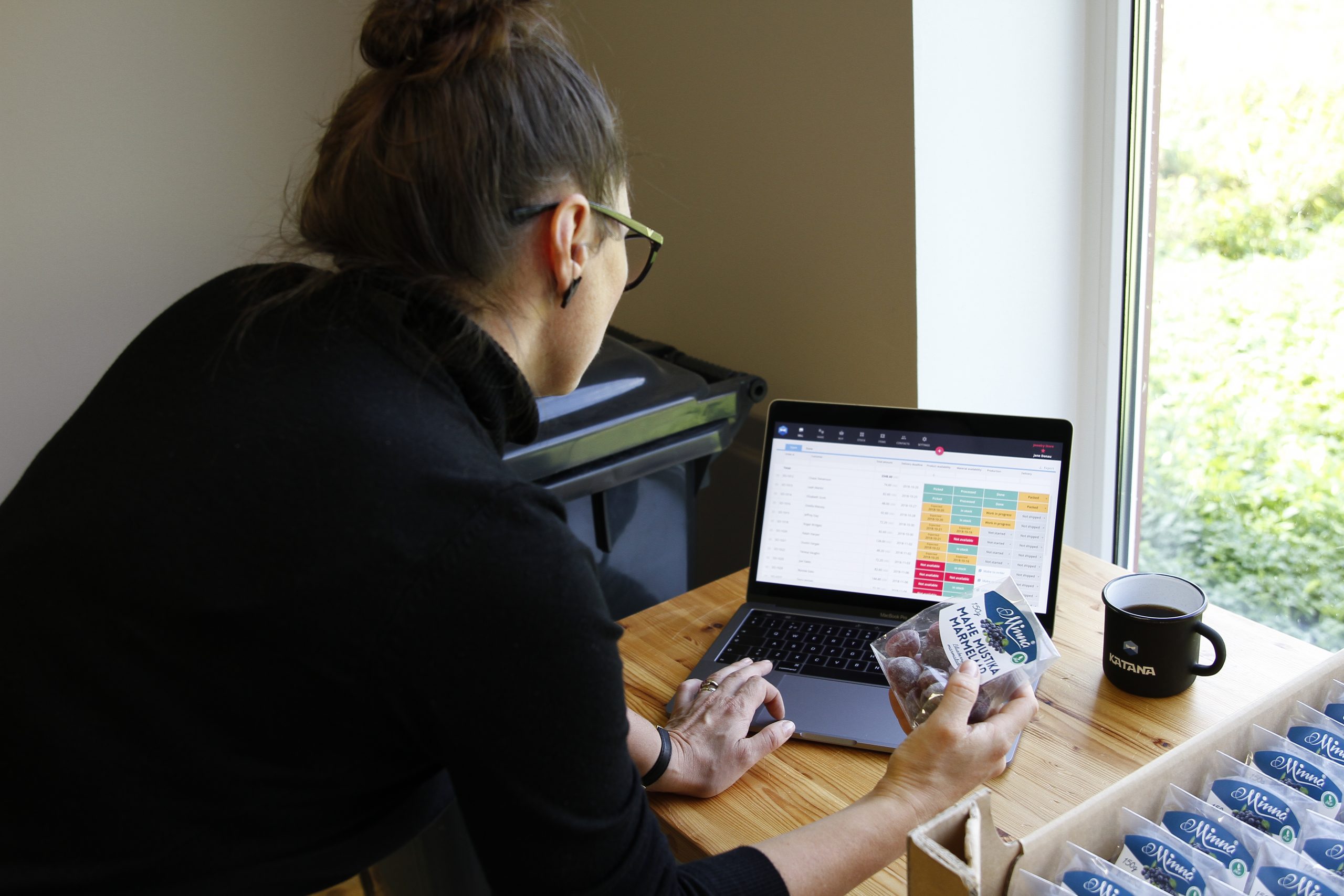
It’s exciting times when your hard work pays off, and you see your business grow, and the number of products you manufacture expand.
But it only takes one batch of faulty products to enter the market to:
- Driveaway customers
- Damage your brand
- Hurt your bottom line
- Undo all your hard work
If you don’t have a system in place to track products, it’s going to be impossible to effectively recall a defective or contaminated item.
That’s why having systems in place to improve product traceability is essential.
Not just for products that have a short shelf life but for products that will become outdated due to technological advancements.
You might think that you don’t need a traceability program since you don’t sell perishable goods. But, it will help you improve production efficiency and product quality control, as you’ll have real-time visibility to understand where problems occur, such as bottlenecks in production.
Now you know what product traceability in manufacturing is and what can happen if you don’t implement it. But what are the benefits of traceability in manufacturing?
Pro tip: Depending on where your business exists within the industry, you will need your traceability software to perform certain functions. For example, a cosmetic production system will help health and beauty professionals prioritize, delegate, and track production tasks.
How to track production in manufacturing?
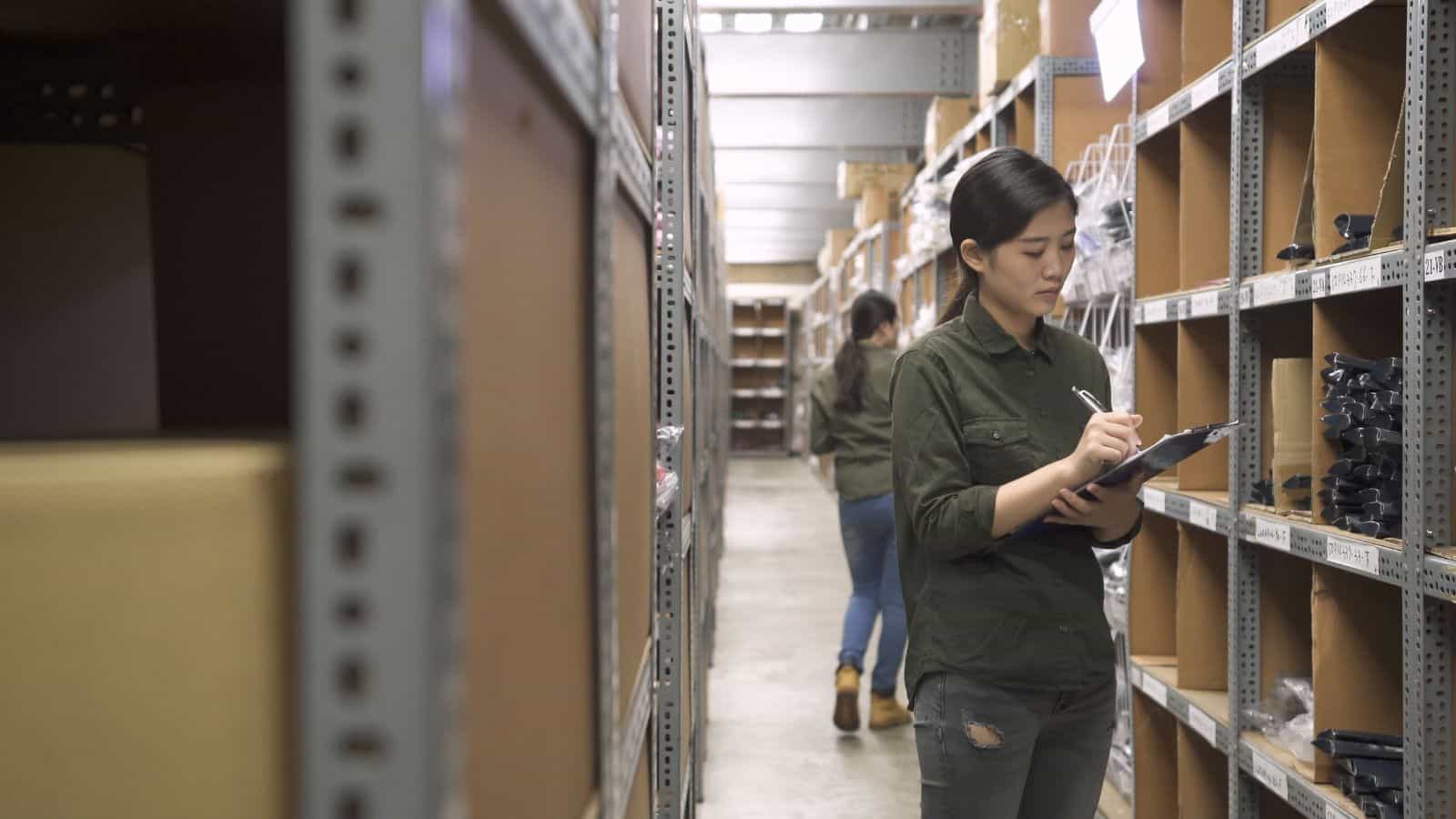
Traceability in manufacturing involves monitoring the process of creating goods from start to finish, including the raw materials used, work-in-progress (WIP), and finished goods. There are several manufacturing traceability methods and tools that can be used to track production in manufacturing, but some of the most popular are:
1. Production planning and control
This involves creating a manufacturing plan outlining the production schedule, resources needed, and the sequence of operations required to create the product. Having a clear plan allows you to track progress and identify any delays or issues that arise.
2. Manufacturing system
A traceability system for manufacturing tracks production in real time, providing a detailed view of the manufacturing process, from raw materials to finished products. This system can track production metrics such as:
- Cycle time
- Downtime
- Machine utilization
3. Barcode and RFID systems
Barcoding and RFID systems are used to track materials and products throughout the manufacturing process. These systems can identify each item and its location, allowing for real-time inventory management and production traceability.
4. Kanban system
The Kanban system is a visual system that uses cards or other visual cues to signal when materials need to be replenished or when a particular task needs to be completed. Manufacturing traceability solutions like this can help to reduce lead times and increase production efficiency.
5. Lean manufacturing principles
Lean principles involve streamlining production processes to eliminate waste and increase efficiency. You can optimize the production process and track progress more effectively by identifying and eliminating bottlenecks.
By implementing these methods and tools, manufacturers can track production more systematically and efficiently, leading to increased productivity and profitability.
Benefits of traceability in manufacturing
Here are the advantages of using a traceability program in your business.
1. Root cause analysis
Having your product information from end-to-end means you can perform an in-depth analysis of your manufacturing routes to see the root cause of any problem.
This will enable you to see in which areas of your production are underperforming and help you make changes to improve your manufacturing lead time.
For example, if some finished products have defects, you’ll have an overview of your entire production line so you can pinpoint where the defects are occurring, such as:
- The products missed a particular process, like a quality check
- A new team member is making mistakes and needs to be trained
- A faulty tool or machine needs repairing
2. Continuous improvement
Following on from the root cause analysis benefit of using product traceability, you can also implement continuous improvement into your production flow.
A continuous improvement system is essentially a form of lean manufacturing.
However, the biggest difference is that with continuous, you and your team members will take responsibility for identifying inefficiencies on the shop floor, developing plans, and implementing improvements for future production runs.
Cloud manufacturing software will be a crucial tool for helping you gather real-time and accurate data on your manufacturing, so you can perform regular audits on your operations to make sure your production is always running smoothly.
Continuous improvement in manufacturing is perfect for those looking to:
- Remove waste
- Adopt green manufacturing into their business
3. Value Stream Mapping
Value stream mapping, also referred to as material and information flow mapping, is a lean management method for helping you understand your manufacturing process and how to redesign it to get the most value from manufacturing.
The value stream map is a traceability program that helps you monitor your:
- Operation steps
- The quantities of raw materials needed
- The time the product spends at each workstation
Since product traceability in manufacturing monitors how your products move through your shop floor, it lends itself well to designing your value stream mapping.
Doing this will help you get a granular picture of your operations and more of an idea of what could be improved on your production lines.
4. Quality and engagement
Including product traceability in your manufacturing means that you and your team members can take accountability and be more engaged along the shop floor by having the processes in place to monitor progress continuously.
Cloud manufacturing software like Katana can help you identify if you need more quality check-ups along your manufacturing process to avoid a defective product being shipped.
5. It’s your obligation
Finally, a lot of manufacturing industries are highly regulated, and having a traceability program is a legal requirement (especially in places such as food production).
That’s why if you work in one of these highly regulated areas, finding batch inventory management systems that can track your end-to-end product development and handle batch numbers is important to avoid any of the issues mentioned earlier in the article.
However, even if you’re not a manufacturer with products under intense scrutiny, using such software allows you to:
- Improve inventory management
- Maximize your return on investments
- Make better business decisions with improved analytics
These were the benefits of using product traceability within your manufacturing. But how do you go about improving product traceability?
How to improve traceability?
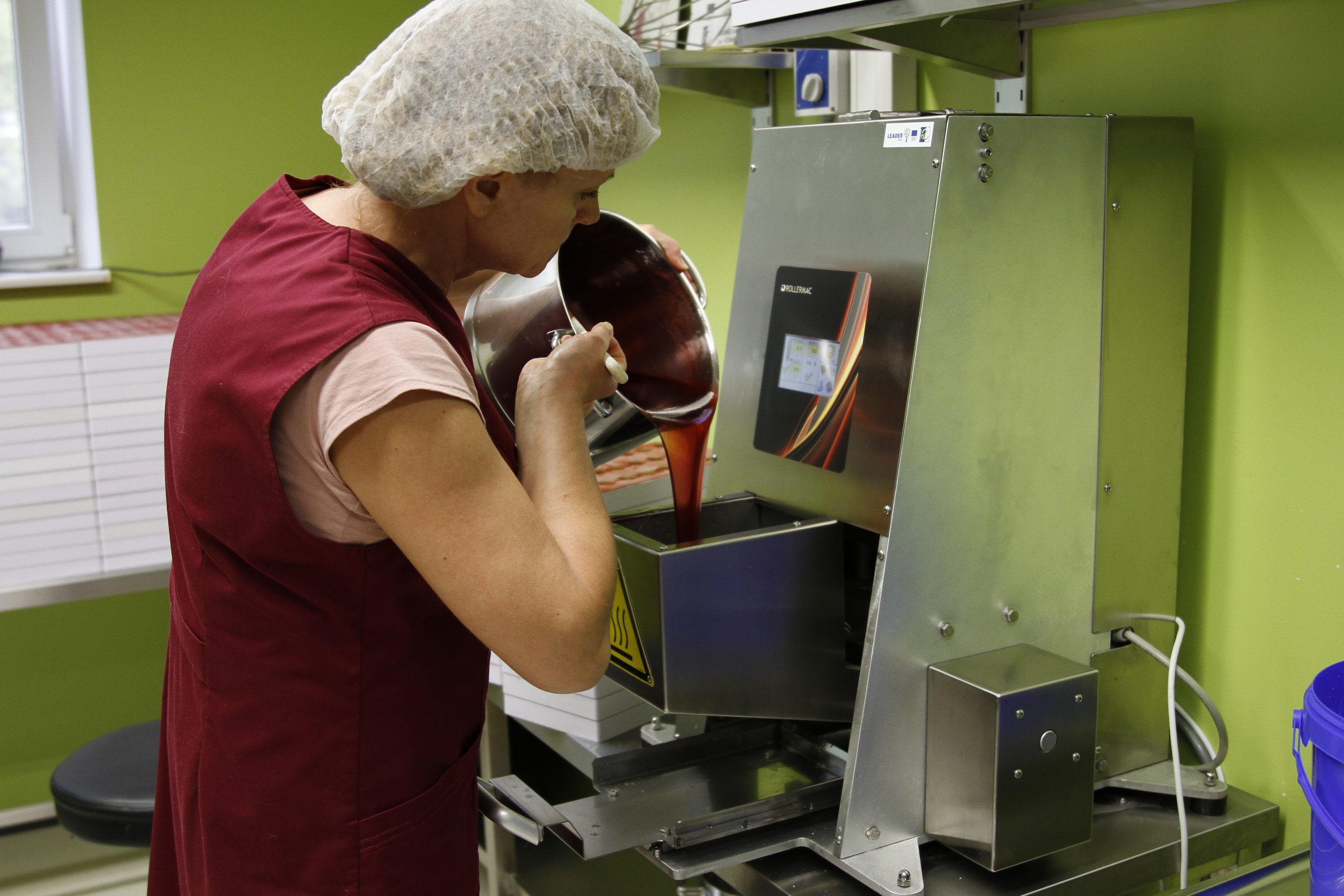
If you want to start improving product traceability in manufacturing, you can do so by:
1. Tracking and record-keeping
If you ever need to do a product recall, your priority is going to be identifying all the affected products, so you can better inform the public when you put out the notice.
Without proper records in place, locating the products will be difficult and will ultimately increase the cost of the product recall, not to mention the damage it’ll do to your brand.
Using a manufacturing software allows you to keep records of:
- Batch numbers and production dates
- Product order numbers
- Expiration dates
- Production timestamps
2. Supply chain visibility
Product traceability in manufacturing not only needs insights into your production, but improving product traceability also needs a better understanding of your supply chain.
Without these insights, you could put yourself in a position to have to initiate more recalls than you’d have to.
This can be due to a 3rd party business incorrectly handling your finished goods after they left your warehouse or a supplier sending you faulty materials or components.
You need to be able to trace your batches both forward to retailers as well as backward to your suppliers, by having a system in place that can quickly identify product’s history by their batch numbers.
3. Proactive monitoring
The longer you leave defective products in circulation, the more difficult it becomes to trace them as they make their way through your supply chain.
One of the goals of improving your product traceability is the ability to spot problems soon, so you can nip any potential issues in the bud and avoid them turning into an even bigger problems.
Being proactive becomes far easier if you’re using dedicated software that provides you with real-time information on production progress, so you can immediately see problems as soon as they appear.
4. Mock recalls
Finally, how do you improve at anything in life?
With practice, practice, and then some more practice.
Performing periodic mock recalls will allow you to determine how long it takes your business to recoup defective products.
When planning a mock recall, you should:
- Be realistic and use a scenario that could likely happen in your business
- Record everything that happens during the mock
- Review the results
- Assess your business’s effectiveness in handling the mock recall
Doing this will help you realize where you’re underperforming in product traceability and fix them now instead of struggling with a product recall later.
Now you know the benefits of traceability in manufacturing, and how to improve traceability, you need a system that can help you bring it all together.
Katana Cloud Inventory
Katana maximizes productivity and gives you an overview of your entire business, from the shop floor and beyond. Katana tracks time and material usage to provide you with the insights you need to grow. Learn more about it with a demo call.
Using Katana for product traceability
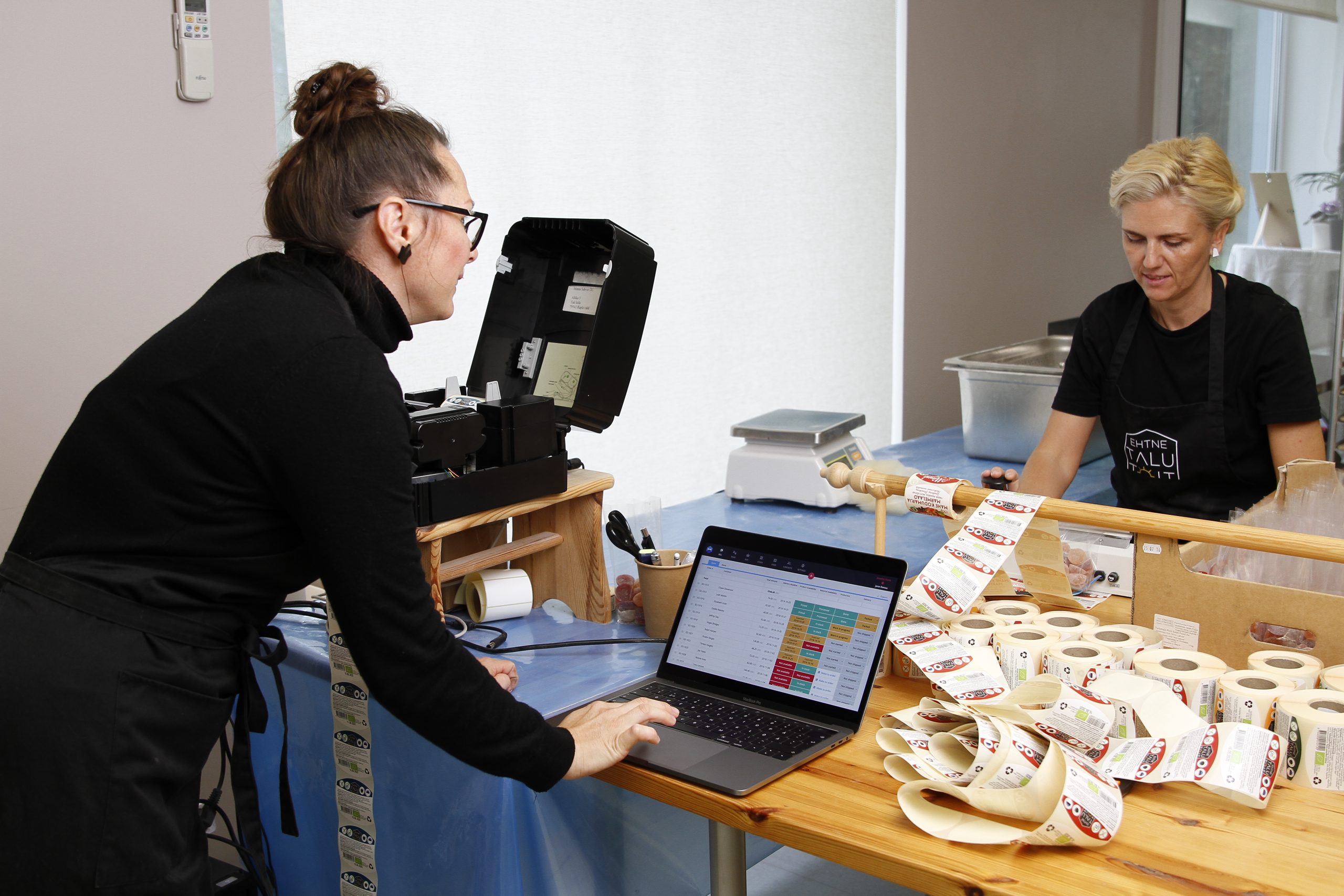
Katana traceability software is a tool for SME manufacturing businesses looking to upgrade their product traceability within their business.
Using Katana allows you to easily:
- Add batch/lot numbers
- Track expiry dates of products
- Track the best before date of products
- Trace any defective or contaminated products back to their batch
- Make your product recall process as smooth as possible
Want to find out how Katana can improve your workflows? Then check out our complete overview of how Katana works:
Better yet, why don’t you see for yourself? Schedule a free demo call with our sales team, see Katana in action, and learn how it will help improve your product traceability.
And that’s it for today, we hope you found this article on product traceability useful, and if you have any questions, please don’t hesitate to get in touch.
And until next time, happy inventory.
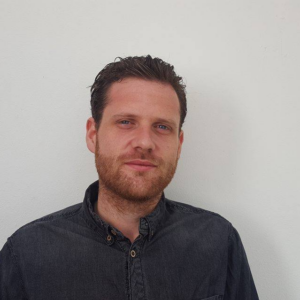
James Humphreys
Table of contents
Get inventory trends, news, and tips every month
Get visibility over your sales and stock
Wave goodbye to uncertainty with Katana Cloud Inventory — AI-powered for total inventory control