Takt time: optimize your production efficiency
Takt time is the secret weapon used by lean manufacturers. It requires a severe shift in the whole company’s mindset. But, if used wisely, it can take your manufacturing to a whole other level. What is takt time, how does it work, and why should you consider tracking it for your business? Let’s find out!
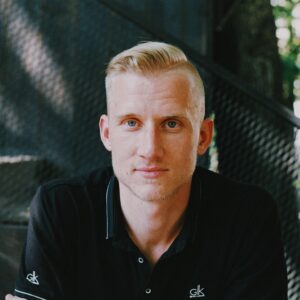
Henry Kivimaa
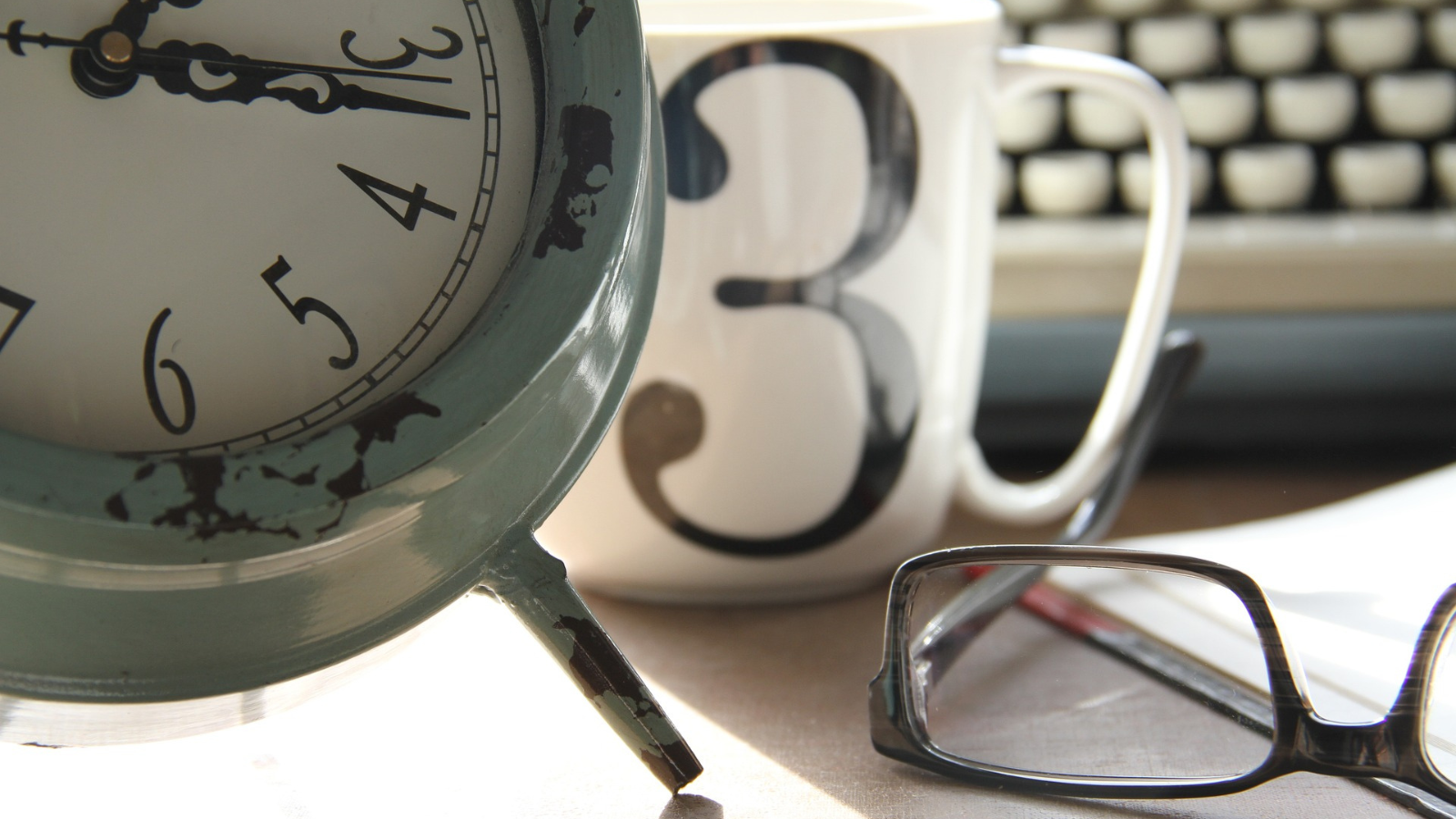
You know what they say: time is money! And when it comes to manufacturing, it’s essential to be smart in managing both. Companies must watch their budgets like hawks since wasting time can be just as harmful as wasting dollars. ItIt’sssential to make the most of every single minute.
Many businesses try to boost their efficiency and cut costs by tracking how much money they save and earn. But there’s another way to think about efficient manufacturing: from a lead time perspective. The idea is to figure out how much time it takes to make each product so that you can deliver it to your customers as fast as possible.
It’s all about balancing your production speed with the needs of your buyers. By timing things right, you can make sure that you’re churning out enough goods to keep your customers happy without wasting any resources. Finding that sweet spot is vital, and that’s where takt time comes into play.
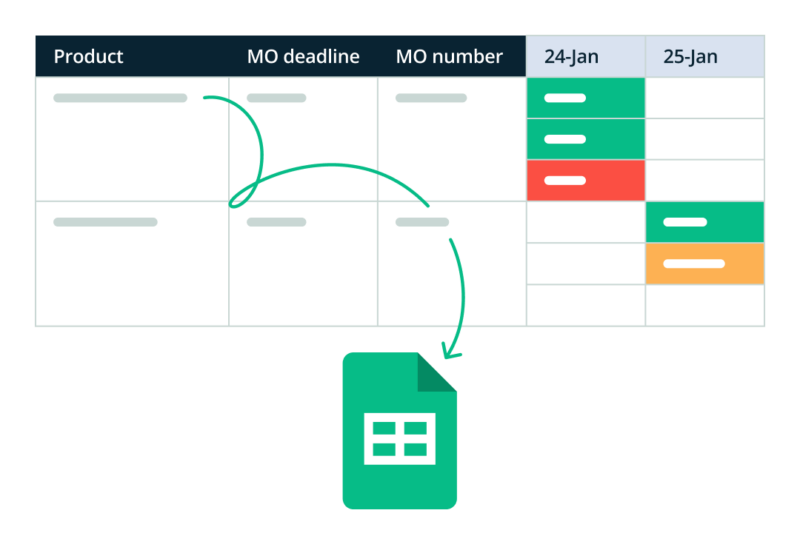
Download a free production schedule template
Download a free production schedule Excel template and start tackling your takt time effortlessly. Eliminate inefficiencies while maximizing productivity.
What is takt time?
Takt time in manufacturing is a lean manufacturing concept to figure out the best pace of production needed to meet customer demand. It is the maximum amount of time that can be spent on producing a unit of product to meet demand within a given period. Essentially, it’s the ideal manufacturing tempo to ensure efficiency and sustainability.
Takt time is an essential component of lean manufacturing because it helps create an optimal production process. It ensures that all team members understand their roles and responsibilities and that everyone works towards the same goal. Takt time also helps identify potential bottlenecks in the production process, which can be addressed to improve overall efficiency. Companies can reduce costs and increase profits by focusing on e minimizing lead time while maximizing efficiency.
Implementing takt time requires a shift from a traditional production mindset to a more customer-focused attitude. It requires continuous monitoring and adjusting of production processes to ensure that demand is being met. It also means openly communicating and collaborating among team members throughout all manufacturing steps. By adopting takt time as a key part of their manufacturing strategy, companies can increase efficiency, reduce waste, and ultimately provide better products and services to their customers.
Fun fact: The word “takt” comes from German and means the rhythm of music. Specifically, it indicates the number of beats within a certain period of time. It is believed to originate from the Latin word “tactus,” meaning “a touch or a feeling.”
What is the takt time formula?
Takt time is calculated using the following formula:
Takt time = Available production time / Customer demand
Available production time — The total time available for production during a given period, such as a day or a week. This may be adjusted for breaks, maintenance, and other non-production activities.
Customer demand — The amount of product required to meet customer needs within the same time period. This can be measured in units, dollars, or other relevant metrics.
An example of how takt time is calculated
For example, if a company has 480 minutes of available production time in a day, and the planned demand is 240 units per day, the takt time would be calculated as follows:
Takt time = 480 minutes / 240 units = 2 minutes per unit
This means the production team should aim to produce one product unit every 2 minutes to meet customer demand. By using takt time as a guide, the production team can ensure that they deliver the right amount of product at the right time while minimizing waste and maximizing efficiency.
Overproduction
Overproduction happens when your production exceeds the previously calculated takt time, meaning you manufacture items faster than the optimal time. It can have both positive and negative consequences.
On the positive side, producing more can result in higher inventory levels, which can help meet unexpectedly high demand. Additionally, it can also lead to increased productivity, reduced lead times, and improved efficiency.
However, what can be seen as safety stock, can turn out to be dead stock in the end. Overproduction can lead to excess inventory and manufacturing waste, which ties up resources and results in increased costs. It can also lead to overburdened employees and an increased risk of defects and errors. In the end, the customer wins in terms of delivery time but receives a less-than-perfect product, eliminating the whole purpose of tracking takt time in the first place.
Underproduction
When a company underproduces, it means that they produce fewer items in the determined takt time or that creating one product takes longer than planned. There are positive and negative aspects to consider in this case.
One potential positive outcome is that workers may have more time to focus on quality, safety, and other important aspects of the production process. If employees are not rushed and can take their time to ensure that each product is of high quality, it can lead to happier clients and better customer loyalty. Also, by not rushing the production process, workers may be less prone to making mistakes or causing accidents, which can improve safety and reduce risks for the workers as well as the company.
However, the negative aspects of not meeting the takt time far outweigh the positive ones. When production is too slow, it can result in delayed orders and lost sales, which can have a significant impact on the company’s finances and reputation. Slow production can also lead to increased costs associated with labor, equipment, and materials, which decreases profitability. This is further amplified if the slow output continues for a more extended period of time, leading to a severe revenue decrease.
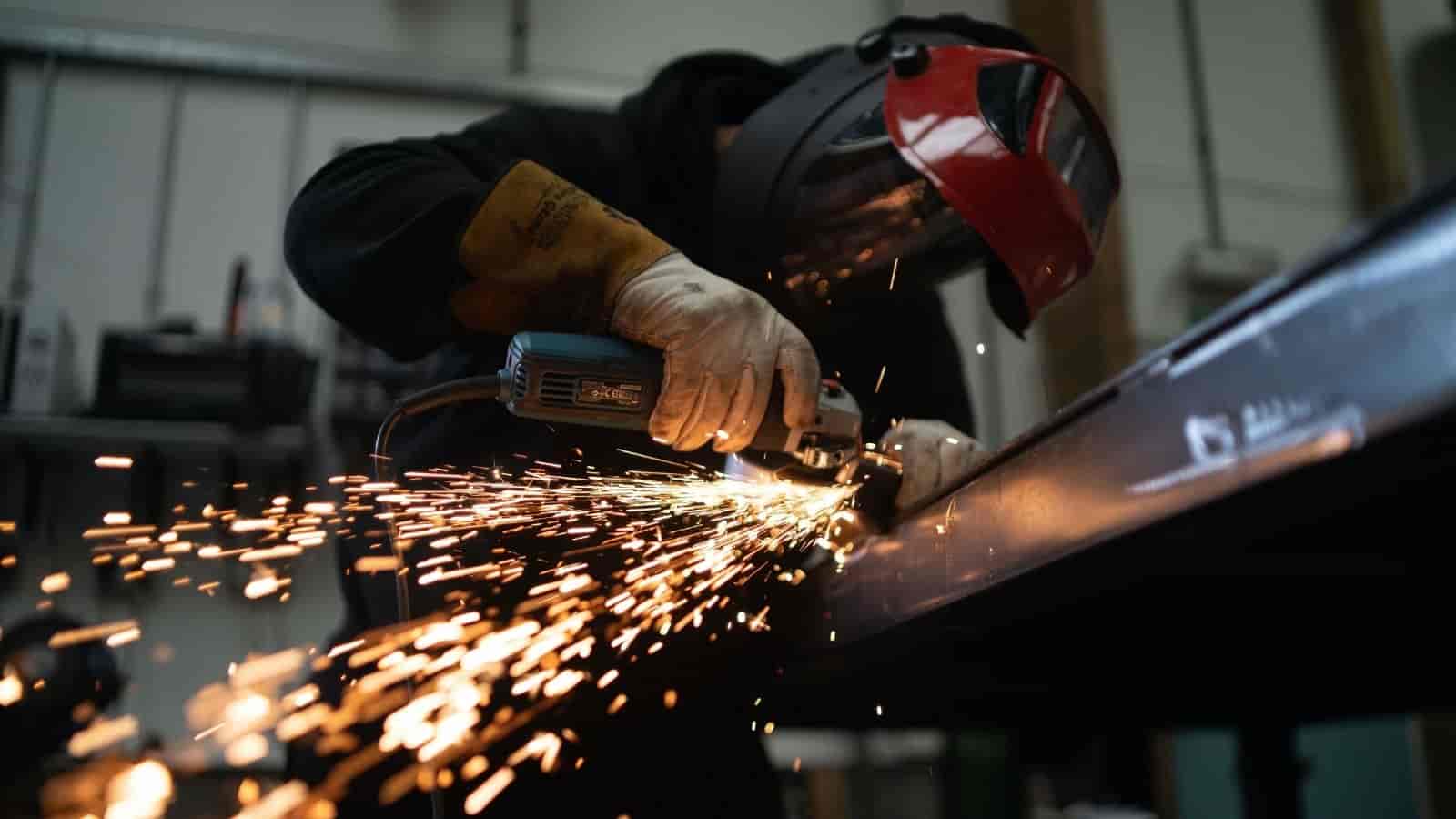
Takt time vs. cycle time
Now that we’ve established what takt time is, it’s time to refresh your knowledge of manufacturing cycle time too.
As its name hints, cycle time is the time it takes to complete one manufacturing process cycle. This could mean manufacturing operations like welding and cutting or the overall production process — it depends on which task or cycle you track.
In simpler terms, cycle time is like running at a race track. Whether you define a cycle as one lap or the entire race, cycle time means how long it takes to get from start to finish. Now, takt time is calculated based on your personal goal or what your coach demands from you. If you have 30 minutes to run five laps, then that means a pace of 6min/lap. Run any slower, and you won’t make it in time. Run too fast, and you’ll be out of breath, wear yourself out, and potentially quit even before the race is over.
In summary, takt time is an estimate of the optimal rate of manufacturing to achieve the best outcomes while minimizing losses. On the other hand, cycle time refers to the actual time taken to complete a task. Although these terms are connected, they do not have the same meaning.
How to keep up with takt time?
Once you’ve calculated the takt time for your business, the next step is to follow it in the day-to-day work. In order to reach takt time, you need to take a systematic approach to optimize your production process.
Identify and eliminate waste
Analyze your production process to determine wasteful business areas, such as overproduction, downtime, unnecessary activities, excess inventory, and defects. Reducing the waste of all your resources will help cut down cycle time and increase overall effectiveness.
Improve your process
Implement improvements in your processes to eliminate waste, reduce cycle time, and increase productivity. This can include automation of manufacturing processes, optimized planning and scheduling, and documenting standard work procedures.
Observe and adjust
Monitor your production process regularly to ensure you are meeting takt time. If you are falling behind, adjust your strategy accordingly or figure out better ways to tackle the bottlenecks. The sooner you notice issues and delays, the easier it is to find new and better solutions.
What are the benefits of using takt time?
Implementing takt time and transitioning the company’s focus from being production and result-driven to more customer and demand-oriented can be challenging and may take some time to adapt to the new approach. However, if done correctly, it can be a huge game changer and help take your business to the next level.
Here are some of the benefits that implementing takt time can bring.
Better demand planning
Takt time helps ensure that the production process is appropriately synchronized with customer demand. Having a target pace for production will help improve the process to meet your buyers’ needs more efficiently.
Reduced waste
By implementing takt time, production processes can be adjusted to reduce waste and optimize efficiency. Understanding the rate at which products need to be produced makes it possible to identify areas of waste and implement changes to reduce or eliminate them.
Improved productivity
Takt time can be a tool to improve productivity by setting clear goals and expectations for workers and manufacturing processes. By providing a clear target rate for production, managers can focus their efforts on streamlining their operations, which can improve overall productivity.
Enhanced quality
Takt time can help ensure that goods are produced to a consistent quality standard. Establishing a tempo for manufacturing will help teams focus on delivering products that easily pass quality control and meet customer needs.
Increased flexibility
Takt time can help organizations be more adaptable and respond to changes in customer demand more flexibly. By following a target rate for production, organizations can quickly adjust production processes to meet changes in buyer trends, which can help reduce lead times and improve customer satisfaction.
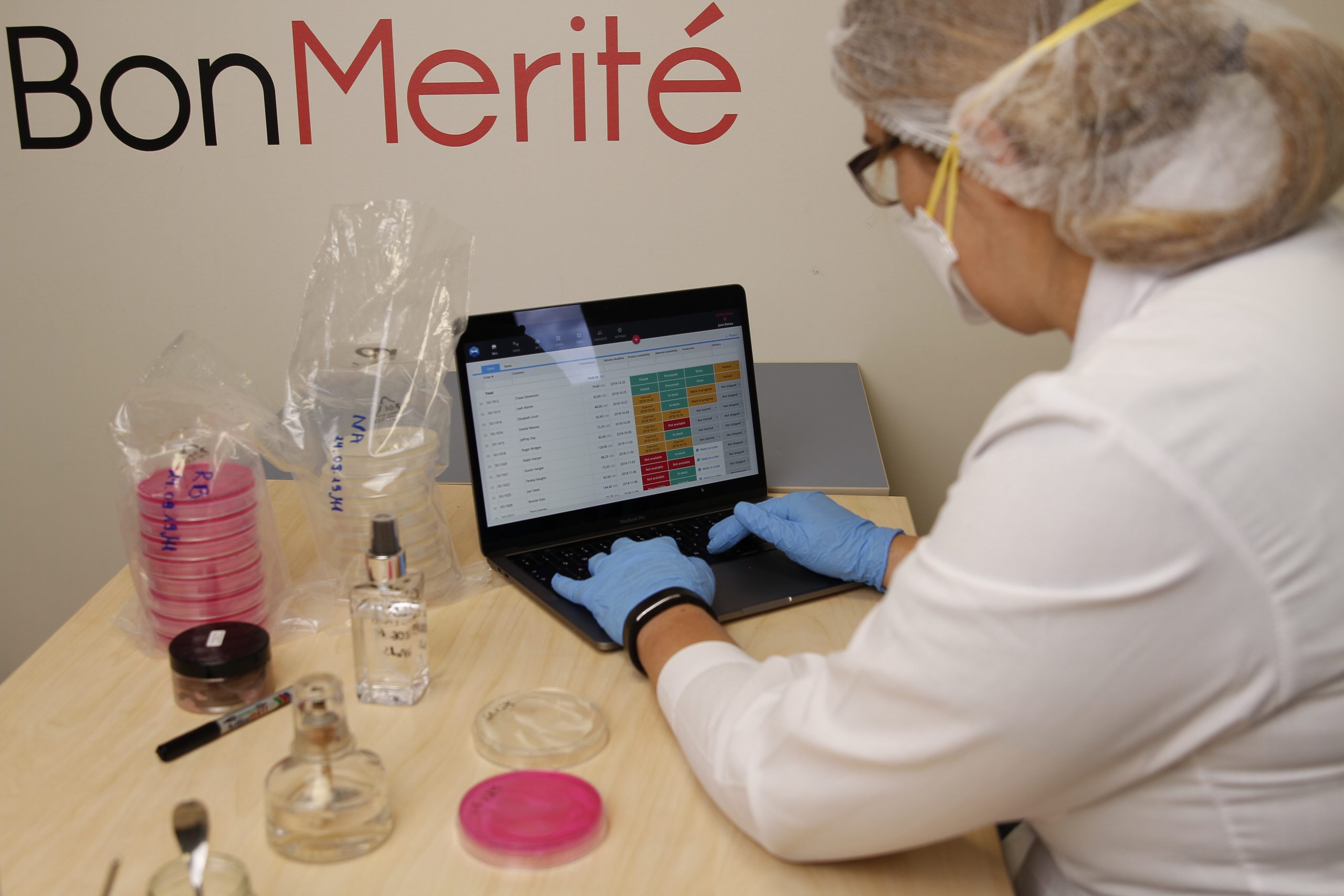
What are the challenges of using takt time?
While the benefits of takt time make it seem worth the hassle, some battles must be won for it to work out. Once you’ve figured out how to tackle these issues, you’ll be left with the benefits to enjoy.
Here are some challenges that you may want to consider before starting your takt time journey.
Demand fluctuations
Takt time assumes that demand for a product is consistent over time. However, in reality, customer demand can be unpredictable and may vary significantly from day to day or even hour to hour. This can make maintaining a consistent production flow difficult, leading to issues with overproduction or underproduction.
Equipment breakdowns
If equipment breaks down, it can disrupt the production process and impact the ability to meet takt time goals. Downtime can lead to delays, increased costs, and reduced efficiency, potentially resulting in decreased customer satisfaction.
Worker skill level
Takt time assumes that all teams are trained and skilled enough to produce a product within the calculated time. However, if the workers lack the necessary skills or experience, they may struggle to meet takt time requirements, leading to quality issues or delays.
Inefficient processes
Inefficient processes can make it difficult to meet takt time requirements. If a process is not optimized or moving from one step to another is challenging, completing them may take longer than expected, leading to bottlenecks and delays.
Changes in product design
If a product’s design is changed or even subtly tweaked, it can impact takt time requirements. This can require adjustments to the production process, which can be time-consuming and costly and may even call for extra training for the workers.
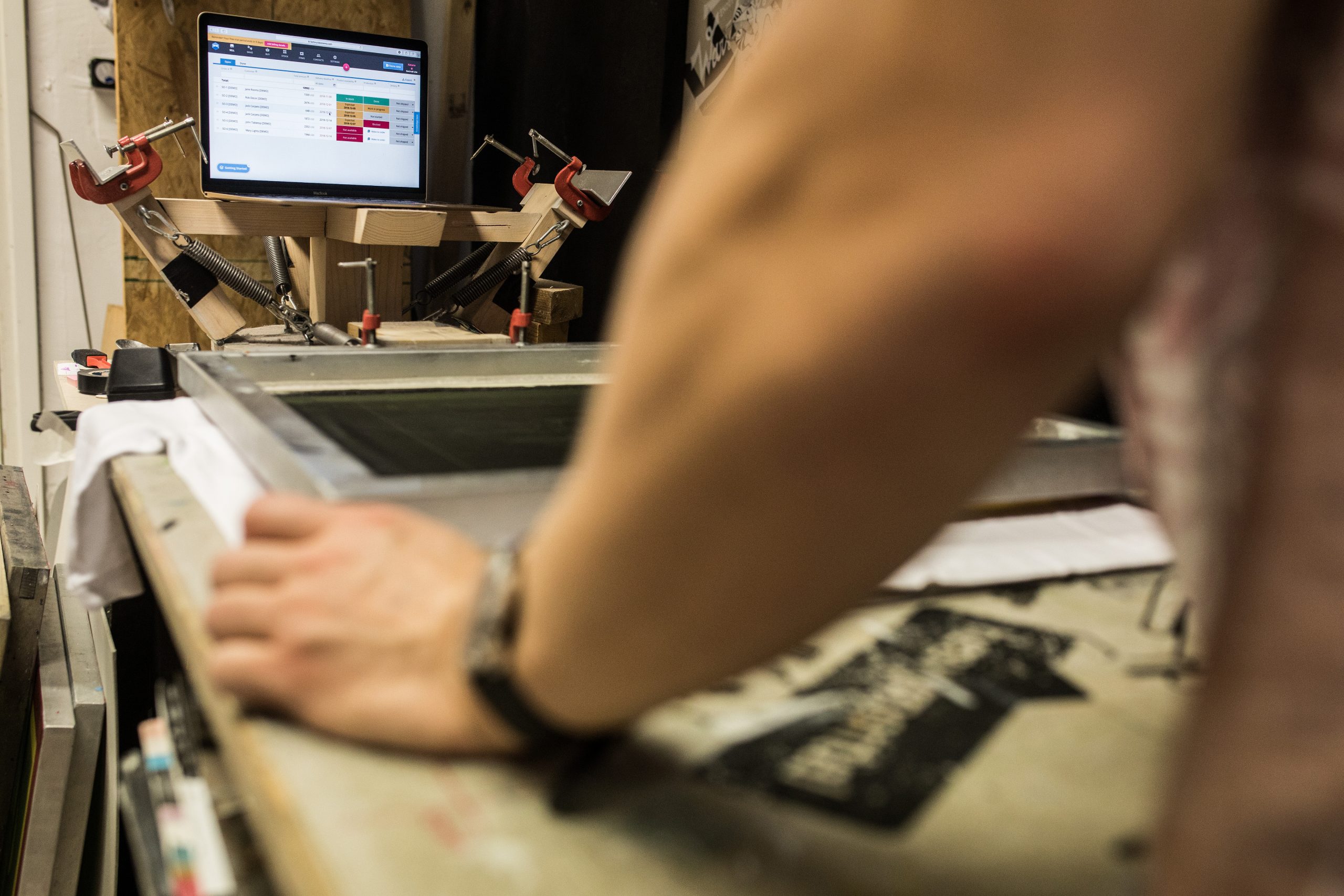
Katana and takt time management
Katana is a cloud-based inventory platform designed to help manufacturers run their businesses more smoothly and efficiently. It also has many beneficial features for tracking and keeping up with takt time.
Production scheduling
Katana allows managers to create tasks for their shop-level workers and adjust them if necessary. You can reprioritize assignments by dragging and dropping them on the task list based on demand, available materials, and other business decisions. This will trigger the automatic reallocation of supplies.
Operators can view, edit and complete their assignments via the Shop Floor App, which is accessible on any smart device. Working on tasks in the app will automatically trigger changes in Katana and update operations and inventory levels in real time.
Time tracking
Katana helps you set up estimates for each task as well as track the actual cycle time spent on them. It provides real-time data on production times, allowing for optimization and improvements to be made to the production process.
If your production rate falls behind takt time, you can use Katana’s data to identify the bottlenecks and take steps to address them. Optimizing your manufacturing process using time tracking in Katana can improve profitability, reduce lead times, and ensure customer satisfaction by meeting demand more efficiently.
Inventory management
Keep an eye on your stock — from raw materials to work-in-progress to finished goods — all in one place. Inventory management can help identify any bottlenecks and delays in production and gives you a chance to tackle them as soon as possible.
Tracking raw materials will help you keep up with the production schedule, avoid running out of supplies, and minimize the risk of delays in manufacturing. Set reorder points to be prepared to restock components before they are all used up.
Data and reporting
Katana offers various insights into all areas of the business. This data can be beneficial for planning for the future as well as conducting a manufacturing analysis of what has already been achieved:
- Sales insights give a good overview of customer demand and trends
- Production reports help identify potential bottlenecks and areas for improvement
- Inventory information can be used to optimize material and product flows
- Time-tracking reports provide a detailed overview of how you’ve been keeping up with takt time so far and which areas need improvement
Integrations
Katana has partnered with several platforms to offer an all-in-one solution to manufacturers. There are integrations for all areas of the business — from accounting to e-commerce, automation to shipping.
Suppose you’ve already found software that works for you and would like to keep using that. In that case, Katana’s open API allows you to build it into your space to create a custom workflow that specifically serves your business.
And that’s it — takt time in a nutshell. By conquering the challenges and taking on this journey into a more customer-oriented manufacturing world, you can be sure to find treasures making it worth your while.
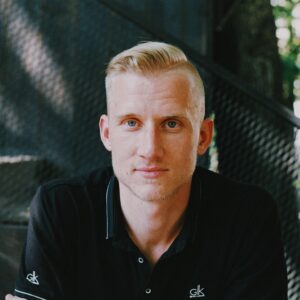
Henry Kivimaa
Table of contents
Get inventory trends, news, and tips every month
Get visibility over your sales and stock
Wave goodbye to uncertainty with Katana Cloud Inventory — AI-powered for total inventory control