Setting up production scheduling software for QuickBooks
Are you using QuickBooks Online for your accounting? It’s a good tool, but wouldn’t it be great if it could help you with other tasks too?
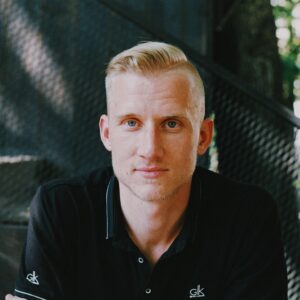
Henry Kivimaa
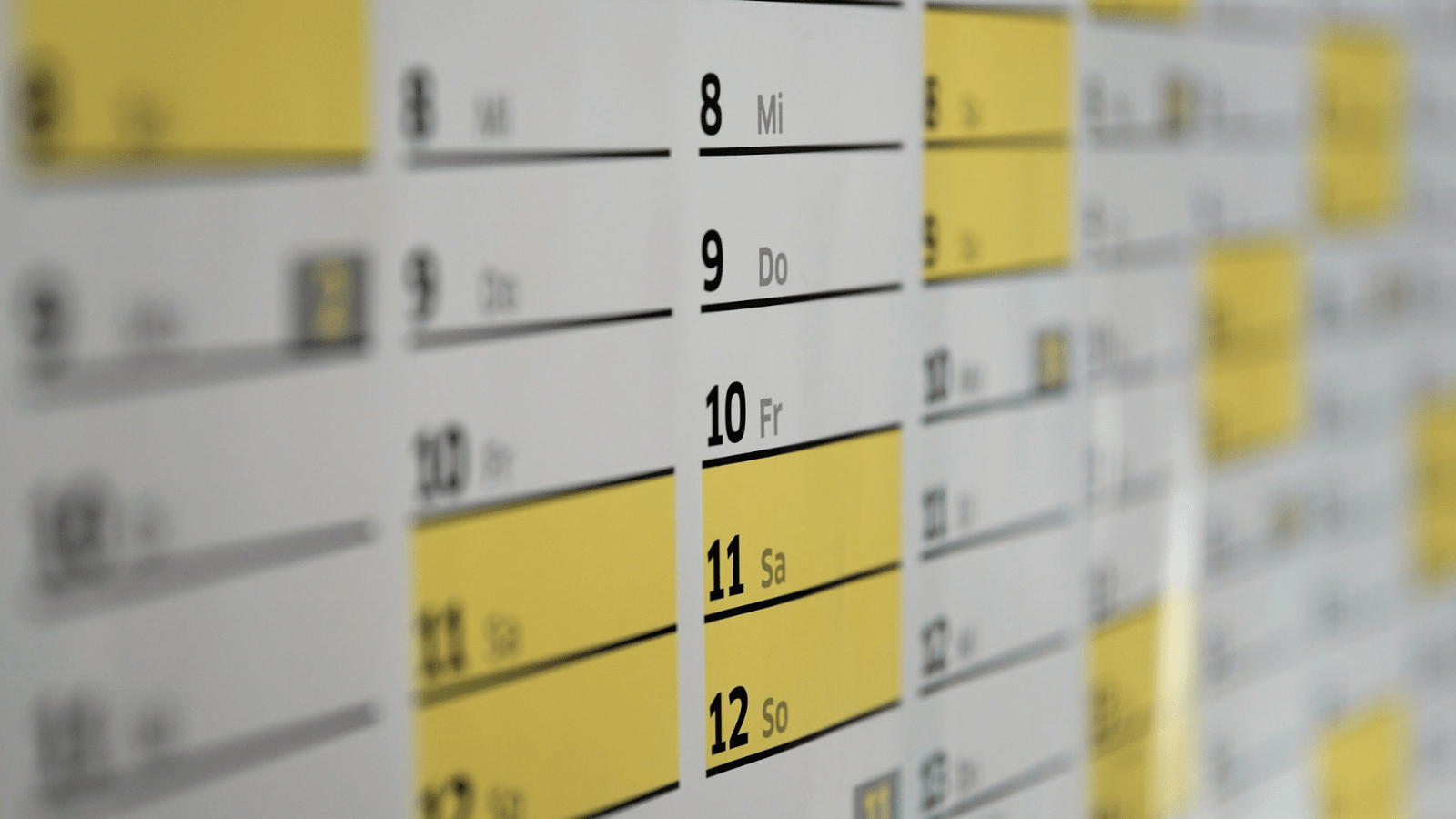
QuickBooks is an ecosystem of tools to keep all your bookkeeping in one system. It can track expenses and income, handle tax liabilities and manage company payroll. As a manufacturer, it’s essential to have your finances under control and QuickBooks helps you take care of that.
Another responsibility most manufacturers have is scheduling their production process — ensuring that your business runs like a well-oiled machine and every task gets done on time. This has probably left you wondering if QuickBooks can do production scheduling.
Does QuickBooks have a scheduling system?
The truth is that there’s no scheduling software for QuickBooks. QuickBooks Desktop and Online are primarily designed as accounting solutions with a focus on managing financial transactions, reporting, and budgeting. Some QuickBooks production scheduling add-ons, like QuickBooks Time, allow users to implement time-tracking software.
QuickBooks Enterprise includes advanced inventory management features, such as tracking inventory levels and costs, creating purchase orders, and generating sales orders. However, it too does not have all the advanced production planning and scheduling features found in specialized manufacturing software.
So, how exactly do other manufacturers bridge this gap?
Many turn to third-party integrations such as Katana, which allows them to sync apps to use QuickBooks Online (QBO) for bookkeeping, and Katana as a manufacturing software that also offers manufacturing scheduling, among many other features. Katana’s native QBO integration creates an all-in-one system where you can manage all aspects of your business.
Imagine having to jump back and forth between different software to get something done. Not only is it a waste of time, but it’s also a major inconvenience. Katana’s QBO integration fixes that issue, increases the efficiency of your manufacturing, and gives you the tools to start implementing QuickBooks visual production scheduling.
Try production scheduling with Katana
Book a demo to get all your questions answered regarding Katana’s features, integrations, pricing, and more.
What should I look for when integrating production scheduling software with QuickBooks?
There are several elements to keep in mind when integrating QuickBooks with production scheduling software:
- Data compatibility: The software should be able to easily import and export data from QuickBooks, including inventory, customer, and vendor information
- Real-time synchronization: The software should be able to synchronize data in real time so that changes made in one system are automatically reflected in the other
- Automated data entry: The software should be able to automate data entry, such as creating invoices and purchase orders in QuickBooks, based on production schedule data
- Advanced inventory management: The software should have advanced inventory management capabilities, such as tracking inventory levels, managing stockouts, and generating purchase orders
- Production scheduling features: The software should have robust production scheduling features, such as bill of materials, routing, capacity planning, and shop floor control
- Reporting and analytics: The software should provide detailed reports and analytics on production scheduling, inventory, and financial data so that you can make informed business decisions
- Ease of use and customer support: The software should be easy to use and have good customer support
It’s always best to research and compare different software options and make sure that the software meets your specific business needs and requirements before making a final decision.
What are the 4 components of production scheduling?
There are many ways to approach schedules and different ideas on what they should include. Here are the four areas that you need to consider:
- Production Planning
- Routing
- Scheduling
- Execution
What do these points mean for your business?
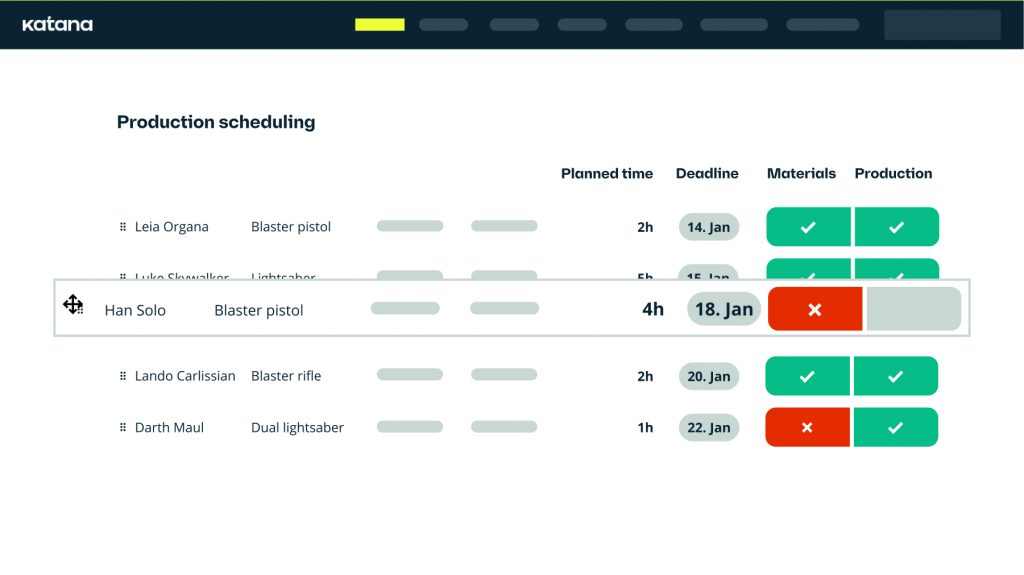
1. Production planning
Production planning is what encompasses all the steps that come before a product is created. It details how production and making the final product will be achieved. That means you have to figure out all the resources that go into manufacturing:
- Materials — this includes all materials and supplies that go into creating your product
- Team — all the people involved in manufacturing, including your employees and supply partners
- Tools — whether you handcraft items or use industrial machinery
- Processes — every step your items go through to go from ingredients to a final product
It’s essential you know what you’re making and how you’re making it before starting to actually make it.
2. Routing
A manufacturing route means the journey your precious item takes when being transformed from the raw material into the final product. Once you’ve mapped out the manufacturing route, it’s easier for the entire team to organize their workflow and collaborate on different processes.
3. Scheduling
Production scheduling means planning all steps ahead and creating a timeline for each process. A schedule helps your team stay within the correct timeframe. No more running around the shop floor trying to chase up orders which are behind schedule.
4. Execution
Now is the time to start your manufacturing process. While your teams are busy executing the plans you’ve previously put together, it is your job to support them and provide them with the necessary tools.
What does production scheduling include?
A production schedule should include all details about the manufacturing process. In many ways, it is like a quality control checklist, but instead of perfecting the product, the main purpose of scheduling is to optimize the production process.
There are a few things to keep in mind when creating a production schedule:
- Efficiency — streamline as much as possible and use your resources wisely
- Productivity — keep your manufacturing going at all times
- Agility — expect the unexpected and be quick to respond to a crisis
- Accuracy — set goals and make sure to stick to them
Keep these four principles in mind when putting together your production schedule. That guarantees a smooth and successful workflow that benefits not only your business but also the customers and your team.
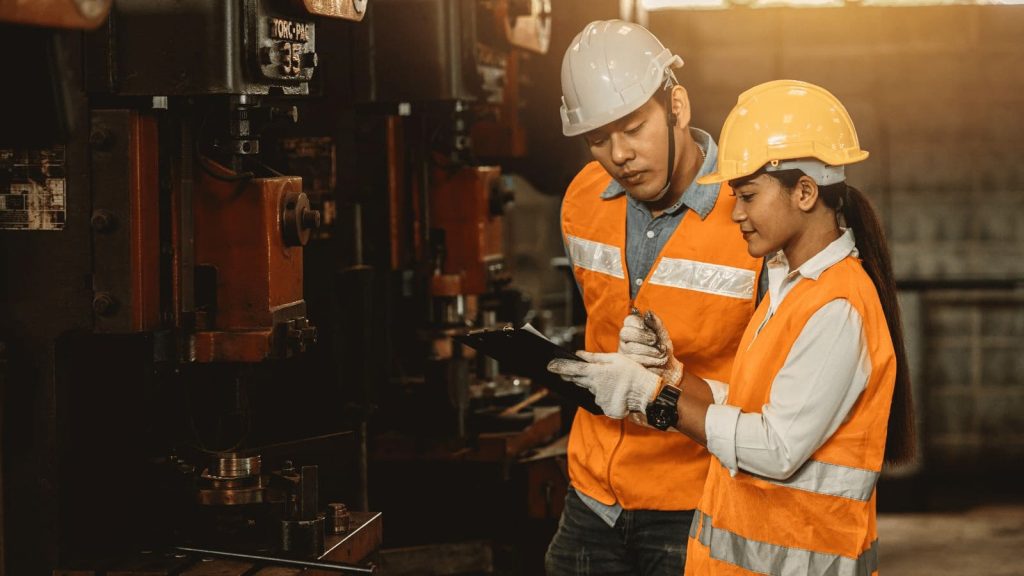
How do you run a production schedule?
Once you’ve put together a complete schedule, it’s time to put it into action. In order to fully benefit from your plan, you need to stick to it as much as possible. If you want your schedule to work out in your favor, make sure you:
- Assign tasks to appropriate personnel
- Ensure enough resources are available
- Track progress on each task
- Report any issues that arise along the way
All steps should be communicated clearly to everyone involved to guarantee a successful execution of the production schedule.
1. Assign tasks to appropriate personnel
Before starting manufacturing, all teams should be trained and informed about their expected results. A team is only as strong as its weakest link, so to avoid mistakes, everyone should be on the same page about the final result and the required standards.
2. Ensure enough resources are available
Once everyone knows their tasks, make sure they also have the necessary tools to fulfill them. That could mean actual tools like machines or equipment but also satisfying working conditions and enough time to perform operations to your standards.
3. Track progress on each task
It’s good to know the exact time consumption per task. For an ongoing production, it gives you transparency on how you’re sticking to the plan. It will also help you arrange future schedules even better, knowing exactly how much time all your processes take.
4. Report any issues that arise along the way
Sometimes mistakes happen, machines fail, or a force majeure event creates a delay in your production. What makes or breaks the schedule is how you deal with unexpected issues. Keep communicating with teams and find workarounds if possible.
Switching from QuickBooks Desktop to Online
Moving to QBO and worried about missing manufacturing features? Watch Katana and Intuit’s joint webinar that covers the transition, why you should do it, and how Katana bridges the gaps for manufacturers.
How to integrate QuickBooks Online with Katana?
Setting up QuickBooks Online (QBO) and Katana could not be any easier (we tried, it wasn’t possible).
Go to Settings screen > Integrations tab and find QuickBooks Online in the list of integrations. Follow the on-screen instructions throughout the setup process and Katana will do the rest.
How does production scheduling work in Katana?
In Katana, you can track manufacturing on two levels — Manufacturing order (MO) and Production operations level.
Manufacturing order level
If you go to Make screen > Schedule tab, you’ll be able to change the status of an MO. Editing the status enables different inventory actions or triggers inventory changes.
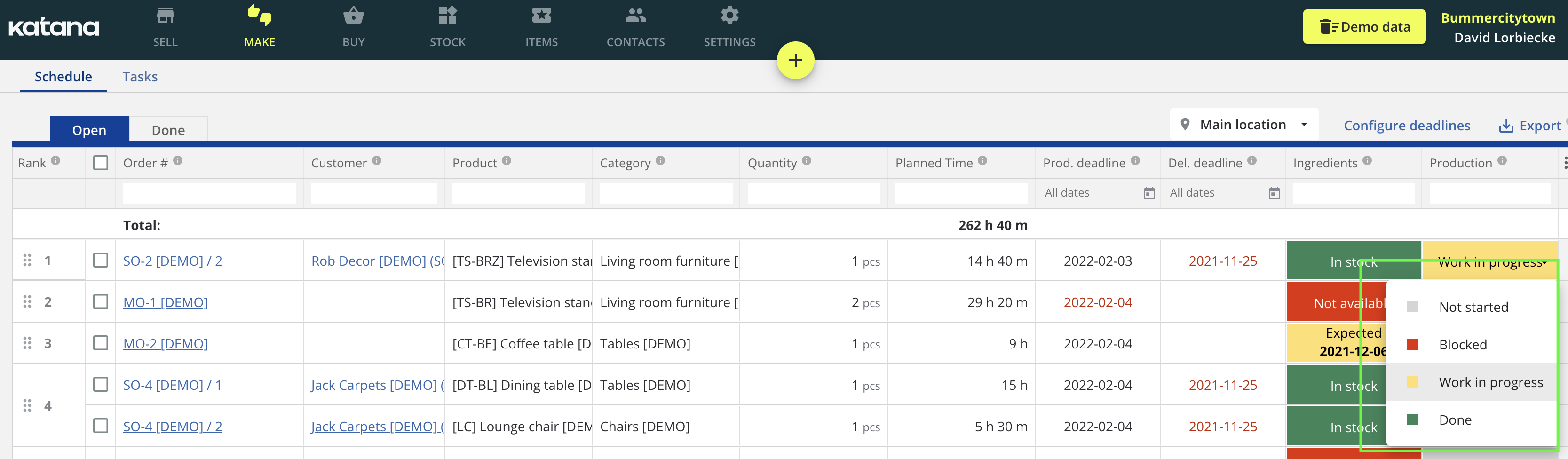
Production operations level
Scheduling on the production operations level is more in-depth and offers more options. To do that, go to Make screen > Tasks tab, where you can access all tasks, whether or not they’re assigned.
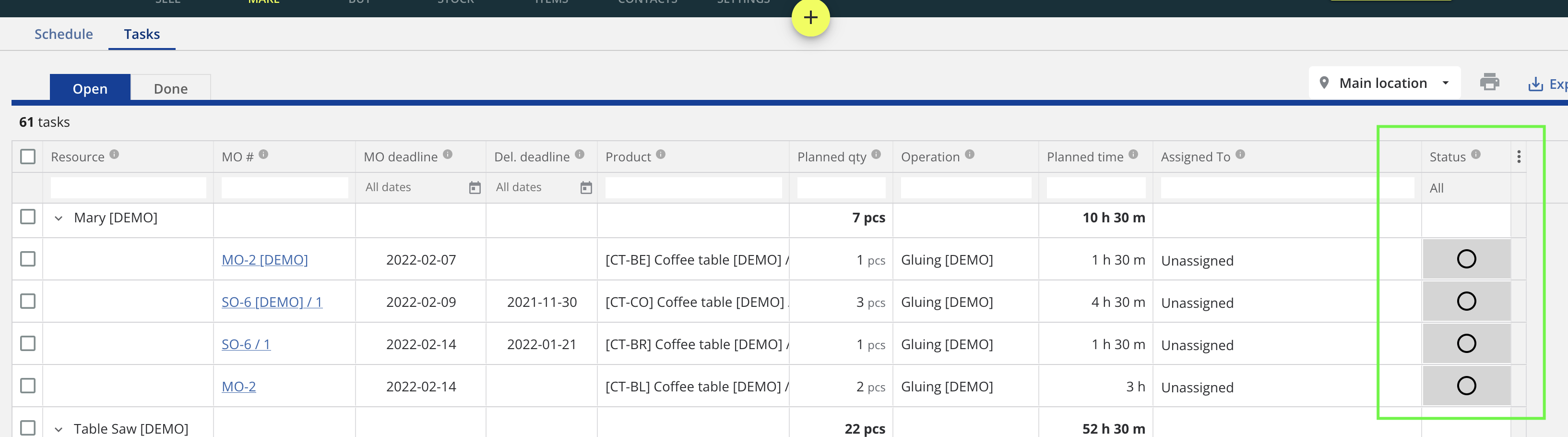
Tasks are visible in Katana as well as Katana’s Shop Floor App, allowing floor-level teams to make changes from their smart devices.
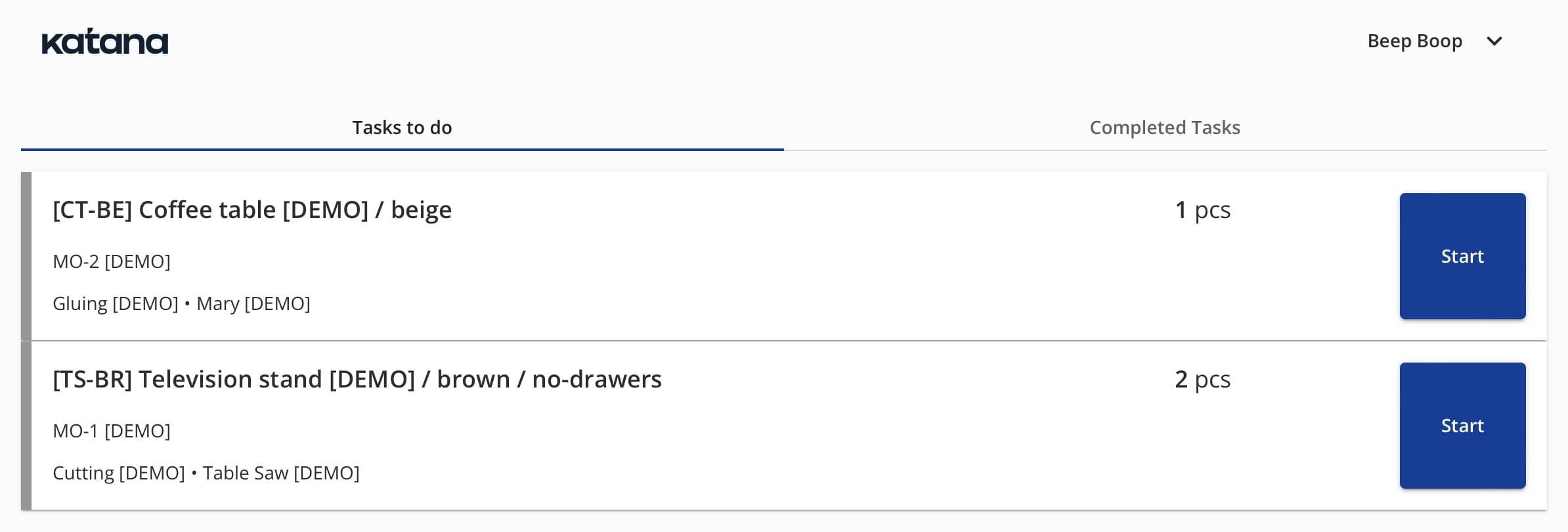
Production scheduling with Katana is a piece of cake, and the QBO integration for accounting is the icing on top.
Get total QuickBooks production control with Katana
Manage your production and accounting in one place and optimize your processes.
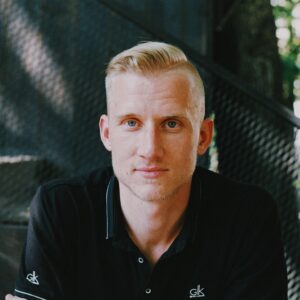
Henry Kivimaa
Table of contents
Get inventory trends, news, and tips every month
Get visibility over your sales and stock
Wave goodbye to uncertainty with Katana Cloud Inventory — AI-powered for total inventory control