Manufacturing inventory management
Manufacturing inventory management requires careful planning due to the various types of inventory involved. It’s also crucial to consider the specific production processes to ensure a smooth flow of materials through each stage.
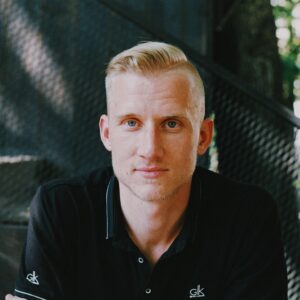
Henry Kivimaa
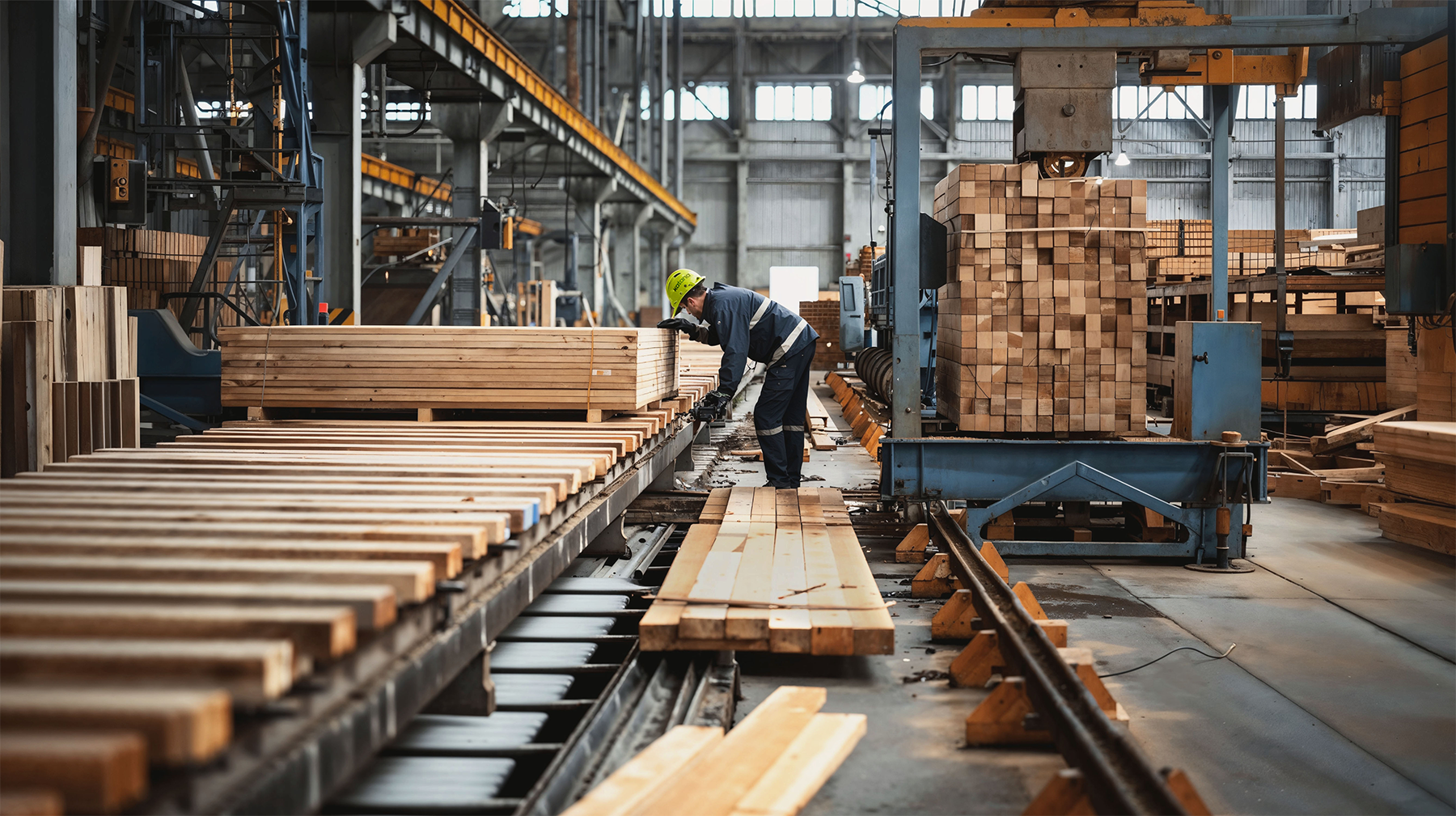
When talking about inventory management, people unusually picture a warehouse with loads of shelving space and a forklift driving around looking for the right package. However, inventory management is much more complex than just stacking boxes on a shelf and retrieving them at a later time.
Managing inventory can also vary wildly depending on the exact business type, the industry, the company’s size, the products it sells, and much more. A small frozen yogurt retailer can’t follow the same methods as an international steel beam manufacturer.
Today, we explore manufacturing inventory management. We explain what it is, what’s special about it, what are some tested and tried strategies, and go over some tips and techniques to help you boost your efficiency in this sector.
First, Let’s answer the question of what manufacturing inventory management is and what sets it apart.
What is manufacturing inventory management?
Manufacturing inventory management is the process of managing the inventory a manufacturing company holds. What sets manufacturing or production inventory management apart is the fact that besides goods waiting to be sold, a manufacturing company also holds other types of inventory.
Most manufacturing companies need to manage four types of stock:
- Raw materials
- Work-in-progress (WIP)
- Finished goods
- Maintenance, repair, operations (MRO)
Let’s dive into these next.
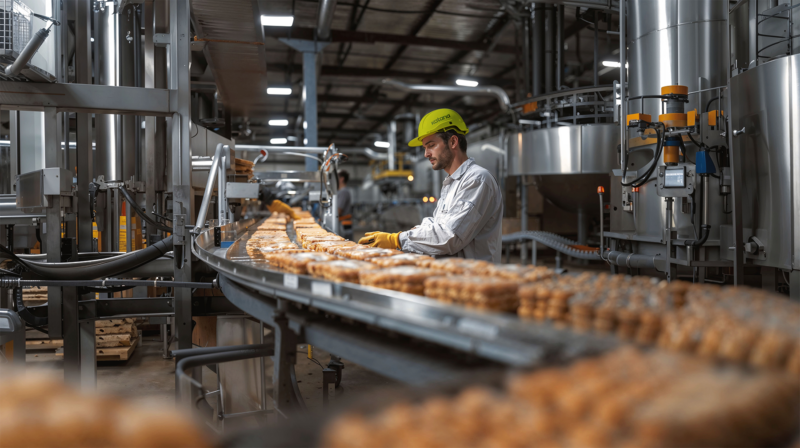
Inventory types used in manufacturing
As mentioned, production companies mostly need to manage four types of inventory. Below you’ll find detailed descriptions with examples and some specifics to consider when managing them.
Raw materials
Raw materials inventory consists of all the materials and components a company uses to produce its goods. This includes all the ingredients, parts, and substances a manufacturer gets from their supplier that haven’t yet undergone any form of transformation within the manufacturing process. These can include:
- Sheet metal
- Microchips
- Fabric
- Flour
- Lumber
For maximum efficiency, manufacturers can store raw materials close to the loading dock where they receive them. This helps store the materials more quickly and reduces the risk of injuries by shortening the distance workers need to transport them.
For the same reasons, facilities can be designed to move raw materials through the manufacturing processes in a linear flow from one side of the building to the next. Manufacturers can minimize unnecessary movement and streamline the production process by designing the layout to facilitate a smooth progression from raw materials storage to production areas.
Want to take full control of your raw materials?
Katana’s cloud-based inventory management software gives you a full overview of all your inventory types and makes managing it all a breeze.
Work-in-progress
Work-in-progress is another type of inventory specific to manufacturers. These are all the items that have gone through some form of processing but have not yet been finished. WIP inventory can include:
- Partially assembled products
- Sub-assemblies
- Components undergoing testing or quality checks
- Goods waiting for further processing stages, such as painting or finishing
- Items in various stages of assembly on the production line
Work-in-progress inventory represents the intermediary state between raw materials and finished goods. The next one on the list is, you guessed it — finished goods.
Finished goods
These are all the items that have been completed and are ready to be sold to your customers. Finished goods inventory includes fully manufactured products waiting to be sold and items waiting for shipment. Usually, the best place to store them is right near the loading dock, where these can be quickly loaded onto trucks.
MRO
Finally, we have MRO inventory. As the name suggests, it includes every item used for maintenance, repair, and operations within the manufacturing facility. MRO inventory supports the production process but is not directly part of the final product. This inventory can include:
- Maintenance supplies such as lubricants, cleaning agents, and tools
- Repair parts and spare components for machinery and equipment
- Office supplies and safety equipment
- Items needed for routine facility upkeep, such as light bulbs and air filters
MRO inventory can often get overlooked, but it’s important to manage it properly to ensure you have everything required to maintain a smooth production flow. Regularly organizing and counting your MRO inventory is much less disruptive than having to stop your machines due to grease running low or a screw coming loose.
As you can see, manufacturing inventory management adds an extra layer of complexity, as there are different types of stock to consider. In the next section, we go over how you can design your warehouse layout to minimize waste and increase productivity.
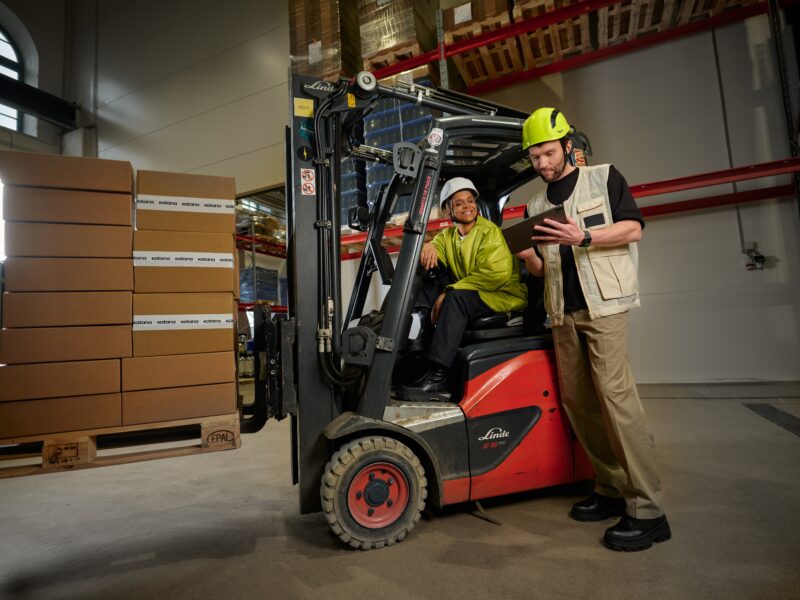
Warehouse layout
We’ve already talked about positioning certain types of inventory near loading docks, but there’s a lot more to it than that. Organizing an efficient warehouse layout is essential for any manufacturing operation. Carefully planning the placement of machines, shelves, and workstations allows manufacturers to streamline their processes, reduce unnecessary movement, and maximize productivity. Here are some key considerations to keep in mind when designing your warehouse layout.
Prioritize flow efficiency
Just as you should store raw materials near the loading dock for quick access, you should design the entire warehouse to facilitate a smooth flow of materials and products. This means positioning machines and workstations in a logical sequence that mirrors the steps in the manufacturing process. For instance, raw materials should move in a linear path from receiving to production to shipping area, minimizing backtracking and confusion.
Create designated zones
Dividing the warehouse into clearly defined zones can help keep things organized and improve efficiency. Common zones include:
- Raw materials storage — Located near the loading dock for quick unloading and access
- Work-in-progress areas — Situated close to production lines to store items currently being processed
- Finished goods storage — Positioned near the shipping area for easy loading onto trucks
- MRO supplies — Kept in a central location where maintenance personnel can easily access them without disrupting production
Optimize shelf placement
Shelving should be arranged to maximize space and accessibility. Vertical shelving can be particularly effective, allowing you to store more items without using additional floor space. Be sure to label shelves clearly and group similar items together to make retrieval quick and easy. Additionally, frequently used materials should be placed at waist height to reduce the strain on workers and speed up access.
Ensure safety and accessibility
Safety is a critical aspect of warehouse design. Make syre all aisles are wide enough to easily move materials and equipment. Emergency exits, fire extinguishers, and first aid stations should be clearly marked and accessible. Additionally, keeping pathways clear of obstructions can prevent accidents and improve efficiency.
Leverage technology
Incorporating technology can greatly enhance warehouse operations. Barcode scanners, inventory management software, and automated storage and retrieval systems (AS/RS) can help keep track of inventory levels and locations. This helps reduce the risk of errors and makes finding everything easy.
Flexible and scalable design
Finally, it’s important to design your warehouse with flexibility and scalability in mind. As your business grows, your storage and production needs may change. That doesn’t mean you have to rent a warehouse that’s three times bigger than your current needs. But make sure the layout can easily adapt to new equipment, increased inventory, or changes in workflow.
Once you have the perfect manufacturer inventory layout, it’s time to think about strategies.
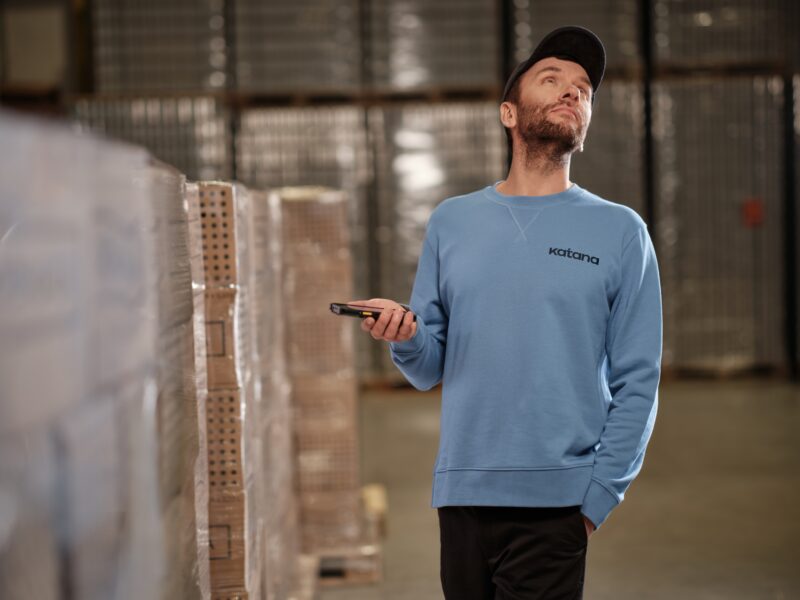
Manufacturing inventory management strategies
Effective inventory management often boils down to choosing the right production inventory management strategies. There’s a long list to choose from. Below are some that you should definitely consider.
Just-in-time (JIT) inventory
The JIT inventory system focuses on reducing waste and increasing efficiency by receiving goods only as they are needed in the production process. This method minimizes inventory costs and reduces the need for large storage spaces. However, it requires a highly reliable supply chain to avoid production delays.
Economic order quantity (EOQ)
EOQ is a formula-based approach to determining the optimal order quantity that minimizes the total costs of inventory, including ordering and holding costs. By calculating the EOQ, manufacturers can place orders at the most cost-effective points, balancing the costs associated with ordering and storing inventory.
ABC analysis
ABC analysis categorizes inventory items into three categories based on their importance and value:
- A items — High-value items with low sales frequency, requiring tight control and accurate records
- B items — Moderate value and sales frequency, needing regular monitoring
- C items — Low-value items with high sales frequency, managed with simple controls
This method helps prioritize management efforts and resources toward the most critical items.
Safety stock
Safety stock acts as a buffer against uncertainties in demand and supply. It works by maintaining a small reserve of critical inventory items so that manufacturers can prevent production halts caused by unexpected shortages or delays from suppliers. It also helps to keep customers happy, as unexpected delays are hated globally. As a downside, safety stock will increase carrying costs compared to strategies like just-in-time.
Vendor-managed inventory (VMI)
In a VMI arrangement, the supplier manages the production inventory levels of their products at the manufacturer’s location. This strategy can reduce the administrative burden on the manufacturer and ensure a more consistent supply of materials, as the vendor takes responsibility for maintaining adequate stock levels.
Lean manufacturing
Lean manufacturing focuses on minimizing waste and improving overall efficiency. In terms of inventory management, this means reducing excess inventory, streamlining production processes, and implementing continuous improvement practices. Lean principles help maintain optimal inventory levels that support efficient production without overstocking.
Demand forecasting
Accurate demand forecasting uses historical data, market trends, statistical methods, and qualitative methods to predict future product demand. By anticipating changes in demand, manufacturers can adjust their inventory levels proactively, avoiding both stockouts and overstock situations.
Inventory turnover ratio
The inventory turnover ratio measures how often inventory is sold and replaced over a specific period. A high turnover ratio means efficient production inventory control and strong sales, while a low turnover ratio may signal overstocking or sluggish sales. Regularly monitoring this ratio helps manufacturers make informed decisions about production and purchasing.
Automation and technology
Implementing advanced inventory management software and automation technologies can greatly enhance production inventory tracking and control. Technologies such as barcode scanning, RFID tags, and IoT devices provide real-time visibility into inventory levels, streamline the ordering process, and reduce human error.
With these strategies, you can’t just implement them all, as some would work against each other. However, you should carefully consider the pros and cons of each, taking into account your industry and the exact business requirements.
In the next section, we dive into some production and inventory management tips you can use to streamline your operations and get the most out of your resources.
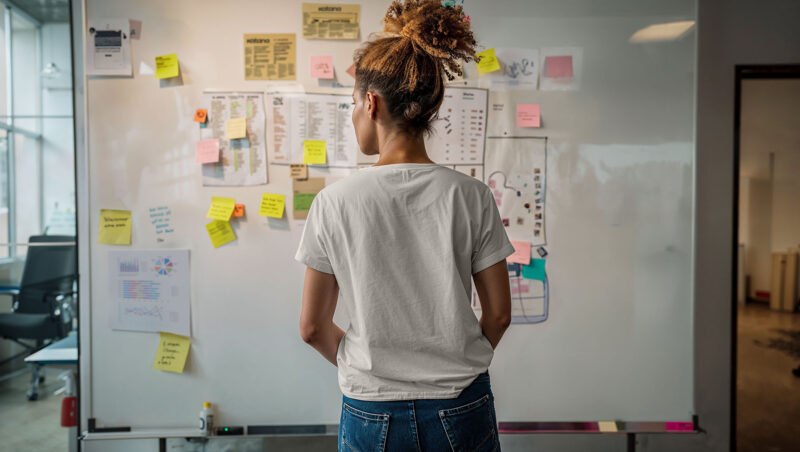
Tips and techniques for production inventory management
Implementing the right strategies is crucial for effective inventory management, but there are also practical tips and techniques you can adopt to streamline your operations further. Here are some actionable steps to help you maximize efficiency and optimize your manufacturing inventory management.
Conduct regular audits and cycle counts
Maintaining accurate inventory records and preventing discrepancies can be done through regular audits and cycle counts. Periodically counting a portion of your inventory helps you ensure that your records align with actual stock levels. Cycle counts are less disruptive than full audits, so you can schedule them more frequently to improve accuracy and quickly identify issues.
Optimize inventory levels with reorder points
To avoid stockouts, set reorder points for each inventory item based on:
- Lead times
- Demand variability
- Safety stock levels
Inventory management software can automate reorder point notifications, ensuring timely replenishment and reducing the risk of running out of stock.
Implement cross-training programs
Improve flexibility and efficiency by cross-training employees to perform multiple roles within the warehouse. When staff members are familiar with various production and inventory management aspects, they can assist in different areas as needed. This helps reduce downtime and boost productivity, and is especially useful in case somebody unexpectedly calls in sick.
Utilize standardized procedures
The best way to achieve consistency and accuracy in inventory management is through standardized operating procedures (SOPs). Develop SOPs for tasks such as:
- Receiving
- Storing
- Picking
- Packing
- Shipping
Training employees to adhere to these procedures minimizes errors and improves efficiency.
Invest in inventory management software
Robust inventory management software offers:
- Real-time visibility into inventory levels
- Streamlined order processing
- Automation of various tasks
- Production management
Seek software that features barcode scanning, automated reorder alerts, and integration with other business systems to significantly reduce human error and improve overall efficiency.
Katana inventory management software
Katana offers all these features and more, allowing you to save hours every week. Book a demo and take a look for yourself how Katana can streamline your operations.
Leverage data analytics
Analyzing inventory data gives valuable insights into trends, demand patterns, and improvement areas. Use data analytics to:
- Identify slow-moving inventory
- Forecast demand
- Optimize stock levels
Data-driven decisions help to optimize stock levels, enhance efficiency, and reduce costs.
Improve supplier relationships
Soft skills don’t get mentioned often, but these can make a big difference in your business. Strong relationships with suppliers ensure a reliable and consistent supply of materials. It may even mean that your orders get prioritized.
Regular communication about lead times, order quantities, and potential issues, along with collaborative planning and forecasting, can align your inventory management efforts with your suppliers’ capabilities.
Enhance warehouse organization
Just like our parents told us, a well-organized warehouse layout is a great way to increase efficiency. Maybe not verbatim, but the meaning behind “Clear your room” is pretty much the same. Ensure that:
- Frequently used items are easily accessible
- Similar items are grouped together
- Shelves and storage areas are clearly labeled for quick retrieval
Implementing visual management techniques like color-coded labels and signs further improves organization and reduces errors.
Implement continuous improvement practices
Create a culture of continuous improvement by encouraging employees to identify inefficiencies and suggest enhancements. Regularly review inventory management processes and seek feedback from your employees. Implementing small, incremental changes can lead to significant long-term improvements in efficiency and productivity.
Use predictive maintenance
Employ data and analytics to predict equipment failures and perform maintenance proactively. Predictive maintenance reduces downtime, extends the lifespan of assets, and ensures a smooth production process.
Monitor key performance indicators (KPIs)
Tracking KPIs related to inventory management helps measure performance and pinpoint areas for improvement. Common KPIs include:
- Inventory turnover ratio
- Order accuracy rate
- Stockout rate
- Lead time
Regular monitoring of these metrics enables informed decision-making and optimization of your manufacturing inventory management practices.
Keep these tips and techniques in mind when you draft your production inventory management strategy.
Katana — your perfect partner for production inventory management
If you’re looking for a way to streamline your inventory control in manufacturing, look no further. Katana is a cloud inventory platform with advanced production features that make managing your manufacturing business a walk in the park.
Katana gives you a real-time overview of your stock, including raw materials, across all your inventory locations and sales channels. In addition, you can:
- Set up bills of materials (BOMs)
- Integrate business tools, like Shopify, QuickBooks Online, and many more
- Forecast inventory demand
- Track your materials and products
- Manage your manufacturing operation
Running a manufacturing business involves a lot of moving parts. Katana brings it all together in one intuitive platform. It gives you a complete overview of your entire business and equips you with the tools to manage it all. To see for yourself how Katana can help your business grow and thrive, book a demo today.
Manufacturing inventory management FAQs
- Implement just-in-time production — Produce goods only as needed, reducing excess inventory.
- Improve forecasting — Use accurate demand forecasting to align inventory with actual sales.
- Streamline supply chain — Optimize supplier relationships and logistics to ensure timely deliveries without overstocking.
- Enhance production scheduling — Synchronize production schedules with demand to avoid unnecessary build-up of inventory.
- Use production planning software — Implement software to schedule and monitor production efficiently.
- Optimize workflow — Streamline processes to minimize bottlenecks and maximize output.
- Regular maintenance — Keep equipment in optimal condition to avoid downtime.
- Monitor key metrics — Track productivity, quality, and efficiency metrics to ensure continuous improvement.
- Maintenance, repair, and operations (MRO) inventory — Supplies used to keep the factory running, like spare parts and tools.
- Raw materials — Basic materials used to produce goods.
- Work-in-progress (WIP) — Items that are in the production process but not yet finished.
- Finished goods — Completed products ready for sale or shipment.
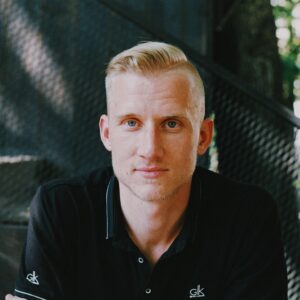
Henry Kivimaa
Table of contents
Get inventory trends, news, and tips every month
Get visibility over your sales and stock
Wave goodbye to uncertainty with Katana Cloud Inventory — AI-powered for total inventory control