DOE in manufacturing: The secret to optimized solutions
Design of experiments (DOE) is where innovation and problem-solving collide. This article explores DOE in manufacturing and its real-world applications.
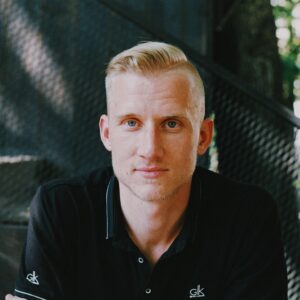
Henry Kivimaa
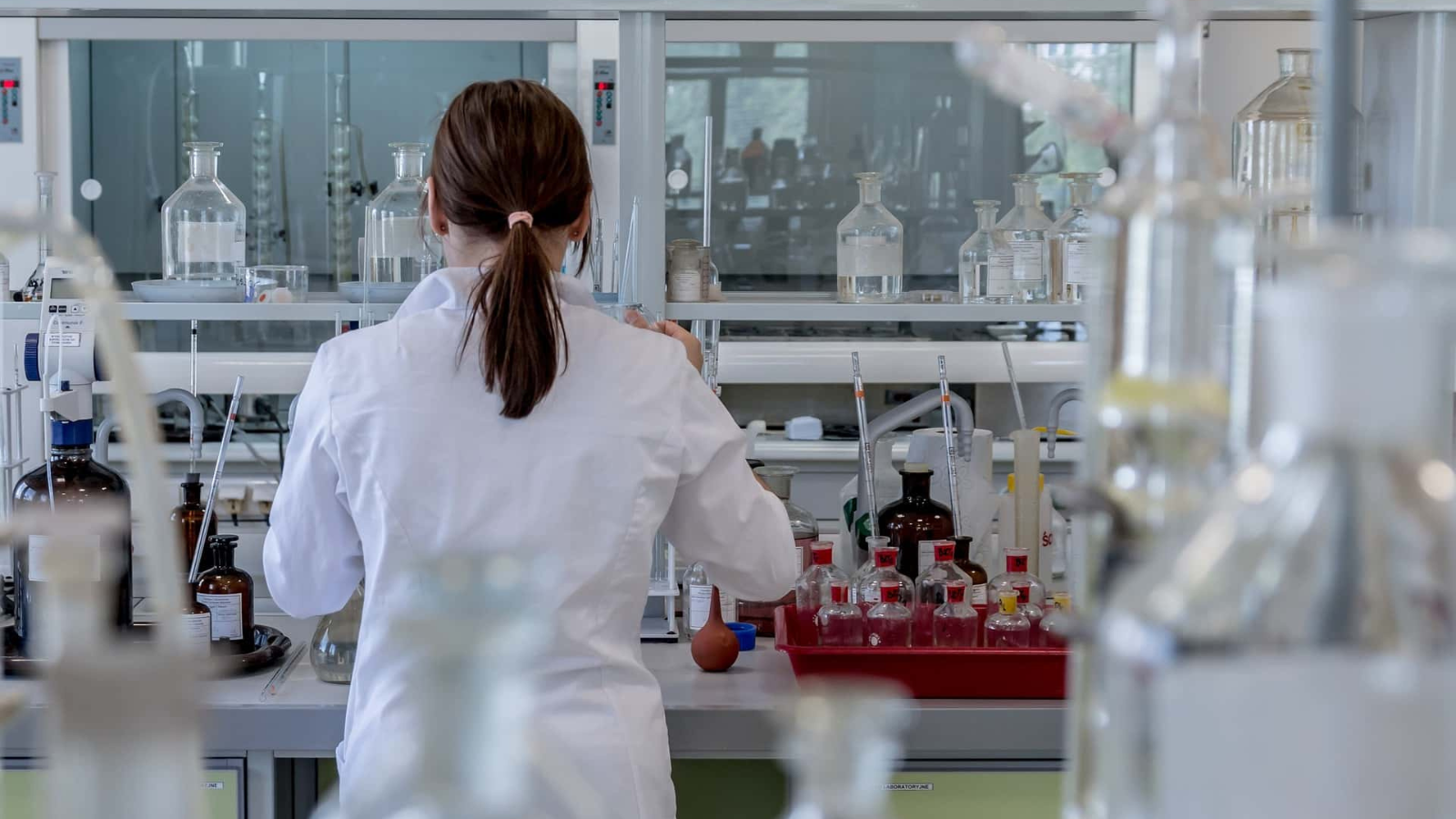
Many children dream of becoming inventors and scientists when they grow up.
Fascinated by the idea of mixing together the next love potion or conducting experiments resulting in flying monkeys and unnatural superheroes — they can’t wait to get their first lab coat. However, as they grow older, many are steered away from these aspirations and led down different paths. But, in the manufacturing world, a new opportunity arises for those with a thirst for experimentation and innovation.
Design of experiments (DOE) allows manufacturers to embrace their inner inventor and scientist.
With DOE, they can tap into their curiosity, push the boundaries of what’s possible, and uncover the hidden potential within their operations. So, whether you’re fantasizing about inventing flying cars or discovering revolutionary materials, don’t abandon those dreams just yet. Experimental design opens up a world of possibilities where you can bring your wildest imaginations to life.
It’s time to dust off those childhood dreams, put on your inventor’s cap, and explore DOE in manufacturing.
What is DOE?
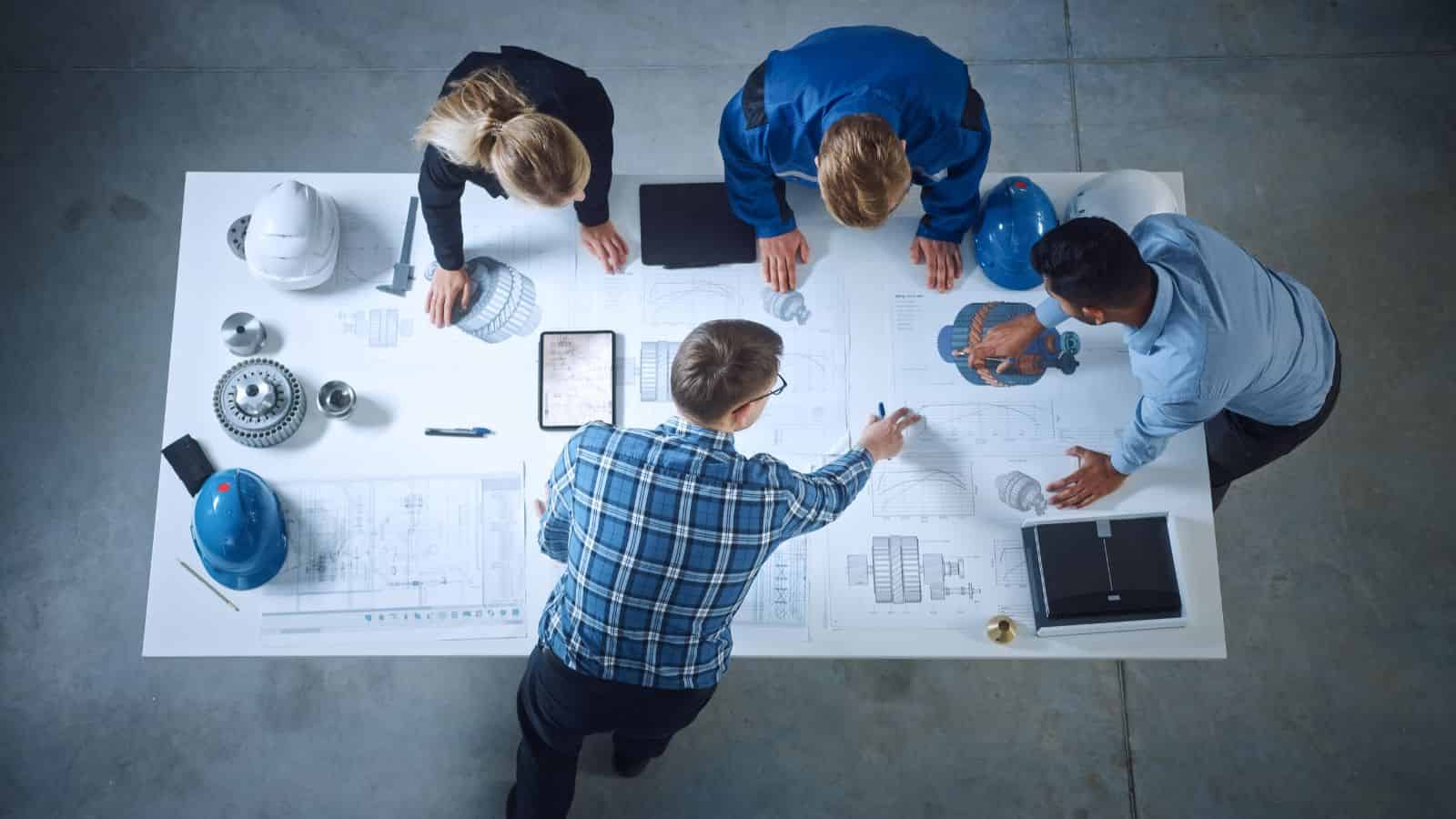
Design of experiments (DOE) is a statistical method used to test how different factors affect an outcome. Scientists plan experiments by changing one factor at a time and measuring the effects. It helps them understand complex systems, optimize processes, and make informed decisions in fields like manufacturing, engineering, and research.
DOE is essentially like a trial-and-error method of finding the recipe for success.
It involves planning and running experiments to gather data on different factors that can affect the outcome of the investigated process or system. By carefully changing and controlling these factors, we can understand how they influence the results. This helps manufacturers make informed decisions to improve efficiency, reduce variability, and enhance the quality of what they’re making.
It’s like conducting scientific experiments to find the best ways to do things and do them even better.
What is DOE in manufacturing?
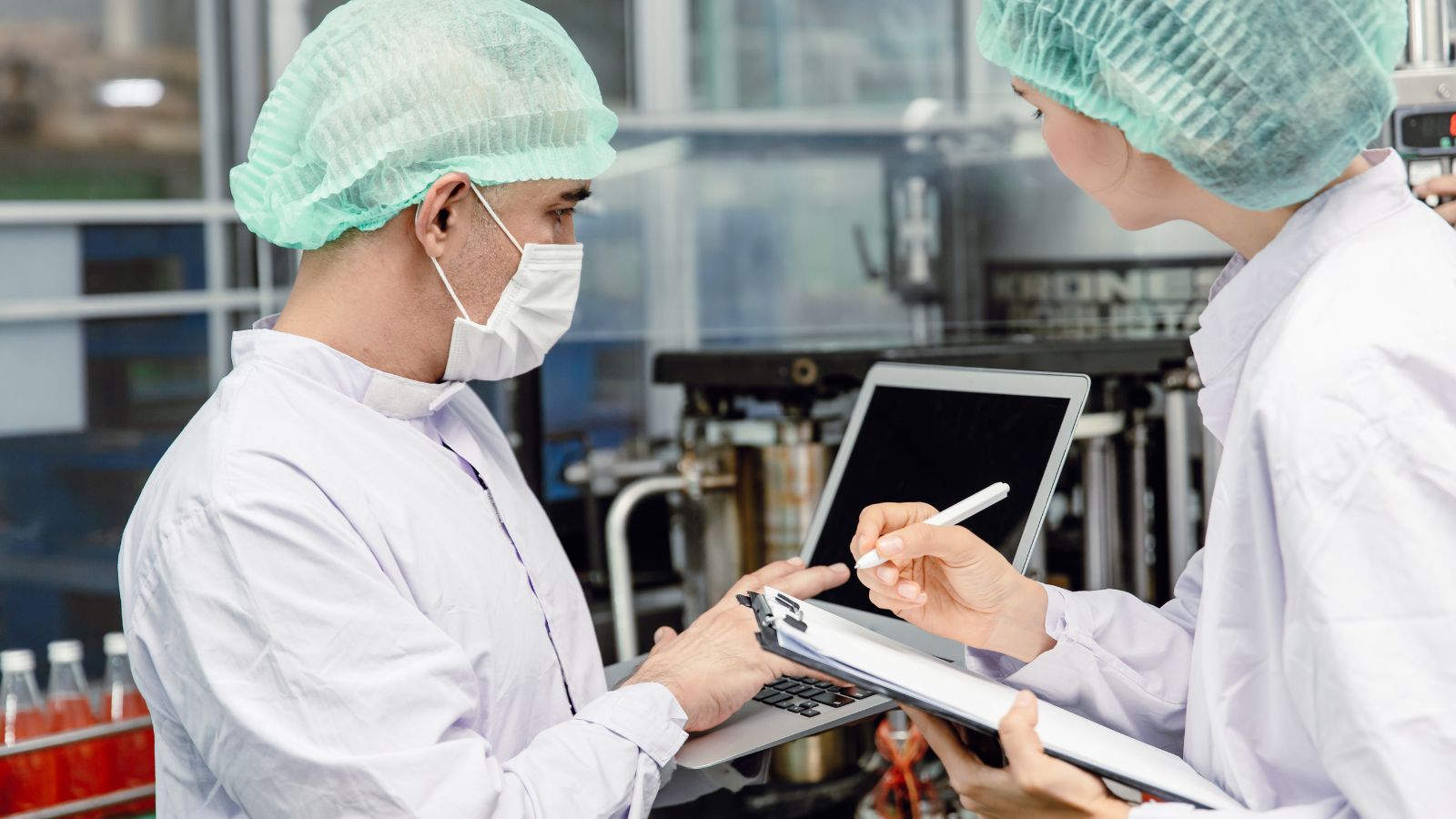
DOE is used in lean manufacturing to improve production by conducting several experiments and finding the most optimal solutions. It helps identify influential factors, improve efficiency, and act on evidence to enhance manufacturing processes. DOE is all about gathering data and analyzing it to make better decisions.
Sounds complicated, but it’s actually nothing else but trying how to get the best results with the least effort and costs.
Imagine you want to bake the perfect cake. Instead of randomly guessing how much flour, sugar, or baking time you need, try DOE to test different amounts and timings. You can see how each change affects the final cake by carefully changing one factor at a time and keeping everything else consistent.
This helps you understand which factors have the most significant impact on the outcome.
While there’s no one formula to calculate DOE, its processes are still very mathematical and technical. With the help of experiments, manufacturers can find the most efficient ways to make products. It’s like finding the recipe for success in manufacturing.
DOE is also used to optimize and improve various aspects of the supply chain, such as:
- Process efficiency
- Inventory management
- Logistics
- Operational performance
With DOE, manufacturers can save time, resources, and money by making informed choices based on evidence rather than just guessing.
Download a free production quality control checklist
Once you’ve mastered the art of DOE in manufacturing, it’s crucial to ensure flawless quality through comprehensive quality control checks. Download a free production quality control checklist to elevate your manufacturing process.
An industry example of DOE
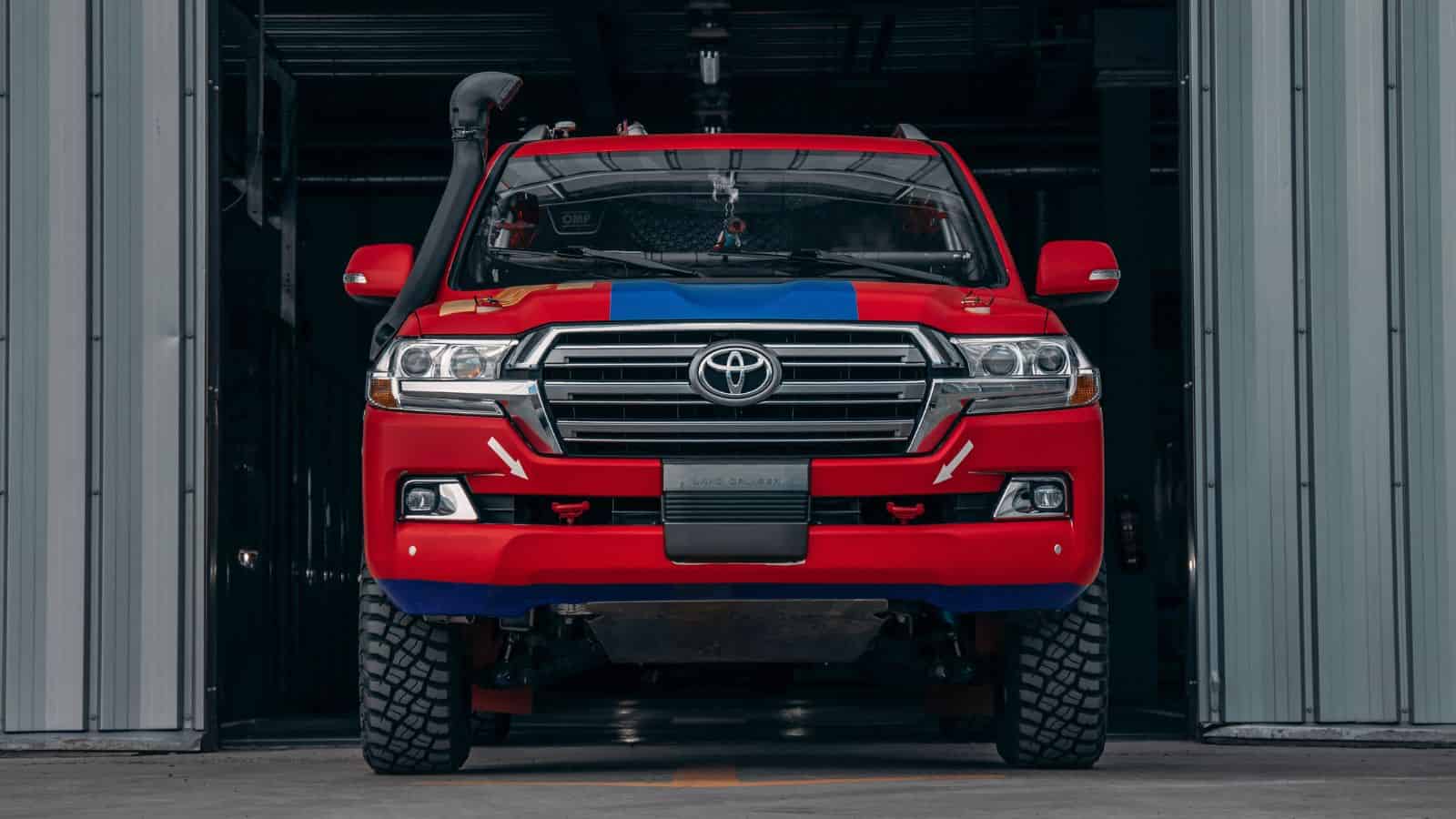
One industry where DOE is widely used is the automotive manufacturing sector.
Let’s take the example of a car manufacturer looking to optimize the paint application process. By implementing DOE, they can regularly test and analyze various factors that affect the quality of the paint finish, such as:
- Paint viscosity
- Application method
- Drying time
- Temperature
Using DOE, the manufacturer can run experiments with different combinations of these factors while keeping other variables constant.
They can measure and analyze the outcomes, such as the various criteria for a paint job quality, like adhesion, dryness, and gloss, to determine the optimal settings for each factor. The manufacturer can adjust the paint application process by identifying the key factors and their optimal ranges, leading to a consistent and high-quality finish across all their cars.
DOE helps automotive manufacturers reduce paint defects, improve customer satisfaction, and streamline production processes. This leads to cost savings by minimizing paint wastage and rework.
Benefits of DOE in manufacturing
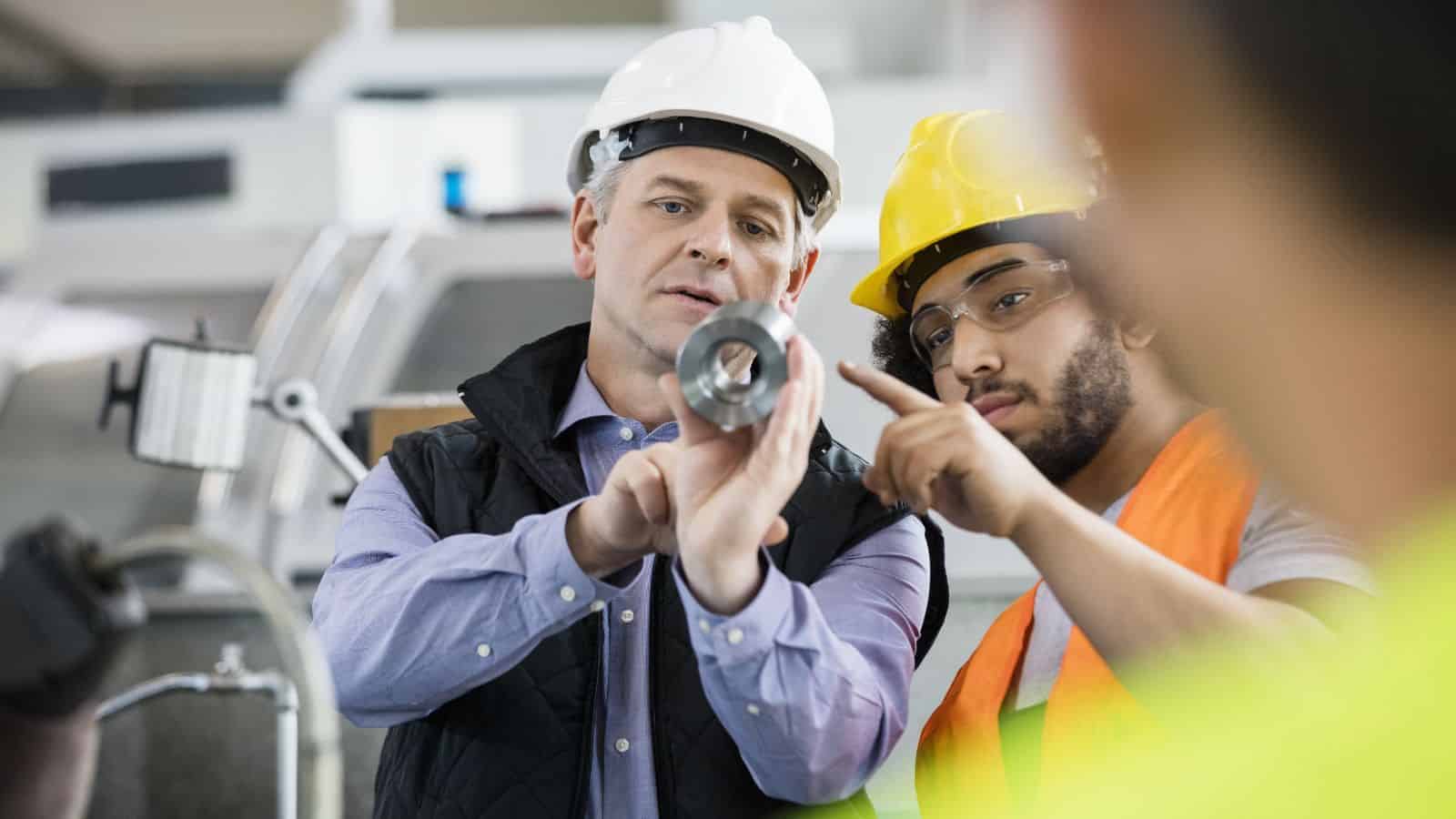
There are several benefits that adopting DOE can have for a manufacturing business.
Improved efficiency
DOE helps identify the optimal settings or conditions for manufacturing processes, leading to increased efficiency and productivity. By systematically testing different factors, manufacturers can determine the most effective ways to produce goods while also reducing waste and saving time.
Enhanced product quality
Through DOE, manufacturers can pinpoint the factors that significantly affect product quality. By optimizing these factors, they can minimize defects, variability, and inconsistencies, increasing the quality of products and meeting customer expectations.
Cost reduction
Manufacturing DOE aids in cost reduction by optimizing processes, minimizing waste, and identifying the key factors that influence outcomes. Manufacturers can then take data-driven steps toward eliminating unnecessary expenses and making the most of their resources.
Decision making
DOE provides manufacturers with valuable data and insights. It allows them to make informed decisions based on statistical analysis and evidence rather than relying on guesses and assumptions. This leads to more reliable and effective process improvements.
Faster time to market
With DOE, manufacturers can identify the optimal process parameters more quickly. Systematically testing various factors can shorten the development and optimization phase, resulting in faster cycle time for new products.
Continuous improvement
DOE is a repetitive process that encourages ongoing improvement. Manufacturers can use DOE to monitor and fine-tune their operations, ensuring they remain efficient and effective over time.
Overall, DOE is a valuable method for achieving operational excellence and staying competitive in the manufacturing industry.
Why is DOE important to understand?
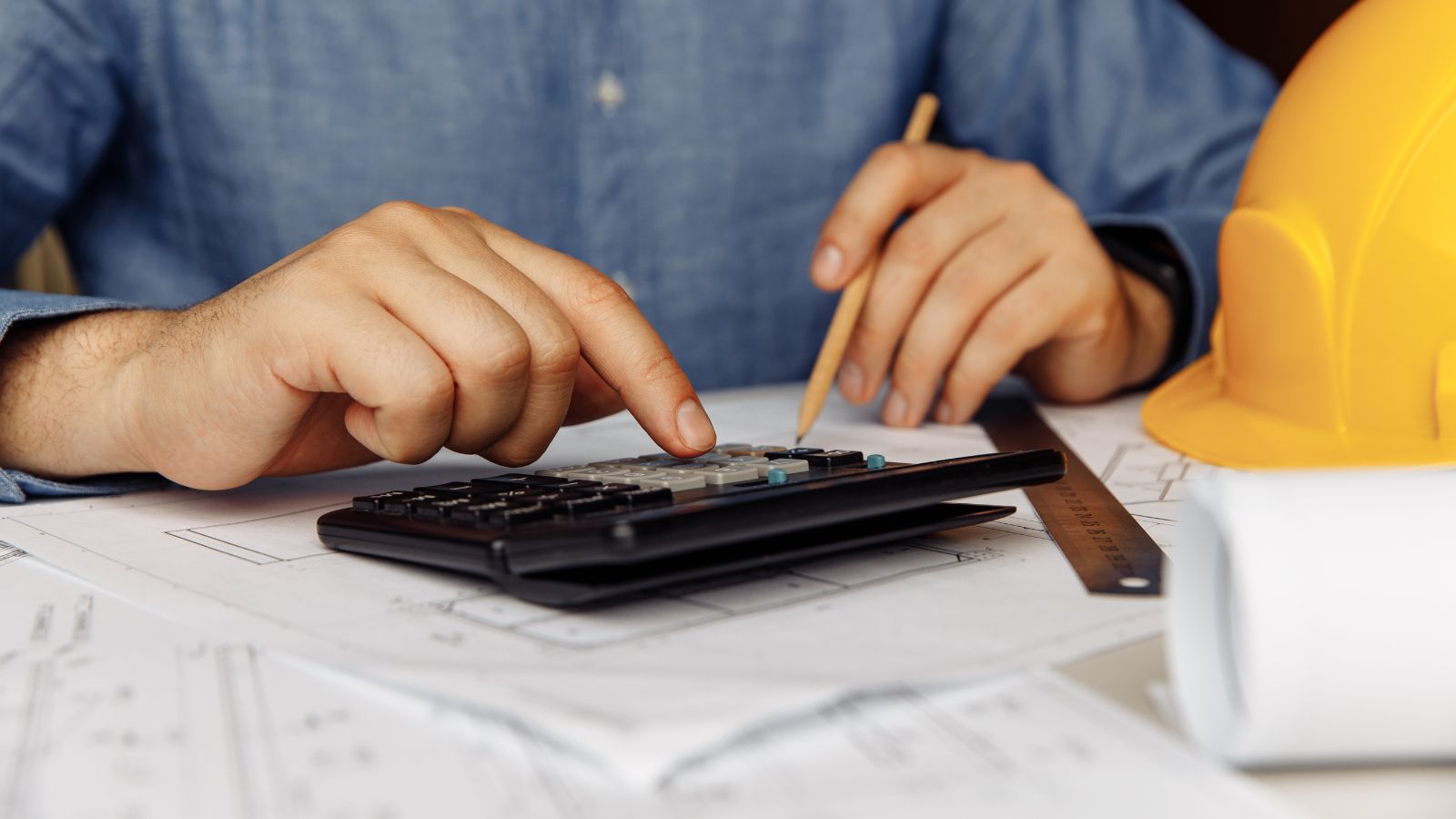
Understanding DOE is crucial for several reasons.
Firstly, DOE allows us to make evidence-based decisions in manufacturing.
We can gain valuable insights into the most impactful factors by conducting well-designed experiments and analyzing data. This knowledge helps us optimize processes, reduce defects, and improve efficiency, ultimately leading to better products and increased productivity. Without understanding DOE, we would rely on speculation and intuition, which can often be unreliable and inefficient.
Secondly, DOE helps us maximize resources and remain cost-effective.
If we identify the critical factors with the most influence, we can make targeted improvements and eliminate unnecessary expenses, leading to reduced costs and increased profits. Additionally, DOE enables us to identify interactions between different factors, optimize processes and achieve the best results. Understanding DOE allows us to unlock our full potential, stay ahead of the competition, and adapt to changing market demands.
Ultimately, DOE is important because it gives us the knowledge and tools to make data-driven decisions, improve efficiency, and drive success in various industries.
Best practices
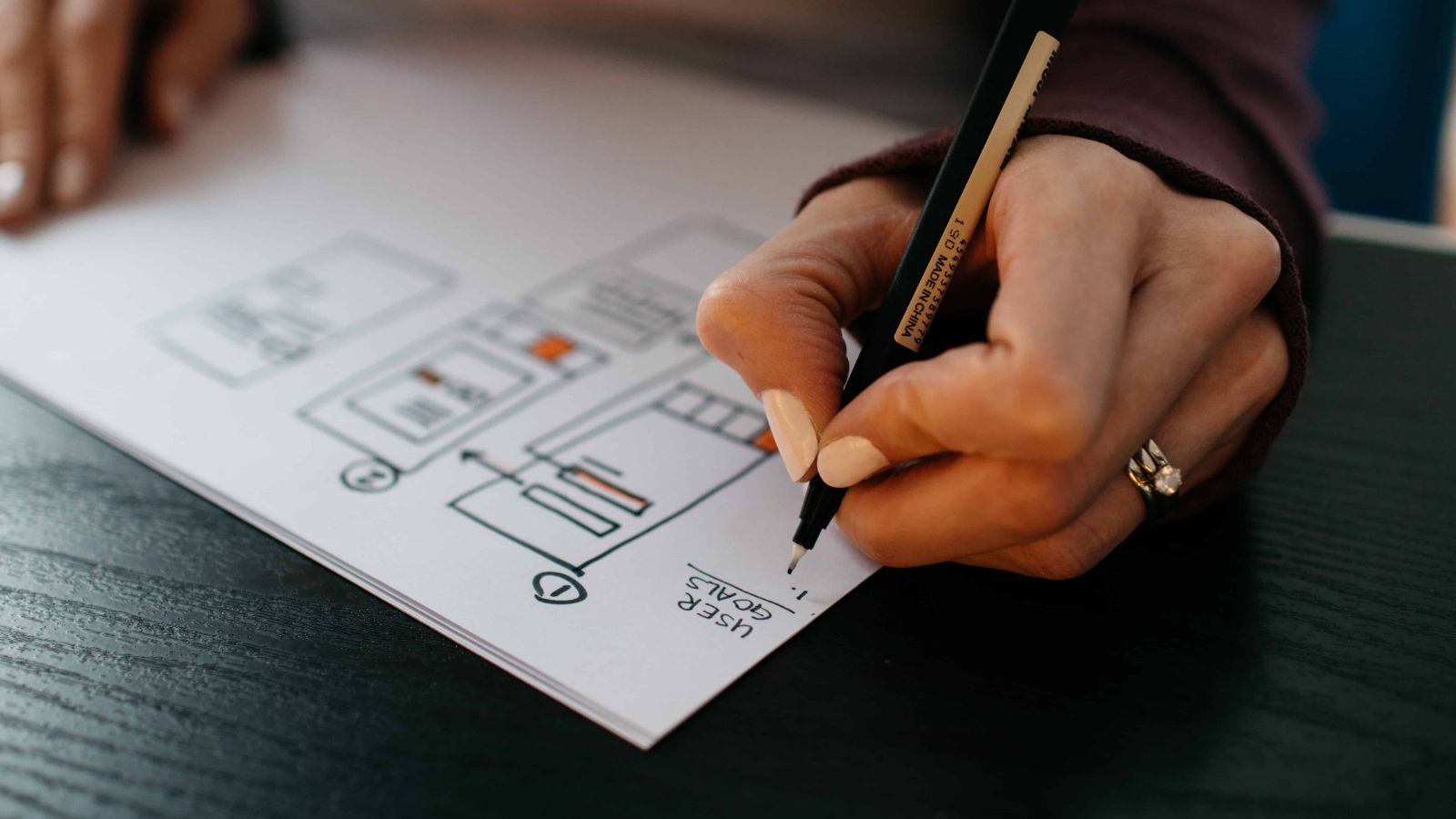
When applying DOE in manufacturing, there are several best practices to follow to ensure effective and reliable results.
- Clear objectives — State the objectives of the experiment clearly and determine what your goals are. This helps to design appropriate experiments and select relevant factors to study.
- Identify key factors —Determine the critical factors that are most likely to impact the outcome of the process or system. Prioritize these factors based on their potential significance.
- Careful planning — Develop a well-planned experiment. Consider various factors, such as the sample size, the design of the experiment itself, and the management of any variables that could potentially affect the results in unintended ways. It’s crucial that the experiments are random and repeated several times to get reliable and unbiased results.
- Controlled constants — Keep all factors, except those being tested, constant or controlled at desired levels. This helps isolate the effects of the factors under investigation and reduces variability in the experiment.
- Data management — Collecting accurate and precise data during experiments is essential in DOE. It ensures that the information gathered is reliable and free from errors. Proper data collection techniques, such as precise measurements and careful recording of observations, can enhance the validity and integrity of your findings.
- Regular improvements — Develop a habit of routinely conducting manufacturing DOE. Use the results from initial experiments to refine the experimental design and perform additional experiments as needed. Continue to evaluate and improve the process based on the new insights.
- Documentation — Maintain thorough documentation of the experimental design, procedures, data, and analysis. This saves all your processes and findings and allows others to understand and build upon your work. Sharing insights with relevant stakeholders promotes knowledge sharing and creates a culture where learning is encouraged.
- Utilize specialized software — Consider using dedicated software tools like Katana Cloud Inventory Software to streamline the DOE process and enhance efficiency. These systems offer built-in features for data collection and analysis, making the entire DOE workflow more seamless and error-free.
- Automation and error minimization — Lean manufacturing software like Katana helps reduce errors and inconsistencies in DOE and data collection. Automation minimizes the risk of miscommunications and ensures accuracy and reliability in the experimentation process.
Whether you want to start conducting thorough manufacturing DOE or simply take better control of your production processes, give Katana a go and see for yourself why other manufacturers use it for their daily tasks. Reach out to our sales team and request a demo now.
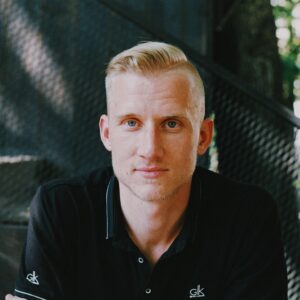
Henry Kivimaa
Table of contents
Get inventory trends, news, and tips every month
Get visibility over your sales and stock
Wave goodbye to uncertainty with Katana Cloud Inventory — AI-powered for total inventory control