Distributed manufacturing: The way of the future?
Distributed manufacturing promotes efficiency, flexibility, and reduces costs. Learn all about it and how to implement it.
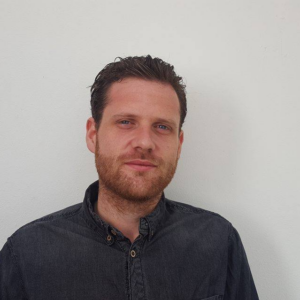
James Humphreys
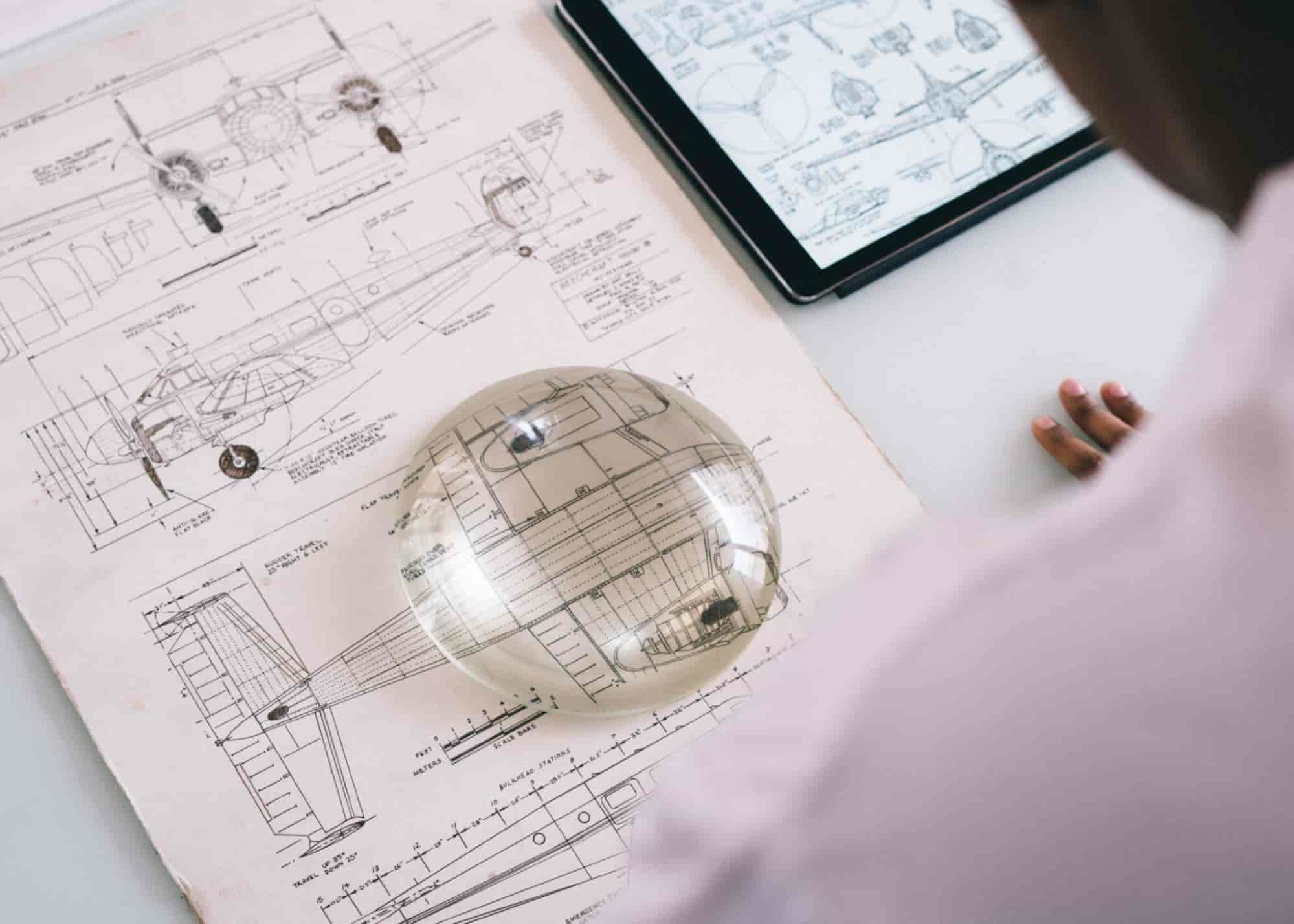
If you’ve tried to buy a car in North America over the past year, you have probably had a run-in with today’s supply chain challenges.
Some parts produced far away are no longer available due to pandemic-related shutdowns, while others are in short supply due to a global semiconductor shortage. This is the new trend towards a just-in-time, globalized economy — the entire world is linked together in a complex web of trade and production. The current system was not designed to deal with sudden disruptions on such a large scale.
But what if there was a way to build resilience into the system by using decentralized manufacturing?
This is the promise of the distributed manufacturing trend.
It also opens up the possibility of decentralized supply chains, which would be much less vulnerable to disruptions.
Before we proclaim this system as one that will save the world, let’s dig a little deeper into what it is distributed manufacturing advantages and disadvantages and how to manage it using advancing software solutions.
Live inventory management software for pipeline inventory
Know exactly where all your items are at a moment’s notice with pipeline inventory software purpose-built for manufacturers tracking multiple inventory types.
What is distributed manufacturing?
Distributed manufacturing is a way of organizing production so that it is spread out across many different locations. This could mean making things closer to where they are needed or using local resources that might otherwise go to waste.
Right now, the vast majority of manufacturing industries takes place in centralized locations, often in countries with low production cost. This has led to a situation where many products are shipped long distances worldwide before they reach consumers.
Distributed production changes this by moving production closer to where it will be used. This could involve setting up small-scale production facilities in different parts of the world or even leveraging a digital platform or 3D printing technology to make products on demand locally.
There are many different ways to organize distributed manufacturing:
- Localized production — This involves having products designed and manufactured closer to where they will be used. For example, a company might have a factory in each country where it sells
- Modular production — This is a way of designing products to make them using modular components that can be produced separately with CNC machining techniques and then added to different assembly systems later
This would make it easier to produce and distribute products locally, as the different parts could be shipped from different places:
- On-demand production — This is where products are only made when they are ordered, using 3D printers, plastic injection molding, or other additive manufacturing techniques, often referred to as make-to-order. This would allow companies to produce things locally without having to keep finished products in stock
- Recycling and upcycling — This involves using local resources that would otherwise be wasted, such as food waste or plastic recycling
This is one of the driving forces behind a switch to distributed manufacturing, as our world continues to struggle with ecological changes due to our current take-make-waste economy — harvesting materials, making products, and throwing them out.
The common thread is that production is spread out across many different local markets and locations, making significant changes to supply chain management.
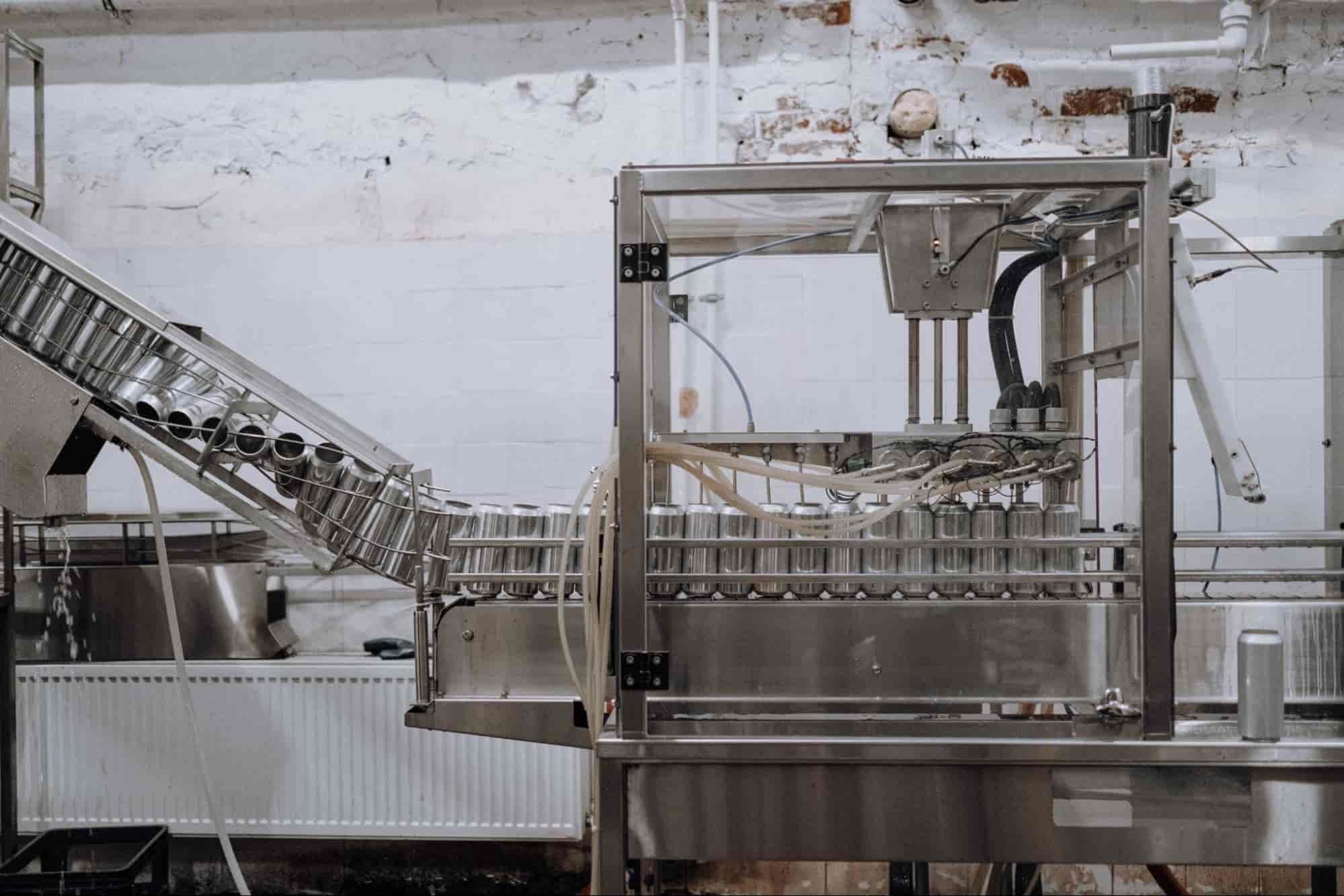
The advantages of using distributed manufacturing in production
With our current unsustainable model, there are constant threats of disruption from things like:
- Natural disasters
- Political instability
- Trade disputes
- Pandemics
Results indicate that a distributed manufacturing model would be much more resilient to these disruptions, as it would not rely on any one location. This is one of the main benefits of distributed manufacturing. But others include:
- Lower shipping costs — Given that products would be made closer to where they will be used. There would be no need to ship them long distances around the world. This could also shorten delivery times for raw materials and allow companies to offer leaner manufacturing processes.
- Quicker turnaround times — With production happening closer to where products are needed, they would not need to be shipped from far away. This would lead to shorter manufacturing lead times and faster turnaround times for customers.
- More local production — Distributed manufacturing would create jobs in the communities where production takes place. This is one of the main selling points for this model, as it could help to revive a local economy.
- Greater flexibility — It allows companies to be more flexible in their production, as they would not be tied to one location. This would make it easier to respond to changes in demand or increase the ability to customize products while also improving disturbance handling.
- Breakdown prevention — By spreading your manufacturing system over several different plants, you can shut down a single pod for short periods in order to do preventive maintenance without having to create production disturbances.
- Less waste — As a production system is spread out across many different locations, there would be less need for finished products to be shipped around the world. This would lead to less waste and a smaller carbon footprint.
Since it is not universally adopted, you can guess that there are also some disadvantages to the process.
Distributed manufacturing challenges
Importantly, some of the advantages above don’t provide a direct improvement over traditional manufacturing. In the centralized manufacturing vs. distribution conversation, it’s important to consider a few things. One is that, in some cases, the disadvantages of distributed manufacturing can cancel out the advantages.
Here are some examples of distributed manufacturing challenges:
- If product manufacturing takes place closer to where they will be used, but the materials needed to make them have to be shipped from far away, then there may not be any reduction in shipping costs or carbon footprint.
- If your manufacturing strategy is to spread out across many different locations, but each location only has a small number of machines and workers, then production may be less efficient than if it were centralized.
- If products are made using local resources or with additive manufacturing techniques, but those resources are of poor quality, then the products may also be of poor production quality
- Finally, if distributed manufacturing companies are not well-organized, then it can be difficult to coordinate production, manage inventory levels, and incorporate strong disturbance management.
Given these challenges, why would anyone want to move to a distributed manufacturing system?
How to manage a distributed manufacturing process efficiently
The key here is how managing distributed manufacturing platforms have become easier and easier as technology has advanced. Imagine trying to run 15 different manufacturing facilities spread all over the world in 1950.
It would be absolute chaos.
But today, there are cloud inventory software solutions that can help you manage every aspect of your distributed manufacturing operation from one central location.
These software solutions can help you with things like:
- Planning and scheduling production
- Managing inventory levels
- Tracking orders and shipments
- Communicating with suppliers and customers
- Analyzing data to improve operations
With the right software in place, you can use distributed manufacturing to your advantage rather than seeing it as a necessary evil.
You can use it to become more flexible and responsive to changes in the market, reduce your carbon footprint, and tap into local resources that you might otherwise not have access to.
In short, distributed manufacturing is the way of the future. It promises to make our supply chains more resilient, our production model more efficient, and our products better quality.
With the right software in place, like the end-to-end manufacturing ERP software from Katana that provides a class-leading user experience, it can be a powerful tool for any manufacturer.
Using manufacturing ERP software for managing your distributed manufacturing
Managing a network of manufacturers across the globe leads many businesses to turn to manufacturing ERP software to help them handle this monumental task.
By doing so, they can use the essential features to get more control over their:
Outsource manufacturing
Create Outsourced purchase orders (OPO) or make stock transfers from your warehouses to ensure your outsource manufacturers have everything they need to make your products.
Contract manufacturers
Suppose you’re using contract manufacturing in your workflow to make a finished product. In that case, you can send partially finished goods to your sub-contractor to perform an operation and track the progress and costs of their service.
Stocks and manufacturing sites
Easily track and manage inventory at multiple warehouses and fulfillment centers, consignment inventory with retailers or resellers, and monitor production in your own factories or with outsourced manufacturing partners.
Online and offline sales
Integrations with popular e-commerce platforms such as Shopify, WooCommerce, and BigCommerce allow manufacturers to track their inventory and sales separately across different channels, all from one place.
Katana ERP offers all this and more. Are you already juggling inventory between multiple locations and contractors? Reach out to our sales team to request a demo and see firsthand how the software can help take your business to the next level.
And until next time, happy inventory tracking.
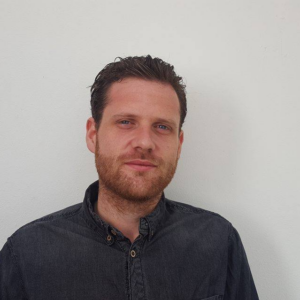
James Humphreys
Table of contents
Get inventory trends, news, and tips every month
Get visibility over your sales and stock
Wave goodbye to uncertainty with Katana Cloud Inventory — AI-powered for total inventory control