26 tips for small manufacturing business owners in 2023
Most useful tips for small manufacturing businesses who want to make 2020 their best year yet. Includes overview of the small manufacturing world in 2019.
Team Katana
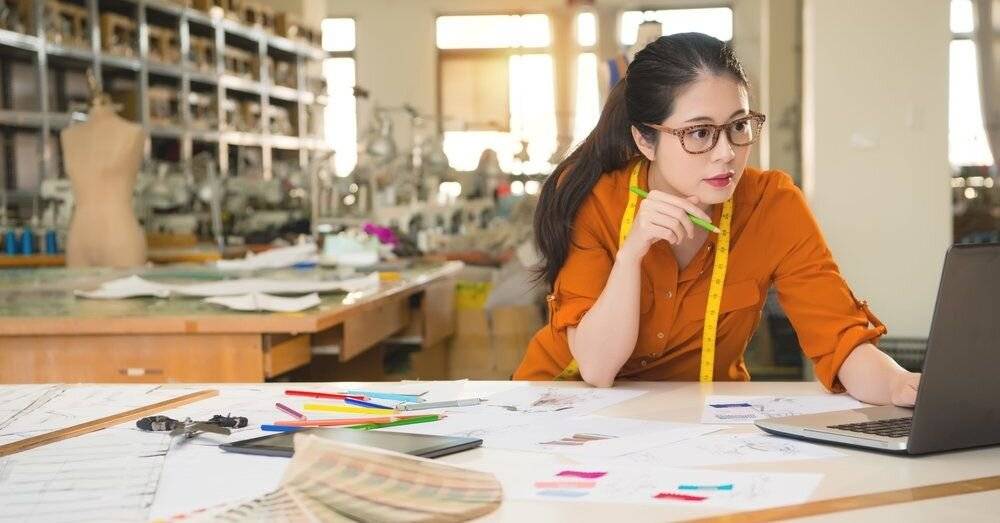
The small manufacturing business has become an increasingly common sight in the small business landscape. The route to becoming a small manufacturer has become very accessible in recent years. Manufacturing businesses with 20 or fewer employees have also seen promising growth in the past years.
Dear ambitious manufacturers,
As another year is (already) drawing to a close, we thought we’d reflect on the past year in the world of small-scale manufacturing.
As owners of small manufacturing businesses, we’re sure you’ve had your fair share of challenges and surprises during 2020. It goes with the territory of owning any small business.
As the global economic and political landscape continues to shift in new and unexpected ways, it’s no time to sit back and be complacent.
For example, there’s been turbulence for the manufacturers who have been using outsource manufacturing, or even just simply buying their materials from China, as there has been an ongoing US-China trade war, which has been affecting many different industries.
This alone is enough of a threat for businesses to figure out how they can fully optimize their practices to survive periods such as this.
That’s why we’ve put together a list of small business manufacturing tips to help you make it through 2021.
Small businesses are an essential part of the economy:
For example, they generate 65% of new jobs.
And they make up the vast majority of total businesses, which includes your small manufacturing business.
Your role in small business manufacturing is an important one, as demand for well-crafted and artisan products continues to increase.
Get a head start with cloud inventory software. Taking these tips and implementing them alongside a real-time cloud inventory system will help you take your business to the next level. Request a demo and see for yourself.
A review of 2021 for the small manufacturing business
So, what has been going on?
We’ve seen new industries continue to rise and play an even bigger part in our lives. Two to watch are 3D printing and drones. Both industries have a multitude of uses, and both have become very accessible and affordable to the average person.
The growth of blockchain, along with advances in AI, robotics, and manufacturing ERP software for small businesses, will change how all businesses operate, including in small manufacturing.
2021 could be a very important year in the world of small manufacturing, as we see the results of economic policies in the US on the world’s economy.
The results remain to be seen, but at the minute manufacturing is looking strong.
People are positive about the role of manufacturing in the future of the US economy. This is a great time to own a small manufacturing business and show the world how unique and awesome you are.
One of the biggest challenges a small manufacturing business faces is competition from larger enterprises, both at home and abroad. But some things are easier for those in small manufacturing.
You can be more adaptive, more dynamic, and run rings around the slower competition.
You have lower manufacturing costs and manufacturing overheads and have the freedom to experiment. Because you’re in charge.
Becoming a small manufacturer has never been more accessible. That’s why more and more people are choosing to do it.
This is great news!
It means that the future of manufacturing is small manufacturing and 2021 could be the best year ever for manufacturers.
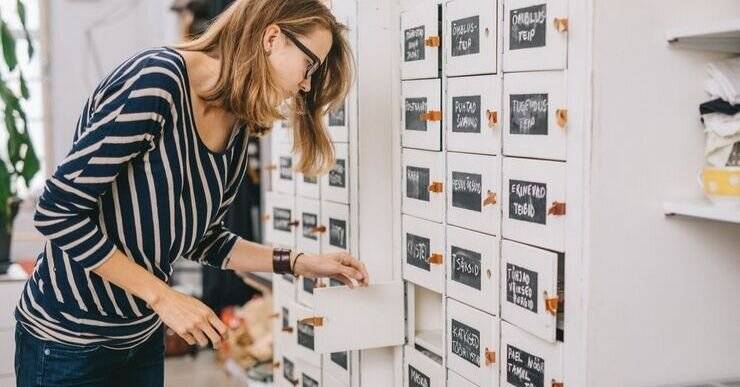
Not all small manufacturers wear overalls. Stella Soomlais has developed a thriving leathercraft workshop based on a philosophy of efficient, high-quality crafting and close to zero waste. She also uses expert marketing to make her small manufacturing workshop known around the world.
Tips for small manufacturers in 2021
We’ve split up these small business manufacturing tips into several categories as follows:
Let’s get to it.
Inventory management
1) Focus on supply chain management — Manufacturing supply chains are becoming more complicated with multiple suppliers and overseas shipping being commonplace. It pays to invest time into making sure this is watertight. Also, accept that emergencies can happen which leads to a supply chain breakdown. Develop your small manufacturing business’ policies to deal with this before it happens. This could be having alternative suppliers, storing stock off-site such as having inventory on consignment, or having a reasonable amount of safety stock.
2) Manage production to cut down on lead times — Prioritize your small business manufacturing order queue, so your staff is always logically working on orders. When a supply order comes in, assign it to the first orders in your queue to minimize prolonged work-in-progress (WIP) manufacturing and ship products faster.
3) Don’t keep inventory lying around — It’s fine to have indirect materials (like MRO) always on hand. But keeping lots of bulky stock around is costing you money. Find a way to cut down on carrying costs as these provide zero value to your product or business. Perhaps you can get more frequent but smaller orders for no additional shipping costs.
4) Don’t invest too much in inventory — It’s better to have the cash-on-hand. Find out how to calculate reorder points accurately for your business to negate the need for it. Realize that having extra inventory is an opportunity cost.
5) Be honest about your dead stock — If you have obsolete stock, then be honest and cut your losses to free up space in your workshop.
6) Learn how to judge the value of a supplier — A supplier that seems more expensive but is more suitable for your small manufacturing business needs, is more valuable to you than one that isn’t. Negotiate with your suppliers to put the above tips for small manufacturers into practice. If you don’t ask, you don’t get.
Workshop productivity
7) Figure out the type of BOM you need — Bill of materials (BOM) is an essential part of your master production Schedule (MPS). There are many types of BOM: modular, configurable, multi-level, the list goes on. Find out the best way to update your BOMs so they are easier to maintain and use in your business.
8) Learn the 5S’s — Lean inventory, a methodology that originated in Japan and can increase your small manufacturing business’ productivity. Spend some time observing your workshop and employees. Where are the lost seconds that add up to lost hours? Make sure you have the fundamentals optimized with the next 5 tips.
9) Seiri (Sort) — Remove unused items in an area to make sure employees are not rummaging through stuff to find something. Classify items by frequency of use. More commonly used items should be easier to access and close together.
10) Seiton (Straighten, Set) — Everything has a place and is always put back in its place. When your employees need a tool, they know exactly where to find it. If it is not there, they know it is in use, and don’t look for it. Of course, with adequate production planning, there is no need for employees to be fighting over tools. Find hierarchies and systems of storage, e.g. place heavy items lower, and so on.
11) Seiso (Shine, Sweep) — Create a clean workshop. Get rid of any dust and dirt. Have a system to regularly remove garbage from your workspaces. Make cleanliness a daily activity and set aside a small amount of time each day for it. Maintain proper lighting, so dust and dirt can be seen. This will promote productivity. You and your employees will have pride in their workplace, which will shine through in your product.
12) Seiketsu (Standardize) — Standardize by having a clear, readable, and accessible bill of materials (BOM) / product recipe. Make scheduling and operations clear through visual management. You can get software that uses a visual streamlines “Kanban” board system to make everything crystal clear.
13) Shitsuke (Sustain) — Now you have dotted the I’s and crossed the T’s, one more challenge remains. You have to keep all the great habits up. Set out clear policies and guidelines, and make sure your staff knows what your standards are. This is how you cultivate a good company culture with staff that is proud to say they work there.
14) Always have something left in the tank — Keep your small manufacturing business’ productivity below 100% capacity, so you can always keep up if you see a sudden spike in demand.
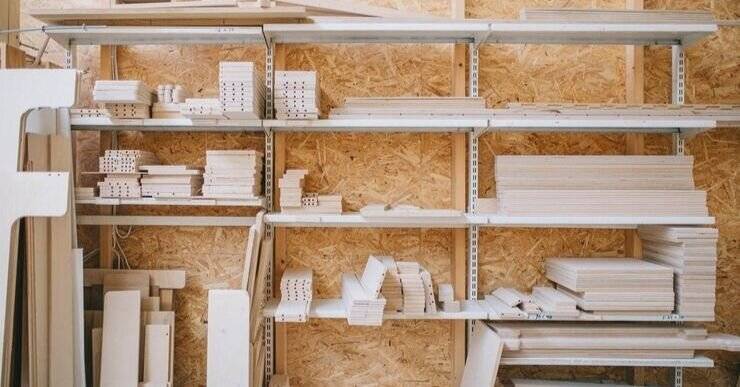
Employment practices
15) Emphasize great communication — Make it open, honest, and a two-way street with your staff. Make your employees feel comfortable to voice their opinion. The result? They will feel more respected, and you will know about problems you might not have known about otherwise.
16) Invest in your staff — Provide opportunities for learning and training for a more flexible workforce in your small manufacturing business. You can fill any skill gaps and improve employee turnover. If you have employees that can operate all your machines and do all operations, you can reduce lead times by changing up staff tasks at a moment’s notice. Let your small workshop be super-efficient in 2019.
17) Take on an apprentice or an intern — A survey of CEOs found 80% of UK CEOs are worried about being able to attract the right kind of talent, and 63% are using apprenticeships and internships to try to fill this gap. In fact, they are seen increasingly as a positive alternative to university for young people.
Marketing and customer engagement
18) Get your website seen — Have a great-looking and functional website? Great. Is anyone looking at it? If your views are less than stellar, it could be because nobody can find them. Learn about search engine optimization (SEO) to remedy this (and use the following tips for small manufacturers below).
19) Become a writer — A blog is a way to let customers find you and become interested in your product. It makes your small manufacturing business more personable, and a known brand in your industry.
20) Use video to show your company’s best side — They say a picture is worth 1,000 words, so a video must be worth a shed load. Explainer videos are professionally animated and voiced-over videos that explain your product to potential customers. They have been shown to significantly boost sales.
21) DIY awesome product photography — There’s no need to spend hundreds or even thousands on a professional photographer when the equipment is affordable and the resources to improve your images are free.
22) Connect with your community — Market in more personal ways. Go out into your local community, go to trade fairs, host events and workshops. If you use your creativity, the possibilities are endless.
23) Collect customer opinions — Offer a way for customers to get in touch with you online or off. This is a great way of finding out how customers perceive your small manufacturing business and get invaluable advice for improvement.
24) Don’t forget your packaging — Getting your e-commerce packaging right is a key part of your marketing efforts as it indicates your brand value, both in your market and to your customers. In some ways, how you package your products can be as important as your products themselves.
One of the best small business manufacturing tips for 2021 is to use great photography to present your products in the best light possible. More and more small manufacturers are using apps like Instagram to communicate directly with customers, so what are you waiting for?
E-commerce
25) Diversify your online store portfolio — Now you’ve become a master of Shopify, you have the expertise to expand to other online platforms, and marketplaces like WooCommerce and Etsy.
26) Offer different product versions — With different pricing, to increase your audience.
27) Beef up your cybersecurity — Two-step authentication is simply not an option. Make sure you invest in securing not only your data but your customer’s data too. Think about hiring a consultant to make sure everything is up to scratch.
A new year for your small manufacturing business
There you have it. 26 handy small business manufacturing tips for 2021. Some are timeless pieces of advice, others are brand-new — all are useful when applied correctly.
You don’t need to incorporate them all at once into your small manufacturing business. First of all, you need to look at what you currently do.
Really observe what is going on.
Take notes and quantify what you didn’t previously quantify. Figure out what it all means. If you immediately start tweaking here and reorganizing there without planning or scheduling, you might do more harm than good.
With the right tool, you can avoid any seasonal rushes, not get swamped with invoices or backorders, manage inventory with WIP tracking software (finished goods and raw materials) and synchronize your sale channels onto one easy-to-understand visual platform.
Katana’s cloud inventory software is such a platform that can provide you with these features and many more. Why not see it for yourself? Request a demo today!
The responsibility is in your hands to figure out what your small manufacturing business needs.
The top management consultants in the world take weeks or months to observe how the business currently operates before they open their mouths to suggest anything.
Take your time and don’t forget to really take customer feedback to heart. How your small manufacturing business is run will show in the customer experience.
Have a pleasant, stress-free, productive, and successful 2021.
And Happy Manufacturing!
Team Katana
Table of contents
Get inventory trends, news, and tips every month
Get visibility over your sales and stock
Wave goodbye to uncertainty with Katana Cloud Inventory — AI-powered for total inventory control