The ultimate guide to obsolete inventory
Consumers are picky.
If they walk into a store filled with too many different products, they might walk right back out. It is a delicate balance between having enough stock to satisfy customers and not having too much of it. Manufacturing companies understand this all too well, as they must keep track of the inventory in their warehouses.
Over time, certain products become obsolete. In the manufacturing industry, it is essential to manage these obsolete inventories so that they do not clog up warehouse space and reduce profits. If you don’t have a plan to manage your old inventory, you could lose out on valuable resources and money.
Below, we’ll look at an obsolete inventory definition, the causes of obsolete inventory, and strategies for managing it.
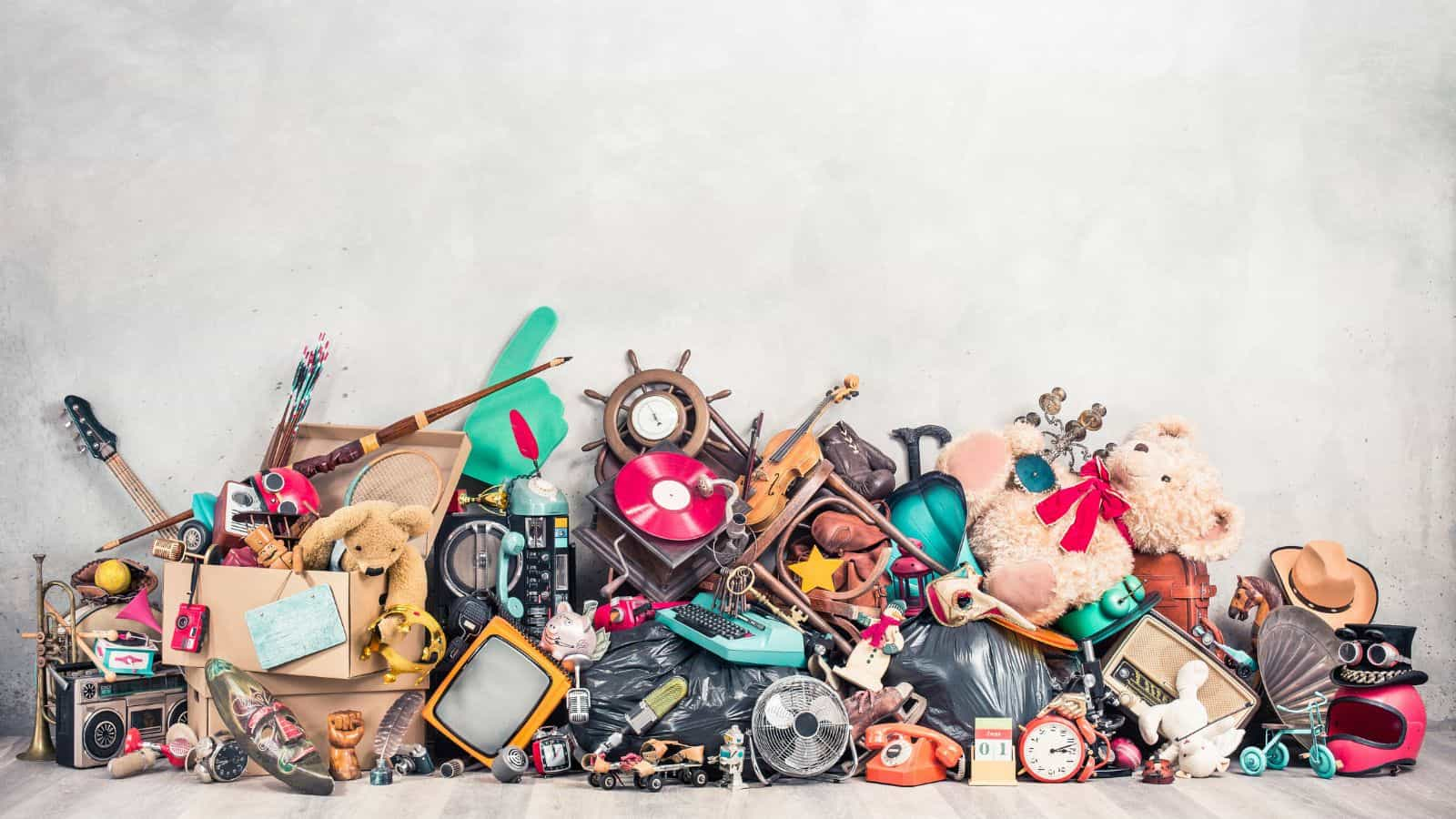
What is obsolete inventory?
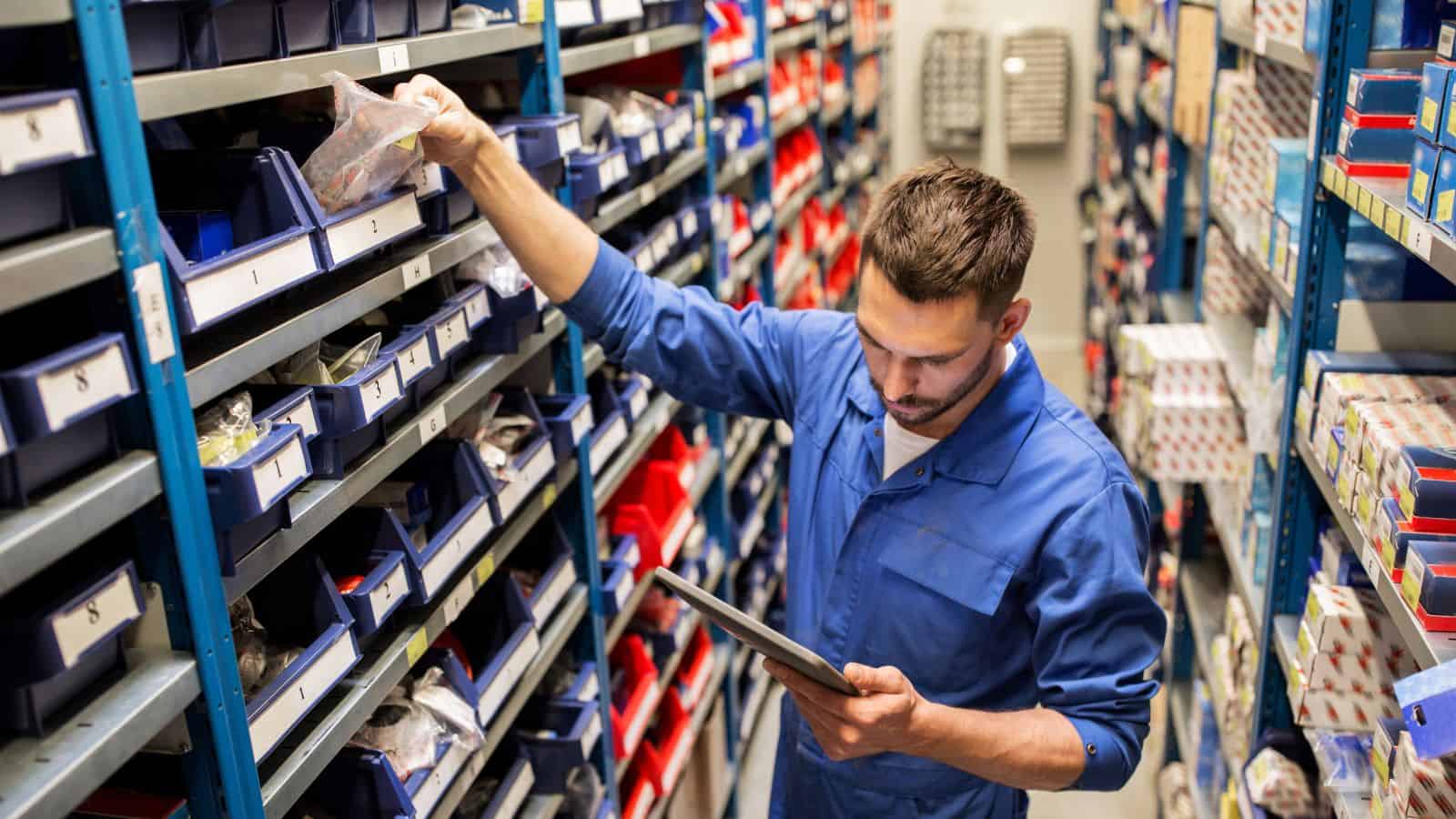
Obsolete inventory is any product sitting in a warehouse for too long and no longer has a buyer. It can include outdated parts, components, or materials no longer used in production. Because these products cannot be sold, they can take up valuable space and resources that could otherwise be used to store more profitable items.
How does obsolete inventory work?
The world is always changing, and other companies are coming out with newer, better versions of the same product. Your products will eventually become obsolete and no longer have a consumer base.
Obsolete inventory accounting
Accounting for obsolete inventory and its value is critical, as it can impact a company’s financial statements. When obsolete inventory benchmarks are reached, the cost of goods sold and the value of total assets will both decrease.
This means that manufacturers must keep track of their inventory to ensure they are not spending too much money on unsellable products.
A write-down is a standard accounting obsolete inventory journal entry used to record the value of the old stock. This write-down is typically done when a company has certain products that are no longer useful and will not be sold.
For example, if the value of 200 units is initially $10,000, but they have become obsolete, the company may write down the value of these units to $5,000. This will then be reflected in their financial statements as a decrease of $5,000 in the cost of goods sold and assets.
A write-off is when a company eliminates an obsolete stock item from its financial statements. This is usually done when a product has become so outdated that it has no value left or is a net negative for the company.
Causes of obsolete inventory
Here are some of the ways that your inventory can become obsolete.
Technological advances
Technology is always changing and improving. This can render a product obsolete as newer products offer more features or better performance at a lower cost.
Consider the example of the VHS tape. Once DVD and Blu-Ray players became popular, VHS tapes were no longer in demand. Now those, too, have been replaced by streaming services.
Innovative companies can cause internal obsolescence by improving and replacing existing products.
Changing customer preferences
You can’t always predict customer preferences. People’s tastes can change quickly, and what was once popular may no longer be in demand.
For example, if your company produces clothing for teens, you must keep up with the trends to remain competitive. If your warehouse consists of items that are no longer in fashion, it could quickly become stale inventory.
New competition
Competitors don’t always need to advance the technology to make your product obsolete. A new brand with a better price or better marketing may be enough to disrupt your market. With so many options for consumers, it’s easy for them to shift away from your product, even if it still meets their needs.
Governmental regulations
Government regulations can also render a product obsolete. If your company manufactures products that are no longer legal or compliant with the law, it will be challenging to sell them.
When the government changes regulations, it is vital to adapt quickly and modify your products to meet the new standards. Compliance is essential, and ignoring new laws could cost your company dearly.
Obsolete inventory examples
Obsolete inventory can come in many forms. Here are some common examples of obsolete items:
- Outdated parts or components
- Excess inventory from discontinued products
- Unsellable dead stock due to a change in customer preferences
- Products that have been replaced with newer versions
Take car parts, for instance. If a particular car model is no longer being produced, the parts that go with it become obsolete and cannot be sold. The company that manufactured these parts will have to write them off, as they are no longer of any use.
Likewise, if a company produces a product that is no longer in demand, its inventory of it becomes obsolete and must be cleared out. This can happen with technology products such as laptops or smartphones, where newer models come out every few months.
If you were the manufacturer of mobile phone antennas, you were likely left with a lot of obsolete stock when smartphones started getting smaller and no longer needed external antennas.
A government policy switch can also cause obsolete inventory. For example, when lead paint was banned from residential use in 1978, many manufacturers were left with a lot of unsellable inventory.
It can be difficult to predict when certain products will become obsolete, but it is crucial to keep track of trends in the industry and be prepared for such a situation.
How to reduce obsolete inventory
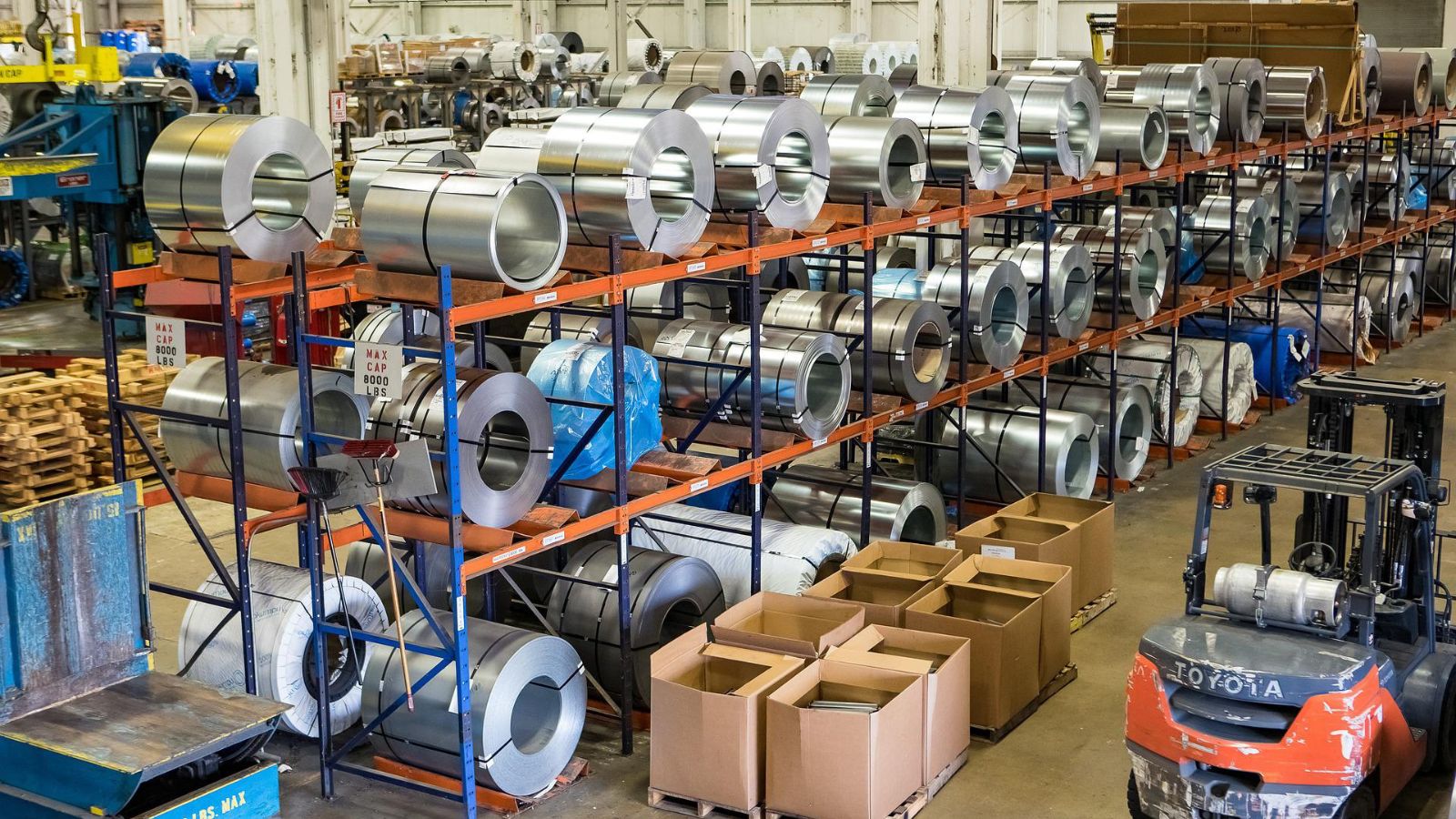
If you find yourself with a warehouse full of slow-moving and obsolete inventory, here are some strategies for reducing it:
- Repurpose — There may be a way to repurpose the inventory into a new product. As Anthony Bourdain famously explained in The Big Short, “it’s not old fish. It’s a whole new thing!”
- Rebrand — If the product is still a viable option, try rebranding it and marketing it to a new demographic
- Sell off — If all else fails, there may still be damaged and obsolete goods that can be sold at a reduced rate for raw materials or scrap
- Donate — Consider donating it to a charity or non-profit organization that can benefit from it
- Recycle — If the entire product cannot be reused, recycle it and reduce your waste costs
Remember, there are often creative solutions to obsolete inventory. Don’t give up too soon!
How to prevent obsolete inventory
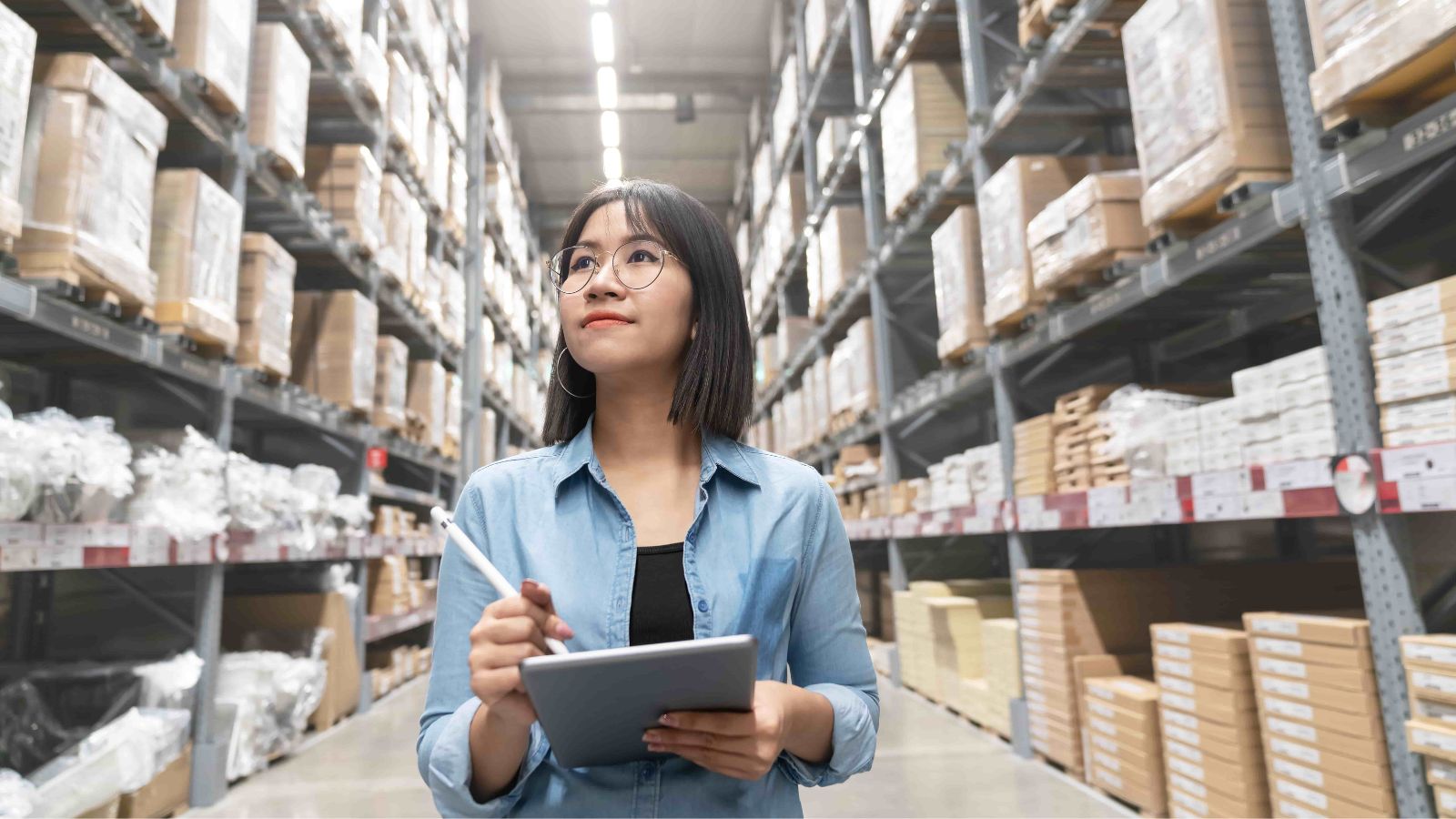
Dealing with an obsolete inventory reserve isn’t a pleasant experience for most companies, so the best way to prevent it is to have a plan in place from the beginning. Here are some tips for preventing obsolete inventory:
- Monitor trends — Keep an eye out for any changes in demand or new technologies that could render your product obsolete
- Buy smartly — Don’t buy too much of any particular item, as this can lead to excess stock when customers move on to something else
- Adjust pricing — If you sense that a product is going obsolete, consider offering discounts so you can move it out faster and make room for newer products
- Automate processes — Use an automated system such as barcode scanning or RFID tagging to keep track of your inventory and detect when certain items are becoming obsolete. This will allow you to act before it’s too late
- Innovate — Introducing new products or improving existing ones can help keep your inventory from becoming obsolete
Obsolete stock is a reality in the manufacturing industry. But with a bit of planning, you can reduce its impact on your business and ensure that only profitable products remain in stock.
How Katana helps with inventory obsolescence
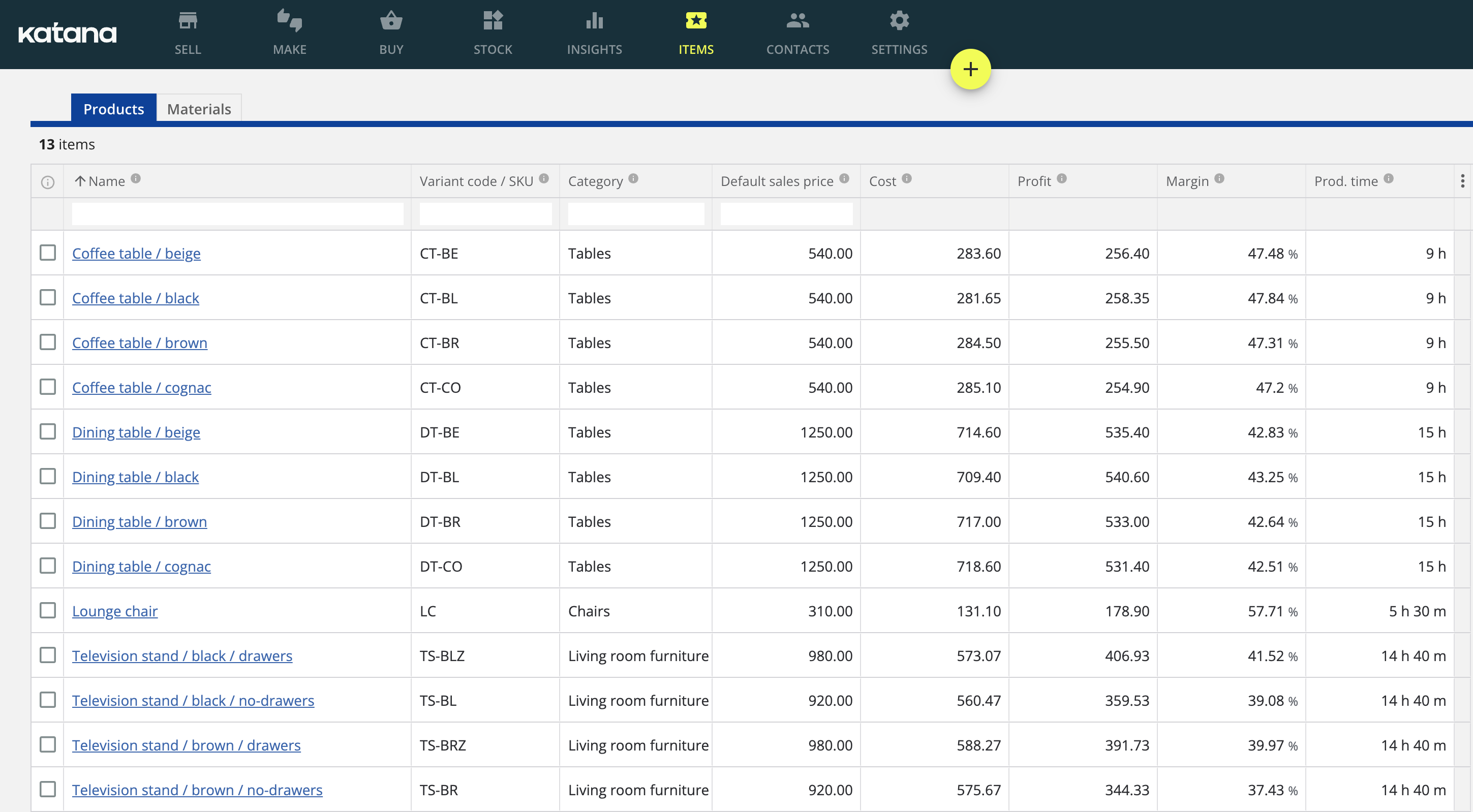
Being proactive is critical when it comes to inventory obsolescence, and having a partner like Katana Cloud Inventory can help. Katana’s manufacturing and inventory management software is an all-in-one platform that allows you to better understand how, why, and where your products are becoming obsolete.
Katana’s software automates and streamlines the entire inventory management process, giving you visibility into your inventory levels in real time. This allows you to identify which products are becoming obsolete and take steps to prevent them from clogging up your warehouse space.
Plus, Katana can also help with pricing decisions so that you can move out older items quickly without sacrificing profits.
With Katana’s powerful tools, you can rest assured that your inventory is always optimized for maximum efficiency and profitability.
Request a demo today!
Obsolete inventory FAQs
What is the definition of obsolete inventory?
Obsolete inventory is any product sitting in a warehouse for too long and no longer has a buyer. It can include outdated parts, components, or materials no longer used in production.
What causes obsolete inventory?
Technological advances, changes in customer demand, governmental policy changes, or many other factors can cause obsolete inventory.
How can I reduce my obsolete inventory?
It can be difficult to move obsolete inventory, but consider repurposing, donating, or discounting the products. You can also use automated systems to detect when certain items are becoming obsolete and adjust your inventory accordingly.
How to get rid of old inventory?
The disposal of obsolete inventory occurs when it cannot be repurposed, kitted, donated, or discounted. Depending on the type of product, this could be done through recycling programs or other disposal methods. At this point, it will be written off as a total loss on the company’s financial statements.
Table of contents
Inventory Management Guide
More guides from Katana
Get visibility over your sales and stock
Wave goodbye to uncertainty by using Katana Cloud Inventory for total inventory control
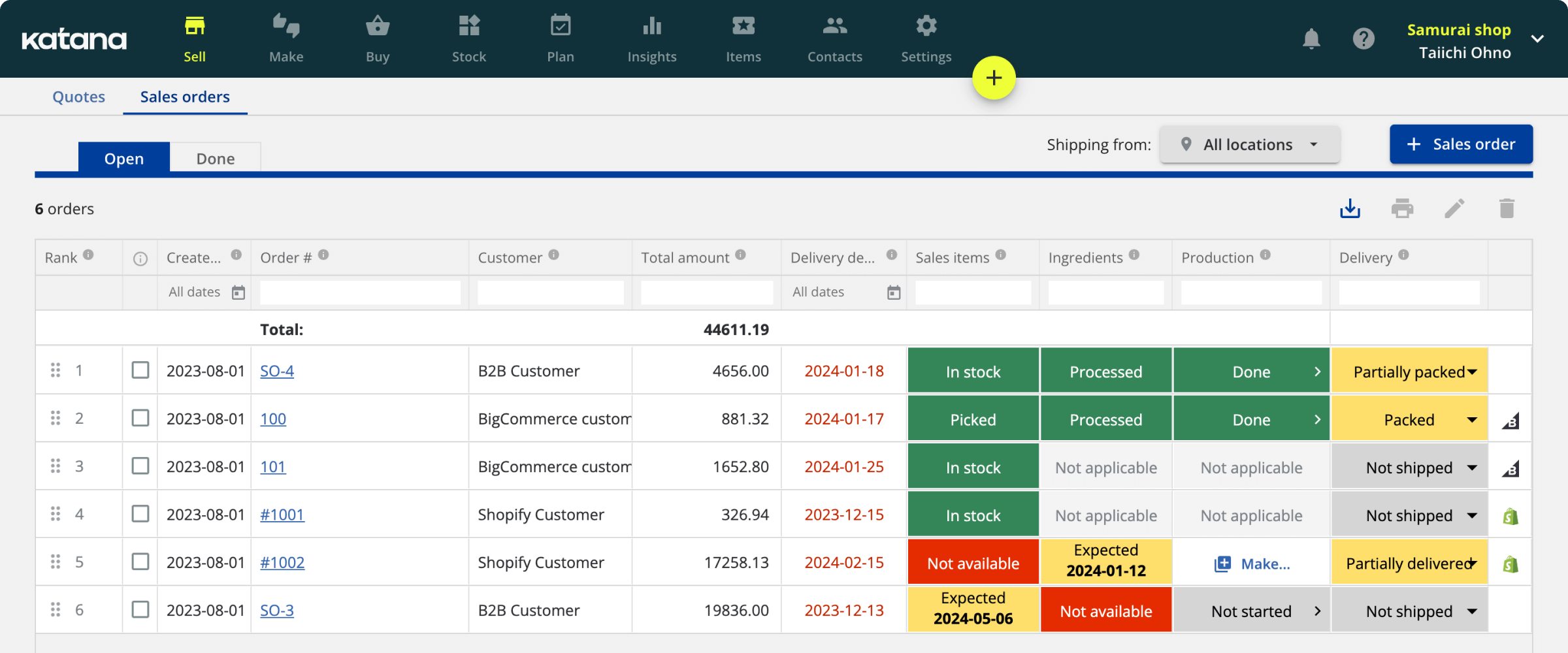