Optimize your factory with a production layout guide
An efficient production layout can improve your workflow and minimize costs. Keep reading to learn about essential strategies and practical tips for optimizing your manufacturing.
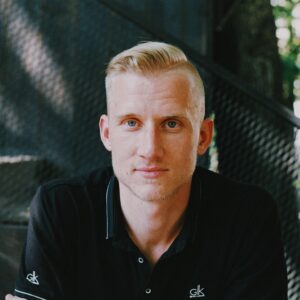
Henry Kivimaa
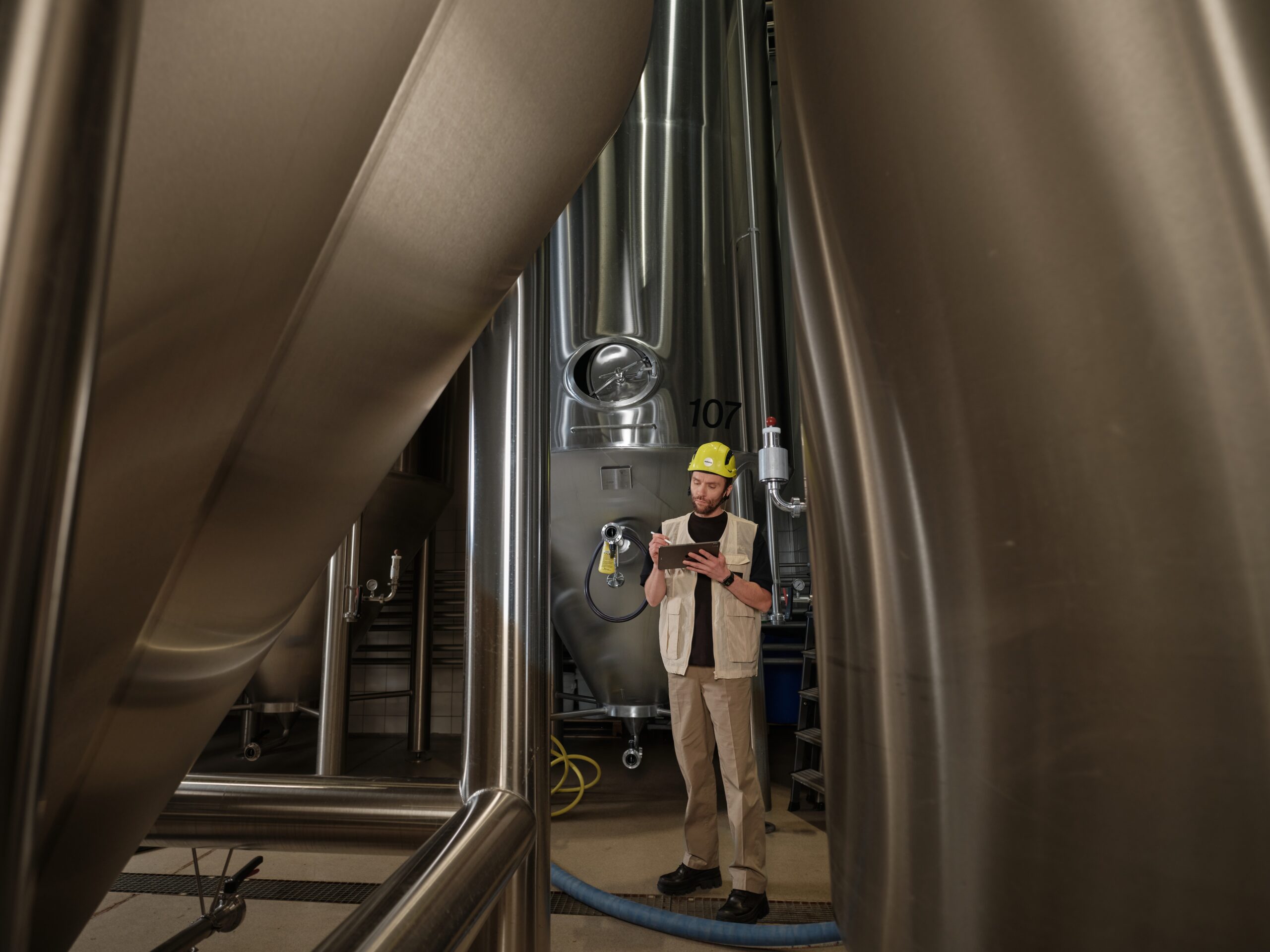
A manufacturer’s success is often attributed to how smoothly their operations work.
While machinery, materials, and skilled staff are important, it’s also essential to ensure the fast and efficient execution of tasks.
Time is money, and wasted time is money wasted. Luckily, there are strategies and methods for identifying and eliminating bottlenecks in your manufacturing processes.
This is where a thorough production layout guide enters the game.
What is production layout?
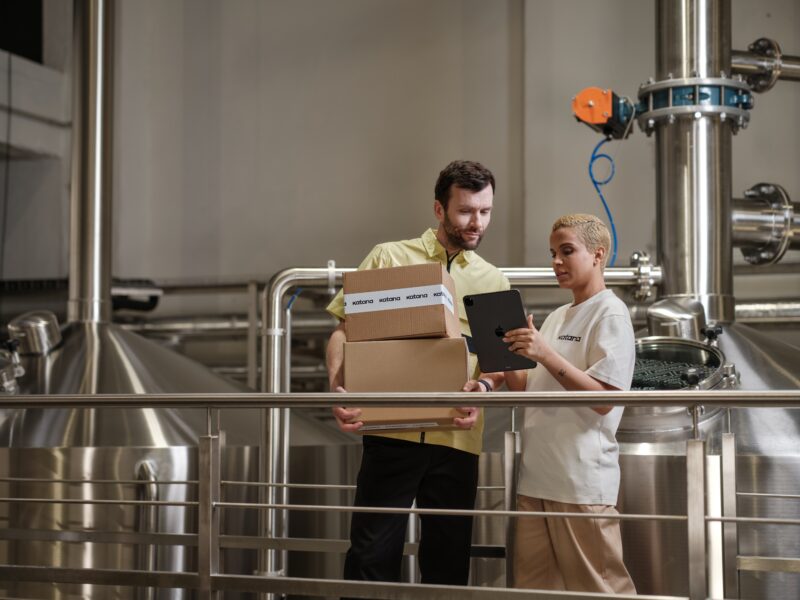
Production layout is the arrangement of physical facilities in a manufacturing plant.
It involves the strategic placement of elements, including machines, workstations, and storage areas, to streamline the flow of materials and workers. A well-designed production layout helps manufacturers minimize their production costs, enhance productivity, and improve the overall efficiency of their processes.
A production layout guide is a document that helps businesses map their factories in a way that’s understandable to all teams and workers.
It provides detailed instructions and best practices for arranging the physical components of your facility. Think of it as a blueprint for organizing your production floor.
A manufacturing layout typically includes tips to optimize workflows and streamline tasks to increase efficiency. Factory layout design helps manufacturers simplify operations, improve cross-team collaboration, and meet production goals while minimizing disruptions and wasting resources.
6 principles of manufacturing layout
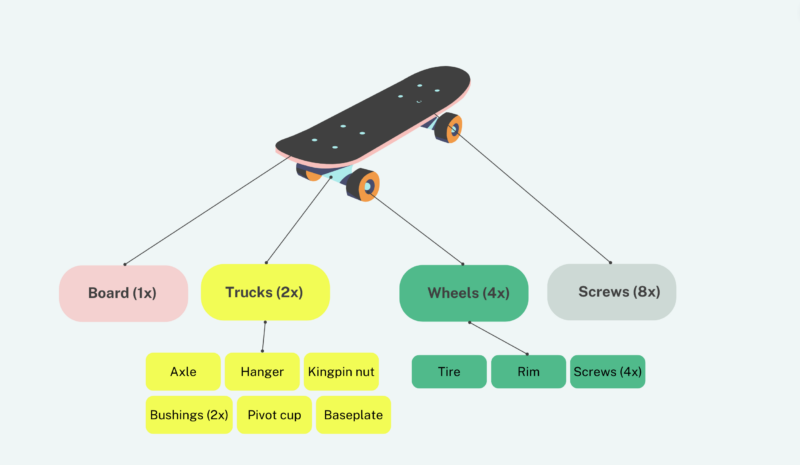
While a manufacturing layout mostly depends on the specific needs of a company, there are some universal truths to keep in mind when creating a production layout guide for your operations.
Material handling
Efficient material handling is all about reducing the time spent moving materials and supplies throughout the production process.
A production layout design will help you ensure that the materials are transported in the shortest possible distance with the least amount of handling. This allows you to reduce the time and cost of each process, minimize the risk of potential damage, and streamline your production flow.
Some techniques employed for better material handling include conveyors, automated material handling systems, and optimized pathways within the facility.
Workflow
An uninterrupted workflow is a solid foundation for maintaining high quality and efficiency.
When creating a factory layout design, it’s recommended to map out all processes in a way that allows for seamless transitions between different stages of production. Each workstation should be strategically placed to keep products flowing logically and safely from one task to another.
Tools like value stream or shop floor planning can minimize bottlenecks and interruptions. A clear overview of the sequence of all necessary tasks helps you align all manufacturing stations accordingly.
Space utilization
Optimal space utilization means making the most of all available space and using it to its full potential.
This means that equipment, workstations, and storage areas are placed in the most effective and safe way for the workers and materials. A well-designed factory layout will help you reduce clutter, improve the movement of materials and products, and ensure that every inch of your space has its purpose.
The most common techniques for space utilization are vertical storage, modular furniture, and strategic zoning. Each allows you to create a more streamlined and productive environment for manufacturing and storage.
Katana for production management
Sign up for a demo call and see how Katana can improve your production processes, streamline your tasks, and automate those mundane day-to-day operations.
Flexibility
As your business grows, so does your production layout.
The factory layout design should support flexibility to accommodate changing processes, product lines, and market demand. Adaptability will allow you to quickly respond to new opportunities or tackle challenges without wasting too many resources.
Module equipment and furniture, adjustable workstations, and a scalable layout can enhance flexibility across the shop floor and ensure that your facility grows along with your business.
Safety
The safety of your workers, equipment, and products should be your top priority.
A safe plant layout reduces the risk of accidents, injuries, and damage. This fosters a trusting relationship with your team and is vital to staff loyalty.
Safety at the workplace can be achieved with proper spacing between machinery, providing safety barriers, adding clear signs around the factory, and maintaining cleanliness in the work areas.
Additionally, consider the long-term well-being of your employees by implementing ergonomic equipment that doesn’t leave them sore after the workday.
Employee morale
Workspace happiness greatly depends on the work environment that your staff is surrounded by daily.
To keep your staff happy and loyal to you, try to make their tasks as smooth and efficient as possible. Comfort, support, and simplicity can boost employee satisfaction, motivation, and productivity.
Think of factors such as adequate lighting, ventilation, ergonomic workstations, and rest areas for lunch or coffee breaks. Involving your team in the creation of a production layout design will tell you exactly what they expect from their daily surroundings and help you create a better space for everyone.
How to design a factory layout
Designing a production layout should begin by mapping out your goals and requirements. Clearly define the objectives of your factory layout design, whether it’s maximizing efficiency, reducing lead times, or optimizing storage.
To find out what needs to be changed, it’s wise to understand your current workflows. This means outlining your processes, identifying bottlenecks, and determining the optimal sequence of operations.
Once your workflow is clear, the next step is gathering detailed information about your resources: the space, the equipment, and the team of workers. With this data, it’s easier to create simulations of various layout options to visualize the different setups and how they could impact the efficiency of your production.
Evaluate these options and analyze how they align with the goals you set at the beginning of the design process. Also, think about the future of your business and stay flexible for any potential changes.
Once you’re happy with the layout, it’s time to develop a detailed implementation plan. Outline the steps needed to transition to the new design, but try to minimize the disruption in your ongoing processes. This plan should include timelines, resource allocation, and responsible staff. It’s also wise to come up with strategies to deal with unexpected challenges in the implementation, like disruptions in production or damage to equipment.
Throughout the whole implementation process, stay aligned with stakeholders and your staff. Remember, your workers are the ones who have to manage and deal with the new layout, so their involvement is crucial. Once done, keep monitoring the processes and ask for continuous feedback to identify any issues and adjust when necessary.
The goal is to ensure that the layout remains efficient and effective as your demands and needs evolve.
Tools and techniques for factory layout design
When designing a production layout, it’s best to use smart software or methods to make the process easier. “Work smarter, not harder” is the motto here.
CAD software is often used to create 2D and 3D models of the factory layout and visualize the planned design before implementing it. This enables the accurate placement of equipment and workstations, ensuring that all the space is used effectively. CAD software also lets you make easy adjustments as the design evolves or your needs change.
Flowcharts are a simple solution to visualize the sequence of processes and materials in your production flow. Having a detailed rundown of your manufacturing allows you to identify bottlenecks, inefficiencies, and areas for improvement.
Simulation software, as the name already hints, lets you run simulations and virtually try out different factory layout designs. This way, you can change the workstations, equipment placement, and worker movements until you find the best solution. You’ll be able to see the benefits and challenges of various setups that you may be torn between and can base your decision on actual data and accurate simulations.
Value stream mapping (VSM) is a technique that maps out the current workflows and creates a future state that shows you exactly what you’re headed toward. It provides a holistic view of your entire production system, helping you target inefficiencies and tackle excess waste. VSM is an excellent way to adopt more lean manufacturing practices in your operations.
5 types of production layout
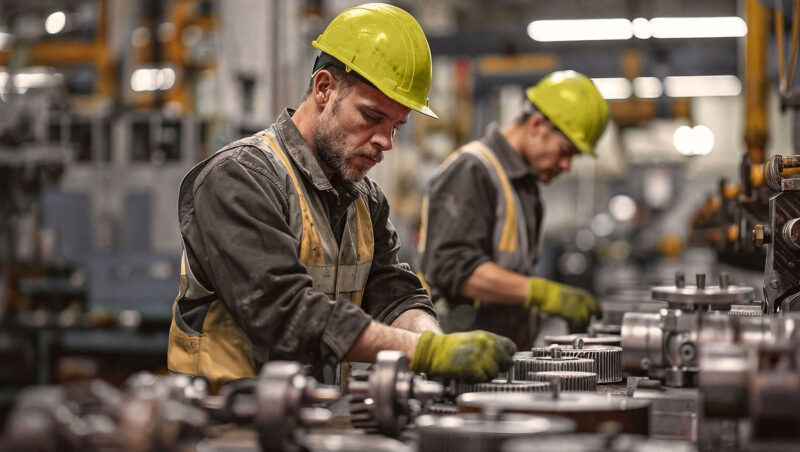
When designing a factory layout, most businesses try to sort the stations and storage spaces together by one leading factor. Here are the primary types of production layouts.
- Process layout — Group similar processes or machines together. This layout provides great flexibility for handling a variety of products or working in small batches at a time. However, it can be too complex and time-consuming for larger operations where products travel across the facility a lot.
- Product layout — Arrange machines and workstations in a line according to the sequence of operations. The high efficiency and speed make this setup ideal for mass and large-scale production. On the other hand, as this layout is designed for a specific product line, it is more sensitive to downtime and isn’t as flexible.
- Cellular layout — Set up different machines into cells that produce a specific family of parts or goods. This layout combines the flexibility of a process layout with the efficiency of a product layout. As a downside, it requires more extensive planning and balancing of workloads, and there could be periods when some equipment goes unused for a while.
- Fixed position layout — Keep the product stationary while workers and machines move around it. This arrangement works for products that are too large or heavy to be moved around the facility and provides more adaptability during the production process. However, it isn’t as efficient as other layouts and requires significant coordination of teams and equipment.
- Combination layout: Integrate elements of various layouts to meet specific production needs. This approach provides manufacturers with the benefits of all the different layouts and gives them the flexibility to adapt to any changes. Due to its diversity and personalization, this can potentially be the most complex, costly, and time-consuming layout to design and implement.
Implementing a factory layout
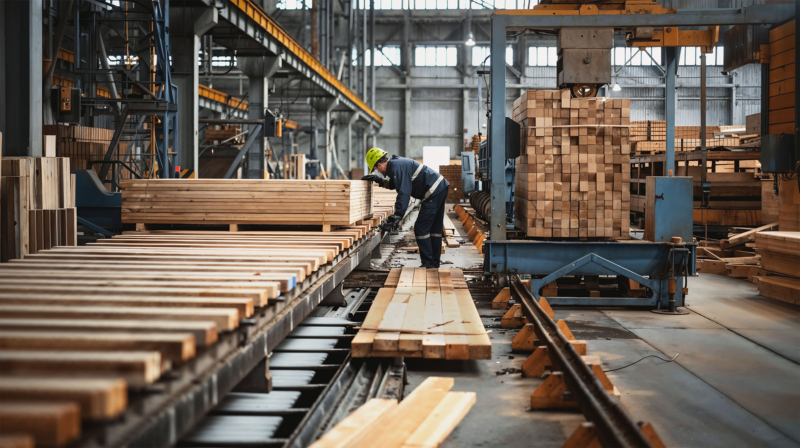
Once you’re confident in your production layout design, it’s time to implement it.
Phased implementation
Depending on the scale of changes that need to be made to your current layout, it’s recommended that the implementation be done in phases. Phased implementation allows you to continue production while some parts of your factory are reorganized, which is especially useful in larger operations that can’t afford complete shutdowns.
Implementing the new setup in stages will also give you the opportunity to test the layout and make changes along the way without having to rearrange the whole design.
Equipment and machinery
One of the most complex steps of a production layout design implementation is the reconfiguration of equipment.
Existing machines have to be relocated, new equipment installed, and all systems accurately integrated into the new setup. Ensure that your machinery has all the necessary utilities, such as power, air, and water, to run smoothly.
Don’t forget to test your equipment before restarting production, or you could risk quality issues and even having to pause manufacturing for a while.
Material handling
To support the new factory layout design, you should also update your material handling systems.
Use conveyors, adjust storage locations, or update your inventory management practices to ensure smooth material flow, minimize handling times, and reduce the risk of bottlenecks.
Remember to train your workers on the new practices to make the transition to your new layout as smooth as possible.
Monitoring
At this stage — as tempting as it may be to put your feet back and relax — it’s crucial to keep an especially keen eye on all the changes you’ve made.
An excellent way to do that is by tracking your key performance indicators (KPIs):
- Production speed
- Error rates
- Generated waste
- Costs
- Equipment downtime
Maintain a feedback loop with your employees. Your team has first-hand experience with the new layout and how it works in practice. Their input can help you find areas for further improvement and adjustment.
Case studies and successful examples
Looking at successful implementations of production layouts can provide inspiration and valuable insights for your own setup.
- Toyota — Lean manufacturing practices and Just-in-time (JIT) production have made Totoya a leading example of efficiency and flexibility. Their primary focus is on eliminating waste and improving productivity in a sustainable and environmentally friendly way.
- Tesla —Tesla’s Gigafactory integrates advanced robotics and automation to streamline battery production and vehicle assembly lines, helping them achieve high productivity and scalability.
- IKEA — A modular production layout provides IKEA with flexibility and efficiency when handling high volumes and a diverse range of products. The Swedish furniture titan offers a great example of space utilization and process optimization.
Main manufacturing layout challenges

Rome wasn’t built in a day, and a proper production layout design doesn’t happen overnight.
It requires careful planning, effort, and overcoming challenges. So, let’s take a look at what issues you might run into and how to tackle them effectively.
- Cost — Redesigning and implementing a new layout requires a high initial investment, which smaller businesses may not have the capital for. However, investing in a personalized manufacturing layout will pay off in the long run.
- Downtime — Some workstations may need to be shut down for the implementation period. This could impact your output, but think of it as taking a breath before continuing to work even more efficiently.
- Employee resistance — If your employees don’t understand the larger impact of a redesign, they might not be on board with it or have some doubts. Be transparent, explain how this will make their jobs easier, and train them to navigate the transition as smoothly as possible.
- Space constraints — Working with limited space can make it difficult to arrange all your equipment, workstations, and materials efficiently. Careful planning and creative solutions can go a long way and help you maximize the use of your available space.
- Scalability — When designing your plant layout, consider future production changes and growth. By leaving room for adaptability, you’ll be able to make minor modifications without completely reorganizing the production floor.
How can Katana help your production layout?
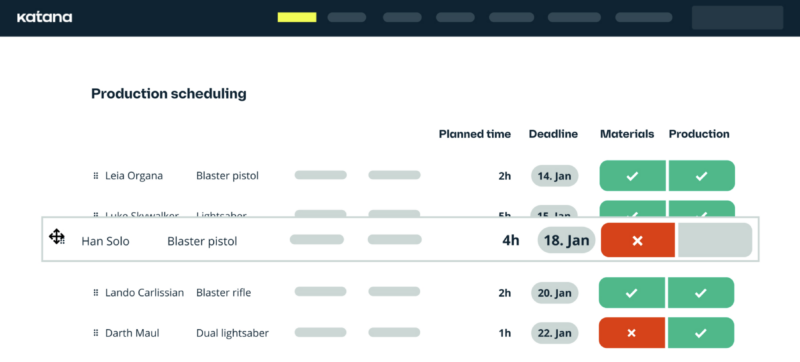
Katana is a powerful cloud-based solution that allows you to optimize your production layouts and streamline manufacturing processes.
Features such as real-time inventory tracking, production planning, and shop floor control help manufacturers achieve greater efficiency and productivity. Katana also offers integrations with various accounting, shipping, ecommerce, and other services to centralize all your production and business processes on one platform.
Take this interactive tour of Katana, see its intuitive interface, and learn how it can benefit your business:
Ready to revolutionize your production layout? Book a demo with Katana today and transform your operations.
Until next time — happy manufacturing!
Table of contents
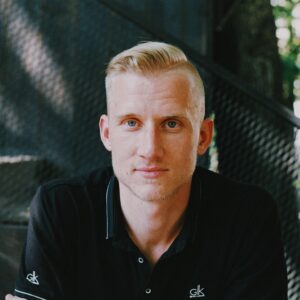
Henry Kivimaa
Get inventory trends, news, and tips every month
Get visibility over your sales and stock
Wave goodbye to uncertainty with Katana Cloud Inventory — AI-powered for total inventory control