What is in-transit inventory? Everything you need to know
When it comes to in-transit goods, implementing inventory management software can provide visibility and transparency of the entire supply chain. But tracking all of your comings and goings can be tricky, so how do you rise to the challenge?

Ioana Neamt
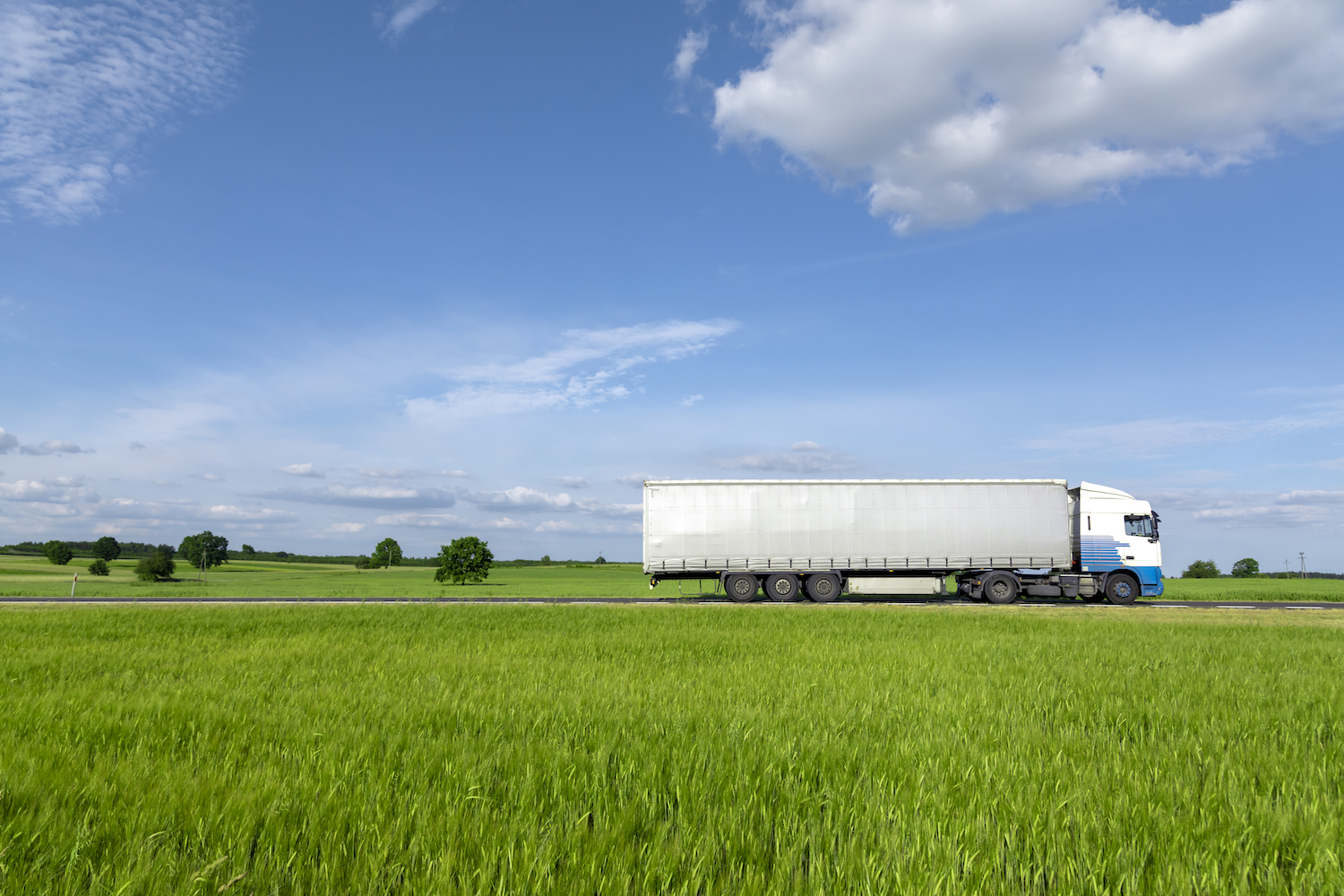
Efficient inventory management is a critical component of any e-commerce or manufacturing business and one that can significantly impact a brand’s reputation and relationship with partners and customers. However, keeping tabs on inventory at all times, whether it’s inventory on hand or in transit, can pose a challenge.
When it comes to in-transit inventory, implementing inventory management software can provide visibility and transparency of the entire supply chain. But tracking all of your comings and goings can be tricky, which is why knowing who is accountable for goods that are in transit to their destination is key.
What is in-transit inventory?
In-transit inventory, otherwise known as pipeline inventory, is inventory that has been shipped from the supplier but is still in transit to its final destination, be it a distribution center, a physical store, or an e-commerce facility.
At this stage, the inventory is not under the direct control of the supplier, which makes it tricky to track and ensure that it will arrive safely at its destination.
Still, goods that are traveling to their destination should be viewed similarly to goods that are on hand, at least until ownership of these goods has been transferred to the buyer. Until that exchange of ownership happens, the supplier is responsible for in-transit inventory.
In-transit inventory ownership
To determine who is responsible for goods in transit, it’s important to establish when the ownership of the goods transfers to the buyer. There are two potential scenarios here — let’s take a look at both of them.
Freight on board (FOB) shipping point
In this case, ownership of in-transit goods transfers to the buyer at the origin at the shipping point when the goods are loaded. It’s the most common type of ownership transfer, and it transfers liability for the goods in transit to the buyer early on in the delivery process. From this point on, the seller is no longer accountable for the location and delivery of in-transit inventory.
Freight on board destination
In the case of FOB destination classification, ownership and accountability transfer to the buyer only when the goods arrive at their destination. The seller owns and is responsible for the goods from the moment they ship until they reach the buyer.
How to account for in-transit inventory
The ownership usually transfers at the same time the money is paid for the goods in transit, depending on the agreement signed between the buyer and seller.
If the title or ownership for the goods is not passed to the buyer, it’s as if no purchase or sale has happened, which means the seller is responsible for the in-transit inventory until it reaches its destination.
If the title is transferred, and the sale is recorded in both the seller and the buyer’s books, that means ownership has been transferred to the buyer, and they are responsible for the goods in transit.
What makes tracking in-transit inventory difficult?
Keeping accurate track of in-transit goods can be a real challenge due to the nature and complexity of supply chain networks. As goods travel through different territories, switching between different transportation options and carriers, it can be tricky to maintain transparency and visibility every step of the way.
Relying on different carriers, switching time zones, traveling through border crossings — all of these stages can come with different challenges, such as mistakes, inaccuracies, tracking inconsistencies, or delays. Unexpected events such as severe weather episodes or customs delays can also disrupt the inventory tracking flow, making it difficult to keep accurate tabs on goods in transit.
Some potential issues can be avoided by insuring goods against damage from natural disasters, in-transit accidents, theft, accidental damage of goods, and so on. Investing in shipping insurance can reduce risk and prevent sellers and buyers from financial losses.
Both the seller and buyer can implement shipping insurance for in-transit goods, depending on the ownership clauses established in the sale contract. Additionally, implementing inventory management software like Katana can enable transparency of the supply chain and make it easier to keep tabs on all shipments in real time.
Calculating in-transit inventory costs
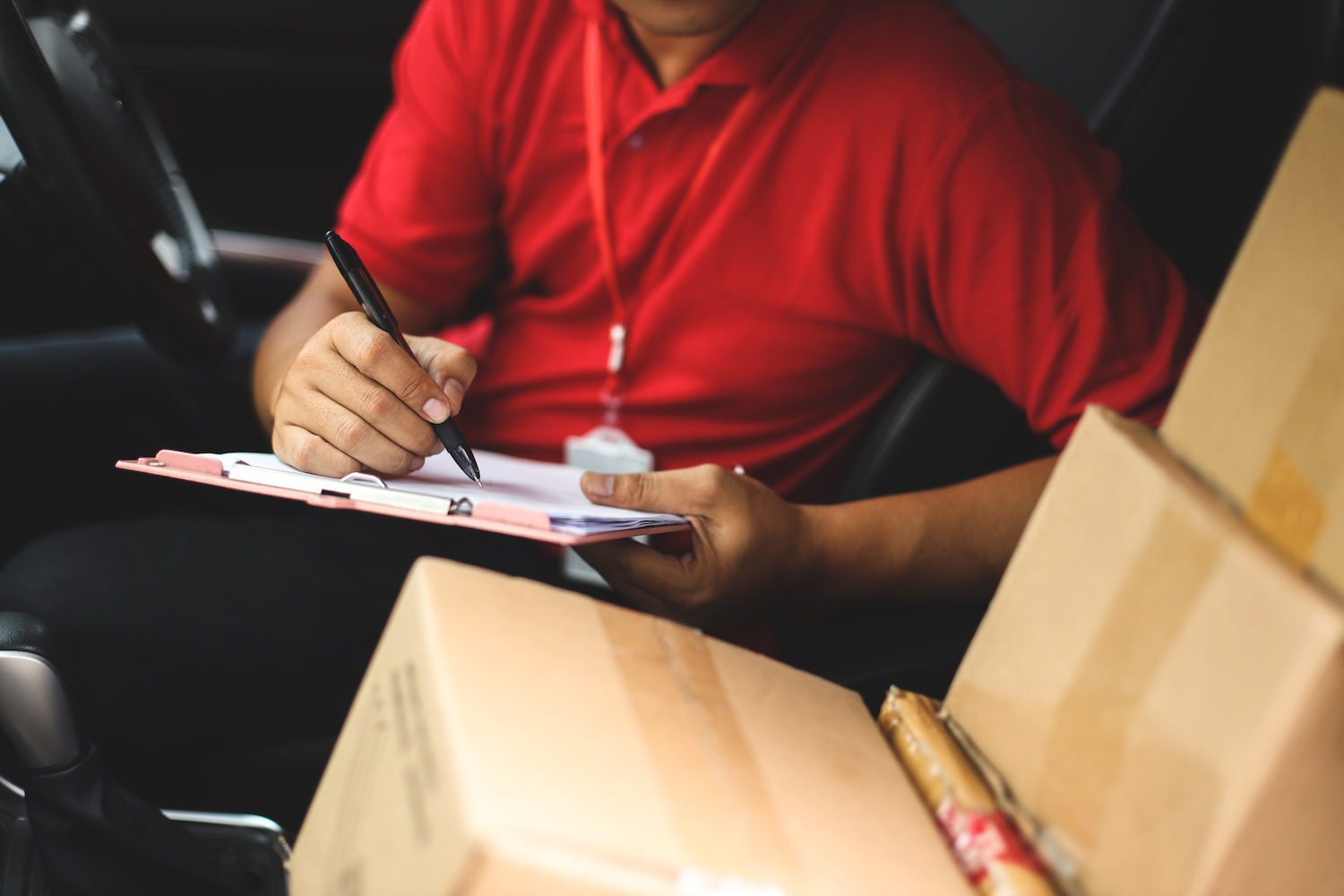
Figuring out your in-transit inventory costs can be challenging, especially given all the unforeseen events that can throw the delivery schedule off track. However, there are ways for businesses to estimate these costs and plan a reliable, realistic budget for their in-transit goods.
First of all, it’s important to establish who covers the costs for in-transit inventory. In the case of a FOB origin shipment, the buyer is liable for the goods as soon as they are shipped. This means they’re basically paying for storage for goods that haven’t physically arrived at their destination yet.
Calculating the costs for these in-transit goods is just like calculating them for on-hand inventory that you already store in a warehouse or facility. You must factor in storage facility costs like heating and utilities, rent, and maintenance costs, as well as insurance costs for the in-transit inventory, if applicable.
For most businesses, these costs will amount to roughly 15% or 20% of the inventory purchase value. When it comes to in-transit inventory, you’ll also be paying storage costs while the goods are still traveling. Depending on how many days the shipment will take to arrive, your total cost will vary, looking something like this:
The daily value of your in-transit inventory = Cost of inventory x storage cost / 365
If you’re waiting to receive an order worth $20,000, and it takes roughly 14 days for the goods to arrive, you can calculate the total costs as follows:
$20,000 x 0.15 / 365 = $8.22 for each day spent in transit, amounting to $115 for the two weeks
This way, you’ll know to budget for $20,115 for the next order.
Keep track of your in-transit inventory with Katana
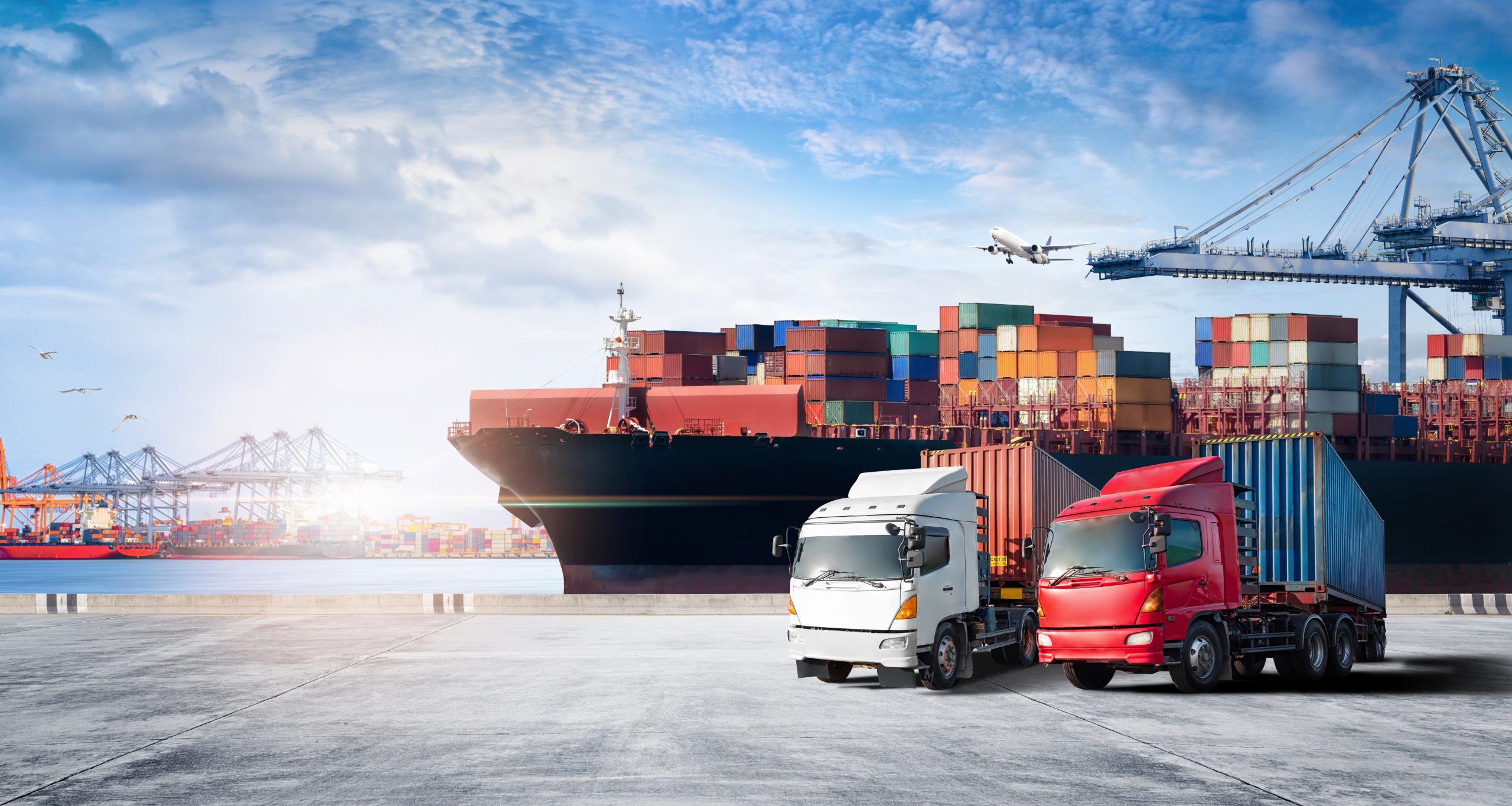
A reliable and efficient inventory management system can help businesses avoid issues related to in-transit inventory, maintain a trustworthy relationship with clients and suppliers alike, and ensure customer satisfaction with each shipment.
Katana’s cloud inventory software enables businesses to keep accurate and real-time tabs on their in-transit goods, ensuring they arrive safely at their destination. It allows users to track sales, estimate and calculate costs and revenue, and identify top-performing and underperforming products using historical data.

Ioana Neamt
Table of contents
Get inventory trends, news, and tips every month
Get visibility over your sales and stock
Wave goodbye to uncertainty with Katana Cloud Inventory — AI-powered for total inventory control