Downtime in manufacturing: how to make it productive
Downtime in manufacturing can sabotage a business or prevent further crises. Read on to learn all about the pros and cons of downtime.
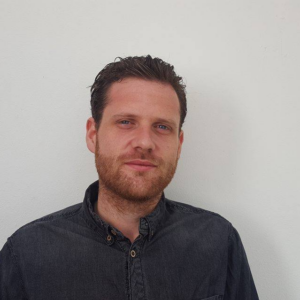
James Humphreys
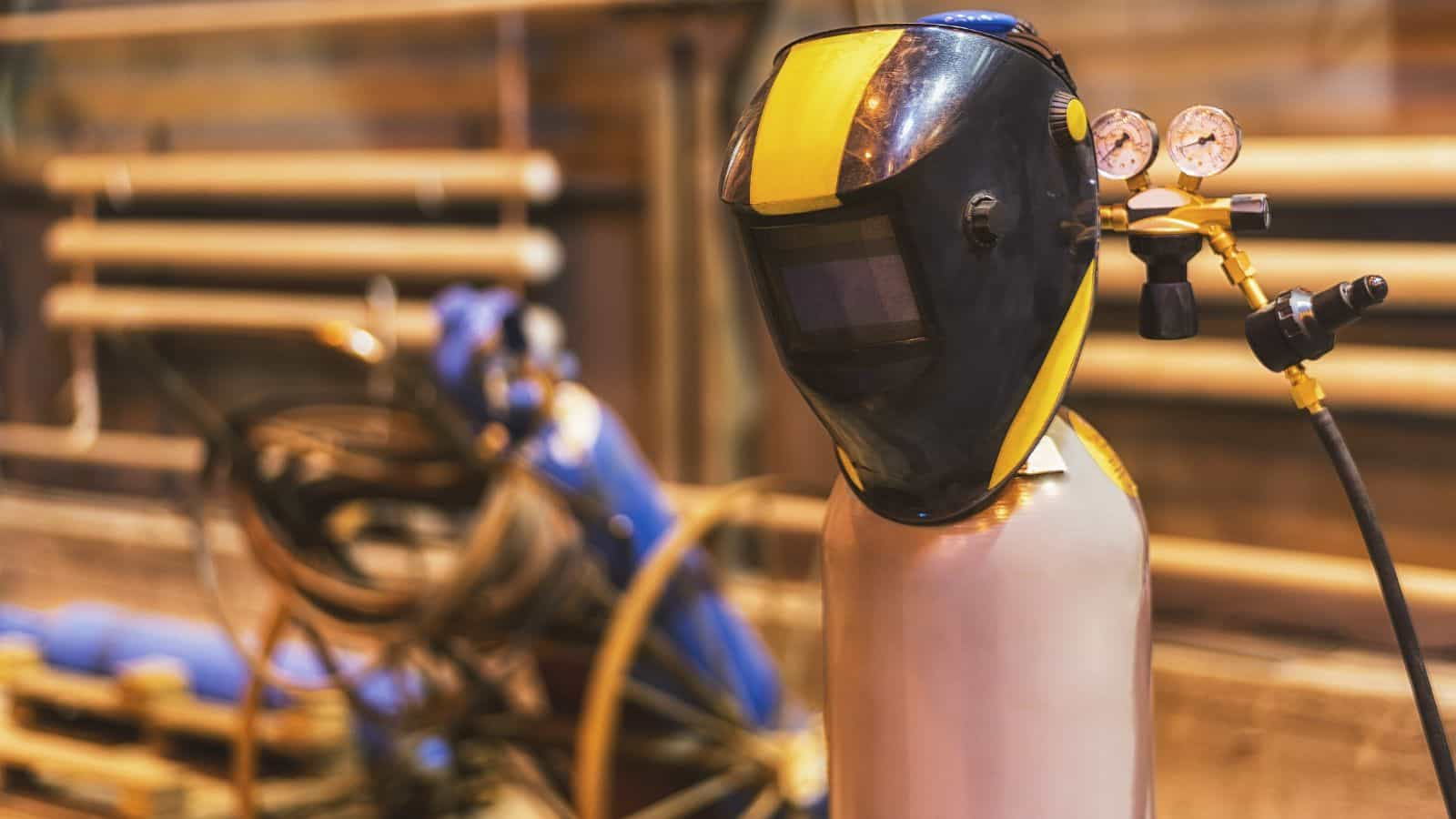
Downtime in manufacturing can be a serious issue. It can be damaging to a business’ reputation, efficiency, and bottom line.
If left unchecked, downtime can cause serious issues such as compromised staff safety, loss of business, or even data breaches.
Downtime can be triggered by equipment failures, material issues, or even a shortage of operators — all of which means that scheduled production must halt.
While production downtime can happen for many reasons, the key is identifying these causes and implementing systems to prevent them from happening again. Interestingly, planned downtime can help to reduce the risk of unplanned downtime and should be a core part of any manufacturing company’s strategy.
In this article, you’ll find out some of the common causes of unplanned downtime, how to calculate the cost of downtime in manufacturing, and ultimately, how to reduce downtime in manufacturing.
What is downtime in manufacturing?
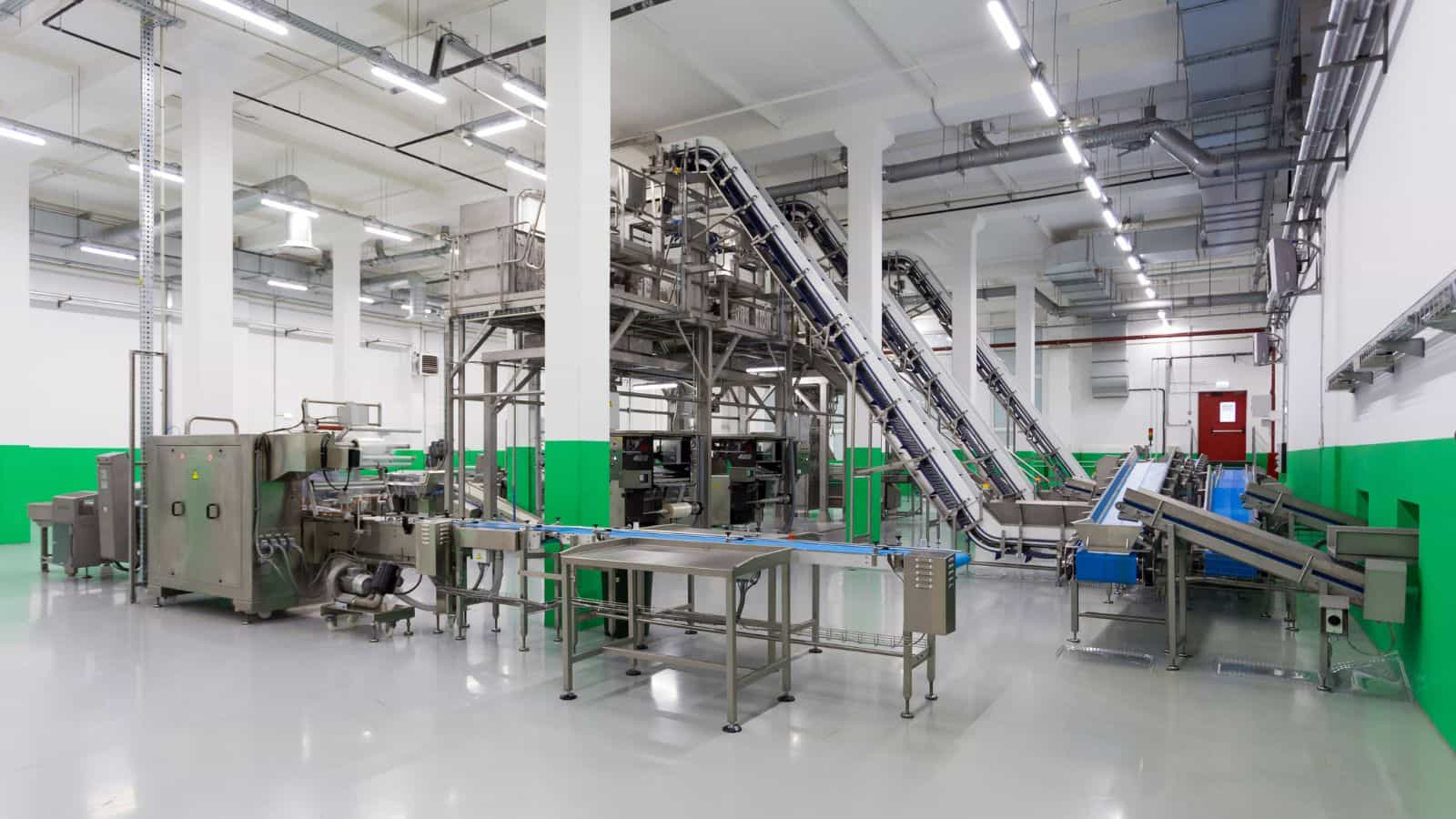
Downtime in manufacturing is exactly what it sounds like – when a company’s manufacturing process stops. Downtime in manufacturing can be planned and thus beneficial, so on the flip side, unplanned downtime is considered unnecessary and disruptive.
Some people use the term machine downtime simply when a piece of equipment, machine, or entire manufacturing system is not functioning. This may refer to a planned or unplanned stop.
As we have already mentioned, there are two types of manufacturing downtime:
- Unplanned downtime — which can be troublesome
- Scheduled downtime — which can be beneficial
It is important to look at the causes of downtime to recognize disruptive patterns, prevent them, and improve manufacturing processes as a whole. Some of the causes of downtime in production might be:
- Inadequate maintenance is often the most prolific cause of downtime in machinery, and it can be very easily fixed. Many companies use AI software to identify when maintenance and inspections should be carried out to minimize disruptions.
- Hardware failure is another common problem for manufacturers. Machine components such as sensors, fans, belts, pumps or motors can fail, or jams can occur within the system. Ensuring that skilled operators and technicians with replacement parts are on-site reduces delays in getting the manufacturing machinery up and running again.
- Delays in material can be another issue faced by manufacturers. If a core material has not arrived on-site in time, then manufacturing obviously must stop. Keeping tight control over supply times and production can help to lessen this problem.
- Human error must be cited as one of the possible causes of production downtime. Mistakes are sometimes made on production lines, changeovers between shifts can be too slow, or key personnel could be unexpectedly absent. All of these could cause unplanned downtime and significant delays in manufacturing.
Suppose you can review these factors and develop a clear understanding of what is causing the greatest delays to your manufacturing process. In that case, you can put new systems in place to make it operate more efficiently.
The cost of unplanned downtime
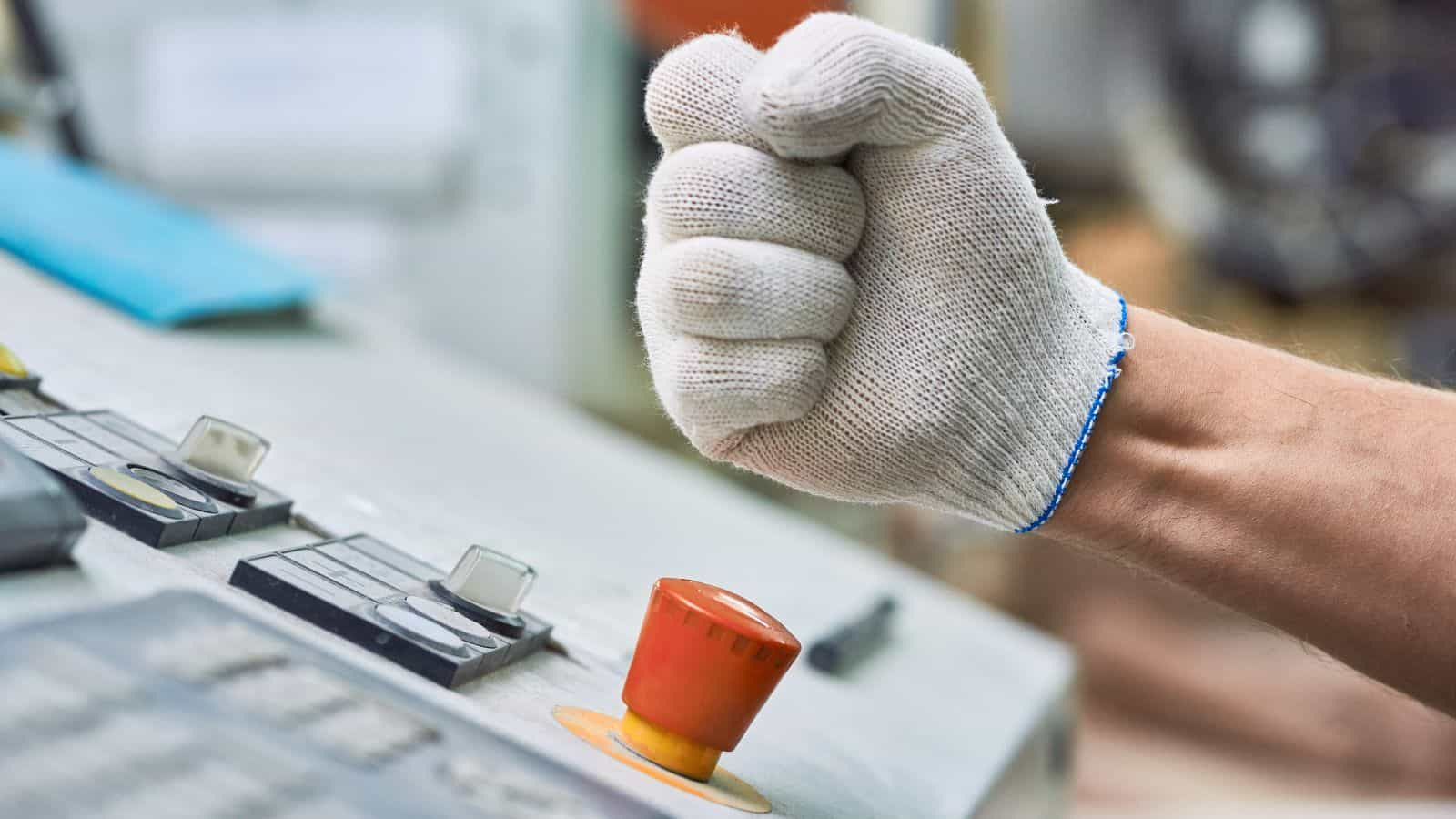
Downtime in manufacturing is taken incredibly seriously. There is an equation to help you calculate exactly how much it is costing you:
Time equipment is down/Planned operating time * 100 = Downtime %
Broken down, this is how you calculate the equation:
- Ascertain what your planned operating time should be in a set period of time. For example, your production should be operational for 10 hours per day, 20 days per month. This will equal 200 hours per month;
- Review the previous set period (for example, last month) and record how much downtime you experienced;
- Subtract the actual downtime from the planned operating time; and
- Convert it into a percentage to find out how efficient your manufacturing process really is.
It will come as no surprise that production downtime is one of the biggest problems faced by manufacturers and is an issue that is being tackled on a daily basis. Keeping well-informed of your manufacturing systems, operating in a lean way, and tracking inventory and production processes are all ways in which downtime in production can be minimized. Centralizing bookkeeping and manufacturing processes using software like Katana can make a real difference.
If we move away from the mathematical equation, some of the tangible costs of downtime in manufacturing are as follows:
- Disappointed customers when they do not receive their goods on time;
- Damaged reputation if these disappointed customers share their grievances with others;
- Lost business due to a decrease in repeat orders;
- Potential significant losses if raw materials are unable to be used due to delays in the manufacturing process;
- Compromised staff safety if machinery isn’t working currently; and
- Unreliable data caused by potentially disrupted IT systems.
Understandably though, the greatest cost of production downtime cited by manufacturing companies is literally their financial losses.
According to a report from Deloitte, pre-Covid unplanned downtime cost industrial manufacturers approximately $50 billion each year, with an average manufacturer experiencing an estimated 800 hours of equipment downtime annually, more than 15 hours per week.
Further to this, data from Analyst firm Aberdeen Research, showed that unplanned downtime in manufacturing can cost a company as much as $260,000 an hour. Interestingly, the same study also found that unplanned downtime is one of the causes of renewed investment in digital transformation.
Benefits of planned downtime
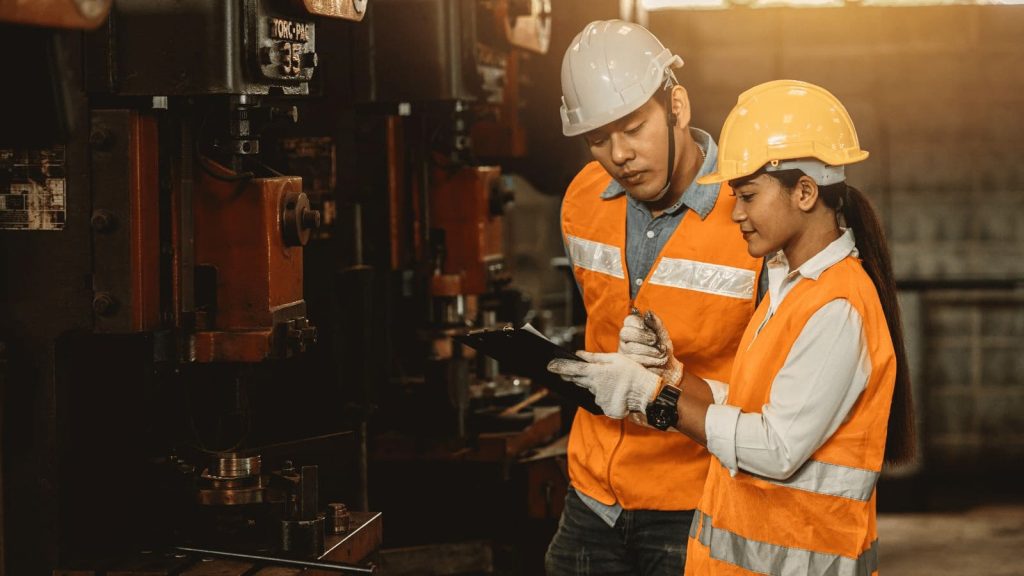
Planned downtime in manufacturing is when a company physically shuts down the machines. This can be for any number of reasons, such as repairing them, maintaining parts, testing certain areas, or upgrading/replacing certain assets. Sometimes this planned downtime is ad-hoc and may be scheduled on a particular timeframe. For example, weekly, or maybe after every 100 hours of operation.
Some of the benefits of being proactive with planned downtime are:
- Increasing the lifespan of the machine. If a machine and its parts are properly looked after, then it is more likely to operate at an optimum level for longer, thus protecting precious profit margins;
- Maintaining the efficiency of a manufacturing process. A machine cannot operate at its height of efficiency if its parts are damaged, unclean or loose;
- Avoiding disruptive downtimes. Planned downtime can reduce the risk of unplanned downtime. A planned downtime can be scheduled to fit with worker shifts and natural breaks in manufacturing — thus, even the downtime can be optimized; and
- Sustaining the correct level of IT support. Updating the software in a machine and manufacturing process is as important as looking after the hardware. It means you can ensure that your IT processes are up-to-date and fully secure.
Katana Cloud Inventory platform
Book a demo to get all your questions answered regarding Katana’s manufacturing features, integrations, pricing, and more.
How can you reduce downtime in manufacturing?
As well as scheduling regularly planned downtime, there are several other things that a manufacturing company can do to reduce unplanned downtime in manufacturing.
These include:
- Auditing equipment: This can be a laborious process, but it is the only way to understand the true operating efficiency of your machinery.
- Upgrading hardware and software: A machine is only as good as its parts, so after auditing it, ensure every aspect of your manufacturing machinery is the best.
- Staff training: This is essential to minimize downtime caused by unnecessary human error. If an error causes an unplanned downtime, properly investigating it can provide meaningful learning. Ensure all your staff is up-to-speed with the technical expertise they need.
- Maximize your cyber security: In this digital manufacturing world, cyber-attacks are becoming all too common, and cyber breaches could cause lengthy disruptions to a manufacturing process. Having protections in place, like two-factor authentication and virus shields, can minimize the chances of unplanned downtime caused by IT issues.
- Plan for the unexpected: Again, this is probably a lengthy process, but make sure you have contingency plans that help you mitigate the fallout from an unexpected accident or event. It could help to get your manufacturing processes back on track with minimal fuss.
- Ensure visibility: Having total visibility over your operations is essential. Most companies are now doing this with the help of manufacturing software that can track sales trends and accurately forecast product demand.
Downtime could ruin the productivity of your manufacturing operations. Reduce the risk of it by minimizing waste, looking after your components, and having full digital visibility of your manufacturing processes.
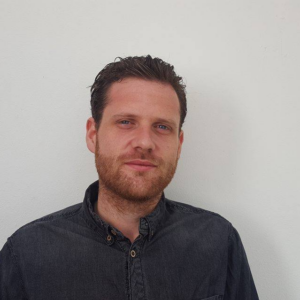
James Humphreys
Table of contents
Get inventory trends, news, and tips every month
Get visibility over your sales and stock
Wave goodbye to uncertainty with Katana Cloud Inventory — AI-powered for total inventory control