What is statistical process control (SPC) and is it for you?
SPC manufacturing is a method of analyzing production processes to identify areas of waste. In this article, we look into statistical process control.
Team Katana
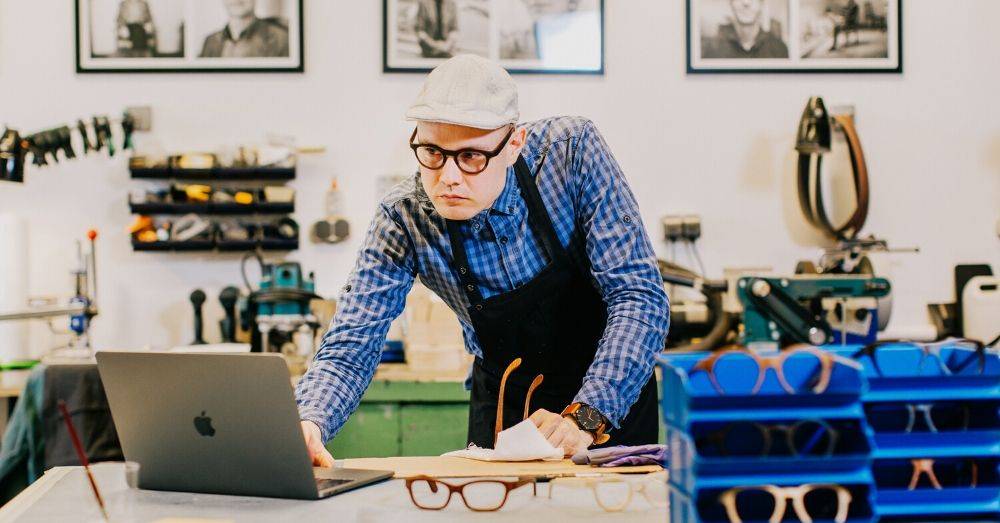
Perfecting the production processes of a factory line is the bane of manufacturers or floor-level managers. That’s why many adopt lean inventory or manufacturing practices to help them achieve this task.
However, it’s one thing to know about lean techniques, but how do you decide which areas of your business you need to improve?
In this article, we’re going to look into SPC manufacturing, a quality improvement technique to help you gather data to monitor your production processes, and make the necessary adjustments.
So, without further ado, let’s begin.
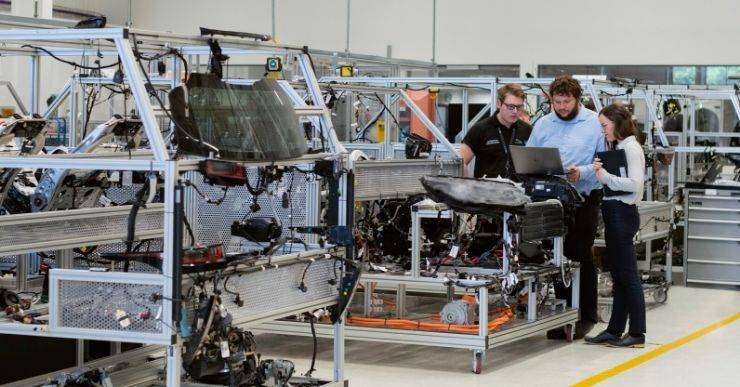
What is SPC?
Statistical process control quality (or SPC for short) is considered the industry standard when it comes to measuring and controlling quality during your production runs.
SPC manufacturing comes in the form of gathering data on your products or processes in real-time using a graph with pre-determined control limits to measure its efficiency.
You can determine what your control limits are by the capability of your production lines.
This means, if the data you gather falls within your control limits, it’s a sign that everything is running as it’s supposed to.
But, if the data falls outside of your control limits, this suggests that issues are occurring, and something needs to change along your production line before it leads to bigger problems.
Using the information you gather, you can identify the areas of inefficiency and waste in your business and quantifying the value of an SPC solution by asking yourself the following questions:
- What are your quality costs?
- Can you make improvements with the data you’re gathering?
- Are you collecting the right data in the right areas?
- Are business decisions being made with up-to-date information?
- Can you easily identify the cause of quality issues?
- Do you know when to perform predictive maintenance? And
- Is your demand forecasting correct?
Now you know what statistical process control quality improvement is, what’s the objective of SPC manufacturing?
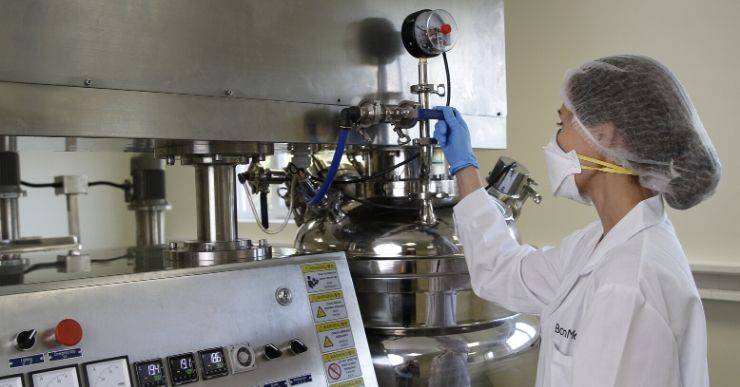
What is the Objective of SPC Manufacturing?
SPC manufacturing is an important tool for improving the quality of your products by analyzing:
- The services you provide to your customers;
- Your management leadership;
- The commitment of management;
- Continuous improvement;
- Your responsiveness;
- Actions based on data;
- Your team members participation; and
- Your dedication to providing quality.
The purpose of adopting SPC tools into your business is to achieve more control over:
- Receiving materials;
- Handling internal rejections;
- Customers;
- Claims;
- Suppliers; and
- Evaluations of any corrective actions taken.
Effective management of these statistical process control examples all plays a part in improving the quality of your production.
Developing and using these performance indicators are linked (directly or indirectly) to customer requirements, satisfaction, and management.
Let’s now take a gander at the variations in SPC manufacturing you need to know.
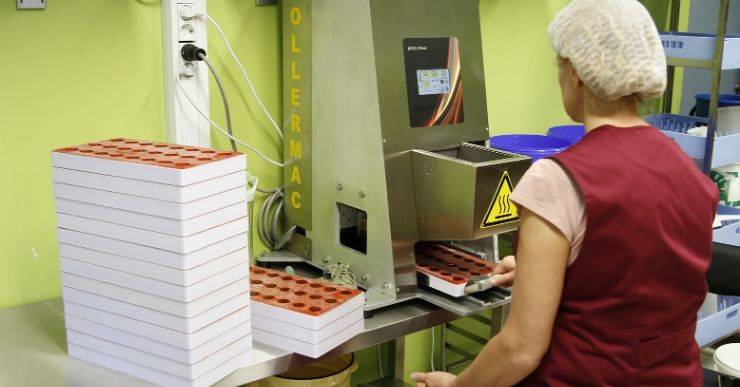
SPC Quality Variations in Manufacturing
You can think of SPC quality as conformance to your production’s specifications, although the issue is that products or characteristics are often not the same, due to processes containing sources of variability.
In the traditional mass-manufacturing process, the finished products (or samples in batch manufacturing) are inspected to determine the quality of the goods.
With SPC tools, you can observe the performance of production to identify variations before they lead to defective products.
fall into one of two categories:
Common causes
Sometimes referred to as a ‘non-assignable’ or a normal source of variation. A common cause is a variation (or issue) that consistently acts on the process and is a reoccurring problem that is predictable.
Statistical process control examples for common variations could be an employee who takes longer than forecasted to finish a task, or the working conditions being poor.
Special causes
Sometimes referred to as ‘assignable’ sources of variations. This means there’s a factor that’s affecting production, but intermittently and unpredictably.
Statistical process control examples for special variations could be equipment malfunctions or even an accident that happened on the way to work, which impeded a worker’s journey.
Knowing these variations can help you adopt SPC lean manufacturing since some minor issues can be ignored, but the larger ones need to be identified and addressed. Otherwise, you’re going to drive up your production costs.
Before we move onto the seven steps to implementing statistical process control quality, let’s first look into the two phases you need to follow if you wish to practice SPC lean production.
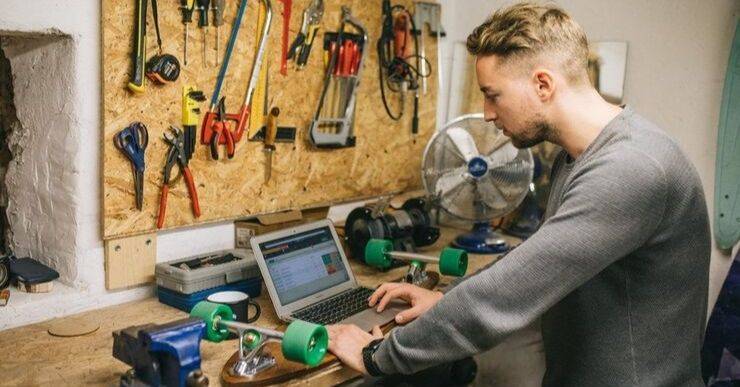
The Two Phases of Statistical Process Control
Now you know what is SPC and the variations you’ll need to identify when getting it set up, you’ll need to understand what it is you’ll need to do.
And this will be done in two phases:
Phase one
Identifying and establishing the process. That’s determining what you’ll be analyzing along your manufacturing routes with SPC tools.
Phase two
Deciding the period or time length you wish to carry out this analysis, depending on the changes made to the 5Ms & E conditions:
- Man;
- Machine;
- Material;
- Method;
- Movement; and
- Environment.
You’ll need to also include the wear rates of your equipment.
The advantages of using SPC manufacturing is improving production quality with early detection systems and the prevention of problems causing further damage.
Not only that, but SPC manufacturing is also a great technique for reducing waste and manufacturing lead time.
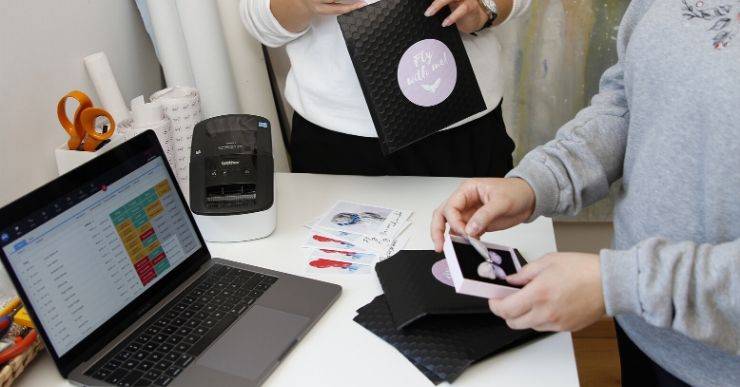
How to Implement SPC Manufacturing in Seven Steps
Following these following steps is going to be crucial for getting set up with SPC manufacturing, starting with:
1. Choosing the Critical-to-Quality (CTQ) Product Characteristics
CTQ in SPC manufacturing is the process of identifying the needs of the customer and translating that information into measurable production and process requirements.
Statistical process control examples of a CTQ could be a baker who makes sweet pastries.
To make the pastries sweet, the baker will need sugar, which will be a defining characteristic of this product.
2. Choosing Your Critical Processes
You can determine if a process is critical or not by knowing that if something was to go wrong with this process, would it have a big impact on at least one of the CTQ characteristics.
You’ll need to monitor these critical processes to achieve SPC lean manufacturing.
An example of a critical process, once again in the context of a baker, could be when the pastries go into the oven, they need to be set to a specific temperature.
3. Deciding Whether Your Machines Can Calculate SPC Autonomously
Can the machines on your production line or your production scheduling software help you collect and analyze SPC data, and also issue alerts when things are starting to get out of control?
If you’re using inefficient Excel spreadsheets, it’s going to be difficult to dedicate your time or team members to performing an analysis each day to make sure production is running smoothly.
Pro tip:
If you want inexpensive SPC tools, you can also look into shop floor control to provide you with automated data collection and analysis.
4. Gathering Information on What Impacts the Output of Your Processes
Identify and monitor anything that is going to affect your production lines.
To get you started, you can follow these statistical process control examples:
Process input: Glue.
Process settings: Cycle time, fixture.
Environment: Temperature, humidity.
The state of the glue and the ambient humidity are variables that you’ll need to control.
5. Control Your Independent Variables Which Have the Biggest Impact on Output
To do this, you’re going to need to choose how to focus your resources on controlling these variables.
You can do this by:
- Gathering data on variables at regular intervals. The amount of time you allow to pass is up to you; or
- Train yourself and team members on how to make calculations and how to plot them on a chart.
For example, out of all the SPC tools, the Xbar-R charts tend to be the most popular. When designing this chart, set the goal for the CPK, and your team members can begin plotting the evolution of that index as time goes by.
6. Always Look to Improve Processes
Now that all your variations are visible with statistical process control charts, the next step is to work toward reducing them.
Using your charts, you can now see your production capabilities, and make changes to make your production more efficient than it is now.
7. Keep it Going
You might manage to reduce variation, but the idea is to adopt SPC manufacturing for the long haul.
Once you achieve your goal, keep setting new targets, and stay in control of the key variables in your production.
When your process characteristics start to drift, your statistical process control systems will notify you.
Once you follow these steps you can consider yourself fully set up. Just, try not to tamper with the process too much, as constantly making little adjustments here and there will make the process unstable.
So, there are the seven steps you can follow to implement SPC manufacturing into your business. But, what are the different SPC tools you can use to help you collect and measure your processes data?
Seven SPC Tools You Can Use
In 1974, Dr. Kaoru Ishikawa put together a collection of SPC tools manufacturers can use to improve their processes, called Guide to Quality Control.
These SPC tools can be found below:
- Cause-and-effect diagram;
- Check sheet;
- Control chart;
- Histogram;
- Pareto chart;
- Scatter diagram; and
- Stratification.
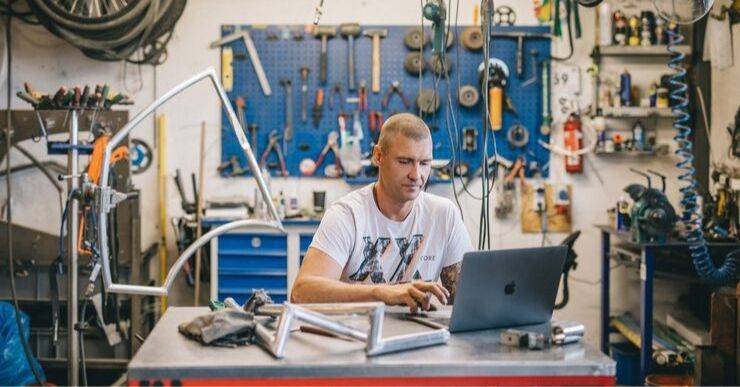
Conclusion
And there you have it, the ins-and-outs to SPC manufacturing and what you need to do to implement this approach.
As for if this approach is for your business or not, you need to understand if you’re going to benefit from having these systems in place.
For smaller manufacturers just starting, in-depth analysis such as this might not be beneficial. But, once you start to scale, learning how to analyze your production lines will help you reduce costs and waste.
However, if the mathematics behind the SPC tools are intimidating, you can always turn to Smart
Manufacturing Software, which will give you more control, in real-time, over:
- Inventory management
- Your reorder points
- Bottleneck management
- Supply chain management
- Sales and manufacturing orders
- Floor-level operations
We hope that you found this article useful, and if you have any questions, feel free to drop us a comment below or over on our social media channels.
And until next time, happy manufacturing.
Team Katana
Table of contents
Get inventory trends, news, and tips every month
Get visibility over your sales and stock
Wave goodbye to uncertainty with Katana Cloud Inventory — AI-powered for total inventory control